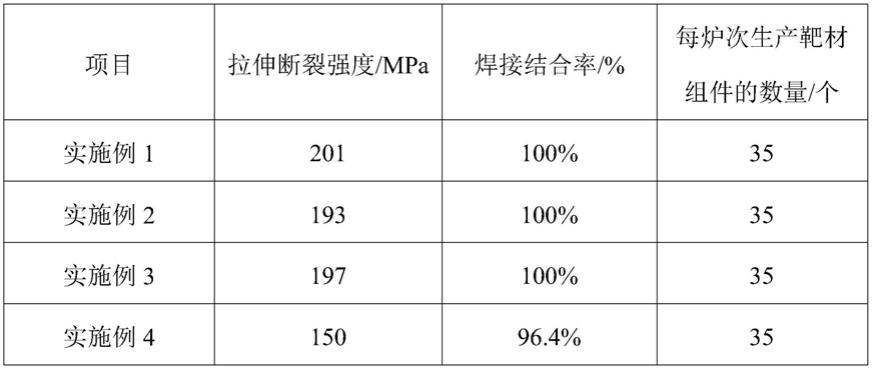
1.本发明属于靶材制备技术领域,具体涉及一种靶材组件的焊接方法。
背景技术:2.靶材组件是磁控溅射过程中的常用物料,其中靶材组件由靶材和背板焊接而成,焊接所用方法通常为扩散焊接的方法。
3.扩散焊接为现有技术常用的一种焊接靶材的方法,扩散焊接的原理为在一定温度和压力下保持一段时间使接触面之间的原子相互扩散,形成联结的焊接方法。靶材在扩散焊接过程中,为了增加扩散层接触面积以及降低焊接面氧化层对焊接的不利影响,一般会在较硬的材料上车螺纹。但是实际中很多材料在扩散焊接后,螺牙未能填满,出现内部焊接质量缺陷,尤其是在靶材和背板硬度相当的时候,例如无氧铜背板、铜合金背板与铜靶材,铝合金背板与铝靶材。
4.cn110421246b公开了一种背板与高纯金属靶材的扩散焊接方法,所述扩散焊接方法包括如下步骤:准备高纯金属靶材与背板,并在背板的焊接面上加工螺纹;组合高纯金属靶材与背板,并将组合材料放置于金属包套中;对装入组合材料的金属包套进行脱气处理,然后将金属包套进行密封;冷等静压密封后的金属包套;对冷等静压处理后的金属包套进行热等静压处理,然后冷却至室温;去除金属包套,完成背板与高纯金属靶材的扩散焊接。该方法通过对组合材料先进行冷等静压处理,再进行热等静压处理,克服了热等静压在低温下达不到工艺压力的缺点,从而保证了螺纹的嵌入效果。然而,该方式应用面比较窄,针对硬度相差较大的材料效果较好,针对靶材和背板硬度相差不大的两种材料,实际效果并不理想。冷态下对硬度相差不大(比如硬度差<50%)的背板和靶材进行冷等静压,因为两者本身硬度相差不大,且硬度大的材料上加工螺纹,使得螺纹处材料强度降低,因此在冷态下加压会导致螺牙弯曲或者是螺牙嵌入不良的情况,甚至会出现螺牙在200mpa以上的压力下被完全压平而无法嵌入的情况。
5.cn110369897b公开了一种靶材与背板的焊接方法,所述方法包括如下步骤:准备靶材与背板,在硬度较高的材料的焊接面上加工螺纹;组合靶材与背板,并将组合材料放置于金属包套中;对装入组合材料的金属包套进行脱气处理,然后将金属包套进行密封;加热密封后的金属包套至第一温度,然后加压至第一压力,随后加热至第二温度,压力随温度升高至第二压力,保温保压后冷却至室温;去除金属包套,完成靶材与背板的焊接。该方法通过先升温再加压的方法,使螺纹更好地嵌入到硬度较小的材料中,提高了焊接面的接触面积,并能够破坏焊接面的氧化层,减少了氧化层对扩散焊接的阻挡作用,提升了焊接强度。然而,此方法针对硬度相差不大(比如硬度差<50%)的背板和靶材效果不佳。硬度相差不大的两种材料,在升温时,同样的都会因为温度升高而降低硬度,实际硬度降低会有一定的效果,但效果并不理想,绝大部分的硬度相近的材料是无法通过此方法彻底解决焊接不良问题的。
6.因此,需要提供一种新的靶材焊接方法,保证靶材与背板之间的焊接强度,提高生
产效率。
技术实现要素:7.本发明的目的在于提供一种靶材组件的焊接方法,将靶材和背板依次进行摩擦焊接和热等静压焊接,得到靶材组件;本发明通过在热等静压焊接前增加摩擦焊接的工艺来实现靶材和背板的预焊接,可以有效的破坏焊接面氧化层,增大焊接的可靠性,将摩擦焊接与热等静压焊接相结合,提高了靶材与背板之间的焊接强度,且生产效率高,由于摩擦焊接后焊接面已经形成接触面,所以热等静压时不需要将每个靶材单独进行包套,降低成本,简化流程,应用广。
8.为达到此发明目的,本发明采用以下技术方案:
9.本发明的目的在于提供一种靶材组件的焊接方法,所述焊接方法包括如下步骤:将靶材和背板依次进行摩擦焊接和热等静压焊接,得到靶材组件。
10.本发明通过在热等静压焊接前增加摩擦焊接的工艺来实现靶材和背板的预焊接,可以有效的破坏焊接面氧化层,增大焊接的可靠性,增强焊接强度。摩擦焊接是利用工件接触面摩擦产生的热量为热源,使工件在压力作用下产生塑性变形而进行焊接的方法;热等静压焊接是一种在高温下利用各项均等的静压力进行压制的工艺方法,该方法集热压和等静压的优点于一身,成形温度低,产品致密,性能优良。本发明所述的靶材焊接方法将摩擦焊接与热等静压焊接相结合,提高了靶材与背板之间的焊接强度,且生产效率高,由于摩擦焊接后焊接面已经形成接触面,所以热等静压时不需要将每个靶材单独进行包套,降低成本,简化流程,应用广。
11.值得说明的是,所述靶材组件包括铜靶材组件、铝靶材组件、钛靶材组件或钽靶材组件。
12.作为本发明优选的技术方案,在所述摩擦焊接之前,将所述靶材和所述背板依次进行车削和清洗。
13.优选地,所述清洗使用的清洗剂包括乙醇。
14.作为本发明优选的技术方案,所述车削之前,在所述靶材和所述背板上分别预留5-10mm的加工余量,例如可以是5mm,5.5mm,6mm,6.5mm,7mm,7.5mm,8mm,8.5mm,9mm,9.5mm,10mm等,但并不仅限于所列举的数值,上述数值范围内其他未列举的数值同样适用。
15.作为本发明优选的技术方案,所述摩擦焊接的压力为10-50mpa,例如可以是10mpa,15mpa,20mpa,25mpa,30mpa,35mpa,40mpa,45mpa,50mpa等,但并不仅限于所列举的数值,上述数值范围内其他未列举的数值同样适用。
16.作为本发明优选的技术方案,所述摩擦焊接的时间为10-40s,例如可以是10s,12s,15s,18s,20s,23s,25s,28s,30s,32s,35s,37s,40s等,但并不仅限于所列举的数值,上述数值范围内其他未列举的数值同样适用。
17.作为本发明优选的技术方案,所述摩擦焊接的转速为0.5-2m/s,例如可以是0.5m/s,0.7m/s,0.9m/s,1m/s,1.2m/s,1.4m/s,1.5m/s,1.6m/s,1.8m/s,2m/s等,但并不仅限于所列举的数值,上述数值范围内其他未列举的数值同样适用。
18.优选地,所述摩擦焊接在摩擦焊机床上进行。
19.值得说明的是,在摩擦焊接时,所述靶材与所述背板的待焊面相对放置,并逐渐靠
近,其中,所述靶材与所述背板中至少一端进行旋转。
20.作为本发明优选的技术方案,所述热等静压焊接的压力为100-180mpa,例如可以是100mpa,105mpa,110mpa,115mpa,120mpa,125mpa,130mpa,135mpa,140mpa,145mpa,150mpa,155mpa,160mpa,165mpa,170mpa,175mpa,180mpa等,但并不仅限于所列举的数值,上述数值范围内其他未列举的数值同样适用。
21.作为本发明优选的技术方案,所述热等静压焊接的温度200-800℃,例如可以是200℃,250℃,300℃,350℃,400℃,450℃,500℃,550℃,600℃,650℃,700℃,750℃,800℃等,但并不仅限于所列举的数值,上述数值范围内其他未列举的数值同样适用。
22.作为本发明优选的技术方案,所述热等静压焊接的时间为2-4h,例如可以是2h,2.1h,2.2h,2.3h,2.4h,2.5h,2.6h,2.7h,2.8h,2.9h,3h,3.1h,3.2h,3.3h,3.4h,3.5h,3.6h,3.7h,3.8h,3.9h,4h等,但并不仅限于所列举的数值,上述数值范围内其他未列举的数值同样适用。
23.优选地,所述热等静压焊接在热等静压机中进行。
24.作为本发明优选的技术方案,所述焊接方法包括如下步骤:
25.(1)将靶材和背板预留5-10mm加工余量,进行车削,而后使用乙醇将其清洗干净,在转速0.5-2m/s、压力10-50mpa的条件下进行摩擦焊接10-40s;
26.(2)在压力100-180mpa、温度200-800℃的条件下进行热等静压焊接2-4h,得到靶材组件。
27.本发明所述的数值范围不仅包括上述例举的点值,还包括没有例举出的上述数值范围之间的任意的点值,限于篇幅及出于简明的考虑,本发明不再穷尽列举所述范围包括的具体点值。
28.相对于现有技术,本发明具有以下有益效果:
29.(1)本发明所述的靶材焊接方法在热等静压焊接前增加摩擦焊接的工艺来实现靶材和背板的预焊接,可以有效的破坏焊接面氧化层,增大焊接的可靠性;
30.(2)本发明所述的靶材焊接方法将摩擦焊接与热等静压焊接相结合,提高了靶材与背板之间的焊接强度,且生产效率高;
31.(3)本发明所述的靶材焊接方法中,由于摩擦焊接后焊接面已经形成接触面,所以热等静压时不需要将每个靶材单独进行包套,降低成本,简化流程,应用广。
具体实施方式
32.下面通过具体实施方式来进一步说明本发明的技术方案。本领域技术人员应该明了,所述实施例仅仅是帮助理解本发明,不应视为对本发明的具体限制。
33.实施例1
34.本实施例提供了一种钽靶材组件的焊接方法,所述焊接方法包括如下步骤:
35.(1)将钽靶材和钽背板预留10mm加工余量,进行车削,而后使用乙醇将其清洗干净,在转速2m/s、压力30mpa的条件下进行摩擦焊接25s;
36.(2)在压力100mpa、温度800℃的条件下进行热等静压焊接2h,得到钽靶材组件。
37.实施例2
38.本实施例提供了一种钛靶材组件的焊接方法,所述焊接方法包括如下步骤:
39.(1)将钛靶材和钛背板预留5mm加工余量,进行车削,而后使用乙醇将其清洗干净,在转速0.5m/s、压力50mpa的条件下进行摩擦焊接10s;
40.(2)在压力150mpa、温度450℃的条件下进行热等静压焊接4h,得到钛靶材组件。
41.实施例3
42.本实施例提供了一种铜靶材组件的焊接方法,所述焊接方法包括如下步骤:
43.(1)将铜靶材和铜背板预留8mm加工余量,进行车削,而后使用乙醇将其清洗干净,在转速1m/s、压力10mpa的条件下进行摩擦焊接40s;
44.(2)在压力180mpa、温度200℃的条件下进行热等静压焊接4h,得到铜靶材组件。
45.实施例4
46.本实施例提供了一种钽靶材组件的焊接方法,参照实施例1所述的焊接方法,区别仅在于:摩擦焊接的转速为0.2m/s;即,所述焊接方法包括如下步骤:
47.(1)将钽靶材和钽背板预留10mm加工余量,进行车削,而后使用乙醇将其清洗干净,在转速0.2m/s、压力30mpa的条件下进行摩擦焊接25s;
48.(2)在压力100mpa、温度800℃的条件下进行热等静压焊接2h,得到钽靶材组件。
49.实施例5
50.本实施例提供了一种钽靶材组件的焊接方法,参照实施例1所述的焊接方法,区别仅在于:摩擦焊接的转速为2.5m/s;即,所述焊接方法包括如下步骤:
51.(1)将钽靶材和钽背板预留10mm加工余量,进行车削,而后使用乙醇将其清洗干净,在转速2.5m/s、压力30mpa的条件下进行摩擦焊接25s;
52.(2)在压力100mpa、温度800℃的条件下进行热等静压焊接2h,得到钽靶材组件。
53.实施例6
54.本实施例提供了一种钽靶材组件的焊接方法,参照实施例1所述的焊接方法,区别仅在于:热等静压焊接的温度为150℃;即,所述焊接方法包括如下步骤:
55.(1)将钽靶材和钽背板预留10mm加工余量,进行车削,而后使用乙醇将其清洗干净,在转速2m/s、压力30mpa的条件下进行摩擦焊接25s;
56.(2)在压力100mpa、温度150℃的条件下进行热等静压焊接2h,得到钽靶材组件。
57.实施例7
58.本实施例提供了一种钽靶材组件的焊接方法,参照实施例1所述的焊接方法,区别仅在于:热等静压焊接的温度为850℃;即,所述焊接方法包括如下步骤:
59.(1)将钽靶材和钽背板预留10mm加工余量,进行车削,而后使用乙醇将其清洗干净,在转速2m/s、压力30mpa的条件下进行摩擦焊接25s;
60.(2)在压力100mpa、温度850℃的条件下进行热等静压焊接2h,得到钽靶材组件。
61.对比例1
62.本对比例提供了一种钽靶材组件的焊接方法,参照实施例1所述的焊接方法,区别仅在于:未进行摩擦焊接;即,所述焊接方法包括如下步骤:
63.(1)将钽靶材和钽背板预留10mm加工余量,进行车削,而后使用乙醇将其清洗干净,在钽背板上加工螺纹,组合钽靶材与加工螺纹后的钽背板,并将组合材料放置于金属包套中,对装入组合材料的金属包套进行脱气处理,然后将金属包套进行密封;
64.(2)在压力100mpa、温度850℃的条件下进行热等静压焊接2h,得到钽靶材组件。
65.对比例2
66.本对比例提供了一种钽靶材组件的焊接方法,参照实施例1所述的焊接方法,区别仅在于:采用轴向静压焊接替代热等静压焊接;即,所述焊接方法包括如下步骤:
67.(1)将钽靶材和钽背板预留10mm加工余量,进行车削,而后使用乙醇将其清洗干净,在钽背板上加工螺纹,组合钽靶材与加工螺纹后的钽背板,并将组合材料放置于金属包套中,对装入组合材料的金属包套进行脱气处理,然后将金属包套进行密封;
68.(2)在压力10mpa、温度850℃的条件下进行轴向静压焊接2h,得到钽靶材组件。
69.(一)将上述实施例与对比例所得靶材进行焊接强度测试,所述测试方法包括如下步骤:
70.采用bg/t 39163-2020《靶材与背板结合强度测试方法》中所述的方法测试拉伸断裂强度,即为焊接强度。
71.将上述实施例与对比例焊拉伸断裂强度测试的结果列于表1。
72.(二)将上述实施例与对比例所得靶材进行焊接结合率测试,所述测试方法包括如下步骤:使用超声波探伤仪来检测靶材和背板的焊接结合率,单位为%。
73.将上述实施例与对比例焊接结合率的测试结果列于表1。
74.(三)将上述实施例与对比例所述的焊接方法进行生产效率测试,所述测试方法包括如下步骤:
75.在d620
×
1500mm的静压炉中进行扩散焊接,记录每炉次生产的靶材组件的数量,以生产数量来评判生产效率,数量越多,生产效率越高。
76.将上述实施例与对比例每炉次生产钽靶材组件的数量列于表1。
77.表1
78.[0079][0080]
由表1可以得出以下几点:
[0081]
(1)由实施例1-3可以看出,本发明所述靶材的焊接方法将摩擦焊接与热等静压焊接相结合,提高了靶材与背板之间的焊接强度,拉伸断裂强度在190mpa以上,焊接结合率高,每炉次生产靶材组件的数量增加,同时不需要做包套,生产效率高;
[0082]
(2)将实施例1与实施例4、5进行对比,可以看出,由于实施例4中摩擦焊接的转速为0.2m/s,低于本发明优选的0.5-2m/s,导致摩擦焊接的效果不显著,无法将靶材和背板牢固的焊接在一起,进而导致拉伸断裂强度低以及焊接结合率降低;由于实施例5中摩擦焊接的转速为2.5m/s,超出本发明优选的0.5-2m/s,导致整个摩擦焊过程难以控制,会造成材料的浪费,导致10mm余量不够,部分产品厚度不达标,同时,转速过快很容易产生焊接面金属飞溅,造成安全隐患;
[0083]
(3)将实施例1与实施例6、7进行对比,可以看出,由于实施例6中热等静压焊接的温度为150℃,低于本发明优选地200-800℃,导致热等静压焊接过程中,靶材与背板的扩散效果不好,进而导致拉伸断裂强度低,焊接结合率低;由于实施例7中热等静压焊接的温度为850℃,超出本发明优选地200-800℃,会破坏靶材的自身结构,导致晶粒长大,造成产品报废;
[0084]
(4)将实施例1与对比例1、2进行对比,可以看出,对比例1未采用摩擦焊接,而是先在背板上加工螺纹,再进行热等静压焊接,该方法焊接效果不佳,靶材与背板无法紧密结合在一起,拉伸断裂强度及焊接结合率大幅降低,此外,由于需要做包套,以及对包套进行抽真空处理,生产效率极低,因包套的缘故,导致每炉次仅生产14个靶材组件;对比例2采用轴向静压焊接,未采用热等静压焊接,轴向静压一般靠的是液压装置或者热压烧结炉,在加热情况下,很难实现大压力,该方法由于压力较低,导致焊接强度不高,进而导致拉伸断裂强度降低,焊接结合率降低,且生产效率降低,每炉次仅生产11个靶材组件。
[0085]
申请人声明,以上所述仅为本发明的具体实施方式,但本发明的保护范围并不局限于此,所属技术领域的技术人员应该明了,任何属于本技术领域的技术人员在本发明揭露的技术范围内,可轻易想到的变化或替换,均落在本发明的保护范围和公开范围之内。