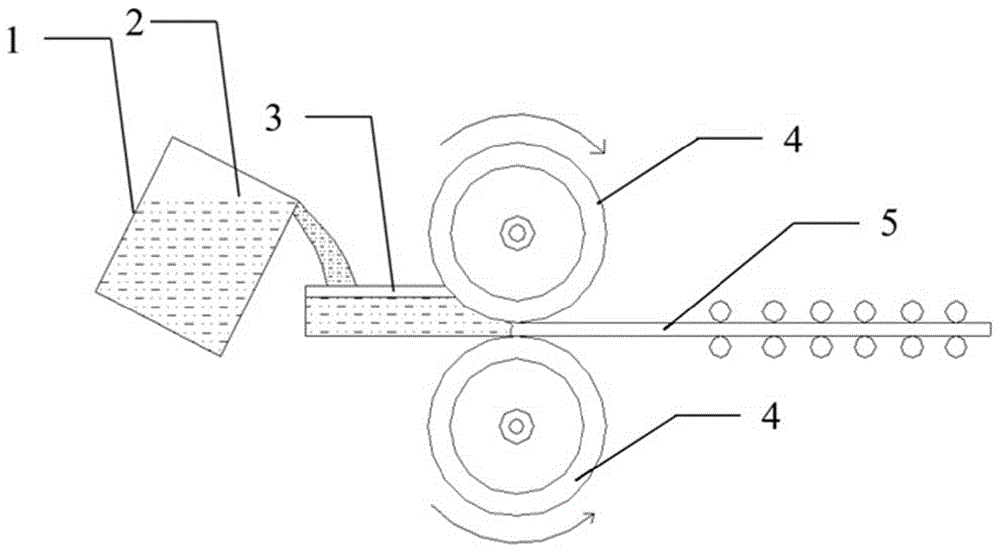
本发明属于铸轧机用铸轧辊领域,具体涉及一种辊套的表面强化方法及辊套。
背景技术:
:双辊连续铸轧技术是将熔炼炉1内的金属熔液2注入前箱3,然后由前箱3将金属熔液2直接送入两个带水冷系统的旋转铸轧辊4之间,熔体在辊缝间极短时间内完成凝固和热轧两个过程(如图1所示),得到板坯5制品。作为连续铸轧工艺核心部件的铸轧辊主要由辊套、辊芯和冷却水通道组成。其中,处于外层的辊套与熔液直接接触,同时实现“结晶”和“轧制”功能,是连续铸造工艺的核心部件。目前,普遍使用的辊套材料为钢辊套(32Cr3Mo1V、20Cr3MoWV、35CrMnMo、45MnMoWV等),由于辊套在整个铸轧过程中始终与高温金属熔液接触,在热-力耦合场的作用下对辊套表面的热疲劳性能、抗热冲击、抗高温软化性能、耐磨损性能等提出了更高要求。目前,在实际生产过程中,每隔一段时间(18天-20天)需要在车床上将辊套表面的磨损层车削掉,车削机加工的量为5-10mm,然后再次装配到铸轧机上使用。频繁的装卸打磨辊套表面不仅造成材料浪费,而且影响生产效率。对辊套表面进行局部强化,提高辊套表面的耐磨损性能,对于提高辊套使用寿命和连续铸轧生产效率具有重要意义。公告号为CN103993143B的中国发明专利公开了一种冷却辊表面加工工艺,其包括以下步骤:对冷却辊辊套(铜辊)进行切削,将辊套固定在旋转轴上,使之旋转;然后对辊套表面进行喷丸处理;对旋转中的辊套表面采用机械滚压的方式进行滚压处理,滚压的作用力为200-500N;然后进行超声波处理。该表面加工工艺通过喷丸、机械滚压、超声波处理三种工艺相结合对辊套进行表面处理,处理工艺复杂,且对辊套的表面强化效果仍有待提升。技术实现要素:本发明的目的在于提供一种辊套的表面强化方法,以解决现有方法对辊套的表面强化效果较差的问题。本发明的第二个目的在于提供上述表面强化方法得到的辊套,以解决现有辊套的表面硬度较低的问题。为实现上述目的,本发明的辊套的表面强化方法的技术方案是:一种辊套的表面强化方法,包括以下步骤:1)使用一外径小于辊套内径的芯轴穿过辊套内腔,将辊套悬挂在芯轴上;2)在辊套上方设置一轴线与芯轴轴线平行的辊轮,辊轮的轴向长度小于辊套的轴向长度,利用辊轮将辊套压紧在芯轴上并由辊轮的转动带动辊套转动,以此实现在辊套表面上以辊轮的轴向长度为碾压范围的局部碾压;3)对辊套表面进行局部碾压直至辊套表面全部被碾压。本发明提供的辊套的表面强化方法,利用内侧芯轴对辊套进行支撑悬挂,依靠表面辊轮将辊套竖直压紧在芯轴上,通过辊轮的局部小范围碾压有序改变辊套表层组织,可方便利用常规压机实现对辊套表面的大作用力碾压(实现局部小范围、大变形量的强化),因而能够显著强化对表层金属晶粒的细化和致密化效果,从而在表面产生细晶强化作用,形成优质表面硬化层,提高辊套的表面强化效果。芯轴与辊套的相对尺寸可在一定程度上影响辊轮对辊套表面施加的碾压力,优选的,步骤1)中,所述芯轴的外径、辊套内径的比值为1:3-1:8。在该优选比例下,可方便辊轮对辊套表面施加较大的碾压力并兼顾对辊套支撑悬挂的稳定性。为进一步提高局部碾压过程的均匀性,优选的,步骤2)中,所述辊轮的外径与辊套的外径的比值为1:2.5-1:20。从兼顾碾压过程的均匀性和方便施加较大的碾压力方面综合考虑,优选的,步骤2)中,所述辊轮的轴向长度与辊套的轴向长度之比为1:10-1:120。为进一步优化对辊套表层(1-10mm)金属晶粒的细化和致密化程度,优选的,步骤2)中,辊轮对辊套施加的压力为50-200MPa。该压力表示的是辊轮作用在辊套上的单位面积的力(N/m2),在这样一个力的作用下可以充分保证辊套表面组织的晶粒细小强化效果。为进一步促进表面强化过程的均匀、高效进行,优选的,步骤2)中,所述辊轮的转动速率为10-120r/min。为进一步改善对辊套表面的细晶强化效果,优选的,所述辊套的材质为合金钢或铜合金。合金钢的型号如为32Cr3Mo1V、20Cr3MoWV、35CrMnMo、45MnMoWV等,铜合金如Cu-Be系、Cu-Cr系等铜合金。本发明的辊套所采用的技术方案是:一种采用上述辊套的表面强化方法制备得到的辊套。本发明提供的辊套,通过局部碾压方式制备优质表面硬化层,该表面硬化层的表面硬度高,可以起到明显的耐磨损作用,提高辊套的抗热疲劳和热冲击性能,从而延长辊套的使用寿命,减少更换频次。附图说明图1为现有技术的连续铸轧工艺原理图;图2为本发明的辊套的表面强化方法的工作原理图;图3为图2的侧向视图;图4为本发明辊套的表面强化方法实施例1所得辊套的表层晶粒和内部晶粒结构示意图;图中,1-熔炼炉,2-金属熔液,3-前箱,4-铸轧辊,5-板坯,6-芯轴,7-辊套,8-辊轮,9-表层晶粒,10-内部晶粒。具体实施方式下面结合附图对本发明的实施方式作进一步说明。本发明的辊套的表面强化方法的实施例1,以常用的32Cr3Mo1V钢辊套材料为例,工作原理图如图2和图3所示,辊套外径为1000mm,单边壁厚为100mm,长度为1200mm,具体表面强化方法采用以下步骤:1)使用一外径小于辊套内径的芯轴6穿过辊套内腔,以将辊套7悬挂在芯轴6上;芯轴6的外径为160mm,辊套7的内径为800mm。2)在辊套7上方设置一轴线与芯轴轴线平行的辊轮8,辊轮轴线与芯轴轴线在同一竖直平面内,辊轮8的轴向长度小于辊套7的轴向长度,利用辊轮8对辊套表面施加径向压力,使辊轮8转动并带动辊套7转动,以此在辊套表面实现以辊轮8的轴向长度为碾压范围的局部碾压;辊轮8的直径为200mm,轴向长度为100mm,施加的径向压力大小为200MPa,辊轮8的转动速率为60r/min。控制辊轮8对辊套表面局部碾压500周次(即辊套的转动周次)后,完成辊套表面上相应部位的表面强化,调整辊轮8沿其轴线方向移动,采用相同局部碾压方式对辊套表面未碾压区域进行表面处理,直至辊套表面全部被碾压。利用实施例的方法,辊套表面在内侧芯轴的固定和表面辊轮的碾压作用下,对辊套表面的细晶强化效果如图4所示,表层晶粒9(表层厚度一般为1-10mm)相对于内部晶粒10得到细化和致密化,从而在表面产生细晶强化作用,该表面硬化层可以起到明显的耐磨损作用,延长辊套的使用寿命,减少更换频次。本发明的辊套的表面强化方法的实施例2,针对的辊套规格、材质与表面强化方法实施例1相同,区别仅在于,辊轮的直径为50mm,轴向长度为20mm,施加的径向压力大小为50MPa,辊轮的转动速率为120r/min。本发明的辊套的表面强化方法的实施例3,针对的辊套规格、材质与表面强化方法实施例1相同,区别仅在于,辊轮的直径为130mm,轴向长度为60mm,施加的径向压力大小为130MPa,辊轮的转动速率为10r/min。本发明的辊套的实施例1-3,分别对应于以上辊套的表面强化方法实施例1-3所得辊套。试验例本试验例考察各表面强化方法实施例所得辊套的表面强化效果,结果如表1所示。其中,晶粒度的检测方法为统计单位面积内的晶粒数目或晶粒的平均线长度(或直径),并与标准晶粒度分级表进行对比,标准晶粒度共分12级,1~4级为粗晶粒,5~6级为中等晶粒,7~8级为细晶粒,9~12级为超细晶粒。表面平均硬度的检测方法为合金钢辊套采用洛氏硬度计进行多个点的测量,铜合金辊套采用布氏或维氏硬度计进行多个点的测量,然后取平均值。表1各辊套的表面强化效果项目晶粒度表面平均硬度400℃高温抗拉强度实施例17级35HRC565MPa实施例29级45HRC620MPa实施例38级38HRC582MPa原辊套5-6级30HRC510MPa由表1的试验结果可知,实施例的方法具有良好的细晶强化作用,晶粒度可以达到7-9级,表面平均硬度达到35-45HRC,400℃高温抗拉强度达到560-650MPa。该表面硬化层可以起到明显的耐磨损作用和抗热循环疲劳作用,提高辊套的高温强度和抗热疲劳性能,从而延长辊套的使用寿命,减少更换频次。当前第1页1 2 3