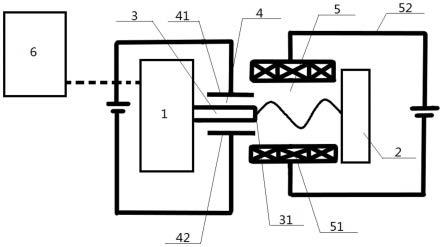
1.本发明涉及一种纳米纤维薄膜的制取技术,属于纳米纤维薄膜材料制备领域,尤其涉及一种外加磁场辅助微流控制取纳米纤维薄膜的系统及使用方法。
背景技术:2.目前,制备纳米纤维最简单、有效的方法是静电纺丝法,如运用聚丙烯腈原料制取纺丝液,再对纺丝液进行静电纺丝以制备纳米纤维,获取的纳米纤维具有良好的蓬松性、导电性能、高强度、耐腐蚀、耐高温与稳定性等特点。
3.但利用静电纺丝技术制备的纳米纤维的有序度、均匀度都不高,普遍呈现为直径很粗且不均匀,会降低该种纳米纤维构成的纳米纤维薄膜的性能,导致纳米纤维薄膜的结构与性能无法达到生物工程、超级电容器等领域的应用要求,大大限制了其应用范围。
4.公开该背景技术部分的信息仅仅旨在增加对本技术的总体背景的理解,而不应当被视为承认或以任何形式暗示该信息构成已为本领域一般技术人员所公知的现有技术。
技术实现要素:5.本发明的目的是克服现有技术中存在的有序度、均匀度均不高的缺陷与问题,提供一种有序度、均匀度均较高的外加磁场辅助微流控制取纳米纤维薄膜的系统及使用方法。
6.为实现以上目的,本发明的技术解决方案是:一种外加磁场辅助微流控制取纳米纤维薄膜的系统,包括微流挤出泵与接收滚筒,所述微流挤出泵的泵内腔中设置有纺丝液,微流挤出泵的侧面设置有与泵内腔相连通的挤出喷嘴,该挤出喷嘴的出液方向与接收滚筒正对设置;所述挤出喷嘴的上、下方对应的设置有上极板、下极板,上极板、下极板构成一个平板电容,且上极板的背部经同一个电路与下极板的背面进行电连接,所述挤出喷嘴上的出液口与接收滚筒之间设置有控制磁场。
7.所述控制磁场位于励磁线圈的内部,该励磁线圈接在励磁电路中,且励磁线圈的左端靠近出液口设置,励磁线圈的右端靠近接收滚筒设置。
8.所述微流挤出泵的驱动机构为步进平移电机,该微流挤出泵的推进速率为0.25ml/h—0.35ml/h;所述接收滚筒的驱动机构为旋转电机,该旋转电机的转速为350r/min—450r/min。
9.所述取纳米纤维薄膜的系统还包括超声波发生器,该超声波发生器的下游为微流挤出泵的泵内腔。
10.一种上述外加磁场辅助微流控制取纳米纤维薄膜的系统的使用方法,包括以下步骤:先将纺丝液置于微流挤出泵的泵内腔中,再导通平板电容、控制磁场所在的电路,然后推进微流挤出泵,以将纺丝液从挤出喷嘴的出液口射出,射出的纺丝液穿经控制磁场后落在转动的接收滚筒上并转为纺丝,随后,纺丝液持续射出,转动的接收滚筒持续对射出的纺
丝液进行牵引拉伸,接收滚筒上收集的纺丝持续增多以构成纤维薄膜,直至泵内腔中的纺丝液全部射出之后,再对接收滚筒上的纤维薄膜进行收集,然后对收集的纤维薄膜进行真空干燥以获得纳米纤维薄膜。
11.所述纺丝液的获得工艺为:先将聚丙烯腈作为溶质添加进分析纯态的nn-二甲基甲酰胺溶液中以获得初步混合液,再搅拌初步混合液以获得纺丝液,该纺丝液中聚丙烯腈的质量百分浓度为16%—20%。
12.所述搅拌初步混合液以获得纺丝液是指:将初步混合液放入集热式磁力搅拌器中进行加热,并搅拌,加热的设定温度为80℃—90℃,搅拌时间为2h—3 h,直至聚丙烯腈完全溶解之后,获得纺丝液。
13.所述取纳米纤维薄膜的系统还包括超声波发生器,该超声波发生器的下游为微流挤出泵的泵内腔;所述纺丝液在进入微流挤出泵的泵内腔之前,先将纺丝液倒入超声波发生器的容器中密封静置11小时—13小时,再对该纺丝液进行超声振动加工,然后将超声振动加工之后的纺丝液置于微流挤出泵的泵内腔中。
14.所述超声振动加工的频率范围为20—22khz,功率范围为900—1200w。
15.所述纺丝液在穿经控制磁场的过程中,纺丝液的运动轨迹为螺旋运动。
16.与现有技术相比,本发明的有益效果为:1、本发明一种外加磁场辅助微流控制取纳米纤维薄膜的系统及使用方法中,包括微流挤出泵、接收滚筒、平板电容与控制磁场,微流挤出泵的泵内腔中设置有纺丝液,应用时,在微流挤出泵的推力作用下,纺丝液的液滴被推至出液口处并射出,此过程为纺丝液运用层流效应,使具有一定粘度的纺丝液在自身重力、粘弹力及微流挤出泵推力的共同作用下,落在接收滚筒上以形成纺丝,同时,接收滚筒开始与纺丝液建立牵引关系,后续随着纺丝液的持续射出,纺丝液会持续受到自身重力、粘弹力、微流挤出泵推力、接收滚筒牵引力的共同作用,持续将射出的纺丝液拉伸成丝,在这个基础之上,由于平板电容使得泵内腔中设置的纺丝液带电,因而从出液口射出的为带电液滴,此时,在接收滚筒的牵引力、控制磁场的磁场力的共同作用下,带电液滴组成的射流的运动轨迹便包括加速直线运动、螺旋运动这两个部分,其中,在出液口处,微流泵的挤出力大于液滴的表面张力、粘弹力,液滴在此过程中做加速直线运动;而在挤出之后,控制磁场中的磁力线绝大部分都是平行于喷丝头的(忽略其他少量不平行于出液口的磁力线),通过左手定则可知,控制磁场中的带电液滴受到的洛伦兹力指向圆心,额外多了一个指向圆心的洛伦兹力,该洛伦兹力拉着带电液滴作圆周运动,不仅能使射流做螺旋运动,而且能降低射流的摆动幅度,缩小螺旋运动的运动半径,既能使液滴在螺旋运动过程中减小了能量的消耗,在其他条件不变的情况下,因能量总和不变,圆周运动消耗的能量减小,导致用于拉伸细化的能量增多,以获得更细的纤维,获得更强的有序度与均匀度,又能使得接收滚筒的能量多用在牵引上,而不用考虑因摆动幅度过大而乱飞的纳米纤维,有利于纳米纤维的细化,获得更有序、均匀的纳米纤维,而纤维的有序度、均匀度的提升更利于最终获取的纳米纤维薄膜的有序度、均匀度的确保。因此,本发明不仅能够获得更细的纳米纤维,而且能获得有序度、均匀度均较高的纳米纤维薄膜。
17.2、本发明一种外加磁场辅助微流控制取纳米纤维薄膜的系统及使用方法中,增设
有超声波发生器,该超声波发生器对纺丝液进行超声振动加工,再将加工后的纺丝液输送给下游的微流挤出泵,纺丝液在进行超声振动加工之前,纺丝液内的大分子链是杂乱无章的,粘度较大,不利于后续纺丝的进行,而当经历超声振动加工之后,大分子链发生了解缠,纺丝液中微小粒子的振动速度、加速度、振幅都有相应程度的增加,从而加强了分子链的蠕动,大幅降低了纺丝液的粘度值,随着粘度值的降低,纺丝液的流动性能得到了明显的改善,接收滚筒中用于克服粘滞力的牵引力就越少,使得用于拉伸纤维的牵引力就会更多,更有利于纤维细化,此外,当解缠后的带电液滴进入磁场时,受到洛伦兹力的作用会重新排序,使得构建的新的大分子链在内部结构上的取向更加一致,从而促进纤维的细化和均匀度,提高了所制纤维的有序度,使其更加密集有序,也就利于最终获得的纳米纤维薄膜的有序度、均匀度的提升。因此,本发明利用超声振动、磁场的组合工艺,以提升纳米纤维薄膜的有序度与均匀度。
18.3、本发明一种外加磁场辅助微流控制取纳米纤维薄膜的系统及使用方法中,超声振动加工的频率范围为20—22khz,功率范围为900—1200w,应用时,频率的限定更利于粘度的降低,尤其当频率为21khz时,粘度的降低效果更佳,更利于获得更有序、更均匀的纳米纤维薄膜。因此,本发明对纺丝液的粘度降低效果较好。
附图说明
19.图1是本发明的结构示意图。
20.图2是本发明的实施例1中获取的纳米纤维的sem图。
21.图3是图2的局部放大图。
22.图4是本发明的实施例1中用作对比的纳米纤维的sem图。
23.图5是图4的局部放大图。
24.图6是本发明中解链前,在磁场作用下纺丝液分子链的示意图。
25.图7是本发明中解链后,在磁场作用下纺丝液分子链的示意图。
26.图8是本发明中实施例3中超声振动、纺丝液粘度的关联示意图。
27.图9是本发明中实施例3中超声振动、纺丝液粘度降低率的关联示意图。
28.图中:微流挤出泵1、接收滚筒2、挤出喷嘴3、出液口31、平板电容4、上极板41、下极板42、控制磁场5、励磁线圈51、励磁电路52、超声波发生器6。
具体实施方式
29.以下结合附图说明和具体实施方式对本发明作进一步详细的说明。
30.参见图1—图9,一种外加磁场辅助微流控制取纳米纤维薄膜的系统,包括微流挤出泵1与接收滚筒2,所述微流挤出泵1的泵内腔中设置有纺丝液,微流挤出泵1的侧面设置有与泵内腔相连通的挤出喷嘴3,该挤出喷嘴3的出液方向与接收滚筒2正对设置;所述挤出喷嘴3的上、下方对应的设置有上极板41、下极板42,上极板41、下极板42构成一个平板电容4,且上极板41的背部经同一个电路与下极板42的背面进行电连接,所述挤出喷嘴3上的出液口31与接收滚筒2之间设置有控制磁场5。
31.所述控制磁场5位于励磁线圈51的内部,该励磁线圈51接在励磁电路52中,且励磁线圈51的左端靠近出液口31设置,励磁线圈51的右端靠近接收滚筒2设置。
32.所述微流挤出泵1的驱动机构为步进平移电机,该微流挤出泵1的推进速率为0.25ml/h—0.35ml/h;所述接收滚筒2的驱动机构为旋转电机,该旋转电机的转速为350r/min—450r/min。
33.所述取纳米纤维薄膜的系统还包括超声波发生器6,该超声波发生器6的下游为微流挤出泵1的泵内腔。
34.一种上述外加磁场辅助微流控制取纳米纤维薄膜的系统的使用方法,包括以下步骤:先将纺丝液置于微流挤出泵1的泵内腔中,再导通平板电容4、控制磁场5所在的电路,然后推进微流挤出泵1,以将纺丝液从挤出喷嘴3的出液口31射出,射出的纺丝液穿经控制磁场5后落在转动的接收滚筒2上并转为纺丝,随后,纺丝液持续射出,转动的接收滚筒2持续对射出的纺丝液进行牵引拉伸,接收滚筒2上收集的纺丝持续增多以构成纤维薄膜,直至泵内腔中的纺丝液全部射出之后,再对接收滚筒2上的纤维薄膜进行收集,然后对收集的纤维薄膜进行真空干燥以获得纳米纤维薄膜。
35.所述纺丝液的获得工艺为:先将聚丙烯腈作为溶质添加进分析纯态的nn-二甲基甲酰胺溶液中以获得初步混合液,再搅拌初步混合液以获得纺丝液,该纺丝液中聚丙烯腈的质量百分浓度为16%—20%。
36.所述搅拌初步混合液以获得纺丝液是指:将初步混合液放入集热式磁力搅拌器中进行加热,并搅拌,加热的设定温度为80℃—90℃,搅拌时间为2h—3 h,直至聚丙烯腈完全溶解之后,获得纺丝液。
37.所述取纳米纤维薄膜的系统还包括超声波发生器6,该超声波发生器6的下游为微流挤出泵1的泵内腔;所述纺丝液在进入微流挤出泵1的泵内腔之前,先将纺丝液倒入超声波发生器6的容器中密封静置11小时—13小时,再对该纺丝液进行超声振动加工,然后将超声振动加工之后的纺丝液置于微流挤出泵1的泵内腔中。
38.所述超声振动加工的频率范围为20—22khz,功率范围为900—1200w。
39.所述纺丝液在穿经控制磁场5的过程中,纺丝液的运动轨迹为螺旋运动。
40.本发明的原理说明如下:本发明中将初步混合液放入集热式磁力搅拌器中进行加热,并搅拌,以使聚丙烯腈完全溶解的目测标准为完全看不到聚丙烯腈晶体颗粒,且溶液跟水一样的清澈,不会挂丝。
41.本发明中若获得纺丝液是通过将初步混合液放入集热式磁力搅拌器中进行加热,并搅拌而得,则后续在进行超声振动加工之前,必须静置,其目的在于静置之后才能保证前面温度和磁力搅拌对溶液的影响最小。
42.本发明中对收集的纤维薄膜进行真空干燥以获得纳米纤维薄膜的原因在于:处于负压状态下隔绝空气,能使纤维薄膜在干燥过程中避免氧化,从而更好的保持原有的特性,干燥时间优选为8h-24h。
43.实施例1:参见图1,一种外加磁场辅助微流控制取纳米纤维薄膜的系统,包括微流挤出泵1与接收滚筒2,所述微流挤出泵1的泵内腔中设置有纺丝液,微流挤出泵1的侧面设置有与泵内腔相连通的挤出喷嘴3,该挤出喷嘴3的出液方向与接收滚筒2正对设置;所述挤出喷嘴3
的上、下方对应的设置有上极板41、下极板42,上极板41、下极板42构成一个平板电容4,且上极板41的背部经同一个电路与下极板42的背面进行电连接,所述挤出喷嘴3上的出液口31与接收滚筒2之间设置有控制磁场5。优选控制磁场5位于励磁线圈51的内部,该励磁线圈51接在励磁电路52中,且励磁线圈51的左端靠近出液口31设置,励磁线圈51的右端靠近接收滚筒2设置。
44.一种上述外加磁场辅助微流控制取纳米纤维薄膜的系统的使用方法,包括以下步骤:先将纺丝液置于微流挤出泵1的泵内腔中,再导通平板电容4、控制磁场5所在的电路,然后推进微流挤出泵1,以将纺丝液从挤出喷嘴3的出液口31射出,射出的纺丝液穿经控制磁场5后落在转动的接收滚筒2上并转为纺丝,随后,纺丝液持续射出,转动的接收滚筒2持续对射出的纺丝液进行牵引拉伸,接收滚筒2上收集的纺丝持续增多以构成纤维薄膜,直至泵内腔中的纺丝液全部射出之后,再对接收滚筒2上的纤维薄膜进行收集,然后对收集的纤维薄膜进行真空干燥以获得纳米纤维薄膜。优选纺丝液的获得工艺为:先将聚丙烯腈作为溶质添加进分析纯态的nn-二甲基甲酰胺溶液中以获得初步混合液,再搅拌初步混合液以获得纺丝液,该纺丝液中聚丙烯腈的质量百分浓度为16%—20。
45.由图4、图5可见,现有技术中在未加磁场控制的情况下,所获得纳米纤维的表面有很多沟壑,形成这种缺陷的原因是在拉伸成丝的过程中,纺丝液的溶剂挥发不及时,导致部分溶剂在纤维表面的残留。
46.由图2、图3可见,本设计所制取的纳米纤维表面更加光滑,且纤维细化程度更好,纤维有序且均匀。
47.实施例2:基本内容同实施例1,不同之处在于:结构上:所述取纳米纤维薄膜的系统还包括超声波发生器6,该超声波发生器6的下游为微流挤出泵1的泵内腔。
48.方法上:纺丝液在进入微流挤出泵1的泵内腔之前,先将纺丝液倒入超声波发生器6的容器中密封静置11小时—13小时,再对该纺丝液进行超声振动加工,然后将超声振动加工之后的纺丝液置于微流挤出泵1的泵内腔中。
49.参见图6,可见在解链之前,纺丝液的液体通过磁场时,分子链呈现为杂乱无章,再参见图7,可见在解链之后,纺丝液的液体通过磁场时,分子链呈现为更一致的取向排列,进而提高了所制纤维的有序度,更加密集有序。该制备方法制取的pan/dmf纤维的平均直径为0.59
µ
m,90%—99%的纤维的直径分布在0.5—0.68
µ
m之间,纤维平均直径减小率高达47%,有效的细化了纤维薄膜,且大幅提高了纤维的有序度与均匀度。
50.实施例3:基本内容同实施例2,不同之处在于:所述超声振动加工的频率范围为20—22khz,功率范围为900—1200w。参见图8与图9,图中的1000w、1200w、1400w分别代表超声波发生器的振动功率。
51.由图8、图9可知,当超声振动的频率为 21khz 时,三种功率条件下,纺丝液粘度的降低率都随时间的增长而增加,而且增长速率相差不大,因此可以认为,当频率足够大时,功率对粘度降低率的影响较小。由此分析可知,振动频率是影响纺丝液粘度降低率的主要因素,而功率对纺丝液粘度降低率起一定的辅助作用。
52.以上所述仅为本发明的较佳实施方式,本发明的保护范围并不以上述实施方式为限,但凡本领域普通技术人员根据本发明所揭示内容所作的等效修饰或变化,皆应纳入权利要求书中记载的保护范围内。