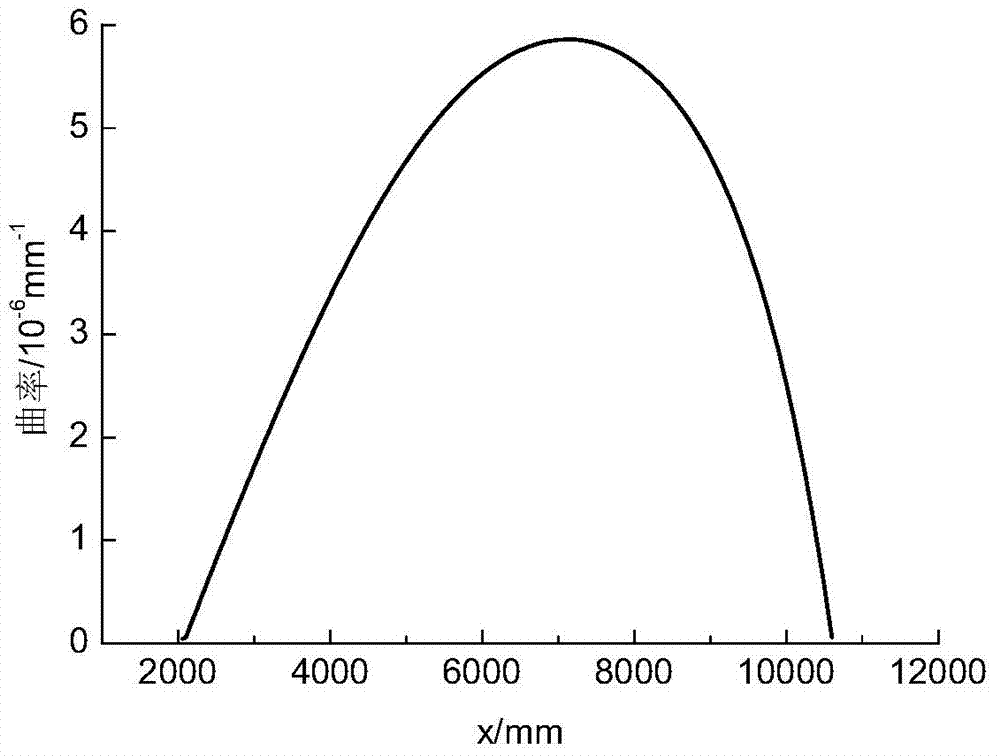
本发明属于机械领域,涉及一种直缝焊管三辊连续矫直工艺方法。
背景技术:大型直缝焊管广泛用于石油、天然气等的远距离运输,且多用于环境条件复杂的危险地段。在大型直缝焊管的实际生产过程中,受成形设备及模具整体直线度、焊接热应力等因素影响,成形后焊管的整体直线度并不满足行业要求,且其弯曲形式为单挠度的平面弯曲,需对其进行矫直处理。目前,大型直缝焊管多采用一次或多次三点式过弯矫直工艺进行修正,即将带有初始挠曲的焊管置于支距可调的两支点上,压点在最大挠曲处施以压力,使焊管反向弯曲后,压点上行,管件弹复,测量其直线度是否满足要求,若不满足,重复上述过程,直至满足要求。它的不足之处:1、现行矫直方法只针对焊管最大挠曲处,未考虑整体挠度分布,因此需要反复测量,多次矫直;2、实际生产依靠矫直工人的经验估计矫直行程,误差波动大、矫直精度差;3、过弯矫直工艺需多次移动管件,多次压制,使得矫直过程不连续、矫直效率低。
技术实现要素:本发明要解决的技术问题是,提供一种高效、高精度的大型直缝焊管三辊连续矫直装置及工艺方法。为解决上述技术问题,本发明方案的具体步骤如下:1、将待矫管件置于辊道上,使其弯曲平面垂直于工作台面,对弯曲平面管件外母线进行等效测量,并通过曲线拟合获得待矫管件的挠度曲线函数表达式。然后根据管件材料性能参数和公式M(x)=K(x)EI(3)得到管件矫直所需的理论弯矩M(x)。其中,Kd为管件截面弹塑性变形区域分界点位于管件内径边界时的初始曲率,K0(x)为初始曲率分布,f(x)为挠度曲线函数表达式;σ0为截距应力,σs为初始屈服应力,E为弹性模量,D为塑性剪切模量;I为管截面惯性矩,R1和R2分别为管件的外圆和内圆的半径;Kd(x)为塑性变形是否深入到管内径的分界曲率;K(x)为加载时曲率;εs为弹性极限应变。2、根据理论矫直弯矩M(x)和两下辊间距L确定矫直载荷F(x),即得矫直所需的矫直载荷-位移关系曲线F-s,并输入三辊连续矫直实时控制系统;3、将待矫管件置于大型直缝焊管三辊连续矫直装置上,两下辊同步转动,同时带动管件轴向移动,上辊按照一定规律对管件连续施压,直至管件全部通过辊系,实现管件的一次性连续矫直。大型直缝焊管三辊连续矫直装置主要包括上辊、下辊和支承辊。两个下辊和一个上辊均为圆弧面,且圆弧半径大于管件半径。支承辊为圆柱形筒体,两个支承辊之间的距离相同,两个支承辊和两个下辊在同一条直线上。本发明与现有技术相比具有以下优点:1、现行的矫直工艺只针对管件弯曲最大处,并未考虑管件的整体挠度分布;本发明通过测量管件的初始挠度曲线,获得了整根管件的最佳理论矫直弯矩及矫直载荷。2、现行的矫直工艺依靠技术工人的经验估计矫直行程;本发明通过实时控制系统控制上辊的载荷施加,提高了矫直精度。3、现行的矫直工艺一般需多次模压达到矫直目的;本发明通过三辊组成的辊系可以一次、连续矫直管件,提高了生产效率。附图说明图1为本发明实例待矫管件初始挠度测量数据及拟合曲线图;图2为本发明实施例待矫管件的初始曲率分布图;图3为本发明实施例待矫管件的矫直弯矩图;图4本发明实施例待矫管件的F-s关系曲线;图5为本发明实施例的辊体结构图;图6为本发明实施例连续矫直结构示意图。图5、图6中:1.上辊、2.支承辊、3.下辊。具体实施方式大型直缝焊管三辊连续矫直装置主要包括上辊、下辊和支承辊。两个下辊和一个上辊均为圆弧面,且圆弧半径大于管件半径。支承辊为圆柱形筒体,两个支承辊之间的距离相同,两个支承辊和两个下辊在同一条直线上。待矫大型直缝焊管的几何尺寸为外径457.2mm、壁厚为12.7mm、管长为12213mm,材料为A516Gr60,材料性能参数为E=200000MPa,D=1833.3MPa,σs=345MPa。具体步骤如下:(1)将管件置于辊道上,使其弯曲平面垂直于水平面,采用位于管件上方的激光位移传感器扫描管件外母线,得到的管件初始挠度分布数据,并采用八阶多项式对其进行拟合,得f(x)=p1x8+p2x7+p3x6+p4x5+p5x4+p6x3+p7x2+p8x+p9,其中p1=2.75×10-30,p2=-1.11×10-25,p3=1.835×10-21,p4=-1.528×10-17,p5=7.888×10-14,p6=-5.805×10-10,p7=2.51×10-6,p8=0.01055,p9=-0.1719,初始挠度测量数据及拟合挠度曲线见图1。(2)借助Matlab数学软件,将拟合所得初始挠度曲线表达式带入式,得到待矫管件初始曲率分布,如图2所示;将其带入式(2)和式(3),即得管件理论矫直弯矩,如图3所示。(3)两下辊辊距L=4000mm,将其与理论矫直弯矩数据带入公式(4),得到该管件矫直的F-s曲线,如图4所示,并将其输入三辊连续矫直实时控制系统。(4)如图5、图6所示,将管件置于辊道上,仍旧保持其弯曲平面垂直于水平面。启动动力系统,两下辊4同步旋转,同时带动管件2轴向移动,上辊1按照实时控制系统设置中的F-s曲线对管件施加载荷,直至管件全部通过辊系,实现管件的一次性矫直。(4)矫直完成后,测得其最大挠度为13mm,直线度为0.1%,满足美国APISpec5L行业标准提出的成品管最大挠度不得超过管长度0.2%的要求。