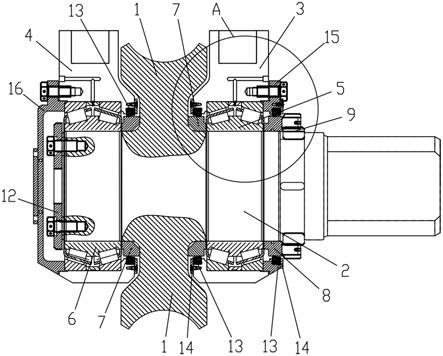
1.本实用新型属于一种用于轧制金属管、金属棒或金属线的连轧机领域,具体涉及一种连轧机轧辊装配结构。
背景技术:2.林州凤宝管业89连轧钢管厂自2017年10月1号热负荷试车至今,连轧机架多次在线发生冒烟问题,造成生产非计划的停机。车间在日常的装配检查过程中,发现轧辊存在内部结构损坏的情况。内部锁紧部件已经出现病态,在很大程度上对生产的顺行造成了影响。为确保生产,轧辊在回装前必须逐个拆解检查内部结构,这一点很大程度上增加了装配组的检查维修工作量。据统计,自2019年元月份开始至10月底,轧辊问题共发生31次,造成生产中断累计时间1056分钟,约18个小时。经过对现场的反复确认和认真分析,认为当前轧辊装配结构上存在诸多不合理处,导致轧辊结构不稳定,频繁出现问题。为了突破瓶颈问题,车间提出对轧辊装配结构进行优化,以提升结构稳定性,保证生产的顺行。
3.目前,轧辊装配主要存在以下几个问题:1、锁紧螺母松动导致轴承内圈移位;2、轴套与轧辊轴之间键条频繁被剪断;3、锁紧螺母防松锁片被撕裂。
4.赛迪原设计轧辊装配结构如图1所示,采用dx474565/dx898675轴承,该型号轴承是铁姆肯公司推出的一款tdo型轴承,包含一个整体式外圈和两个独立内圈,其特点是加宽了轴承的有效支撑间距,具有良好的抗倾覆能力。轧辊两端轴承安装在轴承座中,轴承内圈安装有轴套。轴承座与轴承、轴套一起被安装在轧辊轴上。轴套与轧辊轴设计为大间隙配合,存在0.15~0.22mm设计间隙,且轴套与轧辊轴之间采用键条防转。
5.传动端为固定端,承受主要的轴向轧制负荷,传动端为浮动端,起支撑作用,轴承外圈相对于轴承座可实现轴向5mm的浮动量,以弥补轧辊两端轴承座中心距尺寸的装配误差。轴承与轴套采取分别定为方式,即两端轴承依靠锁紧螺母定位于轴套之上;非传动端轴套依靠轴端压板锁紧与轧辊轴上;传动端轴套靠两半式卡箍固定在轧辊轴上(卡箍下面有垫片,每次装配需配磨厚度以保证卡箍锁紧)。两端外侧透盖将各装配部件进行覆盖密封。
6.在轧辊装配是还存在以下一些问题。
7.1.轧辊装配轴承与轴套分别锁紧,定位方式过于繁琐,且增加了结构出故障的风险。
8.2.卡箍与轴套之间的调整垫片太薄,当轧辊轴与轴套之间键被剪断后,轴套转动,该垫片必然会被撕裂,卡箍锁紧且每次装配需要配磨垫片,不适合现场实际操作,锁紧效果不好。
9.3.通常情况下,轴承在实际轧制过程中轴承内圈所承受的负荷要明显高于外圈,原设计结构采用tdo型独立(双)内圈轴承,为了保证轴承运转过程中两个内圈的同轴度,势必要采用大过盈量来保证两排内圈运转的同步性以及运转的同轴度。这样一来会造成轴承内圈承受轧制工况以外的应力载荷。并且一旦两排内圈发生相对滑动,会直接磨损轴承隔圈,导致轴承轴向游隙得不到保证,缩短轴承寿命。
10.4.锁紧螺母止退锁片不能有效止退,螺母极易出现松动,与透盖发生摩擦,发生冒烟事故,损坏轴承,且由于该部位两端被透盖覆盖,不能及时发现内部锁紧情况。
11.5.一旦锁紧螺母松动退出,靠外侧一列轴承内圈窜出,且轴承不能有效支撑轧辊,导致轴套与轴承座迷宫密封部位发生干涉,损坏相关部件。
12.6.轴套与轧辊轴之间既选用大间隙配合,又使用键条防转,这一设计本意是为了防转,当轴承发生损坏时,使其损坏轴套而保护轧辊不受损坏,但我方认为这一点不符合机械设计常规逻辑,另就现场实际使用效果来看,此设计非但未起到保护轧辊的作用,相反的当键条出现剪断时,会导致轧辊轴被磨损甚至报废不能使用。
13.7.锁紧螺母、卡箍、垫片等部件被透盖整体覆盖,检查内部结构需要拆下两端透盖,并将部件上附着的大量油脂清理后才能操作,过于麻烦,不适合现场频繁批量性作业。同时对润滑脂也是一种浪费。
技术实现要素:14.针对上述现有连轧机轧辊装配存在的技术问题,本实用新型的目的是提供一种连轧机轧辊装配结构。
15.本实用新型的目的是通过以下技术方案实现的。
16.一种连轧机轧辊装配结构,包括轧辊模块,所述轧辊模块包括轧辊和辊轴,还包括:
17.配置所述轧辊模块的前轴承座和后轴承座;
18.配置在前轴承座中的第一轧辊轴承,以及配置在后轴承座中的第二轧辊轴承,所述轧辊通过辊轴、第一轧辊轴承和第二轧辊轴承以可旋转的方式配置在前轴承座和后轴承座中,所述辊轴与第一轧辊轴承和第二轧辊轴承均为间隙配合连接;
19.配置在轧辊两侧的定距环,所述定距环分别与第一轧辊轴承和第二轧辊轴承紧贴;
20.套装于所述辊轴上的轴套,所述轴套与第一轧辊轴承紧贴;
21.套装于所述辊轴上的锁紧件,所述锁紧件与轴套紧贴;
22.配置在第二轧辊轴承侧面的轴端挡板,所述轴端挡板设置在辊轴上。
23.所述第一轧辊轴承和第二轧辊轴承均为tdi型双列圆锥滚子轴承。
24.所述定距环与前轴承座和后轴承座之间均设置有骨架油封,所述前轴承座和后轴承座上均设置有对骨架油封进行限位的限位挡板。
25.所述前轴承座的侧面设置有第一透盖,所述第一透盖与第一轧辊轴承贴紧。
26.所述轴套与第一透盖之间设置有骨架油封,所述第一透盖上设置有对骨架油封进行限位的限位挡板。
27.所述后轴承座的侧面设置有第二透盖,所述第二透盖与第二轧辊轴承贴紧;所述轴端挡板设置在第二透盖与辊轴之间。
28.所述锁紧件包括螺纹卡箍和锁紧螺母,所述螺纹卡箍通过锁紧螺母和梯形螺纹套装于所述辊轴上。
29.本实用新型的有益效果为:与现有连轧机轧辊装配结构相比,本实用新型提供的连轧机轧辊装配结构,装配效率得以明显提升,改进前更换轧辊及轴承完成1架(三辊)3人
配合作业需16小时,改进后同样工作量2人仅需8小时即可完成,节约工时32小时,方便后期日常的保养维护;增强了装配结构的可靠性,减少故障的记录,降低故障几率70%以上;降低了备件成本,每月可减少轴承消耗7-10套、轴承座损耗4-6套、轴套等装配部件7-12套。轧辊损耗880kg、轧辊润滑脂90kg,取得了显著的经济效益。
附图说明
30.图1是本实用新型的结构示意图。
31.图2是图1中a区域的结构放大示意图。
32.图中,1是轧辊,2是辊轴,3是前轴承座,4是后轴承座,5是第一轧辊轴承,6是第二轧辊轴承,7是定距环,8是轴套,9是锁紧件,10是螺纹卡箍,11是锁紧螺母,12是轴端挡板,13是骨架油封,14是限位挡板,15是第一透盖,16是第二透盖。
具体实施方式
33.下面结合附图1和附图2对本实用新型的技术方案进行详细的描述和说明。
34.图1和图2展示了本实用新型连轧机轧辊装配结构的示意图,具体展示了轧辊1、辊轴2、前轴承座3、后轴承座4、第一轧辊轴承5、第二轧辊轴承6、定距环7、轴套8、锁紧件、轴端挡板12、骨架油封13、限位挡板14、第一透盖15和第二透盖16。需要说明的是,图1和图2仅是为了更清楚明白的说明本实用新型的技术方案而作出的结构示意图,并不是对本实用新型技术方案的限定。
35.在本实用新型中,需要说明的是,除非另有明确的规定和限定,术语“安装”、“相连”、“连接”、“设置”应做广义理解,例如,可以是固定相连、设置,也可以是可拆卸连接、设置,或一体地连接、设置,对于本领域的普通技术人员而言,可以根据具体情况理解上述术语在本实用新型中的具体含义。本实用新型中所述的“第一”和“第二”,仅是为了对本实用新型中的部件进行区分,并不是对本实用新型中所使用部件的顺序限定。
36.图1展示了连轧机轧辊装配结构,图2展示了连轧机轧辊装配结构的局部放大示意图。连轧机轧辊用于轧制金属管、棒或线,三个本实用新型的轧辊模块组成一架连轧机;轧辊模块包括轧辊1和辊轴2,辊轴2用于带动轧辊1旋转以轧制金属管、棒或线,轧辊1的端部设置为120度的弧形,三个轧辊1组成一个圆形,用于轧制金属管、棒或线。连轧机轧辊装配结构还包括:前轴承座3、后轴承座4、第一轧辊轴承5和第二轧辊轴承6,前轴承座3和后轴承座4起到安装轧辊模块的作用,作为连轧机的非移动件使用,前轴承座3和后轴承座4上还安装有c型臂,第一轧辊轴承5和第二轧辊轴承6分别安装在前轴承座3和后轴承座4中,轧辊1通过辊轴2、第一轧辊轴承5和第二轧辊轴承6以可旋转的方式安装在前轴承座3和后轴承座4中,辊轴2与第一轧辊轴承5和第二轧辊轴承6均为间隙配合连接,取消了原先的键连接,采用间隙配合连接允许咬钢或抛钢瞬间轴承内圈与辊轴2存在相对蠕动,同时,采用间隙配合连接使辊轴2和轧辊轴承获得必要膨胀变形空间,在辊轴2和轧辊轴承内圈之间还填充有润滑油,减少轧辊轴承内圈的磨损,有利于提升轧辊轴承的使用寿命。辊轴2与外部动力源传动连接,当辊轴2在外部动力源的驱动下旋转时,辊轴2带动轧辊1和轧辊轴承的内圈进行旋转,而前轴承座3、后轴承座4和轧辊轴承的外圈则作为非转动件,允许轧辊1和辊轴2进行旋转,对金属管、棒或线进行轧制。
37.上述的第一轧辊轴承5和第二轧辊轴承6均采用tdi型双列圆锥滚子轴承,现有连轧机轧辊装配结构采用的是tdo型轴承,tdo型轴承具有两个内圈、一个双滚道外圈和一个内隔圈,通过内隔圈宽度来调整轴承轴向游隙;本申请采用的tdi型轴承具有两个外圈、一个内圈和一个外隔圈,通过外隔圈来调整轴承游隙。旋转轧辊轴承类型,需要分析诸多要素,要从各个角度进行全面研究评价,tdi型结构的轧辊轴承205tdi315f在轧辊使用部位、使用条件和实用环境比tdo型轴承结构要适宜,具体如下:1.轴承在运转工作中,内圈承受交变载荷大于外圈,由原来两个内圈变成一个内圈,可同步与轴旋转,提高旋转精度,提高了轧辊轴承的使用寿命;2.轧辊轴承具有一个内圈更便于控制轴向窜动量;3.两个外圈,可分开安装,便于轧辊模块的装配;4.轧辊轴上一个安装面全跳动相互误差小;5.轴承与轧辊轴线方向上中心线误差小;6.按照轴承寿命的理论计算公式计算基本额定动载荷和基本额定定载荷,可以得出:轴承型号为474565/898675d的tdo型轴承的基本额定动载荷cr为881kn,基本额定静载荷cor为2084kn,轴承型号为205tdi315f的tdi型轴承的基本额定动载荷cr为1005kn,基本额定静载荷cor为2173kn,从结果来看,tdi型轴承类型没有tdo型轴长外形尺寸大,但动静荷载比其数值大,如果tdi型轴承空间尺寸等同于tdo型轴承,则tdi型轴承的效果会更好。
38.在轧辊1的两侧设置有定距环7,定距环7分别与第一轧辊轴承5和第二轧辊轴承6紧贴,定位环7用于对第一轧辊轴承5和第二轧辊轴承6进行定位,防止其轴向发生偏移。
39.在轧辊1上设置轴套8和锁紧件,轴套8与第一轧辊轴承5的侧面紧贴,锁紧件与轴套8的侧面紧贴,锁紧件包括螺纹卡箍10和锁紧螺母11,螺纹卡箍10通过锁紧螺母11和梯形螺纹套装于辊轴2上,通过梯形螺纹增强锁紧力。此处的梯形螺纹是指锁紧螺母11和与之配合的螺栓为相互配合的梯形螺纹,梯形螺纹用于传动和位置调整装置中,更适用于本实用新型的连轧机轧辊装配结构。
40.在第二轧辊轴承6的侧面设置轴端挡板12,轴端挡板12用于对第二轧辊轴承6进行限位,轴端挡板12通过螺栓固定设置在辊轴2的侧面上。
41.在定距环7与前轴承座3和后轴承座4之间均设置有骨架油封13,相对应的,在前轴承座3和后轴承座4上均设置有对骨架油封13进行限位的限位挡板14,限位挡板14通过螺钉固定在前轴承座3和后轴承座4上,限位挡板14防止骨架油封13发生位移,使骨架油封13能够起到应有的油封作用。
42.在前轴承座3的侧面设置第一透盖15,第一透盖15与第一轧辊轴承5的外圈紧贴,第一透盖15起到限定第一轧辊轴承5的作用,还具有防尘和密封的作用。在轴套8和第一透盖15之间设置有骨架油封13,在第一透盖15上设置有对骨架油封13进行限位的限位挡板14,限位挡板14通过螺钉固定在第一透盖15上。在轴套8和第一透盖15之间设置骨架油封13的基础上,还可以设置一道防水密封,防水密封与骨架油封13轴向相邻设置,能够增强结构整体密封性,改善进水对润滑油脂的乳化现象。
43.在后轴承座4的侧面设置有第二透盖16,第二透盖16与第二轧辊轴承6的外圈贴紧,第二透盖16起到限定第二轧辊轴承6的作用,还具有防尘和密封的作用。第二透盖16设置为凹字形,凹字形用于容纳轴端挡板12。
44.本实用新型提供的连轧机轧辊装配结构具有如下优点。
45.1.本实用新型改变了轧辊轴承的形式,由原来tdo型轴承改变为tdi型轴承,将轴
向轧制负荷由tdo型轴承的内圈承载改变为tdi型轴承的外圈承载,同时整体式内圈可以保证运转过程中必要的旋转精度。
46.2.保证轧辊宽度、轴径以及相关外部连接尺寸不变的基础上最大限度放大轴承尺寸。
47.3.取消原连轧机轧辊装配结构的键槽防转,且轧辊轴承内圈与轧辊采取间隙配合方式,允许咬钢或抛钢瞬间轧辊轴承内圈与轧辊存在相对蠕动;同时,采用间隙配合使轧辊轴承和辊轴2获得必要的膨胀变形空间。
48.4.配置在前轴承座3的辊轴端为传动端,传动端作为定位端,承受轴向、径向交变轧制载荷;配置在后轴承座4的辊轴端为非传动端,非传动端为浮动端,起到支撑作用,主要承受径向负荷。
49.5.原连轧机轧辊装配结构的轴向卡箍锁紧方式改变为两半环螺母锁紧,采取梯形螺纹锁紧增强锁紧力。
50.本实用新型提供的连轧机轧辊装配结构具有如下的经济效益。
51.每年可减少备件损失费用:
52.3476.92*4*12+936.84*7*12+500*12=251586.72元。
53.每年可减少轴承损坏费用:
54.8*1566*12=150336元。
55.每年可减少润滑脂消耗费用:
56.90*12*24.2=26136元。
57.累计可减少直接经济损失:251586.72+150336+26136=428058.72元。
58.以上所述,仅是本实用新型的优选实施方式,并不是对本实用新型技术方案的限定,应当指出,本领域的技术人员,在本实用新型技术方案的前提下,还可以作出进一步的改进和改变,这些改进和改变都应该涵盖在本实用新型的保护范围内。