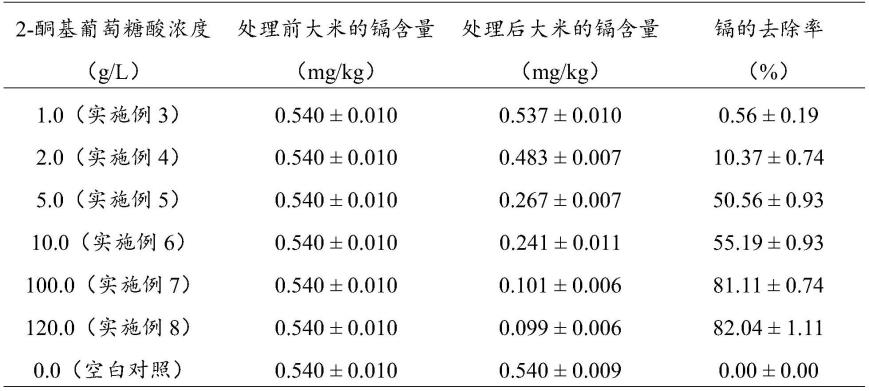
1.本发明涉及污染粮食安全利用技术领域,具体涉及一种镉污染大米的降镉处理方法。
背景技术:2.镉是一种蓄积性的具有很长生物半衰期(在人体中为10~30年)的强毒性的重金属元素,能够通过植物的吸收(或吸附)、富集进入食物链,进而导致镉在人体内的积累,并在积累至一定浓度时引起机体的急慢性中毒,造成肾脏、骨骼、消化等系统的损伤甚至发生畸变和癌变。
3.水稻是我国的大宗粮食作物之一,近年来的产量保持在2.0亿吨/年左右。水稻对土壤环境中的镉具有很强的富集能力,能够通过根系吸收环境中的镉并经镉结合转运蛋白运输至稻谷的籽粒中,从而导致所加工的大米镉含量超出国家规定的限量(≤0.2mg/kg)。21世纪以来,随着工业化和城镇化进程的加快,我国耕地土壤的重金属污染特别是镉的污染状况愈加严重。
4.鉴于镉对人体健康的危害,镉超标大米被严禁流入口粮市场,且其在工业方面的综合利用也受到了诸多的限制。因此,有关镉污染大米的降镉处理技术的研究与应用备受关注。目前文献已报道的镉污染大米的降镉处理方法大致可分为4类,即物理法、化学法、生物法和复合法。其中,化学法是一类通过溶剂(特别是酸碱溶液)的浸提作用将大米中与蛋白结合的镉(络合态的镉)迁移至溶液中的方法,相对来说是一类更适合于对高超标的镉污染大米进行规模化降镉处理的方法。该法能够有效降低镉污染大米中的镉含量,同时也能够保持大米营养物质的相对稳定性及大米外形的完整性。有关利用2-酮基葡萄糖酸处理镉超标大米的研究尚未见到文献报道。同时,化学溶剂的回收以及处理过程产生的二次污染问题,在一定程度上限制了化学法在大米降镉处理中的应用。
技术实现要素:5.本发明的目的在于提供一种镉污染大米的降镉处理方法,本发明利用2-酮基葡萄糖酸处理镉超标大米,可有效降低大米中的镉含量。同时,本发明对2-酮基葡萄糖酸处理废液进行酸化、过滤处理可得到澄清2-酮基葡萄糖酸溶液,解决了化学溶剂回收处理难题。
6.本发明提供了一种镉污染大米的降镉处理方法,将镉污染大米在2-酮基葡萄糖酸溶液中浸提处理,并回收2-酮基葡萄糖酸处理废液。
7.本发明中,所述2-酮基葡萄糖酸溶液的质量浓度为5~120g/l。
8.本发明中,所述浸提时伴随振摇,所述浸提处理的时间为3~8h。
9.本发明中,所述2-酮基葡萄糖酸处理废液的回收方法包括如下步骤:将2-酮基葡萄糖酸处理废液与2-酮基葡萄糖酸发酵液混合,调节ph至1.25~1.35,加入活性炭、黄血盐和硫酸锌反应,抽滤除去固形物得到澄清的2-酮基葡萄糖酸溶液。
10.本发明中,使用所述得到的澄清2-酮基葡萄糖酸溶液对镉污染大米进行降镉处
理。
11.本发明中,所述活性炭的用量为2-酮基葡萄糖酸处理废液与2-酮基葡萄糖酸发酵液混合总体积的0.05~0.15%。
12.本发明中,所述活性炭、黄血盐和硫酸锌质量比为1:1~3:0.5~1。
13.本发明中,所述反应条件为于55~65℃保温反应15~30min。
14.本发明中,所述固形物经去离子水洗涤后再经400~650℃灼烧处理。
15.本发明中,所述2-酮基葡萄糖酸发酵液由变形假单胞菌发酵得到。
16.与现有技术相比,本发明具有如下技术效果:
17.(1)本发明利用2-酮基葡萄糖酸溶液浸提镉超标大米中的镉,能够高效地将大米中的镉转移至2-酮基葡萄糖酸溶液中,有效降低大米中的镉含量,镉的去除率可达到80%以上。
18.(2)本发明将2-酮基葡萄糖酸处理废液与2-酮基葡萄糖酸发酵液混合,经简单的酸化、过滤处理,可以得到澄清的2-酮基葡萄糖酸溶液,该溶液中镉含量在2.00μg/l以下。
19.(3)本发明在回收2-酮基葡萄糖酸处理废液过程中,对酸化过程中产生的废渣进行灼烧处理,可以得到符合建材生产要求的无水硫酸钙,解决了化学溶剂处理过程中产生二次污染的问题。
具体实施方式
20.本发明提供了一种镉污染大米的降镉处理方法,将镉污染大米在2-酮基葡萄糖酸溶液中浸提处理,并回收2-酮基葡萄糖酸处理废液。2-酮基葡萄糖酸是一种由葡萄糖氧化生产的具有光学活性的有机酸,是手性化合物和杂环化合物的构建单元,其目前最为重要的用途是作为食品抗氧化剂d-异抗坏血酸及其盐类合成的前体。本发明利用2-酮基葡萄糖酸溶液浸提镉超标大米中的镉,能够高效地将大米中的镉转移至2-酮基葡萄糖酸溶液中。
21.在本发明中,所述2-酮基葡萄糖酸溶液的质量浓度为5~120g/l。优选地,所述2-酮基葡萄糖酸溶液的质量浓度为10~100g/l。
22.在本发明中,所述浸提时伴随振摇,所述浸提处理的时间为3~8h。优选地,所述浸提处理的时间为4~6h。在本发明的具体实施例中,所述浸提处理在室温下进行。
23.在本发明中,所述2-酮基葡萄糖酸处理废液的回收方法包括如下步骤:将2-酮基葡萄糖酸处理废液与2-酮基葡萄糖酸发酵液混合,调节ph至1.25~1.35,加入活性炭、黄血盐和硫酸锌反应,抽滤除去固形物得到澄清的2-酮基葡萄糖酸溶液。在本发明中,添加活性炭可吸附2-酮基葡萄糖酸处理废液中的大分子杂质,同时起到去色作用;在适度酸性条件下,添加黄血盐和硫酸锌后可使2-酮基葡萄糖酸发酵液中的菌体迅速凝成直径几十到几百微米不等的颗粒,这种现象称为聚凝反应,聚凝反应发生的原因是锌离子吸附在带负电的菌体表面,形成双电层,然后黄血盐与菌体表面锌离子和溶液中游离的锌离子反应形成复盐大分子,其方程式为2k4fe(cn)6+3znso4=k2zn3[fe(cn)6]2+3k2so4,菌体之间通过复盐的架桥作用紧密交联成团,形成结实的聚凝体,正是由于这种聚凝反应的发生,可将2-酮基葡萄糖酸处理废液中的镉以及大部分杂质吸附形成聚凝体,通过过滤即能够获得澄清的2-酮基葡萄糖酸溶液。
[0024]
在本发明中,使用所述得到的澄清2-酮基葡萄糖酸溶液可重复对镉污染大米进行
降镉处理。在本发明中,所述得到的澄清2-酮基葡萄糖酸溶液中镉含量≤2.00μg/l。
[0025]
在本发明中,所述活性炭的用量为2-酮基葡萄糖酸处理废液与2-酮基葡萄糖酸发酵液混合总体积的0.05~0.15%。优选地,所述活性炭用量为2-酮基葡萄糖酸处理废液与2-酮基葡萄糖酸发酵液混合总体积的0.06~0.1%。
[0026]
在本发明中,所述活性炭、黄血盐和硫酸锌质量比为1:1~3:0.5~1。在本发明中,选择合适的黄血盐与硫酸锌配比和用量,可使菌体完全聚凝,从而达到理想的去镉效果。
[0027]
在本发明中,所述反应条件为于55~65℃保温反应15~30min。优选地,所述反应条件为于58~60℃保温反应20~25min。在本发明的研究中发现,温度过低,液体粘度大,反应时间明显延长;温度过高反应过快,会消耗大量能量。因此,适宜的反应温度利于聚凝反应的发生。
[0028]
在本发明中,所述固形物经去离子水洗涤后再经400~650℃灼烧处理。优选地,所述固形物经去离子水洗涤后再经450~600℃灼烧处理。在本发明中,所述固形物主要由硫酸钙和菌体组成,经灼烧处理后,可以得到符合建材生产要求的无水硫酸钙。
[0029]
在本发明中,所述2-酮基葡萄糖酸发酵液由变形假单胞菌发酵得到。在本发明的具体实施例中,所述变形假单胞菌(pseudomonasplecoglossicida)的编号为jsu01,保藏于中国微生物菌种保藏管理委员会普通微生物中心,具体地址为北京市朝阳区北辰西路1号院3号中国科学院微生物研究所,保藏时间为2013年1月18日,保藏编号为cgmcc no.7150。
[0030]
在本发明的具体实施例中,所述发酵方法包括如下步骤:将变形假单胞菌接入种子培养基培养得种子液,将所述种子液接入发酵培养基培养60~80h即得2-酮基葡萄糖酸发酵液。优选地,所述种子液接入发酵培养基培养64~72h。在本发明的具体实施例中,所述种子培养基由下述原料制备得到:结晶葡萄糖20.0g/l,玉米浆干粉5.0g/l,尿素2.0g/l,kh2po42.0 g/l,mgso4·
7h2o 0.5g/l,轻质caco31.0 g/l,调整ph 7.0;在本发明的具体实施例中,所述发酵培养基由下述原料制备得到:结晶葡萄糖180.0g/l,玉米浆干粉10.0g/l,轻质caco345.0 g/l,调整ph 6.7。在本发明中,所述种子培养基与发酵培养基中轻质caco3中含有微量的镉,镉含量为0.275mg/kg。在本发明中,制备得到的2-酮基葡萄糖酸发酵液中含有微量的镉,镉的含量为12.40μg/l。本发明对所述原料来源不作特殊限定。
[0031]
下面将结合本发明中的实施例,对本发明中的技术方案进行清楚、完整地描述。显然,所描述的实施例仅仅是本发明一部分实施例,而不是全部的实施例。基于本发明中的实施例,本领域普通技术人员在没有做出创造性劳动前提下所获得的所有其他实施例,都属于本发明保护的范围。
[0032]
实施例1
[0033]
生产含有2-酮基葡萄糖酸的发酵液:
[0034]
将变形假单胞菌jsu01菌株接入装有50ml种子培养基的500ml锥形瓶中,在30℃、265r/min(偏心距25mm)的条件下振荡培养18h,得到种子液od
650nm
=14.03,ph=7.12。
[0035]
将4ml的种子液接入装有40ml发酵培养基的500ml的锥形瓶中,在30℃、265r/min(偏心距25mm)的条件下振荡培养72h,此时发酵液中的葡萄糖被完全消耗,发酵液od
650nm
=7.04,发酵液中2-酮基葡萄糖酸(以钙盐的形式存在)的质量浓度为160.00g/l。
[0036]
其中,种子培养基由下述原料制备得到:结晶葡萄糖20.0g/l,玉米浆干粉5.0g/l,尿素2.0g/l,kh2po42.0 g/l,mgso4·
7h2o 0.5g/l,轻质caco31.0 g/l;调整ph 7.0;
[0037]
发酵培养基由下述原料制备得到:结晶葡萄糖180.0g/l,玉米浆干粉10.0g/l,轻质caco345.0 g/l;调整ph 6.7。
[0038]
实施例2
[0039]
制备2-酮基葡萄糖酸溶液:
[0040]
取1000ml的2-酮基葡萄糖酸质量浓度为160.00g/l的发酵液,用浓硫酸调节其ph至1.30,再加入1.0g的活性炭、1.3g的黄血盐和0.9g的硫酸锌,搅拌下60℃保温反应20min;降温至25℃左右,抽滤除去固形物,并用100ml的无离子水洗剂固形物,得到1050ml澄清的质量浓度为146.28g/l的2-酮基葡萄糖酸溶液。
[0041]
实施例3
[0042]
镉污染大米的降镉处理方法包括如下步骤:
[0043]
准确称取50.0g的镉污染大米(镉含量0.540mg/kg)样品6份,加入质量浓度为1.0g/l的100ml的2-酮基葡萄糖酸溶液中,室温下振摇浸提4h。浸提结束后,过滤收集经降镉处理的大米并用适量的蒸馏水洗涤3次,每次洗水50ml。烘干经降镉处理的大米,然后取样测定其镉含量。
[0044]
实施例4
[0045]
与实施例3不同的是,2-酮基葡萄糖酸溶液的质量浓度为2.0g/l,其与步骤与实施例3相同。
[0046]
实施例5
[0047]
与实施例3不同的是,2-酮基葡萄糖酸溶液的质量浓度为5.0g/l,其与步骤与实施例3相同。
[0048]
实施例6
[0049]
与实施例3不同的是,2-酮基葡萄糖酸溶液的质量浓度为10.0g/l,其与步骤与实施例3相同。
[0050]
实施例7
[0051]
与实施例3不同的是,2-酮基葡萄糖酸溶液的质量浓度为100.0g/l,其与步骤与实施例3相同。
[0052]
实施例8
[0053]
与实施例3不同的是,2-酮基葡萄糖酸溶液的质量浓度为120.0g/l,其与步骤与实施例3相同。
[0054]
以不使用2-酮基葡萄糖酸溶液浸提处理的大米作为空白对照。
[0055]
表1 2-酮基葡萄糖酸的浓度对镉污染大米降镉处理效果的影响
[0056][0057]
根据表1的测定结果显示:当2-酮基葡萄糖酸溶液的质量浓度达到5.0g/l时,镉的去除率即可达到50%以上;当2-酮基葡萄糖酸溶液的质量浓度达到100.0g/l及以上时,镉的去除率可达到80%以上。
[0058]
实施例9
[0059]
2-酮基葡萄糖酸废液的回收:
[0060]
取100ml含有100.0g/l的2-酮基葡萄糖酸废液(镉含量210.00μg/l,ph 1.26),与200ml的2-酮基葡萄糖酸质量浓度为160.00g/l的发酵液(镉含量12.40μg/l)混合,用浓硫酸调节其ph至1.30,再加入0.3g的活性炭、0.3g的黄血盐和0.2g的硫酸锌,搅拌下60℃保温反应20min;降温至25℃左右,抽滤除去固形物,并用30ml的无离子水洗剂固形物,得到320ml澄清的质量浓度为128.84g/l的2-酮基葡萄糖酸溶液(镉含量1.91μg/l)。该处理过程产生的酸化废渣折干总量为16.61g,其镉含量为1.40mg/kg。酸化废渣经450℃灼烧处理10min后,得到了12.26g的无水硫酸钙。
[0061]
实施例10
[0062]
与实施例1不同的是:将4ml的种子液接入装有40ml发酵培养基的500ml的锥形瓶中,在30℃、265r/min(偏心距25mm)的条件下振荡培养60h,其他步骤与实施例1相同。
[0063]
实施例11
[0064]
与实施例1不同的是:将4ml的种子液接入装有40ml发酵培养基的500ml的锥形瓶中,在30℃、265r/min(偏心距25mm)的条件下振荡培养80h,其他步骤与实施例1相同。
[0065]
实施例12
[0066]
与实施例3不同的是:室温下振摇浸提3h,其他步骤与实施例3相同。
[0067]
实施例13
[0068]
与实施例3不同的是:室温下振摇浸提8h,其他步骤与实施例3相同。
[0069]
实施例14
[0070]
与实施例8不同的是:用浓硫酸调节其ph至1.25,再加入0.15g的活性炭、0.5g的黄血盐和0.25g的硫酸锌,搅拌下55℃保温反应15min,其他步骤与实施例8相同。
[0071]
实施例15
[0072]
与实施例8不同的是:用浓硫酸调节其ph至1.35,再加入0.45g的活性炭、0.9g的黄血盐和0.3g的硫酸锌,搅拌下65℃保温反应30min,其他步骤与实施例8相同。
[0073]
实施例16
[0074]
与实施例8不同的是:酸化废渣经400℃灼烧处理,其他步骤与实施例8相同。
[0075]
实施例17
[0076]
与实施例8不同的是:酸化废渣经650℃灼烧处理,其他步骤与实施例8相同。
[0077]
以上所述仅是本发明的优选实施方式,应当指出,对于本技术领域的普通技术人员来说,在不脱离本发明原理的前提下,还可以做出若干改进和润饰,这些改进和润饰也应视为本发明的保护范围。