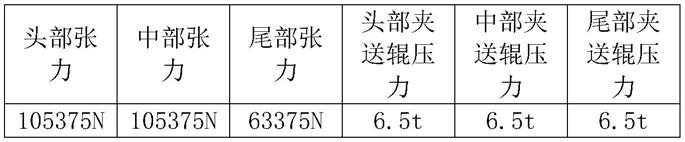
一种
ω
(c)
≥
0.45%的中高碳钢卷取卷形控制方法
技术领域
1.本发明涉及一种控制方法,具体涉及一种ω(c)≥0.45%的中高碳钢卷取卷形控制方法,属于热轧生产技术领域。
背景技术:2.ω(c)≥0.45%的中高碳钢,由于其钢种特性,钢卷生产完成必须及时卸出不得在卷取机内逗留,杜绝卷取机冷却水对其进行喷淋,在下线90分钟通过卷取运输链运输至缓冷墙区域,精整必须在90分钟内进入缓冷墙进行缓冷,所以该钢种对卷形质量要求较高,若一旦产生卷形质量问题造成钢卷在卷取机内滞留或由于卷形质量造成库区无法吊卷,钢卷无法及时进入缓冷墙,会造成钢卷开裂甚至报废等严重问题。
3.但在实际生产过程中该类钢种出现较为严重的扁卷问题,主要是钢卷层与层之间在卷取完成后出现了缝隙,造成缝隙的原因是该钢种在卷取及轧后冷却的过程中发生奥氏体向珠光体转变,而在这一过程中会出现体积膨胀的现象。与普通碳素结构钢(中低碳)相比,高碳钢由于碳含量较高,体积膨胀的较大,以其他钢厂为40mn做的相变膨胀曲线上计算得出的膨胀率为 0.443%,而由此推算下,65mn的膨胀率将会更大,扁卷会更加严重。因此需要采取大张力卷取,带钢在精轧抛钢后,卷取需要较大夹送辊压力才能维持带钢尾部的后张力,但较大的夹送辊压力会造成尾部卷形较为严重的溢出边和错层。
4.初步检索后,中国专利cn 104278201 b《防止热轧高碳钢扁卷的方法》仅针对不同卷取温度下卷取张力进行了相关设定,但对于大张力卷取之下带钢尾部卷形的控制并无说明,也没有相关的启示和介绍,因此,迫切的需要一种新的方案解决上述技术问题。
技术实现要素:5.本发明正是针对现有技术中存在的问题,提供一种ω(c)≥0.45%的中高碳钢卷取卷形控制方法,该方法主要解决该类钢种在卷取完成有由于轧后相变引起的扁卷问题,以及为解决轧后相变扁卷而进行大张力卷取后,卷取尾部卷形较为严重的溢出边和错层问题,大大降低了中高碳钢卷形返修的百分比。
6.为了实现上述目的,本发明的技术方案如下:一种ω(c)≥0.45%的中高碳钢卷取卷形控制方法,其特征在于,所述控制方法包括以下步骤:
7.1)卷取模型在接收到精轧模型传输的带钢钢种、ct温度、厚度、宽度,根据模型后台已设定的参数值,计算出此块带钢需要的卷取单位张力,以及相对应夹送辊压力值;
8.2)带钢头部夹送辊咬钢后,夹送辊按照之前设定的压力进入压力环控制,此时夹送辊无力矩输出;
9.3)带钢头部缠绕至卷筒,卷筒负载建立后(与精轧减张完成),卷筒按照前的下发的单位张力,转化为总张力,并根据总张力按照钢卷卷径计算出所需力矩,卷筒进入力矩环控制;
10.4)当带钢尾部在f7抛钢后,夹送辊开始输出反向力矩,卷筒与精轧之间建张逐步
开始转向卷筒与夹送辊建张;
11.5)f7抛钢后,卷取张力由卷筒与精轧减张,转向卷筒与夹送辊建张,直至带钢卷取完成。
12.作为本发明的一种改进,所述步骤1)具体操作如下:通过精轧模型传输的带钢信息在二级模型根据带钢钢种、温度、厚度和宽度逐一匹配,并按照公式计算单位张力=δs(带钢屈服应力)/206*9.8*(0.1+2/h)*张力修正系数(根据带钢钢种、温度、厚度和宽度进行匹配)出所需张力为30n/mm2~50n/mm2。
13.作为本发明的一种改进,所述步骤2)具体操作如下:带钢头部夹送辊咬钢后,将夹送辊压力分为头部、中部和尾部压力,其中头部压力设定为卷筒咬钢后3圈,随后进入中部压力控制,当f7抛钢后设定为尾部压力,由于夹送辊在f7抛钢无力矩输出,所以将带钢中部和尾部夹送辊压力设定一致,均为小压力设定。
14.作为本发明的一种改进,所述步骤3)具体操作如下:将整个卷取卷钢钢过程的总张力设定分为头部、中部和尾部张力,其中定义头部张力为卷筒咬钢后3圈,中部张力为带钢f7抛钢前,尾部张力为f7抛钢后。
15.作为本发明的一种改进,所述步骤4)具体操作如下:将带钢尾部张力进行减张控制,减张幅度在30%~60%之间。为保证张力转换平稳,当精轧f1抛钢后,夹送辊便开始逐步输出反向力矩,卷筒与精轧建立的张力开始逐步转向由夹送辊承担,需保证在f7抛钢前全部切换完成。具体转换过程为:在精轧第一个机架抛钢与第二个机架抛钢时间段转移所需张力的20%;在精轧第二个机架抛钢与第三个机架抛钢时间段转移所需张力的40%;在精轧第三个机架抛钢与第四个机架抛钢时间段转移所需张力的70%;在精轧第四个机架抛钢与第五个机架抛钢时间段转移所需张力的100%;实现在精轧机组第五个机架抛钢前,精轧末机架与卷筒之间建立的带钢张力逐步都转移到夹送辊与卷筒之间建立带钢张力。
16.作为本发明的一种改进,所述步骤5)具体操作如下:f7抛钢后,夹送辊进入尾部夹送辊压力控制,此时夹送辊尾部压力控制采取小压力控制,其具体压力设定为:夹送辊压力=张力 /(2*压力修正系数*1000),即以尽可能小的夹送辊压力来为带钢提供足够大后张力。
17.相对于现有技术,本发明的优点如下:本发明通过针对高碳钢带钢头部、中部高张力设定,尾部低张力设定,同时尾部减少夹送辊尾部压力设定,最大程度上保证了带钢卷形质量。由于热连轧产线都存在类似问题,因此本发明申请技术可在钢铁行业热连轧产线上投入使用,具有很大的应用推广价值,本发明采用以上技术方案后中高碳钢卷形返修情况由原来的10.97%下降为3.91%,同时薄规格高碳工具钢在返修过程中极易出现表面开裂、钢带断裂等附加风险和质量损失,需返修钢卷数量下降后,从根本上减少了此类安全风险和质量损失。
附图说明
18.图1 1780产线生产线布置图
具体实施方式:
19.为了加深对本发明的理解,下面结合附图对本实施例做详细的说明。
20.实施例1:参见图1,一种ω(c)≥0.45%的中高碳钢卷取卷形控制方法,所述控制方法包括以下步骤:
21.1)卷取模型在接收到精轧模型传输的带钢钢种、ct温度、厚度、宽度,根据模型后台已设定的参数值,计算出此块带钢需要的卷取单位张力,以及相对应夹送辊压力值;
22.2)带钢头部夹送辊咬钢后,夹送辊按照之前设定的压力进入压力环控制,此时夹送辊无力矩输出;
23.3)带钢头部缠绕至卷筒,卷筒负载建立后(与精轧减张完成),卷筒按照前的下发的单位张力,转化为总张力,并根据总张力按照钢卷卷径计算出所需力矩,卷筒进入力矩环控制;
24.4)当带钢尾部在f7抛钢后,夹送辊开始输出反向力矩,卷筒与精轧之间建张逐步开始转向卷筒与夹送辊建张;
25.5)f7抛钢后,卷取张力由卷筒与精轧减张,转向卷筒与夹送辊建张,直至带钢卷取完成。所述步骤1)具体操作如下:通过精轧模型传输的带钢信息在二级模型根据带钢钢种、温度、厚度和宽度逐一匹配,并按照公式计算按照公式单位张力=δs(带钢屈服应力)
26./206*9.8*(0.1+2/h)*张力修正系数(根据带钢钢种、温度、厚度和宽度进行匹配)计算出所需张力为30n/mm2~50n/mm2。
27.所述步骤2)具体操作如下:带钢头部夹送辊咬钢后,将夹送辊压力分为头部、中部和尾部压力,其中头部压力设定为卷筒咬钢后3圈,随后进入中部压力控制,当f7抛钢后设定为尾部压力,由于夹送辊在f7抛钢无力矩输出,所以将带钢中部和尾部夹送辊压力设定一致,均为小压力设定。
28.所述步骤3)具体操作如下:将整个卷取卷钢钢过程的总张力设定分为头部、中部和尾部张力,其中定义头部张力为卷筒咬钢后3圈,中部张力为带钢f7抛钢前,尾部张力为f7抛钢后。所述步骤4)具体操作如下:将带钢尾部张力进行减张控制,减张幅度在30%~60%之间。为保证张力转换平稳,当精轧f1抛钢后,夹送辊便开始逐步输出反向力矩,卷筒与精轧建立的张力开始逐步转向由夹送辊承担,需保证在f7抛钢前全部切换完成。具体转换过程为:在精轧第一个机架抛钢与第二个机架抛钢时间段转移所需张力的20%;在精轧第二个机架抛钢与第三个机架抛钢时间段转移所需张力的40%;在精轧第三个机架抛钢与第四个机架抛钢时间段转移所需张力的70%;在精轧第四个机架抛钢与第五个机架抛钢时间段转移所需张力的100%;实现在精轧机组第五个机架抛钢前,精轧末机架与卷筒之间建立的带钢张力逐步都转移到夹送辊与卷筒之间建立带钢张力。
29.所述步骤5)具体操作如下:f7抛钢后,夹送辊进入尾部夹送辊压力控制,此时夹送辊尾部压力控制采取小压力控制,其具体压力设定为:夹送辊压力=张力/(2*压力修正系数*1000),即以尽可能小的夹送辊压力来为带钢提供足够大后张力。
30.应用实施例1:一种ω(c)≥0.45%的中高碳钢卷取卷形控制方法,所述控制方法包括以下步骤:
31.以生产成品规格2.5*1250mm的65mn为例如下:
32.1.卷取模型在接收到精轧模型传输的带钢钢种65mn、ct温度610℃、厚度2.5mm、宽度 1250mm,模型根据后台已设定的相关参数值,计算出此块带钢头部、中部和尾部需要的卷取单位张力:
33.单位张力=δs(带钢屈服应力)/206*9.8*(0.1+2/h)*张力修正系数
34.=420mpa/206*9.8*(0.1+2/2.5mm)*2.35
35.=42.25n/mm236.张力=单位张力*宽度*厚度
37.=42.25n/mm2*1250mm*2.5mm
38.=105375n
39.带钢尾部张力=张力*60%
40.=105375n*60%
41.=63375n
42.夹送辊压力=张力/(2*0.8*1000)
43.=105375n/2*0.5*1000
44.=6.5t;
45.根据以上计算得出对应头部、中部和尾部张力,以及夹送辊头部、中部和尾部压力值;
[0046][0047]
2.带钢头部夹送辊咬钢后,夹送辊按照之前设定的压力进入头部及中部压力环控制(压力按照6.5t压力进行控制),此时夹送辊无力矩输出;
[0048]
3.带钢头部缠绕至卷筒,卷筒负载建立后(与精轧建张完成),卷筒按照前的下发的单位张力42.25n/mm2,转化为总张力105375n,并进入头部及中部张力控制;
[0049]
4.当带钢尾部在f1抛钢后,夹送辊开始逐步输出反向力矩,卷筒张力控制开始进入尾部张力控制,以最终减张至总张力的60%为目标,在带钢尾部依次经f1~f7轧机时逐步进行减张,试卷筒与精轧之间建张逐步开始转向卷筒与夹送辊建张,并在f7抛钢前减张至总张力的60%,减张至63375n;
[0050]
5.f7抛钢后,夹送辊进入尾部夹送辊压力控制,直至带钢卷取完成。
[0051]
相关参数及控制程序实现自动化后,当模型系统接收到相关带钢钢种、厚度、宽度、温度等信息后,模型相关参数进行自动计算,并下发至现场实现自动控制,无需操作人员手动干预,完全实现自动控制。
[0052]
需要说明的是上述实施例,并非用来限定本发明的保护范围,在上述技术方案的基础上所作出的等同变换或替代均落入本发明权利要求所保护的范围。