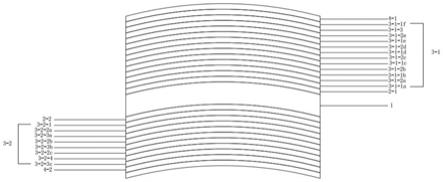
[0001]
本发明涉及树脂镜片制备技术领域,具体涉及一种防护绿色激光笔的树脂镜片及其制备方法。
背景技术:[0002]
近年来,光学树脂镜片在国内外眼镜市场上需求越来越大,树脂镜片与玻璃镜片相比,具有质量轻、染色性能好、易于加工等优点,中高折射率光学树脂镜片更以高透光率、防紫外、超薄等特有的优势获得使用者的青睐。
[0003]
随着半导体激光技术的飞跃发展,低功率半导体激光器实现了小型化。激光器加工工艺与微纳制造工艺的结合,实现了小型低功率半导体激光器的规模化生产,使激光器成本的迅速降低。以激光笔为代表的半导体激光器进入民用领域,在教学、旅游、天文观察、建筑和消防/救灾等领域广泛应用。
[0004]
目前市场上的激光笔以红色和绿色的半导体激光笔为主,其工作波长分别为650nm和532nm。由于人眼对532nm的激光更敏感,其相对照度及对人眼伤害更大。例如,警察在执勤和执法过程中不可避免遇到各种激光笔的照射,因此如何防护眼睛,降低激光笔特别是532nm的绿色激光笔,对人眼的伤害,并保持良好的视觉效果,给眼镜行业提出了新的挑战。
[0005]
防护绿色激光笔光学膜层比一般的常规减反射膜层厚得多。另外,由于光学薄膜的主要材料为无机材料,而高分子树脂镜片基底为有机材料,故因二者物化性质的差异,而导致镀膜后的镜片应力较高,进而导致耐温和耐久性能不佳,尤其是具备防护绿色激光的膜层一般较厚,其对镀膜后的镜片的应力影响特别显著,而影响其的正常使用。因此,如何提供一种防护绿色激光且耐高温耐久的树脂镜片成为本领域亟待解决的问题。
技术实现要素:[0006]
为克服现有技术缺陷,本发明旨在提供一种防护绿色激光笔的树脂镜片及其制备方法,在有效实现防护绿色激光的同时,能通过降低应力来提升树脂镜片的耐久性。
[0007]
本发明是通过以下的技术方案实现的:
[0008]
本发明的一方面提供了一种防护绿色激光的树脂镜片,包括:树脂镜片基片1、加硬层2以及防激光膜层3;其中,所述树脂镜片基片1、加硬层2以及防激光膜层3依次排列,所述加硬层2位于所述树脂镜片基片1表面,所述光学膜层3位于所述加硬层2表面;
[0009]
进一步的,所述树脂镜片基片一面为凸面1-1,即远离人眼面,另一面为凹面1-2,即靠近人眼面;
[0010]
进一步的,所述加硬层包括加硬层2-1和加硬层2-2,所述加硬层2-1和加硬层2-2分别位于凸面1-1以及凹面1-2的表面;
[0011]
更进一步的,所述防激光膜层3包括激光高反膜层3-1和激光吸收降背反膜层3-2,所述激光高反膜层3-1位于所述凸面1-1一侧,即凸面1-1、加硬层2-1以及所述激光高反膜
层3-1依次排列,且所述激光吸收降背反膜层3-2位于所述凹面1-2一侧,即凹面1-2、加硬层2-2以及所述激光吸收降背反膜层3-2依次排列;
[0012]
进一步的,所述防护绿色激光的树脂镜片还包括防水层4,所述防水层4位于所述防激光膜层3表面;更进一步的,所述防水层4-1和防水层4-2分别位于所述激光高反膜层3-1和所述激光吸收降背反膜层3-2的表面。
[0013]
更进一步的,所述加硬层2的材料为有机硅;更进一步优选的,所述有机硅中至少含有ti元素;
[0014]
更进一步的,所述激光高反膜层3-1包括硅铝复合氧化物层、钛铌复合氧化物层以及掺锡氧化铟(ito)层;更进一步优选的,所述激光高反膜层3-1包括六层硅铝复合氧化物层3-1-1a~1f、五层钛铌复合氧化物层3-1-2a~2e以及一层掺锡氧化铟(即ito)层3-1-3;
[0015]
更进一步的,所述激光吸收降背反膜层3-2包括cr吸收层,硅铝复合氧化物层、钛铌复合氧化物层以及ito层;更进一步优选的,所述激光吸收降背反膜层3-2包括一层cr吸收层3-2-1,三层钛铌复合氧化物层3-2-2a~c、三层硅铝复合氧化物层3-2-3a~c以及一层ito层3-2-4;
[0016]
更进一步优选的,所述硅铝复合氧化物层由sio2和al2o3复合材料组成,且其中sio2占所述复合材料的摩尔分数为70%~95%;进一步优选的,其中sio2摩尔量占所述复合材料摩尔量的92%;
[0017]
更进一步优选的,所述钛铌复合氧化物层由tio2和nb2o5复合材料组成,其中tio2占所述复合材料摩尔分数的10%~90%;优选的,其中tio2摩尔量占所述复合材料摩尔量的80%;
[0018]
进一步的,所述加硬层2的厚度为1~5μm;
[0019]
进一步的,所述防激光膜层3的厚度为600~2000nm;
[0020]
更进一步的,所述激光高反膜层3-1的厚度为500~1000nm;
[0021]
更进一步的,所述激光吸收降背反膜层3-2的厚度为500~1000nm;进一步优选的,所述cr吸收层3-2-1的厚度为8~25nm;
[0022]
进一步的,所述防水层4的厚度为4~20nm;
[0023]
进一步的,所述激光高反膜层3-1的绿色激光反射率≥65%;
[0024]
进一步的,所述激光高反膜层3-1的视觉平均透过率≥40%;
[0025]
进一步的,所述激光吸收降背反膜层3-2的绿色激光透过率≤35%;
[0026]
进一步的,所述激光吸收降背反膜层3-2的视觉平均反射率≤6%;
[0027]
本发明另一方面提供了一种上述防护绿色激光树脂镜片的制备方法,包括以下步骤:
[0028]
s1制备加硬层2:在所述树脂镜片基片1的凸面1-1和凹面1-2表面分别形成加硬层2-1和加硬层2-2,即获得含加硬层2的树脂镜片;
[0029]
s2制备防激光膜层3-1和防水层4-1:在所述加硬层2-1的表面形成激光高反膜层3-1,然后在所述激光高反膜层3-1表面形成防水层4-1,即获得含激光高反膜层3-1和防水层4-1的树脂镜片;
[0030]
s3制备激光吸收降背反膜层3-2和防水层4-2:在s2步骤获得的镜片的加硬层2-2表面形成激光吸收降背反膜层3-2和防水层4-2,即得;
[0031]
进一步的,s2中,所述形成激光高反膜层3-1的具体步骤包括:
[0032]
s21:在s1获得的加硬层2-1表面交替分别形成五层硅铝复合氧化物层3-1-1a~1e和五层钛铌复合氧化物层3-1-2a~2e,所述第一层硅铝复合氧化物层3-1-1a位于所述加硬层2-1表面,即获得含五层硅铝复合氧化物层和五层钛铌复合氧化物层的树脂镜片;
[0033]
s22:在步骤s21获得的树脂镜片表面形成含一层ito层3-1-3的树脂镜片;
[0034]
s23:在步骤s22获得的树脂镜片表面形成含一层硅铝复合氧化物层3-1-1f的树脂镜片;
[0035]
进一步的,s3中,所述形成激光吸收降背反膜层3-2的具体步骤包括:
[0036]
s24:在s1获得的加硬层2-2表面形成一层cr吸收层3-2-1,即获得含cr的树脂镜片;
[0037]
s25:在s24获得的含cr树脂镜片表面交替分别形成三层钛铌复合氧化物层3-2-2a~c和二层硅铝复合氧化物层3-2-3a~b,所述第一层钛铌复合氧化物层3-2-2a位于所述加硬层2-1表面,即获得包括三层钛铌复合氧化物层和二层硅铝复合氧化物层的树脂镜片;
[0038]
s26:在s25获得的树脂镜片表面形成一层含ito层3-2-4的树脂镜片;
[0039]
s27:在s26获得的树脂镜片表面形成一层含硅铝复合氧化物层3-2-3c的树脂镜片。
[0040]
有益效果
[0041]
1、本发明采用的减反射膜层具有以下优势:
[0042]
(1)镜片基片凸面采用的激光高反膜层可有效减少激光对树脂镜片的影响。70%的激光能量被正面激光高反膜系反射,保护树脂镜片和人眼不受激光辐射;
[0043]
(2)镜片基片凹面采用的激光吸收降背反膜层可以有效降低凸面高反产生的背反射对人眼造成的眩光效果,激光吸收可以进一步降低激光的能量,从而保护人眼更少的暴露在激光中,采用此设计的树脂镜片可以将市场上常见的100mw绿色激光笔(以532nm为代表波长)对人眼的激光辐射从激光损伤等级3级降低到激光伤害2级的水平;保护了人眼较少受到绿色激光笔偶然伤害;
[0044]
(3)由于膜层材料以tio2为主,掺入一定比例nb2o5,使光学折射率接近tio2,比nb2o5等材料更高,防激光效果更好;
[0045]
(4)该树脂镜片保持了一定的视觉透过率,并且除了激光波长外的其他绿色光线有较高透过,不影响观察红绿灯等日常使用;
[0046]
2、本发明获得的树脂镜片具有耐高温和耐久性:本发明采用摩尔用量严格配比的高折射率材料钛铌复合氧化物材料作为膜层材料,以tio2为主,在树脂眼镜镀膜低离子源能量的情况下,掺入一定比例nb2o5的可以有效规避tio2膜层的易结晶的特性,保证膜层处于无定形态,防止膜层因为结晶崩裂,从而提升膜层和镜片的耐高温和耐高湿性能,进而提高产品的耐久性;另外,采用硅铝复合氧化物层,有效避免了sio2容易形成长柱状结果导致膜层高应力,保持膜层的玻璃态结构,提高膜层的耐高温性能;
[0047]
3、改善产品的重复性和可量产性:在制备低反射钛铌复合氧化物膜层时,由于膜层材料由tio2和nb2o5掺杂,降低了tio2对于iad辅助工艺中o2流量的敏感性,降低了工艺难度并有效改善产品的重复性和可量产性。
附图说明
[0048]
图1是本发明实施例1制备的一种防护绿色激光笔的树脂镜片各层示意图
[0049]
树脂镜片基片1、加硬层2-1和2-2、减反射层3、防水层4-1和4-2;其中,减反射层3包括:包括激光高反膜层3-1(硅铝复合氧化物层3-1-1a、钛铌复合氧化物层3-1-2a、硅铝复合氧化物层3-1-1b、钛铌复合氧化物层3-1-2b、硅铝复合氧化物层3-1-1c、钛铌复合氧化物层3-1-2c、硅铝复合氧化物层3-1-1d、钛铌复合氧化物层3-1-2d、硅铝复合氧化物层3-1-1e、钛铌复合氧化物层3-1-2e、ito层3-1-3、硅铝复合氧化物层3-1-1f)以及激光吸收降背反膜层3-2(cr吸收层3-2-1、钛铌复合氧化物层3-2-2a、硅铝复合氧化物层3-2-3a、钛铌复合氧化物层3-2-2b、硅铝复合氧化物层3-2-3b、钛铌复合氧化物层3-2-2c、ito层3-2-4、硅铝复合氧化物层3-2-3c)
具体实施方式
[0050]
在一个具体的实施方式中,其所述激光高反膜层3-1各层的厚度为:
[0051]
所述第一层硅铝复合氧化物层3-1-1a厚度为0~180nm,优选10~45nm;
[0052]
所述第二层钛铌复合氧化物层3-1-2a厚度为10~120nm,优选40~90nm;
[0053]
所述第三层硅铝复合氧化物层3-1-1b厚度为90~300nm,优选160~270nm;
[0054]
所述第四层钛铌复合氧化物层3-1-2b厚度为7~90nm,优选10~30nm;
[0055]
所述第五层硅铝复合氧化物层3-1-1c厚度为30~240nm,优选100~180nm;
[0056]
所述第六层钛铌复合氧化物层3-1-2c厚度为10~90nm,优选50~80nm;
[0057]
所述第七层硅铝复合氧化物层3-1-1d厚度为20~180nm,优选30~80nm;
[0058]
所述第八层钛铌复合氧化物层3-1-2d厚度为8~80nm,优选10~30nm;
[0059]
所述第九层硅铝复合氧化物层3-1-1e厚度为90~240nm,优选120~200nm;
[0060]
所述第十层钛铌复合氧化物层3-1-2e厚度为8~80nm,优选10~30nm;
[0061]
所述第十一层ito层3-1-3厚度为2~10nm,优选5nm;
[0062]
所述第十二层硅铝复合氧化物层3-1-1f厚度为60~230nm,优选140~220nm;
[0063]
在一个具体的实施方式中,所述激光吸收降背反膜层3-2各层厚度为:
[0064]
所述第一层cr吸收层3-2-1厚度为1~40nm,优选8~25nm;
[0065]
所述第二层钛铌复合氧化物层3-2-2a厚度为8~120nm,优选30~60nm;
[0066]
所述第三层硅铝复合氧化物层3-2-3a厚度为60~220nm,优选80~120nm;
[0067]
所述第四层钛铌复合氧化物层3-2-2b厚度为7~90nm,优选10~40nm;
[0068]
所述第五层硅铝复合氧化物层3-2-3b厚度为10~100nm,优选10~40nm;
[0069]
所述第六层钛铌复合氧化物层3-2-2c厚度为7~120nm,优选30~80nm;
[0070]
所述第七层ito层3-2-4厚度为2~10nm,优选5nm;
[0071]
所述第八层硅铝复合氧化物层3-2-3c厚度为50~150nm,优选60~120nm;
[0072]
在一个具体的实施方式中,s1中,所述制备加硬层2的具体步骤包括:将超声波清洗干净的树脂镜片基片浸入质量百分含量25~30%的加硬液水溶液中,浸渍温度10~20℃,浸渍5秒后以1.0~3.0mm/s的速度提拉出溶液,再将其于70~90℃烘干3小时后将上述基片取出并送至烘干箱内干燥固化,固化温度100~150℃,固化时间120~180min,即所述树脂镜片基片1的凸面1-1和凹面1-2表面分别获得加硬层2-1和加硬层2-2,即得含加硬层2
的树脂镜片;
[0073]
在一个具体的实施方式中,所述步骤s2制备激光高反膜层3-1和防水膜4-1的步骤包括:在真空镀膜机内、采用真空镀膜工艺,将固态膜层材料蒸发后经过气相传输,在s1步骤获得的加硬层2-1表面沉积成薄膜,形成激光高反膜层3-1,再在激光高反膜层3-1表面形成防水膜4-1,具体包括以下步骤:
[0074]
s21:在s1获得的含加硬层2-1的树脂镜片表面交替分别形成五层硅铝复合氧化物层3-1-1a~1e和五层钛铌复合氧化物层3-1-2a~2e,所述第一层硅铝复合氧化物层3-1-1a位于所述加硬层2-1表面,具体包括:
[0075]
s211:在s1获得的含加硬层2-1的树脂镜片表面,在本底真空度≤3
×
10-3
pa、且镀膜舱内温度为50~70℃、有离子源辅助工艺的条件下,采用高能电子束加热硅铝复合氧化物,以速率为将蒸发后的硅铝复合氧化物以纳米级分子形式沉积,获得含第一层硅铝复合氧化物层3-1-1a的树脂镜片;
[0076]
s212:在s211获得的树脂镜片表面,在本底真空度≤3
×
10-3
pa、且镀膜舱内的温度为50~70℃、有离子源辅助工艺的条件下,采用高能电子束加热钛铌复合氧化物,以速率为将蒸发后的钛铌复合氧化物以纳米级分子形式沉积,获得含第二层钛铌复合氧化物层3-1-2a的树脂镜片;
[0077]
s213:重复s211和s212步骤,分别交替形成第三层硅铝复合氧化物层和第四层钛铌复合氧化物层,第五层硅铝复合氧化物层和第六层钛铌复合氧化物层,第七层硅铝复合氧化物层和第八层钛铌复合氧化物层y以及第九层硅铝复合氧化物层和第十层钛铌复合氧化物层,即形成包括第三、五、七、九层硅铝复合氧化物层(即硅铝复合氧化物层3-1-1b~e)、第四、六、八、十层钛铌复合氧化物层(即钛铌复合氧化物层3-1-2b~e)的树脂镜片;
[0078]
s22:在s213获得的树脂镜片表面,在本底真空度≤3
×
10-3
pa、且镀膜舱内的温度为50~70℃、并有离子源辅助工艺的条件下,采用高能电子束加热ito,以速率为将蒸发后的ito以纳米级分子形式沉积,获得含一层ito层3-1-3的树脂镜片;
[0079]
s23:在s22获得的树脂镜片表面,继续采用真空镀膜工艺,重复s211的工艺步骤,形成含硅铝复合氧化物层3-1-1f的树脂镜片;
[0080]
s24:在s23形成的表面所述制备防水层4-1,具体步骤包括:继续采用真空镀膜工艺,在本底真空度≤3
×
10-3
pa、且镀膜舱内的温度为50~70℃条件下,采用高能电子束加热含氟防水材料(优选含有全氟烷(c
12
f
27
n)的防水材料),以速率为将蒸发后的含氟防水材料以纳米级分子形式沉积于所述激光高反膜层3-1表面,形成防水层4-1,即获得含防水层4-1的树脂镜片。
[0081]
在一个具体的实施方式中,所述s3制备激光吸收降背反膜层3-2和防水膜4-2的步骤包括:在真空镀膜机内、采用真空镀膜工艺,将固态膜层材料蒸发后经过气相传输,在s1步骤获得的在加硬层2-2表面沉积成薄膜,形成激光吸收降背反膜层3-2,再在激光吸收降背反膜层3-2表面形成防水膜4-2,具体包括以下步骤:
[0082]
s31:在s1获得的含加硬层2-2的树脂镜片表面,在本底真空度≤3
×
10-3
pa、且镀膜舱内温度为50~70℃、无离子源辅助工艺的条件下,采用高能电子束加热金属cr颗粒,以速率为将蒸发后的cr以纳米级分子形式沉积,形成一层cr吸收层3-2-1,即获得含cr
树脂镜片;
[0083]
s32:在s31获得的含cr树脂镜片表面交替分别形成三层钛铌复合氧化物层3-2-2a~c和二层硅铝复合氧化物层3-2-3a~b,所述第一层钛铌复合氧化物层3-2-2a位于所述加硬层2-2表面,即获得包括三层钛铌复合氧化物层和二层硅铝复合氧化物层的树脂镜片,具体包括:
[0084]
s321:在s31获得的树脂镜片表面,在本底真空度≤3
×
10-3
pa、且镀膜舱内温度为50~70℃、有离子源辅助工艺的条件下,采用高能电子束加热钛铌复合氧化物,以速率为将蒸发后的钛铌复合氧化物以纳米级分子形式沉积,获得含第二层钛铌复合氧化物层3-2-2a的树脂镜片;
[0085]
s322:在s321获得的树脂镜片表面,在本底真空度≤3
×
10-3
pa、且镀膜舱内的温度为50~70℃、有离子源辅助工艺的条件下,采用高能电子束加热硅铝复合氧化物,以速率为将蒸发后的硅铝复合氧化物以纳米级分子形式沉积,获得含第三层硅铝复合氧化物层3-2-3a的树脂镜片;
[0086]
s323:重复s321和s322步骤,分别交替形成第四层钛铌复合氧化物层3-2-2b和第五层硅铝复合氧化物层3-2-3b;
[0087]
s324:再次重复s321步骤,形成第六层钛铌复合氧化物层3-2-2c;
[0088]
s33:在s324获得的树脂镜片表面,在本底真空度≤3
×
10-3
pa、且镀膜舱内的温度为50~70℃、并有离子源辅助工艺的条件下,采用高能电子束加热ito,以速率为将蒸发后的ito以纳米级分子形式沉积,获得第七层含ito层3-2-4的树脂镜片;
[0089]
s34:在s33获得的树脂镜片表面,继续采用真空镀膜工艺,重复s322的工艺步骤,形成含第八层硅铝复合氧化物层3-2-3c的树脂镜片;
[0090]
s35:制备防水层4-2的具体步骤包括:继续采用真空镀膜工艺,在本底真空度≤3
×
10-3
pa、且镀膜舱内的温度为50~70℃条件下,采用高能电子束加热含氟防水材料(优选含有全氟烷(c
12
f
27
n)的防水材料),以速率为将蒸发后的含氟防水材料以纳米级分子形式沉积于激光吸收降背反膜层3-2的表面,形成防水层4-2,即获得含防水层4-2的树脂镜片;
[0091]
在一个具体的实施方式中,所述步骤s2和s3中,离子源辅助沉积工艺参数为:离子源为霍尔源,阳极电压:90~140v,阳极电流:2.5~5a,辅助气为o2,流量为10~30sccm;优选的,所述离子源辅助沉积工艺参数为:离子源为霍尔源,阳极电压:110v,阳极电流:3a,辅助气为o2,流量为15sccm;
[0092]
在一个具体的实施方式中,所述钛铌复合氧化物我们委托常州市瞻驰光电科技股份有限公司开发并生产,钛铌复合氧化物由tio2和nb2o5组成,具体型号(tio2和nb2o5的摩尔分数值)参见实施例和对比例。
[0093]
在一个具体的实施方式中,选取折射率为1.60的树脂镜片作为基片,例如选取其镜片基片制备单体为日本三井化学株式会社的mr-8,以下简称“mr-8”;
[0094]
在一个具体的实施方式中,选取伊藤光学工业株式会社(以下简称为“z117”)型号z117作为加硬液,选择该加硬液制备本发明所述镜片,极大地提高了膜层之间的致密衔接性。
[0095]
(一)实施例
[0096]
实施例1:一种防护绿色激光的树脂镜片
[0097]
1.1材料:镜片基片为mr-8;加硬层为z117;硅铝复合氧化物层:sio2和al2o3摩尔量百分比:92%sio2、8%al2o3,委托常州市瞻驰光电科技股份有限公司开发并生产,材料型号为sa56;钛铌复合氧化物层:tio2和nb2o5摩尔量百分比:80%tio2、20%nb2o5,委托常州市瞻驰光电科技股份有限公司开发并生产,材料型号为ptn28;防水层:采用含有全氟烷(c
12
f
27
n)的防水材料;
[0098]
1.2膜层结构:基片1(凸面1-1和凹面1-2);加硬层2-1和2-2均为2.6~3μm;防激光膜层3包括激光高反膜层3-1和激光吸收降背反膜层3-2,激光高反膜层3-1包括:硅铝复合氧化物层3-1-1a/25.8nm、钛铌复合氧化物层3-1-2a/76.88nm、硅铝复合氧化物层3-1-1b/264.27nm、钛铌复合氧化物层3-1-2b/12.33nm、硅铝复合氧化物层3-1-1c/151.99nm、钛铌复合氧化物层3-1-2c/77.56nm、硅铝复合氧化物层3-1-1d/44.4nm、钛铌复合氧化物层3-1-2d/19.05nm、硅铝复合氧化物层3-1-1e/188.4nm、钛铌复合氧化物层3-1-2e/17.58nm、ito层3-1-3/5nm、硅铝复合氧化物层3-1-1f/204.78nm;激光吸收降背反膜层3-2包括:cr吸收层3-2-1/17.2nm、钛铌复合氧化物层3-2-2a/43.88nm、硅铝复合氧化物层3-2-3a/99.47nm、钛铌复合氧化物层3-2-2b/23.06nm、硅铝复合氧化物层3-2-3b/14.4nm、钛铌复合氧化物层3-2-2c/64.07nm、ito层3-2-4/5nm;硅铝复合氧化物层3-2-3c/82.21nm;防水层4-1和防水层4-2均为10nm;
[0099]
1.3树脂镜片的制备方法包括以下步骤:
[0100]
s1:制作加硬层:将超声波清洗干净的树脂镜片基片浸入质量百分含量27%的加硬液水溶液中,浸渍温度15℃,浸渍5秒后以2.0mm/s的速度提拉出溶液;80℃烘干3小时后将上述基片取出并送至烘干箱内干燥固化,固化温度120℃,固化时间150min,即所述树脂镜片基片1的凸面1-1和凹面1-2表面均获得加硬层,即得含加硬层2-1和2-1的树脂镜片;
[0101]
s2:制备激光高反膜层3-1和防水层4-1的步骤包括:在真空镀膜机内、采用真空镀膜工艺,将固态膜层材料蒸发后经过气相传输,在s1步骤获得的加硬层2-1表面沉积成薄膜,形成激光高反膜层3-1,具体包括以下步骤:
[0102]
s21:在s1获得的含加硬层2-1的树脂镜片表面交替分别形成五层硅铝复合氧化物层3-1-1a~1e和五层钛铌复合氧化物层3-1-2a~2e,所述第一层硅铝复合氧化物层3-1-1a位于所述加硬层2-1表面,具体包括:
[0103]
s211:在s1获得的含加硬层2-1的树脂镜片表面,在本底真空度≤3
×
10-3
pa、且镀膜舱内温度为60℃、有离子源辅助工艺的条件下,采用高能电子束加热硅铝复合氧化物,以速率为将蒸发后的硅铝复合氧化物以纳米级分子形式沉积,获得含第一层硅铝复合氧化物层3-1-1a的树脂镜片;
[0104]
s212:在s211获得的树脂镜片表面,在本底真空度≤3
×
10-3
pa、且镀膜舱内的温度为60℃、有离子源辅助工艺的条件下,采用高能电子束加热钛铌复合氧化物,以速率为将蒸发后的钛铌复合氧化物以纳米级分子形式沉积,获得含第二层钛铌复合氧化物层3-1-2a的树脂镜片;
[0105]
s213:重复s211和s212步骤,分别交替形成第三层硅铝复合氧化物层和第四层钛
铌复合氧化物层,第五层硅铝复合氧化物层和第六层钛铌复合氧化物层,第七层硅铝复合氧化物层和第八层钛铌复合氧化物层以及第九层硅铝复合氧化物层和第十层钛铌复合氧化物层,即形成包括第三、五、七、九层硅铝复合氧化物层(即硅铝复合氧化物层3-1-1b~e)、第四、六、八、十层钛铌复合氧化物层(即钛铌复合氧化物层3-1-2b~e)的树脂镜片;
[0106]
s22:在s213获得的树脂镜片表面,在本底真空度≤3
×
10-3
pa、且镀膜舱内的温度为60℃、并有离子源辅助工艺的条件下,采用高能电子束加热ito,以速率为将蒸发后的ito以纳米级分子形式沉积,获得含一层ito层3-1-3的树脂镜片;
[0107]
s23:在s22获得的树脂镜片表面,继续采用真空镀膜工艺,重复s211的工艺步骤,形成含硅铝复合氧化物层3-1-1f的树脂镜片;
[0108]
s24:在s23获得的树脂镜片表面,继续采用真空镀膜工艺,继续采用真空镀膜工艺,在本底真空度≤3
×
10-3
pa、且镀膜舱内的温度为60℃条件下,采用高能电子束加热含氟防水材料(优选含有全氟烷(c
12
f
27
n)的防水材料),以速率为将蒸发后的含氟防水材料以纳米级分子形式沉积于所述激光高反膜层3-1的表面,形成防水层4-1,即获得含防水层4-1的树脂镜片。
[0109]
s3:制备激光吸收降背反膜层3-2和防水层4-2的步骤包括:在真空镀膜机内、采用真空镀膜工艺,将固态膜层材料蒸发后经过气相传输,在s1步骤获得的在加硬层2-2表面沉积成薄膜,形成激光吸收降背反膜层3-2和防水层4-2,具体包括以下步骤:
[0110]
s31:在s1获得的含加硬层2-2的树脂镜片表面,在本底真空度≤3
×
10-3
pa、且镀膜舱内温度为60℃、无离子源辅助工艺的条件下,采用高能电子束加热金属cr颗粒,以速率为将蒸发后的cr以纳米级分子形式沉积,形成第一层cr吸收层3-2-1,即获得含cr树脂镜片;
[0111]
s32:在s31获得的含cr树脂镜片表面交替分别形成三层钛铌复合氧化物层3-2-2a~c和二层硅铝复合氧化物层3-2-3a~b,所述第一层钛铌复合氧化物层3-2-2a位于所述加硬层2-2表面,即获得包括三层钛铌复合氧化物层和二层硅铝复合氧化物层的树脂镜片,具体包括:
[0112]
s321:在s31获得的树脂镜片表面,在本底真空度≤3
×
10-3
pa、且镀膜舱内温度为60℃、有离子源辅助工艺的条件下,采用高能电子束加热钛铌复合氧化物,以速率为将蒸发后的钛铌复合氧化物以纳米级分子形式沉积,获得含第二层钛铌复合氧化物层3-2-2a的树脂镜片;
[0113]
s322:在s321获得的树脂镜片表面,在本底真空度≤3
×
10-3
pa、且镀膜舱内的温度为60℃、有离子源辅助工艺的条件下,采用高能电子束加热硅铝复合氧化物,以速率为将蒸发后的硅铝复合氧化物以纳米级分子形式沉积,获得含第三层硅铝复合氧化物层3-2-3a的树脂镜片;
[0114]
s323:重复s321和s322步骤,分别交替形成第四层钛铌复合氧化物层3-2-2b和第五层硅铝复合氧化物层3-2-3b;
[0115]
s324:再重复s321步骤,形成第六层钛铌复合氧化物层3-2-2c;
[0116]
s33:在s32获得的树脂镜片表面,在本底真空度≤3
×
10-3
pa、且镀膜舱内的温度为
60℃、并有离子源辅助工艺的条件下,采用高能电子束加热ito,以速率为将蒸发后的ito以纳米级分子形式沉积,获得第七层含ito层3-2-4的树脂镜片;
[0117]
s34:在s33获得的树脂镜片表面,继续采用真空镀膜工艺,重复s252的工艺步骤,形成含第八层硅铝复合氧化物层3-2-3c的树脂镜片;
[0118]
s35:制备防水层4-2:继续采用真空镀膜工艺,在本底真空度≤3
×
10-3
pa、且镀膜舱内的温度为60℃条件下,采用高能电子束加热含有全氟烷(c
12
f
27
n)的防水材料,以速率为将蒸发后的含氟防水材料以纳米级分子形式沉积于激光吸收降背反膜层3-2的表面,形成防水层4-2,即得;
[0119]
其中,所述步骤s2和s3中,离子源辅助沉积工艺参数为:离子源为霍尔源,阳极电压:110v,阳极电流:3a,辅助气为o2,流量为15sccm。
[0120]
实施例2:一种防护绿色激光的树脂镜片
[0121]
2.1材料:镜片基片为mr-8;加硬层为z117;硅铝复合氧化物层:sio2和al2o3摩尔量百分比:92%sio2、8%al2o3,委托常州市瞻驰光电科技股份有限公司开发并生产,材料型号为sa56;钛铌复合氧化物层:tio2和nb2o5摩尔量百分比:50%tio2、50%nb2o5,委托常州市瞻驰光电科技股份有限公司开发并生产,材料型号为ptn55;防水层:采用含有全氟烷(c
12
f
27
n)的防水材料;
[0122]
2.2膜层结构:基片1(凸面1-1和凹面1-2);加硬层2-1和2-2均为2.6~3μm;1.2膜层结构:基片1(凸面1-1和凹面1-2);加硬层2-1和2-2均为2.6~3μm;防激光膜层3包括激光高反膜层3-1和激光吸收降背反膜层3-2,激光高反膜层3-1包括:硅铝复合氧化物层3-1-1a/25.8nm、钛铌复合氧化物层3-1-2a/76.88nm、硅铝复合氧化物层3-1-1b/264.27nm、钛铌复合氧化物层3-1-2b/12.33nm、硅铝复合氧化物层3-1-1c/151.99nm、钛铌复合氧化物层3-1-2c/77.56nm、硅铝复合氧化物层3-1-1d/44.4nm、钛铌复合氧化物层3-1-2d/19.05nm、硅铝复合氧化物层3-1-1e/188.4nm、钛铌复合氧化物层3-1-2e/17.58nm、ito层3-1-3/5nm、硅铝复合氧化物层3-1-1f/204.78nm;激光吸收降背反膜层3-2包括:cr吸收层3-2-1/17.2nm、钛铌复合氧化物层3-2-2a/43.88nm、硅铝复合氧化物层3-2-3a/99.47nm、钛铌复合氧化物层3-2-2b/23.06nm、硅铝复合氧化物层3-2-3b/14.4nm、钛铌复合氧化物层3-2-2c/64.07nm、ito层3-2-4/5nm;硅铝复合氧化物层3-2-3c/82.21nm;防水层4-1和防水层4-2均为10nm;
[0123]
2.3树脂镜片的制备方法同实施例1。
[0124]
实施例3:一种防护绿色激光的树脂镜片
[0125]
3.1材料:镜片基片为mr-8;加硬层为z117;硅铝复合氧化物层:sio2和al2o3摩尔量百分比:92%sio2、8%al2o3,委托常州市瞻驰光电科技股份有限公司开发并生产,材料型号为sa56;钛铌复合氧化物层:tio2和nb2o5摩尔量百分比:20%tio2、80%nb2o5,委托常州市瞻驰光电科技股份有限公司开发并生产,材料型号为ptn57;防水层:采用含有全氟烷(c
12
f
27
n)的防水材料;
[0126]
2.2膜层结构:基片1(凸面1-1和凹面1-2);加硬层2-1和2-2均为2.6~3μm;1.2膜层结构:基片1(凸面1-1和凹面1-2);加硬层2-1和2-2均为2.6~3μm;防激光膜层3包括激光高反膜层3-1和激光吸收降背反膜层3-2,激光高反膜层3-1包括:硅铝复合氧化物层3-1-1a/26.4nm、钛铌复合氧化物层3-1-2a/76.97nm、硅铝复合氧化物层3-1-1b/266.19nm、钛铌
复合氧化物层3-1-2b/14.27nm、硅铝复合氧化物层3-1-1c/150.82nm、钛铌复合氧化物层3-1-2c/77.71nm、硅铝复合氧化物层3-1-1d/44.43nm、钛铌复合氧化物层3-1-2d/19.47nm、硅铝复合氧化物层3-1-1e/186.53nm、钛铌复合氧化物层3-1-2e/19.71nm、ito层3-1-3/5nm、硅铝复合氧化物层3-1-1f/205.86nm;激光吸收降背反膜层3-2包括:cr吸收层3-2-1/17.2nm、钛铌复合氧化物层3-2-2a/43.88nm、硅铝复合氧化物层3-2-3a/99.47nm、钛铌复合氧化物层3-2-2b/23.06nm、硅铝复合氧化物层3-2-3b/14.4nm、钛铌复合氧化物层3-2-2c/64.07nm、ito层3-2-4/5nm;硅铝复合氧化物层3-2-3c/82.21nm;防水层4-1和防水层4-2均为10nm;
[0127]
2.3树脂镜片的制备方法同实施例1。
[0128]
实施例4:一种防护绿色激光的树脂镜片
[0129]
3.1材料:镜片基片为mr-8;加硬层为z117;硅铝复合氧化物层:sio2和al2o3摩尔量百分比:80%sio2、20%al2o3,委托常州市瞻驰光电科技股份有限公司开发并生产,材料型号为sa86;钛铌复合氧化物层:tio2和nb2o5摩尔量百分比:80%tio2、20%nb2o5,委托常州市瞻驰光电科技股份有限公司开发并生产,材料型号为ptn28;防水层:采用含有全氟烷(c
12
f
27
n)的防水材料;
[0130]
2.2膜层结构:基片1(凸面1-1和凹面1-2);加硬层2-1和2-2均为2.6~3μm;1.2膜层结构:基片1(凸面1-1和凹面1-2);加硬层2-1和2-2均为2.6~3μm;防激光膜层3包括激光高反膜层3-1和激光吸收降背反膜层3-2,激光高反膜层3-1包括:硅铝复合氧化物层3-1-1a/25.8nm、钛铌复合氧化物层3-1-2a/76.88nm、硅铝复合氧化物层3-1-1b/264.27nm、钛铌复合氧化物层3-1-2b/12.33nm、硅铝复合氧化物层3-1-1c/151.99nm、钛铌复合氧化物层3-1-2c/77.56nm、硅铝复合氧化物层3-1-1d/44.4nm、钛铌复合氧化物层3-1-2d/19.05nm、硅铝复合氧化物层3-1-1e/188.4nm、钛铌复合氧化物层3-1-2e/17.58nm、ito层3-1-3/5nm、硅铝复合氧化物层3-1-1f/204.78nm;激光吸收降背反膜层3-2包括:cr吸收层3-2-1/17.2nm、钛铌复合氧化物层3-2-2a/43.88nm、硅铝复合氧化物层3-2-3a/99.47nm、钛铌复合氧化物层3-2-2b/23.06nm、硅铝复合氧化物层3-2-3b/14.4nm、钛铌复合氧化物层3-2-2c/64.07nm、ito层3-2-4/5nm;硅铝复合氧化物层3-2-3c/82.21nm;防水层4-1和防水层4-2均为10nm;
[0131]
2.3树脂镜片的制备方法同实施例1。
[0132]
(二)对比例
[0133]
对比例1:一种带激光高反膜的树脂镜片
[0134]
2.1镜片基片为mr-8;凸面材料:加硬层为z117;低折射率:sio2层;高折射率:zro2层;防水层:采用含有全氟烷(c
12
f
27
n)的防水材料;凹面材料:同实施例1;
[0135]
2.2膜层结构:基片1(凸面1-1和凹面1-2);加硬层2-1和2-2均为2.6~3μm;1.2膜层结构:基片1(凸面1-1和凹面1-2);加硬层2-1和2-2均为2.6~3μm;防激光膜层3包括激光高反膜层3-1包括:sio2层3-1-1a/29.2nm、zro2层3-1-2a/74.6nm、sio2层3-1-1b/277.49nm、zro2层3-1-2b/29nm、sio2层3-1-1c/143.99nm、zro2层3-1-2c/68.64nm、sio2层3-1-1d/52.78nm、zro2层3-1-2d/15.3nm、sio2层3-1-1e/187.7nm、zro2层3-1-2e/42.06nm、ito层3-1-3/5nm、sio2层3-1-1f/200.34nm;防水层4-1为10nm;激光吸收降背反膜层3-2,包括:cr吸收层3-2-1/17.2nm、钛铌复合氧化物层3-2-2a/43.88nm、硅铝复合氧化物层3-2-3a/
99.47nm、钛铌复合氧化物层3-2-2b/23.06nm、硅铝复合氧化物层3-2-3b/14.4nm、钛铌复合氧化物层3-2-2c/64.07nm、ito层3-2-4/5nm;硅铝复合氧化物层3-2-3c/82.21nm;防水层4-2为10nm;
[0136]
2.3树脂镜片的制备方法包括以下步骤:
[0137]
s1:制作加硬层:将超声波清洗干净的树脂镜片基片浸入质量百分含量27%的加硬液水溶液中,浸渍温度15℃,浸渍5秒后以2.0mm/s的速度提拉出溶液;80℃烘干3小时后将上述基片取出并送至烘干箱内干燥固化,固化温度120℃,固化时间150min,即所述树脂镜片基片1的凸面1-1和凹面1-2表面均获得加硬层,即得含加硬层2-1和2-1的树脂镜片;
[0138]
s2:制备防激光膜层3-1和防水层4-1:在真空镀膜机内、采用真空镀膜工艺,将固态膜层材料蒸发后经过气相传输,在s1步骤获得的加硬层2-1表面沉积成薄膜,形成激光高反膜层3-1,具体包括以下步骤:
[0139]
s21:在s1获得的含加硬层2-1的树脂镜片表面交替分别形成五层sio2层3-1-1a~1e和五层zro2层3-1-2a~2e,所述第一层sio2层3-1-1a位于所述加硬层2-1表面,具体包括:
[0140]
s211:在s1获得的含加硬层2-1的树脂镜片表面,在本底真空度≤3
×
10-3
pa、且镀膜舱内温度为60℃、无离子源辅助工艺的条件下,采用高能电子束加热sio2,以速率为将蒸发后的sio2以纳米级分子形式沉积,获得含第一层sio2层3-1-1a的树脂镜片;
[0141]
s212:在s211获得的树脂镜片表面,在本底真空度≤3
×
10-3
pa、且镀膜舱内的温度为60℃、无离子源辅助工艺的条件下,采用高能电子束加热zro2,以速率为将蒸发后的zro2以纳米级分子形式沉积,获得含第二层zro2层3-1-2a的树脂镜片;
[0142]
s213:重复s211和s212步骤,分别交替形成包括第三、五、七、九层sio2层(即sio2层3-1-1b~e)、第四、六、八、十层zro2层(即zro2层3-1-2b~e)的树脂镜片;
[0143]
s22:在s213获得的树脂镜片表面,在本底真空度≤3
×
10-3
pa、且镀膜舱内的温度为60℃、并有离子源辅助工艺的条件下,采用高能电子束加热ito,以速率为将蒸发后的ito以纳米级分子形式沉积,获得含第十一层ito层3-1-3的树脂镜片;
[0144]
s23:在s22获得的树脂镜片表面,继续采用真空镀膜工艺,重复s211的工艺步骤,形成含sio2层3-1-1f的树脂镜片;
[0145]
s24:在s23获得的树脂镜片表面,继续采用真空镀膜工艺,继续采用真空镀膜工艺,在本底真空度≤3
×
10-3
pa、且镀膜舱内的温度为60℃条件下,采用高能电子束加热含全氟烷(c
12
f
27
n)的防水材料,以速率为将蒸发后的含氟防水材料以纳米级分子形式沉积于所述激光高反膜层3-1的表面,形成防水层4-1,即获得含防水层4-1的树脂镜片;
[0146]
s3:制备激光吸收降背反膜层3-2和防水层4-2的步骤包括:在真空镀膜机内、采用真空镀膜工艺,将固态膜层材料蒸发后经过气相传输,在s1步骤获得的在加硬层2-2表面沉积成薄膜,形成激光吸收降背反膜层3-2和防水层4-2,具体包括以下步骤:
[0147]
s31:在s1获得的含加硬层2-2的树脂镜片表面,在本底真空度≤3
×
10-3
pa、且镀膜舱内温度为60℃、无离子源辅助工艺的条件下,采用高能电子束加热金属cr颗粒,以速率为将蒸发后的cr以纳米级分子形式沉积,形成第一层cr吸收层3-2-1,即获得含cr树脂镜片;
[0148]
s32:在s31获得的含cr树脂镜片表面交替分别形成三层钛铌复合氧化物层3-2-2a
~c和二层硅铝复合氧化物层3-2-3a~b,所述第一层钛铌复合氧化物层3-2-2a位于所述加硬层2-2表面,即获得包括三层钛铌复合氧化物层和二层硅铝复合氧化物层的树脂镜片,具体包括:
[0149]
s321:在s31获得的树脂镜片表面,在本底真空度≤3
×
10-3
pa、且镀膜舱内温度为60℃、有离子源辅助工艺的条件下,采用高能电子束加热钛铌复合氧化物,以速率为将蒸发后的钛铌复合氧化物以纳米级分子形式沉积,获得含第二层钛铌复合氧化物层3-2-2a的树脂镜片;
[0150]
s322:在s321获得的树脂镜片表面,在本底真空度≤3
×
10-3
pa、且镀膜舱内的温度为60℃、有离子源辅助工艺的条件下,采用高能电子束加热硅铝复合氧化物,以速率为将蒸发后的硅铝复合氧化物以纳米级分子形式沉积,获得含第三层硅铝复合氧化物层3-2-3a的树脂镜片;
[0151]
s323:重复s321和s322步骤,分别交替形成第四层钛铌复合氧化物层3-2-2b和第五层硅铝复合氧化物层3-2-3b;
[0152]
s324:再重复s321步骤,形成第六层钛铌复合氧化物层3-2-2c;
[0153]
s33:在s32获得的树脂镜片表面,在本底真空度≤3
×
10-3
pa、且镀膜舱内的温度为60℃、并有离子源辅助工艺的条件下,采用高能电子束加热ito,以速率为将蒸发后的ito以纳米级分子形式沉积,获得第七层含ito层3-2-4的树脂镜片;
[0154]
s34:在s33获得的树脂镜片表面,继续采用真空镀膜工艺,重复s252的工艺步骤,形成含第八层硅铝复合氧化物层3-2-3c的树脂镜片;
[0155]
s35:制备防水层4-2:继续采用真空镀膜工艺,在本底真空度≤3
×
10-3
pa、且镀膜舱内的温度为60℃条件下,采用高能电子束加热含有全氟烷(c
12
f
27
n)的防水材料,以速率为将蒸发后的含氟防水材料以纳米级分子形式沉积于激光吸收降背反膜层3-2的表面,形成防水层4-2,即得。
[0156]
对比例2:一种带激光高反膜的树脂镜片
[0157]
1.1镜片基片为mr-8;加硬层为z117;凸面镀膜材料:硅铝复合氧化物层:sio2和al2o3摩尔量百分比:92%sio2、8%al2o3,委托常州市瞻驰光电科技股份有限公司开发并生产,材料型号为sa56;高折射率材料:tio2层;防水层:采用含有全氟烷(c
12
f
27
n)的防水材料;凹面镀膜材料:采用与实施例1相同的材料;
[0158]
1.2膜层结构:基片1(凸面1-1和凹面1-2);加硬层2-1和2-2均为2.6~3μm;防激光膜层3包括激光高反膜层3-1,激光高反膜层3-1包括:硅铝复合氧化物层3-1-1a/25.8nm、tio2层3-1-2a/76.88nm、硅铝复合氧化物层3-1-1b/264.27nm、tio2层3-1-2b/12.33nm、硅铝复合氧化物层3-1-1c/151.99nm、tio2层3-1-2c/77.56nm、硅铝复合氧化物层3-1-1d/44.4nm、tio2层3-1-2d/19.05nm、硅铝复合氧化物层3-1-1e/188.4nm、tio2层3-1-2e/17.58nm、ito层3-1-3/5nm、硅铝复合氧化物层3-1-1f/204.78nm;防水层4-1为10nm;激光吸收降背反膜层3-2,包括:cr吸收层3-2-1/17.2nm、钛铌复合氧化物层3-2-2a/43.88nm、硅铝复合氧化物层3-2-3a/99.47nm、钛铌复合氧化物层3-2-2b/23.06nm、硅铝复合氧化物层3-2-3b/14.4nm、钛铌复合氧化物层3-2-2c/64.07nm、ito层3-2-4/5nm;硅铝复合氧化物层3-2-3c/82.21nm;防水层4-2为10nm;
[0159]
2.3树脂镜片的制备方法包括以下步骤:
[0160]
s1:制作加硬层:将超声波清洗干净的树脂镜片基片浸入质量百分含量27%的加硬液水溶液中,浸渍温度15℃,浸渍5秒后以2.0mm/s的速度提拉出溶液;80℃烘干3小时后将上述基片取出并送至烘干箱内干燥固化,固化温度120℃,固化时间150min,即所述树脂镜片基片1的凸面1-1和凹面1-2表面均获得加硬层,即得含加硬层2-1和2-1的树脂镜片;
[0161]
s2:制备防激光膜层3-1和防水层4-1:在真空镀膜机内、采用真空镀膜工艺,将固态膜层材料蒸发后经过气相传输,在s1步骤获得的在加硬层2-1表面沉积成薄膜,形成激光高反膜层3-1和防水层4-1,具体包括以下步骤:
[0162]
s21:在s1获得的含加硬层2-1的树脂镜片表面交替分别形成五层硅铝复合氧化物层3-1-1a~1e和五层tio2层3-1-2a~2e,所述第一层硅铝复合氧化物层3-1-1a位于所述加硬层2-1表面,具体包括:
[0163]
s211:在s1获得的含加硬层2-1的树脂镜片表面,在本底真空度≤3
×
10-3
pa、且镀膜舱内温度为60℃、有离子源辅助工艺的条件下,采用高能电子束加热硅铝复合氧化物,以速率为将蒸发后的硅铝复合氧化物以纳米级分子形式沉积,获得含第一层硅铝复合氧化物层3-1-1a的树脂镜片;
[0164]
s212:在s211获得的树脂镜片表面,在本底真空度≤3
×
10-3
pa、且镀膜舱内的温度为60℃、有离子源辅助工艺的条件下,采用高能电子束加热tio2,以速率为将蒸发后的tio2以纳米级分子形式沉积,获得含第二层tio2层3-1-2a的树脂镜片;
[0165]
s213:重复s211和s212步骤,分别交替形成包括第三、五、七、九层硅铝复合氧化物层(即硅铝复合氧化物层3-1-1b~e)、第四、六、八、十层tio2层(即tio2层3-1-2b~e)的树脂镜片;
[0166]
s22:在s213获得的树脂镜片表面,在本底真空度≤3
×
10-3
pa、且镀膜舱内的温度为60℃、并有离子源辅助工艺的条件下,采用高能电子束加热ito,以速率为将蒸发后的ito以纳米级分子形式沉积,获得含第十一层ito层3-1-3的树脂镜片;
[0167]
s23:在s22获得的树脂镜片表面,继续采用真空镀膜工艺,重复s211的工艺步骤,形成含第十二层硅铝复合氧化物层3-1-1f的树脂镜片;
[0168]
s24:在s23获得的树脂镜片表面,继续采用真空镀膜工艺,继续采用真空镀膜工艺,在本底真空度≤3
×
10-3
pa、且镀膜舱内的温度为60℃条件下,采用高能电子束加热含全氟烷(c
12
f
27
n)的防水材料,以速率为将蒸发后的含氟防水材料以纳米级分子形式沉积于所述激光高反膜层3-1的表面,形成防水层4-1,即获得含防水层4-1的树脂镜片;
[0169]
s3:制备激光吸收降背反膜层3-2和防水层4-2的步骤包括:在真空镀膜机内、采用真空镀膜工艺,将固态膜层材料蒸发后经过气相传输,在s1步骤获得的在加硬层2-2表面沉积成薄膜,形成激光吸收降背反膜层3-2和防水层4-2,具体包括以下步骤:
[0170]
s31:在s1获得的含加硬层2-2的树脂镜片表面,在本底真空度≤3
×
10-3
pa、且镀膜舱内温度为60℃、无离子源辅助工艺的条件下,采用高能电子束加热金属cr颗粒,以速率为将蒸发后的cr以纳米级分子形式沉积,形成第一层cr吸收层3-2-1,即获得含cr树脂镜片;
[0171]
s32:在s31获得的含cr树脂镜片表面交替分别形成三层钛铌复合氧化物层3-2-2a
~c和二层硅铝复合氧化物层3-2-3a~b,所述第一层钛铌复合氧化物层3-2-2a位于所述加硬层2-2表面,即获得包括三层钛铌复合氧化物层和二层硅铝复合氧化物层的树脂镜片,具体包括:
[0172]
s321:在s31获得的树脂镜片表面,在本底真空度≤3
×
10-3
pa、且镀膜舱内温度为60℃、有离子源辅助工艺的条件下,采用高能电子束加热钛铌复合氧化物,以速率为将蒸发后的钛铌复合氧化物以纳米级分子形式沉积,获得含第二层钛铌复合氧化物层3-2-2a的树脂镜片;
[0173]
s322:在s321获得的树脂镜片表面,在本底真空度≤3
×
10-3
pa、且镀膜舱内的温度为60℃、有离子源辅助工艺的条件下,采用高能电子束加热硅铝复合氧化物,以速率为将蒸发后的硅铝复合氧化物以纳米级分子形式沉积,获得含第三层硅铝复合氧化物层3-2-3a的树脂镜片;
[0174]
s323:重复s321和s322步骤,分别交替形成第四层钛铌复合氧化物层3-2-2b和第五层硅铝复合氧化物层3-2-3b;
[0175]
s324:再重复s321步骤,形成第六层钛铌复合氧化物层3-2-2c;
[0176]
s33:在s32获得的树脂镜片表面,在本底真空度≤3
×
10-3
pa、且镀膜舱内的温度为60℃、并有离子源辅助工艺的条件下,采用高能电子束加热ito,以速率为将蒸发后的ito以纳米级分子形式沉积,获得第七层含ito层3-2-4的树脂镜片;
[0177]
s34:在s33获得的树脂镜片表面,继续采用真空镀膜工艺,重复s252的工艺步骤,形成含第八层硅铝复合氧化物层3-2-3c的树脂镜片;
[0178]
s35:制备防水层4-2:继续采用真空镀膜工艺,在本底真空度≤3
×
10-3
pa、且镀膜舱内的温度为60℃条件下,采用高能电子束加热含有全氟烷(c
12
f
27
n)的防水材料,以速率为将蒸发后的含氟防水材料以纳米级分子形式沉积于激光吸收降背反膜层3-2的表面,形成防水层4-2,即得;
[0179]
其中,所述步骤s2和s3中,离子源辅助沉积工艺参数为:离子源为霍尔源,阳极电压:110v,阳极电流:3a,辅助气为o2,流量为15sccm。
[0180]
对比例3:一种带激光高反膜的树脂镜片
[0181]
1.1镜片基片为mr-8;加硬层为z117;凸面镀膜材料:低折射率材料层:sio2;高折射率材料:tio2层;防水层:采用含有全氟烷(c
12
f
27
n)的防水材料;凹面采用与实施例1相同的材料;
[0182]
1.2膜层结构:基片1(凸面1-1和凹面1-2);加硬层2-1和2-2均为2.6~3μm;防激光膜层3包括激光高反膜层3-1,激光高反膜层3-1包括:sio2层3-1-1a/25.8nm、tio2层3-1-2a/76.88nm、sio2层3-1-1b/264.27nm、tio2层3-1-2b/12.33nm、sio2层3-1-1c/151.99nm、tio2层3-1-2c/77.56nm、sio2层3-1-1d/44.4nm、tio2层3-1-2d/19.05nm、sio2层3-1-1e/188.4nm、tio2层3-1-2e/17.58nm、ito层3-1-3/5nm、sio2层3-1-1f/204.78nm;防水层4-1为10nm;凹面为激光吸收降背反膜层3-2,包括:cr吸收层3-2-1/17.2nm、钛铌复合氧化物层3-2-2a/43.88nm、硅铝复合氧化物层3-2-3a/99.47nm、钛铌复合氧化物层3-2-2b/23.06nm、硅铝复合氧化物层3-2-3b/14.4nm、钛铌复合氧化物层3-2-2c/64.07nm、ito层3-2-4/5nm;硅铝复合氧化物层3-2-3c/82.21nm;防水层4-2为10nm;
[0183]
2.3树脂镜片的制备方法包括以下步骤:
[0184]
s1:制作加硬层:将超声波清洗干净的树脂镜片基片浸入质量百分含量27%的加硬液水溶液中,浸渍温度15℃,浸渍5秒后以2.0mm/s的速度提拉出溶液;80℃烘干3小时后将上述基片取出并送至烘干箱内干燥固化,固化温度120℃,固化时间150min,即所述树脂镜片基片1的凸面1-1和凹面1-2表面均获得加硬层,即得含加硬层2-1和2-1的树脂镜片;
[0185]
s2:制备激光高反膜层3-1和防水层4-1的步骤包括:在真空镀膜机内、采用真空镀膜工艺,将固态膜层材料蒸发后经过气相传输,在s1步骤获得的加硬层2-1表面沉积成薄膜,形成激光高反膜层3-1,具体包括以下步骤:
[0186]
s21:在s1获得的含加硬层2-1的树脂镜片表面交替分别形成五层sio2层3-1-1a~1e和五层tio2层3-1-2a~2e,所述第一层sio2层3-1-1a位于所述加硬层2-1表面,具体包括:
[0187]
s211:在s1获得的含加硬层2-1的树脂镜片表面,在本底真空度≤3
×
10-3
pa、且镀膜舱内温度为60℃、有离子源辅助工艺的条件下,采用高能电子束加热sio2,以速率为将蒸发后的sio2以纳米级分子形式沉积,获得含第一层sio2层3-1-1a的树脂镜片;
[0188]
s212:在s211获得的树脂镜片表面,在本底真空度≤3
×
10-3
pa、且镀膜舱内的温度为60℃、有离子源辅助工艺的条件下,采用高能电子束加热tio2,以速率为将蒸发后的tio2以纳米级分子形式沉积,获得含第二层tio2层3-1-2a的树脂镜片;
[0189]
s213:重复s211和s212步骤,分别交替形成包括第三、五、七、九层sio2层(即sio2层3-1-1b~e)、第四、六、八、十层tio2层(即tio2层3-1-2b~e)的树脂镜片;
[0190]
s22:在s213获得的树脂镜片表面,在本底真空度≤3
×
10-3
pa、且镀膜舱内的温度为60℃、并有离子源辅助工艺的条件下,采用高能电子束加热ito,以速率为将蒸发后的ito以纳米级分子形式沉积,获得含第十一层ito层3-1-3的树脂镜片;
[0191]
s23:在s22获得的树脂镜片表面,继续采用真空镀膜工艺,重复s211的工艺步骤,形成含第十二层sio2层3-1-1f的树脂镜片;
[0192]
s24:在s23获得的树脂镜片表面,继续采用真空镀膜工艺,继续采用真空镀膜工艺,在本底真空度≤3
×
10-3
pa、且镀膜舱内的温度为60℃条件下,采用高能电子束加热含全氟烷(c
12
f
27
n)的防水材料,以速率为将蒸发后的含氟防水材料以纳米级分子形式沉积于所述激光高反膜层3-1的表面,形成防水层4-1,即获得含防水层4-1的树脂镜片;
[0193]
s3:制备激光吸收降背反膜层3-2和防水层4-2的步骤:同实施例1的s3步骤;
[0194]
其中,所述步骤s2和s3中,离子源辅助沉积工艺参数为:离子源为霍尔源,阳极电压:110v,阳极电流:3a,辅助气为o2,流量为15sccm。
[0195]
对比例4:一种带激光高反膜的树脂镜片
[0196]
1.1镜片基片为mr-8;加硬层为z117;凸面镀膜材料:低折射率材料层:sio2;钛铌复合氧化物层:tio2和nb2o5摩尔量百分比:80%tio2、20%nb2o5,委托常州市瞻驰光电科技股份有限公司开发并生产,材料型号为ptn28;防水层:采用含有全氟烷(c
12
f
27
n)的防水材料;凹面镀膜采用与实施例1相同的材料;
[0197]
1.2膜层结构:基片1(凸面1-1和凹面1-2);加硬层2-1和2-2均为2.6~3μm;防激光膜层3包括激光高反膜层3-1,激光高反膜层3-1包括:sio2层3-1-1a/25.8nm、钛铌复合氧化物层3-1-2a/76.88nm、sio2层3-1-1b/264.27nm、钛铌复合氧化物层3-1-2b/12.33nm、sio2层
3-1-1c/151.99nm、钛铌复合氧化物层3-1-2c/77.56nm、sio2层3-1-1d/44.4nm、钛铌复合氧化物层3-1-2d/19.05nm、sio2层3-1-1e/188.4nm、钛铌复合氧化物层3-1-2e/17.58nm、ito层3-1-3/5nm、sio2层3-1-1f/204.78nm;防水层4-1为10nm;凹面为激光吸收降背反膜层3-2,包括:cr吸收层3-2-1/17.2nm、钛铌复合氧化物层3-2-2a/43.88nm、硅铝复合氧化物层3-2-3a/99.47nm、钛铌复合氧化物层3-2-2b/23.06nm、硅铝复合氧化物层3-2-3b/14.4nm、钛铌复合氧化物层3-2-2c/64.07nm、ito层3-2-4/5nm;硅铝复合氧化物层3-2-3c/82.21nm;防水层4-2为10nm;
[0198]
2.3树脂镜片的制备方法包括以下步骤:
[0199]
s1:制作加硬层:将超声波清洗干净的树脂镜片基片浸入质量百分含量27%的加硬液水溶液中,浸渍温度15℃,浸渍5秒后以2.0mm/s的速度提拉出溶液;80℃烘干3小时后将上述基片取出并送至烘干箱内干燥固化,固化温度120℃,固化时间150min,即所述树脂镜片基片1的凸面1-1和凹面1-2表面均获得加硬层,即得含加硬层2-1和2-1的树脂镜片;
[0200]
s2:制备激光高反膜层3-1和防水层4-1的步骤包括:在真空镀膜机内、采用真空镀膜工艺,将固态膜层材料蒸发后经过气相传输,在s1步骤获得的加硬层2-1表面沉积成薄膜,形成激光高反膜层3-1,具体包括以下步骤:
[0201]
s21:在s1获得的含加硬层2-1的树脂镜片表面交替分别形成五层sio2层3-1-1a~1e和五层钛铌复合氧化物层3-1-2a~2e,所述第一层sio2层3-1-1a位于所述加硬层2-1表面,具体包括:
[0202]
s211:在s1获得的含加硬层2-1的树脂镜片表面,在本底真空度≤3
×
10-3
pa、且镀膜舱内温度为60℃、有离子源辅助工艺的条件下,采用高能电子束加热sio2,以速率为将蒸发后的sio2以纳米级分子形式沉积,获得含第一层sio2层3-1-1a的树脂镜片;
[0203]
s212:在s211获得的树脂镜片表面,在本底真空度≤3
×
10-3
pa、且镀膜舱内的温度为60℃、有离子源辅助工艺的条件下,采用高能电子束加热钛铌复合氧化物,以速率为将蒸发后的钛铌复合氧化物以纳米级分子形式沉积,获得含第二层钛铌复合氧化物层3-1-2a的树脂镜片;
[0204]
s213:重复s211和s212步骤,分别交替形成包括第三、五、七、九层sio2层(即sio2层3-1-1b~e)、第四、六、八、十层钛铌复合氧化物层(即钛铌复合氧化物层3-1-2b~e)的树脂镜片;
[0205]
s22:在s213获得的树脂镜片表面,在本底真空度≤3
×
10-3
pa、且镀膜舱内的温度为60℃、并有离子源辅助工艺的条件下,采用高能电子束加热ito,以速率为将蒸发后的ito以纳米级分子形式沉积,获得含第十一层ito层3-1-3的树脂镜片;
[0206]
s23:在s22获得的树脂镜片表面,继续采用真空镀膜工艺,重复s211的工艺步骤,形成含sio2层3-1-1f的树脂镜片;
[0207]
s24:在s23获得的树脂镜片表面,继续采用真空镀膜工艺,继续采用真空镀膜工艺,在本底真空度≤3
×
10-3
pa、且镀膜舱内的温度为60℃条件下,采用高能电子束加热含全氟烷(c
12
f
27
n)的防水材料,以速率为将蒸发后的含氟防水材料以纳米级分子形式沉积于所述激光高反膜层3-1的表面,形成防水层4-1,即获得含防水层4-1的树脂镜片;
[0208]
s3制备激光吸收降背反膜层3-2和防水层4-2的步骤包括:同实施例1的s3步骤;
[0209]
其中,所述步骤s2和s3中,离子源辅助沉积工艺参数为:离子源为霍尔源,阳极电压:110v,阳极电流:3a,辅助气为o2,流量为15sccm。
[0210]
对比例5:一种带激光高反膜的树脂镜片
[0211]
1.1镜片基片为mr-8;加硬层为z117;凸面镀膜材料:镜片基片为mr-8;加硬层为z117;硅铝复合氧化物层:sio2和al2o3摩尔量百分比:92%sio2、8%al2o3,委托常州市瞻驰光电科技股份有限公司开发并生产,材料型号为sa56;高折射率材料:nb2o5层;防水层:采用含有全氟烷(c
12
f
27
n)的防水材料;凹面镀膜采用与实施例1相同的材料;
[0212]
1.2膜层结构:基片1(凸面1-1和凹面1-2);加硬层2-1和2-2均为2.6~3μm;防激光膜层3包括激光高反膜层3-1,激光高反膜层3-1包括:硅铝复合氧化物层3-1-1a/26.4nm、nb2o5层3-1-2a/76.97nm、硅铝复合氧化物层3-1-1b/266.19nm、nb2o5层3-1-2b/14.27nm、硅铝复合氧化物层3-1-1c/150.82nm、nb2o5层3-1-2c/77.71nm、硅铝复合氧化物层3-1-1d/44.43nm、nb2o5层3-1-2d/19.47nm、硅铝复合氧化物层3-1-1e/186.53nm、nb2o5层3-1-2e/19.71nm、ito层3-1-3/5nm、硅铝复合氧化物层3-1-1f/205.86nm;防水层4-1为10nm;凹面为与实施例1相同的激光吸收降背反膜层3-2;
[0213]
1.3树脂镜片的制备方法包括以下步骤:
[0214]
s1:制作加硬层:将超声波清洗干净的树脂镜片基片浸入质量百分含量27%的加硬液水溶液中,浸渍温度15℃,浸渍5秒后以2.0mm/s的速度提拉出溶液;80℃烘干3小时后将上述基片取出并送至烘干箱内干燥固化,固化温度120℃,固化时间150min,即所述树脂镜片基片1的凸面1-1和凹面1-2表面均获得加硬层,即得含加硬层2-1和2-1的树脂镜片;
[0215]
s2:制备激光高反膜层3-1和防水层4-1的步骤包括:在真空镀膜机内、采用真空镀膜工艺,将固态膜层材料蒸发后经过气相传输,在s1步骤获得的加硬层2-1表面沉积成薄膜,形成激光高反膜层3-1,具体包括以下步骤:
[0216]
s21:在s1获得的含加硬层2-1的树脂镜片表面交替分别形成五层硅铝复合氧化物层3-1-1a~1e和五层nb2o5层3-1-2a~2e,所述第一层硅铝复合氧化物层3-1-1a位于所述加硬层2-1表面,具体包括:
[0217]
s211:在s1获得的含加硬层2-1的树脂镜片表面,在本底真空度≤3
×
10-3
pa、且镀膜舱内温度为60℃、有离子源辅助工艺的条件下,采用高能电子束加热硅铝复合氧化物,以速率为将蒸发后的硅铝复合氧化物以纳米级分子形式沉积,获得含第一层硅铝复合氧化物层3-1-1a的树脂镜片;
[0218]
s212:在s211获得的树脂镜片表面,在本底真空度≤3
×
10-3
pa、且镀膜舱内的温度为60℃、有离子源辅助工艺的条件下,采用高能电子束加热nb2o5,以速率为将蒸发后的nb2o5以纳米级分子形式沉积,获得含第二层nb2o5层3-1-2a的树脂镜片;
[0219]
s213:重复s211和s212步骤,分别交替形成第三层硅铝复合氧化物层和第四层nb2o5层,第五层硅铝复合氧化物层和第六层nb2o5层,第七层硅铝复合氧化物层和第八层nb2o5层以及第九层硅铝复合氧化物层和第十层钛nb2o5层,即形成包括第三、五、七、九层硅铝复合氧化物层(即硅铝复合氧化物层3-1-1b~e)、第四、六、八、十层nb2o5层(即nb2o5层3-1-2b~e)的树脂镜片;
[0220]
s22:在s213获得的树脂镜片表面,在本底真空度≤3
×
10-3
pa、且镀膜舱内的温度
为60℃、并有离子源辅助工艺的条件下,采用高能电子束加热ito,以速率为将蒸发后的ito以纳米级分子形式沉积,获得含一层ito层3-1-3的树脂镜片;
[0221]
s23:在s22获得的树脂镜片表面,继续采用真空镀膜工艺,重复s211的工艺步骤,形成含硅铝复合氧化物层3-1-1f的树脂镜片;
[0222]
s24:在s23获得的树脂镜片表面,继续采用真空镀膜工艺,继续采用真空镀膜工艺,在本底真空度≤3
×
10-3
pa、且镀膜舱内的温度为60℃条件下,采用高能电子束加热含氟防水材料(优选含有全氟烷(c
12
f
27
n)的防水材料),以速率为将蒸发后的含氟防水材料以纳米级分子形式沉积于所述激光高反膜层3-1的表面,形成防水层4-1,即获得含防水层4-1的树脂镜片。
[0223]
s3:制备激光吸收降背反膜层3-2和防水层4-2的步骤包括:同实施例1的s3步骤;
[0224]
其中,所述步骤s2和s3中,离子源辅助沉积工艺参数为:离子源为霍尔源,阳极电压:110v,阳极电流:3a,辅助气为o2,流量为15sccm。
[0225]
对比例6:一种带激光高反膜的树脂镜片
[0226]
3.1镜片基片为mr-8;加硬层为z117;凸面镀膜材料:硅铝复合氧化物层:sio2和al2o3摩尔量百分比:60%sio2、40%al2o3,委托常州市瞻驰光电科技股份有限公司开发并生产,材料型号为sa66;钛铌复合氧化物层:tio2和nb2o5摩尔量百分比:80%tio2、20%nb2o5,委托常州市瞻驰光电科技股份有限公司开发并生产,材料型号为ptn28;防水层:采用含有全氟烷(c
12
f
27
n)的防水材料;凹面镀膜采用与实施例1相同的材料;
[0227]
2.2膜层结构:基片1(凸面1-1和凹面1-2);加硬层2-1和2-2均为2.6~3μm;1.2膜层结构:基片1(凸面1-1和凹面1-2);加硬层2-1和2-2均为2.6~3μm;激光高反膜层3-1,激光高反膜层3-1包括:硅铝复合氧化物层3-1-1a/25.8nm、钛铌复合氧化物层3-1-2a/76.88nm、硅铝复合氧化物层3-1-1b/264.27nm、钛铌复合氧化物层3-1-2b/12.33nm、硅铝复合氧化物层3-1-1c/151.99nm、钛铌复合氧化物层3-1-2c/77.56nm、硅铝复合氧化物层3-1-1d/44.4nm、钛铌复合氧化物层3-1-2d/19.05nm、硅铝复合氧化物层3-1-1e/188.4nm、钛铌复合氧化物层3-1-2e/17.58nm、ito层3-1-3/5nm、硅铝复合氧化物层3-1-1f/204.78nm;防水层4-1为10nm;凹面材料同实施例1;
[0228]
1.3树脂镜片的制备方法包括以下步骤:
[0229]
s1:制作加硬层:将超声波清洗干净的树脂镜片基片浸入质量百分含量27%的加硬液水溶液中,浸渍温度15℃,浸渍5秒后以2.0mm/s的速度提拉出溶液;80℃烘干3小时后将上述基片取出并送至烘干箱内干燥固化,固化温度120℃,固化时间150min,即所述树脂镜片基片1的凸面1-1和凹面1-2表面均获得加硬层,即得含加硬层2-1和2-1的树脂镜片;
[0230]
s2:制备激光高反膜层3-1和防水层4-1的步骤包括:在真空镀膜机内、采用真空镀膜工艺,将固态膜层材料蒸发后经过气相传输,在s1步骤获得的加硬层2-1表面沉积成薄膜,形成激光高反膜层3-1,具体包括以下步骤:
[0231]
s21:在s1获得的含加硬层2-1的树脂镜片表面交替分别形成五层硅铝复合氧化物层3-1-1a~1e和五层钛铌复合氧化物层3-1-2a~2e,所述第一层硅铝复合氧化物层3-1-1a位于所述加硬层2-1表面,具体包括:
[0232]
s211:在s1获得的含加硬层2-1的树脂镜片表面,在本底真空度≤3
×
10-3
pa、且镀
膜舱内温度为60℃、有离子源辅助工艺的条件下,采用高能电子束加热硅铝复合氧化物,以速率为将蒸发后的硅铝复合氧化物以纳米级分子形式沉积,获得含第一层硅铝复合氧化物层3-1-1a的树脂镜片;
[0233]
s212:在s211获得的树脂镜片表面,在本底真空度≤3
×
10-3
pa、且镀膜舱内的温度为60℃、有离子源辅助工艺的条件下,采用高能电子束加热钛铌复合氧化物,以速率为将蒸发后的钛铌复合氧化物以纳米级分子形式沉积,获得含第二层钛铌复合氧化物层3-1-2a的树脂镜片;
[0234]
s213:重复s211和s212步骤,分别交替形成第三层硅铝复合氧化物层和第四层钛铌复合氧化物层,第五层硅铝复合氧化物层和第六层钛铌复合氧化物层,第七层硅铝复合氧化物层和第八层钛铌复合氧化物层以及第九层硅铝复合氧化物层和第十层钛铌复合氧化物层,即形成包括第三、五、七、九层硅铝复合氧化物层(即硅铝复合氧化物层3-1-1b~e)、第四、六、八、十层钛铌复合氧化物层(即钛铌复合氧化物层3-1-2b~e)的树脂镜片;
[0235]
s22:在s213获得的树脂镜片表面,在本底真空度≤3
×
10-3
pa、且镀膜舱内的温度为60℃、并有离子源辅助工艺的条件下,采用高能电子束加热ito,以速率为将蒸发后的ito以纳米级分子形式沉积,获得含一层ito层3-1-3的树脂镜片;
[0236]
s23:在s22获得的树脂镜片表面,继续采用真空镀膜工艺,重复s211的工艺步骤,形成含硅铝复合氧化物层3-1-1f的树脂镜片;
[0237]
s24:在s23获得的树脂镜片表面,继续采用真空镀膜工艺,继续采用真空镀膜工艺,在本底真空度≤3
×
10-3
pa、且镀膜舱内的温度为60℃条件下,采用高能电子束加热含氟防水材料(优选含有全氟烷(c
12
f
27
n)的防水材料),以速率为将蒸发后的含氟防水材料以纳米级分子形式沉积于所述激光高反膜层3-1的表面,形成防水层4-1,即获得含防水层4-1的树脂镜片;
[0238]
s3:制备激光吸收降背反膜层3-2和防水层4-2的步骤包括:同实施例1的s3步骤;
[0239]
其中,所述步骤s2和s3中,离子源辅助沉积工艺参数为:离子源为霍尔源,阳极电压:110v,阳极电流:3a,辅助气为o2,流量为15sccm。
[0240]
对比例7:一种防护绿色激光的树脂镜片
[0241]
1.1镜片基片为mr-8;加硬层为z117;凸面镀膜材料:硅铝复合氧化物层:sio2和al2o3摩尔量百分比:92%sio2、8%al2o3,委托常州市瞻驰光电科技股份有限公司开发并生产,材料型号为sa56;钛铌复合氧化物层:tio2和nb2o5摩尔量百分比:80%tio2、20%nb2o5,委托常州市瞻驰光电科技股份有限公司开发并生产,材料型号为ptn28;防水层:采用含有全氟烷(c
12
f
27
n)的防水材料;凹面镀膜材料同凸面;
[0242]
1.2膜层结构:基片1(凸面1-1和凹面1-2);加硬层2-1和2-2均为2.6~3μm;防激光膜层3包括激光高反膜层3-1和激光高反膜层3-2,激光高反膜层3-1包括:硅铝复合氧化物层3-1-1a/25.8nm、钛铌复合氧化物层3-1-2a/76.88nm、硅铝复合氧化物层3-1-1b/264.27nm、钛铌复合氧化物层3-1-2b/12.33nm、硅铝复合氧化物层3-1-1c/151.99nm、钛铌复合氧化物层3-1-2c/77.56nm、硅铝复合氧化物层3-1-1d/44.4nm、钛铌复合氧化物层3-1-2d/19.05nm、硅铝复合氧化物层3-1-1e/188.4nm、钛铌复合氧化物层3-1-2e/17.58nm、ito层3-1-3/5nm、硅铝复合氧化物层3-1-1f/204.78nm;激光高反膜层3-2与激光高反膜层3-1
的膜层结构相同;防水层4-1和防水层4-2均为10nm;
[0243]
制备激光吸收降背反膜层3-2和防水层4-2的步骤包括:同实施例1的s3步骤;
[0244]
其中,所述步骤s2和s3中,离子源辅助沉积工艺参数为:离子源为霍尔源,阳极电压:110v,阳极电流:3a,辅助气为o2,流量为15sccm。
[0245]
对比例8:一种防护绿色激光的树脂镜片
[0246]
1.1镜片基片为mr-8;加硬层为z117;凸面镀膜材料:硅铝复合氧化物层:sio2和al2o3摩尔量百分比:92%sio2、8%al2o3,委托常州市瞻驰光电科技股份有限公司开发并生产,材料型号为sa56;钛铌复合氧化物层:tio2和nb2o5摩尔量百分比:80%tio2、20%nb2o5,委托常州市瞻驰光电科技股份有限公司开发并生产,材料型号为ptn28;防水层:采用含有全氟烷(c
12
f
27
n)的防水材料;凹面镀膜材料同凸面;
[0247]
1.2膜层结构:基片1(凸面1-1和凹面1-2);加硬层2-1和2-2均为2.6~3μm;防激光膜层3包括激光高反膜层3-1和减反膜层3-2,激光高反膜层3-1包括:硅铝复合氧化物层3-1-1a/25.8nm、钛铌复合氧化物层3-1-2a/76.88nm、硅铝复合氧化物层3-1-1b/264.27nm、钛铌复合氧化物层3-1-2b/12.33nm、硅铝复合氧化物层3-1-1c/151.99nm、钛铌复合氧化物层3-1-2c/77.56nm、硅铝复合氧化物层3-1-1d/44.4nm、钛铌复合氧化物层3-1-2d/19.05nm、硅铝复合氧化物层3-1-1e/188.4nm、钛铌复合氧化物层3-1-2e/17.58nm、ito层3-1-3/5nm、硅铝复合氧化物层3-1-1f/204.78nm;激光减反膜层3-2包括:硅铝复合氧化物层3-2-3a/26.2nm、钛铌复合氧化物层3-2-2a/17.31nm、硅铝复合氧化物层3-2-3b/46.89nm、钛铌复合氧化物层3-2-2b/19.74nm、ito层3-2-4/5nm;硅铝复合氧化物层3-2-3c/108.25nm;防水层4-1和防水层4-2均为10nm;
[0248]
制备激光吸收降背反膜层3-2和防水层4-2的步骤包括:同实施例1的s3步骤;
[0249]
其中,所述步骤s2和s3中,离子源辅助沉积工艺参数为:离子源为霍尔源,阳极电压:110v,阳极电流:3a,辅助气为o2,流量为15sccm。
[0250]
二、实验例
[0251]
1.测定折射率
[0252]
预实验:我们对实施例以及对比例选用材料的折射率进行了测定,结果如下表1所示:
[0253]
表1
[0254][0255]
由此可见,钛铌复合氧化物材料的折射率较高,可以满足制备需求。
[0256]
表2
[0257][0258]
由此可见,硅铝复合氧化物材料的当sio2比例较高时,折射率较低,可以满足制备防激光镀膜需求。当降低sio2比例时,复合折射率较高,会影响低反射防激光镀膜光谱性能
效果,不能达到本发明的发明目的。