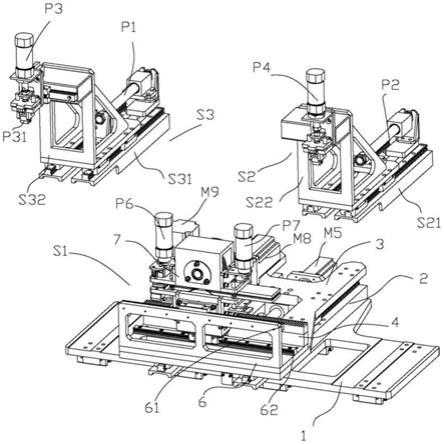
[0001]
本实用新型涉及一种打头机,更确切地说,是一种金属管材或线材的自动打头装置。
背景技术:[0002]
在金属管材或线材的拉伸(铜管拉伸、不锈钢纤维及铝纤维的集束拉伸等),对金属管材或线材的打头(缩径)为必不可少的工序。金属管材或线材的拉伸工艺是使管材或线材通过孔径更小的模头进行挤压和拉伸,往往需要通过多级挤拉达到所设定的尺寸规格。目前行业中实施的打头机都是独立的打头机,通过人工的方式实施各工位的移动和打头,效率低下。
技术实现要素:[0003]
本实用新型主要是解决现有技术所存在的技术问题,从而提供一种金属管材或线材的自动打头装置。
[0004]
本实用新型的上述技术问题主要是通过下述技术方案得以解决的:
[0005]
一种金属管材或线材的自动打头装置,其特征在于,所述的金属管材或线材的自动打头装置包含一打头组件、一第一夹紧组件和一第二夹紧组件,所述的第一夹紧组件和第二夹紧组件分居在所述的打头组件的两侧,
[0006]
所述的打头组件包含一主基板,所述的主基板上设有一对主导轨和一第五电机,所述的主导轨之上设有一可活动的副基板,所述的副基板的前部设有一主齿条和一主支架,所述的主支架上设有一上导向轨条和一下导向轨条,所述的主支架上设有一模头组件,所述的模头组件的一侧设有一第一滑块,所述的模头组件的底部设有一第二滑块,所述的第一滑块与所述的上导向轨条相配合,所述的第二滑块与所述的下导向轨条相配合,
[0007]
所述的模头组件内设有一上压轮、一下压轮、一对上导向板和一对下导向板,所述的上导向板和下导向板相对设置,
[0008]
所述的上压轮的外壁上设有若干环形的上压槽,所述的下压轮的外壁上设有若干环形的下压槽,所述的下压槽与所述的上压槽构成镜面对称,所述的上导向板的内侧壁上设有若干长条状的上导向直槽,所述的下导向板的内侧壁上设有若干长条状的下导向直槽,
[0009]
所述的模头组件的背面设有一上驱动齿轮、一下驱动齿轮和一第八电机,所述的上驱动齿轮与所述的上压轮同轴连接,所述的下驱动齿轮与所述的下压轮同轴连接,所述的上驱动齿轮与下驱动齿轮相互啮合,所述的第八电机驱动所述的下驱动齿轮,所述的下驱动齿轮与所述的主齿条相啮合,
[0010]
所述的模头组件的一侧设有一第六气缸,所述的模头组件的另一侧设有一第七气缸,所述的第六气缸和第七气缸的末端均与对应的上导向板相连接,且所述的第六气缸和第七气缸驱动所对应的上导向板,
[0011]
所述的主基板上还设有一第九电机,
[0012]
所述的第一夹紧组件包含一第一夹紧底座和一第一夹紧支架,所述的第一夹紧支架的顶部设有一第四气缸,所述的第四气缸的末端设有一第四夹线钳,所述的第一夹紧支架与所述的第一夹紧底座的上下接合面通过滑轨滑块相连接,一第二气缸驱动所述的第一夹紧支架前进或后退,
[0013]
所述的第二夹紧组件包含一第二夹紧底座和一第二夹紧支架,所述的第二夹紧支架的顶部设有一第三气缸,所述的第三气缸的末端设有一第三夹线钳,所述的第二夹紧支架与第一夹紧底座的上下接合面通过滑轨滑块相连接,一第一气缸驱动所述的第一夹紧支架前进或后退。
[0014]
本实用新型的金属管材或线材的自动打头装置具有以下优点:本实用新型所采用的滚动模头,通过在模槽内模头的滚动实现对管(线)材均匀的挤压,达到进行拉伸,缩小管(线)径的目的。由于上压轮和下压轮为柱形结构,这种滚动模头上刻多根模槽(模槽的数量和模尺寸与拉伸生产线的级数及各级打头要求相对应)。采用本实用新型的滚动模头较传统的模头,结构更紧凑、生产效率更高。本实用新型机器人与多级拉伸生产线连动后,可实现打头作业的自动化,减少人工作业劳动强度和工作量,提高了产品质量。
附图说明
[0015]
为了更清楚地说明本实用新型实施例或现有技术中的技术方案,下面将对实施例或现有技术描述中所需要使用的附图作简单地介绍,显而易见地,下面描述中的附图仅仅是本实用新型的一些实施例,对于本领域普通技术人员来讲,在不付出创造性劳动的前提下,还可以根据这些附图获得其他的附图。
[0016]
图1为本实用新型的金属管材或线材的自动打头装置的立体结构示意图;
[0017]
图2为图1中的金属管材或线材的自动打头装置的立体结构示意图,为另一个视角;
[0018]
图3为图2中的a区域的细节放大示意图;
[0019]
图4为图2中的金属管材或线材的自动打头装置的立体结构分解示意图;
[0020]
图5为图4中的金属管材或线材的自动打头装置的第一夹紧组件的立体结构示意图;
[0021]
图6为图5中的b区域的细节放大示意图;
[0022]
图7为图4中的金属管材或线材的自动打头装置的进一步的立体结构分解示意图;
[0023]
图8为图7中的c区域的细节放大示意图;
[0024]
图9为图7中的d区域的细节放大示意图;
[0025]
图10为图4中的金属管材或线材的自动打头装置的打头组件的立体结构示意图,为另一个视角;
[0026]
图11为图10中的e区域的细节放大示意图;
[0027]
图12为图4中的金属管材或线材的自动打头装置的打头组件的立体结构示意图,为另一个视角;
[0028]
图13为图12中的f区域的细节放大示意图。
具体实施方式
[0029]
下面结合附图对本实用新型的优选实施例进行详细阐述,以使本实用新型的优点和特征能更易于被本领域技术人员理解,从而对本实用新型的保护范围做出更为清楚明确的界定。
[0030]
如图1至图13所示,该金属管材或线材的自动打头装置s0包含一打头组件s1、一第一夹紧组件s2和一第二夹紧组件s3,该第一夹紧组件s2和第二夹紧组件s3分居在该打头组件s1的两侧。
[0031]
该打头组件s1包含一主基板1,该主基板1上设有一对主导轨2和一第五电机m5,该第五电机m5与丝杆配合。
[0032]
该主导轨2之上设有一可活动的副基板3,该副基板3的前部设有一主齿条 4和一主支架6,该主支架6上设有一上导向轨条61和一下导向轨条62,该主支架6上设有一模头组件7,该模头组件7的一侧设有一第一滑块71,该模头组件7的底部设有一第二滑块72,该第一滑块71与该上导向轨条61相配合,该第二滑块72与该下导向轨条62相配合。
[0033]
该模头组件7内设有一上压轮8、一下压轮9、一对上导向板10和一对下导向板11,该上导向板10和下导向板11相对设置。
[0034]
该上压轮8的外壁上设有若干环形的上压槽81,该下压轮9的外壁上设有若干环形的下压槽91,该下压槽91与该上压槽81构成镜面对称,该上导向板 10的内侧壁上设有若干长条状的上导向直槽101,该下导向板11的内侧壁上设有若干长条状的下导向直槽111。
[0035]
需要说明的是,如果将上压轮8和下压轮9的表面带一定厚度展平,所得的槽孔就是园锥体,园锥体的大头能卡进来线,小头是需要缩小打头的尺寸。该上压轮8和下压轮9切出一个平台,方便穿管(线)材。该上压轮8和下压轮9前进一圈,后退一圈,完成一次打头。后文会进一步加以说明。
[0036]
该模头组件7的背面设有一上驱动齿轮8u、一下驱动齿轮9d和一第八电机 m8,该上驱动齿轮8u与该上压轮8同轴连接,该下驱动齿轮9d与该下压轮9 同轴连接,该上驱动齿轮8u与下驱动齿轮9d相互啮合,该第八电机m8驱动该下驱动齿轮9d,该下驱动齿轮9d与该主齿条4相啮合。
[0037]
该模头组件7的一侧设有一第六气缸p6,该模头组件7的另一侧设有一第七气缸p7,该第六气缸p6和第七气缸p7的末端均与对应的上导向板10相连接,且该第六气缸p6和第七气缸p7驱动所对应的上导向板10。
[0038]
该主基板1上还设有一第九电机m9,该第九电机m9驱动齿轮及工作台设置的齿条导轨配合,实施工位间的移动。
[0039]
该第一夹紧组件s2包含一第一夹紧底座s21和一第一夹紧支架s22,该第一夹紧支架s22的顶部设有一第四气缸p4,该第四气缸p4的末端设有一第四夹线钳p41,该第一夹紧支架s22与该第一夹紧底座s21的上下接合面通过滑轨滑块相连接,该第二气缸p2驱动该第一夹紧支架s22前进或后退。
[0040]
该第二夹紧组件s3包含一第二夹紧底座s31和一第二夹紧支架s32,该第二夹紧支架s32的顶部设有一第三气缸p3,该第三气缸p3的末端设有一第三夹线钳p31,该第二夹紧支架s32与第一夹紧底座s31的上下接合面通过滑轨滑块相连接,该第一气缸p1驱动该第一夹紧支架s32前进或后退。
[0041]
需要说明的是,在主基板1的下方设有工作台(图中未示),工作台上设有工作台导轨(图中未示)和工作台齿条(图中未示)。当第九电机m9转动时,整个自动打头装置在工位间上平移。
[0042]
下面介绍该金属管材或线材的自动打头装置s0的工作方式,包含步骤:
[0043]
1、第三气缸p3和第四气缸p4动作,将夹线钳打开;第六气缸p6和第七气缸p7动作,将模头组件7的对应的导向板10和下导向板11分开;
[0044]
2、将管材拉至打头工位,当给出材料到位信号后,第一气缸p1和第二气缸p2动作,分别推动第三夹线钳p31和第四夹线钳p41前移至工作位,第三气缸p3和第四气缸p4动作,驱动第三夹线钳p31和第四夹线钳p41将线(管) 材夹紧;
[0045]
3、第五电机m5开启,推动丝杆使模头组件7前移,将需打头的线径的卡槽对住已夹持的待加工管材,使之穿入模槽;
[0046]
4、第六气缸p6和第七气缸p7动作,将模头组件7的上导向板10和下导向板11闭合;
[0047]
5、开启第八电机m8,第八电机m8驱动下驱动齿轮9d,下驱动齿轮9d同步驱动主齿条4和上驱动齿轮8u,同时,下驱动齿轮9d带动下压轮9,上驱动齿轮8u带动上压轮8,于是,整个模头组件7开始平移,且下压轮9、上压轮8 同步旋转,当下压轮9、上压轮8旋转一周后停止,完成一次打头;
[0048]
6、第六气缸p6和第七气缸p7动作,将对应的上导向板10和下导向板11分开,第八电机m8反向运转将模头组件7拉回原位。同时在线对线径检测,如果达不到尺寸要求,则重复工步4-6,直至打头达到尺寸要求;
[0049]
7、第三气缸p3和第四气缸p4动作,将线(管)夹头松开;第一气缸p1 和第二气缸p2动作,将第三夹线钳p31和第四夹线钳p41拉回原位。第五电机 m5开启反向,拉动主基板1后撤至原位;
[0050]
8、第九电机m9运转,打头组件s1、第一夹紧组件s2和第二夹紧组件s3 一起平移至下一工位;
[0051]
9、重复步骤2-8,完成本工位打头及移位;
[0052]
10、全部工位完成打头,第九电机m9反向运转,打头组件s1、第一夹紧组件s2和第二夹紧组件s3复位;
[0053]
11、第六气缸p6和第七气缸p7动作,将模头上下模闭合,即对应的上导向板10和下导向板11闭合,第三气缸p3和第四气缸p4动作,将第三夹线钳 p31和第四夹线钳p41闭合。
[0054]
本实用新型所采用的滚动模头,通过在模槽内模头的滚动实现对管(线) 材均匀的挤压,达到进行拉伸,缩小管(线)径的目的。由于上压轮和下压轮为柱形结构,这种滚动模头上刻多根模槽(模槽的数量和模尺寸与拉伸生产线的级数及各级打头要求相对应)。采用本实用新型的滚动模头较传统的模头,结构更紧凑、生产效率更高。本实用新型机器人与多级拉伸生产线连动后,可实现打头作业的自动化,减少人工作业劳动强度和工作量,提高了产品质量。
[0055]
不局限于此,任何不经过创造性劳动想到的变化或替换,都应涵盖在本实用新型的保护范围之内。因此,本实用新型的保护范围应该以权利要求书所限定的保护范围为准。