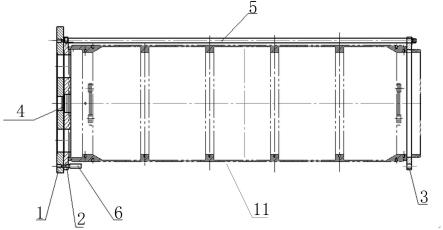
1.本实用新型涉及不带转台的龙门加工中心设备加工壳体外圆径向孔的技术领域,具体为一种加工中心旋转定位机构。
背景技术:2.目前,在对壳体类部件的内腔径向孔进行加工时,由于壳体轴向尺寸长,且内腔径向孔距离壳体端面较近,由于受龙门加工中心行程的限制,常规方法无法加工。
3.具体而言,目前龙门加工中心在加工超长壳体方面主要存在以下缺点:
4.1).对于超过行程的壳体类零件的均布径向孔无法在转台上加工;
5.2).利用刻线分别加工各径向孔,每个孔的加工均需要找正刻线,并且需要多次装夹,加工误差大,效率低。
技术实现要素:6.针对未配置转台的龙门加工中心设备,其加工壳体类零件外圆及内腔多处径向孔存在的技术问题,本实用新型提供一种加工中心旋转定位机构,以解决龙门加工中心在加工超长壳体方面存在的技术问题。
7.本实用新型是采用如下技术方案实现的:一种加工中心旋转定位机构,包括底盘、定位盘、压盘、旋转轴、螺杆和定位销;所述底盘中心开有轴孔,底盘表面环绕其中心开有多个销孔,所述销孔中心位于同一个圆上,底盘的底部水平切割一角形成底部平台;所述定位盘中心开有轴孔,定位盘的一侧设有凸台结构,定位盘上在凸台外环绕中心开有多个螺孔及至少一个销孔,所述螺孔与销孔的中心位于同一个圆上且该圆的直径与底盘上销孔所在圆直径相同;所述压盘中心开有通孔,压盘上环绕通孔开有数量与定位盘上螺孔数量相同的螺孔,压盘上螺孔所在圆与定位盘上螺孔所在圆直径相同;所述螺杆数量与螺孔相同,螺杆通过定位盘和压盘上的螺孔将二者连接以夹持待加工的壳体;旋转轴穿过底盘和定位盘之间的轴孔设置,底盘和定位盘上的销孔通过定位销实现连接定位。
8.底盘上的销孔根据壳体上的径向孔预先加工,数量和角度都根据壳体上的径向孔设计。加工时,底盘通过其底部平台放置与龙门加工中心工作台上并固定,将定位盘通过旋转轴与底盘相连接,找正后将待加工的壳体装在定位盘与压盘之间,定位盘的凸台卡住壳体一端的内腔壁,压盘中心通孔则将壳体另一端套住,然后压盘与定位盘之间通过螺杆连接,这样就能够将待加工的壳体定位。然后通过定位销将定位盘和底盘实现连接固定,这样壳体位置就被固定,龙门加工中心的钻头就可以在壳体的径向实现打孔。打完第一个孔后,转动相应的角度,打第二个孔,直到所有孔都打完。因为底盘上的销孔是按照壳体上待加工的径向孔提前加工好的,所以只要第一个径向孔位置确定后,加工完第一个径向孔,转动定位盘特定的角度,就可以实现对下一个径向孔的加工。定位盘上的螺孔和销位于同一圆上,这样能保证销孔和螺孔位置交错,螺杆和定位销之间也互不干涉。
9.本实用新型通过设计加工中心旋转定位机构,实现了以下技术效果:
10.1)实现一次装夹壳体,完成对壳体外圆、内腔径向孔的加工,节省多次装夹的时间,提高加工效率;
11.2)一次装夹找正完成全部径向孔的加工,减少找正误差,提高壳体外圆、内腔各径向孔的加工精度;
12.3)扩大了加工中心的加工范围。
附图说明
13.图1壳体两端径向加工孔示意图。
14.图2安装好壳体的加工中心旋转定位机构示意图。
15.图3加工中心旋转定位机构底盘正面结构示意图。
16.图4为图3的侧视图。
17.图5加工中心旋转定位机构定位盘正面结构示意图。
18.图6为图5的侧视图。
19.图7加工中心旋转定位机构拉杆结构示意图。
20.图8加工中心旋转定位机构旋转轴结构示意图。
21.图9加工中心旋转定位机构旋压盘结构示意图。
22.图10为图9的侧视图。
23.1-底盘、2-定位盘、3-压盘、4-旋转轴、5-螺杆、6-定位销,7-销孔,8-底部平台,9-螺孔,10-减重孔,11-壳体。
具体实施方式
24.实施例1如图2-10所示,一种加工中心旋转定位机构,包括底盘1、定位盘2、压盘3、旋转轴4、螺杆5和定位销6;所述底盘中心开有轴孔,底盘表面环绕中心开有多个销孔7,所述销孔7中心位于同一个圆上,底盘的底部水平切割一角形成底部平台8;所述定位盘2中心开有轴孔,定位盘2的一侧设有凸台结构,定位盘2上在凸台外环绕中心开有多个螺孔9及至少一个销孔7,所述螺孔9与销孔7的中心位于同一个圆上且该圆的直径与底盘1上销孔7所在圆直径相同;所述压盘3中心开有通孔,压盘3上环绕通孔开有数量与定位盘2上螺孔数量相同且位置一一对应的螺孔9,压盘3上螺孔9所在圆与定位盘2上螺孔9所在圆直径相同;所述螺杆5数量与螺孔9相同,螺杆5通过定位盘2和压盘3上的螺孔9将二者连接以夹持待加工的壳体;旋转轴4穿过底盘1和定位盘2之间的轴孔设置,底盘1和定位盘2上的销孔7通过定位销6实现连接定位。
25.实施例2如图3、4所示,底盘1上的销孔7为6个,其中两个销孔7分布在底盘1的竖直中心线上(上下各一个)。6个销孔按照间隔60度分布,与待加工径向孔的分布相同。
26.实施例3如图3所示,所述销孔7还包括分布在底盘1水平中心线上下侧20度的四个孔以及上下侧15度的四个孔。这些销孔可以满足壳体不同分布的其它径向孔的加工要求。
27.实施例4如图5所示,定位盘2上的螺孔9为四个,相互等间距90度分布,销孔7为一个,位于其中两个螺孔9之间并与两个螺孔9间距45度。这样螺孔和销孔之间就互不干涉。图7中销孔也是四个。
28.实施例5如图3、5所示,底盘1上环绕其中心开有多个减重孔10,定位盘2的凸台上环绕其中心也开有多个减重孔10,可以减轻定位盘和底盘的重量。
29.定位盘2上的轴孔内径大于底盘1轴孔内径;所述旋转轴4的截面呈“凸”字形,并与上述两个轴孔相配,这样旋转轴不容易脱落,边缘倒20度斜角,也不易损坏。定位盘2凸台的直径与压盘3通孔内径相同。定位销6采用菱形销。底盘1的底部平台8到底盘1中心的间距为300mm,销孔7所在圆的直径为540mm。定位盘2上的轴孔内径为80mm,底盘1轴孔内径为60mm。
30.某产品的壳体如图1所示,材料为钛合金ta4,壳体外径为φ500mm,总长1520mm,壳体两端各有一组6-m8-7h的螺纹盲孔,距离端面73mm,受龙门加工中心z轴行程的限制,不能在自带转台上加工,并且内腔其余各径向孔已经加工完成,由于内腔各孔之间存在角向关系,在加工过程中,此两组螺纹孔的角向确定是加工过程中需要解决的难题,并且根据装配关系的要求,每端的6-m8-7h螺纹孔需要一次装夹全部加工完成。
31.通过分析壳体的结构及径向孔的位置,根据壳体的结构特点,需要在龙门加工中心设备上加工,经过研究分析壳体两端内腔两组6-m8-7h的螺纹盲孔的尺寸关系,在自带转台上加工,其已经超出龙门加工中心z轴的行程,无法实现径向孔的加工,若在龙门加工中心的长方形工作台上,则需要提前在壳体上划出径向孔的角向位置刻线,并且每加工一个孔,需要重新装夹找正一次,加工效率低,找正误差累加加大,加工完成的径向孔角向精度低。
32.为此,为了提高壳体径向孔的加工精度及加工效率,减小找正误差,通过分析加工中心转台的结构及查阅相关转台机构设计手册,设计加工中心旋转定位机构(图2-10所示),在龙门加工中心的长方形工作台上,利用已经加工完成径向孔的角向位置,通过转动旋转定位机构,完成壳体两端内腔两组6-m8-7h的螺纹盲孔的加工。
33.本实用新型具体应用时的工作流程:
34.1、首先根据壳体内腔各径向孔的位置关系,设计如图2所示的加工中心旋转定位机构。
35.2、在加工完壳体内腔其余各孔后,在壳体外圆刻线,用于后续定角向使用。
36.3、根据设计的旋转定位辅具,将底盘固定在龙门加工中心工作台上,找正旋转定位辅具,将壳体装入定位盘中,对准外圆上的刻线,利用菱形销固定定位盘和底盘,夹紧,加工一处m8-7h螺纹盲孔,加工完成后将菱形销拔出,转动定位盘至另一位置处,再次利用菱形销固定定位盘和底盘,加工另一处m8-7h螺纹盲孔,如此往复,至加工完6处m6-7h螺纹盲孔。
37.通过两次装夹找正,顺利完成了壳体内腔两端6-m6-7h螺纹盲孔的加工,为公司解决了加工技术难题,此次共计加工此种壳体10件,尺寸全部符合图纸要求,产品已顺利交付客户,为后续加工此类型的壳体结构积累了丰富的加工经验。
38.此旋转定位机构设计,提高了壳体径向孔的加工精度及加工效率。
39.底盘上可以结合实际情况设计多个定位孔,相互之间的夹角根据待加工壳体的情况而定,以满足不同壳体径向孔加工的需要。
40.该自主设计旋转定位机构,摆脱了龙门加工中心z轴行程的限制,实现一次装夹完成对壳体内腔一端径向孔的全部加工,减少了装夹时间和找正次数,提高了加工精度和效率。