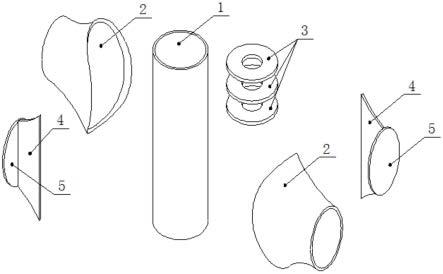
1.本实用新型涉及建筑领域,具体涉及一种外框圆管与椭圆截面仿形管相贯节点。
背景技术:2.随着国家对钢结构的重视及大力推广,钢结构在高层、超高层建筑中的应用越来越广泛,而在不同的连接节点截面结构(如:箱型结构、h型结构、十字型结构等)中,圆管结构以其优异的力学性能以及圆滑、柔美的外观,在高层、超高层钢结构中被广泛用于外框架中作为主受力结构,同时也作为建筑外观造型的重要组成部分。
3.十字型网格交汇节点通常由纵向构件及横向构件相贯而成,是重要的结构受力节点,也是建筑外观的重点。在高层、超高层建筑中为满足结构受力,通常圆管厚度势必很厚,给圆管相贯口的焊接带来困难,焊后质量难以保证,进而会影响到节点受力。为了使相贯节点外观顺滑、圆润美观,且节点受力好,传力明确,发明人提出一种外框圆管与椭圆截面喇叭仿形管相贯节点,本案由此而生。
技术实现要素:4.本实用新型公开一种外框圆管与椭圆截面仿形管相贯节点,技术方案如下:包括主杆圆管及椭圆截面喇叭仿形管,所述椭圆截面喇叭仿形管的一端为规则椭圆截面端,另一端为不规则椭圆截面端,自规则椭圆截面端向不规则椭圆截面端过渡连接部的截面积逐渐增大,且过渡连接部的截面积为不规则椭圆,主杆圆管的侧壁与椭圆截面喇叭仿形管的不规则椭圆截面端相贯连接。
5.进一步,所述主杆圆管的中心线与椭圆截面喇叭仿形管的中心线位于同一平面内。
6.进一步,主杆圆管与椭圆截面喇叭仿形管采用周围全熔透焊接方式焊接固定。
7.进一步,主杆圆管的内部设置圆形加劲板,圆形加劲板焊接在主杆圆管相贯点处的内壁上。
8.进一步,所述圆形加劲板设置多个,多个圆形加劲板间隔排布。
9.进一步,所述椭圆截面喇叭仿形管内部设置截面加劲板,截面加劲板为规则椭圆,截面加劲板焊接在靠近规则椭圆截面端的内壁上。
10.进一步,所述椭圆截面喇叭仿形管内部还设有纵向轴线加劲板,纵向轴线加劲板设置在椭圆截面喇叭仿形管的纵向轴线处,纵向轴线加劲板为异形板,其上下边缘与椭圆截面喇叭仿形管的内壁贴合焊接固定,纵向轴线加劲板的一端与截面加劲板焊接固定。
11.进一步,所述椭圆截面喇叭仿形管采用分片结构组合而成,包括两个上下对称设置的半圆弯弧段以及两个左右对称设置的三角形平面板,三角形平面板介于上下两个半圆弯弧段之间。
12.进一步,两个半圆弯弧段的一端拼合在一起形成规则椭圆截面,两个半圆弯弧段的另一端与三角形平面板拼合在一起形成不规则椭圆截面。
13.进一步,所述主杆圆管热弯形成弯弧段,弯弧段与椭圆截面喇叭仿形管相贯连接。
14.本实用新型所设计的相贯节点是采用圆管与椭圆截面喇叭仿形管相贯而成,整个节点外观顺滑过渡、圆润美观,且所设计的节点受力好,传力明确,无需增加圆管的壁厚也可以具有很好的受力效果,采用不规则椭圆截面的相贯线易于焊接作业,有助于提高焊缝焊接质量。另外,将椭圆截面喇叭仿形管采用分片结构设计,可以取代常规的铸钢件结构,有助于降低工程成本。
附图说明
15.图1为实施例中热弯后的圆管相贯节点的轴测图;
16.图2为无弯折的圆管相贯节点的主视图;
17.图3为图2的俯视图;
18.图4为图2的爆炸图;
19.图5为椭圆截面喇叭仿形管的结构示意图。
具体实施方式
20.下面将结合本实用新型实施例中的附图,对本实用新型实施例中的技术方案进行清楚、完整地描述。
21.本实施例公开一种外框圆管与椭圆截面仿形管相贯节点,如图1至图5所示,其结构主要包括主杆圆管1及椭圆截面喇叭仿形管2,主杆圆管1可以采用无弯折的圆管,也可以根据设计需要将其先热弯形成一个弯弧段(如图1中所示),令弯弧段与椭圆截面喇叭仿形管2相贯连接。本实施例以及图2至图5以无弯折的主杆圆管1与椭圆截面喇叭仿形管2相贯为例来介绍,可以根据设计节点的需要,在主杆圆管1的两侧侧壁各自与一个椭圆截面喇叭仿形管2相贯连接,或者仅选择一侧与椭圆截面喇叭仿形管2相贯连接。相贯处形成相贯线,主杆圆管1与椭圆截面喇叭仿形管2相贯时,主杆圆管1的中心线与椭圆截面喇叭仿形管2的中心线位于同一平面内,主杆圆管1与椭圆截面喇叭仿形管2采用周围全熔透焊接方式焊接固定,焊缝焊接紧密且圆滑过渡。
22.椭圆截面喇叭仿形管2采用不规则喇叭口形状设计,整个结构的喇叭口一端大另一端小,其过渡连接部的截面大小呈不规则椭圆形状的渐变变化。椭圆截面喇叭仿形管2可以采用一体式结构,当然,为了便于加工制作,推荐采用分片式结构设计,如图5所示,整个椭圆截面喇叭仿形管2由四部分拼接组合而成,即分为上、下两个结构相同且对称设置的半圆弯弧段6,以及左右对称设置的两个完全相同的三角形平面板7,三角形平面板7是一个平面结构,而半圆弯弧段6是由半个圆管热弯后形成,拼接时,将两个半圆弯弧段7的一端拼合焊接在一起形成一个规则椭圆截面,将两个三角形平面板7分别放置在上、下两个半圆弯弧段6两侧之间,三角形平面板7与半圆弯弧段6的拼合面焊接固定,这样拼合而成的椭圆截面喇叭仿形管2的另一端呈不规则椭圆截面。即:椭圆截面喇叭仿形管2的一端为规则椭圆截面端,另一端为不规则椭圆截面端,自规则椭圆截面端向不规则椭圆截面端过渡连接部分的截面积逐渐增大,且过渡连接部分的截面积为不规则椭圆。与主杆圆管1相贯连接时,将主杆圆管1的侧壁与椭圆截面喇叭仿形管2的不规则椭圆截面端相贯连接即可。
23.为了提高相贯节点处两个连接管的受力能力,两个连接管内分别设有加劲板,即:
主杆圆管1的内部设置有圆形加劲板3,圆形加劲板3可以设置多个,如图4中设置三个,三个圆形加劲板3间隔排布在主杆圆管1的内部,每个圆形加劲板3的四周焊接在主杆圆管1相贯点附近的内壁上。对于椭圆截面喇叭仿形管2内部则设有两种相互垂直设置的加劲板,一个是设置在靠近规则椭圆截面端的截面加劲板5,另一个是设置在椭圆截面喇叭仿形管2纵向轴线上的纵向轴线加劲板4,截面加劲板5为规则椭圆形状,截面加劲板5的四周焊接在靠近规则椭圆截面端的内壁上。纵向轴线加劲板4为异形板状结构,其所在平面的中心线与椭圆截面喇叭仿形管2的纵向轴线重合,纵向轴线加劲板4的上、下边缘与椭圆截面喇叭仿形管2的上下内壁贴合焊接固定,纵向轴线加劲板4的一端与截面加劲板5焊接固定。
24.尽管已经示出和描述了本实用新型的实施例,对于本领域的普通技术人员而言,可以理解在不脱离本实用新型的原理和精神的情况下可以对这些实施例进行多种变化、修改、替换和变型,本实用新型的范围由所附权利要求及其等同物限定。
技术特征:1.一种外框圆管与椭圆截面仿形管相贯节点,其特征在于:包括主杆圆管及椭圆截面喇叭仿形管,所述椭圆截面喇叭仿形管的一端为规则椭圆截面端,另一端为不规则椭圆截面端,自规则椭圆截面端向不规则椭圆截面端过渡连接部的截面积逐渐增大,且过渡连接部的截面积为不规则椭圆,主杆圆管的侧壁与椭圆截面喇叭仿形管的不规则椭圆截面端相贯连接。2.根据权利要求1所述的一种外框圆管与椭圆截面仿形管相贯节点,其特征在于:所述主杆圆管的中心线与椭圆截面喇叭仿形管的中心线位于同一平面内。3.根据权利要求1所述的一种外框圆管与椭圆截面仿形管相贯节点,其特征在于:主杆圆管与椭圆截面喇叭仿形管采用周围全熔透焊接方式焊接固定。4.根据权利要求1所述的一种外框圆管与椭圆截面仿形管相贯节点,其特征在于:主杆圆管的内部设置圆形加劲板,圆形加劲板焊接在主杆圆管相贯点处的内壁上。5.根据权利要求4所述的一种外框圆管与椭圆截面仿形管相贯节点,其特征在于:所述圆形加劲板设置多个,多个圆形加劲板间隔排布。6.根据权利要求1所述的一种外框圆管与椭圆截面仿形管相贯节点,其特征在于:所述椭圆截面喇叭仿形管内部设置截面加劲板,截面加劲板为规则椭圆,截面加劲板焊接在靠近规则椭圆截面端的内壁上。7.根据权利要求6所述的一种外框圆管与椭圆截面仿形管相贯节点,其特征在于:所述椭圆截面喇叭仿形管内部还设有纵向轴线加劲板,纵向轴线加劲板设置在椭圆截面喇叭仿形管的纵向轴线处,纵向轴线加劲板为异形板,其上下边缘与椭圆截面喇叭仿形管的内壁贴合焊接固定,纵向轴线加劲板的一端与截面加劲板焊接固定。8.根据权利要求1所述的一种外框圆管与椭圆截面仿形管相贯节点,其特征在于:所述椭圆截面喇叭仿形管采用分片结构组合而成,包括两个上下对称设置的半圆弯弧段以及两个左右对称设置的三角形平面板,三角形平面板介于上下两个半圆弯弧段之间。9.根据权利要求8所述的一种外框圆管与椭圆截面仿形管相贯节点,其特征在于:两个半圆弯弧段的一端拼合在一起形成规则椭圆截面,两个半圆弯弧段的另一端与三角形平面板拼合在一起形成不规则椭圆截面。10.根据权利要求1所述的一种外框圆管与椭圆截面仿形管相贯节点,其特征在于:所述主杆圆管热弯形成弯弧段,弯弧段与椭圆截面喇叭仿形管相贯连接。
技术总结本实用新型涉及一种外框圆管与椭圆截面仿形管相贯节点,包括主杆圆管及椭圆截面喇叭仿形管,椭圆截面喇叭仿形管的一端为规则椭圆截面端,另一端为不规则椭圆截面端,自规则椭圆截面端向不规则椭圆截面端过渡连接部的截面积逐渐增大,且过渡连接部的截面积为不规则椭圆,主杆圆管的侧壁与椭圆截面喇叭仿形管的不规则椭圆截面端相贯连接。本实用新型整个节点外观顺滑过渡、圆润美观,且所设计的节点受力好,传力明确,无需增加圆管的壁厚也可以具有很好的受力效果,采用不规则椭圆截面的相贯线易于焊接作业,有助于提高焊缝焊接质量。另外,将椭圆截面喇叭仿形管采用分片结构设计,可以取代常规的铸钢件结构,有助于降低工程成本。本。本。
技术研发人员:水峰 沈李强 袁洋 阙子雄 郑栋 杜冰冰 王笛 冯林涛 陈良 王腾 陈利萍 胡诚安 赵飞宇 曹端雄
受保护的技术使用者:浙江精工重钢结构有限公司
技术研发日:2021.10.19
技术公布日:2022/6/10