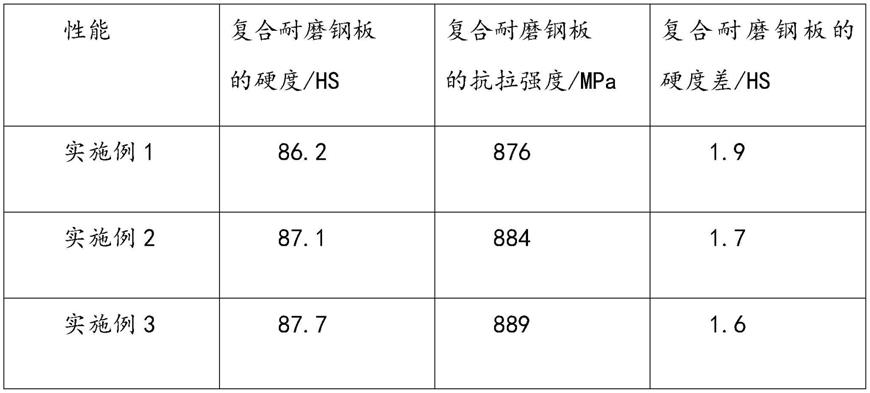
1.本发明涉及钢板轧制技术领域,具体涉及复合耐磨钢板的轧制工艺。
背景技术:2.金属基复合板材的出现和发展,大大地改善及拓展了传统单一金属材料的性能及使用范围。金属基复合板材比传统的单一金属材料有更高的比张度、比刚度和比强度等;其是以一种金属作为基材,以另一种不同物理、化学性能的材料作为复材,并利用复合技术将其进行结合的一种新型复合板材。这对于我国缺乏镍、铬资源的国家来说有着重大意义和社会效益,随着冶金、化工等经济支柱性产业的迅速发展,如矿山机械、煤炭采运、石油化工、建材装饰、船舶工程等对耐磨材料复合板的需求倍增,如矿山机械用轨道、煤炭采用选煤机械、石油天然气输送管道及船体、结构件等,在复合耐磨钢板的生产过程中,钢板轧制是一项必不可少的工序。
3.针对现有技术存在以下问题:
4.1、传统的复合耐磨钢板的轧制工艺,由于采用热压方式对钢板进行压制,但是在对钢板的轧制过程中,无法解决钢板的加热过后容易氧化的问题,从而容易影响后续钢板的轧制工作,进而影响该工艺所轧制出的成品的质量;
5.2、传统的复合耐磨钢板的轧制工艺,钢板回火后的冷却速度较慢,时间较长,无法快速释放钢板回火后的温度,进而达不到提高该复合耐磨钢板的轧制工艺的效率使用初衷,该复合耐磨钢板的轧制工艺的实用性变差,因此需要进行结构创新来解决具体问题。
技术实现要素:6.本发明需要解决的技术问题是提供复合耐磨钢板的轧制工艺,其中一种目的是为了具备防止加热过后的钢板出现氧化的功能,解决传统的复合耐磨钢板的轧制工艺,由于采用热压方式对钢板进行压制,但是在对钢板的轧制过程中,无法解决钢板的加热过后容易氧化的问题;其中另一种目的是为了解决传统的复合耐磨钢板的轧制工艺,钢板回火后的冷却速度较慢,时间较长,无法快速释放钢板回火后的温度的问题,以达到提高该复合耐磨钢板的轧制工艺的效率和实用性的效果。
7.为解决上述技术问题,本发明所采用的技术方案是:
8.复合耐磨钢板的轧制工艺,包括以下步骤,
9.步骤一:将钢板放置到堆板机上进行焊接加热;
10.步骤二:将复合耐磨钢板进行粗轧;
11.步骤三:将粗轧后的复合耐磨钢板进行精轧;
12.步骤四:将精轧工作完成后的钢板进行初次冷却;
13.步骤五:对初次冷却工作完成后的钢板进行淬火;
14.步骤六:对淬火工作完成后的钢板进行回火工作;
15.步骤七:对回火工作完成后的钢板进行二次冷却;
16.步骤八:对钢板进行超声波探伤。
17.本发明技术方案的进一步改进在于:所述步骤一中将钢板放置到堆板机上进行焊接加热时,加热的燃料采用天然气,加热装置的内部均匀设置有多个喷枪口。通过使用天然气为加热燃料,天然气内含有的一氧化碳在燃烧时会产生大量二氧化碳,从而形成保护区,使其隔绝氧气,防止烧制后的钢板在轧制之前与氧气接触二氧化,提高生产出来的钢板的质量。
18.本发明技术方案的进一步改进在于:所述步骤一中将钢板传送加热完成后,需要通过润滑油喷洒装置对加热后的钢板进行润滑油的喷洒。
19.本发明技术方案的进一步改进在于:所述步骤二中将粗轧后的复合耐磨钢板进行粗轧时,粗轧开轧温度为880
‑
940度,粗轧机轧制道次按照8
‑
10道进行控制。
20.本发明技术方案的进一步改进在于:所述步骤三中粗轧后的复合耐磨钢板进行精轧时,精轧开轧温度为800
‑
860度,精轧机轧制道次按照6
‑
9道进行控制。
21.本发明技术方案的进一步改进在于:所述步骤四中将精轧工作完成后的钢板进行初次冷却时,冷却采用acc(加速层流冷却)强水冷工艺,开冷温度780
‑
820度,终冷温度为150
‑
180度。
22.本发明技术方案的进一步改进在于:所述步骤五中对初次冷却工作完成后的钢板进行淬火时,钢板焊接加热时间为1.5
‑
2.0min/mm,快速淬火至室温。
23.本发明技术方案的进一步改进在于:所述步骤七对回火工作完成后的钢板进行二次冷却时,冷却设备内部均匀设置有多个冷却液喷雾口,在钢板回火工作完成的前1
‑
2分钟,需将冷却液喷雾口打开,钢板的回火温度为600
‑
640度,当钢板离开回火设备进入冷却设备时即可保持冷却液喷雾口出液量的稳定。
24.由于采用了上述技术方案,本发明相对现有技术来说,取得的技术进步是:
25.本发明提供复合耐磨钢板的轧制工艺,通过在冷却设备内部均匀设置多个冷却液喷雾口的降温方式,以保证钢板进入冷却设备后能够快速高效的被冷却,能够提高钢板回火后的冷却速度,减少冷却所需要的时间,以达到快速释放钢板回火后的温度的目的,进而提高该复合耐磨钢板的轧制工艺的工作效率和实用性。
具体实施方式
26.下面结合实施例对本发明做进一步详细说明:
27.实施例1
28.本发明提供了复合耐磨钢板的轧制工艺,包括以下步骤,
29.步骤一:将钢板放置到堆板机上进行焊接加热,加热的燃料采用天然气,加热装置内部均匀设置有多个喷枪口,将钢板传送加热完成后,需要通过润滑油喷洒装置对加热后的钢板进行润滑油的喷洒;
30.步骤二:将复合耐磨钢板进行粗轧,粗轧开轧温度为900度,粗轧机轧制道次按照8道进行控制;
31.步骤三:将粗轧后的复合耐磨钢板进行精轧,精轧开轧温度为800
‑
860度,精轧机轧制道次按照7道进行控制;
32.步骤四:将精轧工作完成后的钢板进行初次冷却,冷却采用acc(加速层流冷却)强
水冷工艺,开冷温度780
‑
820度,终冷温度为160度;
33.步骤五:对初次冷却工作完成后的钢板进行淬火,对初次冷却工作完成后的钢板进行淬火时,钢板焊接加热时间为1.5
‑
2.0min/mm,快速淬火至室温;
34.步骤六:对淬火工作完成后的钢板进行回火工作;
35.步骤七:对回火工作完成后的钢板进行二次冷却,冷却设备内部均匀设置有多个冷却液喷雾口,在钢板回火工作完成的前1
‑
2分钟,需将冷却液喷雾口打开,钢板的回火温度为600度,当钢板离开回火设备进入冷却设备时即可保持冷却液喷雾口出液量的稳定;
36.步骤八:对钢板进行超声波探伤。
37.实施例2
38.在实施例1的基础上,本发明提供一种技术方案:包括以下步骤,
39.步骤一:将钢板放置到堆板机上进行焊接加热,加热的燃料采用天然气,加热装置的内部均匀设置有多个喷枪口,将钢板传送加热完成后,需要通过润滑油喷洒装置对加热后的钢板进行润滑油的喷洒;
40.步骤二:将复合耐磨钢板进行粗轧,粗轧开轧温度为910度,粗轧机轧制道次按照9道进行控制;
41.步骤三:将粗轧后的复合耐磨钢板进行精轧,精轧开轧温度为800
‑
860度,精轧机轧制道次按照8道进行控制;
42.步骤四:将精轧工作完成后的钢板进行初次冷却,冷却采用acc(加速层流冷却)强水冷工艺,开冷温度780
‑
820度,终冷温度为170度;
43.步骤五:对初次冷却工作完成后的钢板进行淬火,对初次冷却工作完成后的钢板进行淬火时,钢板焊接加热时间为1.5
‑
2.0min/mm,快速淬火至室温;
44.步骤六:对淬火工作完成后的钢板进行回火工作;
45.步骤七:对回火工作完成后的钢板进行二次冷却,冷却设备内部均匀设置有多个冷却液喷雾口,在钢板回火工作完成的前1
‑
2分钟,需将冷却液喷雾口打开,钢板的回火温度为620度,当钢板离开回火设备进入冷却设备时即可保持冷却液喷雾口出液量的稳定;
46.步骤八:对钢板进行超声波探伤。
47.实施例3
48.在实施例1、实施例2的基础上,本发明提供一种技术方案:优选的,包括以下步骤,
49.步骤一:将钢板放置到堆板机上进行焊接加热,加热的燃料采用天然气,加热装置的内部均匀设置有多个喷枪口,将钢板传送加热完成后,需要通过润滑油喷洒装置对加热后的钢板进行润滑油的喷洒;
50.步骤二:将复合耐磨钢板进行粗轧,粗轧开轧温度为890度,粗轧机轧制道次按照10道进行控制;
51.步骤三:将粗轧后的复合耐磨钢板进行精轧,精轧开轧温度为800
‑
860度,精轧机轧制道次按照9道进行控制;
52.步骤四:将精轧工作完成后的钢板进行初次冷却,冷却采用acc(加速层流冷却)强水冷工艺,开冷温度780
‑
820度,终冷温度为150度;
53.步骤五:对初次冷却工作完成后的钢板进行淬火,对初次冷却工作完成后的钢板进行淬火时,钢板焊接加热时间为1.5
‑
2.0min/mm,快速淬火至室温;
54.步骤六:对淬火工作完成后的钢板进行回火工作;
55.步骤七:对回火工作完成后的钢板进行二次冷却,冷却设备内部均匀设置有多个冷却液喷雾口,在钢板回火工作完成的前1
‑
2分钟,需将冷却液喷雾口打开,钢板的回火温度为600度,当钢板离开回火设备进入冷却设备时即可保持冷却液喷雾口出液量的稳定;
56.步骤八:对钢板进行超声波探伤。
57.复合耐磨钢板的力学性能见下表:
[0058][0059]
本发明所提供的复合耐磨钢板的轧制工艺的有益效果为:
[0060]
本发明通过在冷却设备内部均匀设置多个冷却液喷雾口的降温方式,在钢板回火工作完成之前,就对冷却液喷雾口进行开启,以保证钢板进入冷却设备后能够快速高效的被冷却,能够提高钢板回火后的冷却速度,减少冷却所需要的时间,以达到快速释放钢板回火后的温度的目的,进而提高该复合耐磨钢板的轧制工艺的工作效率和实用性。
[0061]
上文一般性的对本发明做了详尽的描述,但在本发明基础上,可以对之做一些修改或改进,这对于技术领域的一般技术人员是显而易见的。因此,在不脱离本发明思想精神的修改或改进,均在本发明的保护范围之内。