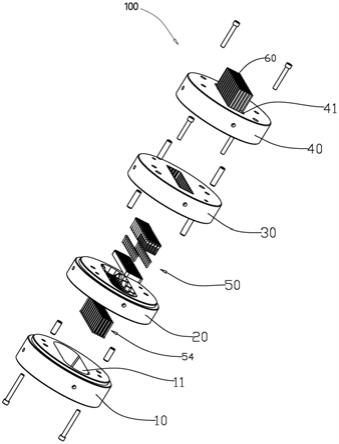
1.本发明涉及模具领域,具体涉及一种多孔蜂窝型材挤压组件。
背景技术:2.随着铝工业技术发展,目前工业用铝的范围在不断扩大,无论是汽车行业,建筑行业,环保行业以及其它各个行业或多或少都会使用工业铝蜂窝产品。
3.现有铝蜂窝产品大部分是以粘联或焊接方式制成,成品尺寸精度差,强度低,无法满足精密生产,目前已有铝挤压蜂窝模具为一体结构,而蜂窝结构限制,只能生产尺寸宽度方向250mm以下蜂窝产品,并且现有的铝挤压蜂窝模具加工周期长,维修困难,制作成本高,导致此类产品成本居高不下,不利于批量化生产。
技术实现要素:4.本发明的目的是提供一种多孔蜂窝型材挤压组件,以解决上述现有技术中存在的问题。
5.为了解决上述问题,根据本发明的一个方面,提供了一种多孔蜂窝型材挤压组件,所述多孔蜂窝型材挤压组件包括导流模体、成型模体以及面模体,所述导流模体和所述面模体可拆卸连接,所述成型模体设置于所述导流模体和所述面模体之间,其中,所述导流模体设有多个第一导流孔和多个第一固定孔,所述导流模体通过所述第一固定孔与所述成型模体固定连接,挤压型材通过所述多个第一导流孔流入所述成型模体并经过所述成型模体形成多孔蜂窝产品。
6.在一个实施例中,所述导流模体具有朝向所述面模体的第二表面和与所述第二表面相对的第一表面,所述第二表面形成有下沉部,所述多个第一导流孔和所述多个第一固定孔设置于所述下沉部内并从所述下沉部延伸至所述导流模体的第一表面。
7.在一个实施例中,所述下沉部内设有支撑板,所述支撑板通过多个连接部与所述下沉部的内壁连接,所述多个连接部之间形成第二导流孔。
8.在一个实施例中,一个所述第一导流孔在所述导流模体的第一表面上形成一个较宽的入口并在下沉部的表面上形成两个较窄的出口;较佳地,两个较窄的出口具有锥形形状或三角形形状,该锥形形状或三角形形状的顶部相互对置。
9.在一个实施例中,所述多个第一固定孔在所述支撑板上分别沿所述支撑板的长度方向布置成m行和沿所述支撑板的宽度方向布置成n列,第m1行的第一固定孔与第m1+1行的第一固定孔在列的方向上错开布置,第m1行的第一固定孔与第m1+2行的第一固定孔在列的方向上对齐布置,以及第m1行的第n1个第一固定孔与第m1+2行的第n1个第一固定孔之间布置所述第一导流孔,其中,1≦m1≦m-2,1≦n1≦n-2,m,n为整数。
10.在一个实施例中,所述成型模体包括成型件以及成型板,所述成型板与所述导流模体的下沉部配合并设有成型件孔和第三导流孔,所述成型件孔与所述成型件配合,所述第三导流孔与所述第一导流孔配合。
11.在一个实施例中,所述成型模体还包括第一固定件,所述支撑板还设有第二固定孔,所述成型板还设有第三固定孔,所述第三固定孔与所述第二固定孔配合,所述第一固定件伸入所述第三固定孔与所述第二固定孔内以将所述成型板与所述支撑板相互固定。
12.在一个实施例中,所述多孔蜂窝型材挤压组件还包括第二固定件,所述成型件包括成型头和成型杆,所述成型杆的上端与所述成型头连接,所述成型杆的下端设有第四固定孔,所述第四固定孔沿所述成型杆的长度方向延伸并与所述第二固定件配合。
13.在一个实施例中,所述成型杆具有圆柱状主体,所述圆柱状主体的外径与所述成型板上的成型件孔的内径配合,其中所述成型杆的侧面设有削边部,所述削边部从成型杆的端面朝向所述成型头延伸一定距离。
14.在一个实施例中,所述成型杆在靠近下端的外壁上还设有可拆卸的止挡部,所述成型件孔的内壁设有与所述止挡部配合的凹槽,通过所述止挡部于所述凹槽的配合将所述成型件与所述导流模体相互定位,较佳地,所述止挡部设置成两个并关于所述成型杆的沿长度方向延伸的中轴线对称。
15.在一个实施例中,所述成型件孔内设置两个对称的凹槽,所述两个对称的凹槽之间设置有与所述削边部配合的配合部;较佳地,所述削边部采用在所述成型杆的圆柱面上加工出的平面形状,以及所述配合部也形成一个平面状,从而与所述削边部紧密配合。
16.在一个实施例中,每一个所述成型杆的下端容纳在每一个所述成型件孔内并通过所述止挡部与所述凹槽配合定位,每一个所述成型头与相邻的成型头之间形成缝隙供型材流过,这些缝隙整体上形成蜂窝形状,从而型材从这些缝隙流出后形成蜂窝型结构。
17.在一个实施例中,所述面模体具有朝向所述导流模体的第一表面和与该第一表面相对的第二表面,所述第一表面的中部设有凹陷部,所述凹陷部与所述导流模体的下沉部配合并形成仿形焊合室,原料在所述仿形焊合室内溶合。
18.在一个实施例中,所述凹陷部内设有中空部,所述中空部沿所述面模体的厚度方向延伸并贯通整个面模体的厚度以及在所述面模体的第二表面上形成开口。
19.在一个实施例中,所述中空部包括第一部分和第二部分,所述第一部分的内径小于所述第二部分的内径,其中所述第一部分的内壁设有突出部以与所述成型头配合,以及在所述成型头的外壁与所述突出部的内壁之间形成间隙以供型材流过。
20.在一个实施例中,所述多孔蜂窝型材挤压组件还包括出料口垫模,所述出料口垫模可拆卸地连接于所述面模体的所述第二表面并在中部形成产品出口,所述产品出口的内径大于所述面模体的中空部的第二部分的内径。
21.在一个实施例中,所述多孔蜂窝型材挤压组件还包括拓展模体,所述拓展模体设有进料口并具有面向所述导流模体的第二表面和与所述第二表面相对的第一表面,所述进料口在所述拓展模体的第一表面上形成第一开口以及在所述拓展模体的第二表面上形成第二开口,所述进料口从第一开口向第二开口的口径逐渐增大;较佳地,所述进料口具有喇叭形结构。
22.在一个实施例中,所述拓展模体、导流模体、面模体以及出料口垫模具有圆盘状主体,从而所述多孔蜂窝型材挤压组件具有圆柱状,其中,所述拓展模体、导流模体、面模体以及出料口垫模的相互接触的两个表面之间通过设置销钉与销孔配合的方式相互定位。
23.在一个实施例中,所述拓展模体、导流模体、面模体以及出料口垫模相互接触的两
个表面都通过一个表面设置凸台另一个表面设置圆环状下沉部的方式相互定位配合。
24.在一个实施例中,所述拓展模体、导流模体、面模体以及出料口垫模通过螺钉可拆卸地相互固定连接。
25.本发明解决了大尺寸一体蜂窝产品不能生产的问题。比现有技术相比,此发明可以大幅降低模具的加工难度,缩短加工时间一半以上,节省了模具制作成本。此外,由于采用新结构,实现了模具从一次报废到多次循环使用转变,同时也降低了维修难度。
附图说明
26.图1是多孔蜂窝型材挤压组件的立体分解图。
27.图2是多孔蜂窝型材挤压组件的剖视图。
28.图3a和图3b是扩展模体的不同视角的立体图。
29.图4a和图4b是导流模体的不同视角的立体图。
30.图4c是图4a的a部分的放大图。
31.图4d是图4b的b部分的放大图。
32.图5a和图5b是成型模体的不同视角的立体分解图。
33.图5c和图5d是成型板的不同设视觉的立体图。
34.图5e是多个成型件安装于成型板上形成的组件的立体图。
35.图6a和图6b是面模体的不同视角的立体图。
具体实施方式
36.以下将结合附图对本发明的较佳实施例进行详细说明,以便更清楚理解本发明的目的、特点和优点。应理解的是,附图所示的实施例并不是对本发明范围的限制,而只是为了说明本发明技术方案的实质精神。
37.本发明的多孔蜂窝型材挤压组件主要用来生产蜂窝型模制产品,例如可以用来生产铝制产品以及塑料产品等,以解决传统工具无法生产诸如大尺寸多孔一体铝蜂窝产品的问题,例如本发明的多孔蜂窝型材挤压组件用来加工铝型材时最大高度尺寸可以做到500mm,最大宽度尺寸可以做到300mm,最大长度尺寸可以做到6000mm。此外,本发明的多孔蜂窝型材挤压组件还可以解决传统工具铝挤压模具加工难度大,生产周期长的问题;以及解决此类铝挤压模具在实际生产中进料困难,出料不一致的问题。需要说明的是,本发明的技术方案不需要同时解决这些问题,在一些方案中,可以解决上述技术问题中的一个问题,在另一些方案中,可以解决上述问题的两个或三个问题,或附带解决其他问题,也就是说,解决上述至少一个问题,本发明的方案与现有技术相比,就具有了优异技术效果。
38.下面以生产多孔蜂窝铝型材制品为例对本发明的多孔蜂窝型材挤压组件进行详细描述。
39.图1是多孔蜂窝型材挤压组件100的立体分解图。如图1所示,多孔蜂窝型材挤压组件100总体上包括可拆卸的拓展模体10、导流模体20、面模体30、出料口垫模40以及成型模体50。导流模体20设置于拓展模体10和面模体30之间,面模体30设置于导流模体20和出料口垫模40之间,成型模体50设置于导流模体20和面模体30内部,拓展模体10设有进料口11,出料口垫模40设有产品出口41,型材通过进料口11进入多孔蜂窝型材挤压组件100,并经过
成型模体50挤压成型后,从产品出口41输出产品60。
40.图2是多孔蜂窝型材挤压组件100的剖视图,图3a和图3b是扩展模体10不同视角的立体图。如图2、图3a和图3b所示,拓展模体10具有面向导流模体20的第二表面13和与第二表面13相对的第一表面12,进料口11优选设置于拓展模体10的中部并沿拓展模体10的厚度方向延伸,并在拓展模体10的第一表面12上形成第一开口121以及在拓展模体10的第二表面13上形成第二开口131,进料口11从第一开口121向第二开口131的口径逐渐增大,例如,进料口11可以设置成喇叭形结构,横截面积较小的棒料在拓展模体10压缩作用下通过进料口11后截面面积增大,实现用更小的设备生产更大尺寸的型材产品。
41.继续参照图3b,在一个实施例中,拓展模体10的第二表面13设有凸台132,凸台132与导流模体20的第一表面的凹槽配合,对拓展模体10进行定位和一定固定作用,即限制拓展模体10在导流模体20的第一表面上进行滑移运动。拓展模体10和导流模体20可以进一步通过例如螺钉和/或销钉相互固定。
42.具体地,返回参照图2,通过将螺钉从拓展模体10的第一表面11贯穿拓展模体10的厚度并伸入到导流模体20的内部,从而将导流模体20与拓展模体10相互固定。在一个实施例中,还可以在拓展模体10的第二表面和导流模体20的第一表面的对应位置设置销钉槽,通过销钉将拓展模体10和导流模体20连接。优选地,拓展模体10形成圆柱状轮廓,第一表面12和第二表面13分别为圆柱体的上表面和下表面。
43.图4a和图4b是导流模体20的不同视角的立体图,图4c是图4a的a部分的放大图,图4d是图4b的b部分的放大图,如图4a、4b、4c和4d所示,导流模体20整体上具有与扩展模体10匹配的尺寸并具有朝向拓展模体10的第一表面21和朝向面模体30的第二表面22。第二表面22形成有下沉部23,下沉部23设有多个第一固定孔232和多个第一导流孔231,多个第一固定孔232和多个第一导流孔231从下沉部23的表面延伸至导流模体20的第一表面21。在一个实施例中,多个第一导流孔231和多个第一固定孔232在下沉部23内交错间隔布置。
44.在一个实施例中,参照图4b,在下沉部23内设有支撑板233,支撑板233通过多个连接部234与下沉部23的内壁235连接,多个连接部234之间形成第二导流孔236。换句话说,可以理解为导流模体20的中部形成有沿导流模体20的厚度方向贯穿第一表面21和第二表面22的通孔,通孔内设置支撑板233,支撑板233通过连接部234连接于通孔的内壁上,支撑板233的一个表面与导流模体20的第一表面21平齐,支撑板233的另一个表面相对于导流模体20的第二表面22形成下沉部23。下沉部23的深度优选设置成与成型模体50的成型板53的厚度大致相等。
45.参照图4c,其示出多个第一固定孔232和多个第一导流孔231的排布方式,如图4c所示,多个第一固定孔232在支撑板233上分别沿支撑板的长度方向布置成m行和沿支撑板的宽度方向布置成n列,第m1行的第一固定孔232与第m1+1行的第一固定孔232在列的方向上错开布置,也就是说,第m1行的第n1个第一固定孔232与第m1+1行的第n1个第一固定孔232没有布置在同一列上。第m1行的第一固定孔232与第m1+2行的第一固定孔232在列的方向上对齐布置,也就是说,第m1行的第n1个第一固定孔232与第m1+2行的第n1个第一固定孔232布置在同一列上。在第m1行的第n1个第一固定孔与第m1+2行的第n1个第一固定孔之间布置第一导流孔231。其中,1≦m1≦m-2,1≦n1≦n-2,m,n为自然数。
46.在一个实施例中,参照图4c和图4d,一个第一导流孔231在导流模体20的第一表面
21上形成一个较宽的入口2311并在下沉部23的第二表面上形成两个较窄的出口2312,也就是说,型材通过第一导流孔231的入口2311进入后,通过第一导流孔231进行分流后再从两个出口2312分别流出。较佳地,两个较窄的出口2312具有锥形形状或三角形形状,该锥形形状或三角形形状的顶部相互对置并都与同一个入口2311流体连通。
47.在一个实施例中,参照图4a-4d,多个第一导流孔231沿多个成排的第一固定孔232排布的方向成排布置。沿支撑板233的周部,也就是围绕第一导流孔231和第一固定孔232布置区域,设有第二固定孔237,第二固定孔237用于将支撑板233与成型模体50相互固定连接,具体为将支撑板233与成型模体50的成型板53固定连接,下文还会进一步详细描述。
48.图5a和图5b是成型模体50的不同视角的立体分解图,图5c和图5d是成型模体50的成型板53的不同设视觉的立体图,其示出成型板53的两个相对的表面。如图5a-5d所示,成型模体50包括成型件51、第一固定件(例如固定螺钉)52以及成型板53,成型板53安装于导流模体20的下沉部23内,并具有朝向下沉部23的第一表面531和与第一表面531相对的第二表面532,第一表面531与下沉部23的上表面接触,第二表面532优选与导流模体20的第二表面22齐平,也就是说,成型板53的厚度与下沉部23的下沉深度基本相等。成型板53设有多个成型件孔533、多个第三导流孔534以及第三固定孔535,多个成型件孔533与成型件51配合,第三导流孔534与导流模体20上的多个第一导流孔231配合,第三固定孔535与导流模体20上的第二固定孔237配合,将成型板53安装于下沉部23内时,每一个成型件孔533与支撑板233上的一个第一固定孔232对准,成型件51的下端伸入成型件孔533内,然后通过将第二固定件(例如螺钉)54穿过第一固定孔232并插入成型件51内固定,从而将成型件51与成型板53以及支撑板233相互定位并固定。第一导流孔231与第三导流孔534对准。待挤压的型材通过第一导流孔231流向第三导流孔534。成型板53的第三固定孔535与支撑板233的第二固定孔237对准,然后将第一固定件(例如螺钉)52通过第三固定孔535插入第二固定孔237内,从而进一步将成型板53与支撑板233相互固定。具体地,第三固定孔535布置成沿成型板53的长度方向延伸的两排,并设置于成型板53的相对的两长侧边的内侧,多个成型件孔533与多个第三导流孔534布置在两排第三固定孔535之间。
49.继续参照图5a和图5b,成型板53上的成型件孔533和第三导流孔534与下沉部23的第一固定孔232和第一导流孔231一一对应配合,也就是说,成型板53上的成型件孔533和第三导流孔534的布置和排列方式与下沉部23内的第一固定孔232和第一导流孔231的布置和排列方式相同。具体地,成型板53的第三导流孔534的入口和出口都与下沉部23的第一导流孔231的出口2312对应配合,也就是说,第三导流孔534的入口和出口具有基本相同的大小并与下沉部23的第一导流孔231的出口2312对齐配合。
50.继续参照图5a和图5b,成型件51总体上包括成型头511和成型杆512,成型杆512的一端(本文称为上端)与成型头511连接,成型杆512的另一端(本文称为下端)的端面设有第四固定孔5121,第四固定孔5121沿成型杆512的长度方向延伸一定距离。成型杆512的下端插入成型板53的成型件孔533内,然后将第二固定件(例如固定螺钉)54通过第一固定孔232插入成型杆512的第四固定孔5121内,从而将成型件51和成型板53固定在下沉部23内,并将成型模体50与导流模体20固定连接。在本实施例中,成型头511具有正六边形截面以加工蜂窝形产品。在一个实施例中,成型头511的宽度或外径大于成型板53的成型件孔533的内径。
51.成型杆512整体上具有圆柱状主体,该圆柱状主体的外径与成型板53上的成型件
孔533的内径配合。其中,成型杆512的侧面设有削边部5122,削边部5122从成型杆512的端面朝向成型头511延伸一定距离,优选延伸大于成型杆512的长度的二分之一。成型杆512在靠近下端的外壁上设有止挡部5123,止挡部5123优选设置成两个并关于成型杆512的沿长度方向延伸的中轴线对称。在一个实施例中,削边部5122位于两个止挡部5123之间并优选位于两个止挡部5123之间的中间位置。两个止挡部5123优选设置成具有圆弧形外表面,以及两个圆弧形外表面的弧度优选设置成相同。在一个实施例中,两个止挡部5123沿垂直于成型杆512的长度方向的高度小于成型头511的外缘与成型杆512的外壁之间的距离。成型板53的成型件孔533的内壁设有与成型杆512的止挡部5123配合的凹槽5331。当成型杆512上设置对称的两个止挡部5123时,成型件孔533内也设置两个对称的凹槽5331,两个凹槽5331之间设置与削边部5122配合的配合部5332,当削边部5122采用在成型杆512的圆柱面上加工出平面的形状时,配合部5332也形成一个平面状,从而与削边部5122贴紧配合,止挡部5123配合嵌入凹槽5331内。凹槽5331的开口设置于成型板53的面向下沉部23的表面(称为下表面)上,凹槽5331沿成型板53的厚度方向延伸一定距离并与成型杆512的止挡部5123的设置位置对应配合,当成型杆512的下端与成型板53的下表面齐平时,止挡部5123抵靠凹槽5331的底部,从而对成型杆53进行限位。止挡部5123可拆卸安装于成型杆512上,安装时,先将成型杆512的下端穿过成型件孔533并向下伸出一定距离,然后将两个止挡部5123对称安装于成型杆512的侧面,然后再将成型杆512向上退出,使得止挡部5123卡入成型件孔533的凹槽5331内定位。
52.图5e是多个成型件51安装于成型板53上形成的组件的立体图,其中,未示出第三导流孔。如图5e所示,多个成型件53整齐布置于成型板53上,其中,每一个成型件51的成型杆512的下端容纳在成型板53的成型件孔533内并通过止挡部5123与凹槽5331配合定位,每一个成型件51的成型头511与相邻的成型头511之间形成缝隙供型材流出,这些缝隙整体上形成蜂窝形状,从而型材从这些缝隙流出后形成蜂窝型结构,由于各个缝隙相互连通,因此,型材流过这些缝隙之后形成多孔蜂窝结构。
53.图6a和图6b是面模体30不同视角的立体图,如图6a和图6b所示,面模体30整体上形成与拓展模体10和导流模体20的形状匹配的圆盘状并包括圆盘状主体31,圆盘状主体31具有朝向导流模体20的第一表面311和与该第一表面311相对的第二表面312,第一表面311的外周形成环形凸出部313,也就是说,第一表面311的高度低于环形凸出部313的高度,从而第一表面311整体上相对于环形凸出部313下沉,并与导流模体20的第二表面22上的凸出部配合,从而将导流模体20与面模体30相互定位。第一表面311的中部还设有凹陷部324,凹陷部324与导流模体20的下沉部配合形成仿形焊合室,原料通过导流模体20的第一导流孔231和第二导流孔236后在仿形焊合室内溶合。凹陷部324内设有中空部32,中空部32沿面模体30的厚度方向延伸并贯通整个面模体30的厚度并在面模体30的第二表面312上形成开口。返回参照图2,在一个实施例中,中空部32从第一表面311向第二表面312的方向依次包括第一部分321和第二部分322,第一部分321的内壁设有突出部323以与成型件51的成型头511配合,并在成型头511的外壁与突出部323的内壁之间形成间隙以供型材流过并形成蜂窝形状。第二部分322的内径大于第一部分321的内径,以形成一个较大的空间便于加工后的产品输出。
54.参照图1-2,出料口垫模40整体上形成与面模体30配合的圆盘状并在中部形成有
产品出口41,产品出口41的内径大于面模体30的中空部32的第二部分322的内径,以方便产品输出。出料口垫模40具有承载压力,提升模具强度的作用。
55.需要说明的是,本发明的多孔蜂窝型材挤压组件100的拓展模体10、导流模体20、面模体30以及出料口垫模40都具有外径大致相等的圆盘状,从而多孔蜂窝型材挤压组件100整体上形成圆柱状,其中,拓展模体10、导流模体20、面模体30以及出料口垫模40的相互接触的两个表面之间都可以通过设置销钉与销孔配合的方式相互定位,以及相互接触的两个表面都可以通过一个表面设置凸台另一个表面设置圆环状下沉部的方式相互定位配合。各个模体之间可以通过螺钉可拆卸地相互固定。
56.使用时,将多孔蜂窝型材挤压组件100安放在工作台面上,然后通过螺钉和销钉将拓展模体10、导流模体20、面模体30、出料口垫模40连接成一体,然后通过外部设备将原料导入拓展模体10。然后原料通过导流模体20的第一导流孔231和第二导流孔236后在仿形焊合室内溶合,再通过成型头511之间的缝隙和面膜体30的中空部32的第一部分321的内壁与成型头511之间间隙挤压出料并进行冷却定型出合格的产品。
57.综上,本发明的多孔蜂窝铝型材挤压组件通过拓展模体将原本截面较小的棒料在拓展模体的作用下,让其面积增大,可以实现用更小的设备生产更大尺寸的型材产品,同时通过将导流模体与成型模体利用螺钉与销钉连接实现结构分离,不仅节省了加工时间,也节约了制造成本,大大降低了此类型材的制造难度,使其横向供料更加顺畅,有效保证铝型材在生产过程中出料和速率的一致性。
58.以上已详细描述了本发明的较佳实施例,但应理解到,在阅读了本发明的上述讲授内容之后,本领域技术人员可以对本发明作各种改动或修改。这些等价形式同样落于本技术所附权利要求书所限定的范围。