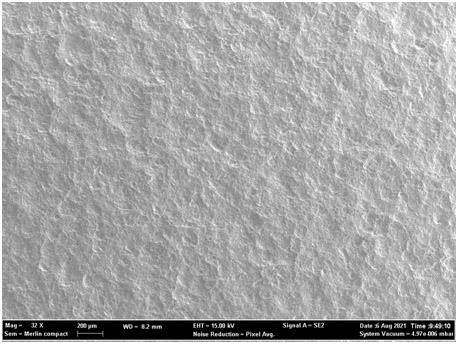
一种汽油车egr用超纯铁素体不锈钢冷轧基料生产工艺
技术领域
1.本发明属于金属冶炼技术领域,涉及一种汽油车egr用超纯铁素体不锈钢冷轧基料生产工艺。
背景技术:2.由于国家对汽车尾气排放提出了新的要求,国内汽车逐步实现国五排放标准转国六排放标准,大部分乘用车主机厂采取新增废气循环再利用系统(egr)来达到尾气排放达标的要求。由于汽油车egr使用环境较柴油车恶劣,使用温度相对较高,故材料的耐高温性能、耐蚀性能以及焊接性能必须优异。材料使用钎焊整体焊接过程对材料的表面要求相对较高,为达到该要求设计的超纯铁素体不锈钢含mo、nb、si等元素较高,故材料在炼钢、连铸、热轧及冷轧等工序中均易发生质量问题。目前市面上主流产品以韩国浦项为主,酒钢2018年已成功开发出汽油车egr用超纯铁素体不锈钢j444e。由于改品种钢使用环境苛刻,故不仅性能要求高,表面质量同样要求高,避免出现麻点、山形压痕、脱皮等缺陷。酒钢针对自有产线开发出一种汽油车egr用超纯铁素体不锈钢冷轧基料生产工艺,通过热处理前预处理及热处理酸洗工艺,很大程度改善了原料表面各种缺陷对冷轧过程的影响,对批量生产质量较好的产品有很大意义。
3.本发明专利考虑汽油车egr用超纯铁素体不锈钢要求较高,炼钢、热轧来料不稳定因素相对较高,热轧轧制后的黑卷通过热处理前处理及合适的热处理酸洗工艺,最终使表面均匀化,给冷轧轧制提供良好的原料。因此,本发明涉及的一种汽油车egr用超纯铁素体不锈钢冷轧基料生产工艺通过改善来料表面缺陷及带来的粗糙影响,从而达到改善汽油车egr用超纯铁素体不锈钢表面综合质量的要求。
技术实现要素:4.本发明的目的在于针对现有技术存在的问题,提供一种汽油车egr用超纯铁素体不锈钢冷轧基料生产工艺,通过对热轧黑卷采取合适的热处理前预处理工艺结合最终热处理及机械化学除磷工艺,达到改善最终产品质量的目的。
5.为此,本发明采取以下技术方案:一种汽油车egr用超纯铁素体不锈钢冷轧基料生产工艺,包括如下步骤:a.热退火酸洗线预处理:对已保温至50-60℃的热轧黑卷料热线采用六辊轧机进行轧制处理,轧制压下率控制到5~10%,对预轧制后的材料不退火处理直接采用破鳞机组对热轧已形成的氧化皮进行初步机械除磷,之后采用抛丸机组进行机械除磷,对抛丸后的材料进行表面重刷处理,通过sic刷毛将表面氧化皮进行再次处理,之后采用硫酸预酸洗和混酸酸洗将黑卷氧化皮完全去除并保证一定的表面下量;b.修磨机组处理:对步骤a处理后的钢卷采用连续四磨头修磨线进行修磨处理,所述连续四磨头修磨线包括1-4号修磨机,所述1号和2号修磨机采用粗修磨砂带进行粗修磨,所述3号和4号修磨机采用旧砂带进行精修磨,钢带上下面各修磨一遍;
c.热退火酸洗线退火酸洗处理:对步骤b中修磨处理后的钢卷进行热退火酸洗处理,所述退火工艺采用材温控制,材温控制范围为990~1010℃,tv值控制范围为100~120mm*m/min,机械除磷及化学除磷继续采用步骤a的工艺,且工艺条件一致,最终得到表面均匀性较好的冷轧机组轧前基料,具体地,tv值指带钢厚度与该厚度下机组允许最高工艺速度的乘积。
6.进一步地,所述步骤a中的破鳞机组采用延伸率模式,延伸率控制在0.5~1%。
7.进一步地,所述步骤a中的抛丸机组的数量为四组,其中,前两组抛丸机采用粒径为800~1000μm的铸丸和切丸的混合丸粒,且铸丸和切丸的比例为4:1,后两组抛丸机采用500~600μm的纯铸丸,所述四组抛丸机的抛速为54~60m/s,流量为7~9kg/m2。
8.进一步地,所述步骤a中的重刷工艺采用投用出入口两组sic重刷辊,均设定为2~4档。
9.进一步地,所述步骤a中的硫酸预酸洗中硫酸预酸洗浓度控制在310~330g/l、酸温控制在85~90℃、金属离子浓度控制在40g/l以内。
10.进一步地,所述步骤a中的混酸酸洗采用硝酸与氢氟酸混合酸,酸浓度分别为80~90g/l和20~25g/l、酸温控制在45~50℃、金属离子浓度控制在20g/l以内。
11.进一步地,所述步骤b中精修磨砂带采用120#砂带且已修磨处理400系不锈钢过钢量达到200~300t为宜,修磨功率50kw。
12.本发明的有益效果在于:1.本发明中热轧黑卷热处理前采用六辊轧机进行轧制,由于热轧已形成的氧化皮与基体膨胀系数有一定差异,通过六辊轧机轧制后氧化皮与基体表面结合力降低,对后续机械除磷和化学除磷提供了良好的条件;2.本发明对破鳞机和抛丸机处理后的材料表面进一步进行均匀机械处理,不但为硫酸预处理提供了良好的条件,对后续材料表面处理后整体表面的均匀度提升有很大作用;3.本发明通过修磨机组对热轧黑卷进行修磨处理,可进一步将热处理线进行预处理后原料残留的表面缺陷进行再次处理,确保将连铸、热轧等带来的原料表面质量缺陷消缺干净;4.本发明对修磨后的材料选择合理的热处理工艺、机械除磷工艺及酸洗工艺,最终得到的冷轧基料表面质量良好。
附图说明
13.图1为实施例1的冷轧基料微观形貌;图2为实施例2的冷轧基料微观形貌。
具体实施方式
14.下面结合附图与实施方法对本发明的技术方案进行相关说明。
15.一种汽油车egr用超纯铁素体不锈钢冷轧基料生产工艺,包括如下步骤:a.热退火酸洗线预处理:对已保温至55℃的热轧黑卷料热线采用六辊轧机进行轧制处理,轧制压下率控制到8%,对预轧制后的材料不退火处理直接采用破鳞机组对热轧已
形成的氧化皮进行初步机械除磷,之后采用抛丸机组进行机械除磷,对抛丸后的材料进行表面重刷处理,通过sic刷毛将表面氧化皮进行再次处理,之后采用硫酸预酸洗和混酸酸洗将黑卷氧化皮完全去除并保证一定的表面下量。
16.具体地,步骤a中的破鳞机组采用延伸率模式,延伸率控制在0.5~1%;抛丸机组的数量为四组,其中,前两组抛丸机采用粒径为800~1000μm的铸丸和切丸的混合丸粒,且铸丸和切丸的比例为4:1,后两组抛丸机采用500~600μm的纯铸丸,所述四组抛丸机的抛速为60m/s,流量为9kg/m2。
17.重刷工艺采用投用出入口两组sic重刷辊,均设定为3档;硫酸预酸洗浓度控制在330g/l、酸温控制在86℃、金属离子浓度控制在40g/l以内;混酸酸洗采用硝酸与氢氟酸混合酸,酸浓度分别为88g/l和25g/l、酸温控制在50℃、金属离子浓度控制在20g/l以内。
18.b.修磨机组处理:对步骤a处理后的钢卷采用连续四磨头修磨线进行修磨处理,所述连续四磨头修磨线包括1-4号修磨机,所述1号和2号修磨机采用120#粗修磨砂带进行粗修磨,所述3号和4号修磨机采用120#旧砂带进行精修磨,钢带上下面各修磨一遍。
19.具体地,步骤b中精修磨砂带采用120#砂带且已修磨处理400系不锈钢过钢量达到200~300t为宜,修磨功率50kw。
20.c.热退火酸洗线退火酸洗处理:对步骤b中修磨处理后的钢卷进行热退火酸洗处理,所述退火工艺采用材温控制,材温控制范围为990~1010℃,tv值控制范围为100~120mm*m/min,机械除磷及化学除磷继续采用步骤a的工艺,且工艺条件一致,最终得到表面均匀性较好的冷轧机组轧前基料。
21.如图1所示,带钢表面为均匀分布的圆润型凹面,相对平整度较高,粗糙度ra达到1.8-2.0μm,对比常规工艺生产的卷粗糙度在3.5-4μm左右,本实施例明显优于目前常规工艺生产的冷轧基料粗糙度。
22.实施例2一种汽油车egr用超纯铁素体不锈钢冷轧基料生产工艺,包括如下步骤:a.热退火酸洗线预处理:对已保温至60℃的热轧黑卷料热线采用六辊轧机进行轧制处理,轧制压下率控制到10%,对预轧制后的材料不退火处理直接采用破鳞机组对热轧已形成的氧化皮进行初步机械除磷,之后采用抛丸机组进行机械除磷,对抛丸后的材料进行表面重刷处理,通过sic刷毛将表面氧化皮进行再次处理,之后采用硫酸预酸洗和混酸酸洗将黑卷氧化皮完全去除并保证一定的表面下量。
23.具体地,步骤a中的破鳞机组采用延伸率模式,延伸率控制在0.5~1%;抛丸机组的数量为四组,其中,前两组抛丸机采用粒径为800~1000μm的铸丸和切丸的混合丸粒,且铸丸和切丸的比例为4:1,后两组抛丸机采用500~600μm的纯铸丸,所述四组抛丸机的抛速为54m/s,流量为7kg/m2。
24.重刷工艺采用投用出入口两组sic重刷辊,均设定为4档,硫酸预酸洗浓度控制在315g/l、酸温控制在88℃、金属离子浓度控制在40g/l以内,混酸酸洗采用硝酸与氢氟酸混合酸,酸浓度分别为80g/l和20g/l、酸温控制在46℃、金属离子浓度控制在20g/l以内。
25.b.修磨机组处理:对步骤a处理后的钢卷采用连续四磨头修磨线进行修磨处理,所述连续四磨头修磨线包括1-4号修磨机,所述1号和2号修磨机采用120#粗修磨砂带进行粗修磨,所述3号和4号修磨机采用120#旧砂带进行精修磨,钢带上下面各修磨一遍。
26.具体地,步骤b中精修磨砂带采用120#砂带且已修磨处理400系不锈钢过钢量达到200~300t为宜,修磨功率50kw。
27.c.热退火酸洗线退火酸洗处理:对步骤b中修磨处理后的钢卷进行热退火酸洗处理,所述退火工艺采用材温控制,材温控制范围为990~1010℃,tv值控制范围为100~120mm*m/min,机械除磷及化学除磷继续采用步骤a的工艺,且工艺条件一致,最终得到表面均匀性较好的冷轧机组轧前基料。
28.如图2所示,带钢表面同样为均匀分布的圆润型凹面,相对平整度较高,粗糙度ra达到1.8-2.0μm,对比常规工艺生产的卷粗糙度在3.5-4μm左右,本实施例明显优于目前常规工艺生产的冷轧基料粗糙度。