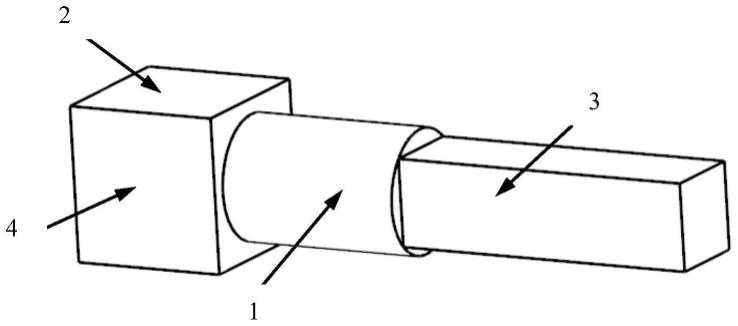
1.本发明涉及机械加工领域,针对于受零件装夹部位干涉受限,无法在零件内孔或外圆上进行试切测量对刀及塞尺测量对刀的情况。本发明能够满足对刀受限一侧刀具的间接对刀需要并具备较高的对刀测量转换精度。
背景技术:2.航空发动机盘类及带法兰结构的短轴类零件在制造过程中需对其一侧工艺凸台进行限位压紧,由于部分零件的工艺凸台轴向厚度较小且需起到径向限位作用,零件自身型面特征除工艺凸台外无有效的外圆面供刀具外圆或内孔对刀使用。一般情况下需保证零件工艺凸台有足够的外伸量以满足数控机床加工刀具对刀需要,在零件装夹前对工艺凸台外圆或内孔进行整周车加工,通过对零件内孔或外圆的精确找正,靠夹具压板空隙处的工艺凸台外伸的外圆或内孔进行塞尺测量对刀。有时候工艺凸台的外伸量过小不足切削刀具圆弧大小即无法满足对刀条件。对于前期无预见性的操作人员,在零件绝大表面完成精加工后需进行受限一侧刀具对刀时,零件的受重复装夹定位及自身加工变形影响容易产生质量问题。
技术实现要素:3.为解决单侧刀具对刀受限问题,使用专用对刀块来间接转化测量对刀,可以有效解决上述对刀受限问题,同时具有较好的对刀测量精度。
4.本发明是通过以下技术方案来实现:
5.一种内孔外圆对刀方式间的测量转换方法,零件主要针对无一侧无有效对刀圆柱面的零件,航空发动机盘类及带法兰结构的短轴类零件,包括如下步骤:
6.步骤1,根据零件结构,在零件不受限一侧机床刀架上安装标准高度刀具;
7.步骤2,在对刀不受限一侧精密圆上使用标准高度刀具进行对刀;
8.步骤3,根据对刀后的精确测量值以建立工件坐标系wcs;
9.步骤4,将磁力表架吸附在机床导轨平面上保证其稳固无松动;
10.步骤5,在磁力表上夹紧专用对刀块;
11.步骤6,在机床刀架上吸附另一块磁力表架并夹紧千分表;
12.步骤7,使用千分表对专用对刀块的水平面进行校平;
13.步骤8,使用千分表对专用对刀块0至20mm长度范围的拉直面进行拉直;
14.步骤9,重复步骤7与步骤8内容直至专用对刀块水平面的平面度跳动≤0.01,在0至20mm长度范围的拉直面跳动≤0.01;
15.步骤10,将刀架上吸附的磁力表架取下;
16.步骤11,将前面完成对刀操作的标准刀刀尖移动至专用对刀块一侧;
17.步骤12,用塞尺检查标准刀刀尖与专用对刀块的贴合程度,即塞尺在刀尖与对刀块间移动存在阻塞;
18.步骤13,记录此时标准高度刀具其径向对刀点在数控机床工件坐标系的x1值;
19.步骤14,将受限一侧刀具刀尖移动至专用对刀块另一侧;
20.步骤15,用塞尺检查受限一侧刀具刀尖与专用对刀块的贴合,即塞尺在刀尖与对刀块间移动存在阻塞;
21.步骤16,在机床上输入x1±2×
(ds+dk),通过以上步骤对受限一侧刀具的对刀进行间接测量转换。(注:其中ds为塞尺厚度,dk为专用对刀块厚度)
22.一种内孔外圆对刀方式间的测量转换方法使用的加工设备,包括光栅尺、脉冲发生器,伺服电机与伺服系统,利用机床精密光栅尺及伺服系统建立待加工零件工件坐标系,通过光栅尺的精确测量反馈、伺服电机的精准移动与伺服系统的计算实现上述内孔外圆对刀方式间的测量转换方法。
23.与现有技术相比,本发明具有以下有益的技术效果:
24.本发明提供一种内孔外圆对刀方式间的测量转换方法,传统对刀必须在零件实体上对刀,对于受工装及零件结构等影响因素无法正常对刀的情况,现有对刀方法难以实现。该方法利用数控设备的测量与移动精度,使用专用对刀块完成对刀受限一侧刀具的对刀操作,具有较强的适应性及现场推广价值。
附图说明
25.图1为对刀块结构示意图;
26.图2为操作步骤流程图;
27.1.对刀块夹持柱面;2.对刀块校平面;3.对刀块拉直面;4.对刀块对刀面;
具体实施方式
28.本实施例通过以上陈述的方法,包括通过标准高度刀具对应回转零件中心,通过零件精密圆建立标准高度刀具相对于工件的精确坐标关系,并对专用对刀块校平与拉直,利用专用对刀块的转介,将非受限一侧刀具径向对刀点的坐标值与受限一侧刀具径向对刀点产生对应关系以完成对受限一侧刀具的对刀操作。此方法适用于各种单侧对刀受限情况下的对刀测量转换,在实际加工中已实际验证,对于精度较高的零件配合刀补的使用及测具的测量监控能够满足高精度加工需要,具有广泛的推广价值和实践意义。
29.例如使用此方法对无有效外圆轮廓且装夹凸台干涉受限的零件其外圆刀进行对刀,使用专用对刀块进行测量转换,在零件内孔进行对刀建立工件坐标系,通过对图1所示专用对刀块水平面使用表分表进行校平,再对专用对刀块的拉直面进行拉直,将内孔刀具刀尖移动至对刀块一侧对刀面,记录其工件坐标系径向示数x1,再将受限一侧刀具刀尖移动至对刀块另一侧对刀面,在受限一侧刀具机床刀位列表的径向参数栏输入x=x1±2×
(ds+dk),即可完成受限一侧刀具的径向对刀。
30.最后应当说明的是:以上实施例仅用以说明本发明的技术方案而非对其限制,尽管参照上述实施例对本发明进行了详细的说明,所属领域的普通技术人员应当理解:依然可以对本发明的具体实施方式进行修改或者等同替换,而未脱离本发明精神和范围的任何修改或者等同替换,其均应涵盖在本发明的权利要求保护范围之内。
技术特征:1.一种内孔外圆对刀方式间的测量转换方法,零件针对无一侧无有效对刀圆柱面的零件,航空发动机盘类及带法兰结构的短轴类零件,其特征在于,包括如下步骤:步骤1,根据零件结构,在零件不受限一侧机床刀架上安装标准车刀刀杆与适配刀片;步骤2,在对刀不受限一侧精密圆上使用标准高度刀具进行对刀;步骤3,根据对刀后的精确测量值以建立工件坐标系wcs;步骤4,将磁力表架吸附在机床导轨平面上保证其稳固无松动;步骤5,在磁力表上夹紧对刀块;步骤6,在机床刀架上吸附另一块磁力表架并夹紧千分表;步骤7,使用千分表对对刀块的水平面进行校平;步骤8,使用千分表对对刀块0mm至20mm长度范围的拉直面进行拉直;步骤9,重复步骤7与步骤8,直至对刀块水平面的平面度跳动≤0.01mm;步骤10,将刀架上吸附的磁力表架取下;步骤11,将前面完成对刀操作的标准刀刀尖移动至对刀块一侧;步骤12,用塞尺检查标准刀刀尖与对刀块的贴合程度,即塞尺在刀尖与对刀块间移动存在阻塞;步骤13,记录此时标准高度刀具其径向对刀点在数控机床工件坐标系的x1值;步骤14,将受限一侧刀具刀尖移动至对刀块另一侧;步骤15,用塞尺检查受限一侧刀具刀尖与对刀块的贴合,即塞尺在刀尖与对刀块间移动存在阻塞;步骤16,在机床上输入x1±2×
(d
s
+d
k
),通过以上步骤对受限一侧刀具的对刀进行间接测量转换,其中d
s
为塞尺厚度,d
k
为专用对刀块厚度。2.根据权利要求1所述的一种内孔外圆对刀方式间的测量转换方法,其特征在于,对刀块长45mm,对刀块由三段结构组成,第一段为10mm
×
10mm
×
10mm的正方体,其上下面用于水平面校平,前后面用于刀具对刀测量转换,第二段为的圆柱体,其圆柱面用于磁力表架夹头的夹持,第三段为5.65mm
×
5.65mm
×
23mm的长方体,其前后上下面均可作为拉直面用于对刀块拉直操作,以便于对刀块轴线与机床导轨平行。3.根据权利要求1所述的一种内孔外圆对刀方式间的测量转换方法,其特征在于,步骤1中,标准车刀刀杆高度h为32,若使用小于此刀杆高度的标准车刀需在刀杆下垫入垫刀片,保证其车刀刀尖与标准车刀刀杆高度h为32的刀尖高度一致,目的是保证车刀刀尖与机床主轴回转中心高度相同。4.根据权利要求1所述的一种内孔外圆对刀方式间的测量转换方法,其特征在于,步骤2中,需选择精密圆对刀,此精密圆的公差是对刀不受限一侧零件轮廓节圆公差中最严格的且尽可能有精密测具进行测量,原则上精密圆的公差≤0.05。5.根据权利要求1所述的一种内孔外圆对刀方式间的测量转换方法,其特征在于,步骤3中,建立的工件坐标系wcs,由标准车刀通过试切法建立。6.根据权利要求1所述的一种内孔外圆对刀方式间的测量转换方法,其特征在于,步骤6中,吸附在机床刀架上的磁力表架夹紧的千分表,分度值为0.002。7.根据权利要求1所述的一种内孔外圆对刀方式间的测量转换方法,其特征在于,步骤7中,对对刀块进行校平,保证在10mm
×
10mm的平面上对对刀块平面度进行评定,保证其平
面度≤0.01mm。8.根据权利要求1所述的一种内孔外圆对刀方式间的测量转换方法,其特征在于,步骤8中,0mm至20mm长度范围为必要拉直长度,拉直长度距离不得≤20mm。9.根据权利要求1所述的一种内孔外圆对刀方式间的测量转换方法,其特征在于,步骤12中,使用的塞尺厚度≤0.05mm。10.根据权利要求1所述的一种内孔外圆对刀方式间的测量转换方法,其特征在于,步骤9中,在0至20mm长度范围的拉直面跳动≤0.01mm。
技术总结本发明公开了一种内孔外圆对刀方式间的测量转换方法,针对无一侧无有效对刀圆柱面的零件,航空发动机盘类及带法兰结构的短轴类零件,对刀块长45mm,对刀块由三段结构组成,第一段为10mm
技术研发人员:鲁斌 王荣 吴海涛 徐扬 俞树霆 赵磊 王晓春
受保护的技术使用者:中国航发动力股份有限公司
技术研发日:2022.09.29
技术公布日:2022/11/22