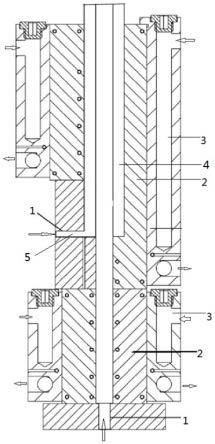
本发明涉及电气化高速铁路技术领域,具体涉及一种高强度耐磨耗铜锡合金接触线的制备工艺。
背景技术:高速铁路已成为电气化铁路的主要发展趋势,我国高铁运营里程超过4万公里,稳居世界第一;我国铁路运营总里程突破15万公里,稳居世界第二。接触线是电气化铁路接触网的关键组成部分,根据高速铁路对接触线的要求,世界发达国家都在发展自己的高速铁路接触线,接触线的材质和品种繁多,但接触线向铜合金化的发展已成为世界接触线发展的总趋势,目前普遍采用的铜合金接触线主要有铜银、铜锡、铜镁、铜铬锆等铜合金接触线。接触网导线在运行过程中,会受到受电弓的相对摩擦,在这一作用过程中导线表面会产生磨损,同时由于工作时间的累积和潮湿、阴暗工作环境等因素的共同作用,导线表面会出现腐蚀等物理现象,在磨损和腐蚀等的共同作用下导线变细或锈蚀,引起的变化统称为磨耗。引起地铁接触网导线磨耗的原因较多,归纳起来主要有以下几项:受电弓碳滑板的机械摩擦,接触线与滑板间的电气腐蚀,接触线氧化,接触线化学腐蚀等。高强度、耐磨耗始终是接触线性能要求的重要指标,本发明特殊的工艺生产的高强度铜锡合金接触线,具有高强度、耐磨耗等性能指标,可广泛应用于电气化高铁的运行要求。
技术实现要素:本发明所要解决的技术问题是克服接触线强度低,易磨耗的缺陷,提供了一种高强度耐磨耗铜锡合金接触线的制备工艺。本发明为解决上述问题所采用的技术方案为:一种高强度耐磨耗铜锡合金接触线的制备工艺,包括以下步骤:步骤一、向冶炼炉的熔融cu液中加入sn,使sn完全固溶于cu形成合金液,cu液上方覆盖150mm的木碳,生产过程中控制cu液温度为1150-1200℃;采用牵引机组上引铸造铜锡杆,铜锡杆挤出模具后水冷;步骤二、对铜锡杆表面进行在线打磨后,采用连续挤压机对打磨后的铜锡杆挤压制备接触线坯体,连续挤压机组采用冷却液对接触线坯体进行冷却,冷却后接触线坯体的温度不超过60℃,控制挤压机转速2.0-2.5r/min;步骤三、选用两辊连续冷轧机,生产中控制轧制速度为1-1.5mm/s,控制乳化液温度不超过55℃,将接触线坯体进行轧制成盘材;步骤四、采用五模拉丝机,将盘材置于放线架,拉出头部插入一号拉模,再依次进入二号拉模、三号拉模、四号拉模、五号拉模,从五号拉模出来的成品铜锡合金接触线进入收线机收排线。进一步的,步骤一中,铜液纯度为99.95%以上,合金液的质量百分比成分为:
sn0.48-0.51%、杂质≤0.1%,余量为cu;铜锡杆的氧含量小于5ppm。坯料被挤出模具后被水冷却,晶粒不能继续长大。本发明中,步骤一上引铸造铜锡杆,包括两个上下设置的模具,位于下部的模具上引的铜锡杆进入位于上部的模具中,位于上部的模具内开设在位于该铜锡杆外周的流道,且位于上部的模具外开设有与该流道连通的浇注口,每个模具的外周均设有水冷系统,水冷系统中冷却水的进出水温度控制区间:30℃
±
5℃,进出水温差控制8-10℃。利用相同的合金液,根据包覆的厚度和下部模具引出的合金杆的直径比例,将合金液分为两份,使上引铸造的合金杆外包覆层状合金质,利于合金相的相互交错,在后续加工利于铸态组织被破碎后再结晶,提高耐磨性。进一步的,步骤二中,进行在线打磨的步骤为:采用在线磨光机对铜锡杆的上下外周面进行打磨加工,采用钢丝磨片进行打磨,同时采用双面多次对称进给量的冷却液冷却打磨,打磨去除铜锡杆表面油污、氧化层、划痕、杂质,其中,采用的冷却液由以下重量份的原料组成:90-97重量份的软水和3-10重量份的抗氧化剂。进一步的,步骤二中挤压温度为500-550℃,利于获得组织均匀的坯体;挤压后的接触线坯体金相组织为cu-sn合金相、α-cu、β-sn三相区组织,无铸态组织。在挤压过程实现动态再结晶,铸态组织被破碎后再结晶,形成晶粒细小、均匀的金相组织,韧性好。进一步的,步骤四中,五次拉拔的总压缩率为73.5%,最终实现标称截面积120mm2铜锡合金接触线。进一步的,步骤四中,五模拉丝机的五次连续拉拔中,步骤四中,五模拉丝机的五次连续拉拔中,第一拉拔道次的压缩率为20-25%,第二拉拔道次的压缩率为24-28%,第三拉拔道次的压缩率为24-28%,第四拉拔道次的压缩率为18-23%,第五拉拔道次的压缩率19-24%。其中,压缩率为拉拔前截面积与拉拔后截面积差值/拉拔前截面积的比值。采用五模巨拉机完成拉拔,拉丝鼓轮直径1.2米,曲率半径较大,有利于保证导线好的平直度。拉拔的成品接触线,经过在线涡流探伤,整齐的卷绕到收线盘具上。本发明中,sn在cu中是以固溶形式存在,铜锡合金是α相的连续固溶体,起固溶强化作用。β相sn溶入到铜基体中,使合金晶格常数变大,并引起晶格畸变,对在滑移面上运动着的位错有阻碍作用,在位错线上偏聚的sn对位错有钉扎作用,起到的强化作用。sn可以直接加入到铜液中,不损耗,且成分稳定。横向晶粒≤0.0024mm。接触线的抗拉强度达到530mpa以上,导电率达大于75%。采用本发明研制生产的高强度铜锡合金接触线,合金元素分布均匀,氧含量小于5ppm,实现了大长度大单重的连续生产,特殊的工艺生产的高强度铜锡合金接触线,具有高强度、耐磨耗、耐腐蚀等性能,可广泛应用于电气化高铁的运行要求。
附图说明
图1为本发明步骤一铸造装置示意图。图中标记:1、合金溶液,2、模具,3、水冷系统,4、流道,5、浇注口。
具体实施方式
下面结合具体实施方式对本发明作进一步详细的说明。本发明的实施例是为了示例和描述起见而给出的,而并不是无遗漏的或者将本发明限于所公开的形式。一种高强度耐磨耗铜锡合金接触线的制备工艺,包括以下步骤:步骤一、高强度铜锡合金接触线的上引杆熔炼选用专用冶炼炉,在纯度99.95%的铜液中加入0.48-0.51%的锡,完全固溶于铜,生产过程中控制铜液温度在1150~1200℃,上引铸造铜锡杆,如图1所示,包括两个上下设置的模具2,位于下部的模具上引的铜锡杆进入位于上部的模具中,位于上部的模具内开设在位于该铜锡杆外周的流道4,且位于上部的模具外开设有与该流道连通的浇注口5,每个模具的外周均设有水冷系统3,水冷系统3中冷却水的进出水温度控制区间:30℃
±
5℃,进出水温差控制8~15℃,铜液上方覆盖150mm的木碳,生产的φ25mm上引铜锡合金杆氧含量小于5ppm;连铸速度为20-25cm/min。步骤二、对铜锡合金杆表面进行在线打磨,处理;采用630连续挤压机,控制挤压机转速2.0-2.5r/min,铜锡合金杆坯在挤压机的腔体内,在高温高压的作用下实现动态再结晶,形成晶粒细小、均匀的金相组织。生产的φ28mm大截面挤压杆,通条性能更加致密均匀;挤压温度为500-550℃,连续挤压机组采用冷却液对接触线坯体进行冷却,冷却后接触线坯体的温度不超过60℃,控制挤压机转速2.0-2.5r/min;步骤三、选用两辊连续冷轧机,生产中控制轧制速度为1-1.5mm/s,控制乳化液温度不超过55℃,将φ28mm大截面挤压杆轧制成φ24mm,以满足后续连续拉拔。步骤四、采用五模巨拉机,将φ24mm的轧制杆连续拉拔,步骤四中,五模拉丝机的五次连续拉拔中,第一拉拔道次的压缩率为20-25%,第二拉拔道次的压缩率为24-28%,第三拉拔道次的压缩率为24-28%,第四拉拔道次的压缩率为18-23%,第五拉拔道次的压缩率19-24%。最终实现标称截面积120mm2铜锡合金接触线,保证了铜锡合金接触线的高抗拉强度。采用五模巨拉机完成,拉丝鼓轮直径1.2米,曲率半径较大,有利于保证导线好的平直度。拉丝鼓轮内部冷却加外部喷淋冷却,模具直接水冷,导线鼓轮之间微滑动,减少了摩擦生热,接触线的拉制温度控制在60℃以下,不会引起组织变化,且提高了出线速度。拉丝鼓轮表面光滑,并略带有锥体设计,鼓轮上缠绕的接触线通过推线装置横向推出,避免了线与线之间的相互滑动而产生的擦伤,提高了接触线的表面质量,拉拔的成品接触线,经过在线涡流探伤,整齐的卷绕到收线盘具上。五模巨拉机:将盘材置于放线架,拉出头部插入一号拉模,再依次进入二号拉模、三号拉模、四号拉模、五号拉模,从五号拉模出来的成品铜锡合金接触线进入收线机收排线。采用上引连铸大截面无氧铜锡合金杆,选用大型连续挤压设备,通过该生产工艺,生产的高强度铜锡合金接触线,室温抗拉强度可达到530mpa以上;高强度铜锡合金接触线中加入了锡元素,并通过对生产过程中的温度、速度、冷加工变形量等进行控制,提升高强度铜锡合金接触线的耐磨耗性能;连续挤压过程中,在冷却液中加入抗氧化剂,大大的提升了高强度铜锡合金接触线的耐腐蚀性。实施例1一种高强度耐磨耗铜锡合金接触线的制备工艺,包括以下步骤:步骤一、上引杆熔
炼选用专用冶炼炉,在铜液中加入锡,完全固溶于铜成合金液,合金成分为0.48%sn、杂质≤0.1%,余量为cu,生产过程中控制铜液温度在1200℃,铸造采用图1,冷却水进出水温度控制30℃
±
5℃,进出水温差控制8℃,铜液上方覆盖150mm的木碳,生产的φ25mm上引铜锡合金杆氧含量小于5ppm;步骤二、对铜锡合金杆表面进行在线打磨,处理;采用630连续挤压机,控制挤压机转速2.0r/min,生产φ28mm大截面挤压杆;挤压温度为540℃,连续挤压机组采用90重量份软水和10重量份抗氧化剂组成的冷却液对接触线坯体进行冷却,冷却后接触线坯体的温度控制在55℃以下,控制挤压机转速2.1r/min;步骤三、选用两辊连续冷轧机,生产中控制轧制速度为1.3mm/s,控制乳化液温度不超过50℃,将φ28mm大截面挤压杆轧制成φ24mm。步骤四、采用五模巨拉机,第一拉拔道次的压缩率为23.4%,第二拉拔道次的压缩率为26.5%,第三拉拔道次的压缩率为25.6%,第四拉拔道次的压缩率为20.7%,第五拉拔道次的压缩率20.14%,直径φ24mm拉拔120mm2接触线:第一道:24*24*0.7854*(1-0.234)=346.53第二道:346.53*(1-0.265)=254.7,第三道:254.7*(1-0.256)=189.497,第四道:189.497*(1-0.207)=150.27,第五道:150.27*(1-0.2014)=120;总压缩:(24*24*0.7854
ꢀ‑ꢀ
120) / 24*24*0.7854=73.47%;拉丝鼓轮直径1.2米,拉丝鼓轮内部冷却加外部喷淋冷却,模具直接水冷,接触线的拉制温度控制在60℃以下。拉丝鼓轮表面光滑,并略带有锥体设计,鼓轮上缠绕的接触线通过推线装置横向拉拔,拉拔的成品接触线,经过在线涡流探伤,整齐的卷绕到收线盘具上。通过该生产工艺,生产的高强度铜锡合金接触线,室温抗拉强度可达到517mpa。其中,采用了微量sn合金化组分,凝固时两相区较窄,其接触线能够获得更好的细化晶粒效果。实施例2一种高强度耐磨耗铜锡合金接触线的制备工艺,包括以下步骤:步骤一、上引杆熔炼选用专用冶炼炉,在铜液中加入锡,完全固溶于铜成合金液,合金成分为0.5%sn、杂质≤0.1%,余量为cu,生产过程中控制铜液温度在1160℃,铸造采用图1,冷却水进出水温度控制30℃
±
5℃,进出水温差控制9℃,铜液上方覆盖150mm的木碳,生产的φ25mm上引铜锡合金杆氧含量小于5ppm;步骤二、对铜锡合金杆表面进行在线打磨,处理;采用630连续挤压机,控制挤压机转速2.4r/min,生产φ28mm大截面挤压杆;挤压温度为500℃,连续挤压机组采用95重量份软水和5重量份抗氧化剂组成的冷却液对接触线坯体进行冷却,冷却后接触线坯体的温度控制在50℃以下,控制挤压机转速2.3r/min;步骤三、选用两辊连续冷轧机,生产中控制轧制速度为1.5mm/s,控制乳化液温度不超过55℃,将φ28mm大截面挤压杆轧制成φ24mm。步骤四、采用五模巨拉机,第一拉拔道次的压缩率为24.1%,第二拉拔道次的压缩率为25%,第三拉拔道次的压缩率为26.2%,第四拉拔道次的压缩率为19.5%,第五拉拔道次的压缩率21.56%,直径φ24mm拉拔120mm2接触线:第一道:24*24*0.7854*(1-0.241)=343.36,第二道:343.36*(1-0.25)=257.52,第三道:257.52*(1-0.262)=190.05,第四道:190.05*(1-0.195)=152.99,第五道:152.99*(1-0.2156)=120。
拉丝鼓轮直径1.2米,拉丝鼓轮内部冷却加外部喷淋冷却,模具直接水冷,接触线的拉制温度控制在55℃以下。拉丝鼓轮表面光滑,并略带有锥体设计,鼓轮上缠绕的接触线通过推线装置横向推出,拉拔的成品接触线,经过在线涡流探伤,整齐的卷绕到收线盘具上。通过该生产工艺,生产的高强度铜锡合金接触线,室温抗拉强度可达到522mpa。实施例3一种高强度耐磨耗铜锡合金接触线的制备工艺,包括以下步骤:步骤一、上引杆熔炼选用专用冶炼炉,在铜液中加入锡,完全固溶于铜成合金液,合金成分为0.51%sn、杂质≤0.1%,余量为cu,生产过程中控制铜液温度在1180℃,铸造采用图1,冷却水进出水温度控制30℃
±
5℃,进出水温差控制10℃,铜液上方覆盖150mm的木碳,生产的φ25mm上引铜锡合金杆氧含量小于5ppm;步骤二、对铜锡合金杆表面进行在线打磨,处理;采用630连续挤压机,控制挤压机转速2.2r/min,生产φ28mm大截面挤压杆;挤压温度为510℃,连续挤压机组采用94重量份软水和6重量份抗氧化剂组成的冷却液对接触线坯体进行冷却,冷却后接触线坯体的温度控制在60℃以下,控制挤压机转速2.5r/min;步骤三、选用两辊连续冷轧机,生产中控制轧制速度为1.0mm/s,控制乳化液温度不超过53℃,将φ28mm大截面挤压杆轧制成φ24mm。步骤四、采用五模巨拉机,第一拉拔道次的压缩率为20.0%,第二拉拔道次的压缩率为28.0%,第三拉拔道次的压缩率为24.5%,第四拉拔道次的压缩率为22.0%,第五拉拔道次的压缩率21.8%,直径φ24mm拉拔120mm2接触线:第一道:24*24*0.7854*(1-0.20)=361.91;第二道:361.91*(1-0.28)=260.58,第三道:260.58*(1-0.245)=196.74,第四道:196.74*(1-0.22)=153.46,第五道:153.46*(1-0.218)=120。拉丝鼓轮直径1.2米,拉丝鼓轮内部冷却加外部喷淋冷却,模具直接水冷,接触线的拉制温度控制在52℃以下。拉丝鼓轮表面光滑,并略带有锥体设计,鼓轮上缠绕的接触线通过推线装置横向推出,拉拔的成品接触线,经过在线涡流探伤,整齐的卷绕到收线盘具上。通过该生产工艺,生产的高强度铜锡合金接触线,室温抗拉强度可达到520mpa。实施例4一种高强度耐磨耗铜锡合金接触线的制备工艺,包括以下步骤:步骤一、上引杆熔炼选用专用冶炼炉,在铜液中加入锡,完全固溶于铜成合金液,合金成分为0.49%sn、杂质≤0.1%,余量为cu,生产过程中控制铜液温度在1170℃,铸造采用图1,冷却水进出水温度控制30℃
±
5℃,进出水温差控制6℃,铜液上方覆盖150mm的木碳,生产的φ25mm上引铜锡合金杆氧含量小于5ppm;步骤二、对铜锡合金杆表面进行在线打磨,处理;采用630连续挤压机,控制挤压机转速2.5r/min,生产φ28mm大截面挤压杆;挤压温度为530℃,连续挤压机组采用97重量份软水和3重量份抗氧化剂组成的冷却液对接触线坯体进行冷却,冷却后接触线坯体的温度控制在40℃以下,控制挤压机转速2.0r/min;步骤三、选用两辊连续冷轧机,生产中控制轧制速度为1.2mm/s,控制乳化液温度不超过52℃,将φ28mm大截面挤压杆轧制成φ24mm。步骤四、采用五模巨拉机,第一拉拔道次的压缩率为22.0%,第二拉拔道次的压缩率为27.1%,第三拉拔道次的压缩率为27.4%,第四拉拔道次的压缩率为18.5%,第五拉拔道
次的压缩率23.3%,直径φ24mm拉拔120mm2接触线:第一道:24*24*0.7854*(1-0.22)=362.86,第二道:362.86*(1-0.271)=264.52,第三道:264.52*(1-0.274)=192.04,第四道:192.04*(1-0.185)=156.51,第五道:156.51*(1-0.233)=120。拉丝鼓轮直径1.2米,拉丝鼓轮内部冷却加外部喷淋冷却,模具直接水冷,接触线的拉制温度控制在53℃以下。拉丝鼓轮表面光滑,并略带有锥体设计,鼓轮上缠绕的接触线通过推线装置横向推出,拉拔的成品接触线,经过在线涡流探伤,整齐的卷绕到收线盘具上。通过该生产工艺,生产的高强度铜锡合金接触线,室温抗拉强度可达到533mpa。耐腐蚀实验:实验所用的接触线分别为对比例和各实施例,对比例为现有购买的铜锡合金接触线,总计5组,沿轴线方向将接触线切割成长度为100mm的试样,清洁处理后,依据gb/t10125-2012《人造气氛腐蚀实验盐雾腐蚀方法中中性盐雾实验》中的相关规定进行实验。盐雾腐蚀实验时间为72h,温度37℃,氯化钠溶液的浓度50g/l,腐蚀溶液ph值7.0,沉降率1.5ml/h。为保证盐雾实验的准确性,每个实施例及对比例接触线取五根作为一组,结果取其平均值,总计5组。年化腐蚀速率0.98206
×
,其中,腐蚀前后重量变化率为g/h,试样表面积单位为m2,年化腐蚀速率单位为mm/a,其盐雾试验结果见表1。表1对比例及各实施例试验结果由上表可知,本发明制备的铜锡合金接触线的抗腐蚀性明显优于现有铜锡合金接触线的抗腐蚀性,且对实施例1-4的接触线观察,肉眼可观察到腐蚀比较均匀,腐蚀面粗糙,无明显腐蚀坑,在放大20倍条件下进行观察,未在接触线表面发现明显腐蚀坑、腐蚀分层等腐蚀缺陷。本发明的产品符合中华人民共和国铁道行业标准tb∕t 2809-2017 电气化铁路用铜及铜合金接触线标准。