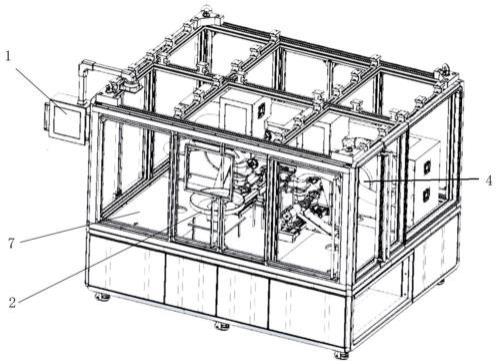
1.本发明涉及动物人工授精自动生产设备技术领域,更具体地说,本发明涉及一种智能化精准高速研磨成型设备。
背景技术:2.随着我国养猪场规模越来越大,产业化越来越集中,母猪人工授精是目前提高繁殖效率的必要手段之一,人工授精器包括输精管、输精管头部和精液瓶,目前市场上输精管头部零件的产能十分低下,需要耗费大量的人工进行手动研磨,来保证头部零件的表面光洁度,从而避免母猪的阴户及阴道划伤感染,因为采用人工研磨所以产品存在合格率低、返工率高、成品之间的尺寸差距大、生产效率低等问题,对于耗材类产品,已经日益无法满足庞大的市场需求。因此,有必要提出一种智能化精准高速研磨成型设备,以至少部分地解决现有技术中存在的问题。
技术实现要素:3.在发明内容部分中引入了一系列简化形式的概念,这将在具体实施方式部分中进一步详细说明。本发明的发明内容部分并不意味着要试图限定出所要求保护的技术方案的关键特征和必要技术特征,更不意味着试图确定所要求保护的技术方案的保护范围。
4.为至少部分地解决上述问题,本发明提供了一种智能化精准高速研磨成型设备,包括:触摸屏、筛盘、粗磨机构、精磨机构、打孔机构和成品检测机构;物料经由所述筛盘排列、筛分后运输至所述粗磨机构制成半成品,半成品经所述精磨机构加工后送至所述打孔机构打孔,然后送至所述成品检测机构进行检验、出货,所述触摸屏用于对设备的运行状况进行控制、监测。
5.优选的是,还包括箱体,所述箱体由箱体梁进行支撑、固定,所述触摸屏通过悬臂与所述箱体连接,所述触摸屏位于所述箱体外部,所述筛盘、所述打孔机构、所述粗磨机构、所述精磨机构和所述成品检测机构均位于所述箱体内,所述箱体底部设置有下料箱,所述下料箱通过下料遮挡板与所述箱体的底部连接,所述下料箱内活动连接有收纳箱,所述成品检测机构的出料端贯穿所述下料遮挡板,并延伸至所述下料箱内。
6.优选的是,还包括运输机构,所述筛盘与所述运输机构连接,所述物料经由所述筛盘排列、筛分后运输至所述运输机构,运输机构将物料依次运送至所述粗磨机构、所述精磨机构进行加工,最后运送至所述打孔机构将物料取出,所述运输机构包括大转盘机构、若干个小转盘机构和大小旋转机构电机;所述小转盘机构呈圆形均匀排列设置在所述大转盘机构上,所述小转盘机构上设置有头部固定机构,所述小转盘机构之间通过皮带连接,所述皮带和所述大转盘机构均与所述大小旋转机构电机连接。
7.优选的是,所述粗磨机构包括粗磨电机、粗磨轮、粗轮架和粗轮传动架;所述粗轮架设置在所述箱体内,所述粗轮架的顶面设置有粗轮调节轨道,所述粗轮传动架通过所述粗轮调节轨道与所述粗轮架连接,所述粗磨电机和所述粗磨轮均设置在所述粗轮传动架
上,所述粗磨电机通过所述粗轮传动架与所述粗磨轮连接。
8.优选的是,所述精磨机构包括精磨电机、精磨轮、精轮架和精轮传动架;所述精轮架设置在所述箱体内,所述精轮架的顶面设置有精轮调节轨道,所述精轮传动架通过所述精轮调节轨道与所述精轮架连接,所述精磨电机和所述精磨轮均设置在所述精轮传动架上,所述精磨电机通过精轮连接轴与所述精磨轮连接。
9.优选的是,所述打孔机构包括头部取出夹具、取出旋转机构和打孔电机,所述头部取出夹具用于夹取加工好的头部零件,所述取出旋转机构用于控制所述头部取出夹具夹取头部零件,并将头部零件转运至所述打孔电机进行打孔,打孔后的成品被所述头部取出夹具放至所述成品检测机构。
10.优选的是,还包括上料装置和吸尘装置;所述上料装置包括原料储存箱和提升装置,所述提升装置用于将所述原料储存箱内的原料运送至所述筛盘内,所述原料储存箱的顶部设置有上料添加口;所述吸尘装置包括粉尘袋、上吸尘口、下吸尘口和负压电机,所述粉尘袋通过吸尘输送管道与所述负压电机连接,所述箱体的顶部通过所述上吸尘口与所述负压电机连通,所述打孔机构通过下吸尘口与所述负压电机连通。
11.优选的是,所述筛盘上设置有排放管组,所述排放管组包括管体、进料单向端盖、出料单向侧盖、限位拦网、吸气装置和喷气装置;所述管体设置在所述筛盘上,所述进料单向端盖设置在所述管体的一端,所述进料单向端盖向所述管体内部开启,所述进料单向端盖位于所述筛盘内部,所述吸气装置设置在所述管体的另一端并位于所述管体内部,所述出料单向侧盖设置在所述管体的侧壁上,并位于所述吸气装置和所述进料单向端盖之间,所述出料单向侧盖向所述管体外部开启,所述喷气装置设置在所述管体的侧壁上并与所述出料单向侧盖的位置相对,所述限位拦网设置在所述管体的内壁,并且所述限位拦网位于所述出料单向侧盖靠近所述吸气装置的一侧。
12.优选的是,所述成品检测机构包括运输线、检测装置和收纳机构;所述运输线的起始端位于所述打孔机构的下方,所述运输线贯穿所述下料遮挡板延伸至所述下料箱内,所述检测装置设置在所述运输线上,所述运输线的末端与所述收纳机构连接,所述收纳机构位于所述收纳箱的上方;所述运输线包括围挡、驱动电机和传送带,所述围挡包裹在所述传送带的外侧,并且所述围挡的顶面设置有下料开口,所述驱动电机和所述检测装置均设置在所述围挡上,所述传送带由若干个适应辊筒组成,所述适应辊筒的两端与所述围挡轴连接,并且所述适应辊筒的两端通过传动带与所述驱动电机连接,所述辊筒包括三个辊环和若干个u型固定卡具,相邻的两个所述辊环之间通过所述u型固定卡具连接,所述u型固定卡具开口向外设置,并且u型固定卡具的u型端向外凸出。
13.优选的是,所述收纳机构包括安装架、正转传送轮、反转传送轮、延长挡板、上挡板、上弧板、下弧板和两台电机;所述正转传送轮、所述反转传送轮、所述延长挡板、所述上挡板、所述上弧板、所述下弧板和所述电机均设置在所述安装架上,所述正转传送轮和所述反转传送轮分别与两台电机连接,所述正转传送轮和所述反转传送轮的表面均设置有若干卡槽;所述延长挡板的一端与所述运输线的末端连接,所述延长挡板的另一端与所述正
转传送轮连接;所述上挡板位于所述延长挡板的上方,所述上挡板的末端与所述上弧板的起始端连接,所述上弧板的末端延伸至所述正转传送轮的四分之一处,并靠近所述反转传送轮的一侧;所述下弧板的起始端设置在所述反转传送轮的四分之一处,并靠近所述正转传送轮的一侧,所述下弧板的末端延伸至所述反转传送轮的底部,所述上挡板和所述延长挡板之间、所述上弧板和所述正转传送轮的卡槽之间、所述下弧板和所述反转传送轮的卡槽之间预留有最低高度。
14.相比现有技术,本发明至少包括以下有益效果:首先在筛盘内放入物料,筛盘会按照一定规律进行排序、筛分、整合,然后排列整合好的物料会运输至粗磨机构进行打磨加工,物料初步研磨成型为头部零件半成品,然后头部零件半成品会运送至精磨机构进行深度研磨,去除产品毛刺,完善产品外观,同时精磨机构可根据不同产品的规格、尺寸、形状对头部零件半成品进行定型、修型,在头部零件精磨结束之后会被送至打孔机构进行打孔制作为成品,打孔后的成品会通过成品检测机构进行运输、检验和出货,成品检测机构可自动识别、检测成品是否合格,并记录生产数据。在每一执行机构处均设计有故障报警功能,通过触摸屏可以提醒操作人员并报告故障位置,通过触摸屏还可方便、高效的查找历史数据。通过实际设备测试,本设备单成品生产耗时约2.8s/个,10000个成品检测中约5-8个残次品,成品率高达99.9%以上。并且一次注入物料后,4h内无需人工参与。通过上述结构的设计,本设备可实现单个产品自动化一体成型,并根据不同产品规格及图纸,进行自动研磨,大大降低人工成本,同时整体研磨过程无需人工参与,从而使产能大大提高,可实现2.8s/个的生产效率,且合格率达到99.9%以上,同时本设备还能自动化记录设备产能及运行时间,自主化设定及排查历史数据。
15.本发明所述的智能化精准高速研磨成型设备,本发明的其它优点、目标和特征将部分通过下面的说明体现,部分还将通过对本发明的研究和实践而为本领域的技术人员所理解。
附图说明
16.附图用来提供对本发明的进一步理解,并且构成说明书的一部分,与本发明的实施例一起用于解释本发明,并不构成对本发明的限制。在附图中:图1为本发明所述的智能化精准高速研磨成型设备的结构示意图;图2为本发明所述的智能化精准高速研磨成型设备的结构示意图;图3为本发明所述的智能化精准高速研磨成型设备中运输机构的结构示意图;图4为本发明所述的智能化精准高速研磨成型设备中精磨机构的结构示意图;图5为本发明所述的智能化精准高速研磨成型设备中粗磨机构的结构示意图;图6为本发明所述的智能化精准高速研磨成型设备中打孔机构的结构示意图;图7为本发明所述的智能化精准高速研磨成型设备的整体结构示意图;图8为本发明所述的智能化精准高速研磨成型设备中上料装置的结构示意图;图9为本发明所述的智能化精准高速研磨成型设备中吸尘装置的结构示意图;图10为本发明所述的智能化精准高速研磨成型设备中排放管组的结构示意图;
图11为本发明所述的智能化精准高速研磨成型设备中输送物料的示意图;图12为图11的剖视图;图13为本发明所述的智能化精准高速研磨成型设备中适应辊筒运送成品的示意图;图14为本发明所述的智能化精准高速研磨成型设备中适应辊筒的结构示意图;图15为本发明所述的智能化精准高速研磨成型设备中标准尺寸和非标尺寸头部零件在适应辊筒上的位置对比图;图16为本发明所述的智能化精准高速研磨成型设备中成品检测机构的结构示意图;图17为本发明所述的智能化精准高速研磨成型设备中收纳机构的结构示意图;图18为本发明所述的智能化精准高速研磨成型设备中收纳机构对头部零件进行收纳时的示意图;图中:1触摸屏、2筛盘、3粗磨机构、31粗磨电机、32粗磨轮、33粗轮架、34粗轮传动架、35粗轮调节轨道、4精磨机构、41精磨电机、42精磨轮、43精轮架、44精轮传动架、45精轮调节轨道、46精轮连接轴、5打孔机构、51头部取出夹具、52取出旋转机构、53打孔电机、6成品检测机构、61运输线、62检测装置、63收纳机构、631安装架、632正转传送轮、633反转传送轮、634延长挡板、635上挡板、636上弧板、637下弧板、638电机、7下料遮挡板、8运输机构、81大转盘机构、82小转盘机构、821头部固定机构、83大小旋转机构电机、9上料装置、91原料储存箱、92提升装置、93上料添加口、10吸尘装置、101粉尘袋、102上吸尘口、103下吸尘口、104负压电机、11排放管组、111管体、112进料单向端盖、113出料单向侧盖、114限位拦网、115吸气装置、116喷气装置、12适应辊筒、121辊环、122u型固定卡具。
具体实施方式
17.下面结合附图以及实施例对本发明做进一步的详细说明,以令本领域技术人员参照说明书文字能够据以实施。
18.应当理解,本文所使用的诸如“具有”、“包含”以及“包括”术语并不排除一个或多个其它元件或其组合的存在或添加。
19.如图1-图18所示,本发明提供了一种智能化精准高速研磨成型设备,包括:触摸屏1、筛盘2、粗磨机构3、精磨机构4、打孔机构5和成品检测机构6;物料经由所述筛盘2排列、筛分后运输至所述粗磨机构3制成半成品,半成品经所述精磨机构4加工后送至所述打孔机构5打孔,然后送至所述成品检测机构6进行检验、出货,所述触摸屏1用于对设备的运行状况进行控制、监测。
20.上述技术方案的工作原理:首先在筛盘2内放入物料,筛盘2会按照一定规律进行排序、筛分、整合,然后排列整合好的物料会运输至粗磨机构3进行打磨加工,物料初步研磨成型为头部零件半成品,然后头部零件半成品会运送至精磨机构4进行深度研磨,去除产品毛刺,完善产品外观,同时精磨机构4可根据不同产品的规格、尺寸、形状对头部零件半成品进行定型、修型,在头部零件精磨结束之后会被送至打孔机构5进行打孔制作为成品,打孔后的成品会通过成品检测机构6进行运输、检验和出货,成品检测机构6可自动识别、检测成品是否合格,并记录生产数据。在每一执行机构处均设计有故障报警功能,通过触摸屏1可
以提醒操作人员并报告故障位置,通过触摸屏1还可方便、高效的查找历史数据。通过实际设备测试,本设备单成品生产耗时约2.8s/个,10000个成品检测中约5-8个残次品,成品率高达99.9%以上。并且一次注入物料后,4h内无需人工参与。通过上述结构的设计,本设备可实现单个产品自动化一体成型,并根据不同产品规格及图纸,进行自动研磨,大大降低人工成本,同时整体研磨过程无需人工参与,从而使产能大大提高,可实现2.8s/个的生产效率,且合格率达到99.9%以上,同时本设备还能自动化记录设备产能及运行时间,自主化设定及排查历史数据。
21.在一个实施例中,还包括箱体,所述箱体由箱体梁进行支撑、固定,所述触摸屏1通过悬臂与所述箱体连接,所述触摸屏1位于所述箱体外部,所述筛盘2、所述打孔机构5、所述粗磨机构3、所述精磨机构4和所述成品检测机构6均位于所述箱体内,所述箱体底部设置有下料箱,所述下料箱通过下料遮挡板7与所述箱体的底部连接,所述下料箱内活动连接有收纳箱,所述成品检测机构6的出料端贯穿所述下料遮挡板7,并延伸至所述下料箱内。
22.还包括运输机构8,所述筛盘2与所述运输机构8连接,所述物料经由所述筛盘2排列、筛分后运输至所述运输机构8,运输机构8将物料依次运送至所述粗磨机构3、所述精磨机构4进行加工,最后运送至所述打孔机构5将物料取出,所述运输机构8包括大转盘机构81、若干个小转盘机构82和大小旋转机构电机83;所述小转盘机构82呈圆形均匀排列设置在所述大转盘机构81上,所述小转盘机构82上设置有头部固定机构821,所述小转盘机构82之间通过皮带连接,所述皮带和所述大转盘机构81均与所述大小旋转机构电机83连接。
23.所述粗磨机构3包括粗磨电机31、粗磨轮32、粗轮架33和粗轮传动架34;所述粗轮架33设置在所述箱体内,所述粗轮架33的顶面设置有粗轮调节轨道35,所述粗轮传动架34通过所述粗轮调节轨道35与所述粗轮架33连接,所述粗磨电机31和所述粗磨轮32均设置在所述粗轮传动架34上,所述粗磨电机31通过所述粗轮传动架34与所述粗磨轮32连接。
24.所述精磨机构4包括精磨电机41、精磨轮42、精轮架43和精轮传动架44;所述精轮架43设置在所述箱体内,所述精轮架43的顶面设置有精轮调节轨道45,所述精轮传动架44通过所述精轮调节轨道45与所述精轮架43连接,所述精磨电机41和所述精磨轮42均设置在所述精轮传动架44上,所述精磨电机41通过精轮连接轴46与所述精磨轮42连接。
25.所述打孔机构5包括头部取出夹具51、取出旋转机构52和打孔电机53,所述头部取出夹具51用于夹取加工好的头部零件,所述取出旋转机构52用于控制所述头部取出夹具51夹取头部零件,并将头部零件转运至所述打孔电机53进行打孔,打孔后的成品被所述头部取出夹具51放至所述成品检测机构6。
26.还包括上料装置9和吸尘装置10;所述上料装置9包括原料储存箱91和提升装置92,所述提升装置92用于将所述原料储存箱91内的原料运送至所述筛盘2内,所述原料储存箱91的顶部设置有上料添加口93;所述吸尘装置10包括粉尘袋101、上吸尘口102、下吸尘口103和负压电机104,所述粉尘袋101通过吸尘输送管道与所述负压电机104连接,所述箱体的顶部通过所述上吸尘口102与所述负压电机104连通,所述打孔机构5通过下吸尘口103与所述负压电机104连通。
27.上述技术方案的工作原理:在进行自动化生产的时候,上料装置9可以为本研磨成型设备供应物料,操作人员可从上料添加口93向原料储存箱91内添加物料,最大容量可实现20000个,约4小时添加一次,然后提升装置92可将原料储存箱91内的物料运送至筛盘2
内,从而实现物料的自动化供应,筛盘2可选用振动筛选盘,可以将物料进行筛分、排序、整合,然后物料会一根一根的运输至运输机构8,依靠气枪的推动力将单根物料推入小转盘机构82上的头部固定机构821进行固定,在大小旋转机构电机83的带动下,小转盘机构82和大转盘机构81均可自转,因小转盘机构82设置在大转盘机构81上,所以小转盘机构82可以使物料自转的同时,公转至粗磨机构3进行粗加工,通过粗轮调节轨道35可以调节粗磨轮32的位置,在进行粗加工的时候,粗磨轮32和物料二者会同时相对转动,从而增加物料的研磨速率和均匀度,并且物料可以在研磨的过程中持续进行移动,进而使得在大转盘机构81上可以设置多个小转盘机构82以实现加工的连续性,提高生产效率,在粗磨电机31的带动下,粗磨轮32飞速旋转,将相对运动的物料初步研磨成型,但是研磨后的头部半成品表面光洁度、形状和尺寸还存在误差,因此需要精磨机构4进行精修,大转盘机构81带动物料经过粗磨机构3的粗加工后继续转动,直至头部半成品运动至精磨机构4,精磨轮42在精磨电机41的带动下转动,同时头部半成品在大转盘机构81和小转盘机构82的带动下可以继续进行自转和公转,精磨轮42和头部半成品二者会同时相对转动,从而增加头部半成品的研磨速率和均匀度,并且在研磨的过程中持续进行移动,进而保证生产的连续性,原理同粗磨机构3内粗加工的原理相同,通过精轮调节轨道45可以调整精磨轮42的相对位置,从而调整精加工的形状、尺寸等。物料在经过粗加工及精加工两次研磨后,便可以通过打孔机构5进行打孔操作,因为运输机构8在持续转动,所以需要通过头部取出夹具51在短时间内实现快速取出,因此头部取出夹具51可采取气动的夹取、运动方式,取出后的半成品在取出旋转机构52的带动下进行水平180
°
旋转,通过打孔电机53对半成品进行打孔得到成品头部零件,为防止钻孔后孔内壁残留毛刺和粉尘,可提前对安装在打孔电机53上的钻头进行精密打磨及细化处理或取用前钻后磨的分段式钻头,以保证孔内壁细腻、平滑,打孔之后的成品会被投放在成品检测机构6进行检测,并穿过下料遮挡板7运输至下料箱内的收料箱中,待收料箱装满后可从下料箱中取出并更换空的收料箱。在粗加工、精加工、打孔的三道工序中,会产生大量的粉尘,因此需要将本研磨成型设备置于箱体内并通过外置的吸尘装置10进行吸尘操作,为了方便操作将触摸屏1通过悬臂延伸至箱体外部,下吸尘口103负责吸取打孔机构5处钻孔的较大的碎屑及粉尘,上吸尘口102设置在箱体顶部,负责抽吸箱体内部研磨及残留的粉尘,在负压电机104的带动下,粉尘会从本研磨设备中吸出,并通过输送管道存放在粉尘袋101中,从而有效防止粉尘污染,保护车间卫生及人员安全。同时为了有效增加该设备的便捷性,在上料装置9、吸尘装置10和本研磨成型设备的底部,分别设计有可移动锁紧轮机构,使设备可以被轻松移动和固定,从而能够轻松改变空间内的设备布局。箱体内也可同时设置多组研磨设备,如图1-7所示的实施例为箱体内配备有两套高速研磨设备,从而可以将上料装置9和吸尘装置10的利用率最大化,并进一步提高加工效率。
28.成品检测机构6内装配有红外线计数仪器,每一成品经过此处时,可自动识别,整体记录生产数据。同时在上料装置9内设计有空料检测装置,可以有效提醒人员原料不足,避免工时浪费及设备无效运转。在每一执行机构处,均设计故障报警功能,以提醒操作者设备故障及告知故障位置。
29.通过实际设备测试,单成品生产耗时约2.8s/个,10000个成品检测中约5-8个残次品,成品率高达99.9%以上。并且一次注入物料后,4h内无需人工参与。
30.在一个实施例中,所述筛盘2上设置有排放管组11,所述排放管组11包括管体111、
进料单向端盖112、出料单向侧盖113、限位拦网114、吸气装置115和喷气装置116;所述管体111设置在所述筛盘2上,所述进料单向端盖112设置在所述管体111的一端,所述进料单向端盖112向所述管体111内部开启,所述进料单向端盖112位于所述筛盘2内部,所述吸气装置115设置在所述管体111的另一端并位于所述管体111内部,所述出料单向侧盖113设置在所述管体111的侧壁上,并位于所述吸气装置115和所述进料单向端盖112之间,所述出料单向侧盖113向所述管体111外部开启,所述喷气装置116设置在所述管体111的侧壁上并与所述出料单向侧盖113的位置相对,所述限位拦网114设置在所述管体111的内壁,并且所述限位拦网114位于所述出料单向侧盖113靠近所述吸气装置115的一侧。
31.上述技术方案的工作原理及有益效果:筛盘2可以将物料一根根的排列在边缘处,然后物料会顶开进料单向端盖112进入到排放管组11的管体111内,物料进入管体111的数量取决于管体111的长度,因为物料需要通过气枪的吹动快速移动到头部固定机构821进行连接,所以气枪需要位于物料的末端对其进行吹气操作,并且需要逐个完成,所以需要物料一根一根的进入气枪的发射机构内,在物料进入管体111内部之后,吸气装置115开启并在管体111内形成负压,如果管体111内的物料较多,则负压会吸动进料单向端盖112向管体111内打开,向内打开的同时会推动物料向管体111内部移动,直至最内侧的物料的端部抵接在限位拦网114上,当管体111内的物料较少,负压会吸动进料单向端盖112向管体111内开启,筛盘2上的物料变会依次进入至管体111内,持续进入的物料会推动最内侧的物料抵接在限位拦网114上,当吸气装置115开启时,喷气装置116关闭,在负压的作用下出料单向侧盖113也保持关闭状态,以上为排放管组11为上料进行的准备工作,当发射机构需要填充物料的时候,吸气装置115关闭,进料单向端盖112关闭(如果管体111内物料较多,进料单向端盖112的端部会搭在物料上无法彻底关闭,也不会影响后续操作),喷气装置116开始喷射气体使出料单向侧盖113开启,使进料单向端盖112承压密封,随后喷气装置116喷射高压气体,将物料从安装出料单向侧盖113的开口处喷至发射机构内,实现发射机构物料的补充,限位拦网114位于出料单向侧盖113的覆盖范围内,以保证物料不会被管体111的侧壁卡住,通过排放管组11可以实现排列好的物料的运输及转运,从而使得单根的物料能够从单独的发射机构喷射至与头部固定机构821连接,从而保证了在运输机构8不停止的情况下物料供应的连续性。
32.在一个实施例中,所述成品检测机构6包括运输线61、检测装置62和收纳机构63;所述运输线61的起始端位于所述打孔机构5的下方,所述运输线61贯穿所述下料遮挡板7延伸至所述下料箱内,所述检测装置62设置在所述运输线61上,所述运输线61的末端与所述收纳机构63连接,所述收纳机构63位于所述收纳箱的上方;所述运输线61包括围挡、驱动电机638和传送带,所述围挡包裹在所述传送带的外侧,并且所述围挡的顶面设置有下料开口,所述驱动电机638和所述检测装置62均设置在所述围挡上,所述传送带由若干个适应辊筒12组成,所述适应辊筒12的两端与所述围挡轴连接,并且所述适应辊筒12的两端通过传动带与所述驱动电机638连接,所述辊筒包括三个辊环121和若干个u型固定卡具122,相邻的两个所述辊环121之间通过所述u型固定卡具122连接,所述u型固定卡具122开口向外设置,并且u型固定卡具122的u型端向外凸出。
33.上述技术方案的工作原理及有益效果:加工好的成品会被头部取出夹具51放置在运输线61上并运输至收纳机构63处进行排列、收纳,运输线61上设置有检测装置62用来进
行计数、检测和标定残次品,组成传送带的适应辊筒12能够自适应不同规格、长度、尺寸的头部零件,如果过头部零件为标准尺寸或较小尺寸,则在其从下料开口掉落的时候,会卡在相邻的两个u型固定卡具122之间,如图15,如果为非标准尺寸的头部零件,则会通过u型固定卡具122的u型端进行限位,通过辊环121的外侧边对其进行支撑,从而保证掉落的头部零件可以整齐的排列在运输线61上,经受检测装置62的检测和标定,对于残次品因为已经进行标定,并且通过触摸屏1进行显示,所以收纳在收纳箱之后无需取出残次品,直接补充合格品的数量即可。
34.在一个实施例中,所述收纳机构63包括安装架631、正转传送轮632、反转传送轮633、延长挡板634、上挡板635、上弧板636、下弧板637和两台电机638;所述正转传送轮632、所述反转传送轮633、所述延长挡板634、所述上挡板635、所述上弧板636、所述下弧板637和所述电机638均设置在所述安装架631上,所述正转传送轮632和所述反转传送轮633分别与两台电机638连接,所述正转传送轮632和所述反转传送轮633的表面均设置有若干卡槽;所述延长挡板634的一端与所述运输线61的末端连接,所述延长挡板634的另一端与所述正转传送轮632连接;所述上挡板635位于所述延长挡板634的上方,所述上挡板635的末端与所述上弧板636的起始端连接,所述上弧板636的末端延伸至所述正转传送轮632的四分之一处,并靠近所述反转传送轮633的一侧;所述下弧板637的起始端设置在所述反转传送轮633的四分之一处,并靠近所述正转传送轮632的一侧,所述下弧板637的末端延伸至所述反转传送轮633的底部,所述上挡板635和所述延长挡板634之间、所述上弧板636和所述正转传送轮632的卡槽之间、所述下弧板637和所述反转传送轮633的卡槽之间预留有最低高度。
35.上述技术方案的工作原理及有益效果:在收纳机构63的下方放置收纳箱,收纳箱可沿头部零件滚动的方向略微倾斜设置,上挡板635从运输线61的末端向内部延伸一段距离,使得在运输线61上的头部零件首先会进入上挡板635的下方,然后再进入上挡板635和延长挡板634之间构成的运输通道中,由此,后进入运输通道的头部零件会推动在先的头部零件进入正转传送轮632的卡槽内,从而防止头部零件堆积并保证头部零件可以依次、连续进入正转转送轮632,避免收纳机构63卡堵,头部零件从正转传送轮632左侧进入卡槽,然后在上弧板636的限位作用下,随着正转传送轮632顺时针转动至右侧四分之一处,此时头部零件的一半位于所述正转传送轮632的卡槽内,另一半位于反转传送轮633的卡槽内,在下弧板637的限位作用下,头部零件会脱离正转传送轮632,并从反转传送轮633的左侧四分之一处逆时针转动运输至其正下方,然后头部零件从下弧板637的端部掉落至收纳箱内,在卡槽和下弧板637的双重限位下,使得头部零件在下落的时候可以保持水平下落,不会出现一边高一边低的情况,进而减少头部零件在收纳箱内错位的情况出现,同时保证了掉落在收纳箱内的头部零件均位于同一方向上,并且可以滚动填平收纳箱,从而使的头部零件可以有序排列在收纳箱中,避免人工规整收纳箱,可以有效提高封装效率。
36.在本发明的描述中,需要理解的是,术语“中心”、“纵向”、“横向”、“长度”、“宽度”、“厚度”、“上”、“下”、“前”、“后”、“左”、“右”、“竖直”、“水平”、“顶”、“底”“内”、“外”、“顺时针”、“逆时针”、“轴向”、“径向”、“周向”等指示的方位或位置关系为基于附图所示的方位或位置关系,仅是为了便于描述本发明和简化描述,而不是指示或暗示所指的装置或元件必
须具有特定的方位、以特定的方位构造和操作,因此不能理解为对本发明的限制。
37.在本发明中,除非另有明确的规定和限定,术语“安装”、“相连”、“连接”、“固定”等术语应做广义理解,例如,可以是固定连接,也可以是可拆卸连接,或成一体;可以是机械连接,也可以是电连接或彼此可通讯;可以是直接相连,也可以通过中间媒介间接相连,可以是两个元件内部的连通或两个元件的相互作用关系,除非另有明确的限定。对于本领域的普通技术人员而言,可以根据具体情况理解上述术语在本发明中的具体含义。
38.尽管本发明的实施方案已公开如上,但其并不仅仅限于说明书和实施方式中所列运用,它完全可以被适用于各种适合本发明的领域,对于熟悉本领域的人员而言,可容易地实现另外的修改,因此在不背离权利要求及等同范围所限定的一般概念下,本发明并不限于特定的细节与这里示出与描述的图例。