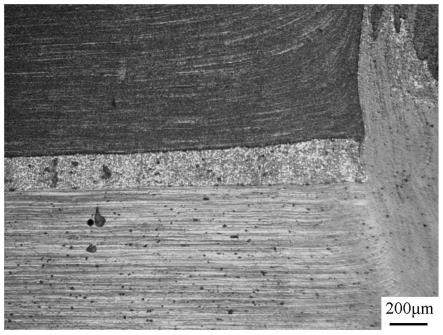
1.本发明涉及金属复合材料的制备加工技术领域,尤其涉及一种高界面结合强度的叠层铝合金制备方法。
背景技术:2.随着现代战争的发展,装甲车辆在未来作战中将会遭受全方位更加致命的攻击,对装甲材料防护和生存能力提出了新的、更高的要求。装甲车辆防护材料要求具有加工性能好、轻量化、抗冲击性能好、焊接性能优异、耐腐蚀性能好等优点。均质装甲很难同时对各种反装甲武器都有效,增加均质装甲厚度虽然可以提高其防护能力,但同时会增加装甲车辆的质量,车辆的灵活性下降。为了进一步提高装甲车辆的抗弹性能,同时防护不同的反装甲武器,利用不同性能的材料制成复合装甲材料成为装甲材料开发的主要方向。复合装甲的性能具有可设计性,即在一定范围内可设计结构和材料,可以根据作战环境及使用部位的不同设计出一系列不同性能、不同质量与厚度的装甲,如:研究表明具有加强筋结构的材料抗弹性能远高于无加强筋结构的抗弹性能。现在的层状复合装甲包括多层铝合金装甲、钛/铝多层复合装甲、钢/铝复合装甲等,虽然层状复合装甲具有一系列的优点,但存在制造技术复杂、成本高、层间结合力差、易开裂等缺点,而且传统方法制备的叠层铝合金界面为平面,组元界面之间结合强度提高受到很大限制,容易出现层间开裂。cn201520994763.2通过在端面堆焊的方法来防止装甲铝合金端面分层开裂,但不能防止装甲铝合金内部的分层开裂。
3.因此,开发一种操作方便、层间结合力强且不容易分层开裂的叠层铝合金的制备方法具有重要意义和实际价值。
技术实现要素:4.本发明的目的在于提供一种高界面结合强度的叠层铝合金制备方法,以解决现有技术中叠层铝合金层间结合力差、容易分层开裂的技术问题。
5.为了实现上述发明目的,本发明提供以下技术方案:
6.本发明提供了一种高界面结合强度的叠层铝合金制备方法,包括以下步骤:
7.(1)将背板、中间板、面板组合后固定,得到组合板;
8.(2)对组合板热处理后进行第一次轧制复合,得到叠层铝合金;
9.(3)在叠层铝合金上设置起焊板和引出板后,再进行搅拌摩擦处理;
10.(4)对搅拌摩擦处理后的叠层铝合金顺次进行热处理、第二次轧制处理、固溶处理和时效处理;
11.所述步骤(3)中搅拌摩擦处理时进给速度为150~250mm/min,搅拌旋转速度为700~900r/min。
12.进一步的,所述步骤(1)中背板包括7n01铝合金或7a52铝合金;所述中间板包括1系纯铝或7a01铝合金;所述面板包括7055铝合金或7a62铝合金。
13.进一步的,所述步骤(1)首先将背板、中间板和面板进行表面处理后再组合,所述表面处理的步骤为:用5~15wt%的naoh溶液碱洗3~10min后用80~100℃水冲洗,然后再用5~15wt%的hno3溶液酸洗3~10min后用5~15℃水冲洗,最后顺次进行吹干、界面打磨处理。
14.进一步的,所述步骤(2)中热处理的温度为400~450℃,热处理的时间为1~3h。
15.进一步的,所述步骤(2)中叠层铝合金的厚度为3~60mm。
16.进一步的,所述步骤(4)中热处理的温度为350~390℃,热处理的时间为1~2h。
17.进一步的,所述步骤(4)中固溶处理的温度为450~500℃,固溶处理的时间为1~3h。
18.进一步的,所述步骤(4)中时效处理的温度为100~150℃,时效处理的时间为12~48h。
19.本发明的有益效果:
20.(1)本发明通过搅拌对叠层铝合金进行摩擦处理,搅拌区的层间结构破坏重熔为一体,通过设计搅拌摩擦区域和路径,制备具有空间结构的叠层铝合金。由于搅拌摩擦焊缝区重熔为一体,层间界面消失,因此,叠层铝合金层间结合强度提高。
21.(2)本发明所提供的制备方法操作方便,能够实现工业化。
22.(3)本发明所提供的制备方法可用于单层金属材料和叠层金属复合材料,以防止金属厚板或叠层金属复合材料的分层开裂。
附图说明
23.图1为本发明的一种高界面结合强度的叠层铝合金制备方法的示意图,其中:1.面板、2.中间层、3.背板、4.焊缝、5.起焊板、6.引出板、7.铆钉;
24.图2为实施例1所制备的叠层铝合金的微观组织图;
25.图3为对比例1所制备的叠层铝合金的微观组织图。
具体实施方式
26.本发明提供了一种高界面结合强度的叠层铝合金制备方法,包括以下步骤:
27.(1)将背板、中间板、面板组合后固定,得到组合板;
28.(2)对组合板热处理后进行第一次轧制复合,得到叠层铝合金;
29.(3)在叠层铝合金上设置起焊板和引出板后,再进行搅拌摩擦处理;
30.(4)对搅拌摩擦处理后的叠层铝合金顺次进行热处理、第二次轧制处理、固溶处理和时效处理。
31.在本发明中,所述步骤(1)中背板包括7n01铝合金或7a52铝合金,优选为7n01铝合金;所述中间板包括1系纯铝或7a01铝合金,优选为1系纯铝;所述面板包括7055铝合金或7a62铝合金,优选为7055铝合金。
32.本发明优选对所述步骤(1)的背板、中间板和面板进行表面处理后再组合,所述表面处理的步骤为:用5~15wt%的naoh溶液碱洗3~10min后用80~100℃水冲洗,然后再用5~15wt%的hno3溶液酸洗3~10min后用5~15℃水冲洗,最后顺次进行吹干、界面打磨处理;优选为用10wt%的naoh溶液碱洗5min后用80℃水冲洗,然后再用10wt%的hno3溶液酸
洗5min后用10℃水冲洗,最后顺次进行吹干、界面打磨处理。
33.在本发明中,所述固定优选为在组合板前后端钻孔,用铝合金铆钉铆接固定。
34.在本发明中,所述步骤(2)中热处理的温度为400~450℃,优选为410~440℃,进一步优选为420~430℃;热处理的时间为1~3h,优选为1.5~2.5h,进一步优选为2h。
35.在本发明中,所述步骤(3)中搅拌摩擦处理时进给速度150~250mm/min,优选为170~230mm/min,进一步优选为190~210mm/min;搅拌旋转速度为700~900r/min,优选为750~850r/min,进一步优选为800r/min。
36.在本发明中,所述步骤(4)中热处理的温度为350~390℃,优选为360~380℃,进一步优选为370℃;热处理的时间为1~2h,优选为1.5h。
37.在本发明中,所述步骤(4)中固溶处理的温度为450~500℃,优选为460~490℃,进一步优选为470~480℃;固溶处理的时间为1~3h,优选为1.5~2.5h,进一步优选为2h。
38.在本发明中,所述步骤(4)中时效处理的温度为100~150℃,优选为110~140℃,进一步优选为120~130℃;时效处理的时间为12~48h,优选为16~44h,进一步优选为20~40h。
39.下面结合实施例对本发明提供的技术方案进行详细的说明,但是不能把它们理解为对本发明保护范围的限定。
40.实施例1
41.(1)首先将厚度为17mm的7n01铝合金背板、厚度为1mm的纯铝中间板,厚度为17mm的7050铝合金面板进行表面处理:用10wt%naoh溶液碱洗5min后用80℃水冲洗,再用10wt%的hno3溶液酸洗5min后用10℃水冲洗,最后用热风吹干,用钢丝刷对界面进行打磨,然后将背板、中间板、面板进行组合,在组合板前后端钻孔,用铝合金铆钉铆接固定,得到组合板;
42.(2)在420℃条件下对组合板热处理2h后进行第一次轧制复合,得到的叠层铝合金的厚度为10mm;
43.(3)在厚度为10mm的叠层铝合金上设置10mm厚铝合金起焊板和引出板,再进行搅拌摩擦处理,其中搅拌摩擦处理时进给速度为200mm/min,搅拌旋转速度为800r/min;
44.(4)搅拌处理后的叠层铝合金在380℃的条件下热处理1.5h后,进行第二次轧制处理,得到厚度为7mm厚的叠层铝合金,再将叠层铝合金在470℃条件下固溶处理2h后,在120℃的条件下时效处理24h,得到高界面结合强度的叠层铝合金。
45.实施例2
46.(1)首先将厚度为20mm的7a52铝合金背板、厚度为1mm的7a01中间板,厚度为15mm的7a62铝合金面板进行表面处理:用5wt%naoh溶液碱洗10min后用100℃水冲洗,再用15wt%的hno3溶液酸洗3min后用15℃水冲洗,最后用热风吹干,用钢丝刷对界面进行打磨,然后将背板、中间板、面板进行组合,在组合板前后端钻孔,用铝合金铆钉铆接固定,得到组合板;
47.(2)在400℃条件下对组合板热处理3h后进行第一次轧制复合,得到的叠层铝合金的厚度为15mm;
48.(3)在厚度为15mm的叠层铝合金上设置15mm铝合金起焊板和引出板,再进行搅拌摩擦处理,其中搅拌摩擦处理时进给速度为150mm/min,搅拌旋转速度为900r/min;
49.(4)搅拌处理后的叠层铝合金在390℃的条件下热处理1h后,进行第二次轧制处理,得到厚度为6mm厚的叠层铝合金,再将叠层铝合金在450℃条件下固溶处理3h后,在110℃的条件下时效处理12h,得到高界面结合强度的叠层铝合金。
50.实施例3
51.(1)首先将厚度为15mm的7n01铝合金背板、厚度为1mm的纯铝中间板,厚度为20mm的7a62铝合金面板进行表面处理:用15wt%naoh溶液碱洗3min后用90℃水冲洗,再用5wt%的hno3溶液酸洗10min后用5℃水冲洗,最后用热风吹干,用钢丝刷对界面进行打磨,然后将背板、中间板、面板进行组合,在组合板前后端钻孔,用铝合金铆钉铆接固定,得到组合板;
52.(2)在450℃条件下对组合板热处理1h后进行第一次轧制复合,得到的叠层铝合金的厚度为11mm;
53.(3)在厚度为11mm的叠层铝合金上设置11mm铝合金起焊板和引出板,再进行搅拌摩擦处理,其中搅拌摩擦处理时进给速度为250mm/min,搅拌旋转速度为700r/min;
54.(4)搅拌处理后的叠层铝合金在350℃的条件下热处理2h后,进行第二次轧制处理,得到厚度为8mm厚的叠层铝合金,再将叠层铝合金在500℃条件下固溶处理1h后,在120℃的条件下时效处理36h,得到高界面结合强度的叠层铝合金。
55.对比例1
56.与实施例1的区别在于,对比例1没有对叠层铝合金进行搅拌摩擦处理和第二次轧制处理,直接在第一次轧制得到7mm厚的叠层铝合金,其他条件与实施例1相同。
57.图2和图3分别为实施例1和对比例1所制备的叠层铝合金的微观组织图,从图2可以看出,搅拌区的层间结构破坏重熔为一体,而图3为典型的层状组织。通过对比可以发现,本发明所制备的叠层铝合金突破了传统叠层铝合金材料界面为平面的局限,制备出具有空间结构的叠层铝合金。由于焊缝区重熔为一体,层间界面消失。因此,叠层铝合金层间结合强度提高。
58.由以上实施例可知,本发明提供了一种高界面结合强度的叠层铝合金制备方法,首先将背板、中间板、面板组合固定后,再对组合板热处理后进行第一次轧制处理,然后对得到的叠层铝合金进行搅拌摩擦处理,最后经热处理、第二次轧制处理、固溶处理和时效处理,得到高界面结合强度的叠层铝合金。本发明所制备的叠层铝合金焊缝区重熔为一体,层间界面消失,层间结合强度大大提高。
59.以上所述仅是本发明的优选实施方式,应当指出,对于本技术领域的普通技术人员来说,在不脱离本发明原理的前提下,还可以做出若干改进和润饰,这些改进和润饰也应视为本发明的保护范围。