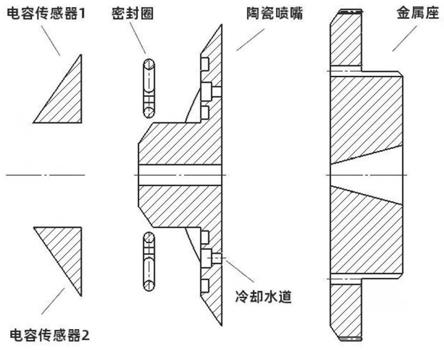
1.本发明涉及嵌入式控制器技术领域,具体涉及一种基于电容原理的双光束激光焊接喷嘴和焊缝自动跟踪系统。
背景技术:2.航空航天结构件中常见的壁板类结构件主要由蒙皮与内部加强筋组成。此类带筋壁板结构件一般采用铆接或者电阻点焊实现蒙皮与立筋之间的连接。这两传统的连接方法不仅劳动强度大,结构强度不高而且会对蒙皮的整体完整性造成损伤。
3.激光焊接制造壁板类结构件是近几年发展起来的先进制造技术,其中的双光束焊接方法具有效率高、变形小、接头质量好等优点。双光束焊接方法就是采用两束激光从立筋两侧同步施焊,如图1所示。采用激光双光束从t型接头的两侧同步进行焊接形成角焊缝,有利于立筋与蒙皮的熔合,而且对蒙皮背面没有损伤。一般认为,采用双光束焊接工艺可以使得t型接头的两侧受热均匀,有利于控制变形。另外,由于两束激光同时焊接,在熔池的交互作用下可以减小热输入产生1+1>2的效果,同时熔池的交互作用有利于立筋与底板处结合面的熔合,利于气孔的逸出。
4.采用双光束焊接技术将立筋焊接在蒙皮(底板)上,如图2所示。采用双光束焊接技术后,与传统的铆接壁板相比由于取消了底边处的翻边结构,双光束焊接结构整体减重16%。筋条与蒙皮之间的连接原来为局部点焊连接,改为双光束焊接后筋条与蒙皮之间为满焊连接,其强度提高4倍以上。传统的铆接或者电阻点焊连接完成后,会在蒙皮(底板)气动面留下深度为0.3mm的凹坑严重影响整体结构完整性与隐身性。采用双光束焊接这种t型结构,可以有效防止蒙皮(底板)气动面的损伤,蒙皮外表面凸起或凹陷不超过0.1mm为光滑型面,电磁辐射与铆接结构相比降低50%以上,实现了钛合金壁板制造的轻量化、高强化、隐身化。
5.但是激光双光束焊接过程中,由于两束激光入射角度的影响以及两侧熔池的互相扰动,使得焊缝内部极易产生气孔、未熔合等缺陷,严重影响焊接质量。
6.采用激光焊接“t”型接头类型的结构时,激光双光束从t型接头的两侧同时进行焊接形成角焊缝,有利于立筋与底板间的熔合,而且对底板背面没有损伤。一般认为,采用激光双光束焊接工艺可以使得t型接头的两侧受热均匀,有利于控制变形。两束激光同时焊接在熔池的交互作用下可以减小热输入,产生1+1>2的效果。
7.现有的双光束激光焊接壁板类结构件,不论采用双机器人平台的加工方式还是龙门式的焊接平台,焊接工人在进行焊接作业时,都采用逐点示教的方式将激光准直光对准焊缝中心记录坐标点,采用连点成线的方式生成焊接路径。这种方法精度较差,效率极低,一般靠目视作业,工作量也极大、工人劳动强度很高。而且提高对中精度的方式,只能对示教点进行加密,从而进一步增加工作量。众所周知,激光焊接以其高效的焊接速率著称。目前的焊接示教过程,占整个焊接过程的90%以上,焊接时间往往只有几秒钟至几十秒钟。因此,采用焊接示教方法对焊缝进行对中,严重影响了工作效率,迫切需要一种自动对中方式
及装置来实现对焊接示教的自动化对中。
8.现有焊接具有焊接速度快,焊接头与拼缝对中精度要求高的特点,给拼缝检测带来很大困难,目前采用激光线结构加一个工业相机的方式,通过三角测量法实现拼缝检测,存在的突出问题是测量装置在激光焊接头前面大约100-150mm处,在激光填丝焊接的情况下,由于送丝装置和拼缝检测装置都安装在激光焊接头的前面,为防止送丝装置的干扰必须将检测装置的安装位置继续提前,导致响应检测信号的延时比较大,系统相应难度增大。
技术实现要素:9.为了解决传统焊接由于送丝装置和拼缝检测装置都安装在激光焊接头的前面,t型焊缝两边的激光焊接头位置无法准确对准的问题。为此,本发明实施例提供一种基于电容原理的双光束激光焊接焊缝自动跟踪系统,该装置应用于激光焊接“t”型拼缝检测,将电容传感器安装在焊接喷嘴上以同步获取焊接喷嘴的位置信息,解决了激光焊接"t"型焊缝自动对焦的问题。同时避免时延处理带来的系统响应问题,从而导致的影响焊接质量的问题。其具体技术方案如下:
10.为实现上述目的,本发明实施例的第一方面提供一种基于电容原理的双光束激光焊接喷嘴,包括陶瓷喷嘴、安装在所述陶瓷喷嘴两侧的第一电容传感器和第二电容传感器;所述第一电容传感器和第二电容传感器之间绝缘设置;所述第一电容传感器和第二电容传感器用于分别同步采集传感器与喷嘴之间的第一电容值和第二电容值,并由mcu控制器对所述第一电容值和第二电容值对应的位置进行计算,得到位置调整增量,并根据所述位置增量控制电机调整喷嘴的位置。
11.进一步的,还包括用于为所述第一电容传感器和第二电容传感器进行冷却的水槽,在所述喷嘴的背部还安装有金属座;所述第一电容传感器和第二电容传感器由紫铜制成,传感器后面加装绝缘垫。
12.本发明实施例的第二方面提供一种基于电容原理的双光束激光焊接焊缝自动跟踪系统,包括:
13.mcu控制器、与所述mcu控制器连接的参数设定及监控平台、伺服电机驱动器以及电容检测装置;与所述mcu控制器和所述伺服电机驱动器均相连的电机、滚珠丝杠滑台、焊接喷嘴,所述电容检测装置通过电容传感器安装在焊接喷嘴上。
14.进一步的,将所述电容传感器与所述焊接喷嘴按照预设角度固定,并进行标定。
15.进一步的,还包括在所述电容传感器的下端安装水套。
16.进一步的,还包括:pwm信号调制模块和差分转换模块;所述电容传感器采集的信号通过pwm信号调制模块进行调制后发送至所述差分转换模块进行差分转换得到差分转换数据,输入至所述mcu控制器,所述mcu控制器根据所述差分转换数据控制所述伺服电机驱动器,进而控制所述伺服电机。
17.进一步的,所述伺服控制模块包括与所述mcu控制器相连的磁隔离、光耦隔离,与所述磁隔离和所述伺服控制器接口连接的d/a转换模块,所述差分模块还分别于所述光耦隔离和所述伺服控制器接口连接,电平转换模块分别与所述光耦隔离和所述伺服控制器接口连接。
18.进一步的,还包括人机交互模块,所述人机交互模块通过io接口或通用工控数据
传输线连接;所述人机交互模块包括指示灯、触摸屏、启动按钮和急停按钮。
19.进一步的,所述mcu控制器采用stm32f427。
20.本发明实施例提供一种基于电容原理的双光束激光焊接喷嘴,包括陶瓷喷嘴、安装在所述陶瓷喷嘴两侧的第一电容传感器和第二电容传感器;所述第一电容传感器和第二电容传感器之间绝缘设置;所述第一电容传感器和第二电容传感器用于分别同步采集传感器与喷嘴之间的第一电容值和第二电容值,并由mcu控制器对所述第一电容值和第二电容值对应的位置进行计算,得到位置调整增量,并根据所述位置增量控制电机调整喷嘴的位置。解决了激光焊接"t"型焊缝自动对焦的问题。
21.本发明的第二方面提供一种基于电容原理的双光束激光焊接焊缝自动跟踪系统,包括:mcu控制器、与所述mcu控制器连接的参数设定及监控平台、伺服电机驱动器以及电容检测装置;与所述mcu控制器和所述伺服电机驱动器均相连的伺服控制模块,依次相连的伺服电机、滚珠丝杠滑台、焊接喷嘴,所述电容检测装置通过电容传感器安装在焊接喷嘴上。该装置应用于激光焊接“t”型拼缝检测,将电容传感器安装在焊接喷嘴上以同步获取焊接喷嘴的位置信息,避免时延处理带来的系统响应问题,从而导致的影响焊接质量的问题。
附图说明
22.图1是现有技术中双光束焊接的结构示意图;
23.图2是采用双光束焊接技术将立筋焊接在蒙皮上的示意图;
24.图3是本发明实施例提供的基于电容原理的双光束激光焊接喷嘴的结构示意图;
25.图4是本发明实施例提供的基于电容原理的双光束激光焊接喷嘴的控制结构示意图;
26.图5是本发明实施例提供的基于电容原理的双光束激光焊接焊缝自动跟踪系统的结构示意图。
具体实施方式
27.以下结合附图对本发明进行说明,但不用来限制本发明的范围。
28.参见图3是本发明实施例提供的基于电容原理的双光束激光焊接喷嘴包括:陶瓷喷嘴、安装在所述陶瓷喷嘴两侧的第一电容传感器和第二电容传感器;所述第一电容传感器和第二电容传感器之间相互绝缘。参见图4,是本发明实施例提供的一种基于电容原理的双光束激光焊接喷嘴的控制结构示意图,包括:主控芯片stm32f427、用于采集两个电容型位移传感器的电容值、并将处理后的电容值转换成pwm信号传送给主控芯片的电容数字转换芯片pcap01,通信模块,所述通信模块的主控芯片采用et1200,et1200是ethercat总线从站通讯模块芯片,主控芯片将接收到的pwm信号处理成为ethercat报文数据包,并发送到ethercat总线上,机器人通过ethercat总线接收到报文数据包后,逆向解码,得到两个方向上的位置偏移量,根据这两个位置偏移量,对焊接轨迹进行调整,实现焊缝跟踪,解决了激光焊接"t"型焊缝自动对焦的问题。
29.上述第一电容传感器和第二电容传感器也可称为电容传感器1和电容传感器2。
30.进一步的,在本发明实施例的具体实施方式中,电容传感器由紫铜制成,背部有一层绝缘材料,安装在陶瓷喷嘴上,陶瓷喷嘴内部开有水槽,通过冷却水循环,保证焊接过程
中电容传感器的温度恒定,两个电容传感器互相之间绝缘。
31.本发明采用基于电容原理的双光束激光焊接喷嘴,将两套电容型位移传感器安装在激光焊接喷嘴上,为确保两套电容型位移传感器之间的绝缘性,专门设计了陶瓷激光焊接喷嘴,电容型位移传感器由紫铜制成,后面加装绝缘垫,由于电容型位移传感器精度受温度影响,而焊接过程中的反射光、等离子体、熔池热辐射等因素会造成电容型位移传感器,所以在陶瓷激光焊接喷嘴上面开有水槽,通过冷却水给电容型位移传感器降温,确保测量精度。焊接前,应调整激光焊接喷嘴的角度,确保两个激光焊接喷嘴正对着“t”型焊缝的两边。传感器输出的两路模拟量也要确保对应无误。
32.参见4和图5,图5是本发明的第二方面提供一种基于电容原理的双光束激光焊接焊缝自动跟踪系统的结构示意图,一种基于电容原理的双光束激光焊接焊缝自动跟踪系统,包括:mcu控制器、与所述mcu控制器连接的参数设定及监控平台、伺服电机驱动器以及电容检测装置;与所述mcu控制器和所述伺服电机驱动器均相连的伺服控制模块,依次相连的伺服电机、滚珠丝杠滑台、焊接喷嘴,所述电容检测装置通过电容传感器安装在焊接喷嘴上。
33.在本发明中,上述焊接喷嘴安装在切割头中,现有技术中,切割头包括焊接喷嘴、聚焦透镜和聚焦跟踪系统等。
34.上述电容传感器与所述焊接喷嘴按照预设角度固定,并进行标定。标定的目的是确保测量的精度和线性信号输出,标定成功后,只要不更换喷嘴、放大器、控制系统就不需要再进行标定。
35.工作时,双光束激光焊接焊缝自动跟踪系统的两个电容传感器同步采集电容传感器与待焊接零件(如图中的凹凸不平的板材)之间的电容值,经过电容数字转换,获得相应的位置模拟量值,经过与预设的位置值进行对比,获得位置调整的两路增量值,对应喷嘴与“t”型焊缝的间隙,伺服电机据此进行位置调整。
36.在本发明实施例的可选实施方式中,为了避免焊接时热辐射、飞溅物和反射光损坏传感器,在所述电容传感器的下端设置有水套。
37.在本发明的可选实施方式中,系统还包括pwm信号调制模块和差分转换模块;所述电容传感器采集的信号通过pwm信号调制模块进行调制后发送至所述差分转换模块进行差分转换得到差分转换数据,输入至所述mcu控制器,所述mcu控制器根据所述差分转换数据控制所述伺服电机驱动器,进而控制所述伺服电机。
38.在本发明的可选实施方式中,所述伺服控制模块包括与所述mcu控制器相连的磁隔离、光耦隔离,与所述磁隔离和所述伺服控制器接口连接的d/a转换模块,所述差分模块还分别于所述光耦隔离和所述伺服控制器接口连接,电平转换模块分别与所述光耦隔离和所述伺服控制器接口连接。
39.在本发明的可选实施方式中,还包括人机交互模块,所述人机交互模块通过io接口或通用工控数据传输线连接;所述人机交互模块包括指示灯、触摸屏、启动按钮和急停按钮。
40.用户可在所述人机交互模块对所述系统进行操作和控制。上述mcu控制器采用stm32系列芯片,可以为stm32f427或stm32f407。
41.本发明实施例提供一种基于电容原理的双光束激光焊接焊缝自动跟踪系统,包
括:mcu控制器、与所述mcu控制器连接的参数设定及监控平台、伺服电机驱动器以及电容检测装置;与所述mcu控制器和所述伺服电机驱动器均相连的伺服控制模块,依次相连的伺服电机、滚珠丝杠滑台、焊接喷嘴,所述电容检测装置通过电容传感器安装在焊接喷嘴上。该装置应用于激光焊接“t”型拼缝检测,将电容传感器安装在焊接喷嘴上以同步获取焊接喷嘴的位置信息,避免时延处理带来的系统响应问题,从而导致的影响焊接质量的问题。
42.虽然,上文中已经用一般性说明及具体实施例对本发明作了详尽的描述,但在本发明基础上,可以对之作一些修改或改进,这对本领域技术人员而言是显而易见的。因此,在不偏离本发明精神的基础上所做的这些修改或改进,均属于本发明要求保护的范围。