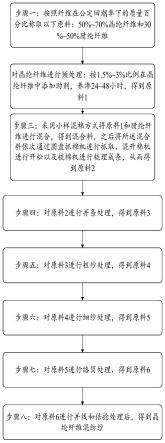
1.本发明涉及纺织技术领域,尤其是涉及一种晶纶纤维混纺纱的制备方法。
背景技术:2.晶纶纤维是近几年国内涤纶短纤维生产企业新研发的项目,旨在涤纶纤维制造工艺的基础上结合腈纶纤维制造工艺,进行工艺嫁接与改造完成的,改性后的涤纶称之为“晶纶”。现有的纺纱产品通常都是采用涤纶纤维与腈纶纤维的混合制成,然而由于涤纶原料与腈纶原料的物理特性能差异大,所制得的纺纱产品上色时需要高温高压条件,且上色率低,并且制得的纺纱产品存在回潮率低,手感差,保暖性较低等问题。
技术实现要素:3.本发明提供一种晶纶纤维混纺纱的制备方法,所制得的晶纶纤维混纺纱可以直接染色,无需高温高压条件,且具有良好的手感舒适和保暖性。
4.为解决上述技术问题,本发明采用的一个技术方案是:提供一种晶纶纤维混纺纱的制备方法,包括以下步骤:
5.步骤一:按照纤维在公定回潮率下的质量百分比称取以下原料:50%~70%晶纶纤维和30%~50%腈纶纤维;
6.步骤二:对晶纶纤维进行预处理:按1.5%~3%比例在晶纶纤维中添加助剂,养渗24~48小时,得到原料1;
7.步骤三:采用小样混棉方式将原料1和腈纶纤维进行混合,得到混合料,之后将所述混合料依次通过圆盘抓棉机进行抓取、混开棉机进行开松以及梳棉机进行梳理成条,从而得到原料2;
8.步骤四:对原料2进行并条处理,得到原料3;
9.步骤五:对原料3进行粗纱处理,得到原料4;
10.步骤六:对原料4进行细纱处理,得到原料5;
11.步骤七:对原料5进行络筒处理,得到原料6;
12.步骤八:对原料6进行并线和倍捻处理后,得到晶纶纤维混纺纱。
13.进一步地,所述对晶纶纤维进行预处理包括:
14.将0.5%~1%的静电剂、0.5%~1%的渗透剂、毛油1%~1.5%的毛油和96.5%~98%的水充分混合,静置30min,得到助剂。
15.进一步地,所述圆盘抓棉机的圆盘打手速度为600r/min,混开棉机抓的梳针打手速度为200r/min-240r/min,梳棉机的出条速度为50m/min。
16.进一步地,所述并条处理采用三道混合并条工艺进行,所述三道混合并条工艺为,第一道将8条原料2喂入并条机,制成一根原料2a,第二道将8条原料2a喂入并条机,制成一根原料2b,第三道将8条原料2b喂入并条机,制成一根原料3。
17.进一步地,所述粗纱处理为,将原料3放入粗纱机进行牵伸,再进行加捻,得到原料
4。
18.进一步地,所述细纱处理为,将原料4进行二次牵伸,并增大牵伸倍数,再进行加捻,得到原料5。
19.进一步地,所述络筒处理为,将原料5在络筒机上加工成筒子,得到原料6。
20.进一步地,所述并线和倍捻处理为,将至少2根原料6放入并线机进行合股,将合股后的原料加入倍捻机进行加捻粘合成股线,得到晶纶纤维混纺纱。
21.进一步地,所述并线机的并线速度为560-580米/min。
22.本发明的有益效果是:本发明的晶纶纤维混纺纱的制备方法中,首先按照纤维在公定回潮率下的质量百分比称取50%~70%晶纶纤维和30%~50%腈纶纤维两种原料,然后对晶纶纤维进行预处理得到原料1,之后采用小样混棉方式将原料1和腈纶纤维进行混合,得到混合料,之后将所述混合料依次通过圆盘抓棉机进行抓取、混开棉机进行开松以及梳棉机进行梳理成条,从而得到原料2;对原料2进行并条处理,得到原料3;对原料3进行粗纱处理,得到原料4;对原料4进行细纱处理,得到原料5;对原料5进行络筒处理,得到原料6;最后对原料6进行并线和倍捻处理后,从而得到晶纶纤维混纺纱,通过上述方式,可以利用晶纶纤维获得混纺纱,扩大了晶纶纤维的应用领域,扩大了优质纺纱原料来源,并且所制得的晶纶纤维混纺纱可以采用常温常压下的腈纶染色工艺,无需高温高压条件,且具有良好的手感舒适和保暖性。
附图说明
23.为了更清楚地说明本发明实施例中的技术方案,下面将对实施例描述中所需要使用的附图作简单地介绍,显而易见地,下面描述中的附图仅仅是本发明的一些实施例,对于本领域普通技术人员来讲,在不付出创造性劳动的前提下,还可以根据这些附图获得其它的附图,其中:
24.图1是本发明提供的一种晶纶纤维混纺纱的制备方法合成流程示意图。
具体实施方式
25.下面将结合本发明实施例中的附图,对本发明实施例中的技术方案进行清楚、完整地描述,显然,所描述的实施例仅是本发明的一部分实施例,而不是全部的实施例。基于本发明中的实施例,本领域普通技术人员在没有做出创造性劳动前提下所获得的所有其它实施例,都属于本发明保护的范围。
26.原料:
27.本发明的各实施例中所用的原料,除下述特殊说明之外,其他均为市售产品。
28.晶纶纤维选自江阴华宏化纤有限公司
29.腈纶纤维选自吉林化纤有限公司
30.一种晶纶纤维混纺纱的制备方法,其包括以下步骤:
31.步骤一:按照纤维在公定回潮率下的质量百分比称取以下原料:50%~70%晶纶纤维和30%~50%腈纶纤维;
32.步骤二:对晶纶纤维进行预处理:按1.5%~3%比例在晶纶纤维中添加助剂,养渗24~48小时,得到原料1。通过添加助剂并养渗24~48小时,可以使得助剂充分渗透到晶纶
纤维内部,可得的可纺性最佳的原料1,保证后道工序的可纺性及纱线品质。
33.步骤三:采用小样混棉方式将原料1和腈纶纤维进行混合,得到混合料,之后将所述混合料依次通过圆盘抓棉机进行抓取、混开棉机进行开松以及梳棉机进行梳理成条,从而得到原料2;
34.步骤四:对原料2进行并条处理,得到原料3;
35.步骤五:对原料3进行粗纱处理,得到原料4;
36.步骤六:对原料4进行细纱处理,得到原料5;
37.步骤七:对原料5进行络筒处理,得到原料6;
38.步骤八:对原料6进行并线和倍捻处理后,得到晶纶纤维混纺纱。
39.其中,在步骤一中,通过按照纤维公定回潮下重量计算配比,能够保证混比的准确性。
40.在步骤二中,所述助剂可通过以下方式获得:将0.5%~1%的静电剂、0.5%~1%的渗透剂、毛油1%~1.5%的毛油和96.5%~98%的水充分混合,静置30min,得到助剂。
41.其中,助剂的上述组分为根据晶纶纤维的特性配置,助剂的各组分的具体型号及添加比例可以根据季节温湿度、原料回潮、含油状态等作微调,其中,通过使各组分的添加比例为0.5%~1%的静电剂、0.5%~1%的渗透剂、毛油1%~1.5%的毛油和96.5%~98%的水,可获得可纺性最佳的原料1。
42.其中,在步骤三中,采用小样混棉方式将原料1和腈纶纤维进行混合。具体为,将原料1和和腈纶纤维放入容器中,再对容器加热至25℃~30℃,在25℃~30℃的温度条件下静置30min~45min,得到颜色均匀的混合料。例如,容器的温度可加热至30℃,从而有利于保证纤维的充分混合均匀,避免混合不均匀而出现花纱现象。其中,具体的混合量例如可以是:总共进行10次原料1和腈纶纤维的混合,每次原料1和腈纶纤维的混合总量为200公斤,按照公定回潮计算,原料1在60~140公斤范围内,腈纶纤维在140~60公斤,进行10次混合后约得到2000
±
10公斤的混合料。
43.其中,在步骤三种,圆盘抓棉机的型号为fa002,其圆盘打手速度为600r/min,伸出肋条距离为-2mm,间隙下降距离为2mm。混开棉机的型号为fa306,其梳针打手速度为200r/min-240r/min。梳棉机的型号为fa186,其出条速度为50m/min,生条重25g/5m,锡林转速为330rm,次辊转速600pm,盖板速度195mm/min。
44.在所述步骤四中,所述并条处理采用三道混合并条工艺进行。其中,三道混合并条工艺具体为:第一道将8条原料2喂入并条机,制成一根原料2a,第二道将8条原料2a喂入并条机,制成一根原料2b,第三道将8条原料2b喂入并条机,制成一根原料3。需要说明的是,并条机的信号为fa306,其中在上述第一道工艺中,并条机的工艺参数为出条定重22.5g/5m,总牵伸倍数8.9倍,后牵伸1.8倍,罗拉隔距30*57,出条速度300m/min。在第二道、第三道工艺中,并条机的工艺参数为定重22g/5m,总牵伸倍数8.18倍,后牵伸1.5倍,罗拉隔距30*57,喇叭口规格7f/3.8,出条速度300m/min。
45.本发明实施例中,并条采用三道并合,可以充分保证纤维混合,避免因混合不均产生染色过程中花纱现象,牵伸与并合根数相匹配可以减少因牵伸倍数过大引起条干恶化。
46.其中,在步骤五中,所述粗纱处理为:将原料3放入粗纱机进行牵伸,再进行加捻,得到原料4。需要说明的是,原料3放入粗纱机a458无铁炮中的锭管,锭管为放置原料3的器
具,为保证原料3的整洁,需要每出两批原料3,进行清理一次。
47.粗纱机型号为a458,其工艺参数为:粗纱定重7g/10m,捻度2.6捻/10cm,总牵伸倍数8.8倍,后牵伸1.44倍,罗拉隔距42*45,钳口隔距块6mm,锭速750rpm。
48.在所述步骤六中,所述细纱处理为,将原料4进行二次牵伸,并加大牵伸倍数,再进行加捻,得到原料5。需要说明的是,细纱机需要采用偏大的牵伸隔距和钳口工艺隔距细纱单锭控制,可以减少细纱断头产生的风箱花,降低消耗,提升效率。需要说明的是,细纱机型号为fa516,工艺参数为:支数:36公支,牵伸倍数:后牵伸倍数1.1倍,钳口隔距块3.5mm,捻度50捻/10cm,罗拉隔距为22*40,锭速为10000rpm,钢丝圈5#。
49.在所述步骤七中,所述络筒处理为,将原料5在络筒机上加工成筒子,得到原料6。络筒机为自动络筒机,可以根据毛衫针织纱要求设置电子切疵门限,控控制万米剪切数在5个以内。其中络筒的速度为1300m/min,电子清纱器通道设置为:粗节+50%、细节-50%、棉结+200%。
50.在步骤八中,所述并线和倍捻处理为,将至少2组原料6放入并线机进行合股,将合股后的原料加入倍捻机进行加捻粘合成股线,得到晶纶纤维混纺纱。
51.其中,并线机型号为dx2310,并线机的并线速度为560-580米/分,因纱支较粗,采用较高速并线,并纱采用加大风机速度,加大吹吸风量,从而可以避免短绒、飞花附入到并线纱中。倍捻机型号为dx321g,倍捻速度为5500,其中可定期加强单锭检修,避免弱捻纱形成。
52.在其他实施例中,步骤一中纱线工艺需要的支数为28公支,每支纤维混比的允许范围
±
2%。
53.实施例:
54.实施例1
55.一种晶纶纤维混纺纱的制备方法,包括以下步骤:
56.步骤一:按照纤维在公定回潮率下的质量百分比称取晶纶纤维51%和腈纶纤维49%;
57.步骤二:对晶纶纤维进行预处理:按1.5%~3%比例在晶纶纤维中添加助剂,养渗24~48小时,得到原料1;
58.步骤三:采用小样混棉方式将原料1和腈纶纤维进行混合,得到混合料,之后将所述混合料依次通过圆盘抓棉机进行抓取、混开棉机进行开松以及梳棉机进行梳理成条,从而得到原料2;
59.步骤四:对原料2进行并条处理,得到原料3;
60.步骤五:对原料3进行粗纱处理,得到原料4;
61.步骤六:对原料4进行细纱处理,得到原料5;
62.步骤七:对原料5进行络筒处理,得到原料6;
63.步骤八:对原料6进行并线和倍捻处理后,得到晶纶纤维混纺纱。
64.实施例2:
65.一种晶纶纤维混纺纱的制备方法,包括以下步骤:
66.步骤一:按照纤维在公定回潮率下的质量百分比称取晶纶纤维70%和腈纶纤维30%;
67.步骤二:对晶纶纤维进行预处理:按1.5%~3%比例在晶纶纤维中添加助剂,养渗24~48小时,得到原料1;
68.步骤三:采用小样混棉方式将原料1和腈纶纤维进行混合,得到混合料,之后将所述混合料依次通过圆盘抓棉机进行抓取、混开棉机进行开松以及梳棉机进行梳理成条,从而得到原料2;
69.步骤四:对原料2进行并条处理,得到原料3;
70.步骤五:对原料3进行粗纱处理,得到原料4;
71.步骤六:对原料4进行细纱处理,得到原料5;
72.步骤七:对原料5进行络筒处理,得到原料6;
73.步骤八:对原料6进行并线和倍捻处理后,得到晶纶纤维混纺纱。
74.对比上述实施例1~2,不同之处在于各组成部分的含量不同。
75.对比例原料晶纶纤维腈纶纤维实施例151%49%实施例270%30%
76.性能检测试验:将实施例1~2制得的晶纶纤维混纺纱,分别由检验人员进行触感检验。
77.对实验组1~2以晶纶纤维混纺纱的感官评价:
78.感官评价项目为手感舒适度和保暖性能;每个项目评分值为1~5分,各项均以1分为最小计分单位。手感越舒适,保暖性越好得分越高;手感差,保暖性差得分越低;
79.评价程序:设置10位5~10年纺织行业的检验人员为评测员,评测员员健康均无不良状况,向每位评测员提供验试样组1~2进行触感和保暖评价,每触感和保暖一个试样后在评分表上做出相应的评分,两个试样的触感和保暖评价之间需至少相隔15min,并使手感恢复至正常状态,并用温度计进行测量。
80.对比例分数项目手感保暖实验组154实验组255
81.根据感官评价结果可以看出,在相同的手感和近似的保暖性下,晶纶纤维性价比要远远高于腈纶纤维,原因在于晶纶与腈纶价格相差极大,差价在40%以上,而实验组2的各项评分结果明显要比其他实验组略高,说明以上文所述的成分加上适宜的配比制得的晶纶纤维混纺纱,其使用于纺织品中具有良好的手感舒适和保暖性。
82.另外将本方案制成的晶纶纤维混纺纱,与现有材料进行对比如下:
83.对比材料1:含量为100%腈纶纱;
84.对比材料2:含量为51%涤纶纤维和49%的腈纶纤维混纺纱。
[0085][0086][0087]
根据感官评价结果可以看出,实验组2的各项评分结果与腈纶纱手感与保暖性无差别,说明以上文所述的成分加上适宜的配比制得的晶纶纤维混纺纱,在相同的手感和近似的保暖性下,晶纶纤维性价比要远远高于腈纶纤维,原因在于晶纶与腈纶价格相差极大,差价在40%以上,而且其使用于晶纶纤维混纺纱中具有良好的手感舒适和保暖性。
[0088]
以上所述仅为本发明的实施例,并非因此限制本发明的专利范围,凡是利用本发明说明书及附图内容所作的等效结构或等效流程变换,或直接或间接运用在其它相关的技术领域,均同理包括在本发明的专利保护范围内。