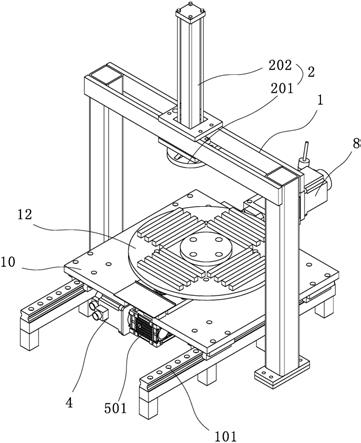
1.本实用新型涉及锯床用夹具技术领域,尤其是涉及一种锯床用四工位转台夹紧锯切装置。
背景技术:2.现在市场上高端模具钢经过锻打后形成不规则型,通常通过铣床或线切割把不规则型的锻造件加工成易装夹的长方体,切割加工成本高,且普通锯床现有的各种固定方式,不适合不规则件自动切割成方型件。
3.例如,在中国专利文献上公开的“四面锯切装置”,其公告号cn201420855800.7,包括装夹机构和四面锯切机构,所述四面锯切机构主要由一个平行安装有两片横向锯片的横向锯切装置和一个平行安装有两片竖向锯片的竖向锯切装置组成,所述装夹机构包括一个断面呈v或u形的通槽以及前后相对设置在通槽两端的推杆;所述装夹机构还包括用于推动推杆沿通槽长度方向上同时运动的原木进给机构。该实用新型中,难以对不规则型的锻造件进行加工。
技术实现要素:4.本实用新型是为了克服上述现有技术中对不规则型的锻造件加工成易装夹的长方体时加工成本高等问题,提供一种锯床用四工位转台夹紧锯切装置,成本低、对不规则件切成方型件实现自动切割;切割精确度高。
5.为了实现上述目的,本实用新型采用以下技术方案:
6.一种锯床用四工位转台夹紧锯切装置,包括龙门架、滑动设置在龙门架上的工作平台、设置在工作平台上的承载平台,在龙门架上方设置有用于夹紧工件的压紧组件,在工作平台和承载平台之间设置有用于控制承载平台转动的转动控制组件。
7.在该技术方案中,龙门架用于整个装置的支撑,承载平台用于放置工件,在使用时,先滑动工作平台调整工件位置,然后用压紧组件将工件夹紧,锯切后再通过旋转控制组件将承载平台旋转90度,进而控制工件旋转90度,再将工件夹紧锯切,得到方形件,整个过程实现了自动切割,且相较于传统的铣床和线切割的方式,该装置成本更低更便捷。
8.作为优选,转动控制组件包括用于带动承载平台转动的转轮控制组件和用于限制承载平台转动的限位控制组件。
9.转轮控制组件用于带动承载平台进行转动,进而带动工件转动,便于从不同方向切割形成方形件;限制控制组件的设置固定承载平台,避免在夹紧或锯切时承载平台带动工件转动影响工件切割精度。
10.作为优选,转轮控制组件包括转轮组件和用于驱动转轮组件转动的转动伺服电机,所述转轮组件设置在承载平台和工作平台之间,所述转轮组件包括与转动伺服电机连接的驱动轮和带动承载平台同步转动的从动轮,驱动轮和从动轮相互啮合。
11.转动伺服电机带动驱动轮转动,驱动轮再带动从动轮转动,由于从动轮与承载平
台固连,从动轮带动承载平台同步转动,进而使工件进行转动,便于从不同方向切割得到方形件。
12.作为优选,在所述转动伺服电机和驱动轮之间设置有减速机组件。
13.减速机组件的设置便于控制驱动轮的转速。
14.作为优选,所述限位控制组件包括设置在工作平台上的若干定位孔、固定在从动轮下表面的定位销和用于控制从动轮和承载平台升降的抬升油缸,定位销和定位孔配合设置。
15.在需要调整角度时,首先通过抬升油缸将从动轮和承载平台抬起,进而使得定位销从定位孔中脱出,再通过转轮控制组件带动承载平台转动,转动一定角度后,抬升油缸下降,使得从动轮底部的定位销设置在定位孔内将承载平台固定,同时还保证了转角精度。
16.作为优选,在工作平台下方设置有用于驱动工作平台移动的进退伺服电机和丝杆组件。
17.工作平台通过进退伺服电机来驱动丝杆组件带动工作平台移动,丝杆组件的设置使得工作平台移动平稳且便于控制工作平台的移动速度。
18.作为优选,丝杆组件包括与进退伺服电机连接的滚珠丝杆和固定在工作平台底部的静音螺母,所述静音螺母套设在滚珠丝杆外。
19.进退伺服电机带动滚珠丝杆转动,使得静音螺母带动工作台沿滚至丝杆发生移动,进而调整工作台上承载平台和工件的位置。
20.作为优选,在所述在龙门架上设置有直线滑轨,直线滑轨与工作平台运动方向平行设置,在工作平台和直线滑轨之间设置有滑块。
21.直线滑轨的设置对工作平台的移动起到了导向和支撑的作用,使得工作平台在滑移过程方向一定且保持滑移平稳。
22.因此,本实用新型具有如下有益效果:成本低、对不规则件切成方型件实现自动切割;切割精确度高。
附图说明
23.图1是本实用新型一种锯床用四工位转台夹紧锯切装置的结构示意图;
24.图2是锯床用四工位转台夹紧锯切装置的侧视图;
25.图3是锯床用四工位转台夹紧锯切装置的后视图;
26.图中:1、龙门架
ꢀꢀ
101、直线滑轨
ꢀꢀ
2、压紧组件
ꢀꢀ
201、压紧盘
ꢀꢀ
202、上压气缸
ꢀꢀ
3、转轮组件
ꢀꢀ
301、驱动轮
ꢀꢀ
302、从动轮
ꢀꢀ
4、转动伺服电机
ꢀꢀ
501、减速机
ꢀꢀ
502、减速机轴
ꢀꢀ
503、支撑轴承
ꢀꢀ
6、定位销
ꢀꢀ
7、抬升油缸
ꢀꢀ
8、进退伺服电机
ꢀꢀ
9、滚珠丝杆
ꢀꢀ
10、工作平台
ꢀꢀ
11、滑块
ꢀꢀ
12、承载平台。
具体实施方式
27.下面结合附图与具体实施方式对本实用新型做进一步的描述。
28.实施例1:
29.如图1、图2、图3所示的实施例1中,一种锯床用四工位转台夹紧锯切装置,其包括用于支撑的龙门架1、滑动设置在龙门架1上的工作平台10、设置在工作平台10上的承载平
台12,在工作平台10和承载平台12之间设置有用于控制承载平台12转动的转动控制组件,在龙门架1的上侧设置有与承载平台12配合将工件夹紧的压紧组件2,压紧组件2包括压紧盘201和上压气缸202,上压气缸202设置在压紧盘201的上方;在使用过程中上压气缸202带动与压紧盘201下压,使得压紧盘201与承载平台12将待锯切的工件夹紧,进而便于对工件进行锯切。在该技术方案中,龙门架1用于整个装置的支撑,承载平台12用于放置工件,在使用时,先滑动工作平台10调整工件位置,然后用压紧组件2将工件夹紧,锯切后再通过旋转控制组件将承载平台12旋转90度,进而控制工件旋转90度,再将工件夹紧锯切,得到方形件,整个过程实现了自动切割。
30.转动控制组件包括用于带动承载平台12转动的转轮控制组件和用于限制承载平台12转动的限位控制组件;其中,转轮控制组件包括转轮组件3和用于驱动转轮组件3转动的转动伺服电机4,转轮组件3设置在承载平台12和工作平台10之间,转轮组件3包括驱动轮301和从动轮302,转动伺服电机4带动驱动轮301转动,而从动轮302固定在承载平台12下方实现承载平台12与从动轮302的同步转动,转动伺服电机4和驱动轮301之间设置有减速机组件,减速机组件包括与转动伺服电机4连接的减速机501、用于连接驱动轮301的减速机轴502,在工作平台10上设置有用于限位减速机轴502的支撑轴承503,另外,其中驱动轮301为小齿轮,从动轮302为大齿轮。
31.限位控制组件包括设置在工作平台10上的若干定位孔、固定在从动轮302下表面的定位销6和用于控制从动轮302和承载平台12升降的抬升油缸7,在需要调整角度时,首先通过抬升油缸7将从动轮302和承载平台12抬起,进而使得定位销6从定位孔中脱出,再通过转轮控制组件带动承载平台12转动,转动一定角度后,抬升油缸7下降,使得从动轮302底部的定位销6设置在定位孔内将承载平台12固定。另外,从动轮302的厚度大于驱动轮301的厚度,避免在承载平台12上移过程中从动轮302从驱动轮301脱离。
32.在工作平台10下方设置有用于驱动工作平台10移动的进退伺服电机8和丝杆组件,丝杆组件包括固定在进退伺服电机8上的滚珠丝杆9和设置在工作平台10底部的静音螺母,滚珠丝杆9穿设在静音螺母内,进退伺服电机8带动滚珠丝杆9转动,使得静音螺母带动工作台沿滚至丝杆发生移动,在龙门架1上设置有直线滑轨101,在工作平台10和直线滑轨101之间设置有滑块11,使工作平台10滑动连接在直线滑轨101上,直线滑轨101成对设置在工作平台10底部的两侧,直线滑轨101对工作平台10的移动起到了导向和支撑的作用,使得工作平台10在滑移过程方向一定且保持滑移平稳。
33.综上所述,一种锯床用四工位转台夹紧锯切装置的工作流程主要是:将工件安放在承载平台12上,输入所锯切尺寸后,由进退伺服电机8带动整个工作台移动,进而带动承载平台12上的工件移动,调整工件的位置,然后通过上压气缸202带动压紧盘201将工件压紧,再进行锯切;锯切完成后,先通过台江油缸将从动轮302和承载平台12抬起,使定位销6脱离工作平台10,再通过转动伺服电机4驱动减速机带动驱动轮301转动,驱动轮301再带动从动轮302转动,而承载平台12固定在从动轮302上,实现了同步转动,在转动90度后,抬升油缸7带动从动轮302和承载固定平台下井,固定在从动轮302上的定位销6重新插接到工作平台10上的定位孔中,再消除齿轮加你,保证转角精度,然后通过进退伺服电机8控制工件位置,便于控制锯切产品的尺寸,再通过压紧盘201压紧,开始锯切,循环后自动退出锯切位,更换材料。这样的切割方式只需转动承载平台12然后调整位置,即可使得不规则型的材
料也可以切割形成若干易装夹的长方体。
34.需要说明的是,上述描述中使用的词语“前”、“后”、“左”、“右”、“上”和“下”指的是附图中的方向,词语“内”和“外”分别指的是朝向或远离特定部件几何中心的方向。
35.以上实施例仅用于说明本实用新型而不用于限制本实用新型的范围。对本领域的技术人员来说,可根据以上描述的技术方案以及构思,做出其它各种相应的改变以及形变,而所有的这些改变以及形变都应该属于本实用新型权利要求的保护范围之内。