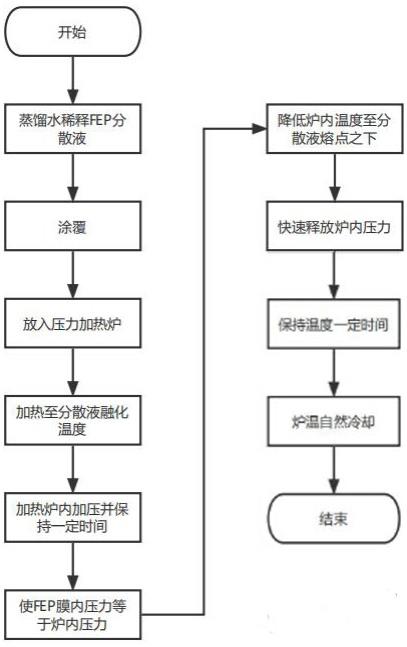
1.本发明属于驻极体技术领域,具体说是一种多孔压电驻极体的制备方法,该驻极体具有优异的电荷热稳定性,尤其适用于高温环境下的使用。
背景技术:2.驻极体是指具有长期储存电极化和空间电荷能力的功能电介质材料。由于所具有的静电、压电、热释电和光学非线性等物理效应,使其在电子工程、环境净化、能源、生物医药工程等领域尤其在传感器工程方面得到了越来越多的应用。
3.驻极体测量传声器相较于传统外极化型的测量传声器对后端的电路要求低很多,可以实现便携测试的应用。随着使用驻极体技术的测量传声器应用范围越来越广泛,其在某些特定的环境下也暴露出了一些缺点,在高温下驻极体的电荷保存能力会出现严重的下降(高温引起驻极体表面电荷脱陷),此缺陷导致驻极体测量传声器在高温环境下无法长期工作。
4.多孔驻极体的出现,能够提高驻极体在高温环境下的电荷存储的稳定性。传统工艺制备封闭微孔结构聚合物的方法主要有两种:一是通过化学发泡工艺得到孔洞结构的材料;二是将聚合物树脂与无机或有机颗粒进行熔融共混后通过挤出或热压工艺形成薄板,利用聚合物树脂和添加颗粒之间巨大的力学性能差异在双向拉伸过程中得到微孔结构的薄膜。
5.现有技术参考如下:cn100505359c公开一种可控微孔结构压电功能膜的制备方法,将具有高热稳定性的聚合物致密膜和与聚合物 致密膜不同熔融温度的聚合物网状膜逐层相间迭全;然后在90℃-500℃温度、1kpa-10mpa压力下,经过2-120 分钟,形成微孔结构聚合物复合膜。
6.cn102150225b公开一种驻极体化薄膜及含有其的驻极体,所述多孔性树脂薄膜(i)含有芯层(a)和表面层(b),所述芯层(a)包含具有孔隙的双轴拉伸树脂薄膜,所述表面层(b)位于该芯层(a)的至少一面上且含有拉伸树脂薄膜,多孔性树脂薄膜(i)是 在加压条件下使非反应性气体渗透到其中、接着在非加压条件下对其实施了加热处理的。在具有孔隙的双轴拉伸树脂薄膜基础上,进一步实施加压处理和加热处理而使孔隙沿厚度方向膨胀时,可以形成各自的体积大的孔隙,在注入电荷时易于在孔隙内存储正负极化的电荷,是制成驻极体化薄膜(ii)后电荷保持性能优异的材料。
7.多孔驻极体传声器的背极板往往带有若干的孔,带有孔的背极板如果使用上述的多孔薄膜,多孔薄膜在粘贴到背极板上后会覆盖住背极板的孔,此时又会造成需要驻极体薄膜二次开孔困扰,为产品的量产与稳定性带来不确定性。
8.因此,需要一种可以直接在带孔的背级板上形成的多孔薄膜,无需二次开孔,且所形成的多孔压电驻极体的电荷稳定性好。
技术实现要素:9.本发明的目的是提供多孔压电驻极体的制备方法,通过分散液在背极板上成膜的同时,对薄膜进行微孔成型,同时可以避免生成过程中高温造成材料分解,保证驻极体储电性能。
10.为了达到上述目的,本发明采用如下的技术方案:多孔压电驻极体的制备方法,包括如下步骤:s1.提供驻极体材料分散液;s2.将驻极体材料分散液涂覆于背极板上;s3.将涂覆有驻极体材料分散液的背极板的容器内,控制温度高于驻极体材料融点温度5℃至15℃,同时,升高容器内压力p2至大于容器外压力p1,在该温度和压力下,维持16min至25min;s4.将温度降低至驻极体材料的熔点温度之下,在该温度和压力p2下保持10min至30min;s5.使容器内压力快速释放p2等于p1,此时驻极体材料内的快速产生压差,内部的空气快速膨胀,驻极体材料内部产生微孔;s6.保持容器内温度低于驻极体材料的熔点温度,维持20min至25min,让驻极体材料内部的微孔定型;s7.产品冷却后,得到多孔压电驻极体。
11.现有技术中的多孔驻极体,多是在独立将驻极体薄膜通过拉伸或者发泡的方式形成微孔之后,贴附于背极板上。在这种情况下,贴附上的微孔驻极体薄膜会封堵住背极板本身的孔,造成在高温环境下驻极体的电荷存储稳定性差。因此,往往需要对驻极体薄膜进行二次开孔,这又造成了工艺上的复杂,为产品的量产与稳定性带来不确定性。而且形成好的再通过热压的方式贴附于背极板上,热压的高温环境,又会损坏已经薄膜上形成的微孔,导致多孔驻极体的性能下降。
12.本发明创造性地采用驻极体材料分散液首先在背极板上形成涂层,将涂层成膜的同时,进行微孔成型。在涂层时,驻极体材料分散液会分布于背极板的孔内,这样,在成膜时,孔壁上同样贴附驻极体薄膜,薄膜不会堵住背极板上的孔,故无需进行二次开孔。所形成的驻极体薄膜分布于背极板表面及孔内,分布面积更大,储电性能更优。
13.根据现有技术的记载,在驻极体材料分散液形成驻极体薄膜时,加热时必须使用比材料熔点高20℃以上的温度,使材料有一定流动性才能结合成膜,否则,成膜性能差,影响驻极体的电荷稳定性。但是,在该温度下,驻极体材料存在可能分解的问题,同样会导致驻极体的储电性能下降。
14.在本发明中,在加热的同时进行增压,发明人发现,高温成膜的温度可以调整至高于材料熔点5℃,就具有优良的成膜效果,因此,本发明可以采用交底温度来实现高温成膜,而在该温度下,材料不会出现分解。这样不仅提高了驻极体的储电性能,而且也有利于节能。这是本发明的另一明显优势。
15.在现有技术中公开的两种形成孔隙的方式中,通常认为拉伸的方式可以在薄膜的长度方向形成孔隙,高压发泡的方式,使多孔性树脂薄膜沿厚度方向膨胀。采用本发明的这种方式,可以同时在驻极体薄膜的长度和厚度方向上形成微孔,进一步增大了孔隙率。这是
本发明的另一明显优势。
16.另外,本发明在成膜的同时,增大压力,还有利于提高驻极体薄膜与背极板之间的贴合牢度。
17.本发明的一实施方式中,步骤s3中,容器内压力p2为压力p1的1.5-3倍。
18.更加优选地,容器内压力p2为压力p1的2倍。
19.本发明的一实施方式中,步骤s5中,容器内压力在2s至4s内释放至p2等于p1。
20.本发明的一实施方式中,步骤s3中,通过向容器内通入气体进行增压,所述气体可以是任何可以使用的气体,优选为空气。
21.本发明的一实施方式中,步骤s3中,维持时间为18min至20min,更加优选为20min。
22.本发明的一实施方式中,步骤s4中,保持容器内温度在低于熔点温度5℃至30℃的范围内。
23.本发明的一实施方式中,步骤s4中,维持时间为20-25min。
24.本发明的一实施方式中,步骤s6中,保持容器内温度在低于熔点温度10℃至40℃的范围内。
25.本发明的一实施方式中,步骤s6中,维持时间为20-25min。
26.本发明的一实施方式中,所述的驻极体材料是全氟乙烯丙烯共聚物(fep)、聚四氟乙烯(ptfe)、聚丙烯(pp)或四氟乙烯—全氟烷氧基乙烯基醚共聚物(pfa)。本发明的一实施方式中,s2中的涂覆方式不做特殊规定,可以是印刷、喷涂、涂刷、浸渍等多种方式。
27.本发明的一实施方式中,步骤s7中,产品的冷却方式为随炉温自然冷却。
28.通过实施上述的技术方案,本发明具有如下的优点:1.本发明采用驻极体材料分散液首先在背极板上形成涂层,将涂层成膜的同时,进行微孔成型,不仅无需进行二次开孔,简化了工艺,而且所形成的驻极体薄膜分布于背极板表面及孔内,分布面积更大,储电性能更优。
29.2. 本发明在高温成膜的同时增大容器内压力,可以在较低温度下实现高温成膜,避免了驻极体材料分解,保证驻极体的储电性能,提高了电荷稳定性。
30.3. 采用本发明的这种方式,可以同时在驻极体薄膜的长度和厚度方向上形成微孔,进一步增大了孔隙率,提高了驻极体材料的储电能力。
附图说明
31.附图1为本发明多孔压电驻极体的制备方法的流程示意图;附图2为本发明不同实施例与对比例所得驻极体的电荷稳定性检测结果。
具体实施方式
32.下面根据附图和具体实施例对本发明作进一步详细说明。
33.需要说明的是,以下实施案例仅用以说明本发明的技术方案,而非对其限制;尽管参照前述实施案例对本发明进行了详细的说明,本领域的普通技术人员应当理解:其依然可以对前述各实施案例所记载的技术方案进行修改,或者对其中部分技术特征进行等同替换;而这些修改或者替换,并不使相应技术方案的本质脱离本发明各实施案例技术方案的范围。
34.多孔压电驻极体的制备方法,包括如下步骤:s1.提供驻极体材料分散液。
35.驻极体材料可以是全氟乙烯丙烯共聚物(fep)、聚四氟乙烯(ptfe)、四氟乙烯—全氟烷氧基乙烯基醚共聚物(pfa)或聚丙烯(pp),这些材料的分散液可以直接购买市售商品,也可以溶于溶剂配置对应的分散液。
36.s2.将驻极体材料分散液涂覆于背极板上,烘干。
37.涂覆的方式有多种,可以是印刷、喷涂、涂刷、浸渍等。具体涂覆方式不做限定,涂覆时确保背极板的孔内也被涂覆到。涂覆厚度为20-40微米。烘干方式也不做限定。
38.s3.将涂覆有驻极体材料分散液的背极板的容器内,控制温度高于驻极体材料融点温度5℃至15℃,同时,升高容器内压力p2至大于容器外压力p1,在该温度和压力下,维持16min至25min。
39.这一步,温度、压力、时间的控制都尤其重要,合理控制各参数值,在驻极体薄膜暂未完全形成之前,高压气体渗入到材料中,随后,高温形成膜状,气体包裹在内,在后续泄压期间,气体突破,从而在驻极体薄膜内部形成微孔。这种形成方式,所形成的驻极体薄膜孔隙率更高,而且有利于提高所带电荷的热稳定性。
40.成膜温度相比一般所要求的温度要更低,现有技术中一般要求对于分散液的成膜温度要高于驻极体材料熔点温度的20℃以上,才能形成优良的膜。而在本方案中,可以在高于驻极体材料熔点温度15℃,甚至在高于驻极体材料熔点温度5℃,即可以高效成膜,而且膜性能优异。
41.发明人通过实验得出,不同驻极体材料对成膜温度的要求不同,但都能在高于对应驻极体材料熔点温度15℃的情况下实现较好效果的成膜。针对不同驻极体材料,又有差异性,在p2为两倍p1的压力下,对于fep,在高于驻极体材料熔点温度5℃即可以实现,而对于ptfe,则最低需要高于驻极体材料熔点温度12℃,才能达到理想的成膜效果。其它材料则需要更高一些的温度。步骤s3的温度过高,虽然成膜性能好,但是具有造成材料分解的风险,影响最终驻极体的储电性能。温度过低,成膜性能差,同样会影响驻极体的储电性能。
42.容器内压力p2不仅对薄膜的微孔形成具有影响,而且结合温度,对成膜性能具有影响,决定着薄膜的性能,容器内压力p2为容器外压力p1的两倍最为合适,容器外压力p1通常指大气压。在该温度和压力下,维持16min至25min,更优选地是维持20min。
43.s4.将温度降低至驻极体材料的熔点温度之下,在该温度和压力p2下保持10min至30min。
44.在此步骤,驻极体薄膜已经形成,这一步骤的实施,是为了在成膜之后,稳定驻极体薄膜的性能。保持容器内温度低于驻极体材料的熔点温度5℃至30℃为宜,在此温度下,膜仍然处于一个软化的状态,此时维持高压p2,可以使得膜与背极板之间更加贴附。
45.s5.使容器内压力快速释放p2等于p1,此时驻极体材料内的快速产生压差,内部的空气快速膨胀,驻极体材料内部产生微孔。
46.该步骤中,压力的释放速率尤其重要,在该步骤中,压力在2秒至4秒内释放完,气体的快速释放,驻极体材料内的快速产生压差,内部的气体快速膨胀,驻极体材料内部产生微孔,形成具有微孔的驻极体薄膜。
47.s6.保持容器内温度低于驻极体材料的熔点温度,维持20min至25min,让驻极体材
料内部的微孔定型。
48.该步骤中,温度可以与步骤s4中相同,也可以不同,优选以低于步骤s4中的温度维持。一方面,在步骤s5中释放一部分压力导致温度有所下降,不用再去进行升温操作;另一方面,更低一点的温度下,微孔定型效果也更好。更加优选地,本步骤中的低于熔点温度10℃至40℃的范围内。
49.s7.产品随炉温自然冷却后,得到多孔压电驻极体,之后放入电场中,背极板接地,进行针式电晕放电极化。充电方式可以有多种,不做限制。
50.本步骤中的冷却方式对驻极体产品的性能也具有一定影响,随炉温缓慢冷却,有利于保证微孔的稳定,取出冷却,加快冷却速度,薄膜会出现收缩,一定程度上影响的微孔,造成微孔的变形,从而影响驻极体的储电性能。
51.实施例1多孔压电驻极体的制备方法,参考流程图附图1,包括如下步骤:s1. 使用蒸馏水对市售聚全氟乙丙烯(fep)分散液进行稀释,蒸馏水与fep比例为1:2。市售fep分散液为三爱富公司的fr463分散液;s2.将fep分散液以浸渍的方式涂覆于背极板上,保证背极板的孔内也被涂覆到;s3.将涂覆有fep分散液的背极板的带有加热功能的压力炉内,fep的融点温度为260℃,控制温度为270℃,同时,升高容器内压力p2至容器外压力p1的两倍,在该温度和压力下,维持20min;s4.将温度降低至250℃,在该温度和压力p2下保持20min;s5.使容器内压力2秒内快速释放至p2等于p1,此时驻极体材料内的快速产生压差,内部的空气快速膨胀,驻极体材料内部产生微孔;s6.保持容器内温度在230℃,维持20min,让驻极体材料内部的微孔定型;s7.产品随炉温自然冷却后,得到多孔压电驻极体。
52.实施例2多孔压电驻极体的制备方法,包括如下步骤:s1. 使用蒸馏水对市售聚四氟乙烯(tpfe)分散液进行稀释,蒸馏水与tpfe比例为1:2。市售tpfe分散液为科慕公司生产的ptfe disp 30 分散液;s2.将tpfe分散液以浸渍的方式涂覆于背极板上,保证背极板的孔内也被涂覆到;s3.将涂覆有tpfe分散液的背极板的带有加热功能的压力炉内,tpfe的融点温度为337℃,控制温度为348℃,同时,升高容器内压力p2至容器外大气压p1的1.5倍,在该温度和压力下,维持25min;s4.将温度降低至330℃,在该温度和压力p2下保持25min;s5.使容器内压力3秒内快速释放至p2等于p1;s6.保持容器内温度在305℃,维持20min,让驻极体材料内部的微孔定型;s7.产品随炉温自然冷却后,得到多孔压电驻极体。
53.实施例3多孔压电驻极体的制备方法,包括如下步骤:s1.使用蒸馏水对市售聚全氟乙丙烯(fep)分散液进行稀释,蒸馏水与fep比例为1:2。市售fep分散液为三爱富公司的fr463分散液;
s2.将fep分散液以涂刷的方式涂覆于背极板上,保证背极板的孔内也被涂覆到;s3.将涂覆有fep分散液的背极板的带有加热功能的压力炉内,fep的融点温度为260℃,控制温度为275℃,同时,升高容器内压力p2至容器外压力p1的3倍,在该温度和压力下,维持20min;s4.将温度降低至230℃,在该温度和压力p2下保持30min;s5.使容器内压力4秒内快速释放至p2等于p1,此时驻极体材料内的快速产生压差,内部的空气快速膨胀,驻极体材料内部产生微孔;s6.保持容器内温度在220℃,维持25min,让驻极体材料内部的微孔定型;s7.产品随炉温自然冷却后,得到多孔压电驻极体。
54.对比例1多孔压电驻极体的制备方法,包括如下步骤:s1. 使用蒸馏水对市售聚全氟乙丙烯(fep)分散液进行稀释,蒸馏水与fep比例为1:2。市售fep分散液为三爱富公司的fr463分散液;s2.将fep分散液以浸渍的方式涂覆于背极板上,保证背极板的孔内也被涂覆到;s3.将涂覆有fep分散液的背极板的带有加热功能的压力炉内,fep的融点温度为260℃,控制温度为305℃,维持20min;s4.产品随炉温自然冷却后,得到多孔压电驻极体。
55.对比例2与实施例1的不同在于,先高温成膜后,再增加压力,进行发泡形成微孔。具体步骤如下:s1. 使用蒸馏水对市售聚全氟乙丙烯(fep)分散液进行稀释,蒸馏水与fep比例为1:2。市售fep分散液为三爱富公司的fr463分散液;s2.将fep分散液以浸渍的方式涂覆于背极板上,保证背极板的孔内也被涂覆到;s3.将涂覆有fep分散液的背极板的带有加热功能的压力炉内,fep的融点温度为260℃,控制温度为270℃,维持20min;s4.升高容器内压力p2至容器外压力p1的两倍,在该压力下,维持20min;s5.将温度降低至220℃,在该温度和压力p2下保持20min;s6.使容器内压力快速释放p2等于p1,此时驻极体材料内的快速产生压差,内部的空气快速膨胀,驻极体材料内部产生微孔;s7.保持容器内温度在200℃,维持20min,让驻极体材料内部的微孔定型;s8.产品随炉温自然冷却后,放入点场中,背极板接地,进行针式电晕放电极化,环境温度100℃、时间5min,得到多孔压电驻极体。
56.对比例3与实施例1的不同在于,不进行步骤s4。
57.对比例4与实施例1的不同在于,不进行步骤s6。
58.对比例5与实施例1的不同在于,步骤s3的温度调整为290℃。
59.对比例6
与实施例1的不同在于,步骤s3的温度调整为250℃。
60.对比例7与实施例1的不同在于,步骤s3的压力调整p2为p1的3.5倍。
61.采用根据本发明上述实施例和对比例工艺制作的驻极体,通过恒压栅控中压的电晕极化进行充电,参数:高压-12000v,中压-800v,驻极体的背极板接地,温度150℃,时长10min。使用表面电荷计测量驻极体表面电位初始压电,本发明制作复合驻极为-440v,传统工艺制作的驻极体-413v。
62.然后将驻极体样品放入150℃的高温干燥炉中进行老化10小时,高温会加快电荷迁移脱险。中间每隔一定时间进行表面电位检测。为方便对比,对数据进行归一化处理,参见附图2。
63.我们实施例1-3的电荷稳定性均高于对比例1-7,具体分析如下:对比例1采用是为经过压力处理的驻极体,驻极体薄膜未进行压力处理,没有形成微孔,此时,驻极体负载电荷的能力弱,在高温老化条件下,电荷损失量大,电荷稳定性最差。
64.对比例2与实施例1的区别是,高温成膜与微孔的形成分开进行,所得驻极体的电荷稳定性也远不如实施例1。
65.对比例3与实施例1的区别是,没有进行步骤s4的保温操作,所得驻极体的电荷稳定性也远不如实施例1。
66.对比例4与实施例1的区别是,没有进行步骤s6的微孔定型操作,所得驻极体的电荷稳定性也远不如实施例1。
67.对比例5与实施例1的区别是,步骤s3的温度采用现有针对分散液高温成膜的温度,高于熔点30℃,所得驻极体的电荷稳定性也远不如实施例1,推测在此温度下,驻极体材料有分解,而且高压环境会加速其分解,导致材驻极体性能下降。
68.对比例6与实施例1的区别是,步骤s3的温度调整为250℃,而此时分散液无法完全成膜,所得驻极体的电荷稳定性也远不如实施例1。
69.对比例7与实施例1的区别是,步骤s3的压力调整p2为p1的3.5倍。而此时过高的压力,加上高温,使得膜的性能下降,所得驻极体的电荷稳定性也远不如实施例1。
70.综上,本发明的方案,在驻极体材料分散液的基础上,进行成膜、微孔成型,通过对工艺步骤的合理优化,综合温度、压力和时间,整体实现驻极体优异的电荷稳定性。