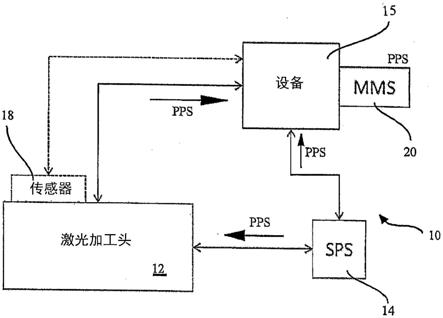
1.本发明涉及一种用于监测工件的借助高能加工射束、尤其激光射束的加工过程的方法,还涉及一种相应的设备和一种具有该设备的加工系统。
背景技术:2.关于这种加工过程的已知示例是激光焊接过程或激光深层焊接过程,其中,激光射束在工件表面上运动。为了控制加工过程,可以将(例如光学相干断层扫描仪的)测量光束指向工件表面。可以通过传感器检测由工件表面反射的光,从而能够连续地控制焊接结果的质量。
3.以这种方式尤其可以表示工件的表面轮廓或蒸汽细长孔洞(dampfkapillare)的深度,蒸汽细长孔洞也称为“keyhole,匙孔”,并且被液态熔体包围。其深度与焊缝深度或焊入深度有关,因此可以考虑用来控制加工过程。对于该测量可用的光学方法例如是光学相干断层扫描(oct)。光学相干断层扫描可以在微米范围内检测沿测量射束轴线的高度差。为此,产生测量光并将其分为测量射束和参考射束。探测测量射束在工件表面上反射的光与参考射束的重叠,以便获得所需的高度信息。这种方法例如在de 10 2015 012 565 b3中描述。
4.为了正确地测量加工结果,关键的是合适地选择测量光束照射到工件表面的测量位置,例如,将测量位置定向到工件表面上的以下地点,在该地点由于吸收加工射束的功率而瞬时地对工件发生所期望的修改,即进行瞬时的加工。在激光焊接中,该加工位置就是蒸汽细长孔洞的位置。
5.如果加工射束相对于工件是静态的,即加工射束相对于工件不发生运动,则加工位置与加工射束在工件表面上的照射点同心,或者与加工射束达到最大功率密度的位置同心。该位置也可以称为“工具中心点(tool center point)”,tcp。然而,如果加工射束和工件相对运动,对于过程观测的最佳工作点可能与该静态加工位置或者说静态tcp不完全相同。对于过程观测的最佳工作点可称为动态加工位置或者说动态tcp,其可能布置在照射点的尾迹中,即沿加工射束的路径发生偏移。例如,蒸汽细长孔洞在激光焊接过程中以小的延迟形成并且形成在如下位置中:该位置在照射点的尾迹中偏移。
6.相对于静态加工位置的动态加工位置,例如蒸汽细长孔洞的位置,可以取决于激光功率、工件材料、工件和加工射束之间的进给运动的速度矢量的方向和量值。然而,在加工过程期间,速度矢量、激光功率或其他参数可能会发生变化。为了正确地监测加工过程,关键的是确定当前动态加工位置,以便能够确定过程观测的最佳观测点。只有这样,才能将光学测量光束定向到该最佳观测位置上,以便例如能够借助oct确定蒸汽细长孔洞的正确深度。
7.确定该偏移的一种可能性是,借助相关的加工系统在加工过程期间确定动态加工位置,在加工系统上设置所需的过程参数,例如加工射束的进给方向、进给速度和功率等。但在该过程中加工的工件通常必须作为废料丢弃。尤其在迄今为止已知的确定动态加工位
置的方法中,通常假设在加工过程中该动态位置不发生变化、或仅以已知方式周期性地变化。此外,如果对动态加工位置有影响的过程参数发生变化,则必须重新执行测量过程。
技术实现要素:8.因此,本发明的任务在于,说明用于监测加工过程的一种方法和一种设备,该方法和设备使得能够以简单快速的方式正确地求取当前的加工位置并且因此正确地定向测量位置。尤其也可以针对不存在之前的具体测量数据的过程参数确定动态加工位置。
9.通过根据独立权利要求的一种方法和一种设备来解决该任务。本发明的有利构型和扩展方案在从属权利要求中描述。
10.根据本公开的一个方面,用于监测工件上的激光加工过程的设备包括计算单元和观测单元,观测单元设置为用于在测量位置处确定激光加工过程的至少一个监测参数。在此,监测参数可以包括适合于监测相应加工过程的参数,例如激光焊接过程中蒸汽细长孔洞的深度。计算单元设置为用于确定相对于激光射束的照射点的当前加工位置,尤其当前动态加工位置。在激光焊接过程中,当前的加工位置可以对应于蒸汽细长孔洞的位置。动态加工位置可以表示以下加工位置:该加工位置相对于照射点的位置或该加工位置关于照射点的偏移是可变的,例如取决于当前的过程参数。为了确定当前的加工位置,计算单元使用激光加工过程的过程参数集以及模型,该模型基于至少一个预给定的比较参数集和对应于该比较参数集的比较加工位置。
11.在此,计算单元和观测单元可以构造成分开的单元,也可以集成在一个单元中。计算单元尤其可以集成在观测单元中。观测单元例如可以包括具有光学相干断层仪的测量设备,该测量设备也包括计算单元。
12.过程参数集可以包括影响加工位置的至少一个过程参数,并且所述至少一个过程参数的值与比较参数集的相应比较参数的值不同。换句话说,对于过程参数集不存在之前就确定了的测量结果。过程参数集和/或比较参数集可以包括以下参数中的至少一个参数:激光射束相对于工件的进给运动的速度矢量、进给速度的量值、进给运动的方向、激光射束的功率以及工件的一个或多个材料参数。可以预给定多个比较参数集,所述多个比较参数集在至少一个参数方面不同。
13.监测参数可以包括蒸汽细长孔洞的深度、在动态加工位置处到工件的间距或地形(topographie)、温度和/或在动态加工位置处反射的光的波长。
14.观测单元可以包括光学相干断层仪,并且设置为用于将光学测量光束指向动态加工位置。观测单元还可以包括偏转单元,例如扫描仪单元或类似物,该偏转单元设置为用于将光学测量光束定向到所期望的位置上,即当前加工位置上。
15.至少一个预给定的比较加工位置可以包括至少一个静态加工位置和至少一个动态加工位置,所述至少一个静态加工位置具有激光射束相对于工件的等于零的进给速度,所述至少一个动态加工位置具有大于零的进给速度。所述至少一个预给定的比较加工位置可以包括具有量值相等且彼此反向的进给运动速度矢量的两个动态加工位置,和/或所述至少一个预给定的比较加工位置包括具有彼此垂直的进给运动速度矢量的两个动态加工位置。
16.设备还可以包括至少一个传感器,该传感器设置为用于求取加工过程的过程参数
集中的至少一个当前过程参数。设备可以包括接口,传感器通过该接口与计算单元连接,以便将加工过程的求取出的当前过程参数传送给计算单元。
17.根据另一方面,激光加工系统包括激光加工头和根据以上示例之一所述的设备,所述激光加工头设置为用于将激光射束指向工件。激光加工系统可以包括接口,激光加工系统通过该接口与计算单元连接,以便将加工过程的至少一个当前过程参数传送给计算单元。激光加工系统可以包括控制装置,该控制装置设置为用于预给定针对加工过程的至少一个当前过程参数,并且用于基于该当前过程参数来控制激光加工系统。激光加工系统还可以包括接口,控制装置通过该接口与计算单元连接,以便将当前过程参数传送给计算单元。激光加工系统可以包括人机接口,该人机接口设置为用于输入和/或选择加工过程的至少一个过程参数并且将相同的参数传送给计算单元。
18.根据另一方面,用于监测工件上的激光加工过程的方法包括以下步骤:借助模型来针对激光加工过程的过程参数集确定相对于激光射束的照射点的当前加工位置,尤其当前动态加工位置,该模型基于至少一个预给定的比较参数集和对应于该比较参数集的比较加工位置,并且确定激光加工过程在该动态加工位置处的至少一个监测参数。
19.可以在设置过程中针对每个预给定的比较参数集确定相对应的比较加工位置。在设置过程中可以求取多个比较加工位置,所述多个比较加工位置包括至少一个静态加工位置和至少一个动态加工位置:所述至少一个静态加工位置具有激光射束相对于工件的等于零的进给速度,所述至少一个动态加工位置具有大于零的进给速度。在求取动态加工位置期间,相应的进给速度可以是恒定的。由两个动态加工位置求取所述静态加工位置,所述两个动态加工位置的进给运动具有量值相等且彼此反向的速度矢量。
20.在一种实施方式中,可以在加工过程之前进行设置过程,在该设置过程中,求取相对于加工射束的照射点的至少一个比较加工位置。然而,也可以预给定或例如存储至少一个比较加工位置。所述比较加工位置可以对应于如下比较参数集:该比较参数集包含若干个过程参数,例如加工射束的激光功率,加工射束与工件之间的相对运动的方向和速度。因此,能够将相应的比较加工位置求取作为比较参数集的函数。基于所求取的比较加工位置和分别与其对应的过程参数,能够针对后续加工过程的特定过程参数集、即针对没有进行过测量的那些过程参数集计算其他加工位置。然后,可以在加工过程期间将测量光束的测量位置定向到计算出的加工位置上。
21.本发明基于以下假设,即确定的加工位置基本上可以表示为过程参数的函数。例如,匙孔相对于加工射束的瞬间照射点的动态偏移的大小取决于工件与加工射束之间的相对速度、加工射束的功率以及可能的其他参数。所述函数,即过程参数与由此得出的相应加工位置之间的关系,能够以数学模型表示,该数学模型能够用于计算加工位置。
22.因此,借助这种模型可以由相对较少数量的测量数据或比较数据来生成大数量的加工位置。如果过程参数发生变化,不一样必须像通常情况下那样重新测量动态加工位置。而是可以针对具有改变的参数的加工过程来计算这些加工位置。
附图说明
23.以下参考附图更详细地阐述本发明的优选实施例。
24.图1示出根据本公开的实施方式的工件(上方)的示意性截面图,以示出在激光焊
接时的蒸汽细长孔洞和测量光束;
25.图2a至2c示出用于阐述根据按照本发明的方法的一种优选实施方式的设置过程的示意图;
26.图3示出用于阐述根据按照本发明的方法的一种优选实施方式的确定当前加工位置的示意图;
27.图4示出根据本发明的一种优选实施方式的设备的示意图;
28.图5示出根据本发明的一种优选实施方式的激光加工系统的示意图。
具体实施方式
29.图1示出根据本公开的实施方式的工件的示意性截面图,以示出在激光焊接时的蒸汽细长孔洞和测量光束。
30.如图1所示,在激光深层焊接过程中,在焊接过程期间沿激光射束1的射束轴线产生蒸汽细长孔洞kh,也称匙孔,该蒸汽细长孔洞被液态熔体2包围。蒸汽细长孔洞的深度td与焊缝深度或焊入深度te有关,因此可以作为用于监测加工过程的监测参数。从进给方向看,固化的熔体4位于液态熔体2后面。
31.为了在焊接过程期间确定焊入深度或者说蒸汽细长孔洞kh的深度,可以将光学相干断层仪的测量光束3平行于激光射束1地或与激光射束同轴地定向到蒸汽细长孔洞kh中。入射光照射到蒸汽细长孔洞kh的底部或者说端部上,该入射光在那里被部分地反射并返回到光学相干断层仪中,借助所述光学相干断层仪能够以更高的精度测量蒸汽细长孔洞kh的深度td。
32.图2a是在工件的借助加工射束的加工过程中期间的几何关系示意图。在本实施例中,加工过程是在工件上借助激光射束1的激光焊接过程。在此,射束轴线垂直于图像平面,而图像平面本身与工件表面wb的平面重合。因此,所示的空间方向x和y在工件表面上相互垂直地延伸,而激光射束的射束轴线与之垂直地伸展。
33.通过激光射束在工件表面wb中产生蒸汽细长孔洞kh,该蒸汽细长孔洞被熔体包围。蒸汽细长孔洞也叫“匙孔”,其从工件表面延伸直到进入工件的确定深度td。所产生的蒸汽细长孔洞的深度对激光焊接过程的结果至关重要。为此,在加工过程期间可以通过用于监测加工过程的观测单元17确定蒸汽细长孔洞的深度作为监测参数。观测单元17例如可以包括光学相干断层仪,并且设置为用于将测量光束3指向工件表面上的测量位置。可以通过观测单元17检测测量光束从工件表面反射的光线。由此,又可以求取在测量位置处到工件表面的间距。
34.根据本实施方式形成蒸汽细长孔洞kh的位置是工件表面的这些位置:在所述位置处,由于吸收激光射束的功率而瞬时地发生对工件的所期望的修改。在下文中将这些位置称为加工位置tcp。因此,用于确定蒸汽细长孔洞深度的最佳测量位置是当前的加工位置。
35.图2a图解出激光射束1相对于工件wb表面不运动的情况,也就是说,激光射束静态地位于工件表面上并以照射点ap落到工件表面上。该照射点ap可以看作是一个坐标系的原点,空间方向x和y的轴线在该照射点处相交。由于激光射束相对于工件表面的静态位置,照射点ap与加工位置tcp、即静态加工位置tcps重合。因此,蒸汽细长孔洞也构造在该点处。
36.图2b示出如下情况:激光射束与工件表面以具有速度矢量v1的进给速度相对于彼
此运动。由于该运动,加工位置tcp不再与激光射束的瞬间照射点ap重合,而是位于照射点ap的尾迹中。在这种情况下,将加工位置称为动态加工位置tcp
i
。因此,在照射点ap与加工位置tcp
i
之间产生偏移。这是因为:在激光焊接中形成的蒸汽细长孔洞可能以低的延迟在工件表面上形成,而激光射束的照射点ap已经在工件表面上进一步移动了。
37.为了正确地监测加工过程必要的是,观测单元的测量位置(在该测量位置处确定监测参数)与当前加工位置tcp尽可能恰好一致。因此,必须尽可能准确地确定激光射束的照射点ap与加工位置tcp之间的偏移或者说当前动态加工位置tcp
i
相对于照射点ap的偏移。
38.在根据本发明的方法中,将观测单元的测量位置定向到之前已计算出的当前加工位置上,所述当前加工位置取决于加工过程的过程参数,例如激光射束相对于工件的进给运动的速度矢量的量值和方向、激光功率以及可能的其他过程参数。这意味着,能够基于瞬时的过程参数来预测当前加工位置tcp,然后相应地定向观测单元的测量位置。
39.为了可以基于加工过程的过程参数来执行对当前动态加工位置的计算,可以在加工过程之前执行设置过程,在该设置过程中尤其涉及对工件的测试加工。在该设置过程中,根据所使用的比较参数来求取相对于激光射束的照射点ap的至少一个比较加工位置。针对多个比较参数集pps
n
分别确定一个对应的比较加工位置tcp
n
,所述多个比较参数集分别包含对加工位置产生影响的若干个过程参数。比较参数集尤其可以包括速度矢量和激光射束的功率p,所述速度矢量说明激光射束相对于工件的进给运动的量值和方向。比较参数集还可以包含其他过程参数,例如工件的材料或者说材料参数。
40.在该方法的一种实施方式中,首先对于激光功率p0测量在工件与激光射束之间没有相对运动情况下的静态加工位置tcp
s
,如图2a示出的那样。接着,对于激光功率p0和大于零的进给速度v1测量至少一个动态加工位置tcp
d1
(图2b)。在此,通过速度矢量来描述进给速度v1的方向和量值。优选地,使矢量在确定加工位置tcp d1
期间保持恒定。
41.静态加工位置tcp
s
和动态加工位置tcp
d1
可以分别表示为其过程参数集pps
s
和pps
d1
的函数。可以基于设置过程期间的测量推导出模型(或者说规律性),该模型允许针对没有进行过测量的过程参数(即该过程参数不直接对应于任何比较参数集)计算并因此预测动态加工位置tcp
i
。借助该模型和加工过程的过程参数,可以确定相应的当前加工位置tcp
i
。
42.为了确定静态加工位置tcp
s
,也可以考虑使用两个动态加工位置tcp
d1
和tcp
‑
d1
,它们的参数集pps
d1
和pps
‑
d1
具有带有相同量值但相反地定向的进给速度矢量,即所述进给速度矢量的方向相对于彼此旋转180
°
。换句话说,可以由具有两个相反速度矢量和的两个动态加工位置tcp
d1
、
‑
tcp
d1
更准确地确定静态加工位置tcp
s
,例如将所述静态加工位置确定为动态加工位置tcp
d1
、
‑
tcp
d1
的空间平均值。
43.附加地或替代地,在设置过程中求取的比较加工位置tcp
n
可以包括两个动态加工位置tcp
d1
、tcp
d2
,它们的进给速度矢量和相互垂直,其中,这两个速度矢量都可以具有垂直于激光射束轴线的分量。因此,除了动态加工位置tcp
d1
之外,还可以针对第二过程参数集pps
d2
测量第二动态加工位置tcp
d2
,该第二过程参数集具有激光功率p0和具有速度矢量的第二进给速度v2。优选地,速度矢量和相互垂直,并且垂直于加工射束的轴线。
44.为了提高预测或者说求取未来加工过程的当前动态tcp
i
的准确度,可以针对具有不同激光功率p
n
和/或不同速度矢量的其他pps
n
重复该过程。
45.图2b示出以下情况:其中,激光射束相对于工件的进给运动的速度矢量沿水平x轴向右定向,相应的动态加工位置tcp
d1
相对于激光射束的瞬时照射位置ap沿x轴向左偏移,而2c示出另一种情况:其中,速度矢量沿y轴向下、即垂直于图2b的矢量地定向,相应的动态加工位置tcp
d2
相对于瞬时照射位置ap沿y轴向上偏移。
46.以这种方式,比较加工位置tcp
n
和相应的比较参数集pps
n
之间的如此确定的关系可以用于创建模型,该关系包括至少一个静态加工位置tcp
s
和/或至少一个动态加工位置tcp
dn
,该模型允许预测或者说计算针对任意过程参数(例如不同的速度矢量或激光功率)的当前动态tcp
i
。在一种实施方式中,该模型可以根据加工过程的当前过程参数集pps
i
计算当前动态加工位置tcp
i
,而不必事先测量针对该过程参数集pps的动态tcp,例如通过插值或根据机器学习模型进行计算,其中,在神经网络中计算tcp
i
。
47.在图3中示出在激光射束相对于工件的进给运动具有速度矢量的情况下由计算单元计算出的当前动态加工位置tcp
i
,所述当前动态加工位置是基于所求取的加工位置tcp
n
和对应于该加工位置的过程参数集pps
n
计算出的,例如基于比较加工位置tcp
d1
、tcp
d2
和/或tcp
s
。在加工过程中,计算出的加工位置tcp
i
可以用于将观测单元17的测量位置定向到该计算出的加工位置上。
48.例如,对于用于监测激光焊接过程或激光深层焊接过程的方法,观测单元17可以包括光学相干断层仪,以便借助光学相干断层仪(oct,optical coherence tomography)来确定蒸汽细长孔洞或者说匙孔kh的当前深度。为了能够正确地确定匙孔深度,测量光束3必须照射到当前加工位置tcp
i
上并因此照射到蒸汽细长孔洞kh中。为此,当前加工位置tcp
i
必须是已知的,以便能够相应地定向测量位置,即测量光束的位置。如果动态tcp
i
的位置在激光加工过程期间发生变化,例如由于激光射束与工件之间的进给运动方向发生变化,则可以通过模型使用当前的进给速度矢量来预测新的动态加工位置tcp
i
。也就是说,能够基于预给定的比较加工位置tcp
n
、针对所执行的加工过程的目前过程参数集pps
i
求取出当前动态加工位置tcpi,所述预给定的比较加工位置分别对应于比较参数集pps
n
并且例如之前在设置过程中就已求取了。例如,能够基于激光射束与工件之间的当前进给运动以及存在的激光功率预测出相应的动态加工位置tcp
i
。结合观测单元的定位单元、例如用于测量光束的偏转单元或扫描单元,该设备能够实时地校正测量位置或者说测量光束的位置,以便测量出正确的匙孔深度。
49.图4示意性地示出用于监测加工过程的设备15的一种实施方式。该设备包括计算单元16,该计算单元针对激光加工过程的过程参数集pps
i
、根据模型来计算相对于激光射束1的照射点ap的当前加工位置tcp
i
,并将其作为测量位置传输到观测单元17中,该设备还包括观测单元17,其用于求取测量位置处的至少一个监测参数,例如间距。计算单元16和观测单元17可以以无线或有线连接的方式耦合,以便相互交换数据。计算单元16可以设置为直接与相应的机器或者说相应的加工系统连接。当然,计算单元16和观测单元17可以共同构造为一个单元,或者计算单元16可以构造为集成在观测单元17中。
50.计算单元16设置为用于基于过程参数集pps
i
计算当前加工位置tcp
i
,所述当前加
工位置又被输出到观测设备17中。计算出的加工位置tcp
i
用于将观测单元17的例如测量光束的测量位置定向到计算出的加工位置tcp
i
上。在激光焊接设备的情况下,这可能对应于所产生的蒸汽细长孔洞的位置,所述蒸汽细长孔洞在加工过程期间在工件表面中形成。
51.计算单元16借助模型、基于以下内容来计算当前加工位置tcp
i
:加工过程的相应的过程参数集pps
i
、预给定的比较加工位置tcp
n
和对应于所述比较加工位置的比较参数集pps
n
。模型可以表示出相应的加工位置tcp
i
与加工参数集pps
i
的相关性或关系。该模型可以存储在计算单元16中,并可作为计算当前加工位置tcp
i
的基础。
52.图5示出激光加工系统10,其包括激光加工头12和设备15。此外,激光加工系统10可以包括sps控制装置14,该sps控制装置设置为用于将当前过程参数集pps
i
输出到激光加工头12中,并以这种方式控制加工过程,即尤其控制激光射束与工件之间的相对进给运动的量值和方向、激光射束的功率等。过程参数集pps
i
也可以被sps控制装置14通过相应的接口输出到计算单元16中。替代地,计算单元16可以直接从激光加工头12接收过程参数集pps
i
。如此,可以将所预测的当前加工位置tcp
i
直接反馈回(zur
ü
ckgesteuert)到过程中,从而提高过程质量。
53.计算单元16可以与人机接口20连接,该人机接口设置为用于输入和/或选择加工过程的过程参数集pps
i
。例如,该人机接口20可以包括图形用户界面。应当理解,也可以设置其他类型的输入接口。
54.优选地,计算单元16在考虑当前过程设置的情况下,即基于当前过程参数集pps
i
地计算当前加工位置tcp
i
。替代地或附加地,计算单元16可以设置为用于基于预给定的过程参数集来计算当前加工位置tcp
i
,所述预给定的过程参数集是针对之前所定义的一个子过程的过程参数集。这使得在没有当前过程参数集的情况下也能够计算当前加工位置tcp
i
。例如,可以针对加工过程的不同子过程选择不同的过程参数集。
55.此外,激光加工头12和/或设备15可以配备有传感器18,所述传感器例如允许测量激光射束与工件之间的当前进给速度及其方向,和/或测量其他参数,例如当前激光功率、温度等。传感器18可以包括固定在激光加工头12的轴上的编码器。可以将测量值作为关于加工过程的过程参数集的当前参数传送给计算单元16。因此,也可以基于由传感器18传送的过程参数集pps
i
来执行对当前加工位置tcpi的预测。
56.以这种方式可以根据加工过程的过程参数集精确地实时确定当前加工位置或者说瞬时加工位置(观测装置的测量位置定向到该加工位置上),并且因此可以连续地监测加工过程。此外,描述过程参数集pps
n
与加工位置tcp
n
之间关系的模型在结构相同的激光加工系统中能够被传输到“数字孪生”上,而不必重新确定该关系。