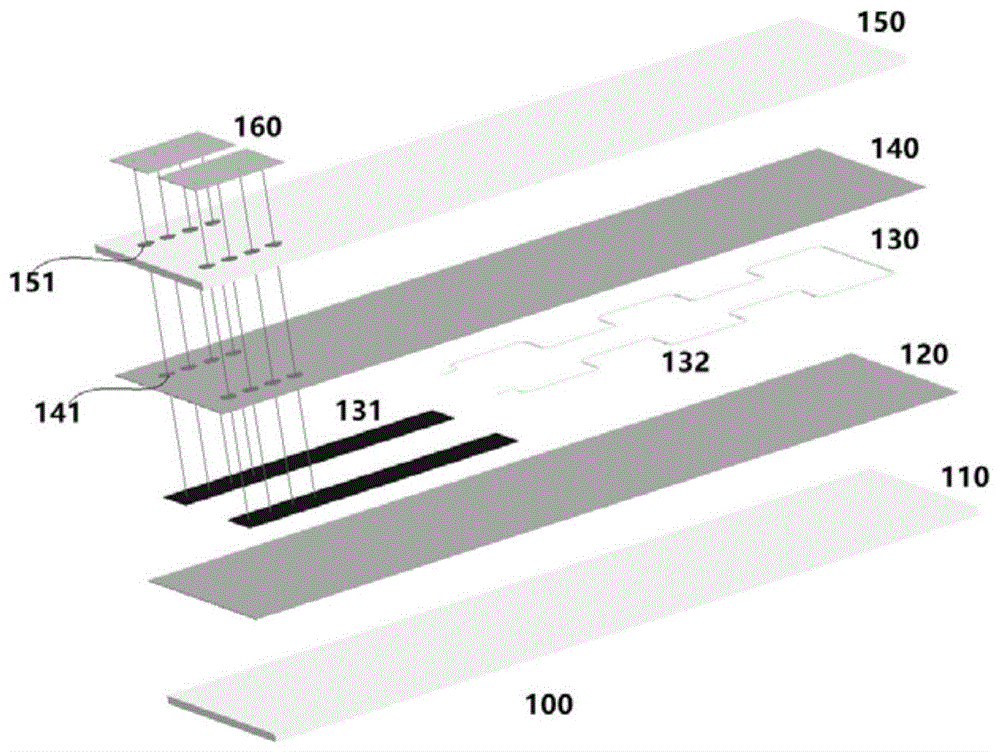
本发明属于电子烟领域,具体而言,本发明涉及加热片及其制备方法和应用。
背景技术:
:电子烟最近几年呈现蓬勃发展的态势,抽烟方式在年轻人身上悄然发生改变,出现了传统的燃烧式抽烟方式与现有的烟油雾化、加热不燃烧的抽烟方式并存,且选择后面两种新型的抽烟方式的人群越来越庞大。在欧美、日本、韩国等地区,电子烟已经发展成为一个百亿美元级别的巨大市场,且仍表现出井喷的态势。现在市面上的电子烟类型主要包括两种,一种为烟油雾化产生模拟烟雾的类型(以下简称“雾化电子烟”),其主要使用雾化器将烟油加热雾化产生烟雾,比较具有代表的品牌是relx、gippro等,该类型电子烟的核心技术在于雾化器的设计和制造,烟油的主要成分包括食用丙三醇、丙二醇,尼古丁盐、食用香精等成分;另一种为低温加热不燃烧类型(以下简称“hnb”),比较具有代表的品牌是iqos。hnb类型电子烟通过加热片对烟蛋进行加热产生烟雾,完全模拟传统烟草的抽烟方式,该类型的核心技术在于加热片的设计与制造。现在市面上的hnb电子烟加热片都是通过在陶瓷基材上印刷加热电极方式得到的。其中,基材主要为ysz、al2o3等陶瓷基板,加热电极材质多使用pt电极、ag/pd电极、ag电极。制备工艺为多次烧结,第一次将陶瓷基板烧结成型,然后按照加热片规格,利用激光划片将产品半切;第二次烧结底面釉料;第三次烧结加热电极、引线电极;第四次烧结表面釉料和焊盘;烧结完成后再将产品一颗颗掰开,分别焊接引线。从现有的制备工艺可以看出,现行的加热片需要经过多次烧结。由于加热电极的电阻与烧结制度有很大的相关性,这会导致过程的控制非常复杂,产品的一致性难于保证。另外由于氧化锆材料本身的原因,针对烧结好的基片进行激光划片会导致材料由于热效应产生微裂纹,影响产品的抗折强度,导致产品在使用过程中极易出现断片。因此,现有加热片有待进一步改进。技术实现要素:本发明旨在至少在一定程度上解决相关技术中的技术问题之一。为此,本发明的一个目的在于提出一种加热片及其制备方法和应用。该加热片制备难度低、使用寿命长且加热效果好、效率高。在本发明的一个方面,本发明提出了一种加热片,根据本发明的实施例,所述加热片包括:基体,所述基体包括:下基板层;下绝缘层,所述下绝缘层设在所述下基板层上;电极,所述电极设在所述下绝缘层上,并且所述电极包括相连的引线电极和加热电极;上绝缘层,所述上绝缘层设在所述电极上,且所述上绝缘层上设有第一开孔;上基板层,所述上基板层设在所述上绝缘层上,且所述上基板层上设有第二开孔,所述第二开孔与所述第一开孔相连;接触电极,所述接触电极设在所述上基板层上,且所述接触电极依次通过所述第二开孔、所述第一开孔与所述引线电极相连;表面釉层,所述表面釉层环绕所述基体的外表面设置,且不覆盖所述接触电极。根据本发明实施例的加热片,上绝缘层和下绝缘层可分别避免上基板层和下基板层在高温时产生离子电导,进而避免电极断路;加热电极可实现加热片的发热,通过控制加热电极的阻值可控制加热电极的发热量,另外加热电极处于产品中间位置,可使得加热片的发热热量更加均匀,加热效果更好;引线电极和接触电极均具有较低的电阻,引线电极可给加热电极通电,接触电极可用于外部电极引线的焊接,与外部电极引线具有极低的接触电阻,且接触电极设在上基板层上方,并通过第二开孔、第一开孔与引线电极相连,而不是设在上绝缘层与下绝缘层之间直接与引线电极相连,这种结构有利于降低加热片的制备难度,提高加热片的使用适应性;表面釉层可保护上下基板层,避免在发热过程中上下基板层因接触外界水汽、碳化物杂质等导致上下基板层老化,即表面釉层可为整个基体提供保护,显著延长加热片的使用寿命。另外,根据本发明上述实施例的加热片还可以具有如下附加的技术特征:在本发明的一些实施例中,分别独立地包括多个所述第一开孔和多个所述第二开孔。由此,可进一步实现接触电极与引线电极的电连接。在本发明的一些实施例中,所述第一开孔和所述第二开孔的数量一致且在竖直方向上位置一一对应。由此,可进一步实现接触电极与引线电极的电连接。在本发明的一些实施例中,所述表面釉层与所述接触电极、所述上基板层、所述上绝缘层、所述引线电极、所述加热电极、所述下绝缘层、所述下基板层的厚度比为10-75:5-34:100-400:6-82:5-34:5-34:6-82:100-400。由此,可进一步提高加热片的品质。在本发明的一些实施例中,所述接触电极、所述引线电极、所述加热电极的材质分别独立的为选自pt、mo/mn、ni、pt/pd、ag/pd中的至少之一。由此,可进一步提高加热片的品质。在本发明的一些实施例中,所述接触电极为方阻为0~20mω/□的第一铂金。由此,可进一步提高加热片的品质。在本发明的一些实施例中,所述引线电极为方阻为0~30mω/□的第二铂金。由此,可进一步提高加热片的品质。在本发明的一些实施例中,所述加热电极为方阻为10~150mω/□的第三铂金。由此,可进一步提高加热片的品质。在本发明的一些实施例中,所述接触电极与所述引线电极、所述加热电极的面积比为1-1.5:1-3:2-5。由此,可进一步提高加热片的品质。在本发明的一些实施例中,所述表面釉层的厚度为10-75μm。由此,可进一步提高加热片的品质。在本发明的一些实施例中,所述上基板层和所述下基板层的厚度分别独立的为100-400μm。由此,可进一步提高加热片的品质。在本发明的一些实施例中,所述上绝缘层和所述下绝缘层的厚度分别独立的为6-82μm。由此,可进一步提高加热片的品质。在本发明的一些实施例中,所述接触电极、所述引线电极和所述加热电极的厚度分别独立的为5-34μm。由此,可进一步提高加热片的品质。在本发明的一些实施例中,所述引线电极和所述加热电极的厚度相当。由此,可进一步提高加热片的品质。在本发明的再一个方面,本发明提出了一种制备上述加热片的方法,根据本发明的实施例,该方法包括:在下基板层表面形成下绝缘层;沿着所述下绝缘层的长度方向,依次在所述下绝缘层表面形成相连的引线电极和加热电极,得到第一基体;·在上基板层上形成第二开孔,并在所述上基板层表面形成上绝缘层,在所述上绝缘层上形成第一开孔;在所述上基板层上远离所述上绝缘层上的表面上形成接触电极,得到第二基体;将所述第一基体与所述第二基体接触放置,依次经等静压、切割和共烧后得到第三基体,所述第三基体的所述接触电极依次通过所述第二开孔和所述第一开孔与所述引线电极相连;在所述第三基体的除开所述接触电极的表面形成表面釉层,经热处理和焊线后得到加热片。根据本发明实施例的制备加热片的方法,上绝缘层和下绝缘层可分别避免上基板层和下基板层在高温时产生离子电导,进而避免电极短路;加热电极可实现加热片的发热,通过控制加热电极的阻值可控制加热电极的发热量;引线电极和接触电极均具有较低的电阻,引线电极可给加热电极通电,接触电极可用于外部电极引线的焊接,与外部电极引线具有极低的接触电阻,且接触电极设在上基板层上方,并通过第二开孔、第一开孔与引线电极相连,而不是设在上绝缘层与下绝缘层之间直接与引线电极相连,这种结构有利于降低加热片的制备难度,提高加热片的使用适应性;表面釉层可保护上下基板层,避免在发热过程中上下基板层因接触外界水汽、碳化物杂质等导致上下基板层老化,即表面釉层可为整个基体提供保护,显著延长加热片的使用寿命。进一步的,在制备过程中,经等静压、切割后,直接将包括上下基板、上下绝缘层、接触电极、引线电极、加热电极的产品一起进行一次烧结,烧结完在其表面形成表面釉层后再进行热处理,简化了加热片的制程,并且避开了针对上下基板的激光划片工艺,消除了由于激光热效应导致产品出现的微裂纹,增强了发热片的抗折强度。另外,根据本发明上述实施例的制备加热片的方法还可以具有如下附加的技术特征:在本发明的一些实施例中,所述上基板层和所述下基板层的材质分别独立的为选自氧化钇含量2-4wt%的ysz、zta和氧化铝含量为2-20wt%的ysz中的至少之一。由此,可进一步提升加热片的品质。在本发明的一些实施例中,所述上绝缘层和所述下绝缘层的材质为氧化铝。由此,可进一步提升加热片的品质。在本发明的一些实施例中,所述接触电极、所述引线电极和所述加热电极的材质为铂金。由此,可进一步提升加热片的品质。在本发明的一些实施例中,所述表面釉层的材质为高温玻璃浆。由此,可进一步提升加热片的品质。在本发明的一些实施例中,所述等静压的压力为25-200mpa,时间为10-120min。由此,可进一步提升加热片的品质。在本发明的一些实施例中,所述高温共烧的温度为1350-1550摄氏度,时间为30-240min。由此,可进一步提升加热片的品质。在本发明的又一个方面,本发明提出了一种电子烟,根据本发明的实施例,所述电子烟中含有上述加热片或采用上述制备加热片的方法制备得到的所述加热片。该加热片表面无微裂纹,且在加热片的表面具有表面釉层对整个加热片进行保护,有利于提升加热片的发热效果和效率,提高加热片的热稳定性,并可延长加热片的使用寿命,由此,有利于提升电子烟的品质,提升电子烟的口感。本发明的附加方面和优点将在下面的描述中部分给出,部分将从下面的描述中变得明显,或通过本发明的实践了解到。附图说明本发明的上述和/或附加的方面和优点从结合下面附图对实施例的描述中将变得明显和容易理解,其中:图1是根据本发明一个实施例的加热片的基体结构爆炸图;图2是根据本发明一个实施例的制备加热片的方法流程示意图。具体实施方式下面详细描述本发明的实施例,所述实施例的示例在附图中示出,其中自始至终相同或类似的标号表示相同或类似的元件或具有相同或类似功能的元件。下面通过参考附图描述的实施例是示例性的,旨在用于解释本发明,而不能理解为对本发明的限制。在本发明的描述中,需要理解的是,术语“中心”、“纵向”、“横向”、“长度”、“宽度”、“厚度”、“上”、“下”、“前”、“后”、“左”、“右”、“竖直”、“水平”、“顶”、“底”、“内”、“外”、“顺时针”、“逆时针”、“轴向”、“径向”、“周向”等指示的方位或位置关系为基于附图所示的方位或位置关系,仅是为了便于描述本发明和简化描述,而不是指示或暗示所指的装置或元件必须具有特定的方位、以特定的方位构造和操作,因此不能理解为对本发明的限制。此外,术语“第一”、“第二”仅用于描述目的,而不能理解为指示或暗示相对重要性或者隐含指明所指示的技术特征的数量。由此,限定有“第一”、“第二”的特征可以明示或者隐含地包括至少一个该特征。在本发明的描述中,“多个”的含义是至少两个,例如两个,三个等,除非另有明确具体的限定。在本发明中,除非另有明确的规定和限定,术语“安装”、“相连”、“连接”、“固定”等术语应做广义理解,例如,可以是固定连接,也可以是可拆卸连接,或成一体;可以是机械连接,也可以是电连接;可以是直接相连,也可以通过中间媒介间接相连,可以是两个元件内部的连通或两个元件的相互作用关系,除非另有明确的限定。对于本领域的普通技术人员而言,可以根据具体情况理解上述术语在本发明中的具体含义。在本发明中,除非另有明确的规定和限定,第一特征在第二特征“上”或“下”可以是第一和第二特征直接接触,或第一和第二特征通过中间媒介间接接触。而且,第一特征在第二特征“之上”、“上方”和“上面”可是第一特征在第二特征正上方或斜上方,或仅仅表示第一特征水平高度高于第二特征。第一特征在第二特征“之下”、“下方”和“下面”可以是第一特征在第二特征正下方或斜下方,或仅仅表示第一特征水平高度小于第二特征。在本发明的一个方面,本发明提出了一种加热片,根据本发明的实施例,参考图1,该加热片包括:基体100和表面釉层(未示出)。根据本发明的实施例,基体100包括:下基板层110、下绝缘层120、电极130、上绝缘层140、上基板层150和接触电极160。具体的,基体的具体形状并不受特别限制,本领域技术人员可以根据实际需要进行选择,例如可以为类多面体、类旋转体。下绝缘层120设在下基板层110上,下绝缘层可设在至少一部分下基板层上,电极130设在下绝缘层120上,电极可设在至少一部分下绝缘层上,下绝缘层可避免下基板层在高温时产生离子电导,进而避免电极断路。电极130包括相连的引线电极131和加热电极132,引线电极和加热电极的具体相连方式并不受特别限制,本领域技术人员可以根据实际需要进行选择,加热电极可实现加热片的发热,通过控制加热电极的阻值可控制加热电极的发热量,引线电极具有较低的电阻,可给加热电极通电,另外加热电极处于产品中间位置,可使得加热片的发热热量更加均匀,加热效果更好。上绝缘层140设在电极130上,电极与上绝缘层的至少一部分相连,且上绝缘层140上设有第一开孔141,上基板层150设在上绝缘层140上,上绝缘层与上基板层的至少一部分相连,且上基板层150上设有第二开孔151,第二开孔151与第一开孔141相连,第二开孔与第一开孔的至少一部分相连,上绝缘层可避免上基板层在高温时产生离子电导,进而避免电极断路。接触电极160设在上基板层150上,接触电极160依次通过第二开孔151、第一开孔141与引线电极131相连。接触电极可用于外部电极引线的焊接,与外部电极引线具有极低的接触电阻,且接触电极设在上基板层上方,并通过第二开孔、第一开孔与引线电极相连,而不是设在上绝缘层与下绝缘层之间直接与引线电极相连,这种结构有利于降低加热片的制备难度,提高加热片的使用适应性。根据本发明的一个实施例,可以分别独立地包括多个第一开孔和多个第二开孔,多个第一开孔及多个第二开孔各自的数量、具体排布方式、第一开孔与第二开孔的具体连接方式并不受特别限制,只要能使接触电极能通过第二开孔、第一开孔实现与引线电极相连即可。例如,第二开孔有序的分布在上基板层的左端、中端或右端,第一开孔有序的独立分布在上绝缘层的左端、中端或右端,且第一开孔中的至少一部分与第二开孔相连通,第一开孔中的至少一部分与引线电极相连,由此,可根据加热片的结构要求设置接触电极的具体位置,方便加热片的安装,也能给电子烟的结构设计提供更多可能。进一步的,第一开孔和第二开孔的数量一致且在竖直方向上位置一一对应。由此,接触电极可通过在竖直方向上连通的第二开孔和第一开孔实现与引线电极的高效连接。根据本发明的再一个实施例,接触电极与上基板层、上绝缘层、引线电极、加热电极、下绝缘层、下基板层的厚度比并不受特别限制,本领域技术人员可以根据实际需要进行选择,例如可以为5-34:100-400:6-82:5-34:5-34:6-82:100-400,进一步的,例如可以为5/10/15/20/25/30/34:100/150/200/250/300/350/400:6/15/25/35/45/55/65/75/82:5/10/15/20/25/30/34:5/10/15/20/25/30/34:6/15/25/35/45/55/65/75/82:100/150/200/250/300/350/400。发明人发现,接触电极太薄会导致接触电极本身的电阻增加,而使得与外部引线的接触电阻较大;接触电极过厚会导致与外部引线的焊接强度降低,导致引线在外部拉力作用下容易脱落,且成本增加。上下基板层的厚度太薄影响上下基板层的强度,导致加热片容易折断;而上下基板层厚度太厚会导致加热电极产生的热量传导至加热片表面的时间过长,影响加热片的发热效率。上下绝缘层太薄会导致绝缘层的绝缘性降低,在使用过程中容易出现击穿短路的现象;而上下绝缘层太厚会导致上下绝缘层分别与上下基板层的共烧性能降低,产品在共烧过程中容易出现分层开裂的现象。引线电极与加热电极太薄会导致引线电极的电阻过大,且通过大电流的性能降低,容易出现电极熔断而断路的现象;引线电极与加热电极太厚会导致产品有电极处的厚度增加,导致产品表面出现明显凸起,进而导致产品强度变差,且成本急剧增加。进一步的,上基板层和下基板层的厚度可以分别独立的为100-400μm,例如可以分别独立的为100μm、150μm、200μm、250μm、300um、350um、400μm。发明人发现,上下基板层的厚度太薄影响上下基板层的强度,导致加热片容易折断;而上下基板层厚度太厚会导致加热电极产生的热量传导至加热片表面的时间过长,影响加热片的发热效率。进一步的,上绝缘层和下绝缘层的厚度可以分别独立的为6-82μm,例如可以为6μm、15μm、25μm、35μm、45μm、55μm、65μm、75μm、82μm。发明人发现,上下绝缘层太薄会导致绝缘层的绝缘性降低,在使用过程中容易出现击穿短路的现象;而上下绝缘层太厚会导致上下绝缘层分别与上下基板层的共烧性能降低,产品在共烧过程中容易出现分层开裂的现象。进一步的,接触电极、引线电极和加热电极的厚度可以分别独立的为5-34μm,例如可以为5μm、10μm、15μm、20μm、25μm、30μm、34μm。发明人发现,接触电极太薄会导致接触电极本身的电阻增加,而使得与外部引线的接触电阻较大;接触电极过厚会导致与外部引线的焊接强度降低,导致引线在外部拉力作用下容易脱落,且成本增加。引线电极与加热电极太薄会导致引线电极的电阻过大,且通过大电流的性能降低,容易出现电极熔断而断路的现象;引线电极与加热电极太厚会导致产品有电极处的厚度增加,导致产品表面出现明显凸起,进而导致产品强度变差,且成本急剧增加。进一步的,引线电极和加热电极的厚度相当,由此,可使得位于电极上方的上绝缘层各处厚度较均匀,提升加热片的性能。根据本发明的又一个实施例,接触电极与引线电极、加热电极的表面积之比可以为1-1.5:1-3:2-5,例如可以为1/1.1/1.15/1.2/1.3/1.4/1.5:1/1.2/1.6/2.0/2.3/2.6/3:2/2.5/3.0/3.5/4.0/4.5/5。发明人发现,若加热电极区域面积过小,在使用过程中会导致发热量不够,烟草利用率较低;而若加热电极区域面积过大,在使用过程中会导致接触电极处的温度很高,而外部引线与接触电极是通过焊接连接,接触电极过高的温度会影响焊点的可靠性。接触电极区域面积过小影响后续的焊接工艺,会出现焊接不充分,焊接脱落的现象,而接触电极区域面积过大会导致后续表面釉层未包覆的空间增加,影响产品的耐老化性能,并且会增加成本。引线电极区域面积的变化,将会直接导致加热区域的变化,会导致发热效率及接触电极处温度的变化。根据本发明的又一个实施例,上基板层和下基板层的材质可以分别独立的为选自氧化钇含量2-4wt%的ysz、zta和氧化铝含量为2-20wt%的ysz中的至少之一。发明人发现,该类基板材质具有很好的强度,用此类基板材质做成的产品在使用过程中具有很好的抗折性能,另外此类基板材质具有较低的导热系数(2-4),具有较好的保温性能,能够更好的节能。上绝缘层和下绝缘层的材质可以为氧化铝,氧化铝具有很好的绝缘电阻,能够极好的解决基板材质高温导电的问题,另外氧化铝具有很好的导热系数(20-30),能够将加热电极提供的热量很好的传导至绝缘层整个平面,从而降低内部热量传导至整个产品表面的时间。接触电极、引线电极和加热电极的材质可以分别独立的为选自pt、mo/mn、ni、pt/pd、ag/pd中的至少之一,优选的,接触电极、引线电极和加热电极的材质可以为铂金,具体的,接触电极可以为方阻为0-20mω/□的第一铂金,例如可以为0mω/□、5mω/□、10mω/□、15mω/□、20mω/□的第一铂金,引线电极可以为方阻为0-30mω/□的第二铂金,例如可以为0mω/□、5mω/□、10mω/□、15mω/□、20mω/□、25mω/□、30mω/□的第二铂金,加热电极可以为方阻为10-150mω/□的第三铂金,例如可以为10mω/□、30mω/□、50mω/□、70mω/□、90mω/□、110mω/□、130mω/□、150mω/□的第三铂金。铂金具有很好的耐大电流性能,在高低温冲击下不易产生老化。表面釉层的材质可以为高温玻璃浆。以上材质的选择都使得本专利涉及的加热片具有良好的实用性和可靠性。根据本发明的实施例,表面釉层(未示出)环绕基体100的外表面设置,且不覆盖接触电极160。发明人发现,表面釉层环绕基体除接触电极的外表面设置,使得表面釉层为整个基体提供了保护,有利于延长加热片的使用寿命。进一步的,表面釉层与下基板层的厚度比可以为10-75:100-400。例如可以为10/20/30/40/50/60/70/75:100/150/200/250/300/350/400。进一步的,表面釉层的厚度可以为10-75μm,例如可以为10μm、20μm、30μm、40μm、50μm、60μm、70μm、75μm。发明人发现,表面釉层与上下基板层的厚度比过高会导致表面釉层在高低温冲击下容易开裂,俗称“釉裂”,开裂后的釉层将会降低对上下基板层的保护作用;而厚度比过低将会同样降低对上下基板层的保护作用,同时过薄的表面釉层难于加工,容易造成包覆孔洞。根据本发明实施例的加热片,上绝缘层和下绝缘层可分别避免上基板层和下基板层在高温时产生离子电导,进而避免电极断路;加热电极可实现加热片的发热,通过控制加热电极的阻值可控制加热电极的发热量,另外加热电极处于产品中间位置,可使得加热片的发热热量更加均匀,加热效果更好;引线电极和接触电极均具有较低的电阻,引线电极可给加热电极通电,接触电极可用于外部电极引线的焊接,与外部电极引线具有极低的接触电阻,且接触电极设在上基板层上方,并通过第二开孔、第一开孔与引线电极相连,而不是设在上绝缘层与下绝缘层之间直接与引线电极相连,这种结构有利于降低加热片的制备难度,提高加热片的使用适应性;表面釉层可保护上下基板层,避免在发热过程中上下基板层因接触外界水汽、碳化物杂质等导致上下基板层老化,即表面釉层可为整个基体提供保护,显著延长加热片的使用寿命。在本发明的再一个方面,本发明提出了一种制备上述加热片的方法,根据本发明的实施例,参考图2,该方法包括:s100:在下基板层表面形成下绝缘层该步骤中,在下基板层表面形成下绝缘层,下基板层可以是采用流延成型的方式成型的,流延成型所得的下基板层各部分成分起伏小,性能均一而稳定,断裂韧性好,且生产效率高,可连续操作。下绝缘层可避免下基板层在高温时产生离子电导,进而避免电极短路。需要说明的是,在下基板上形成下绝缘层的具体方式并不受特别限制,本领域技术人员可以根据实际需要进行选择,例如可以采用丝网印刷的方式在下基板层上形成下绝缘层。进一步的,下基板层可以为陶瓷层,下基板层的材质可以为选自氧化钇含量2-4wt%的ysz、zta和氧化铝含量为2-20wt%的ysz中的至少之一。发明人发现,掺钇氧化锆中氧化钇含量过低将可能导致掺钇氧化锆稳定性较差,使掺钇氧化锆在使用过程中四方相极易转变成单斜相而产生老化,进而导致掺钇氧化锆碎裂;而若掺钇氧化锆中氧化钇含量过高,则会降低掺钇氧化锆本身的强度,导致在使用过程中由于外力的作用而产生断片。进一步的,下绝缘层的材质可以为氧化铝。s200:沿着下绝缘层的长度方向,依次在下绝缘层表面形成相连的引线电极和加热电极该步骤中,沿着下绝缘层的长度方向,依次在下绝缘层表面形成相连的引线电极和加热电极,得到第一基体。加热电极可实现加热片的发热,通过控制加热电极的阻值可控制加热电极的发热量;引线电极和接触电极均具有较低的电阻,引线电极可给加热电极通电。在下绝缘层表面形成相连的引线电极和加热电极的具体方式并不受特别限制,本领域技术人员可以根据实际需要进行选择,例如可以采用丝网印刷的方式。在引线电极和加热电极的具体连接关系为:通电后,电信号从引线电极的一端进入,沿着引线电极到达发热电极,在发热电极电阻的作用下实现发热电极的发热,最后从引线电极的另一端出来。进一步的,引线电极和加热电极的材质可以分别独立的为选自pt、mo/mn、ni、pt/pd、ag/pd中的至少之一,优选的,引线电极和加热电极的材质可以为铂金。具体的,引线电极可以为方阻为0-30mω/□的铂金,由此,可使得其适于为加热电极通电而能耗较低;加热电极可以为方阻为10-150mω/□的铂金,由此,可通过阻值的控制实现发热量的控制,进而实现产品的发热。s300:在上基板层上形成第二开孔,并在上基板层表面形成上绝缘层,在上绝缘层上形成第一开孔该步骤中,在上基板层上形成第二开孔,并在上基板层表面形成上绝缘层,在上绝缘层上形成第一开孔。第一开孔和第二开孔的具体形成方式并不受特别限制,本领域技术人员可以根据实际情况进行选择。上基板上的第二开孔和上绝缘层上的第一开孔的设立是为了让后续位于远离上绝缘层的形成于上基板层上的接触电极能依次通过第二开孔和第一开孔实现与引线电极相连。在这一原则上,第一开孔的具体数目及在上绝缘层上的具体分布形式、第二开孔的具体数目及在上基板层上具体分布形式并不受特别限制,本领域技术人员可以根据实际需要进行选择。在上基板上形成上绝缘层的具体形式也不受特别限制,例如可以采用丝网印刷的方式形成。上基板层可以是采用流延成型的方式成型的,流延成型所得的上基板层各部分成分起伏小,性能均一而稳定,断裂韧性好,且生产效率高,可连续操作。上绝缘层可避免上基板层在高温时产生离子电导,进而避免电极短路。进一步的,上基板层可以为陶瓷层,上基板层的材质可以为选自氧化钇含量2-4wt%的ysz、zta和氧化铝含量为2-20wt%的ysz中的至少之一。发明人发现,掺钇氧化锆中氧化钇含量过低将可能导致掺钇氧化锆稳定性较差,使掺钇氧化锆在使用过程中四方相极易转变成单斜相而产生老化,进而导致掺钇氧化锆碎裂;而若掺钇氧化锆中氧化钇含量过高,则会降低掺钇氧化锆本身的强度,导致在使用过程中由于外力的作用而产生断片。进一步的,上绝缘层的材质可以为氧化铝。s400:在上基板层上远离上绝缘层上的表面上形成接触电极该步骤中,在上基板层上远离上绝缘层上的表面上形成接触电极,得到第二基体。在上基板层上形成接触电极的具体方式并不受特别限制,本领域技术人员可以根据实际需要进行选择,例如可以采用丝网印刷的方式形成。接触电极可用于外部电极引线的焊接,与外部电极引线具有极低的接触电阻,且接触电极设在上基板层上方,并依次通过第二开孔、第一开孔与引线电极相连,而不是设在上绝缘层与下绝缘层之间直接与引线电极相连,这种结构有利于降低加热片的制备难度,提高加热片的使用适应性。进一步的,接触电极的材质可以为选自pt、mo/mn、ni、pt/pd、ag/pd中的至少之一,优选铂金,例如可以为方阻为0~20mω/□的铂金,由此,可使得其与外部电极的接触电阻极低,进一步实现外部电极与引线电极的连接。s500:将第一基体与第二基体接触放置,并进行等静压、切割和共烧处理该步骤中,将第一基体与第二基体接触放置,经等静压、切割后得到第三基体,第三基体的接触电极依次通过第二开孔和第一开孔与引线电极相连。具体的,在等静压之前,需将第一基体与第二基体按照一定的位置关系放置,第一基体的引线电极和加热电极与第二基体的上绝缘层相连,且需使等静压后接触电极能依次通过第二开孔和第一开孔实现与引线电极的相连,进而使得可通过外部电极向接触电极通电至引线电极、加热电极,实现加热电极的发热。通过将等静压处理,可增加产品的致密度,提高产品性能。经等静压后再进行切割和共烧处理,且将切割放在共烧之前,消除了因激光热效应导致加热片产生微裂纹的影响,提升了产品的可靠性,增强了加热片的抗折强度;同时,共烧处理有利于提高电极与上下绝缘层之间的结合力,提升产品性能。由此,在整个制备过程中,只需将上下基板、上下绝缘层、接触电极、引线电极、加热电极和表面釉层一起进行一次烧结,显著简化了加热片的制备工艺,并且避开了针对上下基板的激光划片工艺,消除了由于激光热效应导致产品出现的微裂纹,增强了发热片的抗折强度。根据本发明的一个实施例,等静压处理的条件并不受特别限制,本领域技术人员可以根据实际需要进行选择,例如等静压的温度可以为60-80摄氏度,例如可以为60摄氏度、65摄氏度、70摄氏度、75摄氏度、80摄氏度,压力可以为25-200mpa,例如可以为25mpa、50mpa、75mpa、100mpa、125mpa、150mpa、175mpa、200mpa,时间可以为10-120min,例如可以为10min、30min、50min、70min、90min、110min、120min。发明人发现,在上述等静压处理条件下,可使得等静压后的产品具有较佳的致密度,同时生产效率较佳。根据本发明的再一个实施例,切割处理的具体方式并不受特别限制,本领域技术人员可以根据需要进行选择,例如切割处理可以为激光切割或机械式冲切。发明人实验发现,在这两种切割方式下对等静压后产品进行切割,对最终产品的性能影响较小,符合生产要求,且这两种方式为工厂常用切割方式,不会额外增加企业的生产成本,经济效益高。根据本发明的又一个实施例,共烧处理的条件并不受特别限制,本领域技术人员可以根据实际需要进行选择,例如共烧成型处理的温度可以为1350-1550摄氏度,例如可以为1350摄氏度、1400摄氏度、1450摄氏度、1500摄氏度、1550摄氏度,时间可以为30-240min,例如可以为30min、60min、90min、120min、150min、180min、210min、240min。发明人发现,过低的共烧温度和较短的共烧时间,会使切割后产品烧结不充分,材料没有完全成瓷,瓷体中存在大量的孔洞,进而使得加热片的强度得不到保证;而过高的共烧温度和过长的共烧时间,会导致材料过烧,瓷体晶粒会异常长大,瓷体中也会出现孔洞,加热片的强度也会恶化。总之,合理的烧结温度和烧结时间才能保证加热片材料具有良好的力学性能。s600:在第三基体的除开接触电极的表面形成表面釉层该步骤中,在第三基体的除开接触电极的表面形成表面釉层,经热处理和焊线后得到加热片。需要说明的是,表面釉层的形成方式并不受特别限制,本领域技术人员可以根据实际需要进行选择,例如可以为丝网印刷的方式或侧面浸釉的方式。在热处理过程中表面釉层会出现液相,该液相在保温过程中流平,使基体表面光滑,表面釉层环绕基体除接触电极的外表面设置,表面釉层可保护上下基板层,避免在发热过程中上下基板层因接触外界水汽、碳化物杂质等导致上下基板层老化,即表面釉层可为整个基体提供保护,显著延长加热片的使用寿命。进一步的,表面釉层的材质可以为高温玻璃浆。根据本发明的一个实施例,热处理的条件并不受特别限制,本领域技术人员可以根据实际需要进行选择,例如热处理的温度可以为800-1000摄氏度,例如可以为800摄氏度、850摄氏度、900摄氏度、950摄氏度、1000摄氏度,时间可以为5-15min,例如可以为5min、7min、9min、11min、13min、15min。发明人发现,在过低的热处理温度和过短的热处理时间下,表面釉层没有充分的液化和流平,导致基体表面粗糙,不够光滑,在使用的过程中会有很多的被加热物质粘附于表面,且不易清洗;而在过高的热处理温度和过长的热处理时间下,表面釉层出现流挂的现象,表面釉料会出现流水纹,产品出现表面不平整的现象,导致被加热物质粘附于表面。根据本发明实施例的制备加热片的方法,上绝缘层和下绝缘层可分别避免上基板层和下基板层在高温时产生离子电导,进而避免电极断路;加热电极可实现加热片的发热,通过控制加热电极的阻值可控制加热电极的发热量;引线电极和接触电极均具有较低的电阻,引线电极可给加热电极通电,接触电极可用于外部电极引线的焊接,与外部电极引线具有极低的接触电阻,且接触电极设在上基板层上方,并通过第二开孔、第一开孔与引线电极相连,而不是设在上绝缘层与下绝缘层之间直接与引线电极相连,这种结构有利于降低加热片的制备难度,提高加热片的使用适应性;表面釉层可保护上下基板层,避免在发热过程中上下基板层因接触外界水汽、碳化物杂质等导致上下基板层老化,即表面釉层可为整个基体提供保护,显著延长加热片的使用寿命。进一步的,在制备过程中,经等静压、切割后,直接将包括上下基板、上下绝缘层、接触电极、引线电极、加热电极的产品一起进行一次烧结,烧结完在其表面形成表面釉层后再进行热处理,简化了加热片的制程,并且避开了针对上下基板的激光划片工艺,消除了由于激光热效应导致产品出现的微裂纹,增强了发热片的抗折强度。需要说明的是,上述加热片的特征和优点同样适用于上述制备加热片的方法,对此不再赘述。在本发明的又一个方面,本发明提出了一种电子烟,根据本发明的实施例,所述电子烟中含有上述加热片或采用上述制备加热片的方法制备得到的所述加热片。该加热片表面无微裂纹,且在加热片的表面具有表面釉层对整个加热片进行保护,有利于提升加热片的发热效果和效率,提高加热片的热稳定性,并可延长加热片的使用寿命,由此,有利于提升电子烟的品质,提升电子烟的口感。需要说明的是,上述加热片的优点和特征或者采用上述制备加热片的方法所得的加热片的优点和特征同样适用于该电子烟,对此不再赘述。下面参考具体实施例,对本发明进行描述,需要说明的是,这些实施例仅仅是描述性的,而不以任何方式限制本发明。实施例1在材质为氧化钇含量2wt%的ysz的下基板层表面通过丝网印刷形成氧化铝下绝缘层;沿着下绝缘层的长度方向,依次在下绝缘层表面形成相连的材质均为铂金的引线电极和加热电极,得到第一基体;在材质为氧化钇含量2wt%的ysz的上基板层上形成第二开孔,并在上基板层表面通过丝网印刷形成氧化铝上绝缘层,在上绝缘层上形成第一开孔,第一开孔和第二开孔的数量一致且在竖直方向上位置一一对应;在上基板层上远离上绝缘层上的表面上通过丝网印刷形成材质为铂金的接触电极,得到第二基体;将第一基体与第二基体接触放置,依次经等静压、激光切割和共烧后得到第三基体,第三基体的接触电极依次通过第二开孔和第一开孔与引线电极相连,其中,等静压的压力为25mpa,时间为120min,温度为80摄氏度,高温共烧的温度为1350摄氏度,时间为240min。在第三基体的除开接触电极的表面形成材质为高温玻璃浆的表面釉层,并在800摄氏度下热处理15min,经焊线后得到加热片。该加热片,接触电极与引线电极、加热电极的表面积之比为1:1:5,表面釉层的厚度为10μm,上基板层和下基板层的厚度均为100μm,上绝缘层和下绝缘层的厚度均为6μm,接触电极、引线电极和加热电极的厚度均为5μm。取6个样品进行三点抗折强度测试并与现有多次烧结工艺所得的加热片样品进行比较,结果如表1所示。由表1可知,本申请上述技术方案所得的加热片相对于旧方案所得的加热片的三点抗折强度平均提高41%。表1实施例1方案与旧方案所得样品的三点抗折强度实施例2在材质为氧化钇含量3wt%的ysz的下基板层表面通过丝网印刷形成氧化铝下绝缘层;沿着下绝缘层的长度方向,依次在下绝缘层表面形成相连的材质均为铂金的引线电极和加热电极,得到第一基体;在材质为氧化钇含量3wt%的ysz3的上基板层上形成第二开孔,并在上基板层表面通过丝网印刷形成氧化铝上绝缘层,在上绝缘层上形成第一开孔,第一开孔和第二开孔的数量一致且在竖直方向上位置一一对应;在上基板层上远离上绝缘层上的表面上通过丝网印刷形成材质为铂金的接触电极,得到第二基体;将第一基体与第二基体接触放置,依次经等静压、激光切割和共烧后得到第三基体,第三基体的接触电极依次通过第二开孔和第一开孔与引线电极相连,其中,等静压的压力为55mpa,时间为110min,温度为75摄氏度,高温共烧的温度为1400摄氏度,时间为200min。在第三基体的除开接触电极的表面形成材质为高温玻璃浆的表面釉层,并在850摄氏度下热处理10min,经焊线后得到加热片。该加热片,接触电极与引线电极、加热电极的表面积之比为1:1.2:4.5。表面釉层的厚度为25μm,上基板层和下基板层的厚度均为150μm,上绝缘层和下绝缘层的厚度均为20μm,接触电极、引线电极和加热电极的厚度均为20μm。取6个样品进行三点抗折强度测试并与现有多次烧结工艺所得的加热片样品进行比较,结果如表2所示。由表2可知,本申请上述技术方案所得的加热片相对于旧方案所得的加热片的三点抗折强度平均提高23%。表2实施例2方案与旧方案所得样品的三点抗折强度实施例3在材质为氧化钇含量4wt%的ysz的下基板层表面通过丝网印刷形成氧化铝下绝缘层;沿着下绝缘层的长度方向,依次在下绝缘层表面形成相连的材质均为铂金的引线电极和加热电极,得到第一基体;在材质为氧化钇含量4wt%的ysz的上基板层上形成第二开孔,并在上基板层表面通过丝网印刷形成氧化铝上绝缘层,在上绝缘层上形成第一开孔,第一开孔和第二开孔的数量一致且在竖直方向上位置一一对应;在上基板层上远离上绝缘层上的表面上通过丝网印刷形成材质为铂金的接触电极,得到第二基体;将第一基体与第二基体接触放置,依次经等静压、激光切割和共烧后得到第三基体,第三基体的接触电极依次通过第二开孔和第一开孔与引线电极相连,其中,等静压的压力为85mpa,时间为90min,温度为70摄氏度,高温共烧的温度为1450摄氏度,时间为150min。在第三基体的除开接触电极的表面形成材质为高温玻璃浆的表面釉层,并在900摄氏度下热处理8min,经焊线后得到加热片。该加热片,接触电极与引线电极、加热电极的表面积之比为1:1.16:4。表面釉层的厚度为75μm,上基板层和下基板层的厚度均为200μm,上绝缘层和下绝缘层的厚度均为82μm,接触电极、引线电极和加热电极的厚度均为34μm。取6个样品进行三点抗折强度测试并与现有多次烧结工艺所得的加热片样品进行比较,结果如表3所示。由表3可知,本申请上述技术方案所得的加热片相对于旧方案所得的加热片的三点抗折强度平均提高39%。表3实施例3方案与旧方案所得样品的三点抗折强度序号旧方案(kg)新方案(kg)10.81.1020.851.2030.851.1540.751.1550.901.1060.801.10平均值0.811.13实施例4在材质为zta的下基板层表面通过丝网印刷形成氧化铝下绝缘层;沿着下绝缘层的长度方向,依次在下绝缘层表面形成相连的材质均为铂金的引线电极和加热电极,得到第一基体;在材质为zta的上基板层上形成第二开孔,并在上基板层表面通过丝网印刷形成氧化铝上绝缘层,在上绝缘层上形成第一开孔,第一开孔和第二开孔的数量一致且在竖直方向上位置一一对应;在上基板层上远离上绝缘层上的表面上通过丝网印刷形成材质为铂金的接触电极,得到第二基体;将第一基体与第二基体接触放置,依次经等静压、激光切割和共烧后得到第三基体,第三基体的接触电极依次通过第二开孔和第一开孔与引线电极相连,其中,等静压的压力为115mpa,时间为70min,温度为65摄氏度,高温共烧的温度为1500摄氏度,时间为125min。在第三基体的除开接触电极的表面形成材质为高温玻璃浆的表面釉层,并在950摄氏度下热处理6min,经焊线后得到加热片。该加热片,接触电极与引线电极、加热电极的表面积之比为1.2:2:3.5。表面釉层的厚度为25μm,上基板层和下基板层的厚度均为250μm,上绝缘层和下绝缘层的厚度均为20μm,接触电极、引线电极和加热电极的厚度均为20μm。取6个样品进行三点抗折强度测试并与现有多次烧结工艺所得的加热片样品进行比较,结果如表4所示。由表4可知,本申请上述技术方案所得的加热片相对于旧方案所得的加热片的三点抗折强度平均提高38%。表4实施例4方案与旧方案所得样品的三点抗折强度序号旧方案(kg)新方案(kg)10.951.3521.001.4031.051.3040.981.3051.051.4060.91.45平均值0.991.37实施例5在材质为氧化铝含量为2wt%的ysz的下基板层表面通过丝网印刷形成氧化铝下绝缘层;沿着下绝缘层的长度方向,依次在下绝缘层表面形成相连的材质均为铂金的引线电极和加热电极,得到第一基体;在材质为氧化铝含量为2-20wt%的ysz的上基板层上形成第二开孔,并在上基板层表面通过丝网印刷形成氧化铝上绝缘层,在上绝缘层上形成第一开孔,第一开孔和第二开孔的数量一致且在竖直方向上位置一一对应;在上基板层上远离上绝缘层上的表面上通过丝网印刷形成材质为铂金的接触电极,得到第二基体;将第一基体与第二基体接触放置,依次经等静压、激光切割和共烧后得到第三基体,第三基体的接触电极依次通过第二开孔和第一开孔与引线电极相连,其中,等静压的压力为145mpa,时间为50min,温度为60摄氏度,高温共烧的温度为1550摄氏度,时间为30min。在第三基体的除开接触电极的表面形成材质为高温玻璃浆的表面釉层,并在1000摄氏度下热处理5min,经焊线后得到加热片。该加热片,接触电极与引线电极、加热电极的表面积之比为1:1.2:3。表面釉层的厚度为25μm,上基板层和下基板层的厚度均为300μm,上绝缘层和下绝缘层的厚度均为20μm,接触电极、引线电极和加热电极的厚度均为20μm。取6个样品进行三点抗折强度测试并与现有多次烧结工艺所得的加热片样品进行比较,结果如表5所示。由表5可知,本申请上述技术方案所得的加热片相对于旧方案所得的加热片的三点抗折强度平均提高16%。表5实施例5方案与旧方案所得样品的三点抗折强度序号旧方案(kg)新方案(kg)11.251.4521.351.5031.351.5541.351.5551.301.6061.401.60平均值1.331.54实施例6在材质为氧化铝含量为10wt%的ysz的下基板层表面通过丝网印刷形成氧化铝下绝缘层;沿着下绝缘层的长度方向,依次在下绝缘层表面形成相连的材质均为铂金的引线电极和加热电极,得到第一基体;在材质为氧化铝含量为10wt%的ysz的上基板层上形成第二开孔,并在上基板层表面通过丝网印刷形成氧化铝上绝缘层,在上绝缘层上形成第一开孔,第一开孔和第二开孔的数量一致且在竖直方向上位置一一对应;在上基板层上远离上绝缘层上的表面上通过丝网印刷形成材质为铂金的接触电极,得到第二基体;将第一基体与第二基体接触放置,依次经等静压、激光切割和共烧后得到第三基体,第三基体的接触电极依次通过第二开孔和第一开孔与引线电极相连,其中,等静压的压力为175mpa,时间为30min,温度为62摄氏度,高温共烧的温度为1388摄氏度,时间为60min。在第三基体的除开接触电极的表面形成材质为高温玻璃浆的表面釉层,并在880摄氏度下热处理10min,经焊线后得到加热片。该加热片,接触电极与引线电极、加热电极的表面积之比为1.5:3:5。表面釉层的厚度为25μm,上基板层和下基板层的厚度均为350μm,上绝缘层和下绝缘层的厚度均为20μm,接触电极、引线电极和加热电极的厚度均为20μm。取6个样品进行三点抗折强度测试并与现有多次烧结工艺所得的加热片样品进行比较,结果如表6所示。由表6可知,本申请上述技术方案所得的加热片相对于旧方案所得的加热片的三点抗折强度平均提高17%。表6实施例6方案与旧方案所得样品的三点抗折强度序号旧方案(kg)新方案(kg)11.551.8021.601.8531.61.8541.651.8051.651.9061.601.90平均值1.611.89实施例7在材质为氧化铝含量为20wt%的ysz的下基板层表面通过丝网印刷形成氧化铝下绝缘层;沿着下绝缘层的长度方向,依次在下绝缘层表面形成相连的材质均为铂金的引线电极和加热电极,得到第一基体;在材质为氧化铝含量为20wt%的ysz的上基板层上形成第二开孔,并在上基板层表面通过丝网印刷形成氧化铝上绝缘层,在上绝缘层上形成第一开孔,第一开孔和第二开孔的数量一致且在竖直方向上位置一一对应;在上基板层上远离上绝缘层上的表面上通过丝网印刷形成材质为铂金的接触电极,得到第二基体;将第一基体与第二基体接触放置,依次经等静压、激光切割和共烧后得到第三基体,第三基体的接触电极依次通过第二开孔和第一开孔与引线电极相连,其中,等静压的压力为200mpa,时间为10min,温度为60摄氏度,高温共烧的温度为1350摄氏度,时间为30min。在第三基体的除开接触电极的表面形成材质为高温玻璃浆的表面釉层,并在800摄氏度下热处理5min,经焊线后得到加热片。该加热片,接触电极与引线电极、加热电极的表面积之比为1.1:1:2。表面釉层的厚度为25μm,上基板层和下基板层的厚度均为400μm,上绝缘层和下绝缘层的厚度均为20μm,接触电极、引线电极和加热电极的厚度均为20μm。取6个样品进行三点抗折强度测试并与现有多次烧结工艺所得的加热片样品进行比较,结果如表7所示。由表7可知,本申请上述技术方案所得的加热片相对于旧方案所得的加热片的三点抗折强度平均提高11%。表7实施例7方案与旧方案所得样品的三点抗折强度在本说明书的描述中,参考术语“一个实施例”、“一些实施例”、“示例”、“具体示例”、或“一些示例”等的描述意指结合该实施例或示例描述的具体特征、结构、材料或者特点包含于本发明的至少一个实施例或示例中。在本说明书中,对上述术语的示意性表述不必须针对的是相同的实施例或示例。而且,描述的具体特征、结构、材料或者特点可以在任一个或多个实施例或示例中以合适的方式结合。此外,在不相互矛盾的情况下,本领域的技术人员可以将本说明书中描述的不同实施例或示例以及不同实施例或示例的特征进行结合和组合。尽管上面已经示出和描述了本发明的实施例,可以理解的是,上述实施例是示例性的,不能理解为对本发明的限制,本领域的普通技术人员在本发明的范围内可以对上述实施例进行变化、修改、替换和变型。当前第1页12