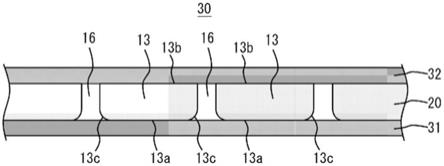
1.本发明涉及具有芯材层的复合材料等。
背景技术:2.形成为所谓三明治结构的结构材料(例如参照专利文献1~专利文献2)的一般特征在于轻量且高刚度。该特征的本质在于单位密度的刚度高。在复合材料产生弯曲应力时,表皮材料的应力负担变大,芯材的应力负担变得相对较小。因此,在芯材层的芯材使用低密度且在一定程度上刚度较高的材料。
3.作为以单一材料形成的轻量的结构材料,提供了被称为i型梁的型材。该i型梁例如用作建筑结构物的梁。i型梁由在上下对置配置的宽度较宽的翼缘板(板材)与将它们连接对位的宽度较窄的腹板(板材)构成,被广泛用作以单一材料形成的轻量且能够实现高刚度的结构。三明治结构及i型梁结构均能够通过增加板材的厚度来指数级地提高刚度。
4.三明治结构的复合材料典型地被用作预制装配式住宅的墙壁材料。该情况下,例如,使用铝板作为表皮材料,使用发泡聚苯乙烯作为芯材。三明治结构的复合材料也被用于航空器和铁道车辆等。该情况下,例如,使用纤维增强塑料材料(frp)作为表皮材料,使用由铝或含浸有树脂的芳纶纸形成的蜂巢结构材料作为芯材。三明治结构的复合材料也被用作捆包箱。该情况下,例如表皮材料由纸构成,芯材也一样由纸构成。芯材使用成形为波形的桁架(truss)结构。
5.三明治结构的芯材的密度比表皮材料小。因此,由于与芯材的轻量化程度对应地来增加芯材的厚度,其结果为,作为三明治结构能够增加比刚度(单位比重(密度)的刚度),实现轻量且高刚度。已知结构材料的弯曲刚度通过增加其截面的弯曲方向的厚度而指数级地提高,在四边形截面的情况下,弯曲刚度与厚度的立方成正比提高。在三明治结构中,若芯材的密度比表皮材料更低,则即使不采用树脂发泡体作为芯材,比刚度也会增加。这在采用金属材料或木质材料等任何材料作为芯材的情况下都是同样的。这是因为,一般来说在考察结构材料的弯曲刚度的情况下,相对于弯曲方向越靠近厚度的中心部分,弯曲变形越少,对结构材料的刚度的贡献越少。从而,降低该中心部分的密度对于确保了刚度的状态下的轻量化来说变得有益。
6.在此,专利文献1的图9公开了芯材、由配置于芯材的两面的纤维增强材料构成的三明治结构体、以及芯材的岛状结构。该芯材是对将聚丙烯树脂压制成形而得的薄膜进行冲压加工,制成圆板状板以后,将圆板状板以形成规定的间隔的方式配置而成的。
7.此外,专利文献2公开了由片材状的基底材料制成的加强结构。在该加强结构中,具有将基底材料分割为多个材料岛的材料衰减部。材料岛被材料衰减部分开,但相互连接。
8.现有技术文献
9.专利文献
10.专利文献1:日本专利第5151535号公报
11.专利文献2:美国专利申请公开第2019/0099964a1号公报
技术实现要素:12.发明要解决的技术问题
13.另外,在专利文献1所记载的三明治结构体中,为了将芯材的岛状结构设置在纤维增强材料上,将通过冲压加工制成的多个圆板状板逐个地配置于纤维增强材料上。然而,将圆板状板逐个配置并不容易。
14.另一方面,在专利文献2所记载的加强结构中,多个材料岛相互连接而一体化。因此,将加强结构层叠于覆盖层相对较容易。然而,在将复合材料成形为三维形状的情况下,由于存在材料岛彼此的连接部,因此将加强结构弯曲的范围受到限制。此外,在将复合材料成形为复杂的三维形状的情况下,各材料岛的变形无法被容错,还有连接部周边发生破损的风险。在专利文献2所记载的加强结构中,随着对复合材料的需求提高,难以提供对三维形状的成形性优异的复合材料。
15.本发明是鉴于这样的情况而完成的,其目的在于提供对三维形状的成形性优异、并且容易制造的复合材料。
16.用于解决上述技术问题的方案
17.为了解决上述技术问题,本技术发明人想到了一种方法,在将成为多个板状片的原料的材料片材粘贴于基材片材的状态下,对材料片材进行切割加工,制作将多个板状片粘贴于基材片材而得的中间片材,利用该中间片材作为后述的转印片材、粘接用芯材片材或复合材料制造用片材等来制造复合材料。作为通过该制造方法得到的复合材料或中间片材,第1发明是一种层叠材料,具备芯材层、层叠于芯材层的表皮材料,芯材层具有沿表皮材料的表面排列的多个板状片,在芯材层中,相邻的板状片隔着间隙或通过切口而成为单体,在多个板状片中,通过形成于外周的切割痕判别的厚度方向上的切割朝向彼此相同。另外,在本说明书中,“中间片材(中间材料)”是指在复合材料的制造过程中的中间工序制成的片材。此外,“芯材层”是指形成三明治结构的中心层的部件。其中,在成形为复合材料前的层叠材料中,即使在处于叠层(canap
é
)结构的情况下,也将与成形后的复合材料中的中心层对应的部件称为“芯材层”。
18.第2发明是在第1发明中,在芯材层中,在俯视下,板状片的合计面积相对于总面积的比例为50%以上。
19.第3发明是在第1或第2发明中,在层叠于板状片的主面中的、位于切割的推进侧作为厚度方向上的切割朝向的主面的表皮材料中,在芯材层侧的面不存在假如在表皮材料上通过切割加工使多个板状片成形就会形成的切割伤。
20.第4发明是在第1~第3的任一项发明中,多个板状片各自由硬质发泡体构成。
21.第5发明是在第1~第3的任一项发明中,多个板状片各自由木材构成。
22.第6发明是在第1~第5的任一项发明中,以表皮材料作为第1表皮材料,进一步具备第2表皮材料,配置在芯材层中的第1表皮材料的相反侧,与第1表皮材料一起夹着芯材层。
23.第7发明是在第6发明中,以芯材层作为第1芯材层,进一步具备:第2芯材层,具有沿第2表皮材料的表面排列的多个板状片;中间粘接层,配置于第1芯材层与第2芯材层之间并将第1芯材层与第2芯材层粘接,依次对第1表皮材料、第1芯材层、中间粘接层、第2芯材层、第2表皮材料进行层叠。
24.第8发明是在第7发明中,中间粘接层由片材状粘接剂形成。
25.第9发明是在第1~第8的任一项发明中,中间粘接层由片材状粘接剂形成。
26.第10发明是在第6~第9的任一项发明中,在相邻的板状片之间的间隙填埋有固化的树脂。
27.第11发明是在第1~第5的任一项发明中,表皮材料为片材状粘接剂。
28.第12发明是在第1~第5的任一项发明中,表皮材料为半固化状态的预浸料。
29.第13发明是在第1、第2、第4或第5发明中,多个板状片相对于表皮材料可剥离地粘贴,被用作能够将多个板状片从表皮材料向其他结构材料转印的转印片材。
30.第14发明是在第13发明中,多个板状片被感温性粘合剂粘贴于表皮材料。
31.第15发明是在第1~第13的任一项发明中,在表皮材料与板状片之间设有用于保持板状片的位置的粘合层或粘接层。
32.第16发明是在第1~第15的任一项发明中,在板状片形成有由贯通孔构成的划分空间。
33.第17发明是粘贴有复合材料的芯材中使用的多个板状片的中间片材的制造方法,进行切割步骤,通过对粘贴于基材片材的状态下的材料片材进行切割加工,将材料片材分割为多个板状片,得到多个板状片被粘贴于基材片材的中间片材,中间片材被用作转印片材或者粘接用芯材片材,所述转印片材能够将多个板状片从基材片材向其他结构材料转印,所述粘接用芯材片材是为了将基材片材用作粘接剂而在层叠于成为复合材料的表皮材料的表皮材料用片材的状态下使基材片材熔解而得的。
34.第18发明是在第17发明中,进行如下步骤:粘贴步骤,对转印片材中的板状片侧粘贴片材状粘接剂或预浸料作为中间片材的表皮材料;转印步骤,在粘贴步骤之后,通过从多个板状片剥下基材片材,将多个板状片转印至中间片材的表皮材料。
35.第19发明是一种复合材料的制造方法,进行如下步骤:粘贴步骤,对通过第17发明的制造方法得到的转印片材中的板状片侧粘贴成为复合材料的表皮材料的表皮材料用片材;转印步骤,在粘贴步骤之后,通过从多个板状片剥下基材片材,将多个板状片转印至表皮材料用片材。
36.第20发明是在第19发明中,表皮材料使用具有伸缩性的片材,在转印步骤中,通过在拉伸基材片材的同时从基材片材10的背面按压转印对象的板状片,进行该板状片的转印。
37.第21发明是在第20发明中,在转印步骤之后进行如下步骤:层叠步骤,利用表皮材料用片材与第2表皮材料用片材夹着多个板状片;蜂巢形成步骤,在使树脂流入由多个板状片构成的芯材层的间隙后,通过使该树脂固化,在芯材层形成树脂的蜂巢结构。
38.发明效果
39.在本发明中,在层叠材料为中间片材的情况下,作为通过在表皮材料(例如基材片材)上进行切割加工来使多个板状片成形的痕迹,在多个板状片中,通过形成于外周的切割痕判别的厚度方向上的切割朝向彼此相同。在中间片材的表皮材料上,与切割加工中的俯视下的切割形状对应地成形有多个板状片。
40.此外,在层叠材料为复合材料的情况下,作为使用上述中间片材而制造的痕迹,在多个板状片中,通过形成于外周的切割痕判别的厚度方向上的切割朝向彼此相同。在复合
材料的表皮材料上,与中间片材中的板状片的排列对应地配置多个板状片。因此,无需在表皮材料的材料(例如表皮材料用片材)上逐个配置多个板状片,能够容易地形成排列了多个板状片的芯材层。
41.此外,相邻的板状片隔着间隙或通过切口而成为单体。因此,在将复合材料成形为三维形状时,与多个材料岛相互连接的复合材料相比,弯曲芯材层的范围的限制较小,对三维形状的成形性优异。根据本发明,能够提供对三维形状的成形性优异、并且容易制造的复合材料。
附图说明
42.图1是实施方式的复合材料的立体图。
43.图2是实施方式的复合材料的截面图。
44.图3是对实施方式的复合材料的芯材层形成有倒角部的一侧的俯视图。
45.图4是实施方式的转印片材的截面图。
46.图5是用于对实施方式的第1制造工序(转印片材的制造方法)进行说明的截面图。
47.图6是在实施方式的第1制造工序中使用的生产线的概略构成图。
48.图7是用于对在实施方式的第1制造工序的压切时,在板状片形成倒角部的状况进行说明的截面图。
49.图8是用于对实施方式的第2制造工序的转印步骤进行说明的截面图。
50.图9是用于对实施方式的第2制造工序的层叠步骤进行说明的截面图。
51.图10是在实施方式的第2制造工序中,使用模腔表面弯曲的成形模具的情况下的截面图。
52.图11是在实施方式的复合材料中,将固化的树脂填充至间隙的情况下的截面图。
53.图12是第1变形例的复合材料的截面图。
54.图13是第2变形例的复合材料的制造过程的层叠材料的截面图。
55.图14是第3变形例的粘接用芯材片材的截面图。
56.图15是用于对第3变形例的粘接用芯材片材的制造过程中的转印步骤进行说明的截面图。
57.图16是第4变形例的粘接用芯材片材的截面图。
58.图17是示出第5变形例中,将粘贴了多个板状片的基材片材(prepreg:预浸料)设置在成形模具上的状态的截面图。
59.图18是第6变形例的复合材料的制造过程的层叠材料的截面图。
60.图19是第7变形例的复合材料的立体图。
61.图20是使用了第7变形例的复合材料的圆筒体的截面图。
62.图21的(a)是第8变形例的复合材料的芯材层的俯视图,图21的(b)是第8变形例的复合材料的截面图。
63.图22是第9变形例的复合材料的芯材层的俯视图。
64.图23的(a)是第10变形例的转印片材的截面图,图23的(b)是第10变形例的复合材料的截面图,图23的(c)是第10变形例的转印片材的制造过程中,对板状片重叠粘合层形成用的转印片材的点部侧的状态的俯视图。
65.图24是第10变形例的其他复合材料的截面图。
66.图25是使用第11变形例的转印片材进行板状片的转印的状况的截面图。
67.图26的(a)是另一变形例的转印片材的截面图,图26的(b)是另一变形例的复合材料的截面图。
68.图27是用于对另一变形例的复合材料中,在第1制造工序的压切时,在相邻的板状片之间形成切口的状况进行说明的截面图。
具体实施方式
69.以下,参照附图对本发明的实施方式进行详细说明。另外,以下的实施方式是本发明的复合材料等的一例,并非用于对本发明、其应用物、或者其用途的范围进行限制。
70.[复合材料的构成]
[0071]
对本实施方式的复合材料(层叠材料)30进行说明。如图1及图2所示,复合材料30是三明治结构的面板。复合材料30具备:芯材层(也称为“中间层”)20;第1表皮材料31,层叠于芯材层20;第2表皮材料32,层叠于芯材层20中的第1表皮材料31的相反侧,与第1表皮材料31一起夹着芯材层20。复合材料30例如能够用于与强度相比更重视轻量和刚度的面板材料。具体而言,复合材料30作为结构材料,能够用于航空器、汽车或自行车(运动用自行车等)等移动体、电气设备、电子设备、办公设备、家电设备、医疗设备、或者建材的板材等。在移动体的情况下,复合材料30能够用作构成外装的空气动力部件。
[0072]
各表皮材料31、32是由与芯材层20不同种类的材料构成的例如皮材料或面板材料。作为各表皮材料31、32的材料,可以使用金属类、塑料类或者无机类的任一种。在本实施方式中,各表皮材料31、32的材料使用了纤维增强塑料。作为纤维增强塑料,能够使用通过碳纤维增强的纤维增强塑料。作为该纤维增强树脂,能够使用在碳纤维中含浸有树脂(基质)的预浸料(例如,三菱化学株式会社制的“pyrofil prepreg(注册商标)”)。该预浸料的基质能够使用热固性环氧树脂。
[0073]
另外,作为纤维增强塑料的纤维,可以使用无机类纤维、有机类纤维或者金属类纤维的任一种,例如能够使用玻璃纤维、碳纤维、芳纶纤维、聚乙烯纤维、聚酯纤维、钨纤维、钢纤维、硼纤维等。此外,作为纤维增强塑料的基质,可以使用热固性树脂或者热塑性树脂的任一种,例如能够使用聚酯树脂、环氧树脂、酚醛树脂、乙烯基酯树脂、聚酰亚胺树脂、聚丙烯树脂、尼龙树脂、聚醚醚酮树脂、聚对苯二甲酸丁二醇酯树脂、或者双马来酰亚胺树脂等。
[0074]
芯材层20层叠于各表皮材料31、32。在芯材层20中,厚度彼此相同的多个板状片13作为芯材排列在二维平面上。多个板状片13沿各表皮材料31、32的表面排列。各板状片13为薄的、平板的碎片。各板状片13为相同材质,并且为相同形状、相同大小。另外,在本说明书中,“多个板状片”中的“多个”表示10以上。层叠材料30中的板状片13的片数至少为10片以上。另外,该片数有时为50片以上。
[0075]
板状片13例如由片材材料、薄膜材料或树脂发泡体构成。板状片13能够使用密度比表皮材料31、32更低的材料。板状片13例如能够使用密度为30kg/m3以上2000kg/m3以下的范围的材料。另外,板状片13的密度也可以根据复合材料30的物性或使用目的适当设计从而设为上述范围以外的值。
[0076]
作为板状片13的材料,能够使用树脂(树脂发泡体等)、木质材料(轻木、单板等胶
合板等)、或者金属类发泡体(铝合金等)。在本实施方式中,板状片13由硬质树脂发泡体构成。板状片13例如由聚甲基丙烯酰亚胺(pmi)独立气泡发泡体(例如“rohacell(注册商标)”(赢创工业集团))构成。从复合材料30的轻量化的观点出发,将板状片13的密度设为30kg/m3以上500kg/m3以下的范围的值(例如110kg/m3)。
[0077]
另外,作为用于板状片13的材料的硬质树脂发泡体,可以使用聚苯乙烯发泡体、聚氯乙烯发泡体、醋酸纤维素泡沫发泡体、聚氨酯发泡体、酚醛发泡体、环氧树脂发泡体、丙烯酸发泡体、聚甲基丙烯酰亚胺发泡体、聚丙烯发泡体、聚对苯二甲酸乙二醇酯发泡体、聚碳酸酯发泡体、聚酰胺酰亚胺发泡体、或者聚苯硫醚发泡体等。
[0078]
如图3所示,在芯材层20中,板状片13的俯视形状(外周形状)为正多边形(在本实施方式中为正六边形)。另外,在将多个板状片13均匀地铺满的情况下,板状片13的俯视形状能够选择三角形、四边形、六边形或正五边形。此外,板状片13的俯视形状也可以是除了这些形状以外的形状,还能够选择其他的多边形、圆形或椭圆形等。板状片13的俯视形状在以多边形为基本形状的情况下,也可以在俯视下在各角形成有倒角或倒圆。
[0079]
板状片13的厚度例如能够设为0.05mm以上10mm以下的范围(例如0.05mm以上2mm以下)。此外,关于板状片13的俯视尺寸,从重心到外周的距离的平均值(360度的平均值,在圆形的情况下为半径)能够设为3mm以上50mm以下的范围的值(例如5mm),在板状片13为正六边形的情况下,能够将一边的长度设为3mm以上10mm以下的范围的值(例如5mm)。其中,板状片13的尺寸也可以设为该段落所记载的范围以外的值。
[0080]
在芯材层20中,全部板状片13相互分离而成为单体。各板状片13的整周相对于相邻的全部板状片13隔着间隙16而分离。各板状片13成为相互独立的岛状结构。相邻的板状片13与上述专利文献2的加强结构不同,并未通过与板状片13相同材料的连接部相互连接。复合材料30是各表皮材料31、32作为i型梁结构中的翼缘板而发挥功能、各板状片13作为腹板而发挥功能的多腹板面板,是各板状片13作为芯材而发挥功能的三明治结构的面板。
[0081]
相邻的板状片13的一边彼此存在间隙16而相互对置。间隙16的宽度w根据在后述的上模23中相邻的刀刃24的间隙的大小等而改变。间隙16的宽度w沿相互对置的边为恒定的。此外,在各板状片13中,全部的边所面临的间隙16的宽度w彼此相等。间隙16的宽度w的尺寸根据复合材料30的尺寸等而适当设计,例如能够设为0mm以上、10mm以下的范围。
[0082]
在芯材层20中,能够根据相邻的板状片13之间的间隙16的尺寸,对板状片13的合计面积相对于层叠材料30的俯视下的总面积的比例r1进行调整。比例r1(%)能够以式1表示。
[0083]
式1:r1=(s2/s1)
×
100
[0084]
在此,s1表示芯材层20的总面积(板状片13与间隙16的合计面积),s2表示全部板状片13的合计面积(从厚度方向观察的情况下的面积)。在间隙16中没有任何填充的状态下,从100(%)减去r1后的值与芯材层20的空隙率r2(%)大致相等。比例r1能够设为小于100%、50%以上(根据情况不同为70%以上)。另外,各板状片13的俯视形状为三角形、四边形、六边形或正五边形的情况下,能够高效地填埋芯材层20的空间。在将一边为5mm的正六边形的板状片13以间隙1mm均匀铺满的情况下,比例r1成为80%。此外,在将一边为5mm的正六边形的板状片13以间隙3mm均匀铺满的情况下,比例r1成为55%。
[0085]
在芯材层20中,多个板状片13被有规律地配置。多个板状片13被均匀地铺满。在本
实施方式中,作为板状片13的配置,采用了板状片13的位置在相邻的板状片列13l之间错开半个间距的交错配置。在本实施方式中,各板状片13的俯视形状为正六边形,板状片13的配置也能够称为在相邻的板状片13之间形成有间隙的蜂巢配置。
[0086]
在各板状片13的一个主面(与各板状片13的排列面平行的两面中的一个面,在图2中为下表面)13a的外周,遍及整周形成有倒角部13c。倒角部13c是示出板状片13由冲压加工而成形的情况的痕迹(切割痕),是圆弧状的曲面(例如0.05mm左右的r面)、或者是像圆弧那样向外侧膨出的曲面。倒角部13c的形状根据冲压加工中使用的刀刃24的刀锋形状等而改变。在各板状片13中,倒角部13c的尺寸遍及整周大致均匀。另外,在本说明书中,板状片13的“主面”是指正侧或背侧的面。
[0087]
此外,在多个板状片13(例如芯材层20的全部板状片13)中,作为使用后述的转印片材10而制造的痕迹,通过形成于外周的切割痕判别的厚度方向上的切割朝向彼此相同。具体而言,在多个板状片13中,在厚度方向上为相同侧的主面13a的外周形成有倒角部13c。此外,作为使用了转印片材10的其他痕迹,在层叠于板状片13的主面13a、13b中的、位于切割的推进侧作为厚度方向上的切割朝向的主面13b的表皮材料32中,在内表面(芯材层20侧的面)不存在切割伤43,该切割伤43是假如在表皮材料32上通过切割加工使多个板状片13成形就会形成的。具体而言,在层叠于板状片13的主面13a、13b中的、外周形成有倒角部13c的一侧的相反侧的主面13b的第2表皮材料32中,内表面不存在切割伤43。在由后述的上模23的刀刃24进行切割的情况下,切割伤43成为v型的凹槽。另外,对于不存在该切割伤43这一点,在板状片13的外周面形成有毛刺13d的变形例(参照图25的(b))也同样如此。
[0088]
[转印片材的构成]
[0089]
接着,对复合材料30的制造中使用的转印片材10进行说明。转印片材10是可将多个板状片13从基材片材11向其他结构材料(在表面具有粘合性或粘接性的结构体)转印的片材。
[0090]
如图4所示,转印片材10具备芯材层20和层叠在芯材层20的基材片材11。在基材片材11的芯材层20侧的面残留有将多个板状片13切割时的切割伤(划痕)43。在芯材层20中,相邻的板状片13隔着间隙16而分离。此外,在多个板状片13中,在厚度方向上,各板状片13中的相同侧的主面13a的外周形成有倒角部13c。另外,转印片材10相当于“层叠材料”,基材片材11相当于“表皮材料”。
[0091]
基材片材11例如使用树脂制的片材或薄膜(热塑性树脂片材等)。作为用于基材片材11的树脂,能够使用聚乙烯、聚丙烯、聚氨酯、聚酯、聚对苯二甲酸乙二醇酯(pet)或者聚碳酸酯等各种各样的树脂。在本实施方式中,作为基材片材11的材料,使用了聚对苯二甲酸乙二醇酯(例如日荣化工株式会社制“加工工序用微粘合片材pet75系列”)。基材片材11的厚度能够设为0.01mm~0.5mm的范围的值(例如0.075mm)。另外,除了树脂制以外,基材片材11还能够使用橡胶制或纸制的片材(或者薄膜)。
[0092]
在基材片材11的一面(图4中的上表面)通过涂布粘合剂(压敏粘接剂,在常温下不固化)而形成有粘合剂层18。作为粘合剂,能够使用丙烯酸类、聚氨酯类、或者硅酮类等各种各样的种类。在上述加工工序用微粘合片材pet75系列的基材片材11的情况下,在一面通过丙烯酸类粘合剂的涂布而预先形成有粘合剂层18。但是,在使用未预先形成有粘合剂层18的基材片材11的情况下,通过喷胶等粘合剂形成粘合剂层18。该情况下,能够使用丙烯酸类
粘合剂等喷胶(例如,3m日本株式会社制“喷胶系列”)。另外,基材片材11也可以使用对树脂薄膜贴合两面粘合薄膜而得的片材。
[0093]
多个板状片13可剥离地粘贴于基材片材11的表面。各板状片13通过粘合剂层18而以恒定的粘合力被保持于基材片材11。各板状片13的、在外周形成有倒角部13c的一侧的相反侧被粘贴在基材片材11。另外,在基材片材11的表面具有粘合性的情况下,也可以省略粘合剂层18。
[0094]
基材片材11上的板状片13的排列成为复合材料30的芯材层20中的板状片13的排列的基础。转印片材10的芯材层20的俯视图与图3相同。
[0095]
具体而言,如图3所示,在芯材层20中,板状片13的俯视形状(外周形状)为正多边形(在本实施方式中为正六边形)。在芯材层20中,全部板状片13相互分离而成为单体。各板状片13成为相互独立的岛状结构。
[0096]
相邻的板状片13的一边彼此存在间隙16而相互对置。间隙16的宽度w沿相互对置的边为恒定的。此外,在各板状片13中,全部的边所面临的间隙16的宽度w彼此相等。此外,在芯材层20中,板状片13的合计面积相对于层叠材料30的俯视下的总面积的比例r1为小于100%、50%以上(根据情况不同为70%以上)。另外,间隙16的宽度w可以沿相互对置的边不为恒定的,在各板状片13中,全部的边所面临的间隙16的宽度w可以不彼此相等。
[0097]
在各板状片13的一个主面13a(在图4中为上表面)的外周,遍及整周形成有倒角部13c。在各板状片13中,倒角部13c的尺寸遍及整周大致均匀。
[0098]
[复合材料的制造方法]
[0099]
复合材料30的制造方法依次进行如下工序:第1制造工序,制造转印片材10;第2制造工序,使用通过第1制造工序得到的转印片材10来制造复合材料30。另外,转印片材10相当于中间片材。
[0100]
在第1制造工序中,依次进行如下步骤:粘贴步骤,将材料片材14粘贴于基材片材11;切割步骤,通过对粘贴于基材片材11的状态下的材料片材14进行冲压加工(压切),将材料片材14分割为多个板状片13。材料片材14是成为板状片13的材料的片材,例如能够使用切片加工至0.05mm以上10mm以下的规定厚度的聚甲基丙烯酰亚胺(pmi)独立气泡发泡体的片材。
[0101]
在粘贴步骤中,制成利用粘合剂层18对长条的基材片材11贴合长条的材料片材14而得的层叠片材19(参照图5的(a))。层叠片材19被卷绕成辊状,设置于生产线50的卷盘51(参照图6)。然后,层叠片材19沿长度方向被展开并通过加压装置15。另外,基材片材11及材料片材14的粘贴可以通过可进行加压或加热加压的压力机、辊子、或者超声波变幅杆等进行。
[0102]
在切割步骤中,通过利用上模23的刀刃24垂直切入加压装置15的下模22上的层叠片材19,由此对材料片材14进行压切。此时,如图5的(b)所示,基材片材11不会被切割,而是被所谓的半切(即以不贯通的程度被切割)。在本实施方式中,多个板状片13在基材片材11上成形,制造转印片材10(参照图5的(c))。另外,刀刃24的俯视形状使用与板状片13的外周形状对应的形状。例如,在成形为正六边形的板状片13的情况下,使用在俯视下为正六边形的刀刃24。在上模23中,多个刀刃24隔着间隙排列在二维平面上。
[0103]
在此,如图7的(a)所示,在冲压加工中,材料片材14的表面中、最先接触刀刃24的
前端的部位29被推入。然后,该部位29的周边发生塑性变形。因此,在利用刀刃24将材料片材14切割之后,如图7的(b)所示,作为塑性变形的痕迹,在板状片13的外周形成倒角部13c。倒角部13c如上所述,是圆弧状的曲面或者像圆弧那样向外侧膨出的曲面。此外,在刀刃24之间形成切屑39。另外,在冲压加工中,根据切割条件不同,有时在各板状片13的主面13a的外周形成毛刺13d(参照图25的(b))而不是倒角部13c。但是,不管在形成哪一个的情况下,在板状片13的主面13a的外周都残留有可判别厚度方向上的切割朝向的切割痕。
[0104]
另外,在本实施方式中,在压切时上模23相对于下模22上下移动,但是也可以通过由轮转模具(模切辊)进行的轮转的加压来进行压切。
[0105]
被加压装置15切割的材料片材14的切屑39成为相互连接的网状片材38。由切屑39构成的网状片材38被卷取卷盘25卷取并去除(参照图6)。此外,在转印片材10的板状片13侧层叠有从设置在其他卷盘26的辊展开的保护薄膜27。多个板状片13被保护薄膜27覆盖。此外,在本实施方式中,利用切刀28将长条的转印片材10以规定的长度切割,分割为多个转印片材10。另外,也可以省略卷取卷盘25的卷取、保护薄膜27的覆盖、切刀28的切割。
[0106]
在第2制造工序中,依次进行如下步骤:转印步骤,将转印片材10上的多个板状片13转印至第1表皮材料用片材31a;层叠步骤,将第2表皮材料用片材32a层叠至多个板状片13。各表皮材料用片材31a、32a是上述表皮材料31、32(参照图2)的材料,例如能够使用半固化状态的预浸料(预浸料片材)。
[0107]
在转印步骤中,首先在成形模具(例如模具)33上配置第1表皮材料用片材31a。接着,如图8的(a)所示,将通过第1制造工序得到的转印片材10配置为使板状片13侧朝向成形模具33上的第1表皮材料用片材31a。接着,如图8的(b)所示,对第1表皮材料用片材31a按压转印片材10的多个板状片13。第1表皮材料用片材31a的表面具有粘合性。因此,多个板状片13被粘贴于第1表皮材料用片材31a。然后,如图8的(c)所示,从多个板状片13剥下基材片材11。如此一来,由于第1表皮材料用片材31a相对于多个板状片13的粘合力大于粘合剂层18相对于多个板状片13的粘合力,因此能够将多个板状片13从基材片材11转印至第1表皮材料用片材31a。
[0108]
另外,作为粘合剂层18的粘合剂,也可以使用感温性粘合剂。例如,在将粘合力在规定的转变温度以上降低的热离型粘合剂(例如nitta株式会社制“感温性粘合片材intelimer胶带热离型”例如转变温度50度)用于粘合剂层18的情况下,在图8的(b)所示的状态下将基材片材11从背侧(在图8中为上侧)开始加热,在粘合剂层18为转变温度以上时,剥下基材片材11。另一方面,在将粘合力在规定的转变温度以下降低的冷离型粘合剂(例如nitta株式会社制“感温性粘合片材intelimer胶带冷离型”例如转变温度25度)用于粘合剂层18的情况下,在图8的(b)所示的状态下将基材片材11从背侧开始冷却,在粘合剂层18为转变温度以下时,剥下基材片材11。在使用感温性粘合剂的情况下,能够容易地从板状片13剥下基材片材11。此外,在剥下基材片材11时,对各板状片13与第1表皮材料用片材31a的粘合状态造成的影响也较小。
[0109]
接着,如图9的(a)所示,在层叠步骤中,首先以与通过转印步骤得到的层叠材料30a的板状片13侧对置的方式分开配置第2表皮材料用片材32a。然后,如图9的(b)所示,将第2表皮材料用片材32a层叠于层叠材料30a的板状片13侧。第2表皮材料用片材32a的表面具有粘合性。因此,多个板状片13被粘贴于第2表皮材料用片材32a。如上地,能够得到由一
对表皮材料用片材31a、32a夹着多个板状片13的层叠材料30b。
[0110]
然后,在各表皮材料用片材31a、32a中使用的预浸料的基质为热固性树脂(例如环氧树脂)的情况下,进行成形步骤。在成形步骤中,使用套袋薄膜对通过层叠步骤得到的层叠材料30b进行密闭。然后,将被套袋薄膜密闭的层叠材料30b在高压釜内以规定的温度及压力(例如0.2mpa、130℃)加热规定时间(例如2小时)。通过该加热的过程,半固化状态的表皮材料用片材31a、32a成为完全固化状态的表皮材料31、32。其结果为,成形为规定形状(图9的(b)的情况下为平板状)并固化的复合材料30完成。
[0111]
另外,在各表皮材料用片材31a、32a中使用的预浸料的基质为热塑性树脂(例如聚酰胺树脂、聚丙烯树脂、聚醚醚酮树脂)的情况下,在加压加热压制成形等成形步骤之后,在比基质的固化温度更低的温度(例如室温)的气氛下冷却层叠材料30b,由此进行固化步骤,完成复合材料30。
[0112]
[本实施方式的效果等]
[0113]
在本实施方式的转印片材10中,作为通过在基材片材11上进行冲压加工来使多个板状片13成形的痕迹,在多个板状片13中,通过形成于外周的切割痕判别的厚度方向上的切割朝向彼此相同。具体而言,在多个板状片13中,厚度方向上的相同侧形成有倒角部13c(或毛刺13d)。在转印片材10的基材片材11上,根据冲压加工中的俯视下的切割形状(冲压形状),使多个板状片13成形。
[0114]
此外,在本实施方式的复合材料30中,作为使用转印片材10制造的痕迹,在多个板状片13中,厚度方向上的相同侧形成有倒角部13c。在复合材料30的第1表皮材料31上,与转印片材10中的板状片13的排列对应地配置多个板状片13。因此,无需在表皮材料用片材31a上逐个配置多个板状片13,就能够容易地形成排列了多个板状片13的芯材层20。此外,在专利文献1的图9的情况下,难以致密地配置圆板状板,而根据本实施方式,还容易在表皮材料用片材31a上致密地配置多个板状片13。
[0115]
此外,在本实施方式的复合材料30中,相邻的板状片13隔着间隙16分离而成为单体。在此,在板状片13中使用硬质发泡体的情况下,以往的三明治结构的复合材料通过具备发泡体、蜂巢结构、或者由相互连接的多个材料岛构成的芯材层,实现了轻量且高刚度。然而,以往的复合材料由于芯材层为连续结构,因此若将缺乏韧性的硬质发泡体弯曲则容易发生破损,难以成形为复杂的三维形状。在使复合材料的形状弯曲的情况下,弯曲的范围受到限制。
[0116]
相对于此,在本实施方式中,如图10所示,即使在使用模腔表面弯曲的成形模具33的情况下,相邻的板状片13也由于间隙16而分离,进而相邻的板状片13彼此的干扰被间隙16抑制。因此,与以往的复合材料相比,即使将芯材层20弯曲也难以发生破损,成形为三维形状时弯曲范围的限制较小。根据本实施方式,能够提供对三维形状的成形性优异、并且容易制造的复合材料30。并且,能够实现复杂的三维形状的复合材料30和弯曲较大的复合材料30。
[0117]
另外,在使用图10所示的成形模具33的情况下,可得到沿成形模具33的模腔表面弯曲的三维形状的复合材料30。不仅在成形模具33的模腔表面为图10所示那样的凸面的情况下,在凹面的情况下,也能抑制相邻的板状片13彼此的干扰。此外,在使用模腔表面弯曲的成形模具33的情况下,根据间隙16的宽度w,对成形模具33的追随性发生变化。因此,能够
根据成形模具33的曲率适当设计间隙16的宽度w。
[0118]
此外,在本实施方式的复合材料30中,各表皮材料31、32的材料中使用了预浸料。因此,在进行加热处理时,预浸料的固化性树脂(基质)流入板状片13之间的间隙16,填埋芯材层20的间隙16。流入的固化性树脂在间隙16发生固化。在间隙16固化的树脂中包含与树脂一起从预浸料流入的短纤维。从而,能够抑制复合材料30的局部的强度降低。另外,有时通过预浸料的树脂填埋芯材层20的间隙16,也有时在板状片13的侧面与表皮材料31、32的内表面的角部形成填角料(fillet),或者在包含气泡的状态下填埋间隙16。此外,在间隙16较大的情况下,作为各表皮材料31、32的材料而使用的预浸料能够使用每单位面积的树脂量较多的预浸料。
[0119]
此外,也可以与预浸料的基质分开地利用压力差对板状片13的间隙16注入固化性树脂(例如热固型、两液反应型、以湿气反应型的粘接剂等)。使注入的固化性树脂在间隙16固化。此外,也可以在2片表皮材料31、32之间追加薄膜状粘接剂。在该情况下,在进行加热处理时薄膜状粘接剂熔解,熔解的粘接剂(固化性树脂)流入间隙16,最终固化。在这些情况下,如图11所示,相邻的板状片13之间的间隙16被固化的树脂6填埋,能够抑制复合材料30的局部的强度降低,还能够使刚度提高。另外,这些工序相当于蜂巢形成步骤,在使固化性树脂流入由多个板状片13构成的芯材层20的间隙16之后,通过使该树脂固化而在芯材层20形成树脂6的蜂巢结构。此外,固化性树脂的填充也能够在表皮材料31、32的材料中未使用预浸料的情况下进行。
[0120]
此外,在本实施方式中,由于板状片13的密度较低,因此能够实现轻量且比刚度优异的复合材料30。另外,在本实施方式中,除了板状片13的密度以外,还能够通过对板状片13的厚度以及间隙16的调整,来调整芯材层20的密度。
[0121]
《第1变形例》
[0122]
在本变形例中,如图12所示,复合材料130还具备:第2芯材层21,具有沿第2表皮材料32的表面排列的多个板状片13;中间粘接层17,配置于第1芯材层20与第2芯材层21之间。中间粘接层17由通过加热熔融而直接热固化的片材状粘接剂(也称为薄膜状粘接剂或粘接片材)形成,将第1芯材层20与第2芯材层21粘接。在复合材料130中,将第1表皮材料31、第1芯材层20、中间粘接层17、第2芯材层21、以及第2表皮材料32以该顺序层叠。另外,中间粘接层17也可以由使片材状粘接剂熔解后的粘接剂层构成。此外,也可以在各芯材层20、21的间隙16填埋固化的树脂6。
[0123]
在本变形例中,在俯视下使第1芯材层20的各板状片13的位置与第2芯材层21的各板状片13的位置一致,但也可以使第1芯材层20的各板状片13的位置与第2芯材层21的各板状片13的位置相互错开。
[0124]
此外,在本变形例中,将芯材层20、21设为2层,但也可以将芯材层20、21设为3层以上。在该情况下,也可以在厚度方向上相邻的芯材层20、21之间设置中间粘接层17。
[0125]
此外,也可以在中间粘接层17不使用片材状粘接剂,而是使用预浸料或者热固性树脂片材(环氧树脂等)。在该情况下,也可以通过层叠多片具有基材片材(预浸料)11与粘贴于基材片材11的多个板状片13的叠层结构的层叠材料10,从而制造复合材料130。在该情况下,由于在加热步骤时树脂流动并流入各板状片13的间隙16,因此能够抑制复合材料30的局部的强度降低。另外,由于基材片材11的表面具有粘合性,因此能够省略用于保持板状
片13的粘合剂。
[0126]
在本变形例中,在芯材层20中,板状片13成为2层结构。在此,在对弯曲的复合材料30进行成形的情况下,板状片13的厚度越大,板状片13的一面中的拉伸变形就越大,根据板状片13的厚度和弯曲的大小不同,板状片13的一面有可能因拉伸变形而发生破损。与此相对,在以相同厚度的复合材料进行比较的情况下,本变形例与板状片13为一层结构的复合材料30相比,各板状片13变薄。因此,各板状片13的一面上产生的拉伸变形变小,即使在将低韧性的硬质树脂发泡体用于板状片13的情况下也难以发生破损。根据本变形例,能够提供对三维形状的成形性更加优异的复合材料30。
[0127]
《第2变形例》
[0128]
在本变形例中,不将通过上述第1制造工序制造的中间片材用作转印片材10,而是用作粘接用芯材片材60(参照图13),该粘接用芯材片材60是为了将基材片材111作为粘接剂使用而在层叠于表皮材料用片材31a的状态下使基材片材111熔解而得的。另外,粘接用芯材片材60能够使用与上述转印片材10相同构成的片材。然而,在转印片材10的情况下,将可从基材片材11剥离各板状片13的粘合剂用于粘合剂层18,但在粘接用芯材片材60的情况下,无需将各板状片13设为可剥离,而是能够通过粘合剂或粘接剂将材料片材14粘贴于基材片材111。
[0129]
例如在板状片13为1层的情况下,在制造复合材料30的第2制造工序中,对成形模具33上的第1表皮材料用片材31a依次层叠粘接用芯材片材60以及第2表皮材料用片材32a。在此,关于粘接用芯材片材60的层叠,如图13所示,可以将板状片13侧粘贴于第1表皮材料用片材31a。此外,也可以将基材片材111侧粘贴于第1表皮材料用片材31a(省略图示)。然后,第2表皮材料用片材32a的层叠的结果为,可得到层叠材料30b。由于通过层叠材料30b制造复合材料30的方法与上述实施方式相同,因此省略说明。另外,在填埋于间隙16的树脂量不足的情况下,也可以使树脂片(与中间粘接层17相同性质的片材,例如片材状粘接剂、预浸料等)层叠于芯材层20的一面或两面。
[0130]
另外,也可以在1片复合材料30的制造中使用多片粘接用芯材片材60。在该情况下,也可以以板状片13在厚度方向上朝向相同侧的方式层叠多片粘接用芯材片材60。此外,关于在厚度方向上相邻的粘接用芯材片材60,可以使基材片材111彼此贴合,也可以使芯材层20彼此贴合。
[0131]
《第3变形例》
[0132]
在本变形例中,使用上述转印片材(第1中间片材)10,制造图14所示的粘接用芯材片材(第2中间片材)60。粘接用芯材片材60的表皮材料111为片材状粘接剂。
[0133]
在粘接用芯材片材60的制造方法中,在上述第1制造工序之后依次进行粘贴步骤与转印步骤。在粘贴步骤中,如图15的(a)及图15的(b)所示,在转印片材10中的板状片13侧粘贴表皮材料111。另外,表皮材料111的片材状粘接剂能够使用背面层叠了独立片材141的粘接剂。
[0134]
在转印步骤中,如图15的(c)所示,通过从多个板状片13剥下基材片材11,将多个板状片13转印至表皮材料111。由此,可得到粘接用芯材片材60。另外,也可以在粘接用芯材片材60中的板状片13侧进行层叠保护薄膜27的工序。
[0135]
《第4变形例》
[0136]
在本变形例中,使用上述转印片材(第1中间片材)10,制造图16所示的复合材料制造用片材(第2中间片材)70。复合材料制造用片材70除了表皮材料61是预浸料(半固化状态)这一点外,与图14所示的粘接用芯材片材60相同。表皮材料61的预浸料能够使用在背面层叠了独立片材41的预浸料。另外,由于复合材料制造用片材160的制造方法除了表皮材料不同以外,与第3变形例相同,因此省略说明。
[0137]
《第5变形例》
[0138]
在本变形例中,通过上述第1制造工序制造的中间片材是在基材片材61中使用了预浸料的复合材料制造用片材70。在该情况下,在复合材料30的制造方法中,如图17所示,在成形模具33上设置粘贴了多个板状片13的基材片材61。然后,通过对基材片材61的多个板状片13层叠第2表皮材料用片材32a,制作层叠材料30b(省略图示)。
[0139]
层叠材料30b与上述实施方式同样地,在高压釜内以规定的温度及压力加热规定时间。其结果为,烧成层叠材料30b,完成使基材片材61及第2表皮材料用片材32a完全固化成形而得的规定形状的复合材料30。
[0140]
根据本变形例,无需进行基材片材61的剥离作业,与上述实施方式相比能够以更少的工序数来制造复合材料30。
[0141]
《第6变形例》
[0142]
在本变形例中,如图18所示,在转印片材10中,基材片材11的背面层叠有独立片材41。独立片材41覆盖基材片材11的背面。
[0143]
独立片材41例如能够使用聚丙烯、聚烯烃、聚酯、聚乙烯、聚对苯二甲酸乙二醇酯、聚氨酯、四氟乙烯、聚四氟乙烯、聚苯硫醚、聚酰亚胺、聚醚醚酮、纸等片材材料或薄膜材料。
[0144]
在基材片材11中使用预浸料的情况下,独立片材41利用预浸料的粘合性而可剥离地设置于基材片材11。此外,在基材片材11中使用热塑性树脂片材的情况下也同样地,独立片材41可剥离地设置于基材片材11。
[0145]
在本变形例中,通过设置独立片材41,在转印步骤时,转印片材10的处理变得容易。因此,基材片材11及板状片13的定位变得容易,能够使复合材料30的成形作业变得容易。
[0146]
《第7变形例》
[0147]
在本变形例中,如图19所示,复合材料131为叠层结构。此外,在表皮材料31上的芯材层20中,条状的板状片13沿恒定方向排列。在相邻的板状片13之间形成有间隙16。另外,在图19中,板状片13未沿其长度方向被分割,但也可以将板状片13沿其长度方向进行分割。此外,倒角部13c形成于各板状片13中的表皮材料31侧的主面13a的外周,在图19及图20中省略了记载。
[0148]
复合材料131能够通过卷绕成圆筒状来制造圆筒体100。在复合材料131中以表皮材料31侧作为内侧进行卷绕的情况下,可得到图20所示的圆筒体100。该情况下,表皮材料31的两个端部31a未层叠有芯材层20,一方的端部31a成为内周面上的粘条(粘贴至一个外侧的表皮材料31的粘贴部位),另一方的端部13a以覆盖最外侧的板状片13的方式层叠。此外,在复合材料131中以表皮材料31侧作为外侧进行卷绕的情况下,可得到圆筒体100。在该情况下,一方的端部31a以覆盖最内侧的板状片13的方式层叠,另一方的端部13a成为外周面上的粘条(粘贴至一个内侧的表皮材料31的粘贴部位)。在最内侧,表皮材料31的端部31a
以覆盖多个板状片13的方式层叠。
[0149]
《第8变形例》
[0150]
在本变形例中,在芯材层20的各板状片13形成有由贯通孔构成的划分空间53。划分空间53在俯视下是划分了周围的空间。另外,一个板状片13中的划分空间53的数量可以是1个,也可以是多个。此外,可以在复合材料30中的全部板状片13形成划分空间53,也可以仅在一部分板状片13形成划分空间53。
[0151]
板状片13的外周形状与上述实施方式同样地,为正多边形(在图21的(a)中为正六边形)。但是,板状片13的俯视形状也可以是正多边形以外的形状(例如,正多边形以外的多边形、圆形、椭圆形等)。此外,划分空间53的俯视形状与板状片13的外周形状相同。但是,划分空间53的俯视形状也可以与板状片13的外周形状不同。
[0152]
划分空间53能够在第1制造工序的切割步骤中,将材料片材14分割为多个板状片13的压切时形成。该情况下,在用于压切的上模23中,在与板状片13的俯视形状对应的刀刃24的内侧,设有与划分空间53的俯视形状对应的刀刃(省略图示)。在复合材料30中,如图21的(b)所示,在厚度方向上与倒角部13c(或毛刺13d)相同的一侧,作为示出通过冲压加工形成划分空间53的情况的痕迹(切割痕),形成有内侧倒角部13e(或内侧毛刺)。在图21的(a)中,省略了倒角部13c及内侧倒角部13e的记载。另外,也可以在材料片材14中形成了划分空间53之后,将材料片材14粘贴于基材片材11,通过与划分空间53的位置匹配的压切,将材料片材14分割为多个板状片13。
[0153]
在复合材料30中,如图21的(b)所示,芯材层20的间隙16被固化的树脂6填埋。树脂6是利用压力差向间隙16注入固化性树脂(例如热固型、两液反应型、以湿气反应型的粘接剂等)并使其固化而得的树脂。固化性树脂例如能够使用rtm(resin transfer molding:树脂传递模塑)成形法注入。该情况下,例如夹着芯材层20的表皮材料用片材31a、32a能够使用不含有树脂的纤维织物(碳纤维或玻璃纤维的织物、或者碳纤维或玻璃纤维无纺布等)、树脂板或者金属板等,在各表皮材料用片材31a、32a与芯材层20之间,能够层叠使用了使固化性树脂无法通过的原材料的树脂片材54。
[0154]
树脂片材54能够使用形成了多个贯通孔54a的开孔片材54a、或者没有贯通孔54a的无孔片材54b。如图21的(b)所示,可以将一方设为开孔片材54a,另一方设为无孔片材54b,也可以将双方均设为开孔片材54a,也可以将双方均设为无孔片材54b。在使用开孔片材54a的情况下,通过使树脂片材54的贯通孔54a的至少一部分与间隙16重叠,从而变得容易将低流动性的固化性树脂填充至间隙16。此外,可以使树脂片材54的至少一部分贯通孔54a与划分空间53重叠,在该情况下,对与贯通孔54a重叠的划分空间53注入固化性树脂,而对除此以外的划分空间53不注入固化性树脂。此外,在树脂片材54的任一贯通孔54a均不与划分空间53重叠的情况下,或者双方均使用无孔片材54b的情况下,不对任一划分空间53注入固化性树脂。在任一情况下,均能控制是否对划分空间53流入固化性树脂。因此,能够根据划分空间53的大小,进行对芯材层20中的空隙率的调节。另外,也可以不对间隙16进行上述固化性树脂的注入。即使在该情况下,通过在各板状片13设置划分空间53,各板状片13也变得容易追随三维形状。
[0155]
《第9变形例》
[0156]
本变形例在板状片13中形成有划分空间53这一点上与第8变形例相同,但如图22
所示,在板状片13形成有蜂巢结构的划分空间53。一个板状片13中的划分空间53的数量可以是1个,也可以是多个。另外,在图22中,虚线表示切割部位(后述的压切的位置)。切割部位相对于一个板状片13的俯视形状为多边形(六边形)。但是,该切割部位的俯视形状也可以是多边形以外的形状。
[0157]
在芯材层20的制造中,在上述第1制造工序中,在将蜂巢结构的材料片材14粘贴至基材片材11之后,通过对粘贴于基材片材11的状态下的材料片材14进行冲压加工(压切),使材料片材14被分割为多个板状片13。然后,根据需要进行切屑的去除,可得到芯材层20。另外,作为材料片材14,能够使用以堵塞蜂巢结构的各贯通孔的方式在蜂巢结构的层的两面将薄膜一体化的片材,也能够使用仅由蜂巢结构的层构成的片材。
[0158]
在图2等的复合材料30、图4等的转印片材10、图13等的粘接用芯材片材60、以及图16等的复合材料制造用片材70等上述全部的实施方式及变形例的层叠材料中,能够使用第8变形例及第9变形例的芯材层20来代替没有划分空间53的芯材层20。对于使各板状片13变得容易追随三维形状这样的技术问题,在层叠材料为转印片材10等中间片材的情况下,层叠材料10具备芯材层20与层叠于芯材层20的表皮材料11,芯材层20具有沿表皮材料11的表面排列的多个板状片13,在芯材层20中,相邻的板状片13隔着间隙或通过切口而成为单体,在板状片13中,形成有划分空间53。此外,在层叠材料为三明治结构的面板等复合材料30的情况下,层叠材料30以表皮材料11作为第1表皮材料,进一步具备第2表皮材料12,配置在芯材层20中的第1表皮材料11的相反侧,与第1表皮材料11一起夹着芯材层20。此外,对于实现能够对芯材层20中的空隙率进行调节的层叠材料这样的技术问题,在层叠材料10、30中,各表皮材料用片材31a、32a与芯材层20之间层叠有使固化性树脂无法通过的树脂片材54。
[0159]
《第10变形例》
[0160]
在本变形例中,在芯材层20的板状片13的主面13a、13b层叠有用于保持板状片13的平面位置的保持部80。保持部80是局部形成了间隙的粘合层或粘接层。
[0161]
在图23中,粘合层80由分别由粘合剂薄膜构成的多个点部80a构成。在粘合层80中,例如,多个点部80a有规律地排列。粘合层80层叠在板状片13的主面13a及主面13b的至少一方。在图23的(a)的转印片材10以及图23的(b)的复合材料30中,粘合层80层叠在板状片13的主面13a及主面13b双方。但是,粘合层80也可以仅层叠在板状片13的主面13a,也可以仅层叠在板状片13的主面13b。根据本变形例,在利用压力差对间隙16注入固化性树脂时,能够抑制板状片13的位置偏离,也能够在复合材料30的完成品中抑制板状片13的位置偏离。
[0162]
将粘合层80设置于板状片13的方法例如可考虑在第1制造工序之前进行的准备工序中,在成为芯材层20的材料的材料片材14的一面或两面印刷多个点部80a。该情况下,在第1制造工序中,将印刷了多个点部80a的材料片材14粘贴于基材片材11,之后,通过冲压加工将材料片材14分割为多个板状片13。
[0163]
此外,作为其他方法,能够使用印刷了多个点部80a的粘合层形成用的转印片材85(参照图23的(c))。该情况下,转印片材85之中印刷有多个点部80a的基材片材86例如能够使用对pet薄膜进行了硅酮处理的树脂片材等易剥离性的片材。点部80a对板状片13的粘合力大于点部80a对基材片材86的粘合力。在该方法中,在第1制造工序中的切割步骤之后,将转印片材85的点部80a侧设为相对于板状片13的主面13a重叠的状态(图23的(c)所示的状
态)。然后,通过剥下基材片材86,能够在板状片13的主面13a转印多个点部80a。另外,在上述准备工序中,也可以不对材料片材14印刷多个点部80a而是使用转印片材85在板状片13的主面13a、13b转印多个点部80a。
[0164]
另外,点部80a也可以不由粘合剂构成,而是由粘接剂薄膜构成。该情况下,固定于各板状片13的点部80a起到作为锚的作用,从而能够抑制板状片13的位置偏离。
[0165]
此外,也可以代替于多个点部80a而如图24所示地,对板状片13的主面13a、13b层叠在厚度方向上形成了多个间隙的粘合片材(或粘接片材)87。粘合片材87能够使用将粘合剂用于材料的网眼片材、或者将粘合剂的纤维交织的无纺布等。粘接片材87能够使用将粘接剂用于材料的网眼片材、或者将粘接剂的纤维交织的无纺布等。在这些情况下,也能够抑制板状片13的位置偏离。
[0166]
本变形例的保持部80能够应用于图2等的复合材料30、图4等的转印片材10、图13等的粘接用芯材片材60、以及图16等的复合材料制造用片材70等上述全部的实施方式及变形例的层叠材料。对于实现能够抑制板状片13的位置偏离的层叠材料这样的技术问题,在层叠材料为转印片材10等中间片材的情况下,层叠材料10具备芯材层20与层叠于芯材层20的表皮材料11,芯材层20具有沿表皮材料11的表面排列的多个板状片13,在芯材层20中,相邻的板状片13隔着间隙或通过切口而成为单体,在表皮材料11与板状片13之间,层叠有用于保持板状片13的平面位置的保持部80。此外,在层叠材料为三明治结构的面板等复合材料30的情况下,层叠材料30以表皮材料11作为第1表皮材料,进一步具备第2表皮材料12,配置在芯材层20中的第1表皮材料11的相反侧,与第1表皮材料11一起夹着芯材层20,在表皮材料11、12与板状片13之间层叠有保持部80。
[0167]
《第11变形例》
[0168]
在本变形例中,转印片材10的基材片材11使用了具有伸缩性的片材材料。基材片材11能够使用例如cpp薄膜(未拉伸聚丙烯)等树脂片材。作为基材片材11的物性值的一例,例如,拉伸强度为100mpa(jis k 7127)以下,拉伸伸长率为200%(jis k 7127)以上。
[0169]
在本变形例中,在进行板状片13的转印的转印步骤中,由作业者或机械以图25所示的箭头的方向拉伸基材片材11的同时,通过利用棒状等的部件或作业者的手指等按压物55从基材片材11的背面按压转印对象的板状片13,向表皮材料用片材31a进行板状片13的转印。根据本变形例,由于通过拉伸基材片材11,转印对象的板状片13与基材片材11之间的粘合力降低,因此板状片13的转印变得容易。例如,在向载置于凸状的曲面上的表皮材料用片材31a进行转印时,由于板状片13相对于表皮材料用片材31a的密合面积变少,因此板状片13的转印变得容易。
[0170]
《另一变形例》
[0171]
在上述实施方式中,也可以不通过压切,而是通过激光切割来切割材料片材14从而分割为多个板状片13。该情况下,如图26的(a)所示,在中间片材10中,作为可判别厚度方向上的切割朝向的切割痕,在各板状片13的主面13a的外周形成毛刺13d。此外,如图26的(b)所示,复合材料30中也在各板状片13的主面13a的外周残留毛刺13d。另外,在进行激光切割的情况下,有时也在各板状片13的主面13a的外周形成倒角部13c作为上述切割痕。此外,通过调整激光切割时的激光的焦点、输出、或者进给速度等,能够控制切割面的状态。
[0172]
在上述实施方式中,也可以不进行压切或激光切割,而是使用沿着要切割的形状
移动刀刃的切割装置(cutting plotter:切绘机)来切割材料片材14从而分割为多个板状片13。该情况下,作为可判别厚度方向上的切割朝向的切割痕,在各板状片13的主面13a的外周形成倒角部13c或毛刺13d。
[0173]
在上述实施方式中,在芯材层20中,相邻的板状片13隔着间隙16而成为单体,但相邻的板状片13也可以通过切口40而成为单体。该情况下,如图27的(a)及图27的(b)所示,相邻的板状片13被相同的刀刃24切割。例如,在成形为正六边形的板状片13的情况下,使用正六边形的排列图案的刀刃24。然后,如图27的(c)所示,在拔出刀刃24时,在图27的(b)的状态下发生了弹性形变的板状片13复原,相邻的板状片13之间残留切口40。
[0174]
在上述实施方式中,作为表皮材料31、32的材料,可以使用金属类的材料。该情况下,各板状片13通过粘接剂与表皮材料31、32接合。作为该粘接剂,例如能够使用乙烯缩醛/酚醛树脂类粘接剂、丁腈橡胶/酚醛树脂类粘接剂、氯丁橡胶/酚醛树脂类粘接剂、环氧树脂类粘接剂、再生橡胶类粘接剂、聚苯并咪唑类(pbi)粘接剂、聚酰亚胺类(pi)粘接剂等。另外,从粘接作业的高效化(粘接剂的涂布量的稳定性与作业性)的观点看来,也可以使用片材状粘接剂(薄膜状粘接剂)。成为该片材状粘接剂的基底的树脂例如为环氧树脂、尼龙/环氧树脂、腈/环氧树脂、丙烯酸/环氧树脂、乙烯基/环氧树脂、改性环氧树脂、环氧树脂/酚醛树脂、聚酰亚胺、尼龙、或者改性聚丙烯等。
[0175]
在上述实施方式中,在将复合材料30例如用于船体面板那样的巨大结构物的情况下,各板状片13的尺寸变大,相邻的板状片13的间隙16的宽度w也变大。例如,板状片13的外形形状为长轴尺寸100mm的变形圆的情况下,间隙16的宽度w可以设为10mm以上。
[0176]
在上述实施方式中,芯材层20中的全部板状片13的形状可以不相同。例如,可以根据复合材料30中的部位的曲率,决定该部位的板状片13的俯视形状。
[0177]
在上述实施方式中,图2所示的复合材料30可以省略第2表皮材料32从而设为叠层结构。该情况下,将复合材料30的板状片13侧相对于加强对象的结构材料粘贴。芯材层20被第1表皮材料31与加强对象的结构材料夹住。
[0178]
在上述实施方式中,芯材层20由沿表皮材料11、12的表面排列的多个板状片13构成,但在转印片材10、粘接用芯材片材60、以及复合材料制造用片材70等中间片材中,芯材层20也可以由形成了多个贯通孔的片材材料(例如蜂巢结构的片材材料)构成。
[0179]
[实施例]
[0180]
对图1及图2所示的结构的复合材料30的实施例进行说明。另外,本发明只要不超过其主旨,则并不限定于本实施例。此外,只要没有特别记载,本实施例中记载的单位和测量方法依据jis标准。
[0181]
板状片13的材料使用了商品名“rohacell(注册商标)”(赢创工业集团)作为聚甲基丙烯酰亚胺(pmi)独立气泡发泡体。板状片13的密度为110kg/m3。此外,板状片13的俯视形状为,以正六边形为基本形状,六个角分别被倒角的形状。关于板状片13的尺寸,厚度为1.0mm,正六边形的一边的长度为5mm,上述各角的倒角的半径为0.5mm。此外,相邻的板状片13间的间隙16的宽度w为1mm。多个板状片13以上述蜂巢排列均匀地配置。另外,作为冲压加工的切割痕,在板状片13的主面(一面)13a的外周形成有半径0.05mm左右的倒角部13c。在俯视下,板状片13相对于总面积的面积比例r1为80.3%(反映了各角的倒角带来的面积减少的计算值)。
[0182]
表皮材料31、32的材料使用了商品名“pyrofil prepreg(注册商标)tr3110 381gmx”(三菱化学株式会社制)作为预浸料。该预浸料的规格为总单位面积重量333g/m2、拉伸弹性模量240gpa的碳纤维的平纹布材料,基质为热固环氧树脂。
[0183]
在加热步骤中,以0.2mpa、130℃将层叠材料30b加热了2小时。其结果为,成形为厚度1.49mm、密度503kg/m3的复合材料30。
[0184]
为了对该复合材料30进行物性评价,基于jis标准k7074(碳纤维增强塑料的弯曲试验方法)进行了弯曲试验。其结果为,弯曲弹性模量为18.9gpa,密度为503kg/m3,单位密度的弹性模量成为非常高的值。根据实施例,能够确认到可得到轻量且高刚度的复合材料30。
[0185]
工业实用性
[0186]
本发明可应用于具有芯材层的复合材料等。
[0187]
附图标记说明
[0188]
10 转印片材(层叠材料、中间片材)
[0189]
11 基材片材(表皮材料)
[0190]
13 板状片
[0191]
13a、13b 主面
[0192]
13c 倒角部
[0193]
13d 毛刺
[0194]
16 间隙
[0195]
18 粘合剂层
[0196]
20 芯材层
[0197]
30 复合材料(层叠材料)
[0198]
31、32 表皮材料
[0199]
40 切口
[0200]
60 粘接用芯材片材(层叠材料、中间片材)
[0201]
70 复合材料制造用片材(层叠材料、中间片材)。