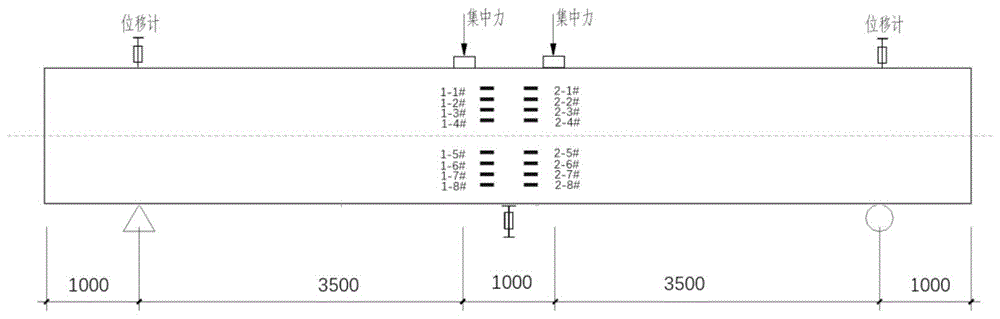
本发明属于锚桩检测
技术领域:
,涉及一种具有可回收钢绞线的锚桩性能检测方法。
背景技术:
:随着经济的不断发展,人们的生活水平日益提高,我国建筑用钢采用了不同产业政策和技术政策。建国后到80年代初,采取限制用钢政策,房屋建筑以砖混结构为主,辅以钢筋混凝土结构,提供以其他材料代替钢材,尽量节约用钢;80年代后期到90年代初,采取合理用钢政策,大量建筑,尤其是公共建筑,采用现浇混凝土楼板,提高建筑结构的抗震性能和整体质量;90年代中后期到现在,我国钢产量大幅增加,建筑用钢的品种和质量均有较大提升,采取鼓励合理用钢政策,限制建造砖混结构建筑,钢筋混凝土建筑在这一时期得到了快速发展。科技的进步让人们的物质生活极大的丰富起来,而人类赖以生存的大气、淡水、海洋、土地和森林等自然资源和环境却受到了巨大的威胁。可持续发展成为了子孙后代能够永续发展和安居乐业符合的唯一答案。在这样的时代背景下,对于现今施工项目提出安全、快捷、环保、高效、经济的要求。2020年建筑行业钢材消耗量4.75亿吨,如果实现临时性质桩基(如围护桩、支撑体系的临时立柱桩等)的钢材的可回收再利用技术方式具有巨大的社会价值和经济价值。在地基围护领域,围护桩等临时性结构寿命周期短,且消耗钢材巨大。由于一般采用的是混凝土灌注桩,钢筋与混凝土相互粘结使得钢筋的无法回收再利用。现有的可回收锚索技术,使用高性能钢绞线代替钢筋,通过回收钢绞线的方式,实现钢材的回收再利用,可回收锚索技术具有极大的经济和环境效益,但是与此同时该技术还缺乏理论研究和工程实例的探索,其主要问题为内配钢绞线桩基的抗弯和抗剪承载力问题,急需一项方便实用的承载力检测方法,以满足可回收技术的产品性能检测。技术实现要素:为解决上述问题,本发明提供了一种具有可回收钢绞线的锚桩性能检测方法,包括以下步骤:s1.使用相同方法和原料制备两根锚桩,分别为第一目标锚桩和第二目标锚桩,基于第一目标锚桩,在第一目标锚桩的跨中,设置第一应变片组和第三位移传感器,在第一目标锚桩的左端设置第一位移传感器,在第一目标锚桩的右端设置第二位移传感器,基于第一目标锚桩的第一钢筋设置第一钢筋计,基于第一目标锚桩的第一钢绞线设置第一钢绞线计;s2.基于电液伺服穿心作动器,通过单调分级加载的方式对第一目标锚桩加载作用力,采集第一应变片组的第一数据,构建荷载跨中挠度曲线模型;采集第一位移传感器、第二位移传感器、第三位移传感器、钢筋计、钢绞线计的第二数据,构建第一应变发展模型;基于荷载跨中挠度曲线模型和第一应变发展模型,构建抗弯承载力评估模型;s3.基于第二目标锚桩的剪跨段,与剪跨段的水平表面呈45°设置第二应变片组;在第二目标锚桩的跨中设置第四位移传感器,在第二目标锚桩的左端设置第五位移传感器,在第二目标锚桩的右端设置第六位移传感器,基于第二锚桩的第二钢筋设置第二钢筋计,基于第二目标锚桩的第二钢绞线设置第二钢绞线计;s4.通过电液伺服穿心作动器,通过s2的方法对第二目标锚桩加载作用力,采集第二应变片组的第三数据,构建抗剪承载力模型,采集第四位移传感器、第五位移传感器、第六位移传感器、第二钢筋计、第二钢绞线计的第四数据,构建第二应变发展模型;基于抗剪承载力模型和第二应变发展模型,构建剪承载力评估模型;s5.基于抗弯承载力评估模型和剪承载力评估模型,构建锚桩性能评估模型,用于所述锚桩的性能,为锚桩的制备和使用提供数据参考依据。优选地,第一应变片组和第二应变片组为120-50aa型混凝土应变片;混凝土应变片的参数包括,电阻值为120±1欧以内,灵敏度为2.0±1%,基底尺寸为58.2*6.5mm,丝栅尺寸为50.0±3.0mm。优选地,第一应变片组和第二应变片组包括三十二个混凝土应变片,其中,每四个混凝土应变片为一组。优选地,电液伺服穿心作动器为100t电液伺服穿心作动器mac-1000,每次加载时间间隔为15分钟。优选地,s2包括以下步骤:s2.1.抗裂弯矩20%的极差由零加载至抗裂弯矩的80%,然后按抗裂弯矩10%的极差继续加载至抗裂弯矩的100%;s2.2.弯矩的100%时未出现裂缝,则按抗裂弯矩5%的极差继续加载至裂缝出现,得到实测开裂荷载;s2.3.第一目标锚桩开裂后按照极限弯矩10%的极差加载至极限荷载的90%,然后按极限弯矩5%的极差继续加载至出现极限状态的检验标志为止,其中,所述极限状态检验标志包括:受拉区混凝土裂缝宽度达到1.5mm,受拉钢筋被拉断,受压区混凝土破坏;s2.4.当第一目标锚桩表面出现较大的裂缝时,撤去百分表,加载到第一目标锚桩完全破坏,记录各仪表读数及荷载最大值;s2.5.对桩进行卸载,记录第一目标锚桩破坏时的裂缝分布情况。优选地,s4包括以下步骤:s4.1.按抗裂弯矩20%的极差由零加载至抗裂弯矩的80%,然后按抗裂弯矩10%的极差继续加载至抗裂弯矩的100%;s4.2.如果达到抗裂弯矩的100%时未出现裂缝,则按抗裂弯矩5%的极差继续加载至裂缝出现,得到实测开裂荷载;s4.3.第二目标锚桩开裂后按照极限弯矩10%的极差加载至极限荷载的90%,然后按极限弯矩5%的极差继续加载至出现极限状态的检验标志为止,其中,所述极限状态的检验标志包括:受拉区混凝土裂缝宽度达到1.5mm,受拉钢筋被拉断,受压区混凝土破坏;s4.4.当第二目标锚桩出现较大的裂缝时,撤去百分表,加载到桩完全破坏,记录各仪表读数及荷载最大值;s4.5.对第二目标锚桩进行卸载,记录第二目标锚桩破坏时的裂缝分布情况。优选地,在正式加载前,为检查仪器仪表读数是否正常,需要进行预加载,预加载所用的荷载是分级荷载的前二级,分三级加载,每级稳定时间为一分钟,然后分级卸载,三级卸完,预加载中检查各个仪表设备的工作状况是否良好,预加载后,调整好仪表并记录初读数。优选地,第一位移传感器、第二位移传感器、第三位移传感器、第四位移传感器、第五位移传感器、第六位移传感器为同一种传感器,传感器为lvdt位移传感器,传感器的参数包括,型号为w-dcd300,精确度为0.05%,量程为0-300mm。本发明的积极进步效果在于:本发明提供了一种具有可回收钢绞线的锚桩性能检测方法,步骤简单,检测准确度高,实用性强,为新型锚桩的性能检测提供了技术依据。附图说明图1为本发明实施例所述的第一应变片组布置示意图;图2为本发明实施例所述的第二应变片组布置示意图;图3为本发明实施例所述的预应力抗弯桩钢筋计、钢绞线计位置分布图;图4为本发明实施例所述的预应力抗剪桩钢筋计、钢绞线计位置分布图;图5为本发明实施例所述的抗弯承载力的荷载-跨中挠度曲线;图6为本发明实施例所述的kw-10-a试件截面混凝土应变发展;图7为本发明实施例所述的kw-10-b试件截面混凝土应变发展;图8为本发明实施例所述的抗剪承载力的荷载-跨中挠度曲线;图9为本发明实施例所述的kj-6-a试件截面混凝土应变发展曲线;图10为本发明实施例所述的kj-6-b试件截面混凝土应变发展曲线。具体实施方式为使本申请实施例的目的、技术方案和优点更加清楚,下面将结合本申请实施例中附图,对本申请实施例中的技术方案进行清楚、完整地描述,显然,所描述的实施例仅仅是本申请一部分实施例,而不是全部的实施例。通常在此处附图中描述和示出的本申请实施例的组件可以以各种不同的配置来布置和设计。因此,以下对在附图中提供的本申请的实施例的详细描述并非旨在限制要求保护的本申请的范围,而是仅仅表示本申请的选定实施例。基于本申请的实施例,本领域技术人员在没有做出创造性劳动的前提下所获得的所有其他实施例,都属于本申请保护的范围。如图1-10所示,本发明提供一种具有可回收钢绞线的锚桩性能检测方法,包括以下步骤:s1.使用相同方法和原料制备两根锚桩,分别为第一目标锚桩和第二目标锚桩,基于第一目标锚桩,在第一目标锚桩的跨中,设置第一应变片组和第三位移传感器,在第一目标锚桩的左端设置第一位移传感器,在第一目标锚桩的右端设置第二位移传感器,基于第一目标锚桩的第一钢筋设置第一钢筋计,基于第一目标锚桩的第一钢绞线设置第一钢绞线计;s2.基于电液伺服穿心作动器,通过单调分级加载的方式对第一目标锚桩加载作用力,采集第一应变片组的第一数据,构建荷载跨中挠度曲线模型;采集第一位移传感器、第二位移传感器、第三位移传感器、钢筋计、钢绞线计的第二数据,构建第一应变发展模型;基于荷载跨中挠度曲线模型和第一应变发展模型,构建抗弯承载力评估模型;s3.基于第二目标锚桩的剪跨段,与剪跨段的水平表面呈45°设置第二应变片组;在第二目标锚桩的跨中设置第四位移传感器,在第二目标锚桩的左端设置第五位移传感器,在第二目标锚桩的右端设置第六位移传感器,基于第二锚桩的第二钢筋设置第二钢筋计,基于第二目标锚桩的第二钢绞线设置第二钢绞线计;s4.通过电液伺服穿心作动器,通过s2的方法对第二目标锚桩加载作用力,采集第二应变片组的第三数据,构建抗剪承载力模型,采集第四位移传感器、第五位移传感器、第六位移传感器、第二钢筋计、第二钢绞线计的第四数据,构建第二应变发展模型;基于抗剪承载力模型和第二应变发展模型,构建剪承载力评估模型;s5.基于抗弯承载力评估模型和剪承载力评估模型,构建锚桩性能评估模型,用于所述锚桩的性能,为锚桩的制备和使用提供数据参考依据。第一应变片组和第二应变片组为120-50aa型混凝土应变片;混凝土应变片的参数包括,电阻值为120±1欧以内,灵敏度为2.0±1%,基底尺寸为58.2*6.5mm,丝栅尺寸为50.0±3.0mm。第一应变片组和第二应变片组包括三十二个混凝土应变片,其中,每四个混凝土应变片为一组。电液伺服穿心作动器为100t电液伺服穿心作动器mac-1000,每次加载时间间隔为15分钟。s2包括以下步骤:s2.1.抗裂弯矩20%的极差由零加载至抗裂弯矩的80%,然后按抗裂弯矩10%的极差继续加载至抗裂弯矩的100%;s2.2.弯矩的100%时未出现裂缝,则按抗裂弯矩5%的极差继续加载至裂缝出现,得到实测开裂荷载;s2.3.第一目标锚桩开裂后按照极限弯矩10%的极差加载至极限荷载的90%,然后按极限弯矩5%的极差继续加载至出现极限状态的检验标志为止,其中,所述极限状态检验标志包括:受拉区混凝土裂缝宽度达到1.5mm,受拉钢筋被拉断,受压区混凝土破坏;s2.4.当第一目标锚桩表面出现较大的裂缝时,撤去百分表,加载到第一目标锚桩完全破坏,记录各仪表读数及荷载最大值;s2.5.对桩进行卸载,记录第一目标锚桩破坏时的裂缝分布情况。s4包括以下步骤:s4.1.按抗裂弯矩20%的极差由零加载至抗裂弯矩的80%,然后按抗裂弯矩10%的极差继续加载至抗裂弯矩的100%;s4.2.如果达到抗裂弯矩的100%时未出现裂缝,则按抗裂弯矩5%的极差继续加载至裂缝出现,得到实测开裂荷载;s4.3.第二目标锚桩开裂后按照极限弯矩10%的极差加载至极限荷载的90%,然后按极限弯矩5%的极差继续加载至出现极限状态的检验标志为止,其中,所述极限状态的检验标志包括:受拉区混凝土裂缝宽度达到1.5mm,受拉钢筋被拉断,受压区混凝土破坏;s4.4.当第二目标锚桩出现较大的裂缝时,撤去百分表,加载到桩完全破坏,记录各仪表读数及荷载最大值;s4.5.对第二目标锚桩进行卸载,记录第二目标锚桩破坏时的裂缝分布情况。在正式加载前,为检查仪器仪表读数是否正常,需要进行预加载,预加载所用的荷载是分级荷载的前二级,分三级加载,每级稳定时间为一分钟,然后分级卸载,三级卸完,预加载中检查各个仪表设备的工作状况是否良好,预加载后,调整好仪表并记录初读数。第一位移传感器、第二位移传感器、第三位移传感器、第四位移传感器、第五位移传感器、第六位移传感器为同一种传感器,传感器为lvdt位移传感器,传感器的参数包括,型号为w-dcd300,精确度为0.05%,量程为0-300mm。实施例1:试件采用kj-6-a和kj-6-b两种规格桩型,几何尺寸和配筋规格如表1所示,其中d表示桩外径,t表示主筋保护层厚度,dr表示普通螺纹钢筋分布圆直径。其桩身配筋图如每种圆桩制作一根,每根试件的长度均为6m。其生产采用现有国内通用工艺流程和技术要求,由浙江中桥预应力设备有限公司专门完成生产制作。kj-10-b试件由浙江中桥预应力设备有限公司通过后张法施加预应力,预应力施加完成后通过四个振弦式钢绞线测力计进行测量,振弦式钢绞线测力计布置所示,预应力钢绞线设置的初始拉力如表2所示。表1表2钢绞线测力计502039502040502046502043钢绞线拉力/kn99.89105.64102.67100.78实验使用的混凝土灌注桩桩身采用强度等级为c25的混凝土,同一批次混凝土按照按照《普通混凝土力学性能试验方法标准》gb/t50081-2002,制作3个尺寸为150mm×150mm×150mm的标准立方体试块。实验使用预应力钢绞线为直径为15.2mm的钢绞线,本次实验没有对钢绞线进行实验测量,根据产品提供的使用说明,其最小抗拉强bai度值≥1860mpa,其最小屈服强度≥1670mpa,符合《预应力混凝土用钢绞线》gbt5224-2003。本模型试验在加载过程中监测桩身的弯矩(应变片)、桩左右两端及跨中的挠度(位移计)。本实验采用益阳市赫山区广测电子有限公司生产的120-50aa型混凝土应变片。产品参数如下,电阻值:120±1欧以内,灵敏度:2.0±1%,基底尺寸:58.2*6.5mm,丝栅尺寸:50.0±3.0mm。试件桩在每个剪跨段布置三十二个应变测点,分成4组每组8个,共三十二个应变片,具体布置图如图1所示,本试验采用lvdt位移传感器,型号为w-dcd300,精确度0.05%,量程0-300mm。为了测量试件挠度特布置3个位移计,分别位于左右两个支座、跨中三处。本试验采用常州金坛德勤土木工程仪器厂出品的振弦式钢筋测力计和振弦式钢绞线测力计,具体分布见图3;试验加载装置参考国家标准进行设计,试验加载装置使用100t电液伺服穿心作动器mac-1000,试验机最大加载量为1000kn,但由于场地限制,最大加载量为550kn。根据上述加载方式,考虑到加载设备的自重的20kn的影响,试件跨中截面弯矩可计算为:式中:mt—试件跨中截面弯矩试验值;p—加载的总荷载值;l—试件长度;w—试件自身重量。参考实验方法标准,桩受剪试验采用单调分级加载,每次加载时间间隔为15分钟,加载程序如下:(1)按抗裂弯矩20%的极差由零加载至抗裂弯矩的80%,然后按抗裂弯矩10%的极差继续加载至抗裂弯矩的100%。(2)如果达到抗裂弯矩的100%时未出现裂缝,则按抗裂弯矩5%的极差继续加载至裂缝出现,得到实测开裂荷载。(3)桩开裂后按照极限弯矩10%的极差加载至极限荷载的90%,然后按极限弯矩5%的极差继续加载至出现极限状态的检验标志为止(极限状态检验标志包括:a)受拉区混凝土裂缝宽度达到1.5mm;b)受拉钢筋被拉断;c)受压区混凝土破坏)。(4)当桩出现较大的裂缝时,撤去百分表,加载到桩完全破坏,记录各仪表读数及荷载最大值。(5)对桩进行卸载,记录桩破坏时的裂缝分布情况。在正式加载前,为检查仪器仪表读数是否正常,需要进行预加载,预加载所用的荷载是分级荷载的前二级,分三级加载,每级稳定时间为一分钟,然后分级卸载,三级卸完。预加载中检查各个仪表设备的工作状况是否良好,预加载后,调整好仪表并记录初读数。对本次实验中均匀配置hrb400级螺纹钢、不施加预应力的kw-10-a桩进行抗弯承载力计算,其极限弯矩为700kn·m。如图5所示,在加载初期,两个试件处于弹性变形阶段,荷载与跨中挠度基本成线性变化。加载至纯弯段出现第一条裂缝,试件的抗弯刚度开始下降,试件kw-10-a得刚度退化更加明显。随着继续加载,试件竖向裂缝数目不断增多,裂缝长度和宽度也不断增大,直至纯弯段的主裂缝宽度超过1.5mm,停止加载,结束实验。采用可回收钢绞线技术新型混凝土实心圆桩试件因采用预应力技术刚度略大于未施加预应力混凝土实心圆桩试件,极限弯矩约大11.6%。两者试件的极限荷载均大于计算软件得出的抗弯承载力结果约18%,说明新型桩在抗弯承载力方面符合设计要求。如图6-7所示,分别为kw-10-a试件和kw-10-b试件跨中界面应变随荷载的发展变化。在裂缝出现以前,试件跨中截面各测点应变都非常小,成线性增长;观察不同高度测点应变变化情况,可知裂缝出现前桩试件跨中截面应变基本满足平截面假定。裂缝出现后,跨中截面受拉区混凝土应变急剧增长,部分应变片由于超出量程或拉坏而过早退出工作,导致测点失效。随着荷载继续增加,竖向裂缝继续开展,不断变宽和变长,截面中性轴不断上移,以及新的裂缝产生,部分受拉区测点应变会失真;而受压区混凝土应变开始稳定增长,直至试件发生破坏,且受竖向裂缝开展的影响比较小。通过对两种类型的混凝土试件进行足尺寸抗弯性能试验,对采用可回收钢绞线技术新型混凝土实心圆桩与均匀配置钢筋的混凝土实心圆桩的抗弯性能进行了对比研究,结论如下:相比未施加预应力混凝土圆桩试件,采用可回收钢绞线技术新型混凝土实心圆桩的裂缝数目更少,施加预应力提高了实心圆桩的抗裂性能。采用可回收钢绞线技术新型混凝土实心圆桩试件的极限抗弯承载力试验值大于承载力计算软件的计算值,预应力混凝土实心圆桩试件的极限抗弯承载力要比未施加预应力混凝土实心圆桩试件的极限抗弯承载力大10%左右,并且其抗弯能力有所提升。实施例2:采用实施例1用到的两种桩型作为试件桩,试件桩在每个剪跨段布置三十二个应变测点,分成4组每组8个,共三十二个应变片,具体布置图如图2所示。本试验采用lvdt位移传感器,型号为w-dcd300,精确度0.05%,量程0-300mm,为了测量试件挠度特布置3个位移计,分别位于左右两个支座、跨中三处。本试验采用常州金坛德勤土木工程仪器厂出品的振弦式钢筋测力计和振弦式钢绞线测力计,具体分布如图4所示。试验加载装置参考国家标准进行设计,试验加载装置使用100t电液伺服穿心作动器mac-1000,试验机最大加载量为1000kn,但由于场地限制,最大加载量为550kn。参考实验方法标准,桩受剪试验采用单调分级加载,每次加载时间间隔为15分钟,加载程序如下:(1)按抗裂弯矩20%的极差由零加载至抗裂弯矩的80%,然后按抗裂弯矩10%的极差继续加载至抗裂弯矩的100%。(2)如果达到抗裂弯矩的100%时未出现裂缝,则按抗裂弯矩5%的极差继续加载至裂缝出现,得到实测开裂荷载。(3)桩开裂后按照极限弯矩10%的极差加载至极限荷载的90%,然后按极限弯矩5%的极差继续加载至出现极限状态的检验标志为止(极限状态检验标志包括:a)受拉区混凝土裂缝宽度达到1.5mm;b)受拉钢筋被拉断;c)受压区混凝土破坏)。(4)当桩出现较大的裂缝时,撤去百分表,加载到桩完全破坏,记录各仪表读数及荷载最大值。(5)对桩进行卸载,记录桩破坏时的裂缝分布情况。在正式加载前,为检查仪器仪表读数是否正常,需要进行预加载,预加载所用的荷载是分级荷载的前二级,分三级加载,每级稳定时间为一分钟,然后分级卸载,三级卸完。预加载中检查各个仪表设备的工作状况是否良好,预加载后,调整好仪表并记录初读数。如图8所示,在加载初期,两试件处于弹性变形阶段,荷载与跨中挠度基本成线性变化。加载至纯弯段出现第一条裂缝后,试件抵抗变形刚度开始下降。当荷载加载至极限弯矩计算值,两桩弯剪段均未出现斜裂缝,直至加载时实验设备加载最大值,两桩弯剪段均未出现斜裂缝。表明两桩的抗剪承载力均符合设计,使用预应力技术的混凝土实心圆桩的刚度略搞于于普通混凝土实心圆桩,且纯弯段的裂缝更少。如图9-10所示,从混凝土应变发展变化中可以看出,裂缝出现之前,各截面应变测点的混凝土应变均成线性增长,应变均非常小;裂缝出现后,受拉区混凝土应变急剧增长,而受压区混凝土应变持续稳定增长。预应力混凝土实心圆桩弯剪段所受的最大压应变远小于普通混凝土实心圆桩,可以推测,相比未施加预应力混凝土实心圆桩试件,预应力混凝土实心圆桩试件开裂剪力更大,裂缝宽度发展更慢,施加预应力显著提高了实心圆桩的抗裂性能。但施加预应力降低了斜截面破坏的变形能力。通过对两种类型的混凝土试件进行足尺寸抗剪性能试验,对采用可回收钢绞线技术新型混凝土实心圆桩与均匀配置钢筋的混凝土实心圆桩的抗剪性能进行了对比研究,结论如下:两种类型的混凝土实心圆桩的剪承载力试验值要大于规范计算的抗剪承载力,均符合设计要求。相比未施加预应力混凝土实心圆桩试件,预应力混凝土实心圆桩试件开裂剪力更大,裂缝宽度发展更慢,施加预应力显著提高了实心圆桩的抗裂性能。最后应说明的是:以上所述实施例,仅为本发明的具体实施方式,用以说明本发明的技术方案,而非对其限制,本发明的保护范围并不局限于此,尽管参照前述实施例对本发明进行了详细的说明,本领域的普通技术人员应当理解:任何熟悉本
技术领域:
的技术人员在本发明揭露的技术范围内,其依然可以对前述实施例所记载的技术方案进行修改或可轻易想到变化,或者对其中部分技术特征进行等同替换;而这些修改、变化或者替换,并不使相应技术方案的本质脱离本发明实施例技术方案的精神和范围。都应涵盖在本发明的保护范围之内。因此,本发明的保护范围应所述以权利要求的保护范围为准。当前第1页12