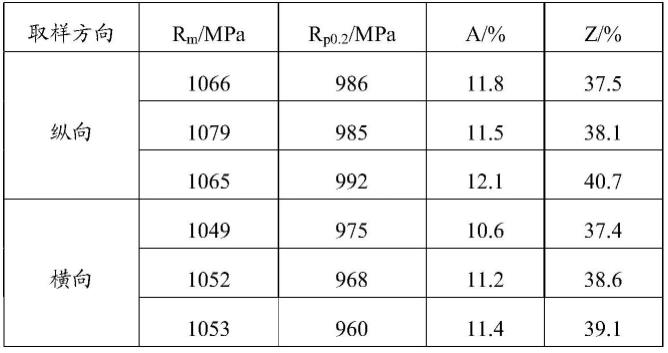
1.本发明属于钛合金材料加工技术领域,尤其涉及一种钛合金大规格棒材的锻造方法。
背景技术:2.钛合金因具有高比强度、比模量、优异的耐腐蚀性能、高韧性和可焊接等性能特点,广泛应用于航空、航天、舰船、兵器、核工业等重要的工业领域。钛元素在自然界中的储量相对丰富,在所有元素中位居第十位。然而与其巨大的储量相对应的是钛合金的使用量不仅远远低于钢和铝合金,并且也远低于铜合金和镁合金,限制其广泛应用的主要因素是其相对于昂贵的成本,钛元素不仅存在分散广并难于提取的因素,同时其繁琐的加工过程和相对较低的成材率,均使得钛合金的成本居高不下,限制了其在建筑、汽车、体育休闲等民用领域的用量。
3.近年来,新一代武器装备开始大量采用钛合金来实现其高减重、长寿命和低成本的设计与应用需求,对钛合金的需求也越来越高,而钛合金居高不下的加工和使用成本已经成为制约其扩大应用的主要障碍,迫切需要发展低成本钛合金材料及其加工技术。
4.钛合金的加工过程一般分为海绵钛冶炼、铸锭熔炼、锻造/轧制等工艺流程。目前,降低钛合金成本主要从降低钛合金化元素成本及采用缩短加工制备工艺两方面着手,例如在航空用钛合金棒材锻造过程中,为制备出满足上述技术要求的高品质钛合金棒材,往往需要在β单相区2~4火次开坯锻造,α+β两相区5~10火次反复墩拔以及1~2火次成型,生产周期长,打磨损耗量大,且成材率低,因而生产成本居高不下。因此,如何通过合理的短流程锻造工艺设计,降低从钛合金铸锭到合格棒材的火次,实现低成本和高综合性能的良好匹配,已成为低成本钛合金关键技术开发的难点。迫切需要发展钛合金低成本化加工技术,解决钛合金材料成本高的瓶颈问题,扩大钛合金的应用领域。
技术实现要素:5.有鉴于此,本发明要解决的技术问题在于提供一种低成本、高性能钛合金大规格棒材的锻造方法,其目的是通过较少的锻造火次成功解决大规格棒材组织均匀化和细晶化的技术问题,在保证钛合金优异力学性能的前提下,降低了锻造工艺低成本,满足了各航空、航天、兵器等领域对低成本、高性能钛合金结构件的需求。
6.本发明提供了一种钛合金大规格棒材的锻造方法,包括以下步骤:
7.s1)将钛合金铸锭加热至1100℃~1200℃,进行1火次锻造,该火次的锻造墩拔次数不超过三墩三拔,单次镦粗变形量为40%~65%,得到开坯后锻坯;
8.s2)将所述开坯后锻坯加热至1000℃~1100℃,进行1火次煅造,该火次的锻造墩拔次数不超过二墩二拔,单次镦粗变形量为45%~60%,然后进行再结晶退火处理,得到第一中间锻坯;
9.s3)将所述第一中间锻坯加热至β相变点温度以下20℃~50℃,进行2~3火次锻
造,每一火次的墩拔次数不超过两墩两拔,单次墩粗变形量为35%~50%,得到第二中间锻坯;
10.s4)将所述第二中间锻坯加热至β相变点温度以下30℃~60℃,进行1火次成型锻造,得到钛合金大规格棒材。
11.优选的,所述钛合金铸锭为tc32钛合金铸锭。
12.优选的,所述步骤s1)中每次镦粗后的锻坯均压制为扁方;所述扁方的高宽比为1:(1.5~3.5)。
13.优选的,所述步骤s1)中每次墩拔均按照轴向墩粗、压制扁方、扁方墩粗、轴向拔长的墩拔过程进行。
14.优选的,所述步骤s1)中墩拔的锻造应变速率逐渐降低,第一次墩拔的锻造应变速率为0.15~0.2s-1
,最后一次墩拔的锻造应变速率为0.05~0.1s-1
,终锻温度不低于850℃。
15.优选的,所述步骤s2)中墩拔为一墩一拔时,墩拔的锻造应变速率为0.05~0.1s-1
,终锻温度不低于850℃;
16.所述步骤s2)中墩拔为二墩二拔时,墩拔的锻造应变速率逐渐降低,第一次墩拔的锻造应变速率为0.08~0.1s-1
,第二次墩拔的锻造应变速率为0.05~0.07s-1
,终锻温度不低于850℃。
17.优选的,所述步骤s2)中再结晶退火处理的温度为800℃~950℃;再结晶退火处理的时间为120~300min。
18.优选的,所述步骤s3)中每火次的墩拔为一墩一拔时,墩拔的锻造应变速率为0.03~0.1s-1
,终锻温度不低于800℃;
19.所述步骤s3)中每火次的墩拔为二墩二拔时,墩拔的锻造应变速率逐渐降低,第一次墩拔的锻造应变速率为0.08~0.1s-1
,第二次墩拔的锻造应变速率为0.03~0.06s-1
,终锻温度不低于800℃。
20.优选的,所述步骤s4)中成型锻造的锻造应变速率为0.05~0.01s-1
,终锻温度不低于800℃。
21.优选的,所述步骤s3)每火次锻造结束后,如果锻坯没有裂纹出现,采用热料回炉的方式进行下一火次的加热锻造。
22.本发明提供了一种钛合金大规格棒材的锻造方法,包括以下步骤:s1)将钛合金铸锭加热至1100℃~1200℃,进行1火次锻造,该火次的锻造墩拔次数不超过三墩三拔,单次镦粗变形量为40%~65%,得到开坯后锻坯;s2)将所述开坯后锻坯加热至1000℃~1100℃,进行1火次煅造,该火次的锻造墩拔次数不超过二墩二拔,单次镦粗变形量为45%~60%,然后进行再结晶退火处理,得到第一中间锻坯;s3)将所述第一中间锻坯加热至β相变点温度以下20℃~50℃,进行2~3火次锻造,每一火次的墩拔次数不超过两墩两拔,单次墩粗变形量为35%~50%,得到第二中间锻坯;s4)将所述第二中间锻坯加热至β相变点温度以下30℃~60℃,进行1火次成型锻造,得到钛合金大规格棒材。与现有技术相比,本发明基于钛合金本身具有的较好断裂韧度和优良的加工性能,采用大变形、反复墩拔,扁方墩拔以及再结晶退火等工艺措施,实现大厚截面锻坯的心部、边缘以及多方向的变形均匀性,并匹配每次墩拔过程中锻造应变速率,控制动态再结晶、静态再结晶与晶粒形核长大的综合平衡,从而以较少的锻造火次成功实现了钛合金棒材组织均匀化和细晶化的技术问题,在保
证钛合金优异力学性能的前提下,降低了锻造工艺成本,满足了各航空、航天、兵器等领域对低成本、高性能钛合金结构件的需求。
附图说明
23.图1为本发明实施例1中得到的钛合金大规格棒材的显微组织图;
24.图2为本发明实施例2中得到的钛合金大规格棒材的显微组织图;
25.图3为本发明实施例3中得到的钛合金大规格棒材的显微组织图。
具体实施方式
26.下面将结合本发明实施例,对本发明实施例中的技术方案进行清楚、完整地描述,显然,所描述的实施例仅仅是本发明一部分实施例,而不是全部的实施例。基于本发明中的实施例,本领域普通技术人员在没有做出创造性劳动前提下所获得的所有其他实施例,都属于本发明保护的范围。
27.本发明提供了一种钛合金大规格棒材的锻造方法,包括以下步骤:s1)将钛合金铸锭加热至1100℃~1200℃,进行1火次锻造,该火次的锻造墩拔次数不超过三墩三拔,单次镦粗变形量为40%~65%,得到开坯后锻坯;s2)将所述开坯后锻坯加热至1000℃~1100℃,进行1火次煅造,该火次的锻造墩拔次数不超过二墩二拔,单次镦粗变形量为45%~60%,然后进行再结晶退火处理,得到第一中间锻坯;s3)将所述第一中间锻坯加热至β相变点温度以下20℃~50℃,进行2~3火次锻造,每一火次的墩拔次数不超过两墩两拔,单次墩粗变形量为35%~50%,得到第二中间锻坯;s4)将所述第二中间锻坯加热至β相变点温度以下30℃~60℃,进行1火次成型锻造,得到钛合金大规格棒材。
28.其中,本发明对所有原料的来源并没有特殊的限制,为市售即可。
29.将钛合金铸锭加热至1100℃~1200℃,进行1火次锻造,该火次的锻造墩拔次数不超过三墩三拔,单次镦粗变形量为40%~65%,得到开坯后锻坯;所述钛合金铸锭优选为tc32钛合金铸锭;tc32钛合金铸锭具有的较好断裂韧度和优良的加工性能;在本发明中,优选将钛合金铸锭加热至1140℃~1200℃,更优选至1160℃~1190℃,进行1火次锻造;在本发明中,该火次的锻造墩拔次数优选为二墩二拔或三墩三拔,更优选为三墩三拔;每次镦粗后的锻坯均优选压制为扁方;所述扁方的高宽比优选为1:(1.5~3.5),更优选为1:(2~3.5);每次墩拔压制扁方的高宽比可以相同,也可以不同,并无特殊的限制;每次墩拔均优选按照墩粗、压制扁方、扁方墩粗、轴向拔长的墩拔过程进行;单次镦粗变形量优选为40%~65%,更优选为45%~65%,再优选为50%~65%;每次镦粗的变形量可以相同,也可不同,并无特殊的限制,在本发明中优选墩拔锻造中每次镦粗的变形量逐渐降低;所述墩拔的锻造应变速率优选逐渐降低,第一次墩拔的锻造应变速率优选为0.15~0.2s-1
,更优选为0.15~0.18s-1
;最后一次墩拔的锻造应变速率优选为0.05~0.1s-1
,更优选为0.08~0.09s-1
;终锻温度优选不低于850℃,更优选为860℃~950℃,再优选为880℃~900℃;锻造结束后,优选水冷快速冷却至室温;水冷后优选还进行表面修模处理,得到开坯后锻坯。
30.在此步骤中通过将铸锭加热到1100℃~1200℃之间进行1火次反复墩拔变形,目的是高温保温时将铸锭的组织均匀化,随后将铸锭粗大的原始β晶粒组织进行充分破碎并细化。与传统钛合金常规墩拔变形不同,本发明将每次墩粗后的锻坯均压制为扁方,随后在
沿着扁方的流线方向上进行墩粗变形,最后在进行传统的拔长变形。采用该锻造工艺,一次墩拔过程同时实现了锻坯在平行于流线方向和垂直于流线方向的变形加工,达到了传统墩拔和换向墩拔相结合的工艺效果,充分改善了锻坯的组织均匀性,进一步减小了锻坯在不同区域组织的差异性,有效消除了锻坯可能出现的各向异性。通过控制墩粗变形量和墩拔的锻造应变速率,实现了钛合金组织的动态再结晶与晶粒形核长大的综合平衡,考虑钛合金相对较差的工艺塑性,因此严格控制墩拔次数不超过三墩三拔。锻造结束后迅速水冷淬火,抑制了在冷却过程中晶粒内析出的长条状α相的粗化,获得了细小均匀的片层组织。
31.将所述开坯后锻坯加热至1000℃~1100℃,进行1火次锻造,该火次的锻造墩拔次数不超过二墩二拔,单次镦粗变形量为45%~60%,然后进行再结晶退火处理,得到第一中间锻坯;在本发明中,优选将开坯后锻坯加热至1030℃~1090℃,更优选至1050℃~1070℃,进行1火次锻造;该火次的锻造墩拔次数不超过二墩二拔,单次镦粗变形量优选为50%~60%;每次镦粗的变形量可以相同,也可不同,并无特殊的限制;当该墩拔为一墩一拔时,墩拔的锻造应变速率优选为0.05~0.1s-1
,更优选为0.06~0.09s-1
;当该墩拔为二墩二拔时,墩拔的锻造应变速率优选逐渐降低,第一次墩拔的锻造应变速率优选为0.08~0.1s-1
,更优选为0.08~0.09s-1
;第二次墩拔的锻造应变速率优选为0.05~0.07s-1
,更优选为0.06~0.07s-1
;终锻温度优选不低于850℃,更优选为860℃~950℃,再优选为860℃~900℃,再优选为860℃~880℃;锻造结束后,优选直接进行再结晶退火处理;所述再结晶退火处理的温度优选为800℃~950℃,更优选为830℃~930℃,再优选为850℃~900℃,最优选为850℃~880℃;再结晶退火处理的时间优选为120~300min,更优选为150~260min,再优选为160~260min;再结晶退火处理结束后,优选在空气中冷却,更优选在空气中冷却至室温;冷却后优选还进行表面修模处理,得到第一中间锻坯。
32.此步骤中首先将锻坯在流线方向上进行反复墩拔变形,使锻坯的晶粒进一步获得破碎并细化,锻造结束后直接将锻坯进行再结晶退火处理,目的是通过静态再结晶,将前两火次锻造后的锻坯由于大变形而产生的相对粗大变形晶粒重新转变为无畸变的晶粒,进一步细化了晶粒组织,提高了工艺塑性。由于采用直接将锻造后的锻坯进行再结晶退火处理,简化了锻坯冷却和重新加热的生产工序,降低了工作量,提高了生产效率,降低了生产成本。
33.将所述第一中间锻坯加热至β相变点温度以下20℃~50℃,进行2~3火次锻造,每一火次的墩拔次数不超过两墩两拔,单次墩粗变形量为35%~50%,得到第二中间锻坯;在本发明中,优选将第一中间锻坯加热至β相变点温度以下20℃~40℃,更优选至β相变点温度以下20℃~35℃,再优选至β相变点温度以下25℃~35℃,进行2~3火次锻造;每一火次的墩拔次数不超过两墩两拔,单次墩粗变形量优选为40%~50%;当每火次的墩拔为一墩一拔时,墩拔的锻造应变速率优选为0.03~0.1s-1
,更优选为0.05~0.09s-1
,再优选为0.05~0.08s-1
;当每火次的墩拔为二墩二拔时,墩拔的锻造应变速率优选逐渐降低,第一次墩拔的锻造应变速率优选为0.08~0.1s-1
,更优选为0.08~0.09s-1
;第二次墩拔的锻造应变速率优选为0.03~0.06s-1
,更优选为0.05~0.06s-1
;终锻温度优选不低于800℃,更优选为800℃~900℃,再优选为820℃~850℃,最优选为820℃~840℃;每火次锻造结束后,如果锻坯没有裂纹出现,可采用热料回炉的方式进行下一火次的加热锻造;锻造结束后,优选在空气中冷却,更优选在空气中冷却至室温,得到二中间锻坯。
34.此步骤将铸锭在β相变点温度以下20℃~50℃,进行2~3火次锻造,目的是进一步细化和均匀化显微组织,由于变形温度较低,避免在变形过程中产生裂纹,因此严格控制每火次墩拔次数不超过两墩两拔,同时通过控制墩粗变形量和墩拔的锻造应变速率,使钛合金显微组织反复发生动态再结晶,以得到组织性能均匀的钛合金棒材。
35.将所述第二中间锻坯加热至β相变点温度以下30℃~60℃,进行1火次成型锻造,得到钛合金大规格棒材;在本发明中,优选将第二中间锻坯加热至β相变点温度以下40℃~60℃,更优选至β相变点温度以下40℃~50℃;所述成型锻造优选为滚圆成型锻造;所述成型锻造的锻造应变速率优选为0.05~0.01s-1
,更优选为0.04~0.01s-1
,再优选为0.04~0.02s-1
;终锻温度优选不低于800℃,更优选为800℃~850℃,再优选为810℃~820℃;锻造结束后,优选在空气中冷却,更优选在空气中冷却至室温,得到钛合金大规格棒材。
36.本发明基于钛合金本身具有的较好断裂韧度和优良的加工性能,采用大变形、反复墩拔,扁方墩拔以及再结晶退火等工艺措施,实现大厚截面锻坯的心部、边缘以及多方向的变形均匀性,并匹配每次墩拔过程中锻造应变速率,控制动态再结晶、静态再结晶与晶粒形核长大的综合平衡,从而以较少的锻造火次成功实现了钛合金棒材组织均匀化和细晶化的技术问题,在保证钛合金优异力学性能的前提下,降低了锻造工艺成本,满足了各航空、航天、兵器等领域对低成本、高性能钛合金结构件的需求。
37.为了进一步说明本发明,以下结合实施例对本发明提供的一种钛合金大规格棒材的锻造方法进行详细描述。
38.以下实施例中所用的试剂均为市售。实施例中所用铸锭的尺寸可以为φ380mm~φ980mm,力学性能检测标准为gb/t 228.1-2010。
39.实施例1
40.本实施例为通过5火次锻造工艺获得tc32低成本、高性能钛合金φ200mm棒材,具体包括如下步骤:
41.步骤一:将检验合格的tc32低成本、高性能钛合金φ530mm铸锭加热到1180℃,进行一火次三墩三拔锻造,第一道次墩拔变形量为60%,控制锻造变形速率为0.15s-1
,墩粗后压制的扁方高宽比为1:3;第二道次墩拔变形量为55%,控制锻造变形速率为0.1s-1
,墩粗后压制的扁方高宽比为1:3;第三道次墩拔变形量为50%,墩拔变形速率为0.08s-1
,墩粗后压制的扁方高宽比为1:2.5;终锻温度900℃,随后浸水快速冷却至室温,经表面修磨处理得到锻坯。
42.步骤二:将步骤一所述锻坯加热到1070℃,进行一火次两墩两拔锻造,第一道次墩拔变形量为60%,控制锻造变形速率为0.08s-1
;第二道次墩拔变形量为50%,控制锻造变形速率为0.06s-1
,终锻温度860℃。随后将锻坯直接放入加热炉中进行再结晶退火处理,退火温度为860℃,保温160min后在空气中冷却,并进行表面修磨处理。
43.步骤三:将完成步骤二的锻坯加热到β相变点温度以下25℃,进行两火次锻造,每火次均为两墩两拔锻造。第一道次墩拔变形量均为45%,控制锻造变形速率为0.09s-1
;第二道次墩拔变形量均为40%,控制锻造变形速率为0.05s-1
,终锻温度820℃,空冷后得到锻坯。
44.步骤四:将步骤三所述锻坯加热到β相变点温度以下50℃,进行1火次棒材滚圆锻造成型,控制锻造变形速率为0.04s-1
。终锻温度810℃,空冷后得到组织性能均匀的棒材。
45.本实施例制备的tc32低成本、高性能钛合金φ200mm棒材经热处理后,在室温条件
下的力学性能如表1所示,显微组织如图1所示,由表1与图1可知其满足相关技术标准要求。
46.表1实施例1中tc32低成本、高性能钛合金φ200mm棒材的力学性能
[0047][0048]
实施例2
[0049]
本实施例为通过5火次锻造工艺获得tc32低成本、高性能钛合金φ300mm棒材,具体包括如下步骤:
[0050]
步骤一:将检验合格的tc32低成本、高性能钛合金φ620mm铸锭加热到1190℃,进行一火次三墩三拔锻造,第一道次墩拔变形量为65%,控制锻造变形速率为0.18s-1
,墩粗后压制的扁方高宽比为1:3;第二道次墩拔变形量为60%,控制锻造变形速率为0.12s-1
,墩粗后压制的扁方高宽比为1:2.5;第三道次墩拔变形量为55%,墩拔变形速率为0.09s-1
,墩粗后压制的扁方高宽比为1:2;终锻温度890℃,随后浸水快速冷却至室温,经表面修磨处理得到锻坯。
[0051]
步骤二:将步骤一所述锻坯加热到1060℃,进行一火次两墩两拔锻造,第一道次墩拔变形量为55%,控制锻造变形速率为0.09s-1
;第二道次墩拔变形量为50%,控制锻造变形速率为0.07s-1
,终锻温度880℃。随后将锻坯直接放入加热炉中进行再结晶退火处理,退火温度为850℃,保温220min后在空气中冷却,并进行表面修磨处理。
[0052]
步骤三:将完成步骤二的锻坯加热到β相变点温度以下30℃,进行两火次锻造,每火次均为两墩两拔锻造。第一道次墩拔变形量均为50%,控制锻造变形速率为0.08s-1
;第二道次墩拔变形量均为45%,控制锻造变形速率为0.06s-1
,终锻温度830℃,空冷后得到锻坯。
[0053]
步骤四:将步骤三所述锻坯加热到β相变点温度以下50℃,进行1火次棒材滚圆锻造成型,控制锻造变形速率为0.03s-1
。终锻温度820℃,空冷后得到组织性能均匀的棒材。
[0054]
本实施例制备的tc32低成本、高性能钛合金φ300mm棒材经热处理后,在室温条件下的力学性能如表2所示,显微组织如图2所示,由表2与图2可知其满足相关技术标准要求。
[0055]
表2实施例2中tc32低成本、高性能钛合金φ300mm棒材的力学性能
[0056][0057]
实施例3
[0058]
本实施例为通过6火次锻造工艺获得tc32低成本、高性能钛合金φ380mm棒材,具体包括如下步骤:
[0059]
步骤一:将检验合格的tc32低成本、高性能钛合金φ860mm铸锭加热到1160℃,进行一火次三墩三拔锻造,第一道次墩拔变形量为60%,控制锻造变形速率为0.16s-1
,墩粗后压制的扁方高宽比为1:3.5;第二道次墩拔变形量为50%,控制锻造变形速率为0.1s-1
,墩粗后压制的扁方高宽比为1:2.5;第三道次墩拔变形量为45%,墩拔变形速率为0.08s-1
,墩粗后压制的扁方高宽比为1:2;终锻温度880℃,随后浸水快速冷却至室温,经表面修磨处理得到锻坯。
[0060]
步骤二:将步骤一所述锻坯加热到1050℃,进行一火次两墩两拔锻造,第一道次墩拔变形量为50%,控制锻造变形速率为0.08s-1
;第二道次墩拔变形量为50%,控制锻造变形速率为0.06s-1
,终锻温度870℃。随后将锻坯直接放入加热炉中进行再结晶退火处理,退火温度为880℃,保温260min后在空气中冷却,并进行表面修磨处理。
[0061]
步骤三:将完成步骤二的锻坯加热到β相变点温度以下25℃,进行三火次锻造,前两火次均为两墩两拔锻造,第三火次为一墩一拔。第一道次墩拔变形量均为40%,控制锻造变形速率为0.08s-1
;第二道次墩拔变形量均为45%,控制锻造变形速率为0.05s-1
,终锻温度840℃,空冷后得到锻坯。
[0062]
步骤四:将步骤三所述锻坯加热到β相变点温度以下40℃,进行1火次棒材滚圆锻造成型,控制锻造变形速率为0.02s-1
。终锻温度810℃,空冷后得到组织性能均匀的棒材。
[0063]
本实施例制备的tc32低成本、高性能钛合金φ380mm棒材经热处理后,在室温条件下的力学性能如表3所示,显微组织如图3所示。由表3与图3可知其满足相关技术标准要求。
[0064]
表3实施例3中tc32低成本、高性能钛合金φ380mm棒材的力学性能
[0065]