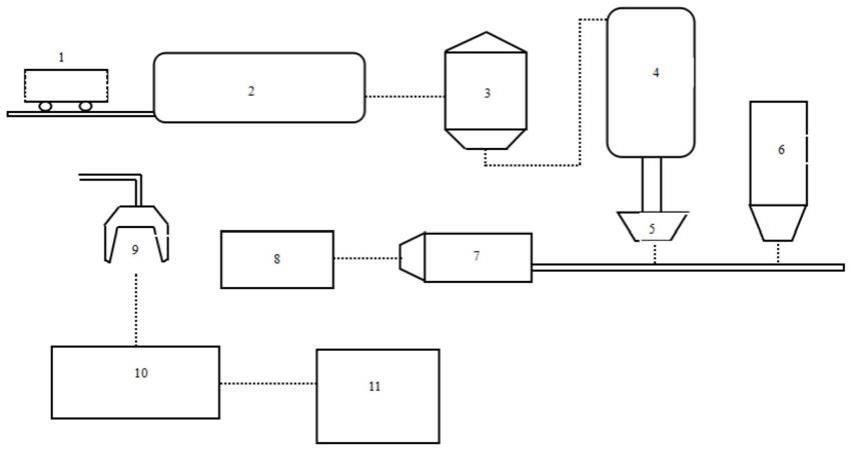
[0001]
本实用新型涉及一种利用钢铁企业脱硫灰制备墙材的装置,特别是一种利用钢铁企业竖炉球团脱硫灰和烧结脱硫灰的湿法脱硫产物制备墙材的装置。
背景技术:[0002]
我国是钢铁大国,钢铁企业遍布全国各省市。对于一个中等规模的钢铁企业来说,仅是烧结脱硫灰及竖炉球团脱硫灰年产量即可达到近10万吨,但是由于这些脱硫灰中掺有一定的灰类杂质,并无法像电厂脱硫灰一样有好的销路,基本是在渣场堆存,污染环境。但是湿法脱硫产生的脱硫石膏的性能基本可以与二水天然石膏持平,因此,若选用合适的烘干与煅烧设备,脱硫石膏完全可以达到建筑石膏粉的要求,并可直接用于水泥、建筑制品,如果进一步深加工开发石膏板、石膏砌块或其他新型建筑材料则会带来更高的附加值和效益。
[0003]
若将脱硫灰应用起来,须将其处理成为半个结晶水产物。因此脱硫灰脱结晶水的处理工艺是脱硫灰利用的关键环节,如何实现高效、环保、经济的脱硫灰脱结晶水处理工艺成为值得关注的问题。
[0004]
半水石膏有α型和β型两种,α半水石膏是由致密的、粗大的、完整的晶体组成,晶体形态多呈柱状、棒状、粒状,也有呈针状和纤维形态;β半水石膏则由疏松的、细小的、不规则的晶粒组成,晶粒形态多呈鳞片状、薄板状晶型。这些特征正是由于它们的形成条件不同所产生的,像β半水石膏在过热的非饱和蒸汽下快速脱水形成,所以晶体疏松、细小,有着非常发育的内表面;而α半水石膏则在有液态水的环境中脱水、重结晶形成,具备形成粗大致密晶体的条件。因此将脱硫灰制备成α半水石膏即可应用在高品质墙材中,具有装备化自动化水平高,空间占地小,系统投资低,烟尘有组织排放等优点。从而为脱硫灰处理利用提供更好的预处理工艺装备,实现现有脱硫灰处理工艺技术装备的升级。
技术实现要素:[0005]
为了实现脱硫灰高效、环保、经济处理利用,本实用新型采用蒸养工艺对脱硫灰进行处理,在高温液态水同时存在的条件下,二水脱硫石膏反应脱掉一个半结晶水,是该处理工艺的主要环节,蒸养系统是该处理过程的主要装备。利用蒸压釜对脱硫灰进行蒸养处理,饱和蒸汽可以直接来自厂区其他生产环节,节能高效;蒸养设备对厂房要求小,大幅度降低了土建费用;生产过程产生的尘汽集中收集有组织排放,降低了烟气处理系统投资,并实现了清洁生产。总之该处理系统自动化程度高,处理效率高,空间占地小,系统投资低,环境排放达标等优点,能够满足脱硫灰处理的环保排放和经济性要求。优选,干燥后的石膏板为墙材。
[0006]
为解决上述技术问题,本实用新型提供一种利用钢铁企业脱硫灰制备墙材的装置,所述脱硫灰制备墙材的装置包括:进料系统(1)、蒸养系统(2)、粉磨系统(3)、熟石膏料仓(4)、给料系统(5)、给水系统(6)、混料系统(7)、成型系统(8)、脱模系统(9)、干燥系统
(10)和成品仓(11);进料系统(1)连接蒸养系统(2),用于将进料系统(1)中的脱硫灰送入蒸养系统(2)中进行蒸养;蒸养系统(2)连接粉磨系统(3),用于将蒸养得到的半水脱硫石膏送入粉磨系统(3)进行粉磨;粉磨系统(3)连接熟石膏料仓(4),用于将粉磨得到的半水脱硫石膏粉送入熟石膏料仓(4);熟石膏料仓(4)连接给料系统(5),用于将熟石膏料仓(4)中的半水脱硫石膏粉送入给料系统(5);给料系统(5)与给水系统(6)分别连接混料系统(7),用于将半水脱硫石膏粉和水送入到混料系统 (7)进行混料搅拌,混料系统(7)连接成型系统(8),用于将搅拌得到的石膏料浆进行成型;脱模系统(9)与成型系统(8)可操作的连接,用于将成型系统 (8)成型后的石膏板脱模;脱模系统(9)与干燥系统(10)可操作的连接,用于将脱模后的石膏板送入干燥系统(10)进行干燥;干燥系统(10)连接成品仓 (11),用于将干燥后的石膏板送入成品仓(11)。
[0007]
其中,所述进料系统(1)包括转运轨道(12)、转运料车(13)、驱动装置 (14)和料盘(15);装有脱硫灰的料盘(15)设置在转运料车(13)上,转运料车(13设置在转运轨道(12),并与驱动装置(14)驱动连接;转运轨道(12) 连接进料系统(1)和蒸养系统(2),用于通过转运轨道(12)将脱硫灰运输入蒸养系统(2)中脱结晶水以得到半水脱硫石膏。
[0008]
其中,蒸养系统(2)包括蒸压釜(16)、蒸汽通入系统(17)和排压系统(18),蒸汽通入系统(17)设置在蒸压釜(16)前端,用于将蒸汽引入工作中的蒸压釜 (16)中,排压系统(18)设置在蒸压釜(16)上部,用于当蒸压釜(16)内蒸汽压力超过工作压力负荷时自动开启,排压至安全压力范围内。
[0009]
其中,粉磨系统(3)包括粉磨系统给料机(19)、第一电机(20)、粉磨机 (21)、出料口(22);第一电机(20)分别可驱动的连接粉磨系统给料机(19) 与粉磨机(21),用于为粉磨系统给料机(19)和粉磨机(21)提供动力;粉磨系统给料机(19)设置在粉磨系统(3)上端,用于给粉磨机(21)供料,出料口(22)设置在粉磨机(21)的下端,用于将粉磨成粉料的半水脱硫石膏粉经出料口(22)送入熟石膏料仓(4)。
[0010]
其中,给料系统(5)包括给料系统给料机(23)和皮带秤(24),给料系统给料机(23)设置在皮带秤(24)上方,用于将熟石膏仓(4)输出的半水脱硫石膏粉经由给料机(23)布料于皮带秤(24)上;皮带秤(24)连接混料系统 (7),用于将皮带秤(24)称量过的半水脱硫石膏粉送入混料系统(7)中。
[0011]
其中,给水系统(6)包括拌合水称量系统(25)和拌合水输送系统(26);拌合水称量系统(25)连接拌合水输送系统(26),拌合水输送系统(26)连接混料系统(7),用于将通过拌合水称量系统(25)称量的水经过拌合水输送系统 (26)送入混料系统(7)中。
[0012]
其中,混料系统(7)包括搅拌器和出料皮带;出料皮带连接成型系统(8),用于将经过搅拌器搅拌后的半水脱硫石膏浆料送入成型系统(8)。
[0013]
其中,成型系统(8)包括模具和刮刀;刮刀设置在模具的上部,用于将模具中的半水脱硫石膏浆料经刮刀平整表面。
[0014]
其中,脱模系统(9)包括电动夹具(27)、伸缩臂(28)和第二电机;第二电机可驱动的连接电动夹具(27)和伸缩臂(28);伸缩臂(28)连接电动夹具(27),用于通过伸缩臂(28)控制电动夹具(27)将石膏板置于干燥系统(10) 的干燥料车(29)上;电动夹具(27)与成型系统(8)的模具中成型的石膏板可夹紧的连接,用于使得平整的所述石膏板脱离所述模具。
[0015]
其中,干燥系统(10)包括干燥料车(29)、运输轨道(30)和干燥箱(31);干燥料车
(29)设置在运输轨道(30)上,运输轨道(30)部分位于干燥箱(31) 内,用于使得燥料车(29)将其上的石膏板通过运输轨道(30)运入干燥箱(31) 中进行干燥。
[0016]
其中,所述转运料车(13)为多层料盘结构,脱硫灰均匀薄铺在每层料盘上。
[0017]
其中,干燥系统(10)中的干燥箱(31)内部采用叠架结构,成型后的脱硫石膏板设置在叠架结构形式的干燥架上。
[0018]
本实用新型还提供一种利用钢铁企业脱硫灰制备墙材的方法,优选采用上述的装置对脱硫灰进行处理的方法,包括以下步骤:
[0019]
(1)脱硫灰由生产环节运输到处理车间,布料于进料系统(1)上,并转运至蒸养系统(2);
[0020]
(2)通过控制系统启动蒸养程序,在一定压力下蒸养6-8h,二水脱硫石膏反应脱掉一个半结晶水生成半水脱硫石膏,出料后进入粉磨系统(3)粉磨成半水脱硫石膏粉并进入熟石膏料仓(4);
[0021]
(3)熟石膏料仓(4)中的半水脱硫石膏粉经由给料系统(5)与给水系统(6) 的拌合水以质量比2.4:1-3.0:1比例混合,经混料系统(7)搅拌成均匀的石膏料浆,优选在搅拌过程中可加入球团粘结剂;
[0022]
(4)拌和好的石膏料浆进入成型系统(8),经刮刀平整表面,再经脱模系统(9) 将成型好的石膏板取下;
[0023]
(5)石膏板转运至干燥系统(10),去除物理水,形成高强度石膏板,根据产品需要分割成合适的大小,并运至成品仓(11)等待出厂。
[0024]
其中,进料系统(1)的转运料车(13)采用多层叠架结构,料层之间存在空间,以利于在蒸养系统(2)中反应完全,每层布料尽量摊薄且均匀;优选,单料层厚度为8-12cm,可通过调整布料面积控制处理量。优选,蒸养系统(2) 的蒸养时间为6-8h,工作压力为1.4-1.5mpa,可基本保证脱硫灰反应完全脱掉一个半结晶水。优选,控制系统为plc控制系统,通过plc控制系统控制进料系统(1)布料、进料,蒸养系统(2)开启、关闭,给料系统(5)及给水系统(6) 比例控制,成型系统(8)刮刀操作,脱模系统(9)脱模,干燥系统(10)进料及干燥石膏板
[0025]
优选,本实用新型涉及一种利用钢铁企业脱硫灰制备墙材的装置,所述脱硫灰制备墙材装置包括:进料系统、蒸养系统、粉磨系统、熟石膏料仓、给料系统、给水系统、混料系统、成型系统、脱模系统、干燥系统、成品仓;所述进料系统包括转运轨道、转运料车、驱动装置、料盘;料盘布料后置于转运料车上,通过转运轨道运输入蒸养系统中脱结晶水;蒸养系统包括蒸压釜、蒸汽通入系统、排压系统,蒸汽通入系统设置在蒸压釜前端,处理过程中蒸汽由此进入工作中的蒸压釜中,排压系统设置在蒸压釜上部,当蒸压釜内蒸汽压力超过工作压力负荷时自动开启,排压至安全压力范围内;粉磨系统包括给料机、电机、粉磨机、出料口;给料机设置在粉磨系统上端,给粉磨机供料,粉磨成粉料的半水脱硫石膏经出料口进入熟石膏料仓,电机为给料机与粉磨机提供动力;给料系统包括给料机、皮带秤,半水脱硫石膏由熟石膏仓输出,经由给料机布料于皮带秤上;给水系统包括拌合水称量系统、拌合水输送系统;经过皮带秤称量过的半水脱硫石膏粉料与经拌合水称量系统称量过的拌合用水分别通过给料机和拌合水输送系统输送入混料系统;混料系统包括搅拌器、出料皮带;经过一定比例混合的半水脱硫石膏浆料出料皮带进入成型系统;成型系统包括模具、刮刀;半水脱
硫石膏浆料在模具中成型,经刮刀平整表面;脱模系统包括电动夹具、伸缩臂、电机;电动夹具将平整的石膏板脱离模具,通过伸缩臂将石膏板置于干燥系统的干燥料车上;干燥系统包括干燥料车、运输轨道、干燥箱;干燥料车将石膏板通过运输轨道运入干燥箱,干燥箱内通入热风干燥石膏板,干燥后的石膏板运入成品仓。
[0026]
优选其中,转运料车为多层料盘结构,作用为布料,将脱硫灰均匀薄铺在每层料盘上。转运料车设计长宽高分别为1.6m*2.5m*1.6m,共可铺设7层料,每层料层厚度约为10cm,每两层料层之间空间约为15cm,尽量降低料层厚度,提高布料层数,既可以保证处理量又可以保证处理效果。
[0027]
优选其中,蒸养系统中的蒸压釜设计工作压力为1.6mpa,耐压试验压力为 2.1mpa,最高允许工作压力为1.5mpa;蒸养过程中,从厂区引出蒸汽管道,将饱和蒸汽通入蒸压釜内,蒸汽温度达到设备时达到150℃,将釜内充满0.5mpa 的过饱和蒸汽,使蒸压釜内压力达到约1.5mpa,同时蒸压釜设有排压系统,当釜内压力过高时,自动卸压至1.5mpa。维持该压力6-8h,充分使二水脱硫石膏反应脱掉一个半结晶水,生成α半水石膏,用于制作墙材。
[0028]
优选其中,干燥系统中的干燥箱内部也采用叠架结构,将成型后的脱硫石膏板材由叉车运输到干燥车间,由夹具将板材转移到干燥架上,放置好板材后,设备内部通过高温或通入高温干气的形式加快板材的干燥。
[0029]
优选本实用新型还涉及一种利用钢铁企业脱硫灰制备墙材的方法,优选采用上述的脱硫灰制备墙材装置对脱硫灰进行处理的方法,包括以下步骤:
[0030]
(1)脱硫灰由生产环节运输到处理车间,布料于进料系统上,并转运至蒸养系统;
[0031]
(2)通过控制系统启动蒸养程序,在一定压力下蒸养6-8h,二水脱硫石膏反应脱掉一个半结晶水生成半水脱硫石膏,出料后进入粉磨系统粉磨成半水脱硫石膏粉并进入熟石膏料仓;
[0032]
(3)熟石膏料仓中的半水脱硫石膏粉经由给料系统与给水系统的拌合水以一定比例混合,经混料系统搅拌成均匀的石膏料浆,搅拌过程中可加入一定量的添加剂;
[0033]
(4)拌和好的石膏料浆进入成型系统,经刮刀平整表面,再经脱模系统将成型好的石膏板取下;
[0034]
(5)石膏板转运至干燥系统,去除物理水,形成高强度石膏板,根据产品需要分割成合适的大小,并运至成品仓等待出厂。
[0035]
本实用新型优点从装置上和方法上实现脱硫灰的处理利用,采用蒸养设备实现脱硫灰脱结晶水处理,工作压力高,脱结晶水效率高,生产连续化,尘汽有效收集处理;采用plc远程控制,具有自动化程度高,生产连续性好,处理效率高,脱硫灰脱结晶水效率高,空间占地小,系统投资低,环境排放达标,生产操作方便等优点。该方法及装置大幅度提高了脱硫灰的处理利用率,改变了以往堆弃处理或者直接低价格外卖的处理方式,为钢铁企业带来一定的经济效益。
附图说明
[0036]
图1利用脱硫灰制备墙材装置示意图。
[0037]
图2进料系统示意图。
[0038]
图3蒸养系统示意图。
[0039]
图4粉磨系统示意图。
[0040]
图5给料系统示意图。
[0041]
图6给水系统示意图。
[0042]
图7脱模系统示意图。
[0043]
图8干燥系统示意图。
具体实施方式
[0044]
一种利用钢铁企业脱硫灰制备墙材的装置如图1所示,所述脱硫灰制备墙材装置包括:进料系统1、蒸养系统2、粉磨系统3、熟石膏料仓4、给料系统5、给水系统6、混料系统7、成型系统8、脱模系统9、干燥系统10、成品仓11;进料系统1连接蒸养系统2,用于将进料系统1中的脱硫灰送入蒸养系统2中进行蒸养;蒸养系统2连接粉磨系统3,用于将蒸养得到的半水脱硫石膏送入粉磨系统3进行粉磨;粉磨系统3连接熟石膏料仓4,用于将粉磨得到的半水脱硫石膏粉送入熟石膏料仓4;熟石膏料仓4连接给料系统5,用于将熟石膏料仓4中的半水脱硫石膏粉送入给料系统5;给料系统5与给水系统6分别连接混料系统 7,用于将半水脱硫石膏粉和水送入到混料系统7进行混料搅拌,混料系统7连接成型系统8,用于将搅拌得到的石膏料浆进行成型;脱模系统9与成型系统8 可操作的连接,用于将成型系统8成型后的石膏板脱模;脱模系统9与干燥系统 10可操作的连接,用于将脱模后的石膏板送入干燥系统(10)进行干燥;干燥系统10连接成品仓11,用于将干燥后的石膏板送入成品仓11。优选,所述连接可采用传输系统进行连接,比如轨道,皮带,链带,传送轮等。
[0045]
进一步,如图1-8所示,所述进料系统1包括转运轨道12、转运料车13、驱动装置14、料盘15;料盘15布料后置于转运料车13上,通过转运轨道12 运输入蒸养系统2中脱结晶水;蒸养系统2包括蒸压釜16、蒸汽通入系统17、排压系统18,蒸汽通入系统17设置在蒸压釜16前端,处理过程中蒸汽由此进入工作中的蒸压釜中,排压系统18设置在蒸压釜16上部,当蒸压釜16内蒸汽压力超过工作压力负荷时自动开启,排压至安全压力范围内;粉磨系统3包括给料机19、电机20、粉磨机21、出料口22;给料机19设置在粉磨系统3上端,给粉磨机21供料,粉磨成粉料的半水脱硫石膏经出料口22进入熟石膏料仓4,电机20为给料机19与粉磨机21提供动力;给料系统5包括给料机23、皮带秤 24,半水脱硫石膏由熟石膏仓4输出,经由给料机23布料于皮带秤24上;给水系统6包括拌合水称量系统25、拌合水输送系统26;经过皮带秤24称量过的半水脱硫石膏粉料与经拌合水称量系统称量过的拌合用水分别通过给料机23和拌合水输送系统26输送入混料系统7;混料系统7包括搅拌器、出料皮带;经过一定比例混合的半水脱硫石膏浆料出料皮带进入成型系统8;成型系统8包括模具、刮刀;半水脱硫石膏浆料在模具中成型,经刮刀平整表面;脱模系统9包括电动夹具27、伸缩臂28、电机;电动夹具27将平整的石膏板脱离模具,通过伸缩臂28控制夹具将石膏板置于干燥系统的干燥料车29上;干燥系统10包括干燥料车29、运输轨道30、干燥箱31;干燥料车29将石膏板通过运输轨道30运入干燥箱31,干燥箱31内通入热风干燥石膏板,干燥后的石膏板运入成品仓11。转运料车13为多层料盘结构,其作用是布料,每层料层尽量摊薄均匀,设计长宽高分别为1.6m*2.5m*1.6m,共可铺设7层料,每层料层厚度约为10cm,每两层料层之间空间约为15cm;蒸养系统2中的蒸压釜16设计工作压力为1.6mpa,耐压试验压力为2.1mpa,最高允许工作压
力为1.5mpa;蒸养过程中,从厂区引出蒸汽管道,将饱和蒸汽通入蒸压釜16内,蒸汽温度达到设备时达到150℃,将釜内充满0.5mpa的过饱和蒸汽,使蒸压釜16内压力达到约1.5mpa,同时蒸压釜16设有排压系统18,当釜内压力过高时,自动卸压至1.5mpa。维持该压力 6-8h,充分使二水脱硫石膏反应脱掉一个半结晶水,生成α半水石膏,用于制作墙材;干燥系统10中的干燥箱31内部也采用叠架结构,将成型后的脱硫石膏板材由叉车运输到干燥车间,由夹具将板材转移到干燥架上,放置好板材后,设备内部通过高温或通入高温干气的形式加快板材的干燥。
[0046]
如图1-8所示,一种利用钢铁企业脱硫灰制备墙材的方法,包括以下步骤: (1)脱硫灰由生产环节运输到处理车间,布料于进料系统1上,并转运至蒸养系统2;(2)通过控制系统启动蒸养程序,在一定压力下蒸养6-8h,二水脱硫石膏反应脱掉一个半结晶水生成半水脱硫石膏,出料后进入粉磨系统3粉磨成半水脱硫石膏粉并进入熟石膏料仓4;(3)熟石膏料仓4中的半水脱硫石膏粉经由给料系统5与给水系统6的拌合水以质量比2.4:1-3.0:1比例混合,经混料系统7 搅拌成均匀的石膏料浆,优选,可以根据实际需要,搅拌过程中可加入质量比 1/200-1/50的球团粘结剂;(4)拌和好的石膏料浆进入成型系统8,经刮刀30 平整表面,再经脱模系统9将成型好的石膏板取下;(5)石膏板转运至干燥系统 10,去除物理水,形成高强度石膏板,根据产品需要分割成合适的大小,并运至成品仓11等待出厂。
[0047]
其中,进料系统1的转运料车13采用多层叠架结构,料层之间存在空间,以利于在蒸养系统中反应完全,每层布料尽量摊薄且均匀。优选,单料层厚度为 8-12cm,可通过调整布料面积控制处理量。优选,蒸养系统的蒸养时间为6-8h,工作压力为1.4-1.5mpa,可基本保证脱硫灰反应完全脱掉一个半结晶水。优选,控制系统为plc控制系统,通过plc控制系统控制进料系统1布料、进料,蒸养系统2开启、关闭,给料系统5及给水系统6比例控制,成型系统8刮刀操作,脱模系统9脱模,干燥系统10进料及干燥石膏板。
[0048]
上述实施方式,不仅限于上述实施例,而且对相关装置的其他组合亦是本实用新型所保护的范围上述实施方式仅供说明本实用新型之用,而并非是对本实用新型的限制,有关技术领域的技术人员,在不脱离本实用新型精神和范围的情况下,还可以做出各种变化和变型,因此所有等同的技术方案也应属于本实用新型的范畴。