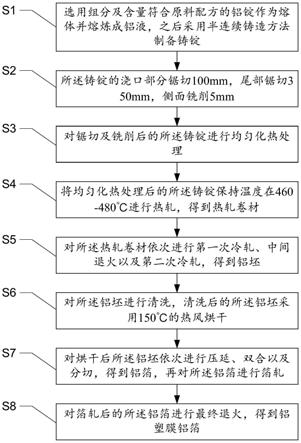
高光亮度铝塑膜铝箔的制备方法及铝塑膜铝箔
【技术领域】
1.本发明涉及铝加工技术领域,尤其是涉及一种高光亮度铝塑膜铝箔的制备方法及铝塑膜铝箔。
背景技术:2.目前,锂电行业飞速发展,其中锂电池包装方式主要分钢壳锂离子电池、铝壳锂离子电池及软包装锂离子电池三种。而软包锂离子电池具有安全性能好、重量轻、容量大、内阻小、设计灵活等优点,现广泛应用于数码产品,如手机、笔记本电脑、蓝牙耳机、电子烟等。
3.软包锂离子电池需要用到铝塑膜铝箔,而铝塑膜铝箔有两种生产方法,分别为铸轧供坯和热轧供坯。其中,采用铝塑膜铸轧供坯制备的,其杯突较低;而采用热轧供坯的,普遍存在过多的铁相使氧化膜失去连续性,表面光亮度不佳,且易发生电化学腐蚀。
4.理论上,两种金属间的腐蚀电位差越大,腐蚀速度就越快,同时,在铝箔复合前的清洗钝化工序中,由于弥散相的存在,还导致铝氧化膜存在缺陷,这些相与铝存在电位差,即8021合金/8079合金主要的第二相为feal3,而feal3腐蚀电位-0.56v,铝基体腐蚀电位-0.85v,而发生接触则会出现腐蚀,形成原电池效应,出现发白甚至发黄的色差现象,失去原本的金属光亮度,以致使锂离子电池的寿命降低。
5.因此,有必要提供一种铝塑膜用铝箔的制备方法以解决上述问题。
技术实现要素:6.本发明实施例的目的在于提供一种高光亮度铝塑膜铝箔的制备方法及铝塑膜铝箔,以解决现有的铝塑膜铝箔由于腐蚀问题而导致其光亮度差,若应用于锂离子电池时,会导致锂离子电池寿命低的问题。
7.第一方面,本发明实施例提供了一种高光亮度铝塑膜铝箔的制备方法,包括以下步骤:
8.步骤s1、选用组分及含量符合原料配方的铝锭作为熔体并熔炼成铝液,之后采用半连续铸造方法制备铸锭,其中,
9.所述原料配方为:si=0.02-0.08wt%、fe=0.7-1.3wt%、cu≤0.02wt%、mn≤0.01wt%、mg≤0.01wt%、zn≤0.02wt%、ti=0.01-0.03wt%、b≤0.003wt%、c≤0.003wt%、v=0.01-0.02wt%,余量为al;
10.步骤s2、所述铸锭的浇口部分锯切100mm,尾部锯切350mm,侧面铣削5mm,其中,侧面铣削后的平直度小于或等于0.2mm/m,表面粗糙度小于5μm;
11.步骤s3、对锯切及铣削后的所述铸锭进行均匀化热处理,其中,所述均匀化热处理的温度为460-610℃,保温时间为6-15小时;
12.步骤s4、将均匀化热处理后的所述铸锭保持温度在460-480℃进行热轧,得到热轧卷材,其中,所述热轧经过多道次可逆轧制,轧制到中间坯厚度为20-25mm后进入三连轧热轧机列,所述热轧卷材的厚度为2.5-5.0mm,终轧温度为230-320℃;
13.步骤s5,对所述热轧卷材依次进行第一次冷轧、中间退火以及第二次冷轧,得到铝坯,其中,第一次冷轧后所述热轧卷材的厚度为0.4-1.2mm,所述中间退火的温度为300-420℃,保温时间为1-3小时,所述铝坯的厚度为0.2-0.4mm;
14.步骤s6、对所述铝坯进行清洗,清洗后的所述铝坯采用150℃的热风烘干,其中,所述清洗的方式依次采用流动水洗、高压碱液喷淋以及漂洗,清洗后所述铝坯的表面的残油小于1mg/m2,铝粉残留小于2mg/m2;
15.步骤s7、对烘干后所述铝坯依次进行压延、双合以及分切,得到铝箔,再对所述铝箔进行箔轧,其中,所述铝箔的厚度为0.03-0.07mm,所述箔轧的轧辊磨削采用砂轮磨削后再采用镜面振动抛光技术进行;
16.步骤s8、对箔轧后的所述铝箔进行最终退火,得到铝塑膜铝箔,其中,所述最终退火采用氮气保护以及负压除油的方式进行,所述铝塑膜铝箔的最终杯突值大于7.5mm。
17.优选的,所述步骤s1中,所述熔炼采用喷吹搅拌熔炼技术进行;所述半连续铸造方法依次包括精炼、除渣、静置、除气、过滤以及结晶,其中,所述精炼的温度为730-750℃,时间为12-30分钟,并通入氮气或氩气,所述静置的温度为735-750℃,时间为15-30分钟。
18.优选的,所述步骤s2中,所述侧面铣削采用数控铣床进行。
19.优选的,所述步骤s4中,所述热轧前,在均匀化热处理的所述与炉之间间隔180个锭子;所述热轧时,所述炉的烧嘴沿其宽度方向分布。
20.优选的,所述步骤s4中,所述热轧的辊道的两端均为尖端相对的锥形结构。
21.优选的,所述步骤s5中,所述第一次冷轧和所述第二次冷轧采用不可逆冷轧机进行,同时,所述第一次冷轧和所述第二次冷轧中的工作辊的相对两侧分别安装有尼龙刷辊。
22.优选的,所述步骤s6中,所述高压碱液喷淋时的压力为4-6mpa,碱液中含有0.9-1.1
‰
的葡萄糖酸钠。
23.优选的,所述步骤s7中,所述箔轧中的轧辊经磨削和抛光后粗糙度小于0.005μm。
24.优选的,所述步骤s8中,所述铝塑膜铝箔的晶粒的直径平均小于10.0μm。
25.第二方面,本发明实施例提供了一种铝塑膜铝箔,所述铝塑膜铝箔由上述的高光亮度铝塑膜铝箔的制备方法制成,所述铝塑膜铝箔应用于锂离子电池。
26.与现有技术相比,本发明中的高光亮度铝塑膜铝箔的制备方法通过限定原料配方并采用不同条件的热轧法制备得到8079合金的铝塑膜铝箔,可以使其厚度保持在0.03-0.07mm,抗拉强度保持在70~100mpa,延伸率达到15%以上,含铁量降低,光亮度提升,腐蚀速度降低,若将其应用于锂离子电池,还能极大程度延长锂离子电池的最终寿命。
【附图说明】
27.为了更清楚地说明本发明实施例中的技术方案,下面将对实施例描述中所需要使用的附图作简单地介绍,显而易见地,下面描述中的附图仅仅是本发明的一些实施例,对于本领域普通技术人员来讲,在不付出创造性劳动的前提下,还可以根据这些附图获得其它的附图,其中:
28.图1为本发明实施例提供的一种高光亮度铝塑膜铝箔的制备方法的流程示意图;
29.图2为现有工艺生产得到的铝塑膜铝箔的光亮度效果与本发明实施例工艺生产得到的铝塑膜铝箔的光亮度效果的对比图;
30.图3为现有工艺生产得到的铝塑膜铝箔的杯突值与本发明实施例工艺生产得到的铝塑膜铝箔的杯突值的对比图;
31.图4为成分设计的数值模拟之相组成预测示意图;
32.图5为有限元模拟之均匀化温度预测示意图;
33.图6为热轧差温轧制的有限元模拟之差温模型示意图;
34.图7为现有工艺生产得到的铝塑膜铝箔的表面形貌与本发明实施例工艺生产得到的铝塑膜铝箔的表面形貌的对比图;
35.图8为本发明实施例中铝箔的表面凹坑冲压成型减薄后的裂纹到针孔的演变示意图。
【具体实施方式】
36.下面将对本发明实施例中的技术方案进行清楚、完整地描述,显然,所描述的实施例仅是本发明的一部分实施例,而不是全部的实施例。基于本发明中的实施例,本领域普通技术人员在没有做出创造性劳动前提下所获得的所有其它实施例,都属于本发明保护的范围。
37.结合图1所示,本发明实施例提供了一种高光亮度铝塑膜铝箔的制备方法,包括以下步骤:
38.步骤s1、选用组分及含量符合原料配方的铝锭作为熔体并熔炼成铝液,之后采用半连续铸造方法制备铸锭。
39.具体地,所述原料配方为:si=0.02-0.08wt%、fe=0.7-1.3wt%、cu≤0.02wt%、mn≤0.01wt%、mg≤0.01wt%、zn≤0.02wt%、ti=0.01-0.03wt%、b≤0.003wt%、c≤0.003wt%、v=0.01-0.02wt%,余量为al。
40.其中,si的含量还可以进行适应性调整,如0.05-0.08wt%、0.02-0.06wt%、0.02-0.07wt%、0.03-0.06wt%、0.03-0.07wt%、0.03-0.08wt%、0.05~0.06wt%、0.05-0.07wt%等。si与fe配合形成金属间化合物,然而,当si的添加量较大时,会导致化合物尺寸的粗化和分布密度的降低,且延展能力和产品断后延伸率性能会由于粗结晶产物而降低,此外,最终退火后再结晶的晶粒尺寸分布的均匀性也会降低。因此,需要对si的含量进行限定。
41.fe的含量也可以进行适应性调整,如0.7-1.2wt%、0.7-1.1wt%、0.8-1.3wt%、0.8-0.95wt%、0.9-1.05wt%等。fe结晶为al3fe金属间化合物,以第二相粒子呈弥散分布在铝合金中,在后续的加工过程中,第二相粒子周围出现高位错区,在后续退火的过程中形核率就高,晶粒得到细化,微细的晶粒提供大量的晶界,使晶界的滑动、旋转更容易产生,有利于后续铝塑膜铝箔深冲变形。当fe含量小于下限时,第二相粒子的分布密度减小,细化效果弱,最终晶粒尺寸分布也变得不均匀;当fe含量大于上限时,晶粒细化效果降低,此外,在铸造中要产生的al-fe基化合物的尺寸较大,铝箔的延伸率和压延能力会降低。因此,需要对fe的含量进行限定。
42.cu是固溶在铝箔中的,其通常降低铝的抗蚀性,是点腐蚀的起源点。其还是增加铝箔强度的元素,具有加工硬化的作用,以降低铝箔的延伸率。当cu的质量含量小于0.005%时,加工硬化的效果较弱,当cu的质量含量大于0.05wt%时,延伸率明显降低,因此,cu的含
量还可以小于0.05wt%,较优选的则是小于0.02wt%,最优的则是小于0.005wt%。
43.mn的作用是固溶在铝基体中,以抑制铝的再结晶。当mn处于非常微量的状态时,可以产生类似于cu的加工硬化作用,然而,当mn的含量较大时,容易导致枝晶偏析,在进行中间退火和最终退火中会延迟再结晶,很难获得均匀的细晶粒。因此,mn的含量调节为小于0.01wt%,更优的则是mn的含量调节为小于0.005wt%。
44.mg的作用是固溶在铝基体中,产生类似于cu的加工硬化作用。当mg的含量较大时,会加大压延加工的难度,且最终产品延伸率也会急剧下降。因此,mg的含量调节为小于0.01wt%,更优的则是mg的含量调节为小于0.005%。
45.b会与晶粒细化时添加的铝钛硼细化剂中的al3ti发生包晶反应,形成粗大的钛聚集,从而晶粒细化效果减弱。因此,b的含量调节为小于0.003wt%,更有的则是调节为小于0.001wt%。
46.v会与al一起形成金属件化合物,在一定量的下可以细化晶粒,然而,当v的添加量较大时,会形成原电池效应,加速腐蚀。因此,需要对v的含量进行限定。
47.c会与铝形成高熔点的化合物al4c3,在后续箔轧压延过程中会逐渐显现破裂成针孔的情况。因此,c的含量调节为小于0.003wt%,更优的则是调节为小于0.001wt%。
48.具体地,所述熔炼采用喷吹搅拌熔炼技术进行,这样既能保证加热和搅拌的同时进行,又不会破坏表面氧化膜,以获得净化的铝液。
49.具体地,所述半连续铸造方法依次包括精炼、除渣、静置、除气、过滤以及结晶,其中,所述精炼的温度为730-750℃,时间为12-30分钟,并通入氮气或氩气,所述静置的温度为735-750℃,时间为15-30分钟。
50.步骤s2、所述铸锭的浇口部分锯切100mm,尾部锯切350mm,侧面铣削5mm。
51.其中,侧面铣削是对所述铸锭的两个侧面进行,侧面铣削后的平直度小于或等于0.2mm/m,表面粗糙度ra小于5μm。
52.具体地,所述侧面铣削采用数控铣床进行,以去除所述铸锭的缺陷层,确保材料的组织和性能。
53.具体地,为了保证所述铸锭的表面质量,铣削完成后所述铸锭进行竖直运输,避免铣削的侧边和即将进行轧制的表面被触碰,即全程采用不接触侧面的运输方式。
54.步骤s3、对锯切及铣削后的所述铸锭进行均匀化热处理。
55.其中,所述均匀化热处理的温度为460-610℃,保温时间为6-15小时。
56.具体地,所述均匀化热处理前,可以在锯切机与加热炉之间间隔放置180个锭子,以起到缓冲的作用,这样不仅节约空间,还能更好地保护所述铸锭的表面。
57.步骤s4、将均匀化热处理后的所述铸锭保持温度在460-480℃进行热轧,得到热轧卷材。
58.其中,所述热轧经过多道次可逆轧制,轧制到中间坯厚度为20-25mm后进入三连轧热轧机列,所述热轧卷材的厚度为2.5-5.0mm,终轧温度为230-320℃。
59.具体地,所述热轧前,在均匀化热处理前的所述锯切与加热炉之间间隔放置180个锭子,以起到缓冲的作用,这样不仅节约空间,还能更好地保护所述铸锭的表面。
60.具体地,所述热轧时,所述热轧炉的烧嘴沿其宽度方向分布,所述铸锭的两个侧面作为主要的热交换面以加热所述铸锭,这样有利于沿其长度方向均匀受热,使其升温速度
快,温度均匀。
61.具体地,所述铸锭在所述热轧炉内受热过程中,其两个侧面不与任何固体物质接触,以避免所述铸锭的表面在所述热轧炉内受损。所述铸锭在进出所述热轧炉的过程中,其两个侧面不与任何固体物质产生相对滑动,以减少所述铸锭在进出炉时的表面损伤,从而确保所述铸锭在进入轧线辊道时的良好表面质量。起吊锭子的夹头需要保证其夹持是,既不损伤工件的表面质量,又能夹住所述铸锭,其夹头为棱柱体状。
62.具体地,为了克服铝坯下表面可能的擦划伤或粘铝,因此,首先需要特别重视辊道、张力辊、导向辊以及轧辊的材质、表面、形状以及运行情况,所以,所述热轧的辊道的两端均为尖端相对的锥形结构,即两边高,中间低,此时,只有下表面边缘与辊道接触,最大限度减少了擦划伤,最边部的表面的不良部分经过工艺切边则可以去除。其次则是改善乳液的冷却润滑性能,防止粘铝,以提高轧制过程中轧制工艺的稳定性。
63.具体地,为了降低杂质元素对所述热轧卷材的影响,则需要控制轧辊的参数、速度及终轧的温度等因素。
64.具体地,为了获得表面质量更好的所述热轧卷材,则需要控制所述轧辊的磨削、辊型及粗糙度,其中,三连轧热轧之前的轧辊的粗糙度(ra)为1.8-2.5μm,而三连轧热轧中的轧辊的粗糙度(ra)则为0.8-1.8μm,且由进口至出口其粗糙度逐渐提高。为了避免粘铝的现象,所述热轧时,其热轧机上均需要配备清刷辊装置。
65.具体地,为了充分适应所述热连轧线大坯锭、高速、大压下量及高表面质量生产的要求,在需要使用与热轧机相匹配的大热容量、大流量及大压力的乳液系统。乳液的冷却润滑既包括对轧辊、铝板的冷却润滑,也包括对辊道的冷却润滑,其中,喷射系统及喷射控制模式是发挥乳液最佳使用效果的条件。所述热轧时通过电加热器进行升温和降温,这样可以避免蒸汽加热时现场环境差、蒸汽和乳液腐蚀蒸汽管及蒸汽进入系统影响乳液品质等缺陷,且热效高,主要通过安装在热轧机乳液管道上的冷热水交换器进行。
66.具体地,乳液净化包括乳液过滤和乳液撇油两部分。为实现乳液大流量的连续过滤,则采用真空负压过滤;为高效撇除乳液表层的浮油,减少乳液撇油损失,则采用浮筒式撇油器;由油水分离器分离浮油中的杂油和乳液,分离出的乳液回流至乳液系统,杂油则外排回收。其中,真空负压过滤器的优点是:整个箱体为焊接结构,结构简单,制作简便,运行可靠,采用液位控制和真空度控制,可长时间无故障连续运行,实现连续循环过滤和完全过滤,过滤能力强,过滤量可达13000l/min,过滤纸的物理过滤、化学过滤和滤饼作用,保证了乳液的过滤精度,且维修方便和一次过滤精度在一定范围内可控。
67.步骤s5,对所述热轧卷材依次进行第一次冷轧、中间退火以及第二次冷轧,得到铝坯。
68.其中,第一次冷轧后所述热轧卷材的厚度为0.4-1.2mm,所述中间退火的温度为300-420℃,保温时间为1-3小时,所述铝坯的厚度为0.2-0.4mm,中间退火采用氮气保护退火,控制氮气中的氧含量低于500ppm。
69.具体地,为了获得表面质量更好的所述铝坯,所述第一次冷轧和所述第二次冷轧采用不可逆冷轧机进行,同时,所述第一次冷轧和所述第二次冷轧中的工作辊(轧辊)的相对两侧分别安装有尼龙刷辊,轧制时,其与所述工作辊相对旋转,以清除所述工作辊上的异物。另外,还可以轧制参数和轧制油参数进行控制。
70.具体地,所述第一次冷轧和所述第二次冷轧采用中温轧制,并使轧制后的铝坯的温度保持在80-200℃,其中,所述中温的温度为100-200℃。
71.具体地,得到所述铝坯后,还需要进行切边,以保证获取更为标准的铝坯。
72.步骤s6、对所述铝坯进行清洗,清洗后的所述铝坯采用150℃的热风烘干。
73.其中,所述清洗的方式依次采用流动水洗、高压碱液喷淋以及漂洗,清洗后所述铝坯的表面的残油小于1mg/m2,铝粉残留小于2mg/m2。
74.具体地,所述高压碱液喷淋时的压力为4-6mpa,碱液中具有0.9-1.1
‰
的葡萄糖酸钠。这样可以阻止水合氧化膜,避免碱渣的形成,同时获得亚光表面的产品。
75.步骤s7、对烘干后所述铝坯依次进行压延、双合以及分切,得到铝箔,再对所述铝箔进行箔轧。
76.其中,所述铝箔的厚度为0.03-0.07mm,所述箔轧采用镜面振动抛光技术进行。
77.具体地,所述箔轧中的轧辊磨削完毕后采用镜面振动抛光技术和多变量参数设计将末道次的所述铝箔的抛光成镜面,以使箔轧后所述铝箔的粗糙度小于0.005μm。所述箔轧通过制控低速,使其轧辊间油膜薄,从而可以使所述铝箔表面更接近其轧辊表面,得到光亮度好的铝塑膜铝箔。
78.步骤s8、对箔轧后的所述铝箔进行最终退火,得到铝塑膜铝箔。
79.其中,所述最终退火采用氮气保护以及负压除油的方式进行,所述铝塑膜铝箔的最终杯突值大于7.5mm。
80.具体地,所述铝塑膜铝箔的晶粒的直径平均小于10.0μm。当然,根据实际需求,还可以进行适应性调整,如小于5.0μm、3.0μm、1.0μm或处于1.0~3.0μm、1.0~5.0μm、1.0~7.0μm、1.0~10.0μm、3.0~5.0μm、3.0~7.0μm、3.0~10.0μm等。
81.具体地,利用金相显微镜(om)对所述铝塑膜铝箔的厚度方向的截面进行观察,对于位于视野内的50个晶粒,将连接晶粒的外延的一点与相同晶粒的外延的另一点的直线距离的最大直径作为最大径x时,便可算出50个晶粒的最大径x的平均值。
82.本发明实施例中的高光亮度铝塑膜铝箔的制备方法通过限定原料配方并采用不同条件的热轧法制备得到8079合金的铝塑膜铝箔,可以使其厚度保持在0.03-0.07mm,抗拉强度保持在70~100mpa,相较于8021合金的铝塑膜铝箔降低10-25mpa,延伸率达到15%以上,含铁量相较于8021合金的铝塑膜铝箔降低0.5%左右,光亮度提升,腐蚀速度降低,只有8021合金的铝塑膜铝箔的65%左右,若将其应用于锂离子电池,在相同的条件下,还能极大程度延长了锂离子电池的最终寿命。
83.图2为现有工艺生产得到的铝塑膜铝箔的光亮度效果与本发明实施例工艺生产得到的铝塑膜铝箔的光亮度效果的对比图,从图中可以看出通过本发明实施例的工艺生产得到的铝塑膜铝箔的光亮度效果更好,得到了提升。
84.图3为现有工艺生产得到的铝塑膜铝箔的杯突值与本发明实施例工艺生产得到的铝塑膜铝箔的杯突值的对比图,从图中可以看出通过本发明实施例的工艺生产得到的铝塑膜铝箔的杯突效果更好,得到了提升。
85.图4为本发明实施例中成分设计的数值模拟之相组成预测示意图;图5为本发明实施例中有限元模拟之均匀化温度预测示意图;图6为本发明实施例中热轧差温轧制的有限元模拟之差温模型示意图。
86.图7为现有工艺生产得到的铝塑膜铝箔的表面形貌与本发明实施例工艺生产得到的铝塑膜铝箔的表面形貌的对比图,从图中可以看出通过本发明实施例的工艺生产得到的铝塑膜铝箔的表面形貌更好,得到了提升。
87.图8为本发明实施例中铝箔的表面凹坑冲压成型减薄后的裂纹到针孔的演变示意图。
88.为了能更高的体现本发明的技术效果,以下将通过具体的原料配方进行举例,具体如下所述:
89.表一为原料配方表
90.元素si/%fe/%cu/%mn/%mg/%zn/%ti/%b/%c/%v/%实施例10.0310.960.0020.00030.0010.0080.01750.002≤0.0030.01-0.02实施例20.0350.750.0010.00080.0010.0070.0180.0010.00010.014实施例30.0240.830.0010.00060.0010.0070.0190.0020.00020.016对比例40.0511.450.0010.0310.0010.0080.0220.0050.00010.014对比例50.1211.550.0020.0280.0010.0080.0180.0070.0040.015
91.表二为工艺条件表
[0092][0093]
表三为检测结果
[0094][0095]
以上五组实施例中,其中实施例1、实施例2及实施例3是以本发明中的限定条件进行的,而实施例4及实施例5则是以现有条件进行的,通过上述表一、表二及表三的对比可以得出,以本发明中的限定条件进行的三个实施例的技术效果在应用于锂离子电池时,各项性能均优于现有条件进行的两个实施例。
[0096]
本发明还提供了一种铝塑膜铝箔,其由上述的高光亮度铝塑膜铝箔的制备方法制成,所述铝塑膜铝箔应用于锂离子电池。
[0097]
本实施例中的铝塑膜铝箔通过采用上述的高光亮度铝塑膜铝箔的制备方法制成,从而可以具备上述的高光亮度铝塑膜铝箔的制备方法所达到的技术效果,同时,在其用于与所述锂离子电池时,还能极大程度的延长锂离子电池的最终寿命。
[0098]
以上所述仅为本发明的实施例,并非因此限制本发明的专利范围,凡是利用本发明说明书及附图内容所作的等效结构或等效流程变换,或直接或间接运用在其它相关的技术领域,均同理包括在本发明的专利保护范围内。