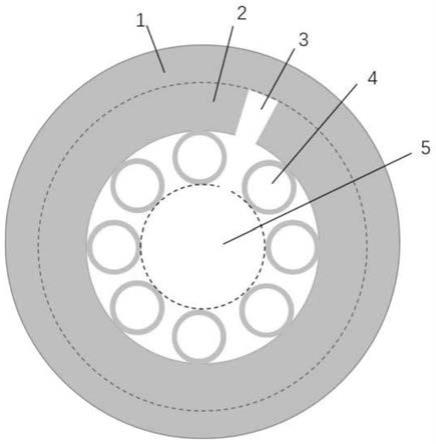
1.本发明属于光纤技术领域,具体涉及一种双包层反谐振空芯光纤及其制备方法。
背景技术:2.近年来,反谐振空芯光纤得到广泛的研究和关注,这种空芯光纤可由一层间隔分布的毛细管以及外石英包层组成,不同于传统空芯带隙光纤的带隙引导型导光机理,它是采用反谐振理论进行光束在中空纤芯的束缚。相比于传统空芯光纤,这类反谐振空芯光纤具有更简单的几何结构、良好的单模传输、更宽的传输窗口和超低传输损耗的优点。
3.由于空芯光纤中空的纤芯可以提供一个长距离稳定的介质与光相互作用的通道,并且空气纤芯中能量占比极高(>99.99%),因此反谐振空芯光纤在气体传感和气体激光领域具有很大的应用潜力。然而,通常光纤中气体或者液体的交换都需要从端面进入,这就使得必须引入空间耦合,不利于器件的全光纤化。此外,考虑到光纤纤芯尺寸与光纤长度比非常小,这将极大增加气体或者液体交换时间,严重影响器件的响应速度,阻碍了其在实际中的应用。目前,已有利用飞秒激光在空芯光子晶体光纤复杂的包层结构上进行开槽侧面通道的研究,然而这种方法操作复杂,并且会破坏光纤的复杂包层结构,产生大的传输损耗。还有利用二氧化碳激光进行光纤包层消蚀,从而产生一条侧面连接外界环境与光纤纤芯的槽道,但由于目前光纤包层毛细管间距较小,在消蚀过程容易破坏毛细管结构,带来很大的损耗。当前空芯光纤在气体传感等领域有很大的发展空间,因此设计一种结构简单、具有低传输损耗、容易处理的空芯反谐振光纤具有重要的意义。
技术实现要素:4.本发明针对现有反谐振空芯光纤响应速度慢,光纤后处理复杂以及处理损耗高的技术难题,提出一种双包层反谐振空芯光纤及其制备方法。
5.本发明提供的双包层反谐振空芯光纤,其结构包括:第一外包层,第二外包层,毛细管层;其中:所述第一外包层,在最外层;该第一外包层界定了内部未封闭包层外表面;所述第二外包层,为未封闭的,在该第二外包层上有一条贯穿光纤的微通道;所述第二外包层与第一外包层紧密连接,并界定了内部未封闭包层内表面;所述毛细管层,作为反谐振层附接至第二外包层内表面,并与第二外包层一起界定具有有效半径的纤芯;所述毛细管层中的毛细管被间隔布置,且相邻的毛细管之间具有间隔。
6.本发明中,所述第二外包层具有一条贯穿光纤的微通道,该微通道联通纤芯与第一外包层的内表面。
7.本发明中,所述第一外包层、第二外包层和毛细管层分别由玻璃制成。
8.本发明中,所述第一外包层容易通过光纤后期处理(如激光消蚀或侧面抛光等方式)去除,从而使第二外包层中微通道直接暴露于外界环境。
9.本发明提供的上述双包层反谐振空芯光纤的制备方法,具体步骤为:步骤1、毛细管拉制:使用玻璃管直接拉制出所需直径的毛细管;步骤2、预制棒制备,具体包括:2.1.将多根毛细管插入到大空芯尺寸的石英管中,对石英管和毛细管进行加热到熔融状态,从而使得毛细管与石英管侧面熔接在一起,并且不发生较大的形变;2.2.对上述步骤得到的光纤预制棒进行侧面抛磨处理,形成未封闭的预制棒外包层;2.3.将未封闭的光纤预制棒插入一个更大外径的石英管中,从而得到双包层反谐振空芯光纤预制棒;步骤3、使用光纤拉丝塔对步骤2得到的光纤预制棒进行拉制处理,得到双包层反谐振空芯光纤。
10.本发明制备的双包层反谐振空芯光纤,可用于制备光纤气体传感器或微流体传感器,所述光纤气体传感器或微流体传感器,可用于气体或微流体光源或激光器中。
11.本发明设计的反谐振空芯光纤,第一外包层可以有效保证光纤的机械可靠性,第二外包层具有未封闭结构,能够极大减小光纤后处理复杂度,容易制备得到低传输损耗、响应速度快的未封闭反谐振空芯光纤。本发明在不改变光纤传输特性的基础上,显著降低了光纤包层处理技术难度,并极大提高了光纤的性能。本发明整体解决了现有反谐振空芯光纤损耗特性与处理复杂性的问题,为全光纤系统中气体或微流体传感应用提供了高可靠性、高灵敏度、有效相互作用长度的理想平台。
附图说明
12.图1为本发明的结构示意图。
13.图2为本发明的限制损耗曲线图,插图为本发明在1.55μm处的基模模场图。
14.图3为本发明的能量占比曲线。
15.图4为本发明包层进行消蚀或者抛磨处理后光纤在1.55μm处模场示意图。
16.图中标号:1为第一外包层,2为第二外包层,3为第二外包层2上的微通道,4为微毛细管,5为纤芯。
具体实施方式
17.如图1所示,为本实施例涉及一种双包层反谐振空芯光纤,所述双包层反谐振空芯光纤包括:最外层的第一外包层1,所述第一外包层界定了内部未封闭包层外表面;第二外包层2,所述第二外包层是未封闭的,在所述包层上有一条贯穿光纤的微通道3,所述第二未封闭外包层2与第一外包层1紧密连接并界定了内部未封闭包层内表面;毛细管层4,所述毛细管层作为反谐振层附接至第二未封闭层2内表面并与其一起界定具有有效半径的纤芯5,所述毛细管层中的毛细管被间隔布置,且相邻的毛细管之间具有间隔。
18.所述第二未封闭外包层2是未封闭的,具有一条贯穿光纤的微通道,所述微通道联通了纤芯与第一外包层的内表面。
19.所述的纤芯直径为30
‑
50μm,毛细管层毛细管数量为6
‑
10个,毛细管厚度为0.2
‑
1μm。
20.所述第二外包层直径为100
‑
120μm,微通道宽带不超过毛细管层相邻毛细管间距。
21.优选地,所述的纤芯直径约40μm,毛细管直径为16μm,毛细管壁厚为420nm,微通道宽带约13μm,如图2所示为其限制损耗仿真结果,在可见光波段500
‑
700nm处,损耗最小可到0.0002db/m,而在近红外波段1000
‑
2000nm的宽谱内,损耗基本都小于0.1db/m,在波长1.55μm处损耗为0.027db/m,插图为其基模模场分布图。
22.如图3所示,在可见光波段500
‑
700nm以及1000
‑
2000nm的传输窗口内,所述双包层反谐振空芯光纤的纤芯能量占比可以达到99.9%,在传输窗口内光纤的基本所有能量都被束缚在纤芯中进行传播。
23.如图4所示,对所述双包层进行包层消蚀或者抛磨处理后结构示意图,使用仿真软件进行计算后,可得到在1.55μm处限制损耗为0.027db/m,纤芯能量占比大于99.9%,可以发现对包层进行处理后,光纤传输性能没有受到明显影响,但此时光纤纤芯与外界通过光纤微通道直接相连,可极大提高光纤内气体或者液体交换速率,显著减小光纤响应时间。
24.上述一种双包层反谐振空芯光纤的制备方法具体为:步骤1、毛细管拉制:使用玻璃管直接拉制出所需直径的毛细管;步骤2、预制棒制备,具体包括:2.1.将多根毛细管插入到大空芯尺寸的石英管中,对石英管和毛细管进行加热到熔融状态,从而使得毛细管与石英管侧面熔接在一起,并且不发生较大的形变;2.2.对上述步骤得到的光纤预制棒进行侧面抛磨处理,从而形成未封闭的预制棒外包层;2.3.将未封闭的光纤预制棒插入一个更大外径的石英管中,从而得到双包层反谐振空芯光纤预制棒;步骤3、使用光纤拉丝塔对步骤2得到的光纤预制棒进行拉制处理,得到双包层反谐振空芯光纤。
25.本发明通过设计一种具有未闭合内包层结构的反谐振空芯光纤,在不改变光纤传输特性的基础上,显著降低了光纤包层处理技术难度,从而极大提高了光纤的响应灵敏度。
26.最后,上述具体实施可由本领域技术人员在不背离本发明原理和宗旨的前提下以不同的方式对其进行局部调整,并非用于限定本发明的保护范围。凡在本发明的精神和原则之内,所作的任何修改、等同替换、改进等,均应包含在本发明的保护范围之内。