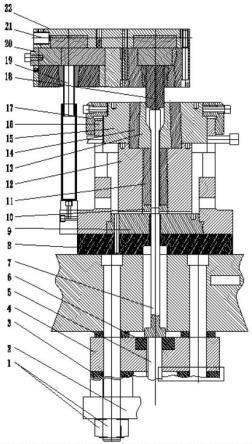
汽车转向系统中间轴u型叉头的双击成型模具及成型工艺
技术领域
1.本发明属于汽车零部件加工领域,具体涉及一种汽车转向系统中间轴的u型叉头双击成型模具及成型工艺。
背景技术:2.汽车转向系统中间轴是汽车传动系统的核心部件之一,包括公轴和母轴,两者通过花键滑动连接。中间轴的公轴一端为u型叉头,其余部分为连接杆,并加工有滑道,即外花键。
3.目前中间轴公轴的加工主要有两种方案:方案1,中间轴采用与其连接杆部直径相近的退火态坯料,先针对头部进行镦粗,然后再进行退火、退火后反挤压成型u型叉头部分,或者不进行退火,加热至900℃,反挤压u型叉头部分。
4.方案2,中间轴采用与其连接杆部直径相近的退火态坯料,冷态挤压棒料的一端,使材料径向流动形成t形头,得到t形坯件,再将t形头的两翼对向弯曲,并形成圆弧,得到公轴端部的u型叉和u型叉内槽。该方案详见本发明人在先申请的专利:cn201911345824.1。
5.以上两种方案存在以下缺点:对于方案1,在成型过程中对头部镦粗后需要进行退火后再反挤压成型u型叉头,或者镦粗后不进行退火,而是加热后再反挤压成型u型叉头;对于前者,加工成本较高,对于后者不仅加工成本高,而且模具寿命较低。
6.对于方案2,材料径向流动时,t型头两翼圆角位置模具受力较大,模具寿命较低,且t型头挤压端圆柱区域残留毛刺需进行清理,增加生产成本;后续弯曲过程,叉头外圆弧部分有开裂风险。
技术实现要素:7.本发明的目的是提供一种汽车转向系统中间轴的u型叉头双击成型模具及成型工艺,该模具将u型叉头的镦挤和反挤压两道工序合并成一道工序,消除了两道工序间冷作硬化带来的影响,节省了退火工序,提高了模具寿命和生产效率,降低了生产成本。
8.为了实现上述目的,本发明所采用的技术方案是:一种汽车转向系统中间轴u型叉头的双击成型模具,包括上模组件和下模组件,所述下模组件设置有放置工件的下凹模,上凹模内设有用于成型u型叉头的叉头成型腔;所述上模组件连接在油压机的压机上模板上,随压机上模板上下移动,上模组件包括分别和所述叉头成型腔配合使用的第一上凸模和第二上凸模,第一上凸模和第二上凸模并排连接在水平滑动件上,水平滑动件吊挂在上模组中的导轨条上,并在水平驱动机构的带动下沿导轨条水平滑动。
9.所述第一上凸模的凸模固定座和上模组件的连接燕尾分座连接,所述第二上凸模的凸模固定座和上模组件的工位固定座板连接,所述连接燕尾分座和所述工位固定座板固定连接在所述水平滑动件上。
10.所述第二上凸模的模芯外对称设有两个随退导向条,随退导向条沿模芯的外表面滑动设置,每个随退导向条和一个杠杆连接。
11.所述第二上凸模的凸模固定座侧面设置有弹簧滑道支架,弹簧滑道支架内设置有滑道,并在滑道内安装弹簧,所述杠杆的一端作为支点转动连接在所述弹簧滑道支架上,杠杆的另一端和所述随退导向条转动连接,杠杆上部靠近支点的位置顶压在所述弹簧上。
12.所述下模组件中设有润滑剂槽,润滑剂槽位于第二上凸模初始位置的正下方,第一上凸模向所述叉头成型腔下压时,第二上凸模的模芯进入润滑剂槽蘸取润滑剂。
13.一种汽车转向系统中间轴的成型工艺,对退火态冷拉棒料进行前处理,得到一个带细杆部的轴类零件,该轴类零件的一端为用于u型叉头成型的粗径端,其余部分均为直径小于粗径端的细杆部,然后利用所述的双击成型模具分两次对所述轴类零件的粗径端冷挤压,以成型u型叉头,接着对已成型u型叉头的零件进行后处理,得到汽车转向系统中间轴成品。
14.上述工艺中,所述双击成型模具先后对所述轴类零件的粗径端进行冷挤压时,先用第一上凸模的模芯向下镦挤零件的粗径端,同时,第二上凸模同步向下运动,第二上凸模的模芯蘸取润滑剂槽中的润滑剂;然后,压机上模板带动第一上凸模和第二上凸模回程,再由水平驱动机构推动第一上凸模和第二上凸模水平移动,使得第二上凸模位于所述叉头成型腔的正上方,然后压机上模板下行,由第二上凸模的模芯向下反挤压被镦挤后的零件粗径端,得到u型叉头。
15.在第二上凸模反挤压零件时,随着u型叉头长度的增长,叉头上端与随退导向条接触并向上推动随退导向条沿第二上凸模的模芯回退,并带动与随退导向条连接的杠杆端部抬起,压缩与杠杆抵接的弹簧。
16.所述前处理包括下料、抛丸、皮膜处理和正挤杆处理。
17.所述后处理包括对u型叉头部分的去毛刺处理、对零件的皮膜处理和对零件上细杆部进行滑道加工处理。
18.本发明的有益效果是:本发明加工的中间轴零件在传统方法中,头部镦挤和反挤压过程中会产生冷作硬化效应,因此需要在两道工序之间增加退火工序,以消除头部硬化效应对反挤压工序模具寿命的影响。采用本发明所述的双击成型模具后,把头部镦挤和反挤压两道工序合并成一道工序,进行连续加工,可以规避冷作硬化带来的影响(影响主要为模具寿命降低),也消除了中间的退火工序,降低了生产成本,且本工序在一工位油压机上进行,有效改善了一台单工位设备每次只能加工一道工序的缺点,提高了生产效率。
附图说明
19.图1为本发明所述的双击成型模具正面的结构剖视图;图2为本发明所述双击成型模具中下模组件正面的结构剖视图;图3为本发明所述双击成型模具中上模组件正面的结构剖视图;图4为本发明所述双击成型模具中第二上凸模侧面的结构剖视图;图5为本发明第一上凸模挤压工件后的模具结构示意图;图6为本发明第二上凸模挤压工件前的模具结构示意图;图7为本发明第二上凸模挤压工件后的模具结构示意图;
图8为本发明所述汽车转向系统中间轴成型过程的工件状态变化示意图;图中标记:1、顶缸吊杆锁母,2、压机顶缸架板,3、四角更换垫筒,4、压机背面贴块,5、压机通用顶杆,6、压紧淬火镶件,7、倒t型顶件器,8、增厚调高垫板,9、主承垫块,10、尾部缩径模芯,11、校正腔内芯,12、校正腔外套,13、成型腔模芯,1301、叉头成型腔,14、成型腔中套,15、成形腔外套,16、台阶模筒座,17、下装大盖母,18、第一上凸模,1801、第一上模芯,1802、第一上模中圈,1803、第一凸模固定座,1804、垫块,19、第二上凸模,1901、第二上模芯,1902、第二上模中圈,1903、第二凸模固定座,1904、主承分割垫块,1905、滑槽,20、工位固定座板,21、油缸连接槽,22、t型导轨垫板,23、连接燕尾分座,24、润滑剂槽,25、随退导向条,26、变程杠杆,27、弹簧滑道支架,28、弹簧,29、滑道,30、压机上模板,31、压机导轨条。
20.100、棒料,200、带细杆部的轴类零件,300、镦挤零件,400、u型叉头零件,500、带滑道零件,600、中间轴成品。
具体实施方式
21.下面结合附图和实施例对本发明作进一步的详细说明,但并不作为对发明做任何限制的依据。
22.实施例1:一种汽车转向系统中间轴的u型叉头双击成型模具,包括上模组件和下模组件,所述上模组件安装在油压机的压机上模板,并随压机上模板上下移动,所述下模组件连接在压机下梁底板上。
23.所述下模组件包括顶缸吊杆锁母1、压机顶缸架板2、四角更换垫筒3、压机背面贴块4、压机通用顶杆5、压紧淬火镶件6、倒t型顶件器7、增厚调高垫板8、主承垫块9、尾部缩径模芯10、校正腔内芯11、校正腔外套12、成型腔模芯13、成型腔中套14、成型腔外套15、台阶模筒座16和下装大盖母17。
24.所述的压机背面贴块4和压机顶缸架板2通过螺栓及顶缸吊杆锁母1连接在压机下梁底板的下表面,螺栓设置四个,分布在压机背面贴块4的四角,且压机背面贴块4和压机下梁底板之间以及压机背面贴块4和压机顶缸架板2之间设置有套在螺栓上的四角更换垫筒3。所述压机背面贴块4的中部设置有上下贯通的通孔,通孔的上端设置有沉槽,并在沉槽内安装压紧淬火镶件6,压紧淬火镶件6和压机背面贴块4过渡配合,压紧淬火镶件6用于承接上方的倒t型顶件器7,压机通用顶杆5自下而上的穿过压机背面贴块4的通孔和压紧淬火镶件6,顶住倒t型顶件器7的下端,倒t型顶件器7可活动的设置在压机下梁底板的通孔中,且倒t型顶件器7向上穿出压机下梁底板。在压机下梁底板上表面放置有增厚调高垫板8,并用螺栓连接,在增厚调高垫板8上表面螺栓连接筒形的台阶模筒座16,在台阶模筒座16内设置主承垫块9和下凹模,主承垫块和增厚调高垫板8在螺栓连接的同时,又被台阶模筒座16内壁的台阶面压紧在增厚调高垫板8上。
25.所述下凹模包括尾部缩径模芯10、校正腔内芯11、校正腔外套12、成型腔模芯13、成型腔中套14和成型腔外套15。所述尾部缩径模芯10的内孔用于成型中间轴尾端的缩径结构,尾部缩径模芯10和校正腔内芯11安装在校正腔外套12的内孔中,且尾部缩径模芯10位于校正腔内芯11的下方,尾部缩径模芯10和校正腔内芯11均与校正腔外套12过盈配合。所述成型腔模芯13、成型腔中套14和成型腔外套15沿径向自内向外依次设置,并位于校正腔外套12的上方,且成型腔模芯13与成型腔中套14、成型腔中套14与成型腔外套15为过盈配
合关系。成型腔模芯13、校正腔内芯11和尾部缩径模芯10形成放置工件的型腔,型腔上端为位于成型腔模芯13内的、用于中间轴u型叉头成型的叉头成型腔1301。成型腔外套15和校正腔外套12之间通过螺栓连接,成型腔外套15的外圆面设置有定位台阶,下装大盖母17压紧在成型腔外套15的定位台阶上,并且下装大盖母17和台阶模筒座16螺栓连接。
26.在所述台阶模筒座16外侧设置有润滑剂槽24,以盛放润滑剂。
27.所述上模组件包括第一上凸模18、第二上凸模19、连接燕尾分座23和工位固定座板20。
28.第一上凸模18用于对工件头部进行镦挤,第一上凸模18包括由内向外设置的第一上模芯1801、第一上模中圈1802和第一凸模固定座1803,第一上模芯1801和第一上模中圈1802通过柱面过盈配合,第一上模中圈1802和第一凸模固定座1803通过锥面过盈配合,第一凸模固定座1803内还通过过盈配合的方式装配有垫块1804,第一上模芯1801和第一上模中圈1802的上端面顶在垫块1804上。所述的第一凸模固定座1803设置在c型的连接燕尾分座23内,并且第一凸模固定座1803上部挂在连接燕尾分座23上。
29.第二上凸模19用于对镦挤后的工件头部反挤压以成型零件的u型叉头,第二上凸模19包括由内向外设置的第二上模芯1901、第二上模中圈1902和第二凸模固定座1903,第二上模芯1901和第二上模中圈1902通过柱面过盈配合,第二上模中圈1902和第二凸模固定座1903通过锥面过盈配合,第二凸模固定座1903内还通过间隙配合的方式装配有主承分割垫块1904,第一上模芯1901和第一上模中圈1902的上端面顶在主承分割垫块1904上。所述的第二凸模固定座1903和工位固定座板20连接,工位固定座板20和所述的连接燕尾分座23固定连接,且工位固定座板20和连接燕尾分座23均与t型导轨垫板22连接,t型导轨垫板22滑动设置在压机导轨条31上,压机导轨条31固定连接在压机上模板30上,在t型导轨垫板22的一侧设置有油缸连接槽21,用于推动t型导轨垫板22水平滑动的水平油缸与油缸连接槽21螺纹连接。通过油缸活塞杆的伸缩推动第一上凸模18和第二上凸模19水平移动,以切换与下模组件配合的上凸模。
30.第二上凸模19中,在第二上模芯1901的相对两侧分别设置两个随退导向条25,随退导向条25滑动设置在第二上模中圈1902和主承分割垫块1904的滑槽1905中,随退导向条25和第二上模芯1901贴合。所述随退导向条25的侧面设置有一个槽口,以连接变程杠杆26。第二上凸模19的第二凸模固定座1903外侧设置一个弹簧滑道支架27,弹簧滑道支架27和第二凸模固定座1903或压机上模板30固定连接,弹簧滑道支架27内设置一个安装弹簧28的滑道29,弹簧滑道支架27下部和所述变程杠杆26的一端转动连接,且弹簧滑道支架27内设置有供所述变程杠杆26上下活动的活动空间,活动空间和所述滑道29连通,以使所述弹簧28能够抵接在变程杠杆26上部的凸台上;所述第二凸模固定座1903开设有供变程杠杆26穿过并上下活动的活动槽,变程杠杆26通过活动槽伸入第二上模中圈1902的滑槽1905中,并通过销轴和随退导向条25侧面的槽口转动连接。
31.在利用第二上凸模19反挤压工件的叉头部分时,叉头向上延长将随退导向条25向上顶起,使得随退导向条25沿第二上模芯1901上移,并抬起变程杠杆26,压缩弹簧28,在压机上模板30回程过程中,弹簧28弹力释放,通过变程杠杆26带动随退导向条25向下移动,回到初始的位置。随退导向条25的设置一方面可以为第二上凸模19导向,另一方面可以合理的分配第二上模芯1901两侧的间隙,保证零件的叉头部分厚薄均匀。
32.实施例2:一种汽车转向系统中间轴的成型工艺,其材质为scm415h,包括如下几个步骤:步骤一,使用退火态冷拉棒料进行下料,得到如图8所示的棒料100,退火态冷拉棒料的要求是:外圆直径尺寸
∅
24.9
±
0.05,外圆无裂纹、夹渣等缺陷,粗糙度为ra3.2以内,退火硬度≤120hb;步骤二,抛丸,采用直径0.6mm的不锈钢钢丸,抛丸时间10至15分钟;步骤三,皮膜处理,采用磷皂化处理或者石墨烯润滑+皂化处理;步骤四,正挤杆,形成一个如图8所示的带有细杆部的轴类零件200,该轴类零件的一端为用于u型叉头成型的粗径端,其余部分均为直径小于粗径端的细杆部,用作后续加工滑道使用;步骤五,双击成型,该工序采用实施例1所述的双击成型模具,主要用于在油压机上成型零件的叉头部分,模具为一凹模两凸模结构,叉头成型步骤:第一上凸模作用:将杆部大端部分镦粗至充满模具的叉头成型腔1301;第二上凸模作用:将镦挤后的大端部分成型为叉头,两位凸模挤压均在同一凹模型腔内进行,由一道工序成型叉头,避免了因镦挤工序带来的冷作硬化所增加的退火工序,也避免了不退火情况下因镦挤造成的冷作硬化造成模具寿命低下,且节省工序,提高了生产效率,降低制造成本;步骤六,去毛刺:使用抛光的方式去除叉头部分棱边的毛刺;步骤七,皮膜处理:磷皂化处理或者石墨烯润滑+皂化处理;步骤八,滑道加工:将正挤杆工序中零件细杆部加工出滑道,作为汽车转向系统中间轴的连接部分,即图8所示的带滑道零件500;步骤九,车削圆柱端面,以成型汽车转向系统中间轴滑道部分尾端,至此完成汽车转向系统中间轴成品600的加工。
33.在上述步骤中,双击成型的具体步骤为:(1)将正挤杆后的工件放入成型腔模芯13和校正腔内芯11中,压机上模板30向下运动,带动上模组件一起下压,此时第一上凸模18的第一上模芯1801与工件接触,使得工件头部镦粗并充满型腔,得到如图8所示的镦挤零件300,在第一上凸模18挤压工件的同时,第二上凸模19同步向下运动,第二上凸模19的第二上模芯1901进入润滑剂槽24蘸取润滑剂。
34.(2)压机上模板30带动上凸模组件回程。
35.(3)水平油缸推动t型导轨垫板22沿压机导轨条31水平移动,带动第一上凸模18和第二上凸模19水平移动,使得第二上凸模19最终停在成型腔模芯13的上方。
36.(4)压机上模板30再次向下运动,第二上凸模19的第二上模芯1901与前述工序得到的镦挤零件300的头部接触进行挤压,形成u型叉头,即图8所示的u型叉头零件400;在u型叉头成型过程中,随着叉子长度增长,叉子顶端与所述的随退导向条25接触并推动随退导向条25向上沿第二上模芯1901回退,同时与随退导向条25连接的变程杠杆26被抬起,对弹簧28压缩。
37.(5)压机上模板30回程,同时被压缩的弹簧28释放弹力,推动变程杠杆26带动随退导向条25向下滑动到原来的位置。
38.(6)水平油缸的活塞回程产生拉力,拉动t型导轨垫板22带动第一上凸模18和第二上凸模19水平移动,使得第一上凸模18重新回到成型腔模芯13的上方。
39.(7)利用压机通用顶杆5将倒t型顶件器7向上顶起,将成型后的工件顶出下模组件。
40.(8)上述过程为双击成型模具动作的一个循环,重复上述过程,即可利用双击成型模具连续动作,完成多个工件头部的双击成型。
41.以上实施例仅用以说明本发明的技术方案而非对其进行限制,所属领域的普通技术人员应当理解,参照上述实施例可以对本发明的具体实施方式进行修改或者等同替换,这些未脱离本发明精神和范围的任何修改或者等同替换均在申请待批的权利要求保护范围之内。