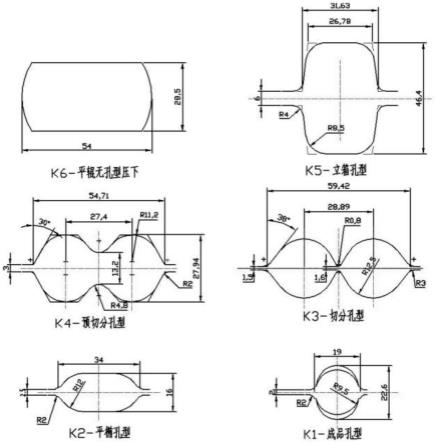
1.本发明涉及一种螺纹钢二切分精轧孔型系统优化方法,适用于18架棒材轧机单线轧制生产线实施技术升级生产二切分20mm规格螺纹。
背景技术:2.随着我国国民经济的蓬勃发展,对中小型建筑钢材需求量日益俱增,质量要求越来越高,在国家提倡节能降耗的大环境下,在保证产品质量的基础上提高产量、节能降耗,是企业急需解决的问题,切分轧制是一种轧钢生产的工艺,与传统工艺相比具有生产率高、节省投资、节约能源、降低成本等优点。在现有产线技术条件下,为实现切分轧制需要新设计φ20mm规格孔型精轧孔型系统。
技术实现要素:3.本发明的目的是提供一种螺纹钢二切分精轧孔型系统优化方法,结合单线轧制原孔型设计提高孔型共用性,优化ф20规格螺纹钢二切分轧制孔型系统。
4.为解决上述技术问题,本发明采用如下技术方案:
5.本发明一种螺纹钢二切分精轧孔型系统优化方法,包括:
6.1)、轧制坯料为150mm
×
150mm方坯,计算总延伸系数,确定轧制道次为16道次;
7.2)、粗、中轧1-10架孔型采用原设计设计单线孔型实现最最大限度共用:粗、中轧1-10架孔型参数表:
[0008][0009][0010]
3)、精轧孔型系统设计专用切分孔型系统:
[0011]
3.1)k6采用平辊无孔型压下设计,压下量26.5mm、宽展12mm;
[0012]
3.2)k5的主要作用是规整k6轧件尺寸,为k4预切分提供尺寸断面适宜的轧件,k5选择立箱子孔型,孔型参数如图1中k5立箱孔型中尺寸:槽深20.2mm、槽底宽31.63mm;
[0013]
3.3)k4预切分孔型为减少切分孔型的不均匀性,使切分楔完成对立箱轧件的压下定位,精确分配对称轧件的断面面积,尽可能减少切分孔型的负担,从而提高切分的稳定性和均匀性,k4孔型参数:侧壁夹角30
°
延伸系数1.14,顶部圆角半径为4.8mm;
[0014]
3.4)k3切分孔型由双圆孔型和切分楔连接而成,孔型参数:延伸系数为1.11,侧壁斜度夹角为38
°
,底部圆角半径为0.8mm;
[0015]
3.5)k2孔型设计采用平椭孔型,为减少切分带撕开后产生的毛刺高度,消除折叠缺陷,k2孔轧件侧面形成充分的鼓形宽展,压下变形量>40%,宽展变形量>20%,孔型尺寸,槽宽34mm、槽深6.75mm。
[0016]
3.6)成品孔型与原设计单线孔型相同。
[0017]
进一步的,原设计单线孔型的具体尺寸参数为:槽宽19mm、槽深8.5mm。
[0018]
与现有技术相比,本发明的有益技术效果:
[0019]
本发明通过ф20规格螺纹钢二切分轧制孔型方案的优化,实现提高产量、节能降本,为今后同类型机组开发提供参考,为相关企业创造可观的经济效益。
[0020]
对比单线轧制日产提升500吨,ф20规格螺纹钢年增达产1万吨钢,20螺吨钢效益(近三年平均)100元/吨,ф20规格螺纹钢年增效可达100万元。
附图说明
[0021]
下面结合附图说明对本发明作进一步说明。
[0022]
图1为ф20规格螺纹钢二切分轧制孔型系统图,图中尺寸单位为mm;
[0023]
图2为1-10架孔型示意图,图中尺寸单位为mm。
具体实施方式
[0024]
一种螺纹钢二切分精轧孔型系统优化方法,具体实施结果步骤如下:
[0025]
1、轧制坯料为150mm
×
150mm方坯,计算总延伸系数,确定轧制道次为16道次。
[0026]
2、粗、中轧1-10架孔型采用原设计设计单线孔型实现最最大限度共用:
[0027]
粗、中轧1-10架孔型参数表
[0028][0029]
[0030]
1-10架孔型如图2所示;
[0031]
3、精轧孔型系统设计专用切分孔型系统:
[0032]
(1)k6采用平辊无孔型压下设计,压下量及宽展如图1中k6采用平辊无孔型压下中所示。
[0033]
(2)k5的主要作用是规整k6轧件尺寸,为k4预切分提供尺寸断面适宜的轧件,选择立箱子孔型,孔型参数如图1中k5立箱孔型中尺寸所示。
[0034]
(3)k4预切分孔型为减少切分孔型的不均匀性,使切分楔完成对立箱轧件的压下定位,精确分配对称轧件的断面面积,尽可能减少切分孔型的负担,从而提高切分的稳定性和均匀性。孔型参数如图1中k4预切分孔型中尺寸所示,侧壁夹角30
°
延伸系数1.14,顶部圆角半径为4.8mm。
[0035]
(4)k3切分孔型由双圆孔型和切分楔连接而成,孔型参数如图1中k3切分孔型中尺寸所示,延伸系数为1.11,为防止耳子产生侧壁斜度夹角为38
°
,底部圆角半径为0.8mm。
[0036]
(5)k2孔型设计采用平椭孔型,为减少切分带撕开后产生的毛刺高度,消除折叠缺陷,k2孔轧件侧面形成充分的鼓形宽展,压下变形量>40%,宽展变形量>20%,孔型尺寸如图1中k2孔型所示。
[0037]
(6)成品孔型与原设计单线孔型相同。
[0038]
4、将加工好的轧辊安装在棒材轧件进行生产;通过结合生产现场实际情况,通过一种ф20规格螺纹钢二切分轧制孔型方案的设计发明,实现提高产量、节能降本,为今后同类型机组开发提供参考,为相关企业创造可观的经济效益,对比单线轧制日产提升500吨,ф20规格螺纹钢年增产可达1万吨钢,20螺吨钢效益(近三年平均)100元/吨,ф20规格螺纹钢年增效=1万吨
×
100元/吨=100万元。
[0039]
以上所述的实施例仅是对本发明的优选方式进行描述,并非对本发明的范围进行限定,在不脱离本发明设计精神的前提下,本领域普通技术人员对本发明的技术方案做出的各种变形和改进,均应落入本发明权利要求书确定的保护范围内。
技术特征:1.一种螺纹钢二切分精轧孔型系统优化方法,其特征在于,包括:1)、轧制坯料为150mm
×
150mm方坯,计算总延伸系数,确定轧制道次为16道次;2)、粗、中轧1-10架孔型采用原设计设计单线孔型实现最最大限度共用:粗、中轧1-10架孔型参数表:机架孔型形状槽深槽宽1h箱441732v箱521303h椭圆36.51504v圆40985h椭圆241346v圆32807h椭圆16.6948v圆21.5559h椭圆11.7568.510v圆32403)、精轧孔型系统设计专用切分孔型系统:3.1)k6采用平辊无孔型压下设计,压下量26.5mm、宽展12mm;3.2)k5的主要作用是规整k6轧件尺寸,为k4预切分提供尺寸断面适宜的轧件,k5选择立箱子孔型,孔型参数如图1中k5立箱孔型中尺寸:槽深20.2mm、槽底宽31.63mm;3.3)k4预切分孔型为减少切分孔型的不均匀性,使切分楔完成对立箱轧件的压下定位,精确分配对称轧件的断面面积,尽可能减少切分孔型的负担,从而提高切分的稳定性和均匀性,k4孔型参数:侧壁夹角30
°
延伸系数1.14,顶部圆角半径为4.8mm;3.4)k3切分孔型由双圆孔型和切分楔连接而成,孔型参数:延伸系数为1.11,侧壁斜度夹角为38
°
,底部圆角半径为0.8mm;3.5)k2孔型设计采用平椭孔型,为减少切分带撕开后产生的毛刺高度,消除折叠缺陷,k2孔轧件侧面形成充分的鼓形宽展,压下变形量>40%,宽展变形量>20%,孔型尺寸,槽宽34mm、槽深6.75mm。3.6)成品孔型与原设计单线孔型相同。2.根据权利要求1所述的螺纹钢二切分精轧孔型系统优化方法,其特征在于,原设计单线孔型的具体尺寸参数为:槽宽19mm、槽深8.5mm。
技术总结本发明公开了一种螺纹钢二切分精轧孔型系统优化方法,包括轧制坯料为150mm
技术研发人员:方琳 郝丽敏 刘洋
受保护的技术使用者:包头钢铁(集团)有限责任公司
技术研发日:2022.11.21
技术公布日:2023/3/28