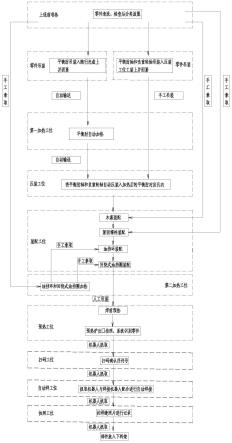
1.本发明涉及一种悬挂臂组件的智能制造工艺。
背景技术:2.悬挂臂包括平衡肘臂、上/下臂,其中主要加工内容有,平衡肘与平衡肘轴、负重轮轴、油挡环的热套,紧固螺栓的装配和焊接,主/付臂与连接臂的压装与焊接,上臂与上臂轴的压装和焊接,整体的制造流程涉及热套、压装、装配、焊接等多种冷热加工工艺类型,操作方式基本上以手工操作方式为主,加工场地也是分散在机加分厂、冲压车间、车体车间这几个部门。操作者在零件高温状态下手工作业,存在安全风险;物流冗长,各分厂交叉制造,生产同步性差;零件整体加热时间长、能耗高,资源浪费大。
技术实现要素:3.本发明的目的是提供一种悬挂臂组件的智能制造工艺,以解决现有技术中存在的问题。
4.为实现本发明目的而采用的技术方案是这样的,一种悬挂臂组件的智能制造工艺,包括以下步骤:
5.1)采用kbk吊装平衡肘,将平衡肘放置于输送线的随行工装上并紧固好。
6.2)所述随行工装自动输送到第一加热工位,自动工频感应加热机对平衡肘需要进行热套的两组孔进行定点精确加热。同时采用kbk将平衡肘轴和负重轮轴吊装到压装工位对应的定位装置上并紧固好。
7.3)当所述平衡肘达到设定温度后,平衡肘随随行工装自动运行到压装工位并紧固好。
8.4)压装机构自动推动平衡肘轴和负重轮轴压入平衡肘对应孔内,待组件自然冷却后,压装机构退回,固紧装置松开,随行工装自动输送到装配工位并紧固好。
9.5)将油挡环和回绕式油挡圈放入第二加热工位进行加热,将紧固螺栓旋入平衡肘轴内,木塞装入负重轮轴内。所述油挡环和回绕式油挡圈加热完毕后装入平衡肘的对应位置并紧固好,自然冷却的组件随随行工装输送到预热工位。
10.6)采用kbk将组件吊装到焊前预热炉,组件预热到150℃~200℃后运输至预热炉出口处拍照,系统识别零件。
11.7)抓取机器人抓取组件并送入扫码工位扫码,确认序列号,抓取机器人与焊接机器人双机配合完成自动焊接,抓取机器人将组件送入拍照工位拍焊缝照片并记录后,将组件放入下料架。
12.进一步,所述随行工装上设置有工装托盘,步骤1)中的平衡肘与工装托盘上的柔性部件接触并紧固。
13.进一步,步骤2)之前还具有通过扫码确定平衡肘代码的步骤。
14.进一步,所述自动工频感应加热机设置有两个加热头,加热头伸入需要加热的部
位进行加热。
15.本发明的技术效果是毋庸置疑的,本发明采用工频精准感应加热、异型结构件自动焊接、悬挂臂组件柔性集成制造的有机结合,解决了原有悬挂臂组件物流冗长,各分厂交叉制造,生产同步性差,零件整体加热时间长、能耗高,资源浪费大,操作者在零件高温状态下手工作业,存在安全风险等问题。
附图说明
16.图1为本发明流程示意图;
17.图2为平衡肘的示意图;
18.图3为平衡肘安装在随行工装上的示意图;
19.图4为随行工装输送到第一加热工位的示意图;
20.图5为平衡肘轴和负重轮轴安装到压装工位的示意图;
21.图6为图5中a-a的剖视图;
22.图7为平衡肘轴和负重轮轴压装到平衡肘上的示意图;
23.图8为油挡环的示意图;
24.图9为回绕式油挡圈的示意图;
25.图10为紧固螺栓和木塞的安装示意图;
26.图11为油挡环和回绕式油挡圈的安装示意图。
27.图中:平衡肘1、平衡肘轴2、负重轮轴3、压装机构4、油挡环5、回绕式油挡圈6、紧固螺栓7、木塞8、随行工装9、自动工频感应加热机10、加热头11和自动输送轨道12。
具体实施方式
28.下面结合实施例对本发明作进一步说明,但不应该理解为本发明上述主题范围仅限于下述实施例。在不脱离本发明上述技术思想的情况下,根据本领域普通技术知识和惯用手段,做出各种替换和变更,均应包括在本发明的保护范围内。
29.实施例1:
30.参见图1,本实施例公开了一种悬挂臂组件的智能制造工艺,包括以下步骤:
31.1)采用kbk吊装平衡肘1,将平衡肘1放置于输送线的随行工装9上并紧固好。图2为平衡肘的示意图,图3为平衡肘安装在随行工装上的示意图。其中,所述随行工装9上设置有工装托盘,步骤1)中的平衡肘1与工装托盘上的柔性部件接触并紧固,kbk为组合式起重机。
32.2)通过扫码确定所述平衡肘1代码,参见图4,所述随行工装9自动输送到第一加热工位,自动工频感应加热机10对平衡肘1需要进行热套的两组孔进行定点精确加热,自动工频感应加热机10设置有两个加热头11,加热头11伸入需要加热的部位进行加热。参见图5,同时采用kbk将平衡肘轴2和负重轮轴3吊装到压装工位对应的定位装置上并紧固好,平衡肘轴2和负重轮轴3分别位于自动输送轨道12的两侧,紧固前需调整好平衡肘轴2和负重轮轴3的放置方向,保证基准齿和四方的安装位置正确无误。图6为所述平衡肘轴2在图5中a-a处的横截面示意图。
33.3)当所述平衡肘1达到设定温度后,加热头11退出零件孔,平衡肘1随随行工装9自动运行到压装工位并紧固好。
34.4)所述平衡肘1在压装工位上就位后,系统接收到就位信号,参见图7,压装机构4自动推动平衡肘轴2和负重轮轴3压入平衡肘1对应孔内,待组件自然冷却后,压装机构4退回,固紧装置松开,随行工装9自动输送到装配工位并紧固好。
35.5)参见图10,将油挡环5和回绕式油挡圈6放入第二加热工位进行自动加热,将紧固螺栓7旋入平衡肘轴2并用定力矩拧紧枪拧紧,木塞8装入负重轮轴3内。参见图11,所述油挡环5和回绕式油挡圈6加热完毕后装入平衡肘1的对应位置并紧固好,自然冷却的组件随随行工装9输送到预热工位。图8为所述油挡环5的示意图,其中的图8a为剖视图,图8b为正视图。图9为所述回绕式油挡圈6的示意图,其中的图9a为剖视图,图9b为正视图。
36.6)采用kbk将组件吊装到焊前预热炉,组件预热到150℃~200℃后运输至预热炉出口处拍照,系统识别零件。
37.7)抓取机器人更换手爪,抓取组件并送入扫码工位扫码,确认序列号,抓取机器人与焊接机器人双机配合完成自动焊接,抓取机器人将组件送入拍照工位拍焊缝照片并记录后,将组件放入下料架。
38.值得说明的是,本实施例采用工频精准感应加热、异型结构件自动焊接、悬挂臂组件柔性集成制造的有机结合,解决了原有悬挂臂组件物流冗长,各分厂交叉制造,生产同步性差,零件整体加热时间长、能耗高,资源浪费大,操作者在零件高温状态下手工作业,存在安全风险等问题。
39.实施例2:
40.参见图1,本实施例公开了一种悬挂臂组件的智能制造工艺,包括以下步骤:
41.1)采用kbk吊装平衡肘1,将平衡肘1放置于输送线的随行工装9上并紧固好。图2为平衡肘的示意图,图3为平衡肘安装在随行工装上的示意图。
42.2)参见图4,所述随行工装9自动输送到第一加热工位,自动工频感应加热机10对平衡肘1需要进行热套的两组孔进行定点精确加热。参见图5,同时采用kbk将平衡肘轴2和负重轮轴3吊装到压装工位对应的定位装置上并紧固好。图6为所述平衡肘轴2在图5中a-a处的横截面示意图。
43.3)当所述平衡肘1达到设定温度后,平衡肘1随随行工装9自动运行到压装工位并紧固好。
44.4)参见图7,压装机构4自动推动平衡肘轴2和负重轮轴3压入平衡肘1对应孔内,待组件自然冷却后,压装机构4退回,固紧装置松开,随行工装9自动输送到装配工位并紧固好。
45.5)参见图10,将油挡环5和回绕式油挡圈6放入第二加热工位进行加热,将紧固螺栓7旋入平衡肘轴2内,木塞8装入负重轮轴3内。参见图11,所述油挡环5和回绕式油挡圈6加热完毕后装入平衡肘1的对应位置并紧固好,自然冷却的组件随随行工装9输送到预热工位。图8为所述油挡环5的示意图,其中的图8a为剖视图,图8b为正视图。图9为所述回绕式油挡圈6的示意图,其中的图9a为剖视图,图9b为正视图。
46.6)采用kbk将组件吊装到焊前预热炉,组件预热到150℃~200℃后运输至预热炉出口处拍照,系统识别零件。
47.7)抓取机器人抓取组件并送入扫码工位扫码,确认序列号,抓取机器人与焊接机器人双机配合完成自动焊接,抓取机器人将组件送入拍照工位拍焊缝照片并记录后,将组
件放入下料架。
48.实施例3:
49.本实施例主要步骤同实施例2,进一步,所述随行工装9上设置有工装托盘,步骤1)中的平衡肘1与工装托盘上的柔性部件接触并紧固。
50.实施例4:
51.本实施例主要步骤同实施例2,进一步,步骤2)之前还具有通过扫码确定平衡肘1代码的步骤。
52.实施例5:
53.本实施例主要步骤同实施例2,进一步,所述自动工频感应加热机10设置有两个加热头11,加热头11伸入需要加热的部位进行加热。