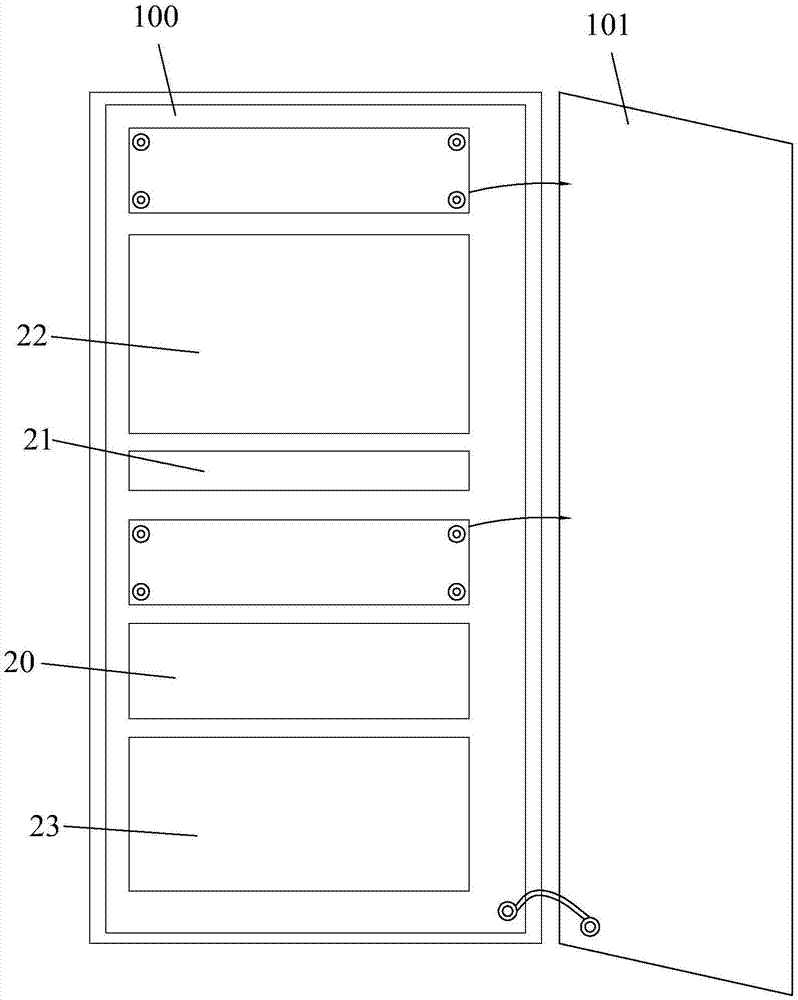
本发明涉及一种静态棒位线性度测量技术,具体涉及在核电厂反应堆内控制棒整个动棒周期内测量棒位线性度,自动给出每组控制棒的线性度判断结果。
背景技术:
:参考中国专利文件cn201310648117.6,公开了一种控制棒位置线性测量系统及方法,使用硬件电路在测量控制棒的位置,其准确性和稳定性完全依赖于硬件电路电子元器件,使得控制棒棒位测量的准确性不够,影响控制棒位置的线性测量。再一方面,在控制棒棒位测量时,如果给定棒棒位信号出错,控制棒的实际棒位受其影响将受到波动,若按照出错的给定棒棒位信号和实际棒位进行测算时,往往会出现错误,可能会将异常当做正常处理,或者将正常信号误认为异常,测量结果准确性差。故急需一种可解决上述问题的核电厂控制棒静态棒位线性度测量方法及装置。技术实现要素:本发明的目的是提供一种核电厂控制棒静态棒位线性度测量方法及对应的电子设备和可读存储介质,测量结果准确。为了实现上有目的,本发明公开了一种核电厂控制棒静态棒位线性度测量方法,包括以下步骤:实时采集反应堆控制棒的测量棒位信号和给定棒位信号;对采集的测量棒位信号和给定棒位信号进行处理,包括步骤:判断所述测量棒位信号是否发生方向性跳变,若是则滤除跳变的测量棒位信号和给定棒位信号;计算将滤除处理后的测量棒位信号及其对应的给定棒位信号之间的棒位差值,从而获得整个控制棒运动过程的线性度表。与现有技术相比,一方面,本发明可滤除跳变的给定棒位信号dp和测量棒位信号mp,排除多余干扰,保证测试结果的准确性,防止出现非必要报警或者将非正常情况作为正常情况,未及时发现错误。再一方面,本发明采集到数据后,自动对采集到的数据进行实时分析处理,并给出整个控制棒运行过程中的线性度结果误差,计算快速,有效解决了核电厂棒控棒位系统控制棒静态棒位线性度测量的问题,为棒位测量系统和棒位探测器设计、应用和维护提供依据,同时保证棒位测量系统和控制棒可用,保障核电安全。较佳地,在实时采集测量棒位信号和给定棒位信号之前,还包括:与棒控棒位系统连接,以实时采集反应堆控制棒的测量棒位信号和给定棒位信号。本发明直接与棒控棒位系统连接,用于获取反应堆控制棒的测量棒位信号和给定棒位信号,整个数据采集结果准确。另一方面,具体地,本发明通过交换机连接到系统局域网中,并依据工业以太网协议与棒控棒位系统连接,以实时采集反应堆控制棒的测量棒位信号和给定棒位信号,无需接线,效率高。较佳地,实时采集反应堆控制棒的测量棒位信号和给定棒位信号时,控制控制棒运动:将控制棒提到低位,以预设棒速提升控制棒,直至将控制棒提到高位后,以预设棒速下插控制棒,直至所述控制棒插到低位。较佳地,对采集到的测量棒位信号和给定棒位信号进行实时分析处理还包括:(a)判断所述棒位差值是否超出对应的预设值,若是则进行报警并标示,所述预设值包括提棒过程对应的预设值,插棒过程的预设值和受方向性跳变影响的预设值。该方案可在控制棒运行过程中确定当前运行状态是否正常,并在出现问题时及时报警,而将出错的位置标示出来,便于后续应用、维修。较佳地,对采集到的测量棒位信号和给定棒位信号进行实时分析处理还包括:(b)在所述测量棒位信号发生方向性跳变时,判断所述棒位差值是否超出对应的预设值,若是则进行报警并标记。该方案针对发生方向性跳变的特殊性,判断棒位差值是否超出发生方向性跳变状态对应的预设值,增加测试结果的准确性。较佳地,滤除跳变的测量棒位信号和给定棒位信号的具体步骤为:判断所述控制棒处于提棒过程还是插棒过程,在提棒过程中,判断任一时刻的测量棒位信号是否大于等于前一时刻的测量棒位信号,若当前测量棒位信号小于前一刻的测量棒位信号,则回溯之前的测量棒位信号,删除所有比当前的测量棒位信号大的前一刻测量棒位信号,直至遇到比当前所述测量棒位信号对应小的前一刻测量棒位信号;在插棒过程中,判断任一时刻的测量棒位信号是否小于等于前一时刻的测量棒位信号,若当前测量棒位信号大于前一刻的测量棒位信号,则回溯之前的测量棒位信号,删除当前的测量棒位信号,直至当前测量棒位信号小于等于前一刻测量棒位信号。较佳地,滤除处理前,还将所述给定棒位信号以测量棒位信号的棒位为单位进行分组并存储。较佳地,对采集到的测量棒位信号和给定棒位信号进行实时分析处理还包括:依据所述棒位差值计算棒位回差从而获得整个控制棒运动过程的回差表。本发明同时测量整个控制棒运行过程中的线性度结果误差和回差,有助于维修人员确认问题。具体地,所述棒位的回差包括提棒最小值、提棒最大值、插棒最小值、插棒最大值、到达回差和离开回差,所述提棒最小值为提棒过程中棒位差值的最小值,所述提棒最大值为提棒过程中棒位差值中的最大值,所述插棒最小值为插棒过程中棒位差值的最小值,所述插棒最大值为插棒过程中棒位差值的最大值,离开回差为提棒最大值和插棒最大值之差,所述到达回差为提棒最小值和插棒最小值之差。通过提棒最小值、提棒最大值、插棒最小值、插棒最大值、到达回差和离开回差可准确直观的发现问题所在。更具体地,对采集到的测量棒位信号和给定棒位信号进行实时分析处理还包括:(b)判断所述到达回差和离开回差是否超出对应的预设值,若是则进行报警并标示。较佳地,依据外部输入的命令或者在分析处理完成后将分析处理的结果显示、导出和/或打印。本发明在分析处理完后,可以支持数据打印、显示和导出,操作方便。本发明还公开了一种电子设备,包括:一个或多个处理器;存储器;以及一个或多个程序,其中所述一个或多个程序被存储在所述存储器中,并且被配置成由一个或多个处理器执行,所述程序包括用于执行上述的核电厂控制棒静态棒位线性度测量方法的指令。较佳地,所述电子设备包括打印机、输入模块和显示模块,所述核电厂控制棒静态棒位线性度测量方法配合对应的输入模块、显示模块和打印机,接收外部输入的命令,并依据外部输入的命令或者在分析处理完成后将分析处理的结果显示、导出和/或打印。本发明还公开了一种计算机可读存储介质,包括与具有存储器的电子设备结合使用的计算机程序,所述计算机程序可被处理器执行以执行上述的核电厂控制棒静态棒位线性度测量方法。附图说明图1是本发明所述监测柜机箱前门打开的结构示意图。图2a是本发明所述核电厂控制棒静态棒位线性度测量方法的流程图。图2b是本发明所述核电厂控制棒静态棒位线性度测量方法采集数据时控制棒运行的状态图。图3是本发明所述核电厂控制棒静态棒位线性度测量方法的具体流程图。图4是本发明第二实施例中对采集到的测量棒位信号和给定棒位信号进行分析处理的方法的流程图。图5是本发明提棒过程中发生方向性跳变时滤除跳变的给定棒信号的示意图。图6是本发明插棒过程中发生方向新跳变时滤除跳变的给定棒信号的示意图。图7是本发明回差曲线表。具体实施方式为详细说明本发明的技术内容、构造特征、所实现目的及效果,以下结合实施方式并配合附图详予说明。参考图1,本发明公开了一种监测柜机箱100,参考图1,监测柜机箱100前门101打开后,可看出所述监控柜机箱100内安装有检测机箱20,检测机箱20包括处理器、存储器、以及程序,其中所述程序被存储在所述存储器中,并且被配置成由处理器执行,所述程序包括用于执行核电厂控制棒静态棒位线性度测量方法200的指令。参考图2a,所述核电厂控制棒静态棒位线性度测量方法200包括以下步骤:(34)实时采集提棒和插棒时的测量棒位信号和给定棒位信号,(35)对采集到的测量棒位信号和给定棒位信号进行分析处理。在本实施例中,处理器包括1个pxie-8135控制器模块,存储器包括1个ni8260数据存储模块。其中,检测机箱20还包括6个pxi-6225数据采集模块,通过交换机连接到系统局域网中,并依据工业以太网协议与棒控棒位系统30连接,采集反应堆控制棒的测量棒位信号和给定棒位信号。较佳者,参考图1,监测柜机箱100还包括分别与所述检测机箱20连接的输入模块21、显示模块22和打印模块23,所述输入模块21输入外部的命令,并将所述命令输送至所述检测机箱20,所述检测机箱20依据外部输入的命令或者在分析处理完成后将分析处理的结果输送至显示模块22显示、输送至打印模块23打印、导出至pdf文件。本实施例中,输入模块21为键盘。参考图3,所述步骤(35)具体步骤包括:(11)判断所述测量棒位信号是否发生方向性跳变,若是则(12)滤除跳变的测量棒位信号和给定棒位信号,(13)计算滤除跳变信号后的测量棒位信号及其对应的给定棒位信号之间的棒位差值,从而获得整个控制棒运动过程的线性度表。其中,在采集测量棒位信号和给定棒位信号之前,将检测机箱20与棒控棒位系统30连接,以可实时采集反应堆控制棒的测量棒位信号和给定棒位信号。参考图2b,执行步骤(34)以开始采集给定棒位信号和测量棒位信号后,操作棒控棒位系统以使控制棒运行,具体包括:(31)控制控制棒提到5步(低位,可依据实际需要确定),以(32)以预设棒速提升控制棒,直至将控制棒提到255步(高位,可依据实际需要确定)后,以(33)以预设棒速下插控制棒,直至所述控制棒插到低位。此时,可停止采集数据(步骤34执行结束)。当然,也可以在连续采集时间超过预设时间时停止采集数据。参考图4,所述步骤(35)中,步骤(11)之前还包括:(14)将所述给定棒位信号以测量棒位信号的棒位为单位进行分组并存储。本实施例中,测量棒位信号mp以8步为单位变化(0,8,16,24……224),每一测量棒位信号mp对应一组连续的给定棒位信号dp。具体地,滤除跳变的测量棒位信号和给定棒位信号的具体步骤为:判断所述控制棒处于提棒过程还是插棒过程。参考图5,在提棒过程中,判断任一时刻的测量棒位信号是否大于等于前一时刻的测量棒位信号,若当前测量棒位信号小于前一刻的测量棒位信号,则回溯之前的测量棒位信号,删除所有比当前的测量棒位信号大的前一刻测量棒位信号(如图5中的测量棒位信号点a),直至遇到比当前所述测量棒位信号对应小的前一刻测量棒位信号,若当前测量棒位信号大于等于前一刻的测量棒位信号,则检测判断下一个测量棒位信号。参考图6,在插棒过程中,判断任一时刻的测量棒位信号是否小于等于前一时刻的测量棒位信号,若当前测量棒位信号大于前一刻的测量棒位信号,则回溯之前的测量棒位信号,删除当前的测量棒位信号(如图6中的测量棒位信号点b),直至当前测量棒位信号小于等于前一刻测量棒位信号,若当前测量棒位信号小于等于前一刻的测量棒位信号,则检测判断下一个测量棒位信号。参考图4,所述步骤(13)之后还包括:(15)依据所述棒位差值计算棒位回差从而获得整个控制棒运动过程的回差表。其中,所述棒位的回差包括提棒最小值withdraw(-)、提棒最大值withdraw(+)、插棒最小值insert(-)、插棒最大值insert(+)、到达回差hysteresis(-)和离开回差hysteresis(+),所述提棒最小值withdraw(-)为提棒过程中棒位差值的最小值,所述提棒最大值withdraw(+)为提棒过程中棒位差值中的最大值,所述插棒最小值insert(-)为插棒过程中棒位差值的最小值,所述插棒最大值insert(+)为插棒过程中棒位差值的最大值,离开回差hysteresis(+)为提棒最大值withdraw(+)和插棒最大值insert(+)之差,所述hysteresis(-)为提棒最小值withdraw(-)和插棒最小值insert(-)之差。通过提棒最小值、提棒最大值、插棒最小值、插棒最大值、到达回差和离开回差可准确直观的发现问题所在。其中,所述步骤(15)具体包括:依据所述棒位差值计算棒位回差,依据棒位回差绘制整个控制棒运动过程的回差列表(见表一),依据棒位回差绘制整个控制棒运动过程中的回差曲线(见图7)。回差表包括回差列表和回差曲线。mpwithdraw(-)withdraw(+)insert(-)insert(+)hysteresis(-)hysteresis(+)0/20/5/158-24-240016-35-340124-26-957132-15-2411…………………表一参考图4,所述步骤(13)之后还包括:(16)判断棒位差值是否超出预设值,若是则(17)进行报警并标示(例如标红)。其中,步骤(15)具体包括:在提棒过程中,判断给定棒信号和对应的测量棒位信号之间的棒位差值是否超出第一预设值,若是则报警并标示,在本实施例中,第一预设值为(-5,+6)。在插棒过程中,判断测量棒位信号及其对应的给定棒位信号之间的棒位差值是否超出第二预设值,若是则报警并标示,在本实施例中,第二预设值为(-6,+5)。当提插棒过程中给定棒信号发生方向新跳变时,判断受到影响的测量棒位信号及其对应的给定棒位信号之间的棒位差值是否超出第三预设值,若是则报警并标示,在本实施例中,第三预设值为(-4,+7)。参考图4,在步骤(15)之后还包括:(18),判断棒位回差是否超出预设值,若是则(19)进行报警并标示(例如标红)。其中,步骤(18)具体为:判断到达回差和离开回差是否超出第四预设值。本实施例中,第四预设值为(-1,+1)。参考图2a、图2b和图4,描述本发明核电厂控制棒静态棒位线性度测量方法200,与棒控棒位系统连接以实时采集测量棒位信号和给定棒位信号;(31)控制控制棒提到5步(低位,可依据实际需要确定),以(32)预设棒速提升控制棒,直至将控制棒提到255步(高位,可依据实际需要确定)后,以(33)以预设棒速下插控制棒,直至所述控制棒插到低位。(34)实时采集反应堆控制棒的测量棒位信号和给定棒位信号,从而获得控制棒运行过程中所有的测量棒位信号和给定棒位信号。(35)对采集的测量棒位信号和给定棒位信号进行处理:(14)将所述给定棒位信号以测量棒位信号的棒位为单位进行分组并存储并执行步骤(11),(11)判断所述测量棒位信号是否发生方向性跳变,若是则(12)滤除跳变的测量棒位信号和给定棒位信号,若否则不滤除,直至滤除处理完所有的测量棒位信号。(13)计算测量棒位信号及其对应的给定棒位信号之间的差值以获取所述棒位差值,执行步骤(15)和步骤(16)。(15)依据所述棒位差值计算棒位回差从而获得整个控制棒运动过程的回差表,执行性步骤(17)。(16)判断棒位差值是否超出预设值,若是则(17)进行报警并标示(例如标红)。(18),判断棒位回差是否超出预设值,若是则(19)进行报警并标示。以上所揭露的仅为本发明的优选实施例而已,当然不能以此来限定本发明之权利范围,因此依本发明申请专利范围所作的等同变化,仍属本发明所涵盖的范围。当前第1页12