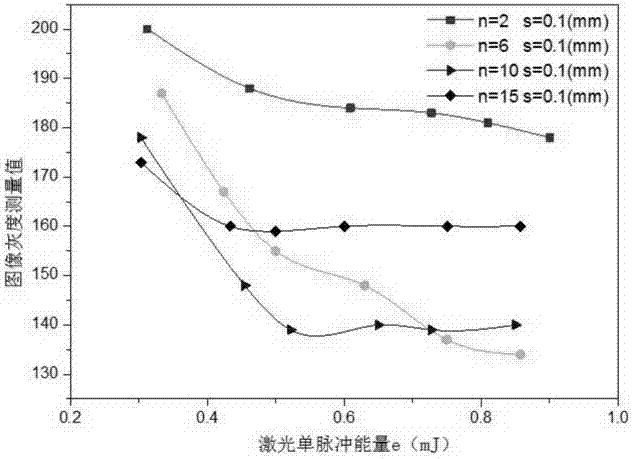
本发明涉及激光标刻领域,尤其涉及一种利用激光在铝锭表面标刻铝锭标识所需的激光标刻工艺参数的估计方法以及利用激光在铝锭表面标刻铝锭标识的方法。
背景技术:
:在铝锭制作完成出厂前,需在铝锭上标记铝锭标识,该铝锭标识通常采用文字、条形码和/或二维码的形式记载铝锭的生产单位、生产日期、化验信息、熔炼炉号、品位信息及重量信息等相关信息。目前,铝锭标识通常是将打印有铝锭标识的纸质标签粘贴在铝锭上或者是利用喷墨标刻、气动标刻或激光标刻方法将铝锭标识标刻在铝锭表面上。其中,将打印有铝锭标识的纸质标签粘贴在铝锭上,费时费力,成本高,且纸质标签在铝锭运输、存储过程中易受损,影响辨识。喷墨标刻以及气动标刻得到的铝锭标识自动辨识性差,辨识不便。采用激光标刻方法在铝锭表面标刻铝锭标识时,需根据标刻需要对激光标刻工艺参数进行选择调节,但是由于铝锭表面凹凸不平,标刻背景图像复杂,导致激光标刻工艺参数选择困难,标刻效果差,标刻效率低,进而导致标刻的铝锭标识尤其是铝锭标识中的一维码以及二维码的自动识别率低。技术实现要素:为提高标刻效果以及标刻效率,本发明提出一种激光标刻工艺参数的估计方法,该估计方法包括如下步骤:步骤1:在待标刻铝锭上进行等水平多因素正交试验,试验过程中,调整激光标刻工艺参数以获得不同的标刻图像的图像灰度值,并记录多组试验数据,该试验数据包括激光标刻工艺参数聚焦激光束直径d、激光机Q频率f、激光扫描速度v、激光功率p和填充线间距s的值以及对应的标刻图像的图像灰度值;步骤2:建立标刻图像的图像灰度值的计算模型方程:其中,G表示标刻图像的图像灰度值,bi(i=0、1、2、3)、b4、b5、......、b9、b10为拟合系数;步骤3:根据所述步骤1中的等水平多因素正交试验的试验数据拟合得出所述图像灰度值的计算模型方程中的拟合系数的值;步骤4:根据目标函数G<150估计得出激光标刻工艺参数激光光斑重叠次数n、聚焦激光束直径d、激光机Q频率f、激光扫描速度v、激光单脉冲能量e以及激光功率p的值。利用该激光标刻工艺参数的估计方法可根据标刻需要的图像灰度值估计出激光标刻工艺参数,且采用估计得到的激光标刻工艺参数标刻得到的标刻图像灰度测量值即标刻图像灰度实际值与利用估计得到的激光标刻工艺参数估计得到的标刻图像灰度估计值之间的吻合度较高。也就是说,利用估计得到的激光标刻工艺参数直接进行激光标刻得到的标刻图像的灰度值与预计得到的标刻图像的图像灰度值较为接近,因此,估计得到的激光标刻工艺参数可直接用于激光标刻,提高了激光标刻效果以及标刻效率。另外,在利用目标函数对激光标刻工艺参数进行估计时,可根据自动识别需要设定目标函数G的具体取值,从而可提高标刻图像的自动识别率。优选地,在所述步骤3中,采用免疫克隆算法拟合得出所述图像灰度值的计算模型方程中的拟合系数的值。进一步地,进行拟合时,采用的亲和度优化目标函数为其中,N为所述步骤1中进行等水平多因素正交试验时采集到的试验数据的组数,Gmj为一次亲和度计算中第j组试验得到的标刻图像的图像灰度估计值,Gcj为一次亲和度计算中第j组试验得到的标刻图像的图像灰度测量值。这样,可进一步提高拟合速度及拟合系数的准确度,进而可提高激光标刻工艺参数的估计精度。本发明还提出一种激光标刻方法,该激光标刻方法包括如下步骤:S1、利用在待标刻的铝锭的表面上烧蚀出浅色标刻背景区,且该浅色标刻背景区的灰度值方差σ2≤50,图像灰度均值M≥150;S2、利用权利要求1-3中任意一项所述的激光标刻工艺参数的估计方法估计出在所述浅色标刻背景区标刻铝锭标识用的激光标刻工艺参数;S3、利用所述步骤S2中估计出的激光标刻工艺参数在所述浅色标刻背景区内标刻所述铝锭标识。优选地,在所述步骤S1中,激光烧蚀工艺参数中填充线间距s的取值范围在0.01-0.2mm,激光扫描速度v的取值范围为500-1000mm/s,激光功率p的取值范围为10-20W,激光机Q频率f的取值范围为50-100kHz。优选地,在所述步骤S3中,在所述浅色标刻背景区内标刻所述铝锭标识时,激光标刻工艺参数中填充线间距s的取值范围为0.01-0.1mm,激光扫描速度v的取值范围为100-200mm/s,激光功率p的取值范围为12-20W,激光机Q频率f的取值范围为20-28kHz。采用该激光标刻方法在铝锭表面上标刻铝锭标识,直接采用估计得到的激光标刻工艺参数在浅色标刻背景区内标刻铝锭标识,而不用对激光标刻工艺参数进行反复调整,提高了铝锭标识的标刻效率;根据自动识别需要设定估计激光标刻工艺参数的目标函数,从而提高标刻得到的铝锭标识的自动识别率。附图说明图1为验证激光光斑重叠次数n、激光单脉冲能量e和填充线间距s对激光标刻效果的影响进行激光标刻试验得到的激光标刻图像;图2为以激光光斑重叠次数n为变化因素进行单因素变化试验得到的标刻图像的图像灰度值的变化曲线图;图3为以激光单脉冲能量e为变化因素进行单因素变化试验得到的标刻图像的图像灰度值的变化曲线图;图4为以填充线间距s为变化因素进行单因素变化试验得到的标刻图像的图像灰度值的变化曲线图;图5为等水平多因素正交试验得到的标刻效果图;图6为验证试验得到的标刻效果图;图7为标刻图像灰度估计值与验证试验得到的标刻图像灰度测量值的对比结果。具体实施方式下面结合附图对本发明激光标刻工艺参数的估计方法以及利用该估计方法估计得出的激光标刻工艺参数在铝锭表面标刻铝锭标识的激光标刻方法进行详细说明。根据激光烧蚀原理可知,激光标刻表面获取的能量取决于激光光斑重叠次数n和激光单脉冲能量e。其中,激光光斑重叠次数n是指在激光标刻过程中激光脉冲光斑沿直线方向移动过程中的内部区域的最大累加烧蚀次数,且在激光扫描速度v慢、Q频率f高时,激光光斑重叠次数n高,反之则反,并可表示为激光单脉冲能量e是指每个激光脉冲所包含的能量,且与激光功率P成正相关,与Q频率f成负相关,并可表示为由此推论可知,在进行激光标刻时,当激光光斑重叠次数n和激光单脉冲能量e相同时,激光标刻对材料能量输入相同,标刻得到的标刻图像的效果相同,即标刻图像的灰度值相同。为验证上述推论是否准确,发明人采用脉冲光纤激光器在材料化学成分如表1所示的牌号为Al99.7的铝块表面上进行标刻验证试验,其中,脉冲光纤激光器的聚焦激光束直径为d0,其他标刻工艺参数如表2所示。表1Al99.7材料化学成分(质量分数)AlFeSiCuCaMgZn99.75%0.17%0.05%0%0.02%0%0.01%表2激光标刻工艺参数其中,s为填充线间距,表示激光在烧蚀表面图形时,扫描线之间的间距。利用表2所示的激光标刻工艺参数在牌号为Al99.7的铝块表面进行标刻得到的激光标刻图像如图1所示。对应表2可知,图1中每一行中的四组标刻验证试验用的激光标刻工艺参数拥有相同的激光光斑重叠次数n、激光单脉冲能量e和填充线间距s;第2行和第3行中的标刻验证试验用的激光标刻工艺参数拥有相同的激光光斑重叠次数n和激光单脉冲能量e,不同的填充线间距s;第4行和第5行中的标刻验证试验用的激光标刻工艺参数拥有相同的激光光斑重叠次数n和激光单脉冲能量e,不同的填充线间距s;第2行和第4行中的标刻验证试验用的激光标刻工艺参数拥有相同的填充线间距s,不同的激光光斑重叠次数n和激光单脉冲能量e;第3行和第5行中的标刻验证试验用的激光标刻工艺参数拥有相同的填充线间距s,不同的激光光斑重叠次数n和激光单脉冲能量e。由此可见,除激光光斑重叠次数n和激光单脉冲能量e外,填充线间距s的取值也会对标刻得到的激光标刻图像的图像灰度值产生影响。为了分别研究激光光斑重叠次数n、激光单脉冲能量e、填充线间距s对激光标刻得到激光标刻图像的图像灰度值的影响,发明人采用脉冲光纤激光器在多块规格均为150mm×150mm×10mm且牌号均为Al99.7的铝块表面上进行单因素变化激光标刻试验,且试验用脉冲光纤激光器的聚焦激光束直径为0.05mm、焦距为20cm、最大输出功率为20W、波长为1064nm、脉冲宽度为100nm。首先,以激光光斑重叠次数n为变化因素进行三组单因素变化激光标刻试验,且该三组单因素变化激光标刻试验中激光单脉冲能量e的取值依次为0.5mJ、0.7mJ和0.9mJ,填充线间距s的取值均为0.1mm,试验标刻规格为8mm×8mm的正方形图形,并选用可避免因光照影响灰度值的扫描仪获取标刻图像的图像灰度值,且三组单因素变化激光标刻试验得到的三条图像灰度值的变化曲线如图2所示。由图2可知,在三条图像灰度值变化曲线起始位置处,图像灰度值分布不等,但随着激光光斑重叠次数n的值增大,三条图像灰度值变化曲线均呈整体下降趋势,且激光单脉冲能量e越大,下降速度越快,当激光光斑重叠次数n在5次到15次之间时,标刻图像取到最低的图像灰度值;在激光光斑重叠次数n达到一定次数后,标刻图像的图像灰度值逐渐上升,并趋于一致;在激光光斑重叠次数n超过15次后,标刻图像的图像灰度值变化缓慢,且趋于一致。其次,以激光单脉冲能量e为变化因素进行四组单因素变化试验,且该四组单因素变化激光标刻试验中激光光斑重叠次数n的取值依次为2、6、10和15,填充线间距s的取值均为0.1mm,试验标刻规格为8mm×8mm的正方形图形,并选用可避免因光照影响灰度值的扫描仪获取标刻图像的图像灰度值,且四组单因素变化激光标刻试验得到的四条图像灰度值的变化曲线如图3所示。由图3可知,四组单因素变化激光标刻试验得到的标刻图像的图像灰度值随着激光单脉冲能量e的增加,均呈下降趋势,且在不同的激光光斑重叠次数n下,图像灰度值下降速度不同,当激光光斑重叠次数为2时,图像灰度值下降速度较慢,随着激光光斑重叠次数n增大,图像灰度值下降速度变快,如激光光斑重叠次数为10和6时;当激光光斑重叠次数n到达一定次数后,图像灰度值趋于一定值,如激光光斑重叠次数为15时。此外,当激光单脉冲能量e小于0.3时,由于能量太小,激光标刻痕迹不明显,图像不清晰。最后,以填充线间距s为变化因素进行四组单因素变化试验,且该四组单因素变化激光标刻试验中激光光斑重叠次数n的取值依次为4、20、3、和10,激光单脉冲能量e的取值依次为0.3mJ、0.3mJ、0.6mJ和0.6mJ,试验标刻规格为8mm×8mm的正方形图形,并选用可避免因光照影响灰度值的扫描仪获取标刻图像的图像灰度值,且四组单因素变化激光标刻试验得到的四条图像灰度值的变化曲线如图4所示。由图4可知,四组单因素变化激光标刻试验得到的标刻图像的图像灰度值随着填充线间距s增大而逐渐增加,当填充线间距s在0.01mm到0.03mm之间变化时,图像灰度值增加明显;当填充线间距s大于0.03mm后,图像灰度值增幅较小趋于平稳;当填充线间距s超过0.1mm时,激光与铝块表面相互作用产生的热量无法影响填充线之间的铝块表面,铝块表面的灰度值几乎不发生变化,无法得到清晰的标刻图像。另外,由于填充线间距s越小,激光标刻效率越低,故,在进行激光标刻时,填充线间距s的取值一般大于0.5mm。通过上述三种单因素变化试验分析,可得出使用脉冲光纤激光器在牌号为Al99.7的铝块表面进行激光标刻时用的激光光斑重叠次数n、激光单脉冲能量e和填充线间距s的取值范围。但是,当激光光斑重叠次数n、激光单脉冲能量e和填充线间距s分别选取不同值时,脉冲光纤激光器在铝块表面进行激光标刻得到的标刻图像的图像灰度值不同,即标刻图像的颜色深度不同,当标刻图像的图像灰度值与标刻背景区的灰度值较为接近时,易导致标刻图像尤其是标刻图像中的条形码和/或二维码的自动识别率降低。为提高使用脉冲光纤激光器在铝锭表面上激光标刻得到的标刻图像的自动识别率,发明人根据上述试验结果建立标刻图像的图像灰度值的计算模型方程,从而根据该标刻图像的图像灰度值的计算模型可得出脉冲光纤激光器在铝锭表面上进行激光标刻所需的激光标刻工艺参数激光机Q频率f、激光扫描速度v以及激光功率p的值。首先,根据图2中所示的激光光斑重叠次数n与标刻图像的图像灰度值之间的对应关系,将仅受激光光斑重叠次数n影响的标刻图像的图像灰度值G1的计算模型方程拟合为:G1=a0+a1n+a2n2+a3n3(1)即其中,ai为拟合系数,i=0、1、2、3。其次,根据图3中所示的激光单脉冲能量e与标刻图像的图像灰度值之间的对应关系,将仅受激光单脉冲能量e影响的标刻图像的图像灰度值G'2的计算模型方程拟合为:其中,a41和a5为拟合系数。接着,根据图4中所示的填充线间距s与标刻图像的图像灰度值之间的对应关系,到将仅受填充线间距s影响的标刻图像的图像灰度值G'3的计算模型方程拟合为:其中,a42和a8为拟合系数。在对G1、G'2和G'3的计算模型方程进行拟合时,可优选采用免疫克隆算法拟合得到拟合系数的值。为提高免疫克隆算法的拟合优度,将G'2和G'3变形为G2和G3,其中,因为当a6=a9=0,a7=a10=1时,G'2=G2,G'3=G3,所以,在使用免疫克隆算法求G'2、G'3、G2和G3的最优解时,G'2最优值包括在G2中,G'3的最优值包括在G3中,故可得标刻图像的图像灰度值G的计算模型方程:G=G1×G2×G3(7)其中,a4=a41+a42即,由于脉冲光纤激光器的聚焦激光束直径d为不可调的工艺参数,且故,其中,bi=aidi,i=0、1、2、3,b4=a4、b5=a5、b6=a6、b7=a7、b8=a8、b9=a9、b10=a10。根据单因素试验得到的激光光斑重叠次数n、激光单脉冲能量e和填充线间距s的取值范围,结合激光光斑重叠次数n和激光单脉冲能量e的物理含义,设置脉冲光纤激光器的可调激光标刻工艺参数及水平如表3所示。表3可调激光标刻工艺参数及水平根据表3设计等水平多因素正交试验,共获取了25组激光标刻工艺参数,采用该25组激光标刻工艺参数进行标刻得到的25个标刻图像如图5所示,并利用可避免因光照影响灰度值的扫描仪获取标刻图像的图像灰度测量值,且激光标刻工艺参数及其对应的标刻图像的图像灰度测量值如表4所示。表4等水平多因素正交试验的试验数据组号s(mm)v(mm/s)P(w)f(kHz)e(mJ)n图像灰度测量值10.0610010200.51012820.0720012220.555.515430.0830014240.58416940.0940016260.623.2517250.1050018280.642.817660.0730016280.5714.6716270.0840018200.92.517080.0950010220.452.219890.1010012240.512145100.0620014260.546.5143110.0850012260.462.6196120.0910014280.514142130.1020016200.85148140.0630018220.823.67150150.0740010240.423201160.0920018240.756139170.1030010260.384.33186180.0640012280.433.5186190.0750014200.72184200.0810016220.7311134210.1040014220.672.75174220.0650016240.672.4169230.0710018260.6913137240.0820010280.367170250.0930012200.63.33168根据上述等水平多因素正交试验的试验数据可知,激光标刻工艺参数与标刻图像的图像灰度值之间没有明显的规律性,标刻图像的图像灰度值邻域内的标刻图像对应的激光标刻工艺参数并非简单地分布在该标刻图像的图像灰度值对应的激光标刻工艺参数的邻域内,而是分布在若干个标刻图像的图像灰度值对应的激光标刻工艺参数的邻域并集之中,比如第1组、第12组、第16组、第20组和第23组试验,试验用的激光标刻工艺参数是在功率P为10~18W,Q频率f为20~28kHz,填充线间距s为0.06~0.09mm,扫描速度v为100~200mm/s取值范围内选取的不同取值的激光标刻工艺参数的进行组合,并计算得出取值不同的激光单脉冲能量e和激光光斑重叠次数n,且这些不同取值的激光标刻工艺参数组合后在铝块表面标刻出图像灰度值相近的标刻图像。但是,并非在以上取值范围之内任意选取的激光标刻工艺参数组合后都可以标刻出图像灰度值相近的标刻图像,而且不同激光标刻工艺参数组合有可能标刻出图像灰度值差异较大的标刻图像。根据以上分析可知,等水平多因素正交试验体现出不同激光标刻工艺参数组合与标刻得到标刻图像的图像灰度值之间的对应关系:多组相异的激光标刻工艺参数进行组合可标刻出图像灰度值相近的标刻图像;不同激光标刻工艺参数组合后可标刻出图像灰度值差异较大的标刻图像。因此,上述所选的等水平多因素正交试验数据代表性强,能够作为的合理数据对标刻图像的图像灰度值G的计算模型方程中的拟合系数进行拟合。根据表4中的等水平多因素正交试验数据拟合得出标刻图像的图像灰度值G的回归经计算模型方程中的拟合系数bi(i=0、1、2、3)、b4、b5、b6、b7、b8、b9和b10,且在拟合过程中,拟合目标是使标刻图像的图像灰度测量值与图像灰度预测值之间的误差和的值最小。为提高拟合速度及拟合准确度,优选采用免疫克隆算法作为拟合算法进行拟合。在拟合过程中,采用的亲和度优化目标函数为:其中,N为水平多因素正交试验时采集到的试验数据的组数,在表4中,N=25,Gmj为一次亲和度计算中第j组试验得到的标刻图像的图像灰度估计值,Gcj为一次亲和度计算中第j组试验得到的标刻图像的图像灰度测量值。利用表4中的等水平多因素正交试验的试验数据拟合得出标刻图像的图像灰度值G的计算模型方程中的拟合系数b0、b1、b2、b3、b4、b5、b6、b7、b8、b9和b10后,得到的标刻图像的图像灰度值G的计算模型方程为:为避免拟合得到的拟合系数不可信,下面利用复决定系数R2与方差分析F值来衡量标刻图像的图像灰度值G的计算模型方程对实测数据集的拟合优度以及计算模型方程的可信度,结果如下:其中,rss为标刻图像的图像灰度测量值与图像灰度估计值之间的残差平方和,tss为标刻图像的图像灰度测量值与图像灰度估计值之间的总偏差平方和;其中,ess为回归平方和,h为回归平方和的自由度,w-h-1为残差平方和的自由度。根据上述结果可知,由于R2=0.97,接近1,拟合优度较好;查F表可知,F=51.45》F0.05(10,15)=2.54,标刻图像的图像灰度值G的计算模型方程的可信度较高。为加深标刻图像的颜色深度,提高标刻图像的自动识别率,发明人设定激光标刻的标刻图像的图像灰度值G<150。也就是说,在利用标刻图像的图像灰度值G的计算模型方程估计得出激光标刻工艺参数时的目标函数为G<150。当然,在实际标刻过程中,用户可根据自动识别需要选取目标函数G的具体值。为验证本发明激光标刻工艺参数的估计方法的有效性,利用表5所示的25组激光标刻工艺参数在牌号为Al99.7的铝块表面进行激光标刻验证试验,标刻图像如图6所示,且采用不同激光标刻工艺参数标刻得到的标刻图像的图像灰度测量值如表5所示。表5激光标刻验证试验的试验数据同时,利用公式(11)可依次计算出利用表5中所示的25组激光标刻工艺参数在牌号为Al99.7的铝块表面进行激光标刻所得的标刻图像的图像灰度估计值,且该图像灰度估计值与激光标刻验证试验所得出的标刻图像的图像灰度测量值的对比结果如图7所示。由图7可知,采用本发明激光标刻工艺参数的估计方法估计得到的标刻图像的图像灰度估计值与激光标刻验证试验所得的标刻图像的图像灰度测量值的吻合度较高。下面,对结合上述激光标刻工艺参数的估计方法对待标刻铝锭上标刻铝锭标识的激光标刻方法进行详细说明,该激光标刻方法包括如下步骤:S1、利用脉冲光纤激光器在待标刻的铝锭的表面上烧蚀出浅色标刻背景区,且该浅色标刻背景区的灰度值方差σ2≤50,图像灰度均值M≥150。优选地,在待标刻的铝锭表面上烧蚀浅色标刻背景区时,激光烧蚀工艺参数中填充线间距s的取值范围在0.01-0.2mm,激光扫描速度v的取值范围为500-1000mm/s,激光功率p的取值范围为10-20W,激光机Q频率f的取值范围为50-100kHz。S2、利用上述激光标刻工艺参数的估计方法估计出在浅色标刻背景区内标刻铝锭标识所需的激光标刻工艺参数;S3、利用脉冲光纤激光器在浅色标刻背景区内标刻铝锭标识,且标刻用的激光标刻工艺参数为步骤S2中估计出得出的激光标刻工艺参数。优选地,在浅色标刻背景区内标刻铝锭标识时,激光标刻工艺参数中填充线间距s的取值范围为0.01-0.1mm,激光扫描速度v的取值范围为100-200mm/s,激光功率p的取值范围为12-20W,激光机Q频率f的取值范围为20-28kHz。当前第1页1 2 3