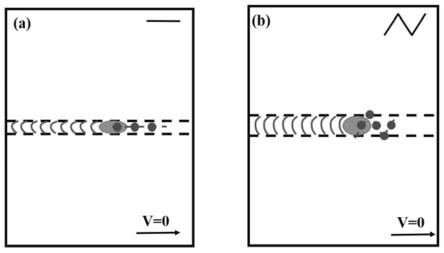
1.本发明涉及焊接技术领域,更具体地,涉及一种薄壁铝合金型材的焊接方法。
背景技术:2.在汽车领域中,为追求汽车的轻量化,提高汽车安全性,并且达到减少油耗的目的,汽车轻量化领域已广泛采用高强高韧的铝合金材料制作的薄钣金件和薄壁型材件,实现车身结构的减重。相较于钢铁材料,铝合金具有密度小、易于加工变形等优点,但是其热导率和热膨胀系数大,使得铝合金焊接接头仍存在成形质量较差的问题。
3.以车身的型材焊接为例,薄壁型材中各型材设计的结构通常不同。在全自动化焊接机器人实际焊接生产中,由于焊接轨迹通常设置为型材接头区的中心位置,并且需要在高生产效率情况下获得完全熔透的接头,于是为了避免在焊接生产过程中焊接参数不断转换使得生产效率降低,通常采用同一套焊接参数:大的焊接电流、大的焊接电压、大焊接功率和快送丝速度等焊接参数,但是同样的焊接参数将导致薄壁型材与复杂结构薄壁型材的焊接难度极大,焊接接头易出现焊缝烧穿的缺陷,严重影响焊接接头的成形质量,并且接头无法达到技术要求。因此,亟需开发一种车用薄壁铝合金型材高质量焊接的焊接方法。
技术实现要素:4.本发明的目的在于提供一种薄壁铝合金型材的焊接方法,以解决现有技术中存在的一个或多个技术问题。
5.为实现上述发明目的,本发明提出技术方案是:一种薄壁铝合金型材的焊接方法,包括:
6.通过计算待焊接薄壁铝合金型材接头区焊接热输入分配比,调整焊接轨迹向型材接头区上表面面积较大的待焊接型材的偏移量;
7.调整焊枪与焊缝之间的倾角;
8.调整焊接起弧位置和收弧位置;
9.采用摆动焊接轨迹进行焊接。
10.优先地,所述焊接热输入分配比的计算是根据不同的焊接工艺相应的焊接热源模型进行计算。
11.优先地,所述不同得焊接工艺包括弧焊、激光焊接和激光-弧焊,所述弧焊、激光焊接和激光-弧焊分别选用双椭球热源模型、高斯面热源+高斯圆锥体热源模型和双椭球热源+高斯圆锥体热源模型。
12.优先地,所述焊接轨迹偏移后待焊接件的接头区热输入分配比为:
13.μ1′
=w1′
/w
1+2
,μ2′
=w2′
/w
1+2
14.其中,μ1′
,μ2′
分别为焊接轨迹偏移后上表面面积较小的待焊接型材和上表面面积较大的待焊接型材的热输入分配比,w1′
,w2′
分别为焊接轨迹偏移后上表面面积较小和上表面面积较大的待焊接型材接头区的热源体积,w
1+2
为接头区两种型材的热源体积和。
15.优先地,焊接轨迹偏移后的型材接头区的热输入能量分配为:
16.q1′
=q
×
μ1′
,q2′
=q
×
μ2′
17.其中,所述q1′
,q2′
分别为焊接轨迹偏移后上表面面积较小的待焊接型材和上表面面积较大的待焊接型材的热输入能量,所述q为焊接热输入的总能量。
18.优先地,所述上表面面积较大的待焊接型材的热输入分配比的取值范围为0.55-0.65,所述上表面面积较大的待焊接型材的偏移量为自焊接接头区中心向上表面面积较大的待焊接型材偏移量,所述偏移量取值范围为0.5-1.0mm。
19.所述焊枪与焊缝倾角调整在60-75
°
之间。
20.所述摆动焊接轨迹为锯齿形,摆动幅度为0.5-1.0mm,摆动频率为2-4hz。
21.所述起弧位置选择待焊接型材接头区横截面宽度较窄的位置,所述收弧位置选择待焊接型材接头区横截面较宽的位置。
22.所述焊接方法适用于薄壁型材的对接焊、搭接焊、角接焊和t型焊。
23.与现有技术相比,本发明提供的薄壁铝合金型材的焊接方法的有益效果为:
24.1.通过计算不同焊接工艺对应的热源模型计算待焊接型材接头区的热输入分配比,控制焊接轨迹由焊接区中心向接头区上表面面积较大的待焊接型材即较大尺寸的型材偏移,使焊接热输入更多地作用于大尺寸型材的接头区。同时,焊枪与焊缝之间采用合理的倾角,改善电弧焊热源的主要加热位置,并且利于机器人焊枪的转向和焊接操作。
25.2.通过改变焊接轨迹,以改善焊接过程中在接头区的热源分配,采用锯齿形摆动焊接轨迹的焊接工艺,相较于常规焊接,摆动焊接轨迹能够增强液态熔池的搅拌能力和对流作用,有利于液态熔池中气孔的逸出,进而减少焊缝中气孔,获得焊缝成形良好和力学性能优异的焊接接头。
26.3.通常焊接起弧时,焊接型材温度低,起弧处的焊缝形貌高而窄,焊缝易出现未熔透的缺陷。然而在焊接收弧时,因为焊接的热量积累,并且没有能够熔化的母材填充弧坑,焊缝易出现缩孔、裂纹和烧穿等缺陷。因此,将待焊接型材接头区横截面宽度较窄的位置设置为起弧位置,将待焊接型材接头区横截面宽度较宽的位置设置为收弧位置,可以明显提高熔透能力,还可以避免收弧位置发生焊缝烧穿的现象。
附图说明
27.图1(a)和(b)分别是双椭球热源模型和高斯面+高斯圆锥体热源模型的示意图;
28.图2(a)和(b)分别是焊接轨迹偏移前和偏移后的双椭球热源分布对比示意图;
29.图3(a)和(b)分别是焊接轨迹偏移前后的面积函数示意图;
30.图4(a)和(b)分别是直线形和锯齿形两种焊接轨迹的对比示意图;
31.图5(a)、(b)和(c)分别是薄壁方管型材、挤压拉弯管材和两种型材的接头形式示意图;
32.图6(a)和(b)分别是接头改善前、后的焊缝表面宏观形貌示意图;
33.图7平板对接焊接的示意图;
34.图8平板对接焊接接头的示意图。
具体实施方式
35.下面将结合本发明的附图,对本发明实施例的技术方案进行清楚、完整的描述。
36.本发明公开的薄壁铝合金材料的焊接方法,用于薄壁铝合金型材在型材接头区通过合理分配焊接热输入的电弧焊接方法,其通过计算型材接头区焊接热输入在较大尺寸和较小尺寸型材上的分配比,调整待焊接的薄壁铝合金型材焊接轨迹向较大尺寸薄壁型材的偏移量,并通过调整焊枪与焊缝之间的倾角,调整起弧位置和收弧位置,采用锯齿形摆动焊接轨迹,以获得焊缝成形质量良好和力学性能优异的焊接接头。
37.其中,在本发明焊接方法的说明中,所述较大尺寸型材是指待焊接的薄壁铝合金型材中,上表面面积较大的型材,亦即大尺寸待焊接件;较小尺寸的型材是指焊接的薄壁铝合金型材中,上表面面积较小的型材,亦即小尺寸待焊接件,且在汽车车身焊接件的型材中,待焊接的两件型材的厚度基本相当。热源分配比及热源分配系数皆指两待焊接型材间的热输入分配比。
38.具体来说,根据不同焊接工艺,如电弧焊、激光填丝焊和激光-电弧复合焊,采用相应的焊接热源模型,计算出型材接头区的焊接热输入占比。如电弧焊采用双椭球热源模型,激光焊接采用高斯面热源+高斯圆锥体热源模型,双椭球热源模型和高斯面+高斯圆锥体热源,激光-弧焊采用双椭球热源+高斯圆锥体热源模型,如图1所示,分别为双椭球热源模型和高斯面+高斯圆锥体热源模型的示意图。
39.以电弧焊的双椭球热源模型为例来说,焊接轨迹向大尺寸待焊接件偏移后,相应地,热源也会有一定的偏移量。由图2可见,两型材接头区的焊接轨迹偏移前的热源体积分别为:
40.w1=(s1×
t1)
41.w2=(s2×
t2)
42.w
1+2
=w1+w243.焊接轨迹偏移后的热源体积分别为:
44.w1′
=(s1′×
t1′
)
45.w2′
=(s2′×
t2′
)
46.则焊接轨迹偏移前待焊接件的接头区热输入分配比(热源分配比):
47.μ1=w1/w
1+2
48.μ2=w2/w
1+2
49.焊接轨迹偏移后待焊接件的接头区热输入分配比:
50.μ1′
=w1′
/w
1+2
51.μ2′
=w2′
/w
1+2
52.其中s1、s1′
、s2、s2′
分别表示小尺寸型材和大尺寸型材焊接轨迹偏移前后的焊接热源的上表面面积,t1、t2、t1′
、t2′
分别表示较小尺寸型材和较大尺寸型材焊接轨迹偏移前后的型材的焊接热源横截面的高度。
53.焊接热输入公式如下:
[0054][0055]
q为焊接线能量热输入值,η为焊接输入吸收率,铝合金电弧焊和激光焊接通常取
值为0.8和0.6,u为焊接电压,i为焊接电流,v为焊接速度。
[0056]
焊接轨迹偏移后的型材接头区的热输入能量分别为:
[0057]
q1′
=q
×
μ1′
[0058]
q2′
=q
×
μ2′
[0059]
根据所述热输入分配系数计算型材接头区的焊接热输入分配比,通过热源模型计算两型材的接头区上表面积的比值,根据不同焊接工艺相对应的热源模型计算出热源模型的偏移量,进一步调整焊接轨迹偏移量,改善焊接轨迹后热源作用位置如图2(a),(b)所示。以双椭球模型为例,假定焊接偏移后两型材的接头区分配的热输入分别为总热输入的0.4和0.6倍。则通过热源分配系数反推计算两型材的双椭球上表面椭圆形面积的比值s1′
:s2′
,进而通过椭圆形的面积公式求得焊接轨迹的偏移量,焊接轨迹偏移前后的面积函数示意图如图3(a),(b)所示。计算方法如下:
[0060]
假定热源配系数已知,双椭球模型的椭圆形的函数为:f(x),则其面积为:
[0061][0062]
焊接轨迹偏移l后:
[0063][0064]
s2′
=s-s1′
[0065]
进而,根据热源分配系数μ1′
和μ2′
,计算偏移量l。
[0066]
优选地,本发明焊接方法中的薄壁型材的厚度优选为1.5-3.0mm;大尺寸型材的焊接热输入的分配比μ的取值范围优选在0.55-0.65之间,焊接轨迹偏移量的取值范围控制在0.5-1.0mm之间。不同形状的薄壁型材接头处的间隙控制在0-1.0mm之间,焊枪与焊缝的倾角调整在60-75
°
之间。
[0067]
此外,在大焊接电流追求完全熔透接头的情况下,型材的焊接区的横截面积越小,则通过该横截面的热量越大,热量积累主要集中于焊接材料,越容易导致焊缝烧穿。通过焊接型材横截面(致密)的热量计算公式如下:
[0068][0069]
k为通过横截面的热量,λ为导热系数,(
△
t/
△
s)为温度梯度,f为截面积,t为传热时间。通过上式进一步验证了通过调整焊接轨迹可以减少通过较小尺寸型材的横截面热流密度、降低较小尺寸型材的热输入积累。
[0070]
如图3所示,本发明中的焊接摆动轨迹选取锯齿形的焊接轨迹,其中摆动幅度控制在0.5-1.0mm之间,摆动频率控制在2-4hz之间。图4为锯齿形摆动焊接轨迹和常规直线型焊接轨迹对比示意图。
[0071]
更进一步地,结合图5所示,本发明优化了焊接起弧位置和收弧位置的设置,即将待焊接型材的宽度较窄位置设置为起弧位置w1,将待焊接型材的宽度较窄位置设置为收弧位置w2。薄壁型材件的宽度若呈现为前窄后宽,焊接起弧位置应为宽度较窄的位置w1,收弧位置则设置在宽度较宽的位置w2。
[0072]
本发明焊接方法适用于薄壁铝合金型材的焊接,可广泛应用于对接接头、搭接接
头、角接接头和t型接头的电弧焊接。型材的形状包括了长方形板材,梯形板材,挤弯型材,方形管材,梯形管材,钣金件等。
[0073]
由于焊接型材的尺寸和形状多样,导致在焊接过程中焊接型材的导热情况不同,如对于管材和挤弯型材的焊接,可以使焊接热输入更多作用于管材,明显减小焊接热输入在挤弯管材接头区的分配。下面以实施例1和实施例2来具体说明本发明的焊接方法。
[0074]
实施例1
[0075]
汽车前保险杠分总成的电弧焊接,一种规格为40*40*200mm的6082-t6铝合金薄壁管材(厚度2mm)和一种规格为40*40*400的6082-t6铝合金挤弯薄壁管材(厚度2mm),焊丝为直径1.2mm的5183焊丝。在福尼斯焊接机器人上进行mig焊接,接头形式为t型接头,焊缝长度为30mm。主要焊接工艺参数分别为:焊接电流为115a,焊接电压为19v,焊接速度为6mm/s。焊接车间生产过程中采用t型焊接接头形式,如选择常规的焊枪轨迹为型材焊接区的中心,焊枪倾角为45
°
,焊枪无摆动轨迹,焊接接头的焊缝成形质量差,焊缝烧穿。
[0076]
使用本发明提出的焊接方法,在焊接过程中,根据双椭球热源模型计算型材接头区的热输入分配比,q
总
=(0.8
×
115
×
19)/6=291.3j/mm,方管和挤弯管材的热输入分配比分别为0.61和0.39,相应地,两型材接头区的热输入分别为q
方管
=0.61
×q总
=177.7j/mm,q
挤弯管材
=0.39
×q总
=113.6j/mm。通过双椭球模型的计算,应将焊接轨迹向方管型材偏移0.75mm。通过调整焊枪角度至75
°
,添加焊枪摆动轨迹锯齿形,摆动幅度0.5-1.0mm,摆动频率2-4hz,同时优化焊接轨迹的起弧位置和收弧位置,改善后的焊接工艺可以合理分配焊接区的热输入,获得焊缝成形良好的焊接接头,并且在焊缝上表面有美观的鱼鳞纹。接头改善前、后的焊缝表面宏观形貌如图6所示。
[0077]
实施例2
[0078]
以长方体铝合金板材(75*150*2.5mm)和梯形体铝合金板材(梯形:5*50*75mm,厚度为2.5mm)的mig对接焊为例,板材为6082-t6铝合金,焊丝为直径为1.2mm的er4047焊丝,焊接示意图如图7(a),(b)所示,其中w1为起弧位置,w2为收弧位置,l1,l2为待焊接两板材能够导热的有效长度,焊接轨迹9为从起弧位置w1到收弧位置w2,焊接后形成焊线wl。其中焊接电流为110a,焊接电压为18.7v,焊接速度为6mm/s,保护气体为纯度99.999%的ar,气体流量15l/min,焊枪摆动轨迹为锯齿形。
[0079]
采用不同的焊接方法的具体焊接实验参数如下表1所示,其中焊接轨迹的数值为正时,表明向长方体铝合金板材偏移,反之,向梯形体铝合金板材偏移。
[0080]
表1不同焊接实验参数的对比表
[0081][0082]
焊缝熔宽、熔深和余高等参数示意图如图7所示。下表2为试样1-6的接头各项参数统计。
[0083]
表2不同焊接实验焊接后的各项焊接质量测试数据对比表
[0084][0085]
由表2可见,试样1-3均在焊接起相较于其他试样差,试样6的焊缝成形质量最好,焊缝上表面形成凹凸且美观的鱼鳞纹,下表面焊根高度均匀,焊缝的横截面气孔率2.8%,并且焊接接头力学性能优异,抗拉强度为238mpa,达到母材强度(310mpa)的76.8%。
[0086]
其中,试样6采用了本发明提出的焊接方法,其焊缝成形及接头的力学性能最佳。其焊接过程包括:
[0087]
首先,根据双椭球热源模型计算板材接头区热输入的占比,q
总
=(0.8
×
110
×
18.7)/6=274.27j/mm,长方体板材和梯形体板材的热输入分配比分别为0.62和0.38,相应地,两板材接头区的热输入分别为:q
长方体板材
=0.62
×q总
=170.05j/mm,q
梯形体板材
=0.38
×q总
=104.22j/mm。通过mig焊接的双椭球模型计算出热源模型的偏移量,焊接轨迹应向长方体板材接头区偏移1mm。在焊接过程中,相较于梯形体板材长度方向l2,热源更多作用于长方体板材长度较长的l1时,热量积累将更加分散,焊接材料的导热面积更大,有利于焊接过程中热传导。
[0088]
其次,焊枪与焊缝间的倾角为60度,焊接轨迹选择了锯齿形轨迹,由于焊枪与焊缝间的倾角增大,以及采用的锯齿形摆动焊接轨迹可以增强电弧对熔池的冲击力、熔池中液态金属对流和熔池搅拌能力,有利于焊缝中气孔逸出,使得气孔率降低,并且进一步增强熔池中液态金属的导热能力,有效改善焊缝烧穿的问题。
[0089]
最后,选择本发明中的起弧位置和收弧位置,如将位置w1设为起弧位置,可有效解决收弧位置的焊穿问题,并使得起弧位置w1处的焊缝成形良好,完全熔透。
[0090]
本发明的技术内容及技术特征已揭示如上,然而熟悉本领域的技术人员仍可能基于本发明的教示及揭示而作种种不背离本发明精神的替换及修饰,因此,本发明保护范围应不限于实施例所揭示的内容,而应包括各种不背离本发明的替换及修饰,并为本专利申请权利要求所涵盖。