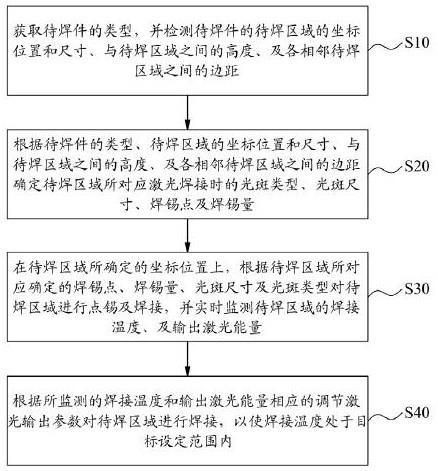
1.本发明属于焊接技术领域,尤其涉及一种激光锡焊方法、装置及系统。
背景技术:2.激光锡焊属于激光加工的一种,它是以激光作为加热源,利用高能量的激光脉冲对材料进行微小区域内的局部加热,使得激光辐射的能量通过热传导向材料的内部扩散而辐射加热引线(或无引线器件的连接焊盘),通过激光锡焊专用焊料(激光焊锡膏/锡丝/锡球或者预制焊料片)向基板传热,当温度达到锡焊料熔点温度时,焊料熔化,基板、引线被焊料润湿,从而形成焊点。由于激光锡焊采用的是非接触式的,局部快速发热,在热能还未完全被传导至不需要焊接点时完成焊接,具有效率快、无机械应力损伤,升温速度快,热影响区小的特点。因此广泛应用于电子工业、汽车电子制造业、智能电器、电子元器件、电机电子、ccm模组、vcm马达线圈等多个领域中。
3.然而现有通常使用激光焊接设备针对同一型号的各个待焊件进行统一批量的自动化焊锡处理,此时工作人员在根据待焊件的元器件类型及其引线类型后确定出所需实施的焊接工艺参数并进行配置,以使对同一型号的各个待焊件均可获得一致的锡焊焊点质量,然而当对不同型号的待焊件进行锡焊处理时,由于不同型号的待焊件的焊盘尺寸、焊点大小、间距、高度等都各不相同,因此其无法存在普适性的焊接工艺参数使得对各个不同型号的待焊件进行锡焊处理,因此每当对不同型号的待焊件进行锡焊处理时,均需要工作人员调试确定出所需实施的焊接工艺参数,使得焊接效率较低,智能化程度较低。
技术实现要素:4.本发明实施例的目的在于提供一种激光锡焊方法,旨在解决现有无法高效的针对各种不同类型待焊件进行焊接的问题。
5.本发明实施例是这样实现的,一种激光锡焊方法,所述方法包括:获取待焊件的类型,并检测所述待焊件的待焊区域的坐标位置和尺寸、与所述待焊区域之间的高度、及各相邻待焊区域之间的边距;根据所述待焊件的类型、所述待焊区域的坐标位置和尺寸、与所述待焊区域之间的高度、及各相邻待焊区域之间的边距确定所述待焊区域所对应激光焊接时的光斑类型、光斑尺寸、焊锡点及焊锡量;在所述待焊区域所确定的坐标位置上,根据所述待焊区域所对应确定的焊锡点、焊锡量、光斑尺寸及光斑类型对所述待焊区域进行点锡及焊接,并实时监测所述待焊区域的焊接温度、及输出激光能量,其中焊接光斑的照射中心作用于所述待焊区域的中心;根据所监测的焊接温度和输出激光能量相应的调节激光输出参数对所述待焊区域进行焊接,以使焊接温度处于目标温度范围内。
6.更进一步地,所述根据所述待焊件的类型、所述待焊区域的坐标位置和尺寸、与所述待焊区域之间的高度、及各相邻待焊区域之间的边距确定所述待焊区域所对应激光焊接
时的光斑类型、光斑尺寸、焊锡点及焊锡量的步骤包括:根据所述待焊件的类型、及各相邻待焊区域之间的边距确定出所述待焊区域所对应激光焊接时的光斑类型;根据所述待焊区域的尺寸、与所述待焊区域之间的高度、及各相邻待焊区域之间的边距确定出所述待焊区域所对应激光焊接时的光斑尺寸;根据所述待焊区域的坐标位置、及与所述待焊区域之间的高度确定出所述待焊区域所对应激光焊接时的焊锡点;根据所述待焊区域的尺寸、及各相邻待焊区域之间的边距确定出所述待焊区域所对应激光焊接时的焊锡量。
7.更进一步地,所述根据所述待焊区域所对应确定的焊锡点、焊锡量、光斑尺寸及光斑类型对所述待焊区域进行点锡及焊接的步骤包括:根据所述待焊区域所对应确定的焊锡点和焊锡量对所述待焊区域进行点锡;根据所述待焊区域所对应确定的光斑尺寸及光斑类型对所述待焊区域进行焊接。
8.更进一步地,所述获取待焊件的类型的步骤包括:获取用户所输入的待焊件的型号;或根据视觉检测机构对待焊件所检测采集的图像信息进行形状和图像的匹配,获取识别到待焊件的型号。
9.更进一步地,所述检测所述待焊件的待焊区域的坐标位置和尺寸、与所述待焊区域之间的高度、及各相邻待焊区域之间的边距的步骤包括:根据测距机构检测与所述待焊区域之间的高度;根据视觉检测机构对待焊件所检测采集的图像信息、及所述测距机构所检测的与所述待焊区域之间的高度,检测确定出待焊区域的坐标位置和尺寸、及各相邻待焊区域之间的边距。
10.更进一步地,所述激光输出参数包括激光脉冲的宽度、能量、峰值功率和重复频率;所述根据所监测的焊接温度和输出激光能量相应的调节激光输出参数对所述待焊区域进行焊接的步骤包括:根据所监测的焊接温度与目标温度范围之间的差值动态调节激光脉冲的宽度、能量、峰值功率及重复频率,以使焊接温度处于目标温度范围内;根据所监测的输出激光能量的波动动态调节激光脉冲的宽度、能量、峰值功率及重复频率,以使焊接温度处于目标温度范围内时稳定所输出的激光能量。
11.更进一步地,所述方法还包括:在对所述待焊区域完成焊接后,检测所述待焊件的焊接是否存在焊接缺陷;若是,则对所述待焊件焊接缺陷的位置重新进行激光焊接。
12.更进一步地,所述光斑类型包括圆形、方形、椭圆形、环形、双焦点型、及一字型。
13.本发明另一实施例的目的还在于提供一种激光锡焊装置,所述装置包括:检测获取模块,用于获取待焊件的类型,并检测所述待焊件的待焊区域的坐标位置和尺寸、与所述待焊区域之间的高度、及各相邻待焊区域之间的边距;参数确定模块,用于根据所述待焊件的类型、所述待焊区域的坐标位置和尺寸、与
所述待焊区域之间的高度、及各相邻待焊区域之间的边距确定所述待焊区域所对应激光焊接时的光斑类型、光斑尺寸、焊锡点及焊锡量;焊接控制模块,用于在所述待焊区域所确定的坐标位置上,根据所述待焊区域所对应确定的焊锡点、焊锡量、光斑尺寸及光斑类型对所述待焊区域依次进行点锡及焊接,并实时监测所述待焊区域的焊接温度、及输出激光能量,其中焊接光斑的照射中心作用于所述待焊区域的中心;焊接调节模块,用于根据所监测的焊接温度和输出激光能量相应的调节激光输出参数对所述待焊区域进行焊接,以使焊接温度处于目标设定范围内。
14.本发明另一实施例的目的还在于提供一种激光锡焊系统,所述系统包括:测距机构,用于检测与待焊件的待焊区域之间的高度;视觉检测机构,用于检测所述待焊件的类型、及与所述测距机构共同检测所述待焊件的待焊区域的坐标位置和尺寸、及各相邻待焊区域之间的边距;点锡机构,用于对所述待焊件的待焊区域进行点锡;焊锡机构,用于对所述待焊件的待焊区域进行激光焊接;传感器机构,用于实时监测所述待焊件的待焊区域的焊接温度、及输出激光能量;及控制机构,用于根据所述测距机构及所述视觉检测机构检测的待焊件的类型、所述待焊件的待焊区域的坐标位置和尺寸、与待焊区域之间的高度、及各相邻待焊区域之间的边距确定出所述待焊区域所对应激光焊接时的光斑类型、光斑尺寸、焊锡点及焊锡量,并根据所述待焊区域所对应确定的焊锡点和焊锡量控制所述点锡机构对所述待焊区域进行点锡,以及根据所述待焊区域所对应确定的光斑尺寸及光斑类型控制所述焊锡机构对所述待焊区域进行焊接,及根据所述传感器机构所监测的焊接温度和输出激光能量相应的控制所述焊锡机构调节激光输出参数对所述待焊区域进行焊接,以使焊接温度处于目标温度范围内直至完成焊接。
15.本发明实施例提供的激光锡焊方法,通过获取检测待焊件的类型,及其待焊件的待焊区域的坐标位置和尺寸、与待焊区域之间的高度、及各相邻待焊区域之间的边距相应的确定出所具体对应激光焊接时的光斑类型、光斑尺寸、焊锡点及焊锡量,并根据光斑类型、光斑尺寸、焊锡点及焊锡量对待焊区域进行相应的点锡及焊接,同时在焊接过程中实时监测待焊区域的焊接温度、及输出激光能量,使得根据所监测的焊接温度和输出激光能量动态的调节激光输出参数,从而使焊接温度维持在目标设定范围内,使得可针对各种不同类型的待焊件进行有效的焊接,解决了现有无法高效的针对各种不同类型待焊件进行焊接的问题。
[0016] 附图说明
[0017]
图1是本发明实施例提供的激光锡焊方法的流程图;图2是本发明实施例提供的激光锡焊方法的又一流程图;图3是本发明实施例提供的激光锡焊装置的结构示意图;图4是本发明实施例提供的激光锡焊装置的又一结构示意图;
图5是本发明实施例提供的激光锡焊系统的结构示意图。
[0018]
具体实施方式
[0019]
为了使本发明的目的、技术方案及优点更加清楚明白,以下结合附图及实施例,对本发明进行进一步详细说明。应当理解,此处所描述的具体实施例仅仅用以解释本发明,并不用于限定本发明。
[0020]
在本发明中,除非另有明确的规定和限定,术语“安装”、“相连”、“连接”、“固定”等术语应做广义理解,例如,可以是固定连接,也可以是可拆卸连接,或一体地连接;可以是机械连接,也可以是电连接;可以是直接相连,也可以通过中间媒介间接相连,可以是两个元件内部的连通。对于本领域的普通技术人员而言,可以根据具体情况理解上述术语在本发明中的具体含义。本文所使用的术语“及/或”包括一个或多个相关的所列项目的任意的和所有的组合。
[0021]
目前,激光锡焊是以激光为热源,利用激光束优良的方向性和高功率密度的特点,通过光学系统将激光束聚集在很小的区域,利用激光束直接照射焊接部位,焊接部位(元器件引线和焊料)吸收光能并转化为热能,温度急剧上升到焊接温度,导致焊料熔化后润湿焊点并更具焊料固有的张力向焊点扩散与焊点的金属层接触后形成合金层,激光加热停止后,焊接部位迅速冷却,焊料凝固,使两者牢牢的结合,从而形成可靠的焊接接头。因此根据激光锡焊的工作原理,其具有如下优点:1、激光加工精度高,光斑小,加工时间程序控制,精度高于传统焊接工艺方式,适用于微小精密件焊锡,焊锡工件对温度比较敏感的场所;2、由于焊接时无需接触,不会给焊接对象造成机械应力,使得可焊接一些其他焊接中易受热损伤或易开裂的元器件,同时解决焊接过程中因接触而带来的静电威胁,使得能在常规方式不易施焊部位进行加工;3、可在元器件密集的电路上对烙铁头无法进入的狭窄部位和在密集组装中相邻元件之间没有距离时变换角度进行照射,而无须对整个电路板加热;其细小的激光束替代烙铁头,使得在元器件表面有其他干涉物时,同样便于加工;4、焊接时仅被焊区域局部加热,其它非焊区域不承受热效应;5、焊接时间短,效率高,并且焊点不会形成较厚的金属间化物层,所以质量可靠;6、可维护性很高,传统电烙铁焊接需要定期更换烙铁头,而激光焊接需要更换的配件极少,因此可以削减维护成本;7、可将入热量降到最低的需要量,热影响区金相变化范围小,且因热传导所导致的变形亦最低;8、能在室温或特殊条件下进行焊接,焊接设备装置简单。例如,激光通过电磁场,光束不会偏移;光在真空、空气及某种气体环境中均能施焊,并能通过玻璃或对光束透明的材料进行焊接;然而现有通常使用激光焊接设备针对同一型号的各个待焊件进行统一批量的自动化焊锡处理,此时工作人员在根据待焊件的元器件类型及其引线类型确定出所需实施的焊接工艺参数并进行配置,以使对同一型号的各个待焊件均可获得一致的锡焊焊点质量,
然而当对不同型号的待焊件进行锡焊处理时,由于不同型号的待焊件的焊盘尺寸、焊点大小、间距、高度等都各不相同,因此其无法存在普适性的焊接工艺参数使得对各个不同型号的待焊件进行锡焊处理,因此每当对不同型号的待焊件进行锡焊处理时,均需要工作人员调试确定出所需实施的焊接工艺参数,使得焊接效率较低,智能化程度较低。本发明通过获取检测待焊件的类型,及其待焊件的待焊区域的坐标位置和尺寸、与待焊区域之间的高度、及各相邻待焊区域之间的边距相应的确定出所具体对应激光焊接时的光斑类型、光斑尺寸、焊锡点及焊锡量,并根据光斑类型、光斑尺寸、焊锡点及焊锡量对待焊区域进行相应的点锡及焊接,同时在焊接过程中实时监测待焊区域的焊接温度、及输出激光能量,使得根据所监测的焊接温度和输出激光能量动态的调节激光输出参数,从而使焊接温度维持在目标设定范围内,使得可针对各种不同类型的待焊件进行有效的焊接。
[0022]
实施例一请参阅图1,是本发明第一实施例提供的激光锡焊方法的流程示意图,为了便于说明,仅示出了与本发明实施例相关的部分,该方法包括:步骤s10,获取待焊件的类型,并检测待焊件的待焊区域的坐标位置和尺寸、与待焊区域之间的高度、及各相邻待焊区域之间的边距;在本发明的一个实施例中,其激光锡焊方法可采用单激光焊接方式或复合激光焊接方法,其中复合激光焊接可解决单激光焊接存在的一些焊接缺陷,如表面成形质量、焊接熔池内的裂纹、气孔等。具体的,复合激光焊接是指采用不同波长的或者不同热源的激光焊接方式,具体采用的是半导体激光和光纤激光复合的方式。其中,在本发明实施例中,其激光锡焊的方式可根据实际使用需要选择上述任一种方式,在此不做具体限定。
[0023]
进一步的,其激光锡焊方法所应用的设备中配备有光学系统(也即激光器)、视觉检测机构及运动单元,具体实施时,其视觉检测机构可采用ccd同轴摄像定位及加工监视系统,其可进行摄像实现图像采集,使得可采集到待焊件的整体或局域的图像信息;同时其视觉检测机构可与光学系统所输出的激光同轴,使得可用于定位待焊件的待焊区域,从而使激光实现对所同轴定位的待焊区域进行锡焊;需要指出的是,其待焊件上存在有多个待焊区域(也即焊接点),其同一待焊件上的各个待焊区域的尺寸、高度等参数信息根据实际使用需要可相同也可不同。同时其视觉检测机构还可对激光焊接过程进行加工监视,使得可清晰呈现焊点并及时矫正对位,保证加工精度和自动化生产。而运动单元可用于驱动光学系统和视觉检测机构的运动。
[0024]
进一步的,在现有技术中,其通常对同一型号的各个待焊件进行统一批量的自动化焊锡处理,因此其工作人员在根据待焊件的元器件类型及其引线类型后确定出所需实施的焊接工艺参数并进行配置,以使对同一型号的各个待焊件均可获得一致的锡焊焊点质量,因此其现有技术不需获取待焊件的型号,而本发明实施例中,为实现在焊锡过程中对各种不同类型的待焊件均进行适应性的焊接工艺参数的调整及配置后进行焊接,因此本发明实施例中,其首先需要获取当前所待焊接的待焊件的类型,以使根据当前待焊件的类型确定出对应的加热参数并进行激光锡焊处理。具体的,其获取待焊件的类型可采用手动化或自动化的处理,具体手动化即为工作人员直接输入当前所待焊接的待焊件的类型,使得实现待焊件的类型获取。具体自动化即为根据图像识别算法相应的识别视觉检测机构所采集的图像信息,使得自动化确定出待焊件的类型。进一步的,其还可以在自动化确定出待焊件
的类型后,工作人员再对所识别的待焊件的类型进行复核,以确定所识别的待焊件的类型是否正确(也即检测自动识别的准确率),同时根据工作人员所复核的结果反馈修正其后续的识别,从而提高所自动化识别的正确率。其中,需要指出的是,其根据该待焊件的类型还可初略确定出各个待焊区域的大致坐标位置、尺寸、各相邻待焊区域之间的边距等相关参数。
[0025]
进一步的,同时由于不同类型的待焊件的待焊区域不同以及待焊件中元器件的类型及位置布局的不同,因此若按照现有统一高度进行激光焊接时,不同类型的待焊件存在各不相同的干涉情况,此时有的待焊件在该高度下存在干涉情况,而有的待焊件在该高度下不存在干涉情况,因此不同类型的待焊件所焊接高度也各不相同。或者在足够高的焊接高度情况下,由于不同类型的待焊件焊接表面高度不同,使得有的待焊件在该高度下与光学系统距离较近,而有的待焊件在该高度下与光学系统又距离较远。因此本发明实施例中,其运动单元带动视觉检测机构在足够高的高度下运动,此时确定出一不会与该待焊件发生干涉的高度,并控制运动单元运动至该高度。或者根据所有预先存储在数据库中的各个类型的元器件确定出不会发生干涉的最低高度,并控制运动单元一直保持在该最低高度进行运动。或者根据所确定的待焊件的类型所对应的具体参数信息调整至相对应的运动高度。
[0026]
进一步的,其激光锡焊方法所应用的设备中还配备有与光学系统所输出的激光同轴的测距机构,具体实施时,其测距机构可以采用激光测距传感器,此时运动单元根据所获取的待焊件的类型带动视觉检测机构运动依次至待焊区域的各个中心位置,其测距机构首先测量出与各个待焊区域的高度,然后其视觉检测机构根据该高度所对应的比例检测出各个待焊区域的坐标位置和尺寸,以及各相邻待焊区域之间的边距。具体例如该待焊件为一焊盘,其各个待焊区域的高度一致,此时视觉检测机构可直接对焊盘的各个焊点进行坐标位置、尺寸以及各相邻焊点之间的边距进行检测。而当待焊区域的高度发生变化时,由于透视现象而使得其视觉检测机构所采集图像中的待焊区域在整体图像中的大小发生变化,此时视觉检测机构若直接根据所采集的图像信息确定待焊区域的尺寸时,则其在后续点锡及焊接过程中,其由于高度位置所发生的改变而使得无法实现准确的点锡高度进行点锡、无法准确的提供焊锡量进行点锡、以及无法准确的配置激光焊接参数进行焊接。
[0027]
因此本发明实施例中,其需要确定与该待焊区域之间的高度,从而实现高度位置补偿,即使当高度位置发生改变时,也可以实现准确点锡而不会产生高度偏移,防止点锡不良;同时根据所确定的与该待焊区域之间的高度可准确的检测出待焊区域的坐标位置和尺寸,以及各相邻待焊区域之间的边距,使得可相应的精确提供焊锡量,以及配置精准的激光焊接参数,从而不会产生由于过量提供焊锡量而导致连焊及堆焊,或由于少量提供焊锡量而导致虚焊的问题。
[0028]
步骤s20,根据待焊件的类型、待焊区域的坐标位置和尺寸、与待焊区域之间的高度、及各相邻待焊区域之间的边距确定待焊区域所对应激光焊接时的光斑类型、光斑尺寸、焊锡点及焊锡量;其中,本发明实施例中,在获取到待焊件的类型、待焊件中各个待焊区域的坐标位置和尺寸、与各个待焊区域之间的高度、及各相邻待焊区域之间的边距后,其相应的根据上述各个参数确定出待焊区域所对应激光焊接时的光斑类型、光斑尺寸、焊锡点及焊锡量。
[0029]
其中,现有激光通常采用圆形光斑,然而其圆形光斑并不适用于所有类型的待焊
件,例如待焊件为细长的矩形焊盘与线束产品时,如果使用圆形光斑,线材和焊盘都无法均匀加热,导致局部温度较高,要么烧毁产品,要么熔锡不彻底,无法覆盖整个焊盘。同时在焊点在高度发生变化时,如果还按照现有的焊锡点高度进行点锡或按照现有的光斑尺寸进行焊接,其均可能产生点锡不良或焊接不良的问题。同时不同的焊点的尺寸大小以及相邻焊点边距也相应的影响其焊锡量,因此如果按照现有的焊锡量进行点锡及焊接,其可能产生连焊、虚焊等问题。
[0030]
因此需要根据不同尺寸的焊盘、不同高度及尺寸的焊接点、相邻焊接点的不同边距,设定不同的焊接工艺参数,建立其与焊接工艺参数一一对应的关系;此时通过视觉检测机构拍照,进行形状和图像匹配,从而识别当前焊盘的尺寸及类型;根据视觉检测机构识别的焊盘以及与测距机构共同检测出的焊盘上各个焊点的坐标位置、尺寸大小、相邻焊接点的边距、及焊点的高度,选择对应的焊接工艺参数,具体的焊接工艺参数包括光斑类型、光斑尺寸、焊锡点及焊锡量。其中,需要指出的是,其光斑类型也即光学设备照射在待焊件上的待焊区域时所呈现的图形类型,其具体例如圆形,矩形等各种形状。其光斑尺寸也即光学设备照射在待焊件上的待焊区域时的尺寸大小。其焊锡点也即点锡机构对待焊件上的待焊区域进行点锡时的点锡高度。其焊锡量也即点锡机构对待焊件上的待焊区域进行点锡时所需的锡料用量。
[0031]
步骤s30,在待焊区域所确定的坐标位置上,根据待焊区域所对应确定的焊锡点、焊锡量、光斑尺寸及光斑类型对待焊区域进行点锡及焊接,并实时监测待焊区域的焊接温度、及输出激光能量;其中,需要指出的是,其激光焊接方式包括锡丝焊接、锡丝焊接、以及锡球焊接。
[0032]
其中锡丝焊接主要包括预热阶段、焊接阶段、及冷却阶段,其中预热阶段中激光出光,对焊盘位置进行预热、实现焊点升温;焊接阶段中送锡装置传送锡丝到焊盘,激光将低于焊件温度高于焊料熔点的能量送到焊盘上,此时在激光和焊盘热量的作用下锡丝融化;冷却阶段中锡丝回抽与焊点脱离,激光逐步减弱到停止,完成焊点成型冷却。
[0033]
其中锡膏焊接主要包括点锡阶段、焊接阶段、及冷却阶段,其中点锡阶段中点锡控制器通过气压精确控制,将锡膏从针筒里挤出并经过针头涂覆到焊点上;焊接阶段中激光缓慢加热锡膏使之融化,并渗透到焊点各部位;冷却阶段中激光逐步减弱到停止,完成焊点成型冷却。
[0034]
其中锡球焊接主要包括上球阶段、喷球阶段、及焊接阶段,其中上球阶段中分球盘转动,锡球从锡球容器掉入到喷嘴里,喷嘴口尺寸略小于锡球,锡球堵住喷嘴口,喷嘴内氮气气压上升;喷球阶段中输出激光,通过激光的高脉冲能量,瞬间熔化置于喷嘴上的锡球,再利用惰性气体的压力作用将熔化后的锡球喷射到焊盘表面,形成互联焊点,同时惰性气体还用于防止锡球在喷出到焊盘过程中氧化;焊接阶段中锡球喷射到焊盘上,在锡球热量与激光的作用下,锡球和焊盘完成融合,惰性气体持续作用,防止锡球和焊盘氧化。
[0035]
其中,本发明实施例中的激光焊接方式具体采用上述所述的锡膏焊接方式,因此其需经上述所述的点锡阶段及焊接阶段,其中由于步骤s20中确定有待焊区域所对应激光焊接时的光斑类型、光斑尺寸、焊锡点及焊锡量,因此在点锡阶段中,其运动单元控制运动至待焊区域的坐标位置上,此时根据焊锡点及焊锡量相应的通过点锡控制器控制针筒的点锡高度(也即焊锡点)以及通过气压精确控制锡膏用量(也即焊锡量),也即控制点锡机构对
待焊区域进行点锡,从而实现对待焊区域的点锡。此时由于点锡高度的确定,使得可以实现高度位置补偿,从而准确点注锡膏,防止点锡不良;同时由于锡膏用量的确定,使得可以实现点注锡膏的精准用量,防止后续的连焊、虚焊等问题的发生。因此其根据上述各种参数所确定光斑类型、光斑尺寸、焊锡点及焊锡量,以及根据所确定的各种信息对相对应的待焊区域进行点锡及焊接,使得即使同一待焊件上的待焊区域的尺寸或高度都不相同的情况下也可实现准确的焊锡点及焊锡量进行点锡,以及所需准确的光斑类型、光斑尺寸进行焊接,使得其自动化及智能化程度高,而现有技术中只能固定程序化的进行固定高度、锡料用量、光斑类型及光斑尺寸的点锡及焊接,使得其在待焊区域尺寸不同的情况下由于固定锡料用量而可能产生连焊或虚焊等问题,其在待焊区域高度不同的情况下由于固定高度而可能产生点锡不良的问题,其在待焊区域高度不同的情况下由于固定激光参数输出而使得激光所照射至待焊区域时出现离焦而改变光斑尺寸的问题。
[0036]
进一步的,其激光锡焊方法所应用的设备中还配备有与光学系统所输出的激光同轴的传感器机构,具体实施时,其传感器机构包括但不限于红外温度传感器、能量检测装置,其中能量检测装置设置于该光学系统的输出端,用于检测输出激光能量的大小。此时在焊接阶段中,其根据光斑类型及光斑尺寸相应的通过光学系统控制相对应的光斑类型及光斑尺寸的激光进行输出,也即控制焊锡机构(也即光学系统)对待焊区域进行焊接,以对待焊区域进行焊接。其中焊接光斑的照射中心作用于待焊区域的中心。其中在焊接的过程中,其传感器机构还实时检测待焊区域的焊接温度、及输出激光能量。
[0037]
此时,需要指出的是,其光学系统、视觉检测机构、测距机构、及传感器机构中多光路同轴设置,避免复杂调试,且光学系统、视觉检测机构、测距机构、及传感器机构均完全独立设置,使得根据实际使用需要选择不同的模块化组合方式。
[0038]
步骤s40,根据所监测的焊接温度和输出激光能量相应的调节激光输出参数对待焊区域进行焊接,以使焊接温度处于目标设定范围内;其中,其根据所监测的焊接温度和输出激光能量相应的调节激光输出参数,具体的,其采用pid温度调节反馈方式进行调节,例如,当监测到的实时焊接温度高于焊接工艺参数对应的设定温度区间的上限值时,控制降低激光输出功率,直到实时焊接温度回到焊接工艺参数对应的设定温度区间内为止,反之当监测到的实时焊接温度低于焊接工艺参数对应的设定温度区间的下限值时,控制升高激光输出功率,直到实时焊接温度回到焊接工艺参数对应的设定温度区间内为止。可以理解的,其激光输出参数除输出功率外还可以包括激光脉冲的宽度、重复频率、占空比等,其主要通过反馈调节方式实现自动调节激光输出参数从而使得焊接温度处于目标设定范围内(也即控制恒温焊接)即可,其调节方式在此不做具体限定。
[0039]
本实施例中,通过获取检测待焊件的类型,及其待焊件的待焊区域的坐标位置和尺寸、与待焊区域之间的高度、及各相邻待焊区域之间的边距相应的确定出所具体对应激光焊接时的光斑类型、光斑尺寸、焊锡点及焊锡量,并根据光斑类型、光斑尺寸、焊锡点及焊锡量对待焊区域进行相应的点锡及焊接,同时在焊接过程中实时监测待焊区域的焊接温度、及输出激光能量,使得根据所监测的焊接温度和输出激光能量动态的调节激光输出参数,从而使焊接温度维持在目标设定范围内,使得可针对各种不同类型的待焊件进行有效的焊接,解决了现有无法高效的针对各种不同类型待焊件进行焊接的问题。
[0040]
实施例二请参阅图2,是本发明第二实施例提供的一种激光锡焊方法的流程示意图,为了便于说明,仅示出了与本发明实施例相关的部分,该第二实施例与第一实施例的方法大抵相同,为简要描述,本实施例中未提及之处,可参考第一实施例中相应内容,具体该方法包括:步骤s11,获取待焊件的类型,并检测待焊件的待焊区域的坐标位置和尺寸、与待焊区域之间的高度、及各相邻待焊区域之间的边距。
[0041]
其中,本发明实施例中,上述获取待焊件的类型可通过多种方式实现,具体本实施例中包括如下两种实现方式:方式一:获取用户所输入的待焊件的型号;方式二:根据视觉检测机构对待焊件所检测采集的图像信息进行形状和图像的匹配,获取识别到待焊件的型号。
[0042]
也即是说,其可以通过方式一实现手动化的确定出待焊件的类型,此时一直需要工作人员选择当前所待焊接的待焊件的具体类型型号,以使根据用户所输入的待焊件的类型相应的进行后续的焊接处理。当然,还可以通过方式二实现自动化的确定出待焊件的类型,此时其视觉检测机构对待焊件进行图像信息的采集,并根据所采集的图像信息与预先存储在数据库中的各个不同类型的元器件进行形状和图像的匹配,以使在所预先存储的数据库中匹配查找出所对应的待焊件的类型,从而相应识别出该待焊件的具体型号。
[0043]
进一步的,在本发明的一个实施例中,上述检测待焊件的待焊区域的坐标位置和尺寸、与待焊区域之间的高度、及各相邻待焊区域之间的边距的步骤包括:根据测距机构检测与待焊区域之间的高度;根据视觉检测机构对待焊件所检测采集的图像信息、及测距机构所检测的与待焊区域之间的高度,检测确定出待焊区域的坐标位置和尺寸、及各相邻待焊区域之间的边距。
[0044]
其中,视觉检测机构对待焊件采集图像信息,而测距机构对待焊区域采集高度信息,此时根据图像信息以及高度信息可相应的确定出其图像中待焊区域的坐标位置和尺寸、及各相邻待焊区域之间的边距。
[0045]
步骤s21,根据待焊件的类型、待焊区域的坐标位置和尺寸、与待焊区域之间的高度、及各相邻待焊区域之间的边距确定待焊区域所对应激光焊接时的光斑类型、光斑尺寸、焊锡点及焊锡量。
[0046]
其中,本发明实施例中,上述根据待焊件的类型、待焊区域的坐标位置和尺寸、与待焊区域之间的高度、及各相邻待焊区域之间的边距确定待焊区域所对应激光焊接时的光斑类型、光斑尺寸、焊锡点及焊锡量可通过如下步骤实现:根据待焊件的类型、及各相邻待焊区域之间的边距确定出待焊区域所对应激光焊接时的光斑类型;根据待焊区域的尺寸、与待焊区域之间的高度、及各相邻待焊区域之间的边距确定出待焊区域所对应激光焊接时的光斑尺寸;根据待焊区域的坐标位置、及与待焊区域之间的高度确定出待焊区域所对应激光焊接时的焊锡点;根据待焊区域的尺寸、及各相邻待焊区域之间的边距确定出待焊区域所对应激光焊接时的焊锡量。
[0047]
其中,上述光斑类型包括圆形、方形、椭圆形、环形、双焦点型、及一字型。进一步的,上述的环形光斑还可由一个中心光斑及环绕于该中心光斑外边的一个环形的外环光斑组成,而且两个光斑都可以实现激光功率和出光时间的实时独立调整。此时可以使用外环光斑的前端对待焊件进行预热,而用中心光斑来进行焊接,然后用外环光斑的后端来稳定熔池,从而减少飞溅、气孔等缺陷,实现更加完美的焊接。
[0048]
其中,上述的双焦点型光斑是通过将光学系统组合透镜进行一系列的改变,光纤发射出来发散的光经过透镜的一系列整形,将一束光分成两束单独的光束,通过机构的精调系统,调节透镜的间距,以此来调节两个光斑的间距。需要指出的是,双焦点型光斑的双光点设计对于规则成对出现的焊点比用单光点焊接效率更高。
[0049]
其中,现有激光通常采用圆形光斑,然而其圆形光斑并不适用于所有类型的待焊件,例如细长的矩形焊盘与线束产品的焊接,如果使用圆形光斑,线材和焊盘都无法均匀加热,导致局部温度较高,要么烧毁产品,要么熔锡不彻底,无法覆盖整个焊盘。而矩形光斑形态可以使得矩形焊盘在加热过程让锡条首位同时受热,因此不会产生锡条变形扭曲而导致的无方位翘曲,使得熔锡的整个过程一蹴而就,可顺利覆盖了整个焊盘;同时矩形光斑形态对于矩形焊点加热填充效果将会更加均匀。比如,方形镀金焊盘,如果用圆形光斑加热,焊盘周边容易脱落,因为热量的不均匀性,可能导致镀金焊盘整个脱落。
[0050]
而在焊接微小焊盘时,如果微小焊盘排列成长长的一排时,不管圆形光斑还是矩形光斑效率都比较低。或者在激光焊接软板密集排线的时候,如果使用单点焊接一个一个去熔锡无疑效率会很低,并且密集型焊点的阻锡带非常窄小,稍有不慎就会连锡,烧毁。因此此时就需要用到一字型光斑,其将激光形状整形成细长的一字,使得可以一口气焊接完十几个焊点。
[0051]
因此,并非所有的待焊件均适用于圆形光斑,此时根据待焊件的类型、及各相邻待焊区域之间的边距确定出待焊区域所对应激光焊接时的光斑类型,使得可以更好的实现对待焊区域的焊接。如上述所述的微小焊盘排列成长长的一排(也即边距较近)时,则可确定采用一字型光斑,使得可有效的提高焊接效率,而根据待焊区域的尺寸、与待焊区域之间的高度、及各相邻待焊区域之间的边距确定出待焊区域所对应激光焊接时的光斑尺寸,其具体为首先根据与待焊区域之间的高度确定出预设激光所照射在待焊区域时对应的实际光斑大小,而根据待焊区域的尺寸及各相邻待焊区域之间的边距确定所需照射在待焊区域时的目标光斑大小,此时根据目标光斑大小相应的调节光学系统的相关参数,使得可将所照射在待焊区域时对应的实际光斑大小最终调整至所需的目标光斑大小。
[0052]
而根据待焊区域的坐标位置、及与待焊区域之间的高度确定出待焊区域所对应激光焊接时的焊锡点,其具体为根据该焊点的位置及高度相应的确定其针筒的点锡高度,使得实现高度补偿以防止点锡不良,当高度位置发生改变时,也可以实现准确点注锡膏;而根据待焊区域的尺寸、及各相邻待焊区域之间的边距确定出待焊区域所对应激光焊接时的焊锡量,其具体为根据该焊点的尺寸大小及相邻焊点边距相应的确定所不会连焊及虚焊的焊锡量,使得保证使用该焊锡量精准焊接时,不会产生虚焊、连焊的问题。
[0053]
步骤s31,在待焊区域所确定的坐标位置上,根据待焊区域所对应确定的焊锡点、焊锡量、光斑尺寸及光斑类型对待焊区域进行点锡及焊接,并实时监测待焊区域的焊接温
度、及输出激光能量;其中,本发明实施例中,上述根据待焊区域所对应确定的焊锡点、焊锡量、光斑尺寸及光斑类型对待焊区域进行点锡及焊接可提高如下步骤实现:根据待焊区域所对应确定的焊锡点和焊锡量对待焊区域进行点锡;根据待焊区域所对应确定的光斑尺寸及光斑类型对待焊区域进行焊接。
[0054]
其中,在点锡阶段中,其运动单元控制运动至待焊区域的坐标位置上,此时根据焊锡点及焊锡量相应的通过点锡控制器控制针筒的点锡高度(也即焊锡点)以及通过气压精确控制锡膏用量(也即焊锡量),从而实现对待焊区域的点锡。
[0055]
进一步的,在焊接阶段中,其根据光斑类型及光斑尺寸相应的通过光学系统控制相对应的光斑类型及光斑尺寸的激光进行输出,以对待焊区域进行焊接。其中焊接光斑的照射中心作用于待焊区域的中心。其中在焊接的过程中,其传感器机构还实时检测待焊区域的焊接温度、及输出激光能量。
[0056]
步骤s41,根据所监测的焊接温度和输出激光能量相应的调节激光输出参数对待焊区域进行焊接,以使焊接温度处于目标设定范围内。
[0057]
其中,激光输出参数包括激光脉冲的宽度、能量、峰值功率和重复频率;上述根据所监测的焊接温度和输出激光能量相应的调节激光输出参数对待焊区域进行焊接的步骤包括:根据所监测的焊接温度与目标温度范围之间的差值动态调节激光脉冲的宽度、能量、峰值功率及重复频率,以使焊接温度处于目标温度范围内;根据所监测的输出激光能量的波动动态调节激光脉冲的宽度、能量、峰值功率及重复频率,以使焊接温度处于目标温度范围内时稳定所输出的激光能量。
[0058]
具体的,温度反馈控制原理为:通过红外检测方式,实时检测激光对待焊件的红外热辐射,形成激光焊接温度和检测温度的闭环控制,通过pid的计算调节,可以有效控制激光焊接温度在设定范围波动。具体例如,当监测到的实时焊接温度高于焊接工艺参数对应的设定温度区间的上限值时,控制降低激光峰值功率,直到实时焊接温度回到焊接工艺参数对应的设定温度区间内为止,反之当监测到的实时焊接温度低于焊接工艺参数对应的设定温度区间的下限值时,控制升高激光峰值功率,直到实时焊接温度回到焊接工艺参数对应的设定温度区间内为止。当然其还可通过负反馈动态调节激光脉冲的宽度、能量、重复频率等其他参数中的任意一个或其组合,使得焊接温度处于目标设定范围内(也即控制恒温焊接)即可,其调节方式在此不做具体限定。
[0059]
其中,上述温度反馈控制中可以选择温度和功率两种模式同时控制,也可以选择分段混合模式控制,可根据温度曲线数据追踪温度过载的时候所使用的功率,然后在通过功率对这个时间点进行限制,能有效的避免温度过载的情况出现。
[0060]
同时,在光学系统的输出端增加一个能量检测装置,用来检测输出激光能量的大小,并将该信号实时的反馈到控制端,与理论设定的能量进行比较,形成一个闭环控制系统,达到准确控制激光能量输出的目的。使得在焊接温度处于目标温度范围内时,其还可以控制激光能量的稳定输出,使得能量输出更加稳定。同时其视觉检测机构还可以观察激光与引线的对位情况以及焊接的过程,可对焊锡过程录像或拍照,实现焊接过程的全程监控,并当检测到点锡或焊接位置与待焊区域的中心坐标位置发生偏移时,立刻控制停止点锡或
焊接,并控制运动单元驱动光学系统运动至待焊区域的准确坐标位置后,再一次进行上述步骤s31及步骤s41的点锡及焊接流程。
[0061]
进一步的,其传感器机构能使待焊件在一定焊接温度范围内焊接,更好地保证焊接效果的一致性,同时还可监测待焊区域温度,以此间接判断焊接效果,当待焊区域温度无法恒定时,发出报警提醒并停止输出激光,避免产品过烧,同时兼具焊中检测的效果,解决焊接检测难的问题。
[0062]
步骤s51,在对待焊区域完成焊接后,检测待焊件的焊接是否存在焊接缺陷。
[0063]
其中,若检测待焊件的焊接存在焊接缺陷时,则执行步骤s61;否则,则完成了该待焊件的焊接,并对下一待焊件重新执行上述步骤s11-步骤s51。
[0064]
其中,焊接缺陷包括连焊、漏焊、堆焊、虚焊等,其可通过视觉检测机构对待焊件进行图像信息的采集,并根据所采集的图像信息检测判断是否存在焊接缺陷,例如连焊通常为焊锡过程中紧邻的几个焊点桥接在一起的现象,此时视觉检测机构检测到相邻的待焊区域连接一体时,则可确定该待焊件存在连焊缺陷,造成此种现象的原因可能是锡量太多或是两个焊点之间的间距太小所造成的,因此后续缺陷处理过程中,则需要减少锡量进行重新焊接。
[0065]
而漏焊通常焊接过程中焊点上没有锡的现象,此时视觉检测机构检测到存在待焊区域没有锡时,则可确定该待焊件存在漏焊缺陷,造成此种现象的原因可能是锡膏或者锡丝没有接触到焊点或者焊盘表面氧化比较严重导致锡无法粘在焊盘上面所造成的,因此后续缺陷处理过程中,则需要调整移动至该待焊区域的坐标位置对应的焊锡点,使其接触到待焊区域进行点锡及焊接。若再次点锡及焊接完成后依旧检测到漏焊缺陷时,则将其待焊件转移至故障区域或发出故障警报,以使工作人员对该待焊件进行故障处理。
[0066]
相应的,堆焊为焊接过程中焊料过多,而虚焊为焊接过程中焊料过少,或激光点在焊盘上的停留时间不够或是温度过低造成的。此外还可通过如下检测方式进行焊接缺陷的检测:一、pcb三角测量法通过光扩散性原理对物体进行检验,使得能够检出其立体形状的截面形状的方法,其通过现有利用的三角测量法设计出的设备进行检测。
[0067]
二、光反射分布测量法利用焊接部位检测装饰,从倾斜方向向内入射光,在上方设置tv摄像,然后对其进行检查。这种操作方法最重要的部分就是如何知道pcb焊料的表面角度,尤其是如何知道照射光度信息等,必须要通过各种灯光色彩来捕捉角度信息。相反,如果是从上方照射,测量的角度则是反射光分布,检查焊料倾斜表面即可。
[0068]
三、变换角度进行摄像检查法利用一个具有变换角度的装置,这个装置一般拥有至少5台摄像机,多个led照明设备,会使用多个图像,采用目测条件进行检查,可靠度比较高。
[0069]
四、焦点检出利用法对于一些高密度的电路板,经过pcb焊接之后,上述三种方法很难检测出最终的结果,因而需要采用第四种方法,也就是焦点检出利用法。这种方法分为多个,比如多段焦点法,这个可以直接检测出焊料表面的高度,实现高精度检测法,同时设置10个焦点面检测器
的话,可以通过求最大输出获得焦点面,检测出焊料表面的位置。如果是通过微细激光束照射对象方法去检测,只要在z方向上错开配置的10个具体针孔,就能成功检测出0.3mm的节距引线装置。
[0070]
因此,在本发明实施例中,通过在对待焊件焊接完成后进行缺陷检测,使得可实现锡多锡少、连锡、漏焊、烧伤等不良状态的检测,避免待焊件焊接不良而直接投入后续使用所可能造成的不良影响。
[0071]
步骤s61,对待焊件焊接缺陷的位置重新进行激光焊接。
[0072]
其中,当检测到待焊件的焊接存在焊接缺陷时,则对待焊件焊接缺陷的位置重新进行激光焊接,在重新激光焊接完成后再次进行焊接缺陷的检测,若检测到无焊接缺陷后,则完成了对该待焊件的激光焊接。若继续检测到焊接缺陷后,则将其待焊件转移至故障区域或发出故障警报,以使工作人员对该待焊件进行故障处理。
[0073]
实施例三请参阅图3,是本发明第三实施例提供的激光锡焊装置的结构示意图,为了便于说明,仅示出了与本发明实施例相关的部分,该装置包括:检测获取模块11,用于获取待焊件的类型,并检测待焊件的待焊区域的坐标位置和尺寸、与待焊区域之间的高度、及各相邻待焊区域之间的边距;参数确定模块21,用于根据待焊件的类型、待焊区域的坐标位置和尺寸、与待焊区域之间的高度、及各相邻待焊区域之间的边距确定待焊区域所对应激光焊接时的光斑类型、光斑尺寸、焊锡点及焊锡量;焊接控制模块31,用于在待焊区域所确定的坐标位置上,根据待焊区域所对应确定的焊锡点、焊锡量、光斑尺寸及光斑类型对待焊区域进行点锡及焊接,并实时监测待焊区域的焊接温度、及输出激光能量,其中焊接光斑的照射中心作用于待焊区域的中心;焊接调节模块41,用于根据所监测的焊接温度和输出激光能量相应的调节激光输出参数对待焊区域进行焊接,以使焊接温度处于目标设定范围内。
[0074]
本发明实施例所提供的激光锡焊装置,其实现原理及产生的技术效果和前述方法实施例相同,为简要描述,装置实施例部分未提及之处,可参考前述方法实施例中相应内容。
[0075]
实施例四请参阅图4,是本发明第四实施例提供的激光锡焊装置的结构示意图,为了便于说明,仅示出了与本发明实施例相关的部分,该第四实施例与第三实施例的结构大抵相同,其区别在于,本实施例中,该装置还包括:焊接缺陷检测模块51,用于在对待焊区域完成焊接后,检测待焊件的焊接是否存在焊接缺陷;激光焊接模块61,用于当焊接缺陷检测模块51检测出待焊件的焊接存在焊接缺陷时,则对待焊件焊接缺陷的位置重新进行激光焊接。
[0076]
进一步的,在本发明的一个实施例中,参数确定模块21包括:光斑类型确定单元,用于根据待焊件的类型、及各相邻待焊区域之间的边距确定出待焊区域所对应激光焊接时的光斑类型;光斑尺寸确定单元,用于根据待焊区域的尺寸、与待焊区域之间的高度、及各相邻
待焊区域之间的边距确定出待焊区域所对应激光焊接时的光斑尺寸;焊锡点确定单元,用于根据待焊区域的坐标位置、及与待焊区域之间的高度确定出待焊区域所对应激光焊接时的焊锡点;焊锡量确定单元,用于根据待焊区域的尺寸、及各相邻待焊区域之间的边距确定出待焊区域所对应激光焊接时的焊锡量。
[0077]
进一步的,在本发明的一个实施例中,焊接控制模块31包括:点锡控制单元,用于根据待焊区域所对应确定的焊锡点和焊锡量对待焊区域进行点锡;焊接控制单元,用于根据待焊区域所对应确定的光斑尺寸及光斑类型对待焊区域进行焊接。
[0078]
进一步的,在本发明的一个实施例中,检测获取模块11包括:第一型号参数获取单元,用于获取用户所输入的待焊件的型号;或第二型号参数获取单元,用于根据视觉检测机构对待焊件所检测采集的图像信息进行形状和图像的匹配,获取识别到待焊件的型号。
[0079]
进一步的,在本发明的一个实施例中,检测获取模块11还包括:高度参数获取单元,用于根据测距机构检测与待焊区域之间的高度;参数检测获取单元,用于根据视觉检测机构对待焊件所检测采集的图像信息、及测距机构所检测的与待焊区域之间的高度,检测确定出待焊区域的坐标位置和尺寸、及各相邻待焊区域之间的边距。
[0080]
进一步的,在本发明的一个实施例中,激光输出参数包括激光脉冲的宽度、能量、峰值功率和重复频率;其中,焊接调节模块41包括:第一焊接调节单元,用于根据所监测的焊接温度与目标温度范围之间的差值动态调节激光脉冲的宽度、能量、峰值功率及重复频率,以使焊接温度处于目标温度范围内;第二焊接调节单元,用于根据所监测的输出激光能量的波动动态调节激光脉冲的宽度、能量、峰值功率及重复频率,以使焊接温度处于目标温度范围内时稳定所输出的激光能量。
[0081]
进一步的,在本发明的一个实施例中,光斑类型包括圆形、方形、椭圆形、环形、双焦点型、及一字型。
[0082]
本发明实施例所提供的激光锡焊装置,其实现原理及产生的技术效果和前述方法实施例相同,为简要描述,装置实施例部分未提及之处,可参考前述方法实施例中相应内容。
[0083]
实施例五请参阅图5,是本发明第五实施例提供的激光锡焊系统的结构示意图,为了便于说明,仅示出了与本发明实施例相关的部分,该系统包括:测距机构100,用于检测与待焊件的待焊区域之间的高度;视觉检测机构200,用于检测待焊件的类型、及与测距机构共同检测待焊件的待焊区域的坐标位置和尺寸、及各相邻待焊区域之间的边距;点锡机构300,用于对待焊件的待焊区域进行点锡;
焊锡机构400,用于对待焊件的待焊区域进行激光焊接;及传感器机构500,用于实时监测待焊件的待焊区域的焊接温度、及输出激光能量;及控制机构600,用于根据测距机构100及视觉检测机构200检测的待焊件的类型、待焊件的待焊区域的坐标位置和尺寸、与待焊区域之间的高度、及各相邻待焊区域之间的边距确定出待焊区域所对应激光焊接时的光斑类型、光斑尺寸、焊锡点及焊锡量,并根据待焊区域所对应确定的焊锡点和焊锡量控制点锡机构300对待焊区域进行点锡,以及根据待焊区域所对应确定的光斑尺寸及光斑类型控制焊锡机构400对待焊区域进行焊接,及根据传感器机构500所监测的焊接温度和输出激光能量相应的控制焊锡机构400调节激光输出参数对所述待焊区域进行焊接,以使焊接温度处于目标温度范围内直至完成焊接。
[0084]
本发明实施例所提供的激光锡焊系统,其实现原理及产生的技术效果和前述方法实施例相同,为简要描述,装置实施例部分未提及之处,可参考前述方法实施例中相应内容。
[0085]
本发明实施例还提供了一种可读存储介质,其上存储有程序,该程序被处理器执行时实现如上述实施例所述的激光锡焊方法步骤。所述可读存储介质,如:rom/ram、磁碟、光盘等。
[0086]
所属领域的技术人员可以清楚地了解到,为描述的方便和简洁,仅以上述各功能单元、模块的划分进行举例说明,实际应用中,可以根据需要而将上述功能分配由不同的功能单元或模块完成,即将存储装置的内部结构划分成不同的功能单元或模块,以完成以上描述的全部或者部分功能。实施方式中的各功能单元、模块可以集成在一个处理单元中,也可以是各个单元单独物理存在,也可以两个或两个以上单元集成在一个单元中,上述集成的单元既可以采用硬件的形式实现,也可以采用软件功能单元的形式实现。另外,各功能单元、模块的具体名称也只是为了便于相互区分,并不用于限制本技术的保护范围。
[0087]
本领域技术人员可以理解,图3及图4中示出的组成结构并不构成对本发明的激光锡焊装置的限定,可以包括比图示更多或更少的部件,或者组合某些部件,或者不同的部件布置,而图1-2中的激光锡焊方法亦采用图3或图4中所示的更多或更少的部件,或者组合某些部件,或者不同的部件布置来实现。本发明所称的单元、模块等是指一种能够被激光锡焊装置中的处理器(图未示)所执行并功能够完成特定功能的一系列计算机程序,其均可存储于激光锡焊装置的存储设备(图未示)内。
[0088]
本领域技术人员还可以理解,图5中示出的组成结构并不构成对本发明的激光锡焊系统的限定,可以包括比图示更多或更少的部件,或者组合某些部件,或者不同的部件布置,而图1-2中的激光锡焊方法亦采用图5中所示的更多或更少的部件,或者组合某些部件,或者不同的部件布置来实现。
[0089]
以上所述仅为本发明的较佳实施例而已,并不用以限制本发明,凡在本发明的精神和原则之内所作的任何修改、等同替换和改进等,均应包含在本发明的保护范围之内。