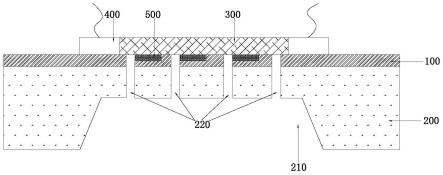
mems结构雾化芯及其制备方法
技术领域
1.本发明特别涉及一种mems结构雾化芯及其制备方法,属于雾化器技术领域。
背景技术:2.雾化技术是通过一定方式将流体介质变成小液滴的过程。目前雾化的方式主要高压气体雾化、超声波雾化、微波加热雾化、电阻加热雾化等。作为雾化技术的“心脏”,雾化芯决定着雾化效果。
3.目前常用的雾化芯结构如图1,其是在多孔陶瓷上,通过印刷工艺形成加热电阻。多孔陶瓷中细小的微孔,是陶瓷雾化芯实现稳定导液和锁液功能的关键。由于表面张力和毛细作用,流体介质可以均匀地渗入到雾化芯中,并吸附在雾化芯表面。
4.多孔陶瓷雾化芯相对于其他雾化方式,在加热过程中,它的温度会上升得更快,温度均匀性更好。但由于电阻浆料通过丝网印刷工艺进行制备,后续还有经过高温烧结等工艺,一方面高温烧结会造成电阻浆料的收缩,从而导致电阻的离散性;另一方面,由于多孔陶瓷支撑结构是微孔结构,在印刷过程中,电阻浆料会渗入孔隙中,从而引起断线、断路等缺陷。而以合金膜片作为加热结构的雾化芯,在在其加热工作状态下,会因为热膨胀系数差异方面的问题,从而会导致合金膜片和多孔陶瓷之间产生空隙,进而影响雾化效果。
技术实现要素:5.本发明的主要目的在于提供一种mems结构雾化芯及其制备方法,从而克服现有技术中的不足。
6.为实现前述发明目的,本发明采用的技术方案包括:
7.本发明实施例提供了一种mems结构雾化芯,包括:
8.支撑结构,所述支撑结构具有背对设置的第一表面和第二表面,所述第一表面设置有储油槽,所述第二表面设置有与所述储油槽相连通的导油孔,所述第二表面与第一表面背对设置;
9.电阻加热结构,所述电阻加热结构设置在所述支撑结构的第二表面,当所述电阻加热结构接入电源后,自所述导油孔输送的流体介质能够与所述电阻加热结构接触并被加热雾化。
10.本发明实施例还提供了所述的mems结构雾化芯的制备方法,其特征在于包括:
11.在支撑结构的第二表面形成图案化的导电材料层,并作为电阻加热结构;
12.在支撑结构的第一表面加工形成储油槽,以及,在所述储油槽的底部形成贯穿所述支撑结构的导油孔,且使自所述导油孔输送的流体介质能够与所述导电材料层接触。
13.与现有技术相比,本发明的优点包括:本发明提供的一种mems结构雾化芯结构的雾化芯可靠性更高,温度的一致性控制的更好,可以精准控制电阻范围;而且还可以精准控制渗油的速率和数量,结合半导体工艺,可以实现批量化、低成本的制造,避免陶瓷工艺烧结时带来的污染。
附图说明
14.图1是现有技术中的一种多孔陶瓷雾化芯样品;
15.图2是本发明实施例1中提供的一种mems结构雾化芯的结构示意图;
16.图3是本发明一典型实施案例中提供的加热电阻的结构示意图;
17.图4是本发明实施例1中提供的一种mems结构雾化芯的制备流程示意图;
18.图5是本发明实施例1中提供的一种mems结构雾化芯的制备流程结构示意图;
19.图6是本发明实施例2中提供的一种mems结构雾化芯的结构示意图。
具体实施方式
20.鉴于现有技术中的不足,本案发明人经长期研究和大量实践,得以提出本发明的技术方案。如下将对该技术方案、其实施过程及原理等作进一步的解释说明。
21.研发一种能够工艺简单、性能好、精度高的雾化芯,适用在电子烟、加湿器、蒸脸器、造雾机、医疗雾化器等应用领域。
22.为了克服目前厚膜印刷和合金膜片制备的多孔陶瓷的雾化芯的缺点,本发明提出在硅基支撑结构上,利用半导体工艺中的沉积技术,实现金属薄膜在硅基表面上的图形化,形成稳定的加热电阻结构;另一方面通过干法和湿法刻蚀,形成精度较高的储油槽,还可以形成精准的导油孔,可以控制雾化过程中流体介质渗透的速率,保持良好的雾化效果。
23.本发明实施例提供了一种mems结构雾化芯,所述mems结构雾化芯以单晶硅为主要基材,分为两部分主要结构,中间核心为加热结构,以沉积金属材料为加热部分;下层为支撑结构,以单晶硅为基材形成的框架结构,中间制备有阵列式微孔。
24.本发明实施例提供了一种mems结构雾化芯,包括:
25.支撑结构,所述支撑结构具有背对设置的第一表面和第二表面,所述第一表面设置有储油槽,所述第二表面设置有与所述储油槽相连通的导油孔,所述第二表面与第一表面背对设置;
26.电阻加热结构,所述电阻加热结构设置在所述支撑结构的第二表面,当所述电阻加热结构接入电源后,自所述导油孔输送的流体介质能够与所述电阻加热结构接触并被加热雾化。
27.在一些较为具体的实施方案中,所述支撑结构包括层叠设置的第一支撑结构和第二支撑结构,其中,所述第一支撑结构的导热系数大于第二支撑结构的导热系数,所述储油槽至少设置在所述第二支撑结构内,所述电阻加热结构设置在所述第一支撑结构上,所述导油孔同时穿过所述第一支撑结构和第二支撑结构。
28.在一些较为具体的实施方案中,所述第一支撑结构为氧化硅支撑结构,所述第一支撑结构的厚度为100nm-2000nm,所述第二支撑结构为单晶硅支撑结构,所述第二支撑结构的厚度为100μm-5000μm,所述储油槽底部的第二支撑结构的厚度为所述第一支撑结构厚度的2-5倍。
29.在一些较为具体的实施方案中,所述第一支撑结构由所述第二支撑结构的表层区域氧化形成。
30.在一些较为具体的实施方案中,所述支撑结构的第二表面设置有多个所述导油孔,多个所述导油孔呈阵列分布;
31.在一些较为具体的实施方案中,所述导油孔横截面形状包括圆形、椭圆形、方形、三角形、米字形中的任意一种或两种以上的组合。
32.在一些较为具体的实施方案中,多个所述导油孔的整体呈方形、s形或口子形分布。
33.在一些较为具体的实施方案中,所述导油孔的孔径为1μm-500μm,相邻导油孔之间的间隙为1μm-500μm。
34.在一些较为具体的实施方案中,所述支撑结构的第二表面具有第一区域和第二区域,所述电阻加热结构包括至少覆设在所述第一区域的图案化的导电材料层,所述导油孔至少设置在所述第二区域。
35.在一些较为具体的实施方案中,所述支撑结构的第二表面的第二区域还设置有多个导引槽,每一所述导引槽还与所述导油孔相连通,并且,所述导引槽的深度小于所述第一支撑结构厚度的1/2。
36.在一些较为具体的实施方案中,所述每个导引槽内还填充有导引层,所述导引层由金属颗粒和和非金属颗粒结合形成,其中,所述金属颗粒与电阻加热结构的材质相同,所述非金属颗粒与第二支撑结构的材质相同,且所述电阻加热结构还直接与所述导引层接触或连接。
37.在一些较为具体的实施方案中,所述导电材料层的厚度为100nm-500μm。
38.在一些较为具体的实施方案中,所述导电材料层的材质包括ni、cr、au、pt、mo、w中的任意一种单质或两种以上形成的合金。
39.本发明实施例还提供了所述的mems结构雾化芯的制备方法,其特征在于包括:
40.在支撑结构的第二表面形成图案化的导电材料层,并作为电阻加热结构;
41.在支撑结构的第一表面加工形成储油槽,以及,在所述储油槽的底部形成贯穿所述支撑结构的导油孔,且使自所述导油孔输送的流体介质能够与所述导电材料层接触。
42.在一些较为具体的实施方案中,所述的制备方法具体包括:
43.将所述支撑结构靠近第二表面的部分单晶硅氧化形成氧化硅,并以氧化形成的氧化硅作为第一支撑结构,以未被氧化的余留部分作为第二支撑结构;
44.在所述支撑结构的第一表面加工形成储油槽,且使所述储油槽的全部设置在所述第二支撑结构内,在所述储油槽的槽底部制作形成所述的导油孔,且使所述导油孔连续穿过第二支撑结构和第一支撑结构;
45.在所述第一支撑结构的表面形成电阻加热结构。
46.在一些较为具体的实施方案中,所述的制备方法具体包括:
47.先在所述第一支撑结构的表层加工形成多个导引槽,使所述导引槽与所述导油孔相连通,之后在所述导引槽内形成包含金属颗粒和和非金属颗粒的导引层,其中,所述金属颗粒与电阻加热结构的材质相同,所述非金属颗粒与第二支撑结构的材质相同;
48.在所述第一支撑结构的表面形成所述电阻加热结构,且使所述电阻加热结构直接与所述导引层接触或连接。
49.如下将结合附图以及具体实施案例对该技术方案、其实施过程及原理等作进一步的解释说明,除非特别说明的之外,本发明实施例所采用的氧化、沉积、刻蚀等工艺均可以是本领域技术人员已知的方式,在此不对其具体的工艺条件进行限定。
50.本发明提供的一种mems结构雾化芯结构主要分为两个部分,一部分是沉积了加热薄膜的结构,另一部分是包含阵列分布的导流孔的渗油结构。此发明不仅使得雾化芯可靠性更高,温度的一致性控制的更好,可以精准控制电阻范围;而且还可以精准控制渗油的速率和数量,结合半导体工艺,可以实现批量化、低成本的制造,避免陶瓷工艺烧结时带来的污染。
51.实施例1
52.请参阅图2和图3,一种mems结构雾化芯结构,包括依次层叠设置的第二支撑结构200、第一支撑结构100和电阻加热结构300,所述第二支撑结构200具有背对第一支撑结构100的第一表面,所述第一支撑结构100具有背对所述第二支撑结构200的第二表面,所述第二支撑结构200的第一表面设置有储油槽210,所述第二支撑结构200的第二表面设置有多个导油孔220,所述导流孔220连续贯穿第一支撑结构100和第二支撑结构200并与所述储油槽210相连通,所述电阻加热结构200设置在所述第一支撑结构100的第二表面,当所述电阻加热结构300接入电源后,自所述导油孔220输送的流体介质能够与所述电阻加热结构300接触并被加热雾化,所述流体介质包括烟油等。
53.在本实施例中,所述第一支撑结构100的导热系数大于第二支撑结构200的导热系数,所述储油槽210的全部设置在所述第二支撑结构200内,所述储油槽210具有沿趋向第一支撑结构100的方向逐渐变化的变径结构,所述储油槽210的径向或横向尺寸沿趋向第一支撑结构100的方向逐渐减小。
54.在本实施例中,所述第一支撑结构100为氧化硅支撑结构,所述第一支撑结构100的厚度为100nm-2000nm,所述第二支撑结构200为单晶硅支撑结构,所述第二支撑结构200的厚度为100μm-5000μm,所述储油槽210底部余留的第二支撑结构200的厚度为所述第一支撑结构100厚度的2-5倍。
55.在本实施例中,所述第一支撑结构100由所述第二支撑结构200的表层区域氧化形成。
56.在本实施例中,所述支撑结构的第二表面设置有多个所述导油孔220,多个所述导油孔220呈阵列分布,所述导油孔220横截面形状包括圆形、椭圆形、方形、三角形、米字形中的任意一种或两种以上的组合,多个所述导油孔220的整体呈方形、s形或口子形分布,所述导油孔220的孔径为1μm-500μm,相邻导油孔220之间的间隙为1μm-500μm。
57.在本实施例中,所述第一支撑结构100的第二表面具有第一区域和第二区域,所述电阻加热结构300包括覆设在所述第一区域的图案化的导电材料层,所述导油孔220设置在所述第二区域,其中,所述导电材料层是呈图形化设置的,所述导电材料层的图形结构可以如图3所示,其可以是圆环形、波浪形、平面螺旋形等。
58.在本实施例中,所述导电材料层的厚度为100nm-500μm,所述导电材料层的材质包括ni、cr、au、pt、mo、w中的任意一种单质或两种以上形成的合金。
59.在本实施例中,所述第一支撑结构100的第一表面还设置有焊盘400,所述焊盘400与所述电阻加热结构300电连接,所述焊盘400可以是金属焊盘等,所述焊盘的尺寸等参数在此不做具体的限定和说明。
60.请参阅图4和图5,一种mems结构雾化芯的制备方法,包括:
61.1)以单晶硅作为制作支撑结构的原料,并对单晶硅进行清洗;
62.2)采用氧化工艺将单晶硅表层的部分区域氧化形成氧化硅,并以氧化后形成的氧化硅部分作为第一支撑结构,以余留部分的单晶硅作为第二支撑结构;
63.3)在所述第一支撑结构的表面光刻形成电阻加热结构的形状;
64.4)在所述第一支撑结构的表面光刻后的区域沉积金属材料形成导电材料层,并以图形化的所述导电材料层作为电阻加热结构;
65.5)采用刻蚀等方式在所述第二支撑结构背对第一支撑结构的表面加工形成储油槽,且使所述储油槽与所述电阻加热结构背对设置,控制所述储油槽底部余留的第二支撑结构的厚度为所述第一支撑结构厚度的2-5倍;
66.6)采用刻蚀等方式在所述第一支撑结构表面未被电阻加热结构覆盖的区域加工形成多个导油孔,且使所述导油孔沿厚度方向连续贯穿所述第一支撑结构和第二支撑结构,并与所述储油槽相连通;
67.7)在所述第一支撑结构的表面制作焊盘,且将所述焊盘与电阻加热结构电连接。
68.实施例2
69.请参阅图6,本实施例中的一种mems结构雾化芯的结构与实施例1基本相同,不同之处在于:本实施例中的第一支撑结构100背对第二支撑结构200的第二表面还设置有多个导引槽,每一所述导引槽还至少与一导油孔220相连通,并且,所述导引槽的深度小于所述第一支撑结构100厚度的1/2,在每个导引槽内还填充有导引层500,所述导引层500由金属颗粒和和非金属颗粒结合形成,其中,所述金属颗粒与电阻加热结构300的材质相同,所述非金属颗粒与第二支撑结构200的材质相同,所述导引层500内的金属颗粒的体积比为50-75%,且所述电阻加热结构300还直接与所述导引层接触或连接,其中,所述金属颗粒和非金属颗粒的粒径均为微纳级,所述金属颗粒和非金属颗粒可以通过烧结、粘结以及压合层方式制作形成,在此不做具体的限定。
70.在本实施例中,可以利用导引层本身与电阻加热结构、氧化硅支撑结构具有很好的相容性的特点,从材料学角度来讲可以加强电阻加热结构与氧化硅支撑结构之间的结合力,另一方面还使导引层作为锚点,从力学角度加强两者之间的结合,克服电阻加热结构与氧化硅支撑结构之间因热膨胀系数差异而可能导致的翘曲、脱离等问题。此外,这些导引槽及导引层的存在,还可以在氧化硅支撑结构中形成立体加热路径(电阻加热结构与氧化硅支撑结构面接触,所呈现的是面加热,这些导引层深入氧化硅支撑结构内部,所以还增加了一个加热维度),进一步提高了加热效率和加热的均匀性。
71.应当理解,上述实施例仅为说明本发明的技术构思及特点,其目的在于让熟悉此项技术的人士能够了解本发明的内容并据以实施,并不能以此限制本发明的保护范围。凡根据本发明精神实质所作的等效变化或修饰,都应涵盖在本发明的保护范围之内。