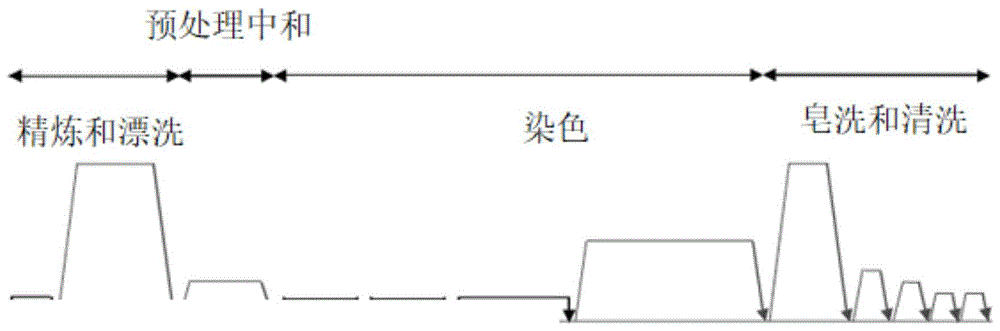
本发明属于ipc分类d06p1/38纺织品的用活性染料染色或印花技术或d01f11/00人造长丝或类似物在制造过程中的化学后处理技术,涉及纺织染色技术,尤其是一种纺织用活性染料及其环保无盐染色工艺。
背景技术:
:纺织印染行业,自从1856年,人类历史上发现第一个合成染料苯胺紫,以及,1954年英国申请了第一个procion活性染料专利,此后,1989年,万得(matex)开始生产megafixb,bes,ms,b-exf,bpsn,re等系列活性染料。活性染料中亲水基团一般为磺酸基团,在染液染料母体呈现负电荷,而在上色过程中,由于纤维素纤维在碱性条件下以纤维素负离子形式存在,因电荷相斥作用,致使染料难以向纤维内扩散。氯化钠等无机盐加至染液中将显著改变上述平衡,促使平衡反应向有利于阴离子染料上染纤维的方向移动。染液中加入氯化钠、硫酸钠后,钠离子的浓度增加,染液的离子强度提高,有利于染料从染液向纤维内扩散。此过程中无机盐担负了促染的作用。以加工棉、麻、化学纤维及其混纺产品、丝绸为主的印染、毛织染整及丝绸厂等排出的印染废水。纤维种类和加工工艺不同,印染废水的水量和水质也不同。其中,印染厂废水水量较大,每印染加工1t纺织品耗水100~200t,其中80%~90%成为废水排出。印染废水具有水量大、有机污染物含量高、碱性大、水质变化大等特点,属难处理的工业废水之一,废水中含有染料、浆料、助剂、油剂、酸碱、纤维杂质、砂类物质、无机盐等。染色废水。随纤维类型、染料种类与浓度、助剂和规模的不同,废水污染程度不同,主要含有有机染料和表面活性剂等,呈碱性cod与bod高而悬浮物少;印染废水含有未反应的染料、颜料或涂料,带有浓重的色泽,还有未反应的助剂,以及反应后的生成物和织物上的脱落物。更严重的还有致癌和致畸的有机化合物,具有毒性的重金属等。印染废水属工业废水中较难治理的一种。由于技术、经济等原因,目前大多数采用的生物-物理治理方法只能达到基本排放要求。虽然在色度上略有下降,但对有机物质只是分解成较小物质,对这些分解产物性质很难控制也很难掌握,无法保证对环境不产生危害。现行处理方法占地面积大,投资多,治理费用高昂,以致生产成本居高不下。据估计,废水治理后达到二级排放标准,则治理费用基本与城市自来水价格相当。如果要达到废水回用要求,治理费用则更高,故实际运作起来相当困难。染色过程中大量无机盐的使用,带来了巨大的环境污染的隐患:高盐废水处理难度大,普遍使用的生化处理法也很难处理高盐废水,细菌很难在高盐度下生存;排放水中的无机盐与土壤接触后,长期会造成土壤的板结,土壤会逐渐失去活性;若采用蒸发法回收无机盐,能耗巨大。为此,行业内多家单位针对低盐乃至无盐活性染色做了很多探索工作。相关改进技术有所公开,比如:浙江银河印染有限公司提出的中国专利申请201710586491.6涉及一种活性染料小浴比染特浅色的无盐染色方法。包括以下步骤:1)坯布前处理;2)活性染料染色;3)冰醋酸中和;4)煮洗处理;5)柔软处理;6)出缸脱水;7)后整理、烘干定型。宁波广源纺织品有限公司提出的中国专利申请201811287108.8涉及一种棉纤维坯布改性染色方法,包括:将棉纤维坯布煮炼后,加入酶、生物改性剂进行改性,得到改性的棉纤维坯布;进行水洗,加入浅色或中色活性染料进行染色,然后再水洗,软化,得到浅色或中色棉纤维染布;或加入深色活性染料进行染色,然后再水洗,加入固色剂进行固色,然后再水洗,软化,得到深色棉纤维染布。但该方法对于活性染料和染色设备具有较大局限性。中国专利申请200710147410.9提供一种棉纤维活性染料无盐染色工艺,包括对纤维素纤维的前处理、改性处理、染色、后处理等步骤。所述改性处理是将棉纤维用聚表氯醇与聚胺的共聚物经高温碱性条件下预处理洗净后,加入专用的匀染剂用活性染料染色,并可以在无盐、无碱或低碱条件下完成染色工序,提高染料上染与固着率。虽然其中采醇类溶剂对于棉纤维进行前处理,提高了棉纤维的可染性和润湿性,减少了棉纤维的煮炼和漂白的前处理工序,且可做到无盐上染;但此法引入了有机溶剂,带来了溶剂挥发废水处理等诸多问题。江苏金太阳纺织科技有限公司201410492816.0公开一种阳离子接枝改性无盐染色再生纤维素纤维的制备方法,以纤维素浆粕为主原料,并依次经过浸渍、压榨、粉碎、老成、黄化、溶解、过滤、脱泡、纺丝、后处理和烘干程序,在溶解工序或纺丝工序,添加纤维素阳离子改性剂,该纤维素阳离子改性剂为胺化试剂、季铵化试剂、氮杂环丁烷阳离子化合物、改性天然阳离子试剂中的一种或多种的混合物。其中采用了阳离子改性法预处理纤维,从而完成活性染料无盐染色,但此方法中的阳离子改性过程工艺较为复杂,且同传统工艺相比,整体的时间加长。还有很多专利中提到了纤维的阳离子改性,不同结构的改性剂,不同的改性工艺,但都或多或少存在工艺复杂、操作时间长、改性剂在棉纤维上分布不均、染不透等问题。中国专利申请201811042020.x公开了一种活性染料的无盐染色方法,包括如下步骤:s1、预处理,将待染织物浸轧包含多元羧酸的整理液中,所述包含多元羧酸的整理液包括:多元羧酸10-30wt%、次亚磷酸钠5-15wt%、余量为水,二浸二轧,浸轧完成后在90-100℃下预烘3-5min;s2、染色,将待染织物浸入到活性染料染液中,50-60℃下入染,以1-2℃/min的速度升温至70-80℃,加入1-15g/l的环糊精季铵盐,保温20-30min,再加入5-20g/l的纯碱,保温25-35min,水洗,皂洗,烘干。中国专利申请201811644200.5提供了一种织物的活性染料无盐染色方法,包括:s1、将纤维素纤维织物半成品浸轧染液,使织物的带液率为60%~85%;所述染液包括活性染料、碱性固色剂和分散均染剂,所述碱性固色剂为碳酸钠、碳酸氢钠、磷酸钠、磷酸氢二钠、偏硅酸钠和柠檬酸钠中的一种或几种,所述分散均染剂为分散剂nno、匀染剂mf和马丙共聚物中的一种或几种;s2、将所述带液率为60%~85%的织物控制其含水率为30%~5%;s3、将所述含水率为30%~5%的织物进行汽蒸固色,经过水洗处理,得到染色织物成品。大连理工大学博士学位论文《活性染料无盐染色的研究》记载,采用高取代度季铵型阳离子淀粉、氨基烯烃聚合物以及紫外线吸收剂bp-4接枝氨基烯烃聚合物作为阳离子化试剂对棉纤维进行物理改性,用于活性染料无盐竭染。具体包括,阳离子淀粉中的季铵基团和氨基烯烃聚合物在一定ph范围内形成的盐酸盐为起到促染作用的阳离子基团。阳离子化棉纤维用于活性染料染色不添加无机盐,固色率可达到或高于传统有盐染色的固色率,在解决活性染料染色中盐污染问题的同时提高了染料的利率。以高取代度阳离子淀粉作为棉纤维阳离子化试剂,采用浸轧-焙烘工艺对棉纤维进行阳离子化,考察了预处理工艺条件对染料固色率的影响;染色结果表明染料固色率与有盐染色相当,但匀染性差;通过超声波降低阳离子淀粉粘度,棉纤维染色匀染性提高,但提高固色率有局限。以高取代度酸降解阳离子淀粉作为棉纤维阳离子化试剂,分别采用浸润和浸轧、焙烘工艺进行预处理,用于活性染料无盐染色。考察了预处理条件对阳离子淀粉在棉纤维上吸附量及染料固色率的影响;探讨了促染机理,对比了有盐和无赫染色工艺中染料固色率、色光、色牢度、整理功能及渗透性;考察了降解阳离子淀粉循环使用情况。以聚乙烯胺和聚烯丙基胺作为棉纤维阳离子化试剂,分别采用浸轧一焙烘和浸润工艺对棉纤维进行改性,用于活性染料无盐染色,考察了浸润工艺预处理条件对聚乙烯胺在棉纤维上吸附量及染料固色率的影响;探讨了促染机理,对比了有盐和无赫染色工艺中染料圃色率、色光、色牢度、整理功能及渗透性;以聚乙烯胺为例,考察了它的循环使用情况。采用氯化亚砜为氯化试剂和溶剂,dmf为催化剂,对紫外线吸收剂bp一4进行了磺酰氯化反应,合成了相应的磺酰氯化合物;利用核磁共振氢谱、红外光谱和质谱表征了所合成的磺酰氯的结构,结构正确。利用氨基烯烃聚合物分子链上氨基的反应性及同一分子链上存在多个可反应基团的优点,采用氯磺化bp-4分别与聚乙烯胺和聚烯丙基胺反应得到了含二苯甲酮结构的试剂用于活性染料无盐染色,并考察了染色性能及纤维抗紫外整理功能。自从1956年活性染料的正式商品化以来,活性染料与棉纤维通过共价键结合,从根本上解决了染色纤维湿处理牢度差的问题。同时,因为活性染料具有色谱齐全,色泽鲜艳,应用工艺简便,适用性强,价格相对便宜等优点。目前,活性染料已成为棉纤维用染料中产量和产值最大的染料,但是活性染料在染色过程中需要加入大量的无机盐(30-loog/l),通过盐效应促使在水溶液中显负电性的活性染料克服电荷阻碍吸附到同样显负电性的棉纤维表面。无机盐的加入造成大量含盐废水的排放,这不仅是一种资源浪费,而且造成严重的环境污染。随着人们环保意识的不断增强,以及相关法律法规的日益完善,活性染料染色盐污染问题亟待解决。消除活性染料染色中的盐污染问题,主要从增加活性染料与棉纤维亲和力着手。但是现有的各种阳离子化试剂也都存在不足之处,如不能循环利用,对纤维本身的性能有影响,小分子试剂用量大,并且有的有毒副作用,高分子试剂不利于染料渗透,染色纤维色光不鲜艳等问题,因此,包括以上公开的文献在内,如附图1所示,已公开的无盐染色中预处理与染色工艺进程依次包括,精炼和漂洗、预处理中和、染色、皂洗和清洗。受到技术方案本身缺陷的制约,作为改进的技术,现有无盐染色尚不能实现大量工业化生产和应用。技术实现要素:本发明的目的是提供一种纺织用活性染料及其环保无盐染色工艺,在应用该活性染料的整个染色过程中无需添加无机盐辅助促染,可顺利完成染色操作,染色后纤维可以获得不低于传统活性染色纤维的色牢度及上染率;染色后纤维色牢度不低于传统活性染色纤维。本发明的目的将通过以下技术措施来实现:一种活性染料的制备,在活性染料中引入至少一种添加剂,必须在合成反应过程中加入,且需在主反应完成后,方可加入添加剂,并调整整个料液的ph值在5.5-7范围内,至反应完毕,喷干后获得新型活性染料;添加的添加剂包括非离子、阴离子(或阳离子)、两性离子表面活性剂、高分子分散螯合剂之类添加剂;添加的添加剂是单一的添加剂,或者是二种或二种以上添加剂混合物;添加剂优选聚丙烯酸盐、甜菜碱表面活性剂;添加剂优选反应型的阳离子化试剂;添加剂加入量为活性染料总质量用量的5–12%;在合成反应过程中加入,指添加剂在主反应过程完成后加入,搅拌10-30min,料液进入喷塔喷干;添加剂加入到活性染料中,在染色过程中,与活性染料、改性后的纤维及染色助剂共同作用,完成无盐染色。一种所述活性染料在无盐染色工艺,具体包括:纤维素纤维前处理工序、纤维素纤维预处理工序、分步加入所述活性染料工序、无盐染色工序和皂洗工序;其中:1)纤维素纤维前处理工序:先使用隔离剂,包括聚丙烯酸钠、马来酸丙烯酸钠、edta钠盐等常规水处理剂;根据水质的情况决定水处理剂的选择,选择的原则为通用原则。在15-40℃规定温度下浸渍处理1-20min;2)纤维素纤维预处理工序:再加入纤维预处理剂,目的是与纤维发生物理化学反应,通过物理间力及化学键沾附及反应在纤维表面;大大增加了可与活性染料进行反应的染座数量,利于染浴中活性染料的活性基团进攻染座,从而在无盐情况下完成染色。可以使用的预处理剂包括:两性表面活性剂、阳离子表面活性剂,高分子季铵盐类物质等;加入后,运行1-20min,在10min内分批加入烧碱;60-80度下反应20-40min;之后清水洗涤、酸洗,完成纤维预处理;3)分步加入活性染料工序:分步加入所述活性染料,运行1-30min;再加入无机碱或有机碱,如烧碱、碳酸钠、碳酸氢钠等无机碱及如甲醇钠,乙醇钾,叔丁醇钾等有机碱类物质;4)无盐染色工序:室温下加入隔离剂;运行5min后,在5-30min内分批加入所述活性染料,运行5min后,分批加入缓冲剂,优选mebufferebf,5min内加完,再次运行5min后加入纯碱,10-15min内加完;然后在50-80度内反应20-40min,升温梯度控制在1-3度。清水洗涤后酸洗,皂洗后完成染色。5)皂洗工序:95至98℃皂洗15-20分钟,然后进行洗水和烘干。本发明的优点和效果:在创制新型活性染料的基础上,结合纤维素纤维预处理,顺利完成活性染色。在染色过程中无需使用无机盐促染,降低染色废水中的盐度,可以提高染料利用率,降低废水中的tds产生量,节省染色时间和劳动力,降低染色成本,节省染色时间,是节能减排的环保染色工艺。固色率高、匀染性好,而且工艺简单,工业化实施容易。增加纤维与染料分子之间的亲和力,操作简单,效率提高,上染率达到90%以上,无盐染色中仅需加碱促染,染色废水可以直接重复使用(视情况补充新鲜水),实现废水减排。节约盐用量100%,节约能耗、水耗,织物的染色深度、均匀度较传统染色工艺更优。附图说明图1为现有传统预处理与染色工艺时间轴进程示意图。图2为本发明实施例1中预处理与染色工艺时间轴进程示意图。图3为本发明实施例1中a、b、c三种灰色染色配方染色后皂洗废水颜色图。图4为本发明实施例2中d、e、f三种卡其色染色配方染色后皂洗废水颜色图。图5为本发明实施例3中g、h、i三种棕色染色配方染色后皂洗废水颜色图。图6为本发明实施例4中j、k、l三种棕色染色配方染色后皂洗废水颜色图。图7为本发明实施例9中合成中加入添加剂的eco活性染料染色布样与以干拼混方式加入添加剂的活性染料染色布样对比图。具体实施方式本发明原理在于,研究表明,棉纤维阳离子化是一种比较直接有效增加染料与纤维亲和力,解决活性染料染色盐污染问题的途径之一。棉纤维阳离子化,即通过化学和物理的方法对棉纤维进行改性,使纤维表面带正电荷,通过正负电荷之间的静电作用增加纤维与染料的亲和力,达到促染的作用。由于棉纤维阳离子化的研究逐步深入,研究还发现其中多采用反应型的阳离子化试剂,包括:环氧类含氮化合物、一氯均三嗪型季铵盐化合物、氮杂环丁烷阳离子化合物等,阳离子化的棉纤维,可在少盐甚至无盐的条件下用于活性染料染色,竭染率和固色率较好,大大降低了盐污染问题。本发明中,活性染料制备时,在活性染料中引入至少一种添加剂,必须在合成反应过程中加入,并调整料液的ph在规定范围,至反应完毕,喷干后获得新型活性染料;添加的添加剂包括非离子、阴离子(或阳离子)、两性离子表面活性剂、高分子分散螯合剂之类添加剂;添加的添加剂是单一的添加剂,或者是二种或二种以上添加剂混合物;添加剂优选聚丙烯酸盐、甜菜碱表面活性剂;添加剂加入量为染料用量的5–12%。在合成反应过程中加入,指添加剂在主反应完成后,加入,搅拌10-30min,料液进入喷塔喷干。本发明中,活性染料制备时,在活性染料中引入的至少一种的添加剂,需在合成过程中加入,且需在主反应完成后,方可加入添加剂,并调整整个料液的ph值在5.5-7范围内,以促使添加剂中以适宜的离子性存在,并与染料分子或添加剂分子自身形成一定的分子内或分子间结合。本专利中eco活性染料中引入的添加剂,与活性染料在特定的环境中,通过分子间氢键、电性引力、分子内电荷转移等,形成了独特的无盐染色用活性染料。本发明中,如附图2所示,所述活性染料在无盐染色工艺中时间轴进程的简洁步骤依次包括,精炼、漂洗和前处理,以及染色、皂洗和清洗。本发明中,所述活性染料在无盐染色工艺具体包括:纤维素纤维前处理工序、纤维素纤维预处理工序、分步加入所述活性染料工序、无盐染色工序和皂洗工序;其中:1)棉纤维前处理工序:先使用隔离剂,包括聚丙烯酸钠、马来酸丙烯酸钠、edta钠盐等常规水处理剂;根据水质的情况决定水处理剂的选择,选择的原则为通用原则。在15-40℃规定温度下浸渍处理1-20min;2)纤维素纤维预处理工序:再加入纤维预处理剂,目的是与纤维发生物理化学反应,通过物理间力及化学键沾附及反应在纤维表面;大大增加了可与活性染料进行反应的染座数量,利于染浴中活性染料的活性基团进攻染座,从而在无盐情况下完成染色。可以使用的预处理剂包括:两性表面活性剂、阳离子表面活性剂,高分子季铵盐类物质等;加入后,运行1-20min,在10min内分批加入烧碱;60-80度下反应20-40min;之后清水洗涤、酸洗,完成纤维预处理;3)分步加入活性染料工序:分步加入所述活性染料,运行1-30min;再加入无机碱或有机碱,如烧碱、碳酸钠、碳酸氢钠等无机碱及如甲醇钠,乙醇钾,叔丁醇钾等有机碱类物质;4)无盐染色工序:室温下加入隔离剂;运行5min后,在5-30min内分批加入所述活性染料,运行5min后,分批加入缓冲剂,优选mebufferebf,5min内加完,再次运行5min后加入纯碱,10-15min内加完;然后在50-80度内反应20-40min,升温梯度控制在1-3度。清水洗涤后酸洗,皂洗后完成染色。5)皂洗工序:95至98℃皂洗15-20分钟,然后进行洗水和烘干。本发明中,只有在合成过程中加入添加剂,并经前述特殊处理后,才能获得本发明活性染料的突出特有性能;而以其他方式的简单干粉拼混,无法得到合格的无盐染料。可以获得优异的应用效果;而简单干拼得到无盐染料,无法获得满意的应用效果。所述活性染料在上染纤维素纤维及含有棉纤维的混纺纤维时,染色过程中无需无机盐促染。无盐染色工艺适用于可用传统活性染料上染的各种纤维及相应混纺纤维。将图1将图2对比,整个无盐染色过程相比传统染色节省时间120min;在设备能力不变的情况下,生产量可提升25%;染色成本可以降低7%。下面结合附图和实施例对本发明作进一步说明。实施例1:作为对比的三种灰色活性染料配方分别为:a:megafix黄eco-ye0.70%,megafix红eco-rb0.50%,megafix蓝eco-bl0.80%,总剂量2.00%,60℃×30min,强度100%,mebufferebf0.8g/l。b:活性黄1451.00%,活性红1960.64%,活性蓝2202.50%,总剂量4.14%,60℃×60min,强度93.4%,na2so480g/l,na2co320g/l。c:活性黄1450.92%,活性红1950.65%,活性蓝2211.81%,总剂量3.38%,60℃×60min,强度97.4%,na2so480g/l,na2co320g/l。前述中,a、b、c三种灰色染色配方染色后皂洗废水颜色如附图3所示。实施例2:作为对比的三种卡其色活性染料配方分别为:d:megafix黄eco-ye1.40%,megafix红eco-rb0.15%,megafix蓝eco-bl0.45%,总剂量2.00%,60℃×30min,强度100%,mebufferebf0.8g/l。e:活性黄1451.74%,活性红1950.26%,活性蓝2201.54%,总剂量3.54%,60℃×60min,强度105.7%,na2so480g/l,na2co320g/l。f:活性黄1451.60%,活性红1950.25%,活性蓝2211.02%,总剂量2.87%,60℃×60min,强度95.4%,na2so480g/l,na2co320g/l。前述中,d、e、f三种卡其色染色配方染色后皂洗废水颜色如附图4所示。实施例3:作为对比的三种棕色活性染料配方分别为:g:megafix黄eco-ye1.10%,megafix红eco-rb0.50%,megafix蓝eco-bl0.40%,总剂量2.00%,60℃×30min,强度100%,mebufferebf0.8g/l。h:活性黄1451.28%,活性红1950.57%,活性蓝2201.32%,总剂量3.17%,60℃×60min,强度104.2%,na2so480g/l,na2co320g/l。i:活性黄1451.20%,活性红1950.57%,活性蓝2210.88%,总剂量2.65%,60℃×60min,强度97.5%,na2so480g/l,na2co320g/l。前述中,g、h、i三种棕色染色配方染色后皂洗废水颜色如附图5所示。实施例4:作为对比的三种深红色活性染料配方分别为:j:megafix黄eco-ye0.60%,megafix红eco-rb1.25%,megafix蓝eco-bl0.15%,总剂量2.00%,60℃×30min,强度100%,mebufferebf0.8g/l。k:活性黄1450.64%,活性红1951.10%,活性蓝2200.45%,总剂量2.19%,60℃×60min,强度104.2%,na2so480g/l,na2co320g/l。l:活性黄1450.70%,活性红1951.24%,活性蓝2210.35%,总剂量2.29%,60℃×60min,强度97.5%,na2so480g/l,na2co320g/l。前述中,j、k、l三种深红色染色配方染色后皂洗废水颜色如附图6所示。本发明实施例1、2、3、4中,染色时间节省30min;染料用量节省明显,不同颜色染料节省量不同;染料利用率高;染色纤维色牢度不低于传统活性染色的色牢度;无盐染色可采用传统染色设备上染,无需增加新设备;各道洗水量大大减少;减少了水洗次数,染色周期缩短;盐碱用量的减少,降低了工人的劳动强度。实施例5:在无盐染色工艺的稳健性实验中:选取深灰色活性染料,在不同的染色温度下、不同的浴比下及不同染色时间,对比评估无盐染色工艺的结果重现性。实施例6:在红外线染色机、油浴染色机、震荡染色机三种不同类型的染色设备条件下,不同的操作人员连续3天重复染色,染色结果如下表:前述中,实验结果显示,无盐染色工艺,稳定可靠,结果重现性高,对于染色设备、操作人员无特殊要求。实施例7:某工厂试应用例:选用无盐染料中的三个颜色:深红、黑及绿松石,在某工厂对棉纤维进行无盐活性染色,同期对比了相同颜色的传统活性染色。下表中的百分数为与传统工艺对比的节省比例。颜色时间%用水量%用电量%助剂量%co2排放%深红1116212117黑1220424625绿松石35163915137实施例8:无盐染色东南亚某工厂大试成本测算:染色机:hisakaworksnozzer110mm;面料:100%棉,320kg;浴比:1:5;染料:ecobk0017veryblack;metreateco-d(xg/l)及氢氧化钠(yg/l),预处理棉纤维,70度下30min,之后水洗及酸洗;染色配方:megafix红eco-rr0.302%;megafix蓝eco-bl0.238%;megafix黑eco-gb3.725%;隔离剂1.0%;ebf0.8%;碳酸钠20%。实施例9:对比两种不同方法制备的无盐染色用活性染料,用相同的染色配方和无盐染色工艺上染棉纤维:染色配方:0.3%黄eco-yr,3%红eco-rr,0.3%蓝eco-bn;0.8g/l的mebuffertmebf,meclearhm0.5g/l,20g/l的纯碱,染色时间为60度*30min。如附图7所示。反应过程中引入添加剂得到的eco活性染料与添加剂与活性染料干粉干拼得到的用于无盐染色用的活性染料相比,后者干拼法无盐染色用活性染料即使采用本专利所述无盐染色工艺,也不能得到同前者相关的无盐染色效果;而且,染料在纤维表面上色不均匀,存在色差及色浅问题。以上本发明实施例中,与传统活性染料对比染色实验中,均采用了红黄蓝三原色,利用不同的配比,获得了灰色、卡其色、棕色及深红色。染色时,在对棉纤维预处理改性后,染色中未加元明粉和碳酸钠,仅加入了一款无盐染色助剂ebf,顺利完成染色,染色后纤维色牢度不低于传统染色牢度。本发明实施例中,1)染色过程中,对纤维进行了预处理改性,所以染色过程中无需添加无机盐,避免了高盐废水的产生,降低废水中的tds值,减轻对废水生化处理细菌伤害。可以获得不低于传统有盐染色的效果,棉纤维的色牢度均等同或优于传统法;同时,避免了传统工艺中无机盐搬运、溶解等操作,降低了现场工人的劳动强度,提高了劳动效率。2)染色过程中,因棉纤维的改性处理,大大提高了染料的上染率,降低了染料的损耗;固色率不受影响;同时皂洗的强度降低了,减少了皂洗次数,染色后纤维易于洗涤,降低了用水量也减少了废水量;同时,废水中氯离子的含量也大为降低。3)染色过程中,新型活性染料水解率低于传统活性染色工艺,且整个染色工艺的周期大为缩短。节约染色时间,增加生产率。4)无盐染色工艺的整体成本低于传统活性染色工艺。当前第1页12