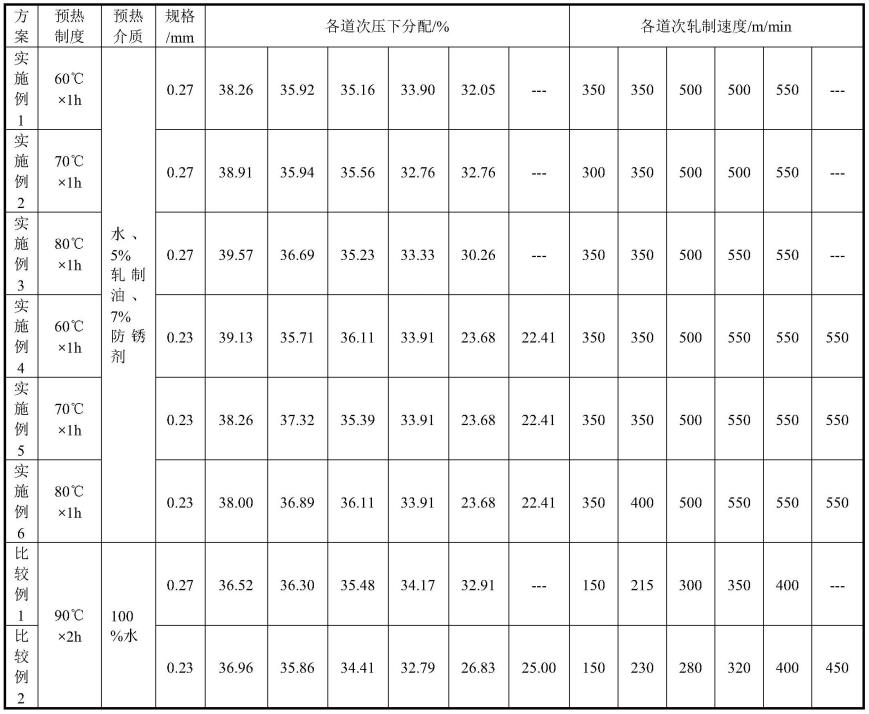
1.本发明涉及取向硅钢冷轧工艺技术领域,尤其涉及一种抑制取向硅钢冷轧边裂的轧制方法。
背景技术:2.目前,高磁感取向硅钢普遍采用冷轧时效工艺,采用大压下、出口闭乳及高速轧制等方法将轧制温度提高至180℃~220℃调整固溶碳氮化物状态以促进磁性能改善。在化学成分(通常含3.0%~3.4%硅)和轧前组织(15%~30%珠光体硬质相和表层粗化组织)共同影响下,取向硅钢冷轧抗裂性恶化且对轧制温度敏感性增强,其时效轧制过程极易发生断带事故,导致生产效率和成材率降低,因此冷轧工序成为限制取向硅钢提质增效的技术瓶颈之一。
3.生产实践表明,边裂防控是降低取向硅钢冷轧断带率的关键所在。对于冷轧断带事故防控主要是抑制边裂形成扩展的材料学和力学条件,除改善轧材材质及组织状态等边裂形成内在因素外,通过冷轧轧制工艺调控则成为抑制边裂形成外在力学因素重要技术手段。但是,取向硅钢“高载荷、低润滑”时效轧制方式进一步增加了冷轧边裂防控难度,一方面带钢在较高压应力作用下产生裂纹,另一方面轧辊加速磨损则使带钢应力难以调控。
技术实现要素:4.为了克服现有技术的不足,提供一种抑制取向硅钢冷轧边裂的轧制方法,在保障轧材抗裂性和时效温度前提下提高其冷轧效率和成材率。
5.为了达到上述目的,本发明采用以下技术方案实现:
6.一种抑制取向硅钢冷轧边裂的轧制方法,所述取向硅钢包含如下重量百分含量的化学元素:c:0.040%~0.060%,si:3.10%~3.35%,mn:0.150%~0.200%,p:0.010%~0.030%,s:0.0050%~0.0070%。
7.具体包括如下步骤:
8.(1)钢卷预热:采用水浴加热装置进行钢卷预热,钢卷温度达60℃~80℃并保温1小时~2小时,以保证钢卷上线温度处于韧性温度区间并避免带钢形成边裂或脆断。加热方式是将蒸汽通入添加5%~15%的轧制油和防锈剂的除盐水介质,避免钢卷锈蚀对边裂控制和轧制稳定性产生不利影响。
9.(2)轧制控制:将1.80mm~2.30mm厚常化钢板冷轧至成品厚度。第1道次至第3道次采用33%~40%大压下率、300m/min~800m/min高速轧制,通过提高变形热和降低带钢与环境介质热交换量使带钢温度由第1、2道次的120℃~170℃逐步达到第3道次180℃~200℃时效温度,避免带钢脆性断裂的同时保障时效处理对磁性能的改善效果。第4道次至成品道次采用20%~35%压下率递减方式轧至成品厚度(以各道次压下率递减的方式进行轧制),并进行成品板形及边部应力调控,避免严重边裂和断带事故以提高冷轧成材率。
10.(3)乳液分配:第1道次至第3道次轧机两侧均采用500l/min~600l/min低供乳量
改善润滑条件,并保障时效温度;第4道次至成品道次轧机两侧采用1000l/min~2000l/min高供乳量分段式控制以改善轧辊热膨胀均匀性和边部应力控制。各道次乳液采用分段式分布改善板形及轧辊热膨胀均匀性,即:带钢边部段(0/10~1/10带钢宽度)乳液量分配比例为0%~20%,外部段(1/10~2/10带钢宽度)乳液量分配比例0%~30%、中部段(2/10~4/10带钢宽度)0%~40%。
11.(4)轧辊辊形及粗糙度控制:成品道次工作辊采用粗糙度为0.2μm~0.4μm的零凸度轧制,以改善产品表面质量及板形;其余道次工作辊采用粗糙度1.0μm~2.0μm提高轧制温度并改善轧制稳定性,以凸度0.02mm~0.08mm改善边部应力状态。为增加边部应力值调控及板形控制域,二中间惰辊采用凸度为0.2mm~0.6mm,采用双锥度一中间辊:第1段锥度1.5
‰
~2.2
‰
、锥长130mm~180mm,第2段锥度2.2
‰
~2.6
‰
、锥长160mm~220mm。
12.(5)边部应力控制:为控制轧制过程带钢边裂形成和扩展力学条件,避免因边部应力过大导致裂纹形成和扩展,各道次采用微应力方式调整as-u-roll和一中间辊重叠量调控,其中:第1至3道次边部应力按照
±
45mpa调控、第4道次至成品道次边部应力按照
±
35mpa调控。
13.与现有技术相比,本发明的有益效果是:
14.(1)与现有取向硅钢冷轧前水浴加热相比,本发明通过添加5%~15%的轧制油和防锈剂的除盐水介质,突破了钢卷水浴加热对取向硅钢冷轧稳定性和辊系磨损的不利影响。在解决了钢卷锈蚀导致的轧制打滑和轧辊损伤,有效提高轧制过程稳定性和轧制速度。在此基础上,钢卷预热后锈蚀明显减轻,使轧辊吨钢消耗降低5%的同时,轧制速度提升100m/min~200m/min,单卷轧制时间缩短0.5小时~1小时。
15.(2)与现有取向硅钢冷轧均匀式乳液喷射方式相比,本发明采用的第4道次至成品道次高供乳量和乳液分段式控制,改善取向硅钢时效轧制过程中轧辊热膨胀均匀性。在此基础上,结合一中间辊双锥度和压下优化配置,有效提高了现有单as-u-roll二十辊森吉米尔轧机的板形调控能力,使冷轧成品板形明显改善,相应成品板形值由10ui提高至8~9ui。
16.(3)本发明采用带钢边部微应力调控手段进行一中间辊辊形及板形调控机构的匹配设计,有效实现对取向硅钢冷轧边裂的有效控制,可将边裂长度由4~5mm降低至1~3mm,冷轧成材率5.04%~10.55%。
具体实施方式
17.本发明公开了一种抑制取向硅钢冷轧边裂的轧制方法。本领域技术人员可以借鉴本文内容,适当改进工艺参数实现。特别需要指出的是,所有类似的替换和改动对本领域技术人员来说是显而易见的,它们都被视为包括在本发明。本发明的方法及应用已经通过较佳实施例进行了描述,相关人员明显能在不脱离本发明内容、精神和范围内对本文所述的方法和应用进行改动或适当变更与组合,来实现和应用本发明技术。
18.一种抑制取向硅钢冷轧边裂的轧制方法,所述取向硅钢包含如下重量百分含量的化学元素:c:0.040%~0.060%,si:3.10%~3.35%,mn:0.150%~0.200%,p:0.010%~0.030%,s:0.0050%~0.0070%。工艺流程:原料预热
→
上卷
→
第1道次两侧供乳轧制
→
第2道次两侧供乳轧制
→
第3道次两侧供乳时效轧制
→……→
成品道次轧制
→
卸卷。
19.具体包括如下步骤:
20.(1)钢卷预热:按常规高磁感取向硅钢成分冶炼,轧前厚度为2.30mm。采用水浴加热装置进行钢卷预热,加热介质添加5%轧制油及7%防锈剂,钢卷预热温度达60℃~80℃后保温1小时。
21.(2)轧制制度:将2.30mm厚常化钢板冷轧至成品厚度。第1道次压下率38%~40%,轧制速度350~450m/min,轧制温度达120~140℃;第2道次压下率35%~38%,轧制速度350~450m/min、轧制温度达140℃~170℃;第3道次压下率33%~35%,轧制速度450m/min~500m/min,轧制温度达180℃~200℃;第4道次至末道次采用25%~33%压下率递减方式轧至成品厚度,轧制速度450m/min~800m/min,轧制温度70℃~150℃。
22.(3)乳液分配制度:第1道次至第3道次轧机入口侧及出口侧供乳量500l/min~550l/min,第4道次至成品道次两侧乳液1000l/min~2000l/min,各道次带钢横向乳液分配比例:边部段0%~15%、外部段20%~30%、中部段30%~40%。
23.(4)轧辊使用制度:成品道次工作辊粗糙度0.3μm、零凸度,其余道次工作辊粗糙度1.5μm、凸度0.4mm。双锥度一中间辊:1.8
‰×
150mm+2.3
‰×
180mm;二中间辊凸度0.4mm。
24.(5)边部应力控制:第1道次边部应力按照
±
40mpa调控、第2道次边部应力按照
±
35mpa调控、第3道次边部应力按照
±
35mpa调控、第4道次至成品道次边部应力按照
±
25mpa调控。
25.实施例:
26.本发明实施例及比较例的化学成分见表1;相应实施例的钢卷预热及轧制工艺参数见表2;相应实施例的轧辊参数见表3;相应实施例的乳液分配工艺参数见表4;相应实施例的各道次轧制温度及边部应力见表5;相应实施例的实施例与比较例冷轧成材率、磁性能对比见表6。
27.表1实施例及比较例取向硅钢化学成分(wt.%)
28.方案csimnps实施例10.0433.130.1520.0130.0053实施例20.0483.180.1570.0190.0058实施例30.0533.200.1660.0180.0061实施例40.0563.240.1770.0230.0062实施例50.0553.260.1730.0250.0068实施例60.0583.280.1980.0250.0068比较例10.0503.200.1850.0120.0055比较例20.0553.250.1730.0180.0062
29.表2钢卷预热及轧制工艺参数
[0030][0031]
表3轧辊参数
[0032][0033]
表4乳液分配工艺参数
[0034][0035]
表5各道次轧制温度及边部应力
[0036][0037]
表6实施例与比较例冷轧成材率、磁性能对比
[0038][0039][0040]
表6为实施例与比较例的冷轧效果比较,本发明提供的实施例在保障冷轧时效轧制工艺和成品性能不出现劣化的前提下,使边裂长度降低2mm~4mm,实现对边裂和断带事故的有效防控,冷轧成材率5.04%~10.55%。在此基础上,通过轧制过程轧制应力调控,冷
轧成品板形改善1iu~2iu。本发明可有效降低钢卷水浴加热导致锈蚀,使轧辊吨钢消耗降低5%的同时,轧制速度提升100m/min-200m/min,单卷轧制时间缩短0.5小时~1小时。
[0041]
以上所述,仅为本发明较佳的具体实施方式,但本发明的保护范围并不局限于此,任何熟悉本技术领域的技术人员在本发明揭露的技术范围内,根据本发明的技术方案及其发明构思加以等同替换或改变,都应涵盖在本发明的保护范围之内。