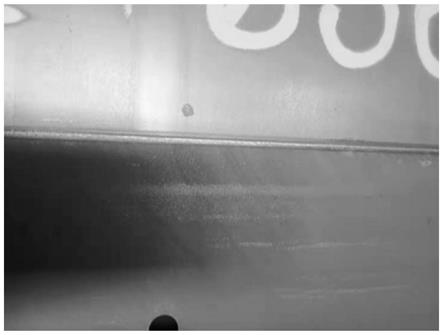
980mpa级低屈强比冷轧双相钢及其酸轧工序的焊接方法
技术领域
1.本发明涉及轧钢生产工艺技术领域,尤其涉及一种980mpa级低屈强比冷轧双相钢以及一种用于980mpa级低屈强比冷轧双相钢酸轧工序的焊接方法。
背景技术:2.利用焊接设备将前后两个钢卷焊接起来实现钢铁企业的连续生产,是提高生产效率、降低生产成本的重要工艺技术手段。被广泛应用于酸轧联合生机组、连续退火/镀锌机组等以实现连续高效的生产。激光焊是一种通过聚焦的激光束作为能源轰击焊件所产生的热量进行焊接的方法。由于激光具有折射、聚焦等光学性质,使得激光焊具有热输入低、焊接变形小,不受电磁场影响等特点被广泛应用于酸轧联合机组进行原料的焊接。若焊接效果不加,容易在酸洗和冷轧过程中发生沿焊缝断带事故,不利于连续生产严重影响生产效率和生产安全,需要对其生产节奏、过渡材、焊接关键工艺等进行详细研究,以便获得良好的焊接质量促进连续、高效的生产。
3.公开号为cn 112025081a的专利文献公开了一种激光焊机焊接qp980及以上超高强钢焊接方法,包括以下步骤:1)调整激光焊机的工作流程,先调整入口段,再调整出口段,最后调整中间段;2)调整保护气喷嘴位置;3)调整横吹气压;4)过渡料选择;5)采用水冷装置降温;6)优化焊接参数;7)采用qcds焊缝检测系统实时监控焊缝质量;8)优化预热及退火装置;9)生产焊接之前的设备维护,实现了碳当量为0.575%以上焊接性较差qp980的生产,但该技术方案对生产节奏、过渡材选择依据、原料要求、带头/尾处理、气体保护以及焊缝质量评估等进行介绍,不利于焊接全流程的指导,对国内外相同类型设备生产980mpa级低屈强比冷轧双相钢的推广不利。
4.公开号为cn 104842056a的专利文献公开了一种超高强双相钢激光拼焊板焊缝增塑装置及工艺,通过将超高强双相钢拼焊板的焊缝置于导热材料与冷却板之间,保证焊接板材的平整度的同时采用电磁吸盘精确定位对材料进行装配;接通高频加热线圈调整输出功率,保证输出温度800~850℃,保温时间3~5min,对焊缝组织进行奥氏体化;采用注有冷却液的冷却板对超高强双相钢拼焊板的焊缝进行快速冷却;调整高频加热线圈输出功率,保证输出温度250-300℃,保温5~30s;降低冷却液流速,提高高频加热线圈输出功率,保证输出温度300~380℃,保温时间10~90s,对焊缝进行局部配分过程;将高频加热线圈输出功率减小到零;采用注有冷却液的冷却板对超高强双相钢拼焊板的焊缝进行快速冷却至室温。得到的焊缝晶粒尺寸平均值1.5μm-4.0μm,超高强钢双相钢拼焊板杯突值为7.3~9.9mm,拼焊板杯突值提高了43%。但该技术方案对生产节奏、过渡材选择依据、原料要求、带头/尾处理、焊接关键工艺参数等未进行详述,且设备进行了特殊改造,不利于使用常规机组完成酸轧原料的焊接。
5.公开号为cn 113118630a的专利文献公开了一种差厚度激光拼焊板的制备方法,将两块厚度(厚度差≤0.5mm,c含量差≤0.03%,mn含量差≤0.4%)不同的dp钢板净化处理后,冷却风干后置于焊接工作台。dp钢板的水平间隙为0mm,垂直方向的间隙为0.05~
0.08mm,焊接过程中,离焦量为0.2~1.0mm;激光功率为3.7~4.2kw;焊接速度5.0~8.0m/min;激光偏移量为0.4~0.7mm,采用保护气体测吹装置吹气,吹气口距离焊缝20~28mm;测吹装置吹气口与待焊dp钢板之间呈30~60
°
保护气体为氩气,气体流量为900~1000l/h;实现了590dp和780dp成品进行了焊接。但该技术方案的成品焊接厚度较薄且未对生产节奏、过渡材选择提供依据,不能对980mpa级低屈强比冷轧双相钢酸轧工序的焊接方法提供指导。
技术实现要素:6.本发明所要解决的技术问题是:提供一种能确保酸轧工序稳定、高效生产的980mpa级低屈强比冷轧双相钢。
7.为解决上述技术问题本发明所采用的技术方案是:980mpa级低屈强比冷轧双相钢,按重量百分比计包括c:0.10~0.17%、si:0.45~1.00%、mn:1.60~2.40%、p≤0.015%、s≤0.008%、als:0.010~0.080%、n≤0.008%、cr:0.20~0.80%、v:0.02~0.12%;其余元素为fe及不可避免的杂质。
8.进一步的是:按重量百分比计包括c:0.10~0.15%、si:0.45~0.85%、mn:1.75~2.30%、p≤0.010%、s≤0.005%、al:0.025~0.065%、n≤0.004%、cr:0.30~0.70%、v:0.045~0.10%;其余元素为fe及不可避免的杂质。
9.本发明还公开了用于上述980mpa级低屈强比冷轧双相钢酸轧工序的焊接方法,所采用的技术方案是:所述焊接选用980mpa级低屈强比冷轧双相钢作为衔接材,将衔接材和原料钢卷剪切后,使衔接材和原料钢卷的焊接面对齐并处于同一水平面上再添加焊丝进行焊接,焊接后对焊缝进行焊后退火、打磨处理,并通过测量焊缝厚度、杯突试验对焊缝质量进行检查;
10.其中,钢卷焊接前需冷却至≤60℃,焊接前后的两个钢卷中强度较高带钢的屈服强度应低于强度较低钢带屈服强度的1.3倍;
11.焊接所选用衔接材的碳当量按照下述公式计算的数值控制在0.25~0.65范围内,所述碳当量公式为ceq=c+mn/6+si/24+ni/40+cr/5+mo/4+v/14(%);
12.焊丝的化学成分为c:0.02~0.15%、si:0.55~1.0%、mn:1.35~1.90%、p≤0.030%、s≤0.030%、cu≤0.50%、ti+zr:0.02~0.30%、al:0.10~0.50%;
13.焊接后通过热循环对焊缝进行热处理,功率为40kw,频率为30khz,焊缝热处理电流补偿量为0~15%,焊缝热处理的加热过程中要求加热速度≤20℃/s,冷却时以冷速≤15℃/s冷却至300℃以下后进行空冷。
14.进一步的是:所述剪切采用双切剪,剪切过程中剪刃与钢带之间的倾角为2
°
,剪刃间隙范围控制为0.30~0.65mm。
15.进一步的是:所述剪刃间隙的控制根据钢带厚度按下述要求确定,当带钢厚度≤2.5mm时剪刃间隙为0.30mm,带钢厚度每增加0.5mm则剪刃间隙增加0.05mm;剪刃按照周期≤7800t或剪切次数≤13500次进行更换,每次更换剪刃后都应对剪刃的侧间隙进行标定,确保剪切横截面与带钢纵向成90
°
,且需确保证剪切端面光滑、平直,无毛刺、分层等缺陷。
16.进一步的是:剪切时,钢卷的切除长度按照下述要求进行控制,保证板形及表面质量后进行焊接;
17.所述切除长度控制要求为:当带钢厚度t<2.75mm时切除长度为6.5mm,当2.75mm≤带钢厚度t<4.0mm时切除长度为5.6mm,当带钢厚度t≥4.0mm时切除长度为4.8mm,并确保带头带尾的缺陷能完全切除,不会恶化焊接质量。
18.进一步的是:所述带钢的表面平直度要求为≤230umit,镰刀弯要求为≤20mm/10m,h
c-h
40
的凸度要求为≤130μm。
19.进一步的是:所述焊接采用激光焊机进行焊接,焊机厚度的跳跃范围≤1.4h1,宽度的跳跃范围≤300mm且每侧≤150mm,其中,h1为较薄带钢的厚度,单位为mm;激光焊接过程中利用聚焦位或光斑位置将激光束聚焦为焊接光斑,聚焦位的高度调节范围为0~9.0mm、z轴控制精度为
±
0.05mm,光斑位置的调节范围为
±
1.5mm、x轴控制精度为
±
0.05mm。
20.进一步的是:所述激光焊接的功率为12
±
0.8kw,焊接速度按照带钢厚度控制为2.1~4.4
±
0.3m/min,喂丝速度按照带钢厚度控制为1.9~4.0
±
0.3m/min;焊接过程中全程通入气体保护,保护气体为he、n2和co的混合气体,焊接时的辅助气体为he;焊接完成后采用碾压轮对焊缝进行清理,碾压轮的压力≤60kn、碾压轮的高度为0~7.5mm;
21.其中,当带钢厚度≤2.5mm时焊接速度为4.4
±
0.3m/min,带钢厚度每增加0.5mm则焊接速度降低0.3m/min,焊接速度的补偿范围为0~15%;当带钢厚度≤2.5mm时喂丝速度为1.5
±
0.3m/min,带钢厚度每增加0.5mm则焊接速度增加0.3m/min,喂丝速度的补偿范围为0~15%;
22.焊接保护气体中he的流量为45~51nl/h,n2的流量为8.0~12.0nl/h,co的流量为1.8~2.3nl/h,混合气体的露点≤-50℃、压力为0.4~0.7mpa、温度为5~50℃;
23.辅助气体he的流量为90~160nl/min、压力为0.4~0.7mpa、温度为5~50℃。
24.进一步的是:所述焊接过程中,焊缝的厚度为原料钢带厚度的1.02~1.15倍;焊缝取样进行杯突试验时,取样点数至少为3个,左右两个点取在距边部100~200mm范围内,第三个点取在钢带的中部,取样点冲孔孔径为15mm且冲孔距离焊缝100mm;
25.杯突试验的要求为,若裂口在热影响区及时裂口垂直于焊缝方向以及裂口垂直于焊缝方向时判定为焊缝合格;若裂口与焊缝重合时则判定为焊缝质量不合格;并且一大卷内不允许有两个焊缝,否则判定为不合格;
26.焊接进行宽度跳跃衔接时需进行冲月牙湾实验,实验要求为,
27.(1)在焊缝处冲切,冲切量为相对于窄带钢宽进去30mm,
28.(2)窄变宽的情况下,从焊缝向入口侧偏离较宽一侧240mm位置处和焊缝处进行两次冲切,
29.(3)宽变窄的情况下,从焊缝向出口侧偏离较宽一侧240mm的位置处和焊缝处进行两次冲切,
30.经实验无问题后方可进行宽度跳跃钢卷的过渡。
31.本发明的有益效果是:本发明通过对980mpa级低屈强比冷轧双相钢的组分按c:0.10~0.17%、si:0.45~1.00%、mn:1.60~2.40%、p≤0.015%、s≤0.008%、als:0.010~0.080%、n≤0.008%、cr:0.20~0.80%、v:0.02~0.12%;其余元素为fe及不可避免的杂质进行控制,并在酸轧前按下述方法进行焊接,即选用980mpa级低屈强比冷轧双相钢作为衔接材,将衔接材和原料钢卷剪切后,使衔接材和原料钢卷的焊接面对齐并处于同一水
平面上再进行焊接,焊接后对焊缝进行焊后退火、打磨处理,并通过测量焊缝厚度、杯突试验对焊缝质量进行检查;钢卷焊接前需冷却至≤60℃,焊接前后的两个钢卷中强度较高带钢的屈服强度应不高于强度较低钢带屈服强度的1.3倍;焊接所选用衔接材的碳当量的数值控制在0.25~0.65范围内,所述碳当量公式为ceq=c+mn/6+si/24+ni/40+cr/5+mo/4+v/14(%)。从而有效的解决了现有技术存在的生产过程中不稳,生产效率不高的技术问题,达到了提供一种能保证980mpa级低屈强比冷轧双相钢酸轧工序生产稳定、高效的目的。
附图说明
32.图1为本发明焊接后焊缝质量的示意图。
具体实施方式
33.为了便于理解本发明,下面结合附图及实施例对本发明进行进一步的说明。
34.本发明所公开的980mpa级低屈强比冷轧双相钢,按重量百分比计包括c:0.10~0.17%、si:0.45~1.00%、mn:1.60~2.40%、p≤0.015%、s≤0.008%、als:0.010~0.080%、n≤0.008%、cr:0.20~0.80%、v:0.02~0.12%;其余元素为fe及不可避免的杂质。本发明所公开的用于上述980mpa级低屈强比冷轧双相钢酸轧工序的焊接方法为焊接选用980mpa级低屈强比冷轧双相钢作为衔接材,将衔接材和原料钢卷剪切后,使衔接材和原料钢卷的焊接面对齐并处于同一水平面上再进行焊接,焊接后对焊缝进行焊后退火、打磨处理,并通过测量焊缝厚度、杯突试验对焊缝质量进行检查;钢卷焊接前需冷却至≤60℃,焊接前后的两个钢卷中强度较高带钢的屈服强度应低于强度较低钢带屈服强度的1.3倍;焊接所选用衔接材的碳当量按照下述公式计算的数值控制在0.25~0.65范围内,所采用的的碳当量公式为ceq=c+mn/6+si/24+ni/40+cr/5+mo/4+v/14(%)。本发明所公开的用于980mpa级低屈强比冷轧双相钢酸轧工序的焊接方法通过对衔接材料的包括温度、平直度、镰刀弯和凸度在内的材质参数、厚度/宽度过渡、表面质量良、剪切工艺及质量、以及包括焊丝选择、激光功率、焊接速度等关键焊接工艺进行调控,如图1所示,获得了表面光滑、无裂缝,焊缝区不存在夹杂、未焊透、错边等缺陷的焊缝,确保了酸解工序稳定、高效的生产,能够对国内外相类似机组生产980mpa级低屈强比冷轧双相钢提供指导。
35.根据实际需要还可对980mpa级低屈强比冷轧双相钢组分进行进一步优化,按重量百分比计包括c:0.10~0.15%、si:0.45~0.85%、mn:1.75~2.30%、p≤0.010%、s≤0.005%、al:0.025~0.065%、n≤0.004%、cr:0.30~0.70%、v:0.045~0.10%;其余元素为fe及不可避免的杂质。
36.本发明所公开的焊接方法中,在选用原料钢卷时,要求原料表面要求不得有严重的凹凸印、划伤、折皱,目视正常的热轧氧化铁皮,不得存在超出标准的缺陷,同时需焊接钢卷的浪形、翘曲等不宜过大。焊接的原料钢卷厚度范围为2.2~6.0mm、宽度范围为850~1500mm。在选用980mpa级低屈强比冷轧双相钢作为衔接材时,衔接材的表面平直度要求为≤230umit,镰刀弯要求为≤20mm/10m,h
c-h
40
的凸度要求为≤130μm。
37.本发明的焊接方法在进行焊接前需要对先衔接材和原料钢卷进行剪切,剪切采用双切剪,剪切过程中剪刃与钢带之间的倾角为2
°
,前一个钢卷尾部与后一个钢卷的头部在焊接前需用双切剪切除一定长度保证板形及表明质量后方可进行焊接,剪刃间隙范围控制
为0.30~0.65mm;具体的剪刃间隙的控制根据钢带厚度按下述要求确定,当带钢厚度≤2.5mm时剪刃间隙为0.30mm,带钢厚度每增加0.5mm则剪刃间隙增加0.05mm;剪刃按照周期≤7800t或剪切次数≤13500次进行更换,每次更换剪刃后都应对剪刃的侧间隙进行标定,确保剪切横截面与带钢纵向成90
°
,且需确保证剪切端面光滑、平直,无毛刺、分层等缺陷。
38.另外,剪切时,钢卷的切除长度按照下述要求进行控制,保证板形及表面质量后进行焊接;所述切除长度控制要求为:当带钢厚度t<2.75mm时切除长度为6.5mm,当2.75mm≤带钢厚度t<4.0mm时切除长度为5.6mm,当带钢厚度t≥4.0mm时切除长度为4.8mm,并确保带头带尾的缺陷能完全切除,不会恶化焊接质量。
39.本发明的焊接方法中采用激光焊接进行焊接,焊机厚度的跳跃范围≤1.4h1,宽度的跳跃范围≤300mm且每侧≤150mm,其中,h1为较薄带钢的厚度,单位为mm;激光焊接过程中利用聚焦位或光斑位置将激光束聚焦为焊接光斑,聚焦位的高度调节范围为0~9.0mm、z轴控制精度为
±
0.05mm,光斑位置的调节范围为
±
1.5mm、x轴控制精度为
±
0.05mm。激光焊接的功率为12
±
0.8kw,焊接速度按照带钢厚度控制为2.1~4.4
±
0.3m/min;焊接过程中全程通入气体保护,保护气体为he、n2和co的混合气体,焊接时的辅助气体为he。
40.由于980mpa级低屈强比冷轧双相钢的合金含量较高且焊接性能不良,焊接过程中需要添加焊丝辅助焊接,焊丝的化学成分为c:0.02~0.15%、si:0.55~1.0%、mn:1.35~1.90%、p≤0.030%、s≤0.030%、cu≤0.50%、ti+zr:0.02~0.30%、al:0.10~0.50%;焊丝的直径为0.9mm,采用焊丝辅助焊接后既可填充焊缝低于带钢的部份以改善特殊钢焊缝区域的性能又可以消除缝隙间的空白区域。焊接完成后采用碾压轮对焊缝进行清理,碾压轮的压力≤60kn、碾压轮的高度为0~7.5mm;其中,当带钢厚度≤2.5mm时焊接速度为4.4
±
0.3m/min,带钢厚度每增加0.5mm则焊接速度降低0.3m/min,焊接速度的补偿范围为0~15%;当带钢厚度≤2.5mm时喂丝速度为1.5
±
0.3m/min,带钢厚度每增加0.5mm则焊接速度增加0.3m/min,喂丝速度的补偿范围为0~15%;焊接保护气体中he的流量为45~51nl/h,n2的流量为8.0~12.0nl/h,co的流量为1.8~2.3nl/h,混合气体的露点≤-50℃、压力为0.4~0.7mpa、温度为5~50℃;辅助气体he的流量为90~160nl/min、压力为0.4~0.7mpa、温度为5~50℃。焊接过程中,焊缝的厚度为原料钢带厚度的1.02~1.15倍。
41.焊接后通过热循环对焊缝进行热处理,功率为40kw,频率为30khz,焊缝热处理电流补偿量为0~15%,焊缝热处理的加热过程中要求加热速度≤20℃/s,冷却时以冷速≤15℃/s冷却至300℃以下后进行空冷。焊接完成后的焊缝需要经焊后退火、打磨后,表面要求光滑、无裂缝,且焊缝区不能存在夹杂、未焊透、错边等缺陷,此外需通过测量焊缝厚度、杯突试验对焊缝质量进行检查。
42.焊缝取样进行杯突试验时,取样点数至少为3个,左右两个点取在距边部100~200mm范围内,第三个点取在钢带的中部,取样点冲孔孔径为15mm且冲孔距离焊缝100mm;杯突试验的要求为,若裂口在热影响区及时裂口垂直于焊缝方向以及裂口垂直于焊缝方向时判定为焊缝合格;若裂口与焊缝重合时则判定为焊缝质量不合格;并且一大卷内不允许有两个焊缝,否则判定为不合格;焊接进行宽度跳跃衔接时需进行冲月牙湾实验,实验要求如下:
43.(1)在焊缝处冲切,冲切量为相对于窄带钢宽进去30mm,
44.(2)窄变宽的情况下,从焊缝向入口侧偏离较宽一侧240mm位置处和焊缝处进行两
次冲切,
45.(3)宽变窄的情况下,从焊缝向出口侧偏离较宽一侧240mm的位置处和焊缝处进行两次冲切,
46.经实验无问题后方可进行宽度跳跃钢卷的过渡。
47.实施例
48.实施例1
49.将钢卷温度为42℃、尺寸规划为4.35*1280mm的980mpa级低屈强比冷轧双相钢(化学成分为0.140%c、0.56%si、2.03%mn、0.009%p、0.003%s、0.040%als、0.53%cr、0.072%v,其碳当量为0.60)钢卷的带尾剪切除5.6mm后,与温度为47℃、尺寸规格为4.20*1265mm的980mpa级低屈强比冷轧双相钢(化学成分为0.130%c、0.61%si、2.07%mn、0.011%p、0.003%s、0.036%als、0.52%cr、0.068%v,其碳当量为0.58)钢卷的带头剪切5.8mm,采用焊接电流为12.5kw配合以2.1m/min的喂丝速度将焊丝(化学成分为0.11%c、0.60%si、2.04%mn、0.015%p、0.008%s、0.010%cu、0.030%ti、0.15%al)并以3.2m/min的速度进行焊接。经上述焊接工艺焊接后的焊缝平整光滑,无结瘤,无焊疤,无焊穿,杯突试验未出现沿焊缝开裂、冲月牙弯效果良好,在酸洗和冷轧过程中均未出现焊缝导致的断带事故。
50.实施例2
51.将钢卷温度为40℃、尺寸规划为3.60*1330mm的980mpa级低屈强比冷轧双相钢(化学成分为0.138%c、0.57%si、1.98%mn、0.009%p、0.002%s、0.041%als、0.075%v,其碳当量为0.62)钢卷的带尾剪切除5.6mm后,与温度为42℃、尺寸规格为3.50*1315mm的热镀锌780dp(化学成分为0.10%c、0.26%si、1.78%mn、0.010%p、0.004%s、0.044%als、0.53%cr、0.27%mo,其碳当量为0.58)钢卷的带头剪切5.2mm,采用焊接电流为12.3kw配合以2.6m/min的喂丝速度将焊丝(化学成分为0.10%c、0.18%si、1.95%mn、0.011%p、0.007%s、0.030%cu、0.018%ti、0.15%al)并以3.3m/min的速度进行焊接。经上述焊接工艺焊接后的焊缝平整光滑,无结瘤,无焊疤,无焊穿,杯突试验未出现沿焊缝开裂、冲月牙弯效果良好,在酸洗和冷轧过程中均未出现焊缝导致的断带事故。
52.对比例1
53.将钢卷温度为53℃、尺寸规划为3.65*1300mm的980mpa级低屈强比冷轧双相钢(化学成分为0.132%c、0.58%si、2.01%mn、0.005%p、0.002%s、0.043%als、0.072%v、0.53%cr,其碳当量为0.60)钢卷的带尾剪切除5.6mm后,与温度为60℃、尺寸规格为4.30*1280mm的dc06(化学成分为0.0018%c、0.01%si、0.07%mn、0.007%p、0.004%s、0.044%als、0.078%ti,其碳当量为0.011)钢卷的带头剪切1.5mm,采用焊接电流为12.5kw配合以3.5m/min的喂丝速度将焊丝(化学成分为0.11%c、0.62%si、1.85%mn、0.015%p、0.008%s、0.010%cu、0.025%ti)并以5.5m/min的速度进行焊接。经上述焊接工艺焊接后的焊缝质量不佳,杯突试验未出现沿焊缝开裂,更改衔接材后进行生产。