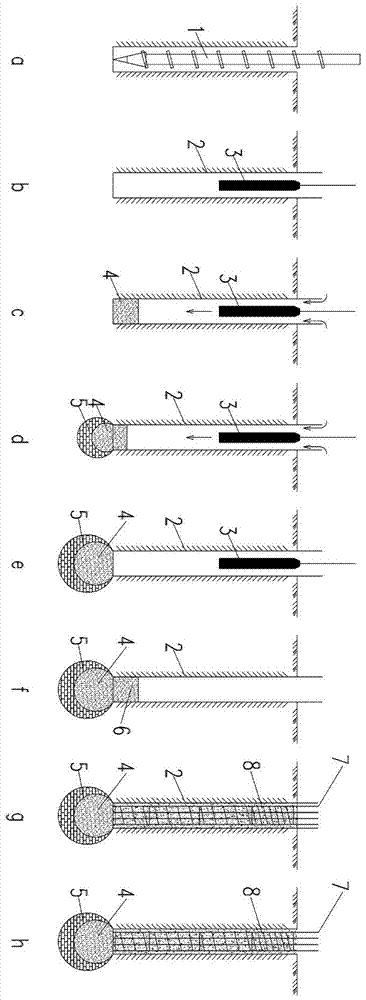
本发明涉及桩基施工技术,尤其涉及一种载体桩的施工方法。
背景技术:在专利号ZL98101041.5专利文献中公开了一种混凝土桩的施工技术,该技术的特点是通过在桩底端进行填料夯实挤密等操作形成人造持力层,使上部荷载通过混凝土桩身和桩底端的人造持力层,传递到较好持力层上,从而提高桩的承载力。但是该专利在施工过程中也陆续发现一些存在的问题:①该技术的一个特征为重锤是在夯击出护筒底端一定距离后再进行填料夯扩,并且要求收锤时锤出护筒的深度大于50cm,因此在当桩端持力层为易扰动土层时,这种锤出护筒的夯击方式会造成对持力层产生较大扰动,因此需要夯填更多的填料,才能使被扰动的土层达到所需要的密实度,其弊病一是增加了材料成本,二是填料量过大会造成对邻桩的破坏,出现较大的质量问题。②由于所采用的建筑垃圾等填料的粒径较大,因此每次填料时均需将重锤提出护筒上口才能完成填料,其弊病一是重锤自落夯击时落距较大、能量较高,加重了对桩端持力层的扰动,二是每次都提出重锤耗时较多过程缓慢,大大降低了施工工效。③因重锤和护筒之间空隙较小,其弊病一是重锤夯击时周围没有排气通道会在锤底产生气托,影响锤击能量,二是重锤夯击出护筒后再次上提时仍然受没有排气通道的影响,会在锤底和土体之间产生负压区,不仅加大了提升重锤所需要的能量,真空负压区的存在也会加剧地下水的回涌,加大施工难度的同时降低了工效。④所采用的建筑垃圾等填料多为拆迁砖甚至是新砖,其弊病一是随着建设的发展粘土砖使用越来越少,使夯填料的成本不断加大,二是易造成建筑垃圾的二次污染。⑤该技术还包括夯填干硬混凝土的工序,但在重锤夯击过程中干硬混凝土中的石料被重锤基本夯击成粉状,极大的降低了干硬混凝土的强度。因此,需要一种能够解决上述问题,且工序简单,成本仍较低的施工方法。
技术实现要素:本发明是为了解决上述的问题而提出的,目的在于提供一种载体桩的施工方法,通过对填料、重锤、护筒的重新设计,实现填料和重锤夯击的同步进行,通过重锤夯击方式的改变,避免对桩端土体的扰动并省时省力的形成桩端载体,通过填料成分的改变提高载体强度,从而在显著提高桩基承载能力的同时,实现工效的提高和成本的节约。为了实现上述目的,本发明包括一种载体桩的施工方法,其步骤包括:1)在桩位处,将护筒沉入至设定深度;2)在护筒中沉入重锤,重锤外壁与护筒内壁之间的间隙符合下述要求:①能够形成气流通道使空气流通顺畅;②能够使将要填入的水泥拌合物顺利通过间隙落入护筒内底部;3)同步进行填料和重锤夯击操作,即一边通过护筒的上口向护筒中填入水泥拌合物,一边向上提升重锤后使重锤自由下落对水泥拌合物进行夯击;上述水泥拌合物的最大粒径小于重锤外壁与护筒内壁之间的间隙,上述重锤夯击的操作符合下述要求:①重锤向上提升时重锤底端始终不超出护筒的上口;②重锤下落夯击时重锤底端始终不击出护筒底端;以保证重锤始终是在护筒的内部对水泥拌合物进行低落距、小能量夯击;4)重复进行上述步骤3)的同步填料和重锤夯击操作,使桩端下一定深度和范围内的土体被加固密实,在此过程中重锤底端始终不击出护筒底端;5)通过下述两种标准之一控制密实度:①测量重锤在不填料时的三击贯入度,贯入度测量值满足设计值时停止夯击,贯入度测量值不满足设计值时,继续进行填料夯击直至满足设计值;②根据地质条件和荷载要求计算水泥拌合物的设定填充量,根据设定填充量将全部的水泥拌合物夯实完毕;在此过程中重锤底端始终不击出护筒底端;从而在桩端形成由被夯实的水泥拌合物和被挤密土体形成的桩端载体,实现载体桩的等效计算面积Ae:6)通过下述方法之一进行桩身的施工:①现浇混凝土桩身:在护筒中沉入钢筋笼后浇注桩身混凝土,再提出护筒成桩;②现浇混凝土桩身:在护筒中浇注混凝土后在混凝土中反插钢筋笼,再提出护筒成桩;③预制混凝土桩身:在护筒内植入预制混凝土桩身后提出护筒,将预制混凝土桩身与桩孔壁的空隙用固化剂填满;④预制混凝土桩身:提出护筒后,以桩孔为导向植入预制混凝土桩身,预制混凝土桩身的底部与桩端载体结合。上述施工方法的步骤1)中,护筒沉入的方式包括下述方法之一或者组合:①在护筒内放置重锤,利用重锤的冲击动能对地基土体进行冲切,形成桩孔后向下沉入护筒;②采用柴油锤或者液压锤或者电动锤带动内管夯击护筒,使内管和护筒同步沉入;③采用螺旋钻或旋挖钻或人工挖孔的方式取土成孔后,将护筒沉入到桩孔中;④采用锤击或振动或者静压的方式,将带有预制桩尖或者活瓣桩尖的护筒向下沉入。上述施工方法的步骤2)中,重锤外壁与护筒内壁之间的间隙大于2cm,以形成空气通道和保证将要填入的水泥拌合物的通过。上述施工方法的步骤3)、4)中,水泥拌合物是以水泥和砂或小粒径碎石或上述材料的混合料加水拌合而成。上述施工方法的步骤4)中,使桩端下一定深度和范围内的土体被加固密实,是指桩端以下深度3~5m,直径2~3m范围内的土体被挤密,并保证施工地面不隆起,邻桩载体不破坏。上述施工方法的步骤5)中的控制标准①中,三击贯入度是指:重锤在不填料时下落夯击后的当次下沉数值即为一击贯入度,连续以相同的落距测量三次为三击贯入度;贯入度测量值满足设计值是指:三击贯入度中的后一次贯入度小于或者等于前一次的贯入度,三击贯入度的总值小于设计值,设计值的取值范围为0~50mm。上述施工方法的步骤5)中,载体桩的等效计算面积Ae,Ae值是根据三击贯入度和被加固土层的土性确定的,Ae值的取值范围为1.4~4.5m3。上述施工方法的步骤5)中,当三击贯入度满足设计值或者全部的水泥拌合物夯实完毕时,重锤底端与护筒底端持平,以保证护筒内不充留水泥拌合物。上述施工方法的步骤5)结束后,向护筒内部灌注水泥浆或水泥砂浆,该水泥浆或水泥砂浆的灌注数量,在护筒内部的高度小于2m。其目的和作用是在下一灌注桩身混凝土工序时避免底部混凝土的离析,或者在下一植入预制混凝土桩身工序时在提高结合部的固结强度。上述施工方法的步骤6)中的方法③和方法④中,预制混凝土桩身包括预应力管桩或预制钢筋混凝土实心桩。上述施工方法的步骤6)中的方法③和方法④中,植入预制混凝土桩身时采用重锤轻击预制混凝土桩身的顶端,使预制混凝土桩身底端更好的与桩端载体结合。本发明的载体桩的施工方法,主要技术特点和优势体现在:①改变重锤的夯击方式:第一,重锤向上提升时重锤底端始终不超出护筒的上口,落距低所以夯击能量小,第二,重锤下落夯击时重锤底端始终不击出护筒底端,从两方面保证了重锤始终是在护筒的内部对水泥拌合物进行低落距、小能量夯击,因此所填入的水泥拌合物是被逐渐挤扩出护筒外,从而避免填料夯击时对持力层土体的扰动,同时提高桩端载体的成型速度和工效。②对填料、重锤、护筒的重新设计,实现填料和重锤夯击的同步进行:第一,加大了重锤和护筒之间的间隙,形成空气通道使重锤能够顺利的、能量不减的提升和下落,也避免了提升重锤时形成负压区吸、抽桩端土体和地下水;第二,减小了填充加固料的粒径,使水泥拌合物顺利的从重锤和护筒之间的间隙落入护筒底端,避免了原本重锤必须提出护筒口等待填料后才能夯击的落后手段,保证重锤不间断的连续做功大大提高工效,特别是保证了上述重锤始终是在护筒的内部对水泥拌合物进行低落距小能量夯击的特征的实施。③改变填料成分,提高载体强度:所填入的水泥拌合物的填料成分为比表面积较大的细颗粒亲水物质,对施工时封闭地下水的效果极佳,也避免了原来的夯击过程对大颗粒骨料的破坏,同时水泥拌合物具备胶结性质从而显著增强了载体强度,进而提高桩基承载力。④填料夯击和控制密实度过程连续完成,无须进行原来的检测密实度后再夯填干硬混凝土过程,即避免了对桩端土体进一步扰动,又节约工序提高工效。⑤成孔过程可采用多种手段,桩身施工可采用现浇和预制,显著提高适用范围,在各种土层和基础形式中均可适用。附图说明图1是本发明的载体桩施工方法的一个实施例的工序图;图1中,1为振动器,2为护筒,3为重锤,4为水泥拌合物,5为被挤密土体,6为水泥砂浆,7为预制混凝土桩身。图2是本发明的载体桩施工方法的另一个实施例的工序图;图2中,1为螺旋钻,2为护筒,3为重锤,4为水泥拌合物,5为被挤密土体,6为水泥砂浆,7为钢筋笼,8为桩身混凝土。具体实施方式下面通过具体实施例对本发明作进一步说明。图1是本发明的载体桩施工方法的一个实施例的工序图,首先,如图1中a所示,在地基中的桩位处,通过振动器1的振动下压将带有预制桩尖的护筒2沉入至设计深度;然后,如图1中b所示,在护筒2中放置重锤3,重锤3的外壁与护筒2的内壁之间的间隙为5cm;然后,如图1中c所示,同步进行填料和重锤夯击操作,即一边通过护筒2的上口向护筒2中填入水泥和砂和小粒径碎石组成的拌合物4,一边向上提升重锤3后使重锤3自由下落对水泥拌合物4进行夯击,水泥拌合物4的最大粒径小于2cm,重锤3向上提升时其底端始终不超出护筒2的上口,重锤3下落夯击时其底端始终不击出护筒2底端;然后,如图1中d所示,重复进行上述的同步填料和重锤夯击的操作,使桩端下一定深度和范围内的土体被加固密实,在此过程中重锤3底端始终不击出护筒2底端;然后,如图1中e所示,测量重锤3在不填料时相同落距的连续三击贯入度,在此过程中重锤3底端始终不击出护筒2底端,当后一次的贯入度小于或等于前一次的贯入度且三击贯入度总值小于设计值10cm时,停止重锤3夯击,此时重锤3底端与护筒2底端持平,从而在桩端形成由被夯实的水泥拌合物4和被挤密土体5共同组成的桩端载体,实现载体桩的等效计算面积Ae;然后,如图1中f所示,提出重锤3,在护筒2内填入高度为50cm的水泥砂浆6;然后,如图1中g所示,提出护筒2,在桩孔上方垂直放置预制混凝土桩身7,利用重锤3轻击预制混凝土桩身7的桩顶,使其以桩孔为导向向下沉入;最后,如图1中g所示,继续锤击直至预制混凝土桩身7底面与桩端载体顶面结合,完成载体桩的施工。图2是本发明的载体桩施工方法的另一个实施例的工序图,首先,如图2中a所示,在地基中的桩位处,采用螺旋钻1旋转取土成孔至设计深度;然后,如图2中b所示,在桩孔中将护筒2沉入至设定深度,在护筒2中放置重锤3,重锤3的外壁与护筒2的内壁之间的间隙为4cm;然后,如图2中c所示,同步进行填料和重锤夯击操作,即一边通过护筒2的上口向护筒2中填入水泥和砂组成的拌合物4,一边向上提升重锤3后使重锤3自由下落对水泥拌合物4进行夯击,水泥拌合物4的最大粒径小于1cm,重锤3向上提升时其底端始终不超出护筒2的上口,重锤3下落夯击时其底端始终不击出护筒2底端;然后,如图2中d所示,重复进行上述的同步填料和重锤夯击的操作,使桩端下一定深度和范围内的土体被加固密实,在此过程中重锤3底端始终不击出护筒2底端;然后,如图2中e所示,将设定填充量的水泥拌合物4全部夯实完毕,在此过程中重锤3底端始终不击出护筒2底端,从而在桩端形成由被夯实的水泥拌合物4和挤密土体5共同组成的桩端载体,实现载体桩的等效计算面积Ae;然后,如图2中f所示,在护筒2内填入高度为30cm的水泥砂浆6;然后,如图2中g所示,提出重锤3后在护筒2内沉入钢筋笼7后,在护筒2内灌注桩身混凝土8;最后,如图2中h所示,提出护筒2后对桩身混凝土8进行振捣密实,完成载体桩的施工。以上实施例只是描述性的,而非限定性的,不能以此限定本发明的保护范围,在上述说明的基础上所引申出的其它不同形式的变化或变动,仍处于本发明的保护范围之中。