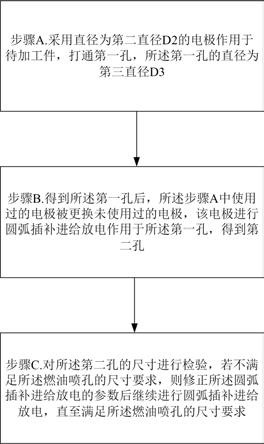
[0001]
本发明涉及加工制造领域,尤其涉及一种燃油喷孔的加工方法以及燃油喷嘴。
背景技术:[0002]
燃油喷嘴为发动机的关键部件,例如作为燃气涡轮发动机燃烧室的关键构件之一,其主要功能是将燃油雾化,加速混合气形成,保证稳定燃烧和提高燃烧效率,而且要高稳定的性能要求,在燃烧室大推力、高温升的工作环境下,燃油喷嘴一般带有热防护设计结构,避免其在很短工作周期内发生低循环疲劳、蠕变疲劳时效等。为满足燃气涡轮发动机的更大推重比、更高燃烧效率、更复杂工况的需求,新一代燃油喷嘴内部油路更加复杂,主燃级与预燃级喷孔的供油流道盘曲交错,整体的异型结构对现有制造技术及能力提出了挑战。
[0003]
燃油流量均匀性是影响燃烧室出口温度分布的主要因素之一,燃烧室出口温度分布品质对涡轮工作的可靠性起着关键的作用。主燃级油路的加工质量直接影响燃油雾化质量和燃油流量分布均匀性,如果燃油雾化效果差,会使过大的油滴喷至燃烧室壁面,使其过热、结焦,进而导致发动机排气冒烟及污染物增加。
[0004]
主燃级喷孔的直径一般较微小,尺寸范围在φ0.3-0.5mm之间,并沿喷嘴零件外轮廓圆周均布。现有技术中,对于主燃级喷孔这样的微小孔加工方法可分为机械加工方法和特种加工方法两大类,其中机械加工方法主要为机械钻削加工,特种加工方法主要包括激光加工和电火花打孔。
[0005]
然而,发明人在完成本发明的过程中发现,若对主燃级油路喷孔采用机械钻孔加工能够获得良好的尺寸精度和孔的形状,生产效率较高。使用的钻削刀具直径细小,需要保证微小孔切削系统的稳定,对钻削设备、刀具及切削工艺参数有着非常高的要求。虽然机械钻孔能够获得良好的切削质量,但由于钻削出口处的毛刺翻向弯曲的流道内壁,同时孔径微小,不能通过人工和手动工具去除毛刺(即燃油喷孔需要是近净成形的),这样会直接影响喷孔流量的稳定和工作性能,因此机械钻孔的方法不适合在这种构型的喷孔上使用。
[0006]
激光加工是典型的光热效应加工过程,几乎不受工件材料的限制,可以获得大深径比的微小孔,其非接触式的加工形式,无切削力,可用于薄壁零件的加工;激光加工按脉冲宽度来划分为毫秒激光、纳秒激光和飞秒激光,其中飞秒激光加工可以获得几乎无重熔层的微小孔,但是其加工效率较低,设备投资大,国内技术成熟度较低,对封闭管路的加工深度控制仍在攻关阶段中,在主燃级喷孔的加工过程中易产生对壁击伤的现象,不能满足燃油喷嘴的使用性能。
[0007]
电火花打孔适用于导电金属材料的加工,可加工深径比100以上的微小孔,高速电火花加工效率非常高,适合数量多、密度高的群孔加工,通过放电能量的优化,在适当降低打孔速度的情况下,能够控制电火花打孔的重熔层厚度;但由于放电间隙的存在以及电蚀产物的非正常放电,因此普通的电火花打孔设备不能够满足0.01mm以内的尺寸加工精度,且孔口易出现加工锥度和圆角,这些缺陷都会对主燃级喷孔的喷射性能产生不利影响。
[0008]
因此,本领域需要一种可以实现燃油喷孔的近净成形的加工方法,解决封闭内型腔油路喷孔的加工难题,保证最终喷孔的尺寸精度和圆柱,避免内壁孔口毛刺和加工对壁击伤,同时能够精密控制喷孔的尺寸大小,获得良好的内孔圆柱度,重熔层厚度控制在0.01mm以内,从而满足主燃级油路喷孔的性能要求。
技术实现要素:[0009]
本发明的目的在于提供一种燃油喷孔的加工方法。
[0010]
本发明的目的在于提供一种燃油喷嘴。
[0011]
根据本发明一个方面的一种燃油喷孔的加工方法,所述燃油喷孔的直径为第一直径d1,所述加工方法的加工精度为0.01mm以内,进行电火花加工,所述加工方法的步骤包括:步骤a.采用直径为第二直径d2的电极作用于待加工件,打通第一孔,所述第一孔的直径为第三直径d3;步骤b.得到所述第一孔后,所述步骤a中使用过的电极被更换未使用过的电极,该电极进行圆弧插补进给放电作用于所述第一孔,得到第二孔。
[0012]
在所述加工方法的一个或多个实施例中,还包括:步骤c.对所述第二孔的尺寸进行检验,若不满足所述燃油喷孔的尺寸要求,则修正所述圆弧插补进给放电的参数后继续进行圆弧插补进给放电,直至满足所述燃油喷孔的尺寸要求。
[0013]
在所述加工方法的一个或多个实施例中,在所述步骤b中,进行圆弧插补进给放电分两步进行,第一次圆弧插补量为d1=d1-d3-0.01mm,加工得到孔径d4,第二次圆弧插补量为d2=d1+d1-d4。
[0014]
在所述加工方法的一个或多个实施例中,所述燃油喷孔包括沿环形周向分布的多个燃油喷孔,定义周向相邻的所述燃油喷孔为第一燃油喷孔、第二燃油喷孔,所述加工方法包括:s1.执行所述步骤a、所述步骤b得到所述第一燃油喷孔;s2.执行所述步骤a、所述步骤b得到所述第二燃油喷孔;其中,在所述s2中执行所述步骤a采用的电极为在所述s1中执行所述步骤b采用的电极。
[0015]
在所述加工方法的一个或多个实施例中,所述s1以及所述s2还包括在执行所述步骤a、所述步骤b后还执行步骤c,对所述第二孔的尺寸进行检验,若不满足所述燃油喷孔的尺寸要求,则修正所述圆弧插补进给放电的参数后继续进行圆弧插补进给放电,直至满足所述燃油喷孔的尺寸要求。
[0016]
在所述加工方法的一个或多个实施例中,重复执行所述s1、所述s2,逐个将周向分布的多个燃油喷孔加工完毕。
[0017]
在所述加工方法的一个或多个实施例中,所述第二直径d2与所述第一直径d1的关系满足以下公式:d2=d1-s-d,其中,s为电火花放电间隙,d为圆弧插补加工量。
[0018]
在所述加工方法的一个或多个实施例中,加工所述电极的步骤包括:步骤a1.将毛坯件切削,毛坯件包括基部以及电极部;步骤a2将毛坯件切削,包括基部以及电极部;步骤a3.将电极部从连接所述基部的一端至另一端分为三段磨削,依次磨削为直径为第四直径d4的第一段、直径为第五直径d5的第二段以及直径为第六直径d6的第三段,其中d4>d5>d6,使得第一段、第二段、第三段各直径间关系满足以下公式:(d4-d5)=(d5-d6)≥[2
×
(d6-d2)];
步骤a4.将所述步骤a2的所述第一段、所述第二段以及所述第三段的直径磨削至第二直径d2。
[0019]
根据本发明另一个方面的一种燃油喷嘴,用于燃气涡轮发动机,包括至少一个燃油喷孔,所述燃油喷孔通过以上任意一项所述的加工方法得到。
[0020]
在所述燃油喷嘴的一个或多个实施例中,所述燃油喷嘴为主燃级喷嘴,所述至少一个燃油喷孔为多个主燃级燃油喷孔。
[0021]
综上,本发明的进步效果包括但不限于以下之一或组合:1.通过圆弧插补式电火花成形加工,保证最终喷孔的尺寸精度和圆柱度。该方法解决了封闭内型腔油路喷孔的加工难题,避免了内壁孔口毛刺和加工对壁击伤;同时能够精密控制喷孔的尺寸大小,获得良好的内孔圆柱度,重熔层厚度控制在0.01mm以内,满足了主燃级油路喷孔的性能要求;2.长悬深微小直径成型电极在加工时容易产生弯曲,通过分段磨削的步骤,能够获得满足尺寸要求的成型电极,其外径尺寸的波动范围控制在微米级,提高了电极的加工一致性,从而提高了喷孔加工的加工精度;3. 对于具有多个喷嘴的燃烧室供油环而言,每个喷嘴的主喷口加工一致性可以缩小全环燃油供给的流量波动,提高整个发动机燃烧室性能。
附图说明
[0022]
本发明的上述的以及其他的特征、性质和优势将通过下面结合附图和实施例的描述而变得更加明显,需要注意的是,附图均仅作为示例,其并非是按照等比例的条件绘制的,并且不应该以此作为对本发明实际要求的保护范围构成限制,其中:图1是根据一实施例的主燃级喷嘴的喷孔的结构示意图。
[0023]
图2是根据图1的a-a向剖视图。
[0024]
图3是根据一实施例的燃油喷孔的加工方法的流程图。
[0025]
图4是加工一实施例的加工方法采用的电极的流程图。
[0026]
图5是一实施例的喷孔的加工方法采用的电极的结构示意图。
[0027]
图6是根据图4的加工电极流程中电极部分段结构示意图。
[0028]
图7是根据图3的加工喷孔的设备结构示意图。
具体实施方式
[0029]
下述公开了多种不同的实施所述的主题技术方案的实施方式或者实施例。为简化公开内容,下面描述了各元件和排列的具体实例,当然,这些仅仅为例子而已,并非是对本发明的保护范围进行限制。“一个实施例”、“一实施例”、和/或“一些实施例”意指与本申请至少一个实施例相关的某一特征、结构或特点。因此,应强调并注意的是,本说明书中在不同位置两次或多次提及的“一实施例”或“一个实施例”或“一替代性实施例”并不一定是指同一实施例。此外,本申请的一个或多个实施例中的某些特征、结构或特点可以进行适当的组合。
[0030]
本申请中使用了流程图用来说明根据本申请的实施例的系统所执行的操作。应当理解的是,前面或下面操作不一定按照顺序来精确地执行。也可以将其他操作添加到这些
过程中,或从这些过程移除某一步或数步操作。
[0031]
需要说明的是,下述实施例中为了更加清楚直观地说明,对加工过程的各部件结构具有特定的尺寸,但本领域技术人员应当理解到,这并不代表本发明仅适用于特定尺寸的燃油喷孔的加工。
[0032]
如图1以及图2所示,在一实施例中,燃油喷嘴以燃气涡轮发动机的主燃级喷嘴100为例,具有多个主燃级燃油喷孔10,以图示相邻的第一燃油喷孔11、第二燃油喷孔12为例。孔径为φ0.44mm至0.45mm,位于φ1.5mm深0.5mm的台阶内孔上,喷口轴向长度为3mm,12处沿外轮廓圆周均布,喷孔10的喷口与主燃级油路的铸造成型内部流道贯通。内部流道形状弯曲,进油口距离喷口相对较远。
[0033]
参考图1至图3,以及图5、图7,加工燃油喷孔10的步骤可以包括:步骤a.采用直径为第二直径d2的电极作用于待加工件,打通第一孔,所述第一孔的直径为第三直径d3;具体地,关于电极4的设计以及加工方法,在后续的介绍中会详细描述。电极按照喷孔的尺寸孔径为φ0.44mm至0.45mm,位于φ1.5mm深0.5mm的台阶内孔上,喷口轴向长度为3mm,预留粗加工电火花位,及插补精加工火花位,电极4整体结构如图5所示,包括基部41以及电极部42外径可选定为φ0.37-0.01mm,长度为5mm。
[0034]
加工时使用如图7所示的精密电火花成型机,包括机床工作台1,分度夹盘2,燃油喷嘴工件3,电极4,快换加长杆5,电极装夹角度微调装置6;三爪夹具21,手摇柄22,分度盘23,锁紧螺栓24。
[0035]
首先将燃油喷嘴工件3装夹在分度夹盘23上,找正工件3各定位基准在0.01mm以内;使用快换加长杆5夹持电极4,拉直电极4尾柄在0.005mm以内,测头分中电极的基部41,确定电极4位置;设置放电参数,粗加工第一燃油喷孔11,将喷口打通,电极前端透过0.5mm,孔径控制在φ0.42mm以内;即此时得到第一燃油喷孔11的粗加工形态,即第一孔。
[0036]
步骤b.得到所述第一孔后,所述步骤a中使用过的电极被更换未使用过的电极4,该电极4进行圆弧插补进给放电作用于所述第一孔,得到第二孔。
[0037]
具体而言,在得到第一孔之后,更换电极4,拉直成型电极4的基部在0.005mm以内,测头分中电极的基部41,确定电极4的位置;竖直向下进给放电,半精加工第一燃油喷孔11,修整孔径锥度,电极4前端透过0.5mm;通过数控程序控制电极进行圆弧插补进给放电,抬出电极4,即得到第二孔。
[0038]
优选地,在所述步骤b中,进行圆弧插补进给放电可以分两步进行,第一次圆弧插补量为d1=d1-d3-0.01mm,加工得到孔径d4,第二次圆弧插补量为d2=d1+d1-d4,如此可以进一步提高加工的精度。
[0039]
在得到第二孔后,可以进行检验步骤,即进行步骤c,对第二孔的尺寸进行检验,若不满足所述燃油喷孔的尺寸要求,则修正所述圆弧插补进给放电的参数后继续进行圆弧插补进给放电,直至满足所述燃油喷孔的尺寸要求。
[0040]
具体的检验方法可以使用针规检查第一燃油喷孔11内孔,φ0.44mm针规通过、φ0.45mm针规不进;如喷孔尺寸未到达尺寸,使用小于φ0.44mm的针规检查孔径实际值,并相
应修改数控程序中的补偿参数,电极重新穿入内孔至相同深度,进行圆弧插补进给放电,直至φ0.44mm针规通过、φ0.45mm针规不进。
[0041]
但本领域技术人员可以理解到,并非都需要对第二孔的尺寸进行检验,需要检验的情况一般是工艺尚不成熟的试验阶段,若经过多次试验后得到稳定可靠的圆弧插补参数,得到的第二孔尺寸稳定,那么完全可以无需进行检验步骤c或者加工完毕后仅对部分加工的燃油喷孔进行抽检。
[0042]
加工得到第一燃油喷孔11后,需要对第二燃油喷孔12进行加工。此时松开分度夹盘2的锁紧装置,切换工件3角度至电极4对准第二燃油喷孔12,重新锁紧分度夹盘2。
[0043]
使用对第一燃油喷孔11圆弧插补放电加工的电极4对第二燃油喷孔12进行粗加工,将喷口打通,电极前端透过0.5mm,孔径控制在φ0.42mm以内。
[0044]
接下来的步骤与加工第一燃油喷孔11类似,此处不再赘述。加工得到第二燃油喷孔12后,继续重复以上步骤,加工在周向分布的剩余的燃油喷孔,完成所有主燃级喷嘴的燃油喷孔的加工。
[0045]
承上可知,采用以上实施例介绍的加工方法,通过在步骤a、步骤b更换电极,防止由于电极磨损不均和表面附着物增加而导致放电间隙不稳定的存在以及电蚀产物的非正常放电,以及步骤b的圆弧插补式电火花成形加工,保证最终喷孔的尺寸精度和圆柱度。该方法解决了封闭内型腔油路喷孔的加工难题,避免了内壁孔口毛刺和加工对壁击伤;同时能够精密控制喷孔的尺寸大小,获得良好的内孔圆柱度,重熔层厚度控制在0.01mm以内,满足了主燃级喷嘴的喷孔的性能要求。对于具有多个喷嘴的燃烧室供油环而言,每个喷嘴的主喷口加工一致性可以缩小全环燃油供给的流量波动,提高整个发动机燃烧室性能。
[0046]
参考图4至图6,在一些实施例中,电火花加工所使用的电极4为精密微细电极,电极部直径小于0.40mm,长径比大于10的电极,采用分段磨削方式加工制备,加工方法可以包括:步骤a1.确定电极4的电极部42的尺寸,例如图5所示的,电极部42外径可选定为φ0.37-0.01mm,长度为5mm。确定电极部42的外径,即第二直径d2,基于以上加工方法,可以根据燃油喷孔的尺寸,预留粗加工电火花位,及插补精加工火花位。具体公式如下:d2=d1-s-d其中,s为电火花放电间隙,即预留粗加工电火花位,由电加工参数决定,可以通过工艺试验获得,实施例中实际为0.05mm。d为圆弧插补加工余量,即插补精加工火花位,也可以通过工艺试验获得,一般为0.02mm至0.05mm,本实施例中选择为0.03mm。如此可以选定的电极尺寸可以进一步保证燃油喷孔的加工质量。
[0047]
步骤a2将毛坯件切削,毛坯件包括基部41以及电极部42;具体的步骤可以是:车削加工整批次数量的紫铜电极,车削电极部42外径至φ0.65-0.02mm,车削电极基部41至φ6mm-(0.02mm至0.03mm),基部41将做为每个电极之后的磨削、检测、电加工过程的统一基准,且同批次的电极基部41尺寸要有较好的一致性,方便后续的磨削和检测;磨削首件电极,使用小型外圆磨床或手摇磨床,以电极基部41为基准,装夹找正跳动在0.002mm以内,修整砂轮,粗磨电极端外径见光,电极部42尺寸磨削至约φ0.63mm,计算得出砂轮零位。
[0048]
步骤a3.将电极部42从连接所述基部的一端至另一端分三段磨削,依次磨削为直
径为第四直径d4的第一段421、直径为第五直径d5的第二段422以及直径为第六直径d6的第三段423,其中d4>d5>d6,各直径间关系满足以下公式:(d4-d5)=(d5-d6)≥[2
×
(d6-d2)]具体可以是:分段半精磨首件电极的电极部42,如图4所示,首先磨削电极部42第三段423的1.5mm长部分至φ0.39mm,再磨削电极部42第二段422的2mm部分至φ0.44mm,最后磨削电极部42第一段421的1.5mm部分至φ0.49mm。
[0049]
步骤a4.将所述步骤a3的所述第一段、所述第二段以及所述第三段的直径磨削至第二直径d2,并且磨削过程采用径向走刀方向,禁止进行轴向走刀。优选地,在进行步骤a3的半精磨后,步骤a4进行磨削之前,可以修整砂轮的尺寸以及直线度,以保证微细电极的尺寸和形状精度。
[0050]
以上介绍的分段磨削的有益效果在于,发明人发现,对于电极部直径小于0.40mm,长径比大于10的电极而言,通过步骤a3中第一段、第二段、第三段的尺寸设计,以及步骤a4中采用径向走刀方向,禁止进行轴向走刀的步骤,使得以上实施例介绍的加工方法相比于现有技术的径向走刀结合轴向走刀的磨削方法而言,实施例的加工方法可以保证微细电极的尺寸和形状精度,以及加工一致性,从而保证燃油喷孔的加工质量。其原理在于,相比于现有技术的轴向精磨削方式,实施例介绍的加工方法可以保证弱刚性电极部位的尺寸精度,径向走刀可以保证电极待加工的刚性较强部位首先进行磨削,而弱刚性部位最后进行磨削接触,强刚性部位与弱刚性部位的磨削余量满足上述公式的比例关系,以此来保证微细电极部位在磨削过程的稳定性,避免让刀及折弯变形,从而保证微细电极的尺寸和形状精度,以及加工一致性。
[0051]
步骤a4具体可以为:精磨首件电极的电极部42,砂轮径向进给,磨削电极的电极部425mm全长度的外径至φ0.37mm,砂轮径向退出,禁止轴向进给。
[0052]
得到电极4之后,可以进行检验步骤,具体可以包括:投影仪检测电极部42外径尺寸与直线度,如尺寸超出电极公差要求,计算调整磨削砂轮零位;磨削整批次数量的成型电极,过程中投影仪抽检电极外径磨削尺寸,如发现尺寸波动,及时修整砂轮;整批次数量的电极磨削完成后,进行投影仪100%复检,按电极部42外径实测值,以微米级分类,为电火花成型分级使用;圆弧插补放电补偿参数按已分类电极外径的实际值做相应修改。
[0053]
如此加工的有益效果在于,发明人发现,长悬深微小直径成型电极在加工时容易产生弯曲,而通过分段磨削的步骤,能够获得满足尺寸要求的成型电极的电极部42,其外径尺寸的波动范围控制在微米级,提高了电极的加工一致性,从而提高了喷孔加工的加工精度。
[0054]
可以理解到,在一些实施例中,可以是同一主体实施加工电极以及进行燃油喷孔的加工步骤,但不以此为限,例如可以提前委托批量加工购买电极,待有加工需要时再进行燃油喷孔的加工。
[0055]
综上,采用上述实施例提供的燃油喷孔的加工方法以及燃油喷嘴的有益效果在于:1.通过圆弧插补式电火花成形加工,保证最终喷孔的尺寸精度和圆柱度。该方法解决了封闭内型腔油路喷孔的加工难题,避免了内壁孔口毛刺和加工对壁击伤;同时能够精密控制喷孔的尺寸大小,获得良好的内孔圆柱度,重熔层厚度控制在0.01mm以内,满足了主燃级油路喷孔的性能要求;2.长悬深微小直径成型电极在加工时容易产生弯曲,通过分段磨削的步骤,能够获得满足尺寸要求的成型电极,其外径尺寸的波动范围控制在微米级,提高了电极的加工一致性,从而提高了喷口加工的加工精度;3. 对于具有多个喷孔的主燃级喷嘴而言,每个喷孔的加工一致性可以缩小全环燃油供给的流量波动,提高整个发动机燃烧室性能。
[0056]
本发明虽然以上述实施例公开如上,但其并不是用来限定本发明,任何本领域技术人员在不脱离本发明的精神和范围内,都可以做出可能的变动和修改。因此,凡是未脱离本发明技术方案的内容,依据本发明的技术实质对以上实施例所作的任何修改、等同变化及修饰,均落入本发明权利要求所界定的保护范围之内。