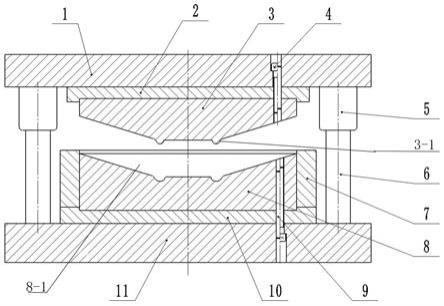
1.本发明涉及膜片弹簧的加工,具体是一种膜片弹簧加工工艺。
背景技术:2.离合器是汽车传动系统的重要部件,膜片弹簧是离合器中重要的压紧元件,在其内孔圆周表面上开有许多均布的长径向槽,在槽的根部制成较大的长圆形或矩形窗孔,可以穿过支承铆钉,这部分称之为分离指;从窗孔底部至弹簧外圆周的部分形状像一个无底宽边碟子,其截面为截圆锥形,称为碟簧部分。
3.目前膜片弹簧,通常采用的加工工艺流程为落料冲中孔
→
冲窗口
→
冲分离指槽
→
挤压窗口圆角
→
压淬成形
→
中温回火
→
分离指高频淬火成形
→
低温回火
→
抛丸
→
检测工序制作完成,工艺流程较多且单一,造成生产效率低,产品精度也不高,指端跳动差,产品合格率低,疲劳寿命缩短,影响到离合器总成的性能。
技术实现要素:4.本发明的目的是为克服现有技术的不足,而提供一种膜片弹簧加工工艺,用该工艺加工,不仅可以减少工序,提高膜片弹簧的生产效率,降低成本并消除累积的误差,提高产品尺寸精度和合格率,延长膜片弹簧使用寿命。
5.实现本发明目的的技术方案是:一种膜片弹簧加工工艺,包括如下步骤:步骤一、将膜片弹簧的原材料落料、冲中孔,即在冲床上同时落出膜片弹簧的外圆形状及冲出中孔形状;步骤二、冲窗口,将步骤一制得的膜片弹簧置于窗口冲床上,冲出窗口形状;步骤三、冲分离指槽,将步骤二冲好窗口的膜片弹簧置于分离指槽冲床上,冲出分离指槽;步骤四、挤压窗口圆角,将步骤三冲好分离指槽的膜片弹簧置于压力机上,通过窗口圆角模具直接一次性挤压出窗口圆角;步骤五、冷压成形,将步骤四挤压好窗口圆角的膜片弹簧置于压力机上,通过冷压成形模具把膜片弹簧的角度和分离指弯钩同时冷压成形;步骤六、淬火,将步骤五冷压成形的膜片弹簧在网带炉中加热,加热温度为860
±
10℃,加热后在油槽中用油冷却;步骤七、中温回火,将步骤六淬火后的膜片弹簧放在网带回火炉中,中温回火,温度为380
±
10℃;步骤八、分离指高频淬火,用高频机对膜片弹簧分离指端进行加热,加热温度为860
±
10℃,加热后用水快速冷却,提高分离指硬度;步骤九、低温回火,温度为200
±
10℃;步骤十、抛丸;
步骤十一、检测。
6.步骤五所述的冷压成形模具,包括上模板、上垫板、成形凸模、导套、导柱、成形凹模抱板、成形凹模、下垫板、下模板;所述成形凸模由长方体和与长方体一体成形的等腰梯形组成,在等腰梯形的上底边与两腰的连接处设有弧形凸起;所述成形凸模根据膜片弹簧的形状设计,成形凸模上的弧形凸起根据膜片弹簧分离指弯钩形状设计,弧形凸起的弧长m=r5~r10mm,r为圆弧半径,弧形凸起的深度h= 4~6 mm,以方便分离指弯钩形状快速形成,不存在干涉;所述成形凹模为长方体,其上表面具有能够与成形凸模的等腰梯形的形状拟合的凹陷部;成形凸模倒置与上模板固定连接,成形凸模与上模板之间设有上垫板;成形凹模固定在下模板上,成形凹模与下模板之间也设有下垫板,成形凹模抱板与成形凹模紧固在一起;上模板和下模板之间通过导套和导柱连接,导套安装于上模板,导柱对应导套安装于下模板。
7.步骤六所述淬火,膜片弹簧加热后只需在油槽中用油冷却,不需要成形模具和液压机。
8.步骤八所述的分离指高频淬火,不需要分离指成形模具和液压机。
9.本发明膜片弹簧加工工艺中,步骤一所用冲床,步骤二所用窗口冲床,步骤三所用分离指槽冲床,步骤四所用窗口圆角模具均为现有技术。
10.本发明膜片弹簧加工工艺中,用冷压成形模具代替现有工艺中的压淬成形,减少了膜片弹簧成形模具、成形设备和压力机,降低了成本,提高膜片弹簧的生产效率;减少多次成形,可消除累积误差,提高产品尺寸精度,提高产品的合格率,膜片弹簧的使用寿命和性能都得到很大的提高。
附图说明
11.图1为本发明膜片弹簧加工工艺中冷压成形模具的结构示意图;图2为图1中成形凸模的结构示意图;图中:上模板1、上垫板2、成形凸模3、弧形凸起3
‑
1、固定螺钉4、导套5、导柱6、成形凹模抱板7、成形凹模8、凹陷部8
‑
1、固定销9、下垫板10、下模板11。
12.图3为膜片弹簧的结构示意图;图中:r1为膜片弹簧的第一角度;r2为膜片弹簧的第二角度;l为分离指弯钩。
具体实施方式
13.下面结合实施例和附图对本发明内容作进一步的说明,但不是对本发明的限定。
实施例
14.一种膜片弹簧加工工艺,包括如下步骤:步骤一、将膜片弹簧的原材料落料、冲中孔,即在冲床上同时落出膜片弹簧的外圆形状及冲出中孔形状;步骤二、冲窗口,将步骤一制得的膜片弹簧置于窗口冲床上,冲出窗口形状;步骤三、冲分离指槽,将步骤二冲好窗口的膜片弹簧置于分离指槽冲床上,冲出分离指槽;步骤四、挤压窗口圆角,将步骤三冲好分离指槽的膜片弹簧置于压力机上,通过窗口圆角模具直接一次性挤压出窗口圆角;步骤五、冷压成形,将步骤四挤压好窗口圆角的膜片弹簧置于压力机上,通过冷压成形模具把膜片弹簧的角度和分离指弯钩同时冷压成形;步骤六、淬火,将步骤五冷压成形的膜片弹簧在网带炉中加热,加热温度为860
±
10℃,加热后在油槽中用油冷却;步骤七、中温回火,将步骤六淬火后的膜片弹簧放在网带回火炉中,中温回火,温度为380
±
10℃;步骤八、分离指高频淬火,用高频机对膜片弹簧分离指端进行加热,加热温度为860
±
10℃,加热后用水快速冷却,提高分离指硬度;步骤九、低温回火,温度为200
±
10℃;步骤十、抛丸;步骤十一、检测。
15.参照图1
‑
3,步骤五所述的冷压成形模具,包括上模板1、上垫板2、成形凸模3、固定螺钉4、导套5、导柱6、成形凹模抱板7、成形凹模8、固定销9、下垫板10、下模板11;成形凸模3由长方体和与长方体一体成形的等腰梯形组成,在等腰梯形的上底边与两腰的连接处设有弧形凸起3
‑
1;成形凸模3根据膜片弹簧的形状设计,如图3所示;成形凸模3上的弧形凸起3
‑
1根据膜片弹簧分离指弯钩l形状设计,弧形凸起3
‑
1的弧长m=r5~r10mm,r为圆弧半径,弧形凸起3
‑
1的深度h= 4~6 mm,如图2所示;成形凹模8为长方体,其上表面具有能够与成形凸模3的等腰梯形的形状拟合的凹陷部8
‑
1;成形凸模3倒置与上模板1通过固定螺钉4固定连接,成形凸模3与上模板11之间设有上垫板2;成形凹模8通过固定销9固定在下模板11上,成形凹模8与下模板11之间设有下垫板10,成形凹模抱板7与成形凹模8紧固在一起,成形凹模抱板7除了保护成形凹模8的作用外,还起到定位作用;上模板1和下模板11之间通过导套5和导柱6连接,导套5安装于上模板1,导柱6对应导套5安装于下模板11。
16.本发明膜片弹簧加工工艺中,用冷压成形模具代替现有工艺中的压淬成形,减少了膜片弹簧成形模具、成形设备和压力机,降低了成本,提高膜片弹簧的生产效率。