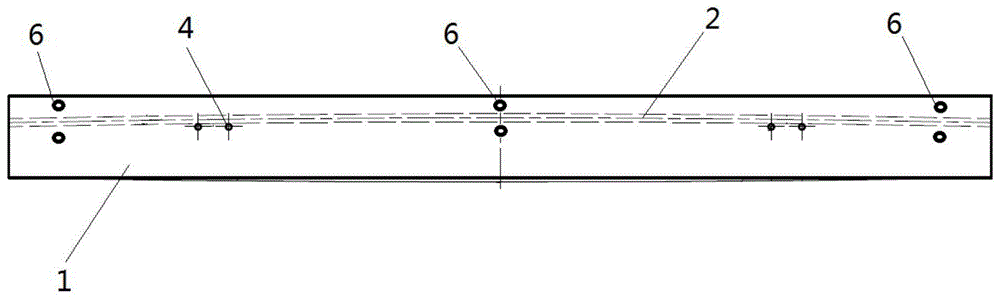
本实用新型涉及轨道及桥梁工程
技术领域:
,尤其涉及一种轨板梁结构系统。
背景技术:
:铁路桥梁是铁路跨越河流、湖泊、海峡、山谷或其他障碍物,以及为实现铁路线路与铁路线路或道路的立体交叉而修建的构筑物。铁路桥梁采用最多的是梁式桥。它是一种使用最广泛的桥梁型式,可细分为简支梁桥、连续梁桥和悬臂梁桥。板梁是桥梁的上部结构。桥梁在建成后,由于列车等荷载的作用,会产生一个向下的位移,这个位移也叫挠度;这会导致桥面实际高程与设计时的高程不符。为了消除或降低不相符的程度,需要设置一个预拱,即让桥梁在建造的过程中向上做高一定的高度,让建成的桥面高程比设计高程高一个数值,这样列车车辆上桥后,桥面高度就可以和设计高程基本一致。而且,现有的铁路桥梁,轨道板是轨道板,板梁是板梁,结构复杂,建造成本高。此外,现有的板式无砟轨道均采用多个间隔设置的扣件系统来固定钢轨,这些扣件系统给钢轨提供间断的支撑点,这是造成铁路轨道振动源和钢轨表面短波不平顺的主要原因。短波不平顺使钢轨与车轮磨损严重,长此以往,车轮受损成多边形,因而需要定期对钢轨和车轮进行打磨,否则将极大影响列车运行的舒适性、安全性和不平稳;而且,经常打磨也会缩短钢轨和车轮的寿命。技术实现要素:本实用新型旨在提供一种轨板梁结构系统,该轨板梁结构系统纵向抗弯、抗拉能力强,将轨道功能和桥梁功能合二为一,构成简单,可降低建造成本,同时又能对钢轨提供连续支撑,利于延长钢轨和列车的寿命。为达到上述目的,本实用新型采用的技术方案如下:一种轨板梁结构系统,包括板体,所述板体内预留有纵向后张预应力孔道。进一步的,所述板体顶面有内凹形成的用于嵌装钢轨的承轨槽,所述承轨槽纵向贯穿板体的两端面,承轨槽平行间隔设有两条。进一步的,后张预应力孔道有至少两组,两条承轨槽的下方分别有一组纵向后张预应力孔道。优选地,两条承轨槽下方的两组后张预应力孔道对称设置。进一步优选地,后张预应力孔道共有4-6个。进一步的,板体侧面设置有预埋吊装套管和第三轨支架固定管套。进一步的,板体的两端有与限位凸型挡台匹配的约束缺口。优选地,板体的长度为长度为4.8m-9.8m。进一步优选地,板体的厚度为400mm~700mm。上述轨板梁结构系统的生产方法,包括以下步骤:步骤a,绑扎板体的钢筋笼骨架,并入钢模;步骤b,在所述后张预应力孔道的对应位置安装波纹管+衬管,衬管出边摸,并安装预埋管套;步骤c,浇筑混凝土,砼初凝后,拔出衬管,并继续蒸汽养护;步骤d,脱模,吊出,检验。与现有技术相比,本实用新型具有以下有益效果:1,本实用新型将轨道功能和桥梁功能合二为一,不仅构成简单,而且可降低建造成本,是一种全新的桥梁的上部结构;在板体内预留纵向后张预应力孔道,通过在其内穿预应力束,在列车运行之前,对预应力束施加预拉应力,从而在板体中提前施加预应力,使得板体承受压应力,进而使其产生一定的形变,来抵抗列车冲击荷载,提高其抗弯能力和刚度。2,本实用新型在板体顶面预留有内凹的承轨槽,将钢轨直接嵌装在承轨槽中,可对钢轨提供连续支撑,消耗掉绝大部分的振动源,使列车运行平顺,延长钢轨和列车的寿命。附图说明图1是板体的主视图;图2是板体的俯视图;图3是板体的左视图;图中:1-板体、2-后张预应力孔道、3-承轨槽、4-预埋吊装套管、5-约束缺口、6-第三轨支架固定管套。具体实施方式为了使本实用新型的目的、技术方案及优点更加清楚明白,以下结合附图,对本实用新型进行进一步详细说明。如图1、2、3所示,本实用新型公开的轨板梁结构系统,它包括板体1,板体1内预留有纵向后张预应力孔道2。后张预应力孔道2的个数根据需要设置。通过在纵向后张预应力孔道2内穿预应力束,在板体1受外力之前,对预应力束施加预拉应力,从而在板体1中提前施加预应力,使得板体1承受压应力,进而使其产生一定的形变,来提高其抗弯能力和刚度。本实施例中板体1为镂空板,当需要安装齿轨时,板体1为实心板。将上述板体1用于铁路桥梁时,为避免短波不平顺,板体1顶面有内凹形成的用于嵌装钢轨的承轨槽3,承轨槽3纵向贯穿板体1的两端面,承轨槽3平行间隔设有两条。本具体实施方式中的“顶面”是指板体1安装使用时的上表面。后张预应力孔道2有两组,两组纵向后张预应力孔道2分别位于其中一条承轨槽3的下方。两组后张预应力孔道2对称设置,后张预应力孔道2共有6个。当然,后张预应力孔道2也可设置为3组、四组甚至更多,但两条承轨槽3的下方应各有一组。使用时,将钢轨直接嵌装在承轨槽3中,可对钢轨提供连续支撑,消耗掉绝大部分的振动源,使列车运行平顺,延长钢轨和列车的寿命。在板体1侧面设置有预埋吊装套管4和第三轨支架固定管套6。板体1的两端有与限位凸型挡台匹配的约束缺口5,约束缺口5为半圆形,通过将约束缺口5与限位凸型挡台装配,可对单个板体1进行限位,而且便于将多个板体1连续拼装。板体1的尺寸根据需要设置,板体1的厚度与其长度成正比例关系。本实施方式中板体1的长度为4.8m-9.8m,板体1的厚度为400~700mm。此外,本实施方式还提供了厚度与长度的关系表,见表1。表1轨道板板长(mm)轨道板板厚(mm)480040058004506800500780058088006509800700本实用新型公开的上述轨板梁结构系统的生产方法,前期需要制造出与板体1匹配的钢模型,然后按以下步骤进行生产:步骤a,绑扎板体1的钢筋笼骨架,并入钢模;步骤b,在后张预应力孔道2的对应位置安装波纹管+衬管或其他管道,衬管或其他管道出边摸。板体1在安装时的上表面是预制时的下表面,有承轨槽3的一面朝下。板体1在预制时设反拱度,后张预应力孔道2对应位置安装的管道设同样的反拱度。板体纵向后张预应力孔道2有4-6个。根据板体1的长度变化,可增加或减少纵向后张预应力孔道2的个数。步骤c,浇筑混凝土,砼初凝后,拔出衬管,并继续进行蒸汽养护;步骤d,脱模,吊出轨板梁,进行验证。取出衬管的空间位置,即在衬管的原始位置处形成后张预应力孔道2,完成板体1的制作。板体1制作完成后,后续进行预应力张拉和继续养护。具体步骤如下;步骤1,在后张预应力孔道2中穿预应力束;步骤2,使用千斤顶张拉预应力束,张拉时,板体1是反面放置的,有承轨槽3的一面朝下。张拉完成后,采用高分子砼进行封锚。通过预应力张拉使板体1预拱5mm-10mm。步骤3,封锚后的轨板梁吊入水养池,继续进行水养和自然养护。本实用新型提供一种全新的桥梁的上部结构,将轨道功能和桥梁功能合二为一,不仅构成简单,而且可降低建造成本。在板体内预留纵向后张预应力孔道,通过在其内穿预应力束,在板体中提前施加预应力,使得板体承受压应力,进而使其产生一定的形变,当列车经过时,内穿的预应力束会先抵抗列车冲击荷载。并且本实用新型可对钢轨提供连续支撑,利于列车运行平顺,延长钢轨和列车的寿命。当然,本实用新型还可有其它多种实施方式,在不背离本实用新型精神及其实质的情况下,熟悉本领域的技术人员可根据本实用新型作出各种相应的改变和变形,包括非框架板,但这些相应的改变和变形都应属于本实用新型所附的权利要求的保护范围。当前第1页12