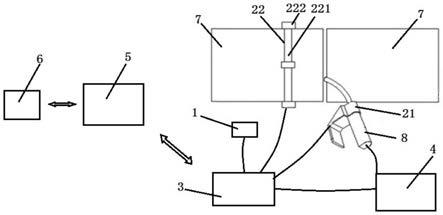
[0001]
本发明涉及焊接设备技术领域,尤其是涉及一种焊接数据智能采集监控系统。
背景技术:[0002]
在长输管道施工过程中,焊接设备的地理位置时常随着施工进程而不断改变,工程管理者难以及时、准确地掌握和有效管理焊接设备的工作情况。目前,在我国山区、丘陵及水网密集等特殊地带的油气管道施工中,对于管道的焊接方式仍然主要采用半自动焊接方式,此种焊接方式的施工质量很大程度上依赖于焊工的技术水平和责任心,而焊接过程缺少有效的监控手段。然而,近几年发生的管道环焊缝开裂事件,其主要原因是施工过程中焊接工艺执行不严格所致,而类似焊接道数、层数及焊接参数的异常变化所导致的焊缝力学性能不能够满足实际要求是无法通过无损检测所发现的,因此给焊接质量管控带来了诸多的不确定性。
[0003]
而目前在石化领域工程建设过程中,由于施工环境恶劣,工种危险系数高,致使施工单位面临巨大的管理困难。面对建设工地面积大、人员多、设备物资分散、管理作业流程琐碎等特点,采用传统的人工巡视、手工记录的工作方式,显然已无法满足大型项目管控的要求。因此需要一种高效、准确的施工操作管理系统以辅助进行规范化操作,从而利用信息化手段实现监管模式的创新,解决建设工程中出现的“监管力度不强,监管手段落后”的难题。
技术实现要素:[0004]
本技术方案要解决的技术问题是如何提供一种利用信息化手段以实现对焊接操作人员及焊接施工质量进行监控与管理的焊接数据智能采集监控系统。
[0005]
为了解决上述技术问题,本技术方案提供了一种焊接数据智能采集监控系统,其包括:操作信息录入装置、焊接层间温度及焊接位置采集装置、焊接数据采集装置、数据传输装置、云端服务器及监控终端;其中操作信息录入装置、焊接层间温度及焊接位置采集装置以及焊接数据采集装置均与数据传输装置电性连接;操作信息录入装置用以采集操作预置信息与待焊接管道的预热温度并传输至数据传输装置;焊接层间温度及焊接位置采集装置用以采集焊枪焊接时的焊接层间温度与焊接位置数据并传输至数据传输装置;焊接数据采集装置用以采集实时焊接数据并传输至数据传输装置;数据传输装置通过无线网络传输方式将操作预置信息、预热温度、焊接层间温度、焊接位置数据及实时焊接数据传输至云端服务器进行存储,并且云端服务器将预热温度、焊接层间温度、焊接位置数据及实时焊接数据与操作预置信息进行计算对比,以判定是否符合焊接工艺,如判定不符合焊接工艺则发出警示信息;监控终端通过无线网络传输方式与云端服务器电性连接,以获取焊接操作数据及警示信息。据此,通过焊接数据智能采集监控系统可在焊接施工前将操作人员信息、焊接工艺参数及焊接环境条件等信息通过无线网络传输至云端服务器进行存储,在焊接施工过程中可实时采集焊接操作数据并上传至云端服务器,由云端服务器据以计算判断焊接操
作数据是否符合焊接工艺要求,当不符合焊接工艺要求时,云端服务器可及时向现场管理者或质量监管人员等的监控终端发送警示信息,以辅助对焊接现场焊接质量的实时把控,确保焊接质量的稳定;另外,云端服务器还可对操作预置信息、实际焊接数据及是否符合焊接工艺要求等信息进行存储留档,以便后期对于焊接施工过程的查询与分析,对于完善焊接质量管理体系,提升焊接施工质量提供了详实的数据支持。
[0006]
作为本技术方案的另一种实施,焊接层间温度及焊接位置采集装置是由焊接层间温度采集装置与焊接位置采集装置构成;焊接层间温度采集装置装设于焊枪的手柄前部并包括:焊枪连接部、采集装置装设部、采集电路板及焊渣挡板部,其中焊枪连接部为横向截面为u形的半管体并结合于采集装置装设部的上端且用以套设固定于焊枪的手柄前部,采集装置装设部为上端厚度大于下端厚度的块状体且前侧面是面向焊枪的前端,采集装置装设部的后侧面开设有采集板安装室,采集板安装室朝前侧面开设有贯通采集板安装室与前侧面的数个温度传感器安装孔,温度传感器安装孔中装设有温度传感器,采集板安装室内装设采集电路板,温度传感器与采集电路板电性连接,采集电路板还具有三轴加速度传感器用以感测焊枪的转动角度,以使采集电路板根据转动角度启用数个温度传感器中的其中一个进行焊接层间温度的感测,采集电路板与数据传输装置电性连接,焊渣挡板部为片状体并结合于采集装置装设部的下端,用以防止焊渣溅射到操作人员的手部;而焊接位置采集装置是绕设固定于待焊接管道上临近焊接处的位置并包括:防火带、数个光敏传感器及两个卡扣,其中该数个光敏传感器彼此间隔而布设于防火带上,且各光敏传感器的光敏元件均朝向防火带的同一侧,各光敏传感器的缆线穿设于防火带内并于防火带上的一穿口穿出而电性连接数据传输装置,两个卡扣装设于防火带的两个端部,将防火带绕设于待焊接管道上临近焊接处的位置处,并使光敏元件朝向焊接处,通过两个卡扣的对合扣固而将焊接位置采集装置固定于待焊接管道上。据此,通过装设于焊枪的手柄前部的焊接层间温度采集装置可对焊接时的焊接层间温度进行实时采集,通过绕设固定于待焊接管道上的焊接位置采集装置可对焊接时的焊接位置数据进行实时采集。
[0007]
作为本技术方案的另一种实施,云端服务器存储焊接层间温度及数个光敏传感器感测的感光信号,并且云端服务器根据感光信号判断当数个光敏传感器为依序且全部感光时为完成一道焊接,云端服务器将完成一道焊接的次数进行累加以计算焊接道数,云端服务器将存储的焊接层间温度及计算的焊接道数与操作预置信息中预设的焊接层间温度及焊接道数进行比对,当判断存储的焊接层间温度与预设的焊接层间温度不同及/或计算的焊接道数与预设的焊接道数不同时则发出警示信息。
[0008]
作为本技术方案的另一种实施,焊接层间温度及焊接位置采集装置是装设于焊枪的手柄前部并包括:焊枪连接部、采集装置装设部、采集电路板及焊渣挡板部,其中焊枪连接部为横向截面为u形的半管体并结合于采集装置装设部的上端且用以套设固定于焊枪的手柄前部,采集装置装设部为上端厚度大于下端厚度的块状体且前侧面是面向焊枪的前端,采集装置装设部的后侧面开设有采集板安装室,采集板安装室朝前侧面开设有贯通采集板安装室与前侧面的数个温度传感器安装孔,温度传感器安装孔中装设有温度传感器,采集板安装室内装设采集电路板,温度传感器与采集电路板电性连接,采集电路板还具有三轴加速度传感器用以感测焊枪的转动角度及焊枪的移动轨迹,并且采集电路板根据转动角度启用数个温度传感器中的其中一个进行焊接层间温度的感测,采集电路板与数据传输
装置电性连接,焊渣挡板部为片状体并结合于采集装置装设部的下端,用以防止焊渣溅射到操作人员的手部。据此,通过焊接层间温度及焊接位置采集装置便可实现对于焊接层间温度与焊接位置数据的实时采集。
[0009]
作为本技术方案的另一种实施,云端服务器存储焊接层间温度及由三轴加速度传感器根据设定的频率采集的其x轴、y轴及z轴相对于三维笛卡尔坐标系的加速度,并由云端服务器计算焊接道数,焊接道数计算步骤为:
[0010]
计算加速度平均值:云端服务器将每次依序接收的10组x轴、y轴及z轴的加速度数据按照y轴的加速度由小到大的顺序重新排序为10组第一次排序后的加速度数据,然后依序计算相邻的2组加速度数据中y轴的加速度的差值的绝对值,之后按照差值的绝对值由小到大的顺序将产生每个差值的绝对值的2组加速度数据进行排序且将相同的加速度数据进行合并,以形成10组第二次排序后的加速度数据,取前5组第二次排序后的加速度数据并计算x轴、y轴及z轴的加速度平均值;
[0011]
计算y轴方向弧度值:由云端服务器根据每次计算得到的加速度平均值计算三轴加速度传感器的y轴与三维笛卡尔坐标系y轴之间的弧度值:其中,αy为y轴与三维笛卡尔坐标系y轴之间的弧度值,avx为x轴的加速度平均值,avy为y轴的加速度平均值,avz为z轴的加速度平均值;
[0012]
计算焊枪的移动轨迹坐标:由云端服务器根据每次计算得到的三轴加速度传感器的y轴与三维笛卡尔坐标系y轴之间的弧度值,计算焊枪相对于待焊接管道截面圆心的移动轨迹坐标:xwg=φp
×
cosαy,ywg=φp
×
sinαy,其中,xwg为焊枪相对于待焊接管道截面圆心处的x轴坐标值,ywg为焊枪相对于待焊接管道截面圆心处的y轴坐标值,φp为待焊接管道的半径;并建立焊枪移动轨迹坐标集合{xwg,ywg∣(xwg1,ywg1),(xwg2,ywg2)
…
(xwgn,ywgn)},n为计算(xwg,ywg)坐标的次序值;
[0013]
判断是否完成一道焊接:云端服务器根据操作预置信息中的包含焊道起始端与终止端的至少两个焊道坐标值{(x1,y1)
…
(xn,yn),n>=2}计算得到检测点坐标范围{(x1±
x1×
10%,y1±
y1×
10%)
…
(xn
±
xn
×
10%,yn
±
yn
×
10%),n>=2},然后判断当焊枪移动轨迹坐标集合中的部分坐标符合依次序出现在检测点坐标范围内时则为完成一道焊接;
[0014]
计算焊接道数:云端服务器将完成一道焊接的次数进行累加;
[0015]
云端服务器将存储的焊接层间温度及计算的焊接道数与操作预置信息中预设的焊接层间温度及焊接道数进行比对,当判断存储的焊接层间温度与预设的焊接层间温度不同及/或计算的焊接道数与预设的焊接道数不同时则发出警示信息。
[0016]
作为本技术方案的另一种实施,温度传感器安装孔的开设数量为四个,且四个温度传感器安装孔的分布呈十字形分布,以使四个温度传感器的测量范围包围但并不覆盖焊枪的焊枪嘴于焊接面焊接时的熔池,并使四个温度传感器的测量范围的边缘处彼此重合。以此,可使四个温度传感器不受焊枪握持角度和移动路线的影响,而确保总有一个温度传感器能够感测到熔池的焊接温度。
[0017]
作为本技术方案的另一种实施,由三轴加速度传感器根据设定的频率采集其x轴、y轴及z轴相对于三维笛卡尔坐标系的加速度,并由采集电路板根据加速度计算三轴加速度
传感器的x轴与三维笛卡尔坐标系x轴之间的角度值:θx=αx
×
180/π,其中,αx为x轴与三维笛卡尔坐标系x轴之间的弧度值,ax为x轴的加速度值,ay为y轴的加速度值,az为z轴的加速度值,θx为x轴相对于三维笛卡尔坐标系x轴之间的角度值,并于采集电路板设定与呈十字形分布的四个温度传感器相对应的第一角度变化范围、第二角度变化范围、第三角度变化范围及第四角度变化范围,当θx处于第一角度变化范围时,采集电路板启用呈十字形分布状下侧的温度传感器感测焊接层间温度,当θx处于第二角度变化范围时,采集电路板启用呈十字形分布状右侧的温度传感器感测焊接层间温度,当θx处于第三角度变化范围时,采集电路板启用呈十字形分布状左侧的温度传感器感测焊接层间温度,当θx处于第四角度变化范围时,采集电路板启用呈十字形分布状上侧的温度传感器感测焊接层间温度。
[0018]
作为本技术方案的另一种实施,操作预置信息包括:焊工信息、焊枪编号、焊口编号、预设的电流、预设的电压、预设的待焊接管道的预热温度、预设的焊接层间温度、预设的焊接道数、预设的送丝速度、预设的焊接速度;实时焊接数据包括:电流、电压。
[0019]
作为本技术方案的另一种实施,焊接数据采集装置包括:安装于焊接主机内部电路中的电流传感器与电压传感器;数据传输装置将电流传感器采集的电流与电压传感器采集的电压传输至云端服务器进行存储,并由云端服务器计算送丝速度v=k1i+k2li2,其中v为送丝速度,l为干伸长度,k1和k2为系数,i为电流传感器采集的电流;云端服务器根据首个光敏传感器及最后一个光敏传感器之间的弧长与完成一道焊接的时间计算焊接速度,或者根据焊枪移动轨迹坐标集合中的首个坐标及最后一个坐标之间的弧长与完成一道焊接的时间计算焊接速度。
[0020]
作为本技术方案的另一种实施,操作信息录入装置是由扫码枪及温度传感器构成。结合目前在施工现场对于操作信息如焊接人员身份信息、待焊接管道的管口信息、焊枪设备信息均广泛采用编码方式的应用(如条形码、二维码等),利用扫码枪可快速扫描上述操作信息,提高焊接施工的效率,另外还可减少由人工信息录入带来的信息录入错误及操作舞弊情况的发生。
附图说明
[0021]
图1为本发明焊接数据智能采集监控系统的第一具体实施例的示意图;
[0022]
图2为本发明焊接数据智能采集监控系统的第二具体实施例的示意图;
[0023]
图3为本发明中焊接层间温度采集装置套设于焊枪前部的示意图;
[0024]
图4为本发明中焊接层间温度采集装置的侧面剖视图;
[0025]
图5为本发明中的温度传感器感测范围的示意图。
[0026]
附图中的符号说明:
[0027]
1操作信息录入装置;2焊接层间温度及焊接位置采集装置;21焊接层间温度采集装置;211焊枪连接部;212采集装置装设部;2121采集板安装室;2122温度传感器安装孔;213焊渣挡板部;22焊接位置采集装置;221防火带;222光敏传感器;3数据传输装置;4焊接主机;5云端服务器;6监控终端;7待焊接管道;8焊枪;9测量范围;a熔池;α第一角度变化范围;β第二角度变化范围;ε第三角度变化范围;ω第四角度变化范围。
具体实施方式
[0028]
有关本发明的详细说明及技术内容,配合图式说明如下,然而所附图式仅提供参考与说明用,并非用来对本发明加以限制。
[0029]
目前,随着我国对油气行业地面工程建设质量要求的不断提升,工程全生命周期管理已成为必然趋势。本发明的焊接数据智能采集监控系统可以对手工焊、半自动焊接及全自动焊接参数进行实时采集与分析,以实现对焊接过程的实时跟踪,为早发现质量隐患,减少重大质量问题的出现,进一步提升油气管道质量管控能力提供管控手段的支持。并且可为油气田地面工程及长输管道工程建设建立准确、及时、全面的数据采集方案,所采集的数据经智能化处理,可为焊接的智能管理、施工过程的安全预警、质量提升提供强有力的保障。
[0030]
如图1所示,为本发明焊接数据智能采集监控系统的第一具体实施例,该焊接数据智能采集监控系统包括:操作信息录入装置1、焊接层间温度及焊接位置采集装置、焊接数据采集装置(图未标示)、数据传输装置3、云端服务器5及监控终端6;其中操作信息录入装置1、焊接层间温度及焊接位置采集装置以及焊接数据采集装置均与数据传输装置3电性连接;操作信息录入装置1用以采集操作预置信息与待焊接管道7的预热温度并传输至数据传输装置3;焊接层间温度及焊接位置采集装置用以采集焊枪8焊接时的焊接层间温度与焊接位置数据并传输至数据传输装置3;焊接数据采集装置用以采集实时焊接数据并传输至数据传输装置3;数据传输装置3通过无线网络传输方式将操作预置信息、预热温度、焊接层间温度、焊接位置数据及实时焊接数据传输至云端服务器5进行存储,并且云端服务器5将预热温度、焊接层间温度、焊接位置数据及实时焊接数据与操作预置信息进行计算对比,以判定是否符合焊接工艺,如判定不符合焊接工艺则发出警示信息;监控终端6通过无线网络传输方式与云端服务器5电性连接,以获取焊接操作数据及警示信息。本发明中,该操作预置信息包括焊工信息、焊枪编号、焊口编号、预设的电流、预设的电压、预设的待焊接管道的预热温度、预设的焊接层间温度、预设的焊接道数、预设的送丝速度、预设的焊接速度,而实时焊接数据包括安装于焊接主机4内部电路中的电流传感器(图未标示)与电压传感器(图未标示)所采集的电流和电压。而该监控终端6可为便携式电脑、平板电脑、手机或其他监控设备。
[0031]
更详细而言,如图1所示,该焊接层间温度及焊接位置采集装置是由分别独立的焊接层间温度采集装置21与焊接位置采集装置22构成。结合图3及图4所示,该焊接层间温度采集装置装21设于焊枪8的手柄前部并包括:焊枪连接部211、采集装置装设部212、采集电路板(图未标示)及焊渣挡板部213,其中焊枪连接部211为横向截面为u形的半管体并结合于采集装置装设部212的上端且用以套设固定于焊枪8的手柄前部,采集装置装设部212为上端厚度大于下端厚度的块状体且前侧面是面向焊枪8的前端,即面向焊枪嘴部位,采集装置装设部212的后侧面开设有采集板安装室2121,采集板安装室2121朝前侧面开设有贯通采集板安装室2121与前侧面的数个温度传感器安装孔2122,温度传感器安装孔2122中装设有温度传感器(图未标示),采集板安装室2121内装设采集电路板,温度传感器与采集电路板电性连接,采集电路板还具有三轴加速度传感器(图未标示)用以感测焊枪8的转动角度,以使采集电路板根据转动角度启用数个温度传感器中的其中一个进行焊接层间温度的感测,本发明中该三轴加速度传感器可以应用现有的三轴加速度传感器,如adxl345加速度传
感器,但也可以应用其它型号或类型的三轴加速度传感器,本发明对此不进行限定;采集电路板与数据传输装置3电性连接,焊渣挡板部213为片状体并结合于采集装置装设部212的下端,用以防止焊渣溅射到操作人员的手部。而焊接位置采集装置22是绕设固定于待焊接管道7上临近焊接处的位置并包括:防火带221、数个光敏传感器222及两个卡扣(图未标示),其中该数个光敏传感器222彼此间隔而布设于防火带221上,且各光敏传感器222的光敏元件(图未标示)均朝向防火带221的同一侧,各光敏传感器的缆线穿设于防火带内并于防火带上的一穿口穿出而电性连接数据传输装置,两个卡扣装设于防火带221的两个端部,将防火带221绕设于待焊接管道7上临近焊接处的位置处,并使光敏元件朝向焊接处,通过两个卡扣的对合扣固而将焊接位置采集装置22固定于待焊接管道7上。本发明中,该光敏传感器222可为紫外线传感器、防火带221可由两层防火织带缝制而成,该光敏传感器222的缆线是穿设于两层防火织带的夹层内,以保护缆线不受高温或飞溅的焊渣而损毁,该数个光敏传感器222可彼此间隔相同距离而均匀布设于防火带221上,以此可对焊接操作的进程进行信号间隔的良好响应,但该数个光敏传感器222也可根据管道焊接的实际操作需要而使彼此之间的间距不同;另外,该两个卡扣可为织带卡扣,并可通过两个卡扣而调节防火带的长度,以适应不同管径的待焊接管道。通过装设于焊枪的手柄前部的焊接层间温度采集装置可对焊接时的焊接层间温度进行实时采集,通过绕设固定于待焊接管道上的焊接位置采集装置可对焊接时的焊接位置数据进行实时采集。
[0032]
该云端服务器5存储焊接层间温度及该数个光敏传感器感测的感光信号,并且云端服务器5根据感光信号判断当数个光敏传感器222为依序且全部感光时为完成一道焊接,云端服务器5将完成一道焊接的次数进行累加以计算焊接道数,云端服务器5将存储的焊接层间温度及计算的焊接道数与操作预置信息中预设的焊接层间温度及焊接道数进行比对,当判断存储的焊接层间温度与预设的焊接层间温度不同及/或计算的焊接道数与预设的焊接道数不同时则发出警示信息。
[0033]
如图2所示,为本发明焊接数据智能采集监控系统的第二具体实施例,于该实施例中除了焊接层间温度及焊接位置采集装置2与第一实施例不同之外,其它装置及构成是与第一实施例相同的,该焊接层间温度及焊接位置采集装置2的结构与第一实施例中的焊接层间温度采集装置的结构相同,除了可以采集焊接层间温度外,还可以采集焊枪的移动轨迹。本实施例中,该焊接层间温度及焊接位置采集装置2为一个独立的装置且装设于焊枪8的手柄前部,结合图3及图4所示,其包括:焊枪连接部211、采集装置装设部212、采集电路板(图未标示)及焊渣挡板部213,其中焊枪连接部211为横向截面为u形的半管体并结合于采集装置装设部212的上端且用以套设固定于焊枪8的手柄前部,采集装置装设部212为上端厚度大于下端厚度的块状体且前侧面是面向焊枪8的前端,即面向焊枪嘴部位,采集装置装设部212的后侧面开设有采集板安装室2121,采集板安装室2121朝前侧面开设有贯通采集板安装室2121与前侧面的数个温度传感器安装孔2122,温度传感器安装孔2122中装设有温度传感器(图未标示),采集板安装室2121内装设采集电路板,温度传感器与采集电路板电性连接,采集电路板还具有三轴加速度传感器(图未标示)用以感测焊枪8的转动角度及焊枪8的移动轨迹,并且采集电路板根据转动角度启用数个温度传感器中的其中一个进行焊接层间温度的感测,采集电路板与数据传输装置3电性连接,焊渣挡板部213为片状体并结合于采集装置装设部212的下端,用以防止焊渣溅射到操作人员的手部。本实施例通过焊接
层间温度及焊接位置采集装置便可实现对于焊接层间温度与焊接位置数据的实时采集。
[0034]
在本发明中,该三轴加速度传感器水平初始状态的三轴方向是与三维笛卡尔坐标系相一致,而相对于水平横向静置的待焊接的管道,该三轴加速度传感器水平静置时,其z轴方向与重力方向一致,其y轴方向与管道的径向一致,其x轴方向与管道的轴向一致,且在该三轴加速度传感器采集三轴加速度前需先设定三轴加速度传感器采集三轴加速度的频率。
[0035]
于本实施例中,云端服务器5存储焊接层间温度及由三轴加速度传感器根据设定的频率采集的其x轴、y轴及z轴相对于三维笛卡尔坐标系的加速度,并由云端服务器计算焊接道数,焊接道数计算步骤为:
[0036]
计算加速度平均值:云端服务器将每次依序接收的10组x轴、y轴及z轴的加速度数据按照y轴的加速度由小到大的顺序重新排序为10组第一次排序后的加速度数据,然后依序计算相邻的2组加速度数据中y轴的加速度的差值的绝对值,之后按照差值的绝对值由小到大的顺序将产生每个差值的绝对值的2组加速度数据进行排序且将相同的加速度数据进行合并,以形成10组第二次排序后的加速度数据,取前5组第二次排序后的加速度数据并计算x轴、y轴及z轴的加速度平均值。由于焊接操作是人工手持焊枪进行的,因此焊接轨迹难免会有偏移,而计算加速度平均值的目的是为了获得焊枪移动轨迹更为精确的数据,本实施例对上述加速度数据的组数(每次依序接收10组x轴、y轴及z轴的加速度数据及取前5组第二次排序后的加速度数据)仅是举例说明,且并不对具体组数进行限定,通过技术方案可明确得知的是,上述加速度数据的组数越多,计算得出的焊枪移动轨迹就越是精确。
[0037]
计算y轴方向弧度值:由云端服务器根据每次计算得到的加速度平均值计算三轴加速度传感器的y轴与三维笛卡尔坐标系y轴之间的弧度值:其中,αy为y轴与三维笛卡尔坐标系y轴之间的弧度值,avx为x轴的加速度平均值,avy为y轴的加速度平均值,avz为z轴的加速度平均值。
[0038]
计算焊枪的移动轨迹坐标:由云端服务器根据每次计算得到的三轴加速度传感器的y轴与三维笛卡尔坐标系y轴之间的弧度值,计算焊枪相对于待焊接管道截面圆心的移动轨迹坐标:xwg=φp
×
cosαy,ywg=φp
×
sinαy,其中,xwg为焊枪相对于待焊接管道截面圆心处的x轴坐标值,ywg为焊枪相对于待焊接管道截面圆心处的y轴坐标值,φp为待焊接管道的半径;并建立焊枪移动轨迹坐标集合{xwg,ywg∣(xwg1,ywg1),(xwg2,ywg2)
…
(xwgn,ywgn)},n为计算(xwg,ywg)坐标的次序值。本实施例中,对于本步骤的计算是在二维坐标系下完成的,其中是以待焊接管道圆心作为二维坐标系的原点,而建立焊枪移动轨迹坐标集合是为了建立焊枪于二维坐标系中的移动轨迹。
[0039]
判断是否完成一道焊接:云端服务器根据操作预置信息中的包含焊道起始端与终止端的至少两个焊道坐标值{(x1,y1)
…
(xn,yn),n>=2}计算得到检测点坐标范围{(x1±
x1×
10%,y1±
y1×
10%)
…
(xn
±
xn
×
10%,yn
±
yn
×
10%),n>=2},然后判断当焊枪移动轨迹坐标集合中的部分坐标符合依次序出现在检测点坐标范围内时则为完成一道焊接。通过对焊枪移动轨迹坐标是否按照顺序位于检测点坐标范围内的判断,且该检测点坐标范围至少包含焊道起始端与终止端的坐标范围,以可准确的获知焊枪是否完成了一道焊接。
[0040]
计算焊接道数:云端服务器将完成一道焊接的次数进行累加。
[0041]
该云端服务器5将存储的焊接层间温度及计算的焊接道数与操作预置信息中预设的焊接层间温度及焊接道数进行比对,当判断存储的焊接层间温度与预设的焊接层间温度不同及/或计算的焊接道数与预设的焊接道数不同时则发出警示信息。
[0042]
在本发明中(包括上述第一及第二实施例),该温度传感器安装孔的开设数量为四个,且四个温度传感器安装孔的分布呈十字形分布,如图4所示,该温度传感器安装孔于采集装置装设部内可以为具有一定角度的倾斜状开设贯通,结合图5所示,以使四个温度传感器的测量范围9包围但并不覆盖焊枪的焊枪嘴于焊接面焊接时的熔池a,并使四个温度传感器的测量范围9的边缘处彼此重合。以此可使四个温度传感器不受焊枪握持角度和移动路线的影响,而确保总有一个温度传感器能够感测到熔池的焊接温度。而采集电路板根据转动角度启用四个温度传感器中的其中一个进行焊接层间温度的感测的具体方式为:由三轴加速度传感器根据设定的频率采集其x轴、y轴及z轴相对于三维笛卡尔坐标系的加速度,并由采集电路板(其相当于小型处理单元,其上可具有微处理器mcu及存储器)根据加速度计算三轴加速度传感器的x轴与三维笛卡尔坐标系x轴之间的角度值:θx=αx
×
180/π,其中,αx为x轴与三维笛卡尔坐标系x轴之间的弧度值,ax为x轴的加速度值,ay为y轴的加速度值,az为z轴的加速度值,θx为x轴相对于三维笛卡尔坐标系x轴之间的角度值,并于采集电路板设定与呈十字形分布的四个温度传感器相对应的第一角度变化范围、第二角度变化范围、第三角度变化范围及第四角度变化范围,当θx处于第一角度变化范围时,采集电路板启用呈十字形分布状下侧的温度传感器感测焊接层间温度,当θx处于第二角度变化范围时,采集电路板启用呈十字形分布状右侧的温度传感器感测焊接层间温度,当θx处于第三角度变化范围时,采集电路板启用呈十字形分布状左侧的温度传感器感测焊接层间温度,当θx处于第四角度变化范围时,采集电路板启用呈十字形分布状上侧的温度传感器感测焊接层间温度。如图5所示,以上第一、第二、第三及第四角度变化范围α、β、ε、ω于二维坐标系中集合在一起是呈圆状,且第一、第二、第三及第四角度变化范围α、β、ε、ω是根据四个温度传感器的装设位置与倾斜角度设置的,其可以但不限定为第一角度变化范围α为-45
°
≤θz≤45
°
,第二角度变化范围β为-135
°
≤θz<-45
°
,第三角度变化范围ε为45
°
<θz≤135
°
,第四角度变化范围ω为θz>135
°
或θz<-135
°
。
[0043]
在本发明中,由云端服务器计算送丝速度可通过公式v=k1i+k2li2实现,其中v为送丝速度,l为干伸长度,k1和k2为系数,i为电流传感器采集的电流,其中该干伸长度l是焊接工艺规程规定的,而系数k1和k2通常也称为经验常数,按照焊接工艺规程规定,当干伸长度l为19mm时,该系数k1=0.0266、k2=0.0000332。而由云端服务器计算焊接速度可为:针对第一实施例而言,云端服务器根据首个光敏传感器及最后一个光敏传感器之间的弧长与完成一道焊接的时间(该时间可由云端服务器中的时钟统计)计算焊接速度;针对第二实施例而言,云端服务器根据焊枪移动轨迹坐标集合中的首个坐标及最后一个坐标之间的弧长与完成一道焊接的时间计算焊接速度。
[0044]
在本发明中,该操作信息录入装置可由扫码枪及温度传感器构成。结合目前在施工现场对于操作信息如焊接人员身份信息、待焊接管道的管口信息、焊枪设备信息均广泛采用编码方式的应用(如条形码、二维码等),利用扫码枪可快速扫描上述操作信息,提高焊接施工的效率,另外还可减少由人工信息录入带来的信息录入错误及操作舞弊情况的发
生。而焊接数据采集装置除了包括安装于焊接主机内部电路中的电流传感器与电压传感器外,还可包括温、湿度传感器等。
[0045]
本发明的焊接数据智能采集监控系统可在焊接施工前将操作人员信息、焊接工艺参数及焊接环境条件等信息通过无线网络传输至云端服务器进行存储,在焊接施工过程中可实时采集焊接操作数据并上传至云端服务器,由云端服务器据以计算判断焊接操作数据是否符合焊接工艺要求,当不符合焊接工艺要求时,云端服务器可及时向现场管理者或质量监管人员等的监控终端发送警示信息,以辅助对焊接现场焊接质量的实时把控,确保焊接质量的稳定。另外,云端服务器还可对操作预置信息、实际焊接数据及是否符合焊接工艺要求等信息进行存储留档,以便后期对于焊接施工过程的查询与分析,对于完善焊接质量管理体系,提升焊接施工质量提供了详实的数据支持。
[0046]
以上仅为本发明的较佳实施例,并非用以限定本发明的专利范围,其他运用本发明的专利构思所做的等效变化,均应属于本发明的专利保护范围。