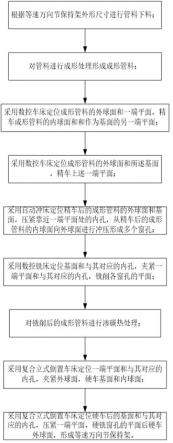
1.本发明涉及机械加工技术领域,尤其涉及一种等速万向节保持架加工方法。
背景技术:2.万向节保持架内、外球面形状尺寸、窗口形状尺寸、内外球面中心偏置误差及形位公差精度要求高,且壁较薄,加工中易变形,传统的加工方法很难保证其精度,也很难保证内外球面的同轴度误差要求。
3.现有的等速万向节保持架在制造方法通常包括:下料-加热-镦粗-冲孔-滚锻-校正-毛坯粗加工-拉削窗口-热处理-精磨加工-振动光饰。下料前,原材料未经有效的热处理,导致下料时管料强度、硬度和表面质量等通常不达标,影响成品保持架的性能;而且传统方案中,毛坯成型包括加热-镦粗-冲孔-滚锻-校正步骤,这些步骤为热加工成型,耗能非常大;在拉削窗口过程中,装夹定位繁琐,需多次装夹,加工速度慢,刀具成本高,并且窗口处会形成尖角,后续热处理加工时易产生应力集中,形成裂纹甚至断裂;整个加工过程中步骤繁多,工艺复杂,降低了生产效率。
技术实现要素:4.本发明的目的在于解决背景技术中的至少一个技术问题,提供一种等速万向节保持架加工方法。
5.为实现上述目的,本发明提供一种等速万向节保持架加工方法,包括:根据等速万向节保持架外形尺寸进行管料下料;对管料进行成形处理形成成形管料;采用数控车床定位成形管料的外球面和一端平面,精车成形管料的内球面和和作为基面的另一端平面;采用数控车床定位成形管料的外球面和所述基面,精车所述一端平面;采用自动冲床定位精车后的成形管料的外球面和所述基面,压紧靠近所述一端平面处的内孔,从精车后的成形管料的内球面向外球面进行冲压形成多个窗孔;采用数控铣床定位所述基面和与其对应的内孔,夹紧所述一端平面和与其对应的内孔,铣削各所述窗孔的平面;对铣削后的成形管料进行渗碳热处理;采用复合立式倒置车床定位所述一端平面和与其对应的内孔,夹紧外球面,硬车所述基面和内球面;采用复合立式倒置车床定位硬车后的所述基面和与其对应的内孔,压紧所述一端平面,硬铣所述窗孔的平面后硬车外球面,形成等速万向节保持架。
6.根据本发明的一个方面,所述管料为正火状态,硬度值为hb170-220,奥氏体晶粒度≤5级。
7.根据本发明的一个方面,所述成形处理为缩口成形或者冷辗扩成形。
8.根据本发明的一个方面,缩口成形时,采用上模座和下模座合模成形,分模线位于保持架外球面中心位置,上模座和下模座的内弧面圆弧和直径为所述等速万向节保持架的外球面圆弧和直径。
9.根据本发明的一个方面,铣削各所述窗孔的平面时,一次安装两把铣刀一次完成相对两个窗孔的上平面和下平面的铣削。
10.根据本发明的一个方面,所述渗碳热处理包括装料、上料、清洗、烘干、渗碳淬火、淬后清洗、回火、移动和下料。
11.根据本发明的一个方面,所述清洗为:将铣削后的成形管料推进行清洗机,清洗温度60℃
±
10℃,清洗时间≥60分钟,其中,清洗机内的清洗液每周检测一次,每1-3个月更换一次。
12.根据本发明的一个方面,所述烘干为:将清洗后的成形管料推至烘干炉,烘干温度:480℃
±
10℃,烘干时间≥60分钟。
13.根据本发明的一个方面,所述淬后清洗为:将渗碳淬火后的成形管料推进清洗机,清洗温度60℃
±
10℃,清洗时间≥50分钟,其中,清洗机内的清洗液每周检测一次,每1-3个月更换一次。
14.根据本发明的一个方面,所述回火为:将工件推进回火炉,回火温度170℃
±
10℃,回火时间≥150分钟,其中,所述回火与所述渗碳淬火的时间间隔≤2小时。
15.根据本发明的方案,能够保证等速万向节保持架的尺寸和形状精度,能够保证同轴度,而且加工过程中不会导致工件变形。不仅如此,通过本发明的方案,加工制造过程中,管料强度、硬度和表面质量能够有效得到提高和保证,整个过程耗能低,加工速度快,成本低,而且窗孔处不会形成尖角,不会产生应力集中和断裂现象,能够大大提高生产效率和成品良品率。
附图说明
16.图1示意性表示根据本发明的一种实施方式的等速万向节保持架加工方法的流程图;图2示意性表示根据本发明的等速万向节保持架加工方法得到的等速万向节保持架的结构图。
具体实施方式
17.现在将参照示例性实施例来论述本发明的内容。应当理解,论述的实施例仅是为了使得本领域普通技术人员能够更好地理解且因此实现本发明的内容,而不是暗示对本发明的范围的任何限制。
18.如本文中所使用的,术语“包括”及其变体要被解读为意味着“包括但不限于”的开放式术语。术语“基于”要被解读为“至少部分地基于”。术语“一个实施例”和“一种实施例”要被解读为“至少一个实施例”。
19.保持架作为固定式等速万向节关键零件,用于限制等速万向节中钢球活动区域,保持架外球面与钟形壳内球面、保持架内球面与星形套内球面采用间隙配合,保持架内、外球面开有数个窗孔(一般为6个或8个),窗孔平面与钢球采用间隙配合(最小配合间隙为
零)。
20.固定式等速万向节装配流程为:将星形套装入保持架内,合件装入钟形壳内,钢球依次装入。星形套能否装入保持架内,须满足保持架窗孔长度必须大于星形套的装配高度,保持架能否装入钟形壳内,也与保持架窗孔长度有关联。由于固定式等速万向节内腔部空间限制,保持架结构尺寸受到限制,保持架的壁厚较薄(厚度一般为4.0-8.0),同时保持架必须有一定的强度和耐磨性,因而材料选用低碳合金结构钢(一般采用20crmnti,sae8617h),采用渗碳热处理方法,保持架窗孔梁要有足够的强度,并且梁宽度保持一致,因而保持架设置的窗孔形状完全一致,窗孔形状设置满足星形套和钟形壳装配要求。
21.基于本发明的上述等速万向节保持架的结构及要求,本发明提出以下具体方案。
22.图1示意性表示根据本发明的一种实施方式的等速万向节保持架加工方法的流程图。如图1所示,根据本发明的等速万向节保持架加工方法,包括以下步骤:根据等速万向节保持架外形尺寸进行管料下料;对管料进行成形处理形成成形管料;采用数控车床定位成形管料的外球面和一端平面,精车成形管料的内球面和和作为基面的另一端平面;采用数控车床定位成形管料的外球面和所述基面,精车上述一端平面;采用自动冲床定位精车后的成形管料的外球面和基面,压紧靠近一端平面处的内孔,从精车后的成形管料的内球面向外球面进行冲压形成多个窗孔;采用数控铣床定位基面和与其对应的内孔(即靠近基面一侧的内孔部位),夹紧一端平面和与其对应的内孔(即靠近该平面一侧的内孔部位),铣削各窗孔的平面;对铣削后的成形管料进行渗碳热处理;采用复合立式倒置车床定位一端平面和与其对应的内孔,夹紧外球面,硬车基面和内球面;采用复合立式倒置车床定位硬车后的基面和与其对应的内孔,压紧一端平面,硬铣窗孔的平面后硬车外球面,形成等速万向节保持架。
23.根据本发明的上述方案,能够保证等速万向节保持架的尺寸和形状精度,能够保证同轴度,而且加工过程中不会导致工件变形。不仅如此,通过上述方案,加工制造过程中,管料强度、硬度和表面质量能够有效得到提高和保证,整个过程耗能低,加工速度快,成本低,而且窗孔处不会形成尖角,不会产生应力集中和断裂现象,能够大大提高生产效率和成品良品率。
24.根据本发明的一种实施方式,管料下料前的原材料采取用20crmnti,sae8617h的低碳合金钢的冷拉钢管,冷拉钢管是热轧棒料经过热穿孔成管坯,由管坯后冷拉钢管,由于钢管的钢材已经经过变形轧制且壁厚薄不能按照棒材标准对低倍组织、非金属夹杂物、淬透性等进行控制。因而必须对热轧棒材、冷拔钢管原材料按各自要求分别控制。
25.热轧棒材原材料满足化学成份:含碳量(0.18~0.23)%、含硅量(0.17~0.37)%、含锰量(0.80~1.10)%、含铬量(1.00~1.30)%、含钛量(0.04~0.10)%、含磷量(≤0.030)%、含硫量(≤0.030)%,此处百分比为质量百分比。低倍组织满足一般疏松≤2.0级;中心疏松≤2.0级;锭型偏析≤2.5级;一般点状偏析≤1.0级;边缘点状偏析≤1.0级。非金属夹杂物满足:a类细夹杂物≤2.0;a类粗夹杂物≤2.0;b类细夹杂物≤2.5;b类粗夹杂物≤2.5;c类细
夹杂物≤2.0;c类粗夹杂物≤2.0;d类细夹杂物≤2.5;d类粗夹杂物≤2.5。
26.冷拔无缝钢管满足化学成份仍按热轧棒材要求。
27.硬度:钢管以正火状态交货,硬度值应为hb170-220。
28.晶粒度:按yb/t5148渗碳法,925℃
×
8小时,奥氏体晶粒度不粗于5级。
29.表面质量:按gb/t8162标准规定。
30.钢管尺寸允许偏差:外径允许偏差
±
0.15毫米,内径允许偏差
±
0.50毫米,因保持架原材料采用低碳合金钢,为满足表面有足够强度、耐磨、心部有足够韧性,故采用渗碳热处理方法实现。
31.根据本发明的一种实施方式,采用钢管切割机进行管料下料,采用成形切割刀具,系统自动监控切割刀具使用寿命,具备自动分离料头、料尾,下料管料的功能。
32.根据本发明的一种实施方式,对管料进行成形处理形成成形管料,成形处理为采用油压机安装成形专用模具缩口成形或采用冷辗扩机安装辗压专用模具冷辗扩成形。缩口成形时,采用上模座和下模座合模成形,分模线位于保持架外球面中心位置,上模座和下模座的内弧面圆弧和直径为保持架外球面圆弧和直径,因而缩口成形的保持架外球面直径是由上、下模具腔决定,因而保持架外球面尺寸和形状是稳定的。
33.根据本发明的一种实施方式,采用数控车床定位成形管料的外球面和一端平面,精车成形管料的内球面和和作为基面的另一端平面为:采用缩口成形或冷辗扩成形的外球面和其中一端平面作为定位夹紧基准,外球面夹紧位置应确保在切削作用下夹紧牢固,分工步完成对基面(另一端平面)及内球面车削。
34.根据本发明的一种实施方式,采用数控车床定位成形管料的外球面和基面,精车一端平面为:采用缩口成形或冷辗扩成形的外球面和已车削基面为定位夹紧基准,完成对与基面相对的一端平面的车削,满足保持架总高度要求,并对保持架外球面中心高附加控制。
35.根据本发明的一种实施方式,根据窗孔形状和壁厚选择合适的冲床吨位,采用从内球面向外球面冲压,窗孔形状由冲头决定,同时对外球面的圆弧和基面进行定位,对于基面相对的一端平面处的内孔进行压紧。由于保持架布置的数个窗孔形状一致,可一次完成数个窗孔冲压,具备窗孔分度均匀,变形均匀一致性好、生产效率高、劳动安全保证等特点。
36.根据本发明的一种实施方式,采用基面和与其对应的内孔为定位基准,与基面相对的一端平面和内孔为夹紧基准,采用数控铣床一次安装2把专用铣刀一次完成相对窗孔的上平面和下平面铣削。
37.根据本发明的一种实施方式,渗碳热处理包括装料、上料、清洗、烘干、渗碳淬火、淬后清洗、回火、移动和下料。
38.在本实施方式中,采用自动控制渗碳热处理多用炉或连续炉进行渗碳处理。装框时,多个成形管料同时进行渗碳处理,各成形管料应整齐或错位摆放,各成形管料之间保持≥1毫米间隙,成形管料不能装出料筐高度。上料时,用行车装料筐吊到推车,推车推到升降台,移动到清洗机前。
39.清洗时,将成形管料推进行清洗机,清洗温度60℃
±
10℃,清洗时间≥60分钟,清洗液每周检测一次,每1-3个月更换一次。
40.烘干:将成形管料推至烘干炉,烘干温度:480℃
±
10℃,烘干时间≥60分钟。
41.渗碳淬火:将成形管料推进渗碳炉,按工件工艺技术要求设置工艺参数对工件进行渗碳淬火。每个作业阶段应对设备和仪表进行观察,记录到《渗碳淬火过程监控记录表》,异常情况及时汇报,生产过程中,应按规定(每小时检查1次)检查丙烷站、压送站的工作状况;渗碳炉每月定期烧碳黑一次,炉温及碳势每周校验一次,验证方法为九点法,渗层均匀性≤0.2毫米,并形成记录,每周检查一次淬火油位并及时添加,每季度检测一次淬火油冷却特性。
42.淬后清洗:将成形管料推进清洗机,成形管料淬后清洗。清洗温度60℃
±
10℃,清洗时间≥50分钟,清洗液每周检测一次,每一至三个月更换一次,形成记录。
43.回火:将成形管料推进回火炉,工件回火。回火温度170℃
±
10℃,回火时间≥150分钟,零件淬火与回火间隔≤2小时。
44.移动:回火结束,将成形管料拉到小车上,移动到升降台前,将工件和料框通过升降台推至推车上。
45.下料:用行车将成形管料和料框吊到卸料装斗。摆放时小心磕碰伤,保证工件整齐,数量一致。
46.在渗碳处理处理过程中进行对成形管料进行监控,监控的过程参数为:高温均热阶段、强渗阶段、扩散阶段、降温均热阶段的温度、碳势、时间。淬火油温度、淬火冷却特性曲线、淬火冷却时间、回火的温度和时间、满足有效渗碳层、金相组织、表面硬度、心部硬度、变形量等要求。
47.根据本发明的一种实施方式,渗碳处理结束后,采用复合立式倒置车床,采用小端面(与基面相对的一端平面)的大内孔(与前述一端平面对应的内控部分)为定位基准,外球面为夹紧基准,配置硬车端面刀片和断续切削的硬车内球面刀片,按预先编制程序,完成对基面及内球面的硬车。
48.然后,采用复合立式倒置车床,先完成硬铣窗孔平面,再硬车外球面,其中硬铣窗孔平面是以硬车后的基面及内孔为定位,利用窗孔定位棒对准窗孔位置,立即对另一端面压紧,采用预先编制程序,一次安装2把硬铣刀片,一次完成相对窗孔上平面、下平面硬铣,通过数控分度,完成所有窗孔平面硬铣。后采用断续切削外球面硬车刀片完成对外球面硬车,至此形成等速万向节保持架,等速万向节保持架的结构如图2所示。
49.根据本发明的上述方案,通过上述方法得到的等速万向节保持架的形状和尺寸精度能够得到有效保证,而且等速万向节保持架的力学性能优异,不会产生应力集中和裂纹断裂的问题,并且整个加工工艺简单快捷,定位基准少,降低了工艺难度,有效提高了生产效率和成品良品率。
50.最后说明的是,以上优选实施例仅用以说明本发明的技术方案而非限制,尽管通过上述优选实施例已经对本发明进行了详细的描述,但本领域技术人员应当理解,可以在形式上和细节上对其作出各种各样的改变,而不偏离本发明权利要求书所限定的范围。