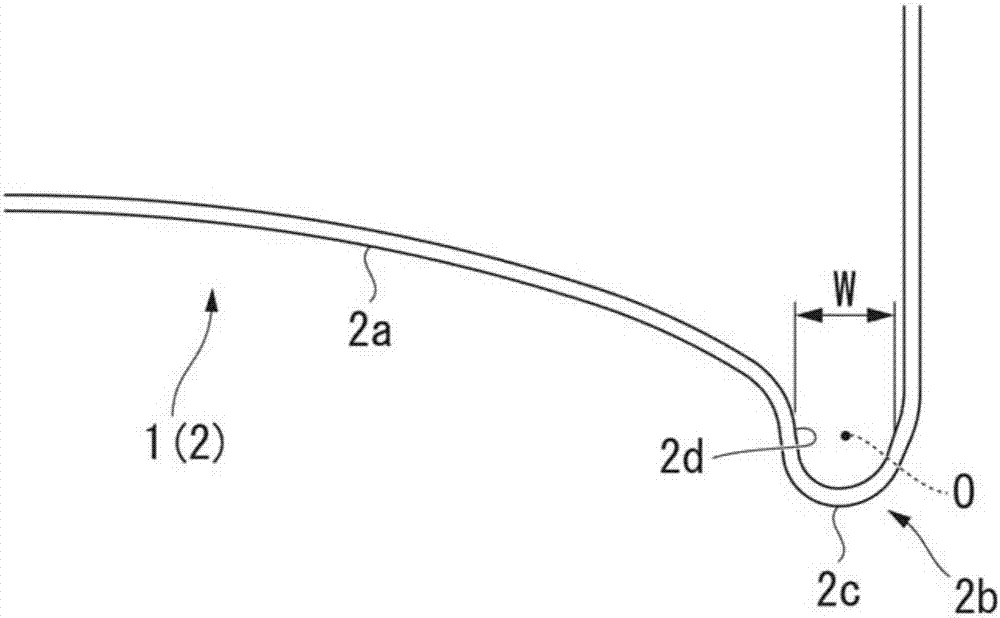
本发明涉及瓶罐及其制造方法。本申请基于2016年11月29日在日本申请的专利申请2016-231588号要求优先权,并且在此援引其内容。
背景技术:
:作为这种瓶罐,例如在专利文献1中记载有如下的瓶罐:其具备:大径的瓶体部;肩部,被连续设置在该瓶体部的罐轴方向上端,并且随着朝向罐轴方向上方而逐渐缩径;口部,被连续设置在该肩部的罐轴方向上端,并且向罐轴方向上方延伸,瓶体部的罐轴方向上端部的壁厚比该上端部之外的瓶体部的罐轴方向上部的壁厚更厚。另外,在该专利文献1中,作为这种瓶罐的制造方法,记载有如下的制造方法:对金属制的有底筒状体实施多次减薄加工而形成DI罐,该DI罐具备开口部和被连续设置在该开口部的罐轴方向下端且向罐轴方向下方延伸的瓶体部,并且该瓶体部的罐轴方向上部比开口部薄,在对上述有底筒状体实施最后的减薄加工来形成DI罐时,通过事先在多个减薄模具之间进行上述减薄加工的冲头的外表面、与有底筒状体的瓶体部的形成预定部中的罐轴方向上端部对应的位置上形成凹部,来制造在有底筒状体中瓶体部的形成预定部中的罐轴方向上端部比该上端部之外的瓶体部的形成预定部中的罐轴方向上部的厚度更厚的DI罐,并且基于该DI罐成型上述肩部和口部而制造上述瓶罐。并且,在该专利文献1中还记载了,在基于这种DI罐形成瓶罐的情况下,通常有必要将DI罐的开口部中的壁厚最厚的部分的壁厚设为与瓶体部中的壁厚最薄的部分的壁厚相比厚80μm(0.08mm)以上。专利文献1:日本专利公开2009-082989号公报但是,作为这种瓶罐,一般流通较多的是其瓶体部的外径(瓶体部的外周面的直径)为约66mm的瓶罐。另一方面,这种瓶罐具有如下问题:特别是对于儿童或手小的女性、握力弱的老人等而言较粗而难以握持,例如在开闭盖时有可能因手打滑或不留神而导致将瓶罐掉落。因此,近年来,瓶体部的外径细的瓶罐的需求提高。然而,对于这种细径的瓶罐而言,如专利文献1所记载的,如果通过在冲头的外表面的与罐轴方向上端部对应的位置上形成凹部,从而在DI罐中将开口部中的壁厚最厚的部分的壁厚设为比瓶体部中的壁厚最薄的部分的壁厚大80μm以上,则导致该壁厚最厚的部分与壁厚最薄的部分之间产生的高低差大小在有底筒状体的内径中所占的比例较大。因此,在拔出冲头时,有可能因凹部卡在有底筒状体中而容易产生冲头的拔出不良,从而显著降低瓶罐的制造效率或成品率。技术实现要素:本发明是在这种背景下提出的,其目的在于提供一种即使为瓶体部的外径细的瓶罐,在制造工序中也难以产生冲头的拔出不良的瓶罐,并且提供一种能抑制因这种冲头的拔出不良而导致的制造效率或成品率的降低的瓶罐的制造方法。为了解决上述问题并实现这种目的,本发明的瓶罐在与罐主体的底部一体成型的外周部,从上述底部朝向上述罐主体的上端开口部依次形成有以罐轴为中心的圆筒状的瓶体部、随着朝向上端侧而缩径的肩部、从该肩部进一步朝向上端侧延伸的颈部、以及盖安装部,上述瓶罐的特征在于,上述瓶体部的外周面的直径φ1为58mm以下,该瓶体部的外周面的直径φ1与上述罐主体的从底部的下端至上述上端开口部的上述罐轴方向的高度h之比φ1/h为0.35以下,上述瓶体部中的上述罐主体的壁厚最厚的部分与壁厚最薄的部分的壁厚差为0.05mm以下。另外,本发明的瓶罐的制造方法为这种瓶罐的制造方法,其特征在于,具备:DI冲压工序,对金属板经拉深加工而成型的杯状坯料实施再拉深及减薄加工和底部成型加工,成型形成有上述底部和外径与上述瓶体部相同的圆筒部的有底圆筒体;瓶肩颈成型工序,通过使该有底圆筒体的上述圆筒部的上端侧部分缩径,成型上述肩部和随着从该肩部朝向上端侧而进一步缩径的上述颈部;和盖安装部成型工序,在上述颈部的上端部成型上述盖安装部,在上述DI冲压工序中成型为,上述有底圆筒体的上述圆筒部中的壁厚最厚的部分与壁厚最薄的部分的壁厚差为0.05mm以下。由于上述结构的瓶罐的瓶体部的外径即瓶体部的外周面的直径φ1为58mm以下,因此儿童或手小的女性、老人也容易握持,且盖的开闭容易,并且不留神而将瓶罐掉落的可能性也小。此外,由于可将该瓶体部的外周面的直径φ1与上述罐主体的从底部的下端至上述上端开口部的上述罐轴方向的高度h之比φ1/h设为0.35以下,并且将罐主体的高度设为大于细的瓶体部的外径,因此能充分确保瓶罐的内容量。并且,在上述结构的瓶罐及其制造方法中,上述有底圆筒体中的上述圆筒部的壁厚最厚的部分与壁厚最薄的部分的壁厚差为0.05mm以下,即,该壁厚最厚的部分与壁厚最薄的部分之间的厚度差在有底圆筒体的内径中所占的比例极小。因此,在对杯状坯料实施再拉深及减薄加工和底部成型加工而成型有底圆筒体的DI冲压工序中,从有底圆筒体拔出冲头时的拔出性优良,发生冲头卡在有底圆筒体的内周面上而拔出不良的情况较少,能够进行稳定的成型。因此,即使为如上所述的细径的瓶罐,在其制造工序中也能够抑制制造效率或成品率下降。但是,为了确保罐主体的强度,在这种瓶罐中,通常在上述罐主体的底部的中央形成有向罐轴方向内侧凹陷的圆顶部,并且在与该圆顶部的外周缘部相连的上述罐主体的底部的外周,在绕上述罐轴的圆周方向上形成有在沿上述罐轴的剖面中突端部呈凸曲线状且向上述罐轴方向的外侧突出的环状凸部,在使底部朝下将罐主体竖立在水平面上时,该环状凸部的突端绕上述罐轴而成的圆成为与该水平面接地的接地圆。但是,在如上述的细径的瓶罐中,该接地圆的直径也小,从而导致竖立在水平面上的罐主体容易倒下。因此,优选该接地圆的直径、即环状凸部的突端绕罐轴而成的圆的直径φ2与上述瓶体部的外周面的直径φ1之比φ2/φ1大于0.85,并且形成为使接地圆在罐主体的底部中尽可能位于外周侧。另一方面,对由如上述的制造方法制造的瓶罐,在通过上述DI工序来成型形成有具备圆顶部和环状凸部的底部和圆筒部之后,通过利用喷射喷嘴对该有底圆筒体的内表面喷雾出涂料并将其干燥而形成涂膜,由此提供耐蚀性。然而,对于细径的瓶罐而言,特别是在如上述形成为使接地圆位于罐主体的底部的尽可能外周侧时,由于由喷射喷嘴进行的涂料的喷雾范围被有底圆筒体的圆筒部遮挡,因此有可能无法将涂料充分遍布到有底圆筒体的内表面中的环状凸部的突端附近。因此,如上述在罐主体的底部的中央形成有向罐轴方向内侧凹陷的圆顶部,并且在与该圆顶部的外周缘部相连的罐主体的底部外周,在绕罐轴的圆周方向上形成有在沿罐轴的剖面中突端部呈凸曲线状且向罐轴方向的外侧突出的环状凸部的情况下,为了使涂料充分地遍布到上述有底圆筒体的内表面中的环状凸部的突端附近,优选将在沿上述罐轴的剖面中在上述环状凸部的突端部所成的凸曲线的中心位置上的该环状凸部的内周面的相对于上述罐轴的径向宽度W设为2.5mm以上,扩大该环状凸部在有底圆筒体内表面上的开口宽度,从而使喷射到有底圆筒体的内表面上的涂料弹回而容易流入到环状凸部的突端附近。如上述所说明的,根据本发明,即使为易于握持的细径的瓶罐,也能确保内容量的同时,能防止在其制造工序中产生冲头的拔出不良并能稳定地成型,从而能抑制制造效率或成品率的下降。附图说明图1是表示本发明的瓶罐的一实施方式的局部剖视侧视图。图2是图1中的A部的放大剖视图。图3是表示本发明的瓶罐的制造方法的一实施方式的流程图。具体实施方式图1及图2是表示本发明的瓶罐的一实施方式的图,图3是表示本发明的瓶罐的制造方法的一实施方式的图。如图1所示,本实施方式的瓶罐的罐主体1具备底部2和与该底部2一体形成且从底部2的外周缘向上端侧(在图1中为上侧)延伸的外周部3,本实施方式的瓶罐呈朝向该上端侧缩径且以罐轴C为中心的大致多段的有底圆筒状。在底部2的中央形成有向罐轴C方向的内侧(罐主体1的上端侧)凹陷且沿罐轴C的剖面为大致圆弧状的圆顶部2a,并且在该圆顶部2a的外周缘部沿绕罐轴C的圆周方向连续形成有剖面呈凸曲线状且朝向罐轴C方向的外侧(罐主体1的下端侧)突出的环状凸部2b。另外,在外周部3,从底部2朝向罐主体1的上端侧的开口部4依次形成有:圆筒状的瓶体部5,其以罐轴C为中心;圆锥台面状的肩部6,其随着朝向上端侧而以恒定的倾斜度逐渐缩径;筒状的颈部7,从该肩部6进一步朝向上端侧延伸;和盖安装部8,其仍为筒状且在本实施方式中对该盖安装部8实施螺纹切削加工。在制造这种瓶罐的本发明的瓶罐的制造方法的一实施方式中,如图3的流程图所示,首先,通过在由深拉冲压机进行的深拉冲压工序中将铝合金等金属板冲裁为圆板状并实施拉深加工,从而制造深度浅的杯状坯料。接着,在由DI(DrawingandIroning,拉深减薄)冲压机进行的DI冲压工序中利用冲头和多个拉深模具对该杯状坯料实施再拉深及减薄加工而使其向罐轴C方向延伸,并且通过实施底部成型加工,从而成型在底部2形成有上述圆顶部2a和环状凸部2b的有底圆筒体(DI罐)。在此,在本实施方式中,通过深拉冲压工序形成为杯状坯料的金属板为JISH4000中的A3004或A3104铝合金,使用经205℃×20分钟的烘焙之后的0.2%屈服点在235N/mm2~265N/mm2范围内的铝合金。另外,在由该杯状坯料成型的有底圆筒体的外周部形成有以上述罐轴C为中心的圆筒部,该圆筒部的外径为与罐主体1的瓶体部5的外径(后述的φ1)大致相等的恒定外径。即,有底圆筒体的圆筒部的外径为58mm以下。另外,在上述底部成型加工中,优选以后述的环状凸部2b的突端绕罐轴C而成的圆的直径φ2与瓶体部5的外周面的直径φ1(有底圆筒体的圆筒部的外径)之比φ2/φ1大于0.85的方式,成型环状凸部2b。另外,在上述底部成型加工中,优选以后述的环状凸部2b的内周面的径向宽度W为2.5mm以上的方式成型环状凸部2b。在第一清洗工序中清洗并干燥如此成型的有底圆筒体,接着在涂装工序中对内外表面实施涂装之后进行干燥烧结。在该过程中,使有底圆筒体沿圆周方向旋转的同时,通常利用多个喷射喷嘴从该有底圆筒体的开口部喷射涂料,从而对有底圆筒体的内表面进行涂装。此外,在利用瓶肩颈翻边机(ボトルネッカー)的瓶肩颈成型工序中利用金属模使圆筒部的上述上端侧部分的下端侧缩径而成型上述肩部6和颈部7,接着在盖安装部成型工序中通过对颈部7的上端侧实施上述螺纹切削加工等而形成上述盖安装部8,由此以上述方式实施涂装后的有底圆筒体成型为如图1所示的瓶罐的罐主体1。在通过第二清洗工序清洗并干燥如此成型的罐主体1之后,在检查工序中检查有无气孔或有无外面的异物附着、伤痕、污染、印刷不良等后运送到饮料工厂等中,在填充饮料等内容物之后在盖安装部8安装未图示的盖并密封后上市。此外,在上述各工序期间或各工序中,进行切断有底圆筒体的上端缘的修边或按照需要再成型底部的环状凸部2b的剖面形状的底部改形。并且,在由这种实施方式的制造方法制造的本实施方式的瓶罐中,该罐主体1的上述瓶体部5的外径,即图1所示的瓶体部5的外周面的直径φ1为58mm以下,该瓶体部5的外周面的直径φ1与罐主体1的从底部2的下端(在本实施方式中为罐主体1的外表面中的环状凸部2b的突端)至上端侧的上述开口部4的罐轴C方向的高度h之比φ1/h为0.35以下,进一步瓶体部5中的罐主体1的壁厚最厚的部分与壁厚最薄的部分的壁厚差为0.05mm以下。另外,如图2所示,在本实施方式的瓶罐中,上述环状凸部2b的向罐轴C方向外侧突出的突端部2c以沿罐轴C的剖面呈大致半圆弧状的方式突出。从罐轴C方向的外侧与该突端部2c相切且与罐轴C垂直的平面和环状凸部2b所成的接地圆的直径、即罐主体1外表面中的环状凸部2b的突端绕罐轴C而成的圆的直径φ2与上述瓶体部的外周面的直径φ1之比φ2/φ1大于0.85。此外,罐主体1在如此向罐轴C方向的外侧以剖面大致半圆弧状突出的环状凸部2b的突端部2c中的内周面被形成为在罐轴C方向上该半圆弧的中心O位置上的相对于罐轴C的半径方向(也称作与罐轴C垂直的方向或径向)的宽度W为2.5mm以上。即,在本实施方式中,以利用与罐轴C垂直且通过上述半圆弧的中心O的平面切断后的环状凸部2b内表面的内侧面与外侧面之间的间隔为2.5mm以上的方式,通过DI冲压工序和底部改形来形成环状凸部2b。换言之,在沿罐轴C的剖面(通过罐轴C且与罐轴C平行的剖面)中,在中心O的罐轴C方向位置上的突端部2c的内周面的径向的宽度W为2.5mm以上。由于如此构成的瓶罐的罐主体1的瓶体部5的外径,即瓶体部5的外周面的直径φ1为58mm以下,因此易于握持,且即使为儿童或手小的女性、老人也容易进行盖的开闭,并且因未成功地握持而将瓶罐掉落的可能性也小。另外,即使如此瓶体部5的外径较细,该瓶体部5的外周面的直径φ1与罐主体1的从底部2的下端至上端的开口部4的罐轴C方向的高度h之比为0.35以下,能够相对于瓶体部5的外径加大罐主体1的高度,从而能够充分地确保瓶罐的内容量。此外,为了如此确保内容量的同时,更易于握持罐主体1,优选上述直径φ1为58mm以下。此外,优选将直径φ1设为48mm以上,更优选为52~57mm,但并不限定于此。另外,优选将直径φ1与高度h之比φ1/h设为0.30以上,更优选为0.34~0.35,但并不限定于此。并且,在上述结构的瓶罐及其制造方法中,将罐主体1的作为瓶体部5的有底圆筒体(DI罐)中的圆筒部的壁厚最厚的部分与壁厚最薄的部分的壁厚差设为0.05mm,并且形成于该壁厚最厚的部分与壁厚最薄的部分之间的厚度差的大小相对于伴随外周面的直径φ1变细而变小的有底圆筒体的内径所成的比例极小。因此,当在DI冲压工序中利用冲头和多个拉深模具对杯状坯料实施再拉深及减薄加工和底部成型加工而成型有底圆筒体时,拉拔冲头时冲头卡在有底圆筒体的内周面上的情况较少,所谓的冲头拔出性良好。此外,在成型这种圆筒部的壁厚最厚的部分与壁厚最薄的部分的壁厚差小的有底圆筒体时,在DI冲压工序中使用无凹部且具有外径恒定的圆筒面状的外周面的冲头即可,而无需使用如专利文献1所记载的冲头那样的具有凹部的冲头。即使使用这种冲头,但由于本实施方式的瓶罐的直径φ1较小,因此难以产生专利文献1所记载的发明所要解决的壁厚不均匀的问题,从而不会产生缺料或瓶体断裂。因此,根据如此构成的瓶罐及其制造方法,因如上述的冲头卡止而产生拔出不良的情况较少,能够稳定地成型有底圆筒体而制造罐主体1。因此,即使如上述瓶体部5的外周面的直径φ1为58mm以下的瓶罐,也能够进行有效的制造,并且还能防止产品成品率下降。此外,优选将瓶体部5中的罐主体1的壁厚最厚的部分与壁厚最薄的部分的壁厚差、即有底圆筒体的圆筒部的壁厚最厚的部分与壁厚最薄的部分的壁厚差设为极小,更优选为0.010~0.040,但并不限定于此。另外,本实施方式的瓶罐被形成为,罐主体1的底部2中的环状凸部2b的突端绕罐轴C(圆周方向)而成的圆的直径φ2与上述瓶体部5的外周面的直径φ1之比φ2/φ1大于0.85,并且该环状凸部2b的突端在底部2中最靠外周侧。因此,即使仍为如上述的细瓶罐,也通过使该环状凸部2b的突端接地而提高竖立放置瓶罐时的稳定性,能防止如在开盖状态下瓶罐容易倾倒而导致内容物溢出的情况。此外,优选将直径φ2与直径φ1之比φ2/φ1设为0.95以下,更优选为0.85~0.95,但并不限定于此。另一方面,在本实施方式中,环状凸部2b在该环状凸部2b的突端部2c在沿罐轴C的剖面中所成的凸曲线(半圆弧)的中心O位置上的内周面相对于罐轴C的径向宽度W为2.5mm以上,即较大地确保环状凸部2b的突端部2c在有底圆筒体内表面上的开口宽度。因此,当在涂装工序中如上述利用喷射喷嘴喷雾出涂料而对在DI冲压工序中成型的有底圆筒体的内表面进行涂装时,即使因罐主体1的作为瓶体部5的有底圆筒体的圆筒部的外径较小而喷雾范围被遮挡,也能够通过使喷雾出的涂料弹回而使涂料从以较大的宽度W开口的环状凸部2b的开口部还流入到突端的里侧内表面中以切实地实施涂装,从而能防止因涂装不均而损坏耐蚀性。特别是,在如上述环状凸部2b的突端在罐主体1的底部2中最靠外周侧的情况下,是效的。此外,优选将上述宽度W设为1.0mm以上,更优选为2.0~2.5mm,但并不限定于此。此外,优选在沿罐轴C的剖面中比如上述呈凸曲线状的突端部2c更靠罐主体1的上端侧的环状凸部2b的内壁面2d与罐轴C所成的角度为0°即与罐轴C平行,或者在8°为止的范围内以随着朝向上端侧而朝向罐主体1的内周侧的方式倾斜。详细而言,内壁面2d光滑地连接圆顶部2a和突端部2c,并且内壁面2d相对于突端部2c的中心O位于罐轴C方向上端侧。并且,优选内壁面2d与罐轴C所成的角度为0°~8°。虽然若该内壁面2d相对于罐轴C以超过8°的角度随着朝向上端侧而朝向罐主体1的内周侧倾斜,则涂料易于流入,但有可能降低罐主体1的底部2的耐压强度。[实施例]接着,列举本发明的实施例对本发明的效果进行证实。在本实施例中,首先基于上述实施方式成型将被制造为如下的两种瓶罐的有底圆筒体(DI罐):瓶体部5的外周面的直径φ1为58mm以下,该瓶体部5的外周面的直径φ1与罐主体1的从底部2的下端至上端的开口部4的罐轴C方向的高度h之比φ1/h为0.35以下,瓶体部5中的罐主体1的壁厚最厚的部分与壁厚最薄的部分的壁厚差为0.05mm以下,进一步环状凸部2b的突端绕罐轴C而成的圆的直径φ2与瓶体部5的外周面的直径φ1之比φ2/φ1大于0.85。将上述两种瓶罐作为实施例1、2,在表1中示出制造为瓶罐时的各尺寸和比率。此外,壁厚差为如下的值:将成型的有底圆筒体中三个罐的瓶体部5(有底圆筒体的圆筒部)的壁厚,对各个罐求出以每一罐为单位在沿罐轴C方向距离有底圆筒体的底部和上端分别为有底圆筒体高度的20%的部位处,沿圆周方向等间隔分别测量八个点时的最大值与最小值之差,并将其平均后的值。另外,作为对于这些实施例1、2的比较例,基于专利文献1所记载的制造方法制造了将被制造为如下的一种瓶罐的有底圆筒体(DI罐):虽然瓶体部5的外周面的直径φ1与实施例1相同,但高度h低且比率φ1/h大于0.35,比率φ2/φ1小于0.85,并且瓶体部5中的罐主体1的壁厚最厚的部分与壁厚最薄的部分的壁厚差大于0.05。将其作为比较例1,在表1中示出制造为瓶罐时的各尺寸和比率。此外,壁厚差为将同样成型的有底圆筒体中三个罐的瓶体部5的壁厚,对各个罐求出以每一罐为单位在沿罐轴C方向距离底部和上端分别为有底圆筒体高度的20%的部位处,沿圆周方向等间隔分别测量八个点时的最大值与最小值之差并将其平均后的值,该比较例1的瓶罐的壁厚差均大于0.05mm。[表1]φ1(mm)h(mm)φ1/hφ2(mm)φ2/φ1实施例152.61570.3447.60.90实施例258.01660.3550.00.86比较例152.61240.4242.00.80其结果,对于实施例1、2的瓶罐而言,即使连续成型1000罐有底圆筒体,也不会因冲头的拔出不良而导致DI冲压机停止。相反,在制造比较例1的瓶罐时,在制造1000罐有底圆筒体之前,因冲头的拔出不良而导致DI冲压机频繁停止,无法避免制造效率或产品成品率的下降。接着,作为实施例11、12分别制造100罐如下的两种瓶罐:直径φ1、φ2、高度h、比率φ1/h、φ2/φ1及壁厚差与实施例1相同,并且将在沿罐轴C的剖面中环状凸部2b的突端部2c所成的凸曲线的中心O位置上的环状凸部2b的内周面相对于罐轴C的径向宽度W设为2.5mm,作为比较例11、12分别制造100罐该宽度W小于2.5mm的两种瓶罐。并且,通过测量这些瓶罐的ERV(瞬间电流值)来判断在罐主体1的内表面中涂装是否切实地实施至环状凸部2b的突端,将在各100罐中具有ERV为25mA以上的瓶罐的情况评价为叉的标记(×),将不存在ERV为25mA以上的瓶罐的情况评价为圈的标记(○)。表2中与宽度W一同示出该结果。此外,ERV通过如下方法来获取:首先,将浓度为1%的盐水注入到罐主体1内,并将罐主体1用作阳极,接着使作为阴极的不锈钢制棒浸渍到罐主体1内的盐水中之后,对阳极与阴极之间施加4秒钟6.2伏电位差,测量施加该电位差之后的瞬间电流(ERV)。[表2]W(mm)ERV(mA)实施例113.0○实施例122.5○比较例112.0×比较例121.5×根据该表2的结果,在将上述宽度W设为2.5mm以上的3.0mm及2.5mm的实施例11、12中,未确认到ERV为25mA以上的瓶罐,即未确认到在罐主体1的内表面具有涂装不匀或涂装不良的瓶罐,与此相对,在上述宽度W为2.0mm及1.5mm的比较例11、12中,确认到ERV为25mA以上的瓶罐,有可能因涂装不良而导致耐蚀性的降低。产业上的可利用性根据本发明,即使为瓶体部的外径细的瓶罐,也能提供在制造工序中难以产生冲头的拔出不良的瓶罐,从而能抑制因瓶体断裂而导致的制造效率或成品率的下降。附图标记说明1罐主体2罐主体1的底部2a圆顶部2b环状凸部2c环状凸部2b的突端部2d环状凸部2b的内壁面3罐主体1的外周部4开口部5瓶体部6肩部7颈部8盖安装部C罐轴φ1瓶体部5的外周面的直径h罐主体1的从底部2的下端至上端的开口部4的罐轴C方向的高度φ2环状凸部2b的突端绕罐轴C而成的圆的直径O在沿罐轴C的剖面中环状凸部2b的突端部2c所成的凸曲线的中心W在沿罐轴C的剖面中环状凸部2b的突端部2c所成的凸曲线的中心O位置上的环状凸部2b的内周面的相对于罐轴C的径向宽度当前第1页1 2 3