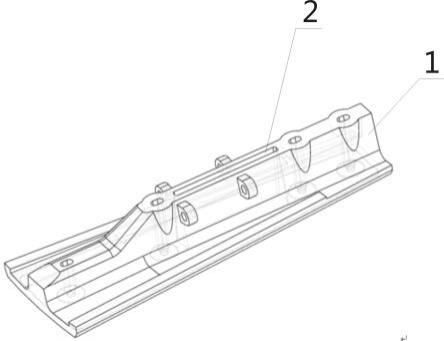
1.本发明涉及磨机衬板制造技术领域,尤其是涉及一种复合镶嵌衬板的制造方法。
背景技术:2.公知的,矿业在国民经济社会发展中的地位举足轻重,伴随国家工业化和城镇化水平的加速推进,基础设施建设进一步的发展,对于能源、金属等大宗商品的需求非常高,带动矿业商品市场趋势向好。
3.随着富矿枯竭,矿山品位持续下降,以及能源开采费用的增加,大型高效粉磨装备已成为选矿厂中的主流设备,矿山装备大型化发展已得到迅猛发展。目前世界最大自磨机规格已达到φ12.2
×
11m,在运行、世界最大半自磨机规格已达到φ12.2
×
7.6m。在此条件下,作为易磨损件,耐磨衬板的结构、尺寸亦变得更加复杂和厚大。与此同时,客户对长寿命耐磨衬板、衬板的等倍寿命更换等也提出了更高的要求。目前大型自磨机衬板在使用过程中,由于自磨机物料填充率较高,达到30-35%,物料规格较大,最大直径达到φ300mm,造成磨机衬板长时间处于与物料的反复研磨状态,局部磨损过快失效过早,对衬板整体寿命、处理矿量及衬板更换产生较大影响,是较为突出的薄弱点。
技术实现要素:4.为了克服背景技术中的不足,本发明公开了一种复合镶嵌衬板的制造方法。
5.为了实现所述发明目的,本发明采用如下技术方案:一种复合镶嵌衬板的制造方法,根据自磨机衬板现场使用结果,结合3d扫描分析技术,通过研究衬板的磨损规律,确定衬板高磨损区域,对高磨损区域进行复合镶嵌处理,具体操作步骤如下所述:(1)、在原结构衬板的高磨损区域设置工作面宽度小、装配面宽度大的锥形腔体结构,同时保证衬板最小壁厚>35mm,且腔体高度与衬板高度等同,形成基体衬板;(2)、根据基体衬板锥形腔体结构的特点,设计耐磨块的外形结构,耐磨块设置为多块的分体式结构,其整体结构为锥形且与锥形腔体结构相同,与基体衬板的锥形型腔保留单边1-3mm装配间隙,且装配面的间隙大于工作面间隙;(3)、对上述的基体衬板及耐磨块进行精整打磨后,对基体衬板锥形腔体的工作面腔体口的对应位置放置泡沫板密封,并将基体衬板工作面朝下、装配面朝上摆放,支垫平整稳固;(4)、将衬板填充胶放入容器内搅拌均匀,将耐磨块起吊放入容器内的衬板填充胶里浸涂,起吊面不浸涂;(5)、接上一步骤,将浸涂后的耐磨块依次放入基体衬板的锥形腔体内,调整好间隙后沿着缝隙灌入衬板填充胶,灌入时适当活动耐磨块,便于衬板填充胶充分灌入,灌满为止;(6)、等待十分钟,衬板填充胶液面下降时及时补灌,衬板填充胶液面不再下降后,
等待24小时固化,检验镶嵌质量,即可完成基体衬板与耐磨块的复合镶嵌,形成整体产品。
6.所述的复合镶嵌衬板的制造方法,基体衬板采用低合金钢,各组份的质量百分比为:碳0.80-1.00%;硅0.50-0.80%;锰0.80-1.00%;磷≤0.040%;硫≤0.040%;铬2.00-2.50%;钼0.30-0.50%,余量为铁,采用中频炉熔炼,孕育变质处理+吹氩精炼。
7.所述的复合镶嵌衬板的制造方法,基体衬板浇注方式采用底注式,热处理方式为正火+回火,热处理装炉时对基体衬板锥形腔体进行石棉保护,基体衬板硬度控制在hb330-360,冲击吸收能量kn2控制在30j以上。
8.所述的复合镶嵌衬板的制造方法,耐磨块采用高耐磨材料,各组份的质量百分比为:碳2.50-3.00%;硅0.50-1.00%;锰0.50-1.00%;磷≤0.040%;硫≤0.040%;铬18.0-23.0%;钼1.50-2.00%;铜0.50-1.00%;镍0-0.40%,余量为铁,采用中频炉熔炼,孕育变质处理+吹氩精炼。
9.所述的复合镶嵌衬板的制造方法,耐磨块的热处理方式淬火+回火的,淬火温度为950~1100℃,回火温度为200~250℃,最终获得马氏体组织,硬度达到hrc60。
10.所述的复合镶嵌衬板的制造方法,在多块分体式的耐磨块的底面即装配面上均设置起吊把和减重槽,减重槽深度不超过衬板失效厚度。
11.由于采用了上述技术方案,本发明具有如下有益效果:本发明所述的复合镶嵌衬板的制造方法,通过对基体衬板与耐磨块结构、材料工艺的设计,并选用衬板填充胶,流动性好,收缩率低,抗压强度高,满足设备装配的大间隙填充要求,实现了基体衬板和耐磨块的复合镶嵌。本发明的复合镶嵌过程操作简单,成本低,适当降低了衬板整体重量,解决了因衬板局部耐磨性差、整体提前更换导致金属浪费的问题,大幅提升了衬板整体使用寿命和金属利用率,有利于提升磨矿效率。
附图说明
12.图1是本发明基体衬板的结构示意图。
13.图2是本发明基体衬板的背面结构示意图。
14.图3是本发明耐磨块的结构示意图。
15.图4是本发明耐磨块的镶嵌复合示意图。
16.图中:1、基体衬板;2、锥形腔体;3、耐磨块;4、起吊把;5、减重槽;6、衬板填充胶。
具体实施方式
17.通过下面的实施例可以详细的解释本发明,公开本发明的目的旨在保护本发明范围内的一切技术改进。
18.结合附图1-4所述的复合镶嵌衬板的制造方法,根据自磨机衬板现场使用结果,结合3d扫描分析技术,通过研究衬板的磨损规律,确定衬板高磨损区域,对高磨损区域进行复合镶嵌处理,具体操作步骤如下所述:(1)、在原结构衬板的高磨损区域设置工作面宽度小、装配面宽度大的锥形腔体2结构,同时保证衬板最小壁厚>35mm,且锥形腔体高度与衬板高度等同,形成基体衬板1;基体衬板1采用低合金钢,各组份的质量百分比为:碳0.80-1.00%;硅0.50-0.80%;锰0.80-1.00%;磷≤0.040%;硫≤0.040%;铬2.00-2.50%;钼0.30-0.50%,余量为铁,采用中频炉熔
炼,孕育变质处理+吹氩精炼;基体衬板浇注方式采用底注式,热处理方式为正火+回火,热处理装炉时对基体衬板1锥形腔体2进行石棉保护,基体衬板硬度控制在hb330-360,冲击吸收能量kn2控制在30j以上(2)、根据基体衬板1锥形腔体2结构的特点,设计耐磨块3的外形结构,耐磨块3设置为多块的分体式结构,其整体结构为锥形且与锥形腔体2结构相同,与基体衬板1的锥形型腔2保留单边1-3mm装配间隙,且装配面的间隙大于工作面间隙;在多块分体式的耐磨块3的底面即装配面上均设置起吊把4和减重槽5,减重槽5深度不超过衬板失效厚度;耐磨块3采用高耐磨材料,各组份的质量百分比为:碳2.50-3.00%;硅0.50-1.00%;锰0.50-1.00%;磷≤0.040%;硫≤0.040%;铬18.0-23.0%;钼1.50-2.00%;铜0.50-1.00%;镍0-0.40%,余量为铁,采用中频炉熔炼,孕育变质处理+吹氩精炼;耐磨块的热处理方式淬火+回火的,淬火温度为950~1100℃,回火温度为200~250℃,最终获得马氏体组织,硬度达到hrc60。
19.(3)、对上述的基体衬板1及耐磨块3进行精整打磨后,对基体衬板1锥形腔体2的工作面腔体口的对应位置放置泡沫板密封,并将基体衬板1工作面朝下、装配面朝上摆放,支垫平整稳固;(4)、将衬板填充胶6放入容器内搅拌均匀,将耐磨块3起吊放入容器内的衬板填充胶里浸涂,起吊面不浸涂;耐磨块3选用流动性好,收缩率低,抗压强度高,且满足设备装配的大间隙的充填要求,优选北京天山 ts99 高性能衬板填充胶、太森 ts6503 背衬胶或德邦 3496 破碎机背衬填充材料;(5)、接上一步骤,将浸涂后的耐磨块依次放入基体衬板的锥形腔体内,调整好间隙后沿着缝隙灌入衬板填充胶,灌入时适当活动耐磨块,便于衬板填充胶充分灌入,灌满为止;(6)、等待十分钟,衬板填充胶液面下降时及时补灌,衬板填充胶液面不再下降后,等待24小时固化,检验镶嵌质量,即可完成基体衬板与耐磨块的复合镶嵌,形成整体产品。
20.本发明所述的复合镶嵌衬板的制造方法,制造的进料端外圈衬板在国外某矿大型自磨机上获得应用,经验证,复合镶嵌衬板使用寿命较一般结构衬板提升约30%。
21.本发明未详述部分为现有技术。
22.为了公开本发明的发明目的而在本文中选用的实施例,当前认为是适宜的,但是,应了解的是,本发明旨在包括一切属于本构思和发明范围内的实施例的所有变化和改进。