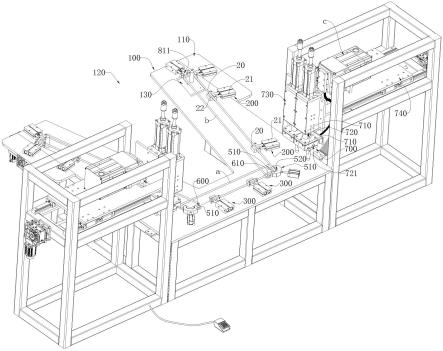
1.本实用新型涉及一种装配式建筑设备,具体涉及一种箱梁框筋的焊接装置。
背景技术:2.目前,在装配式建筑构建的生产中,箱梁构建需要先手工扎结箱梁的钢筋骨架,箱梁钢筋骨架包括多个通过纵向排列纵筋连接箱梁框筋,箱梁框筋普遍与箱梁的横截面仿形,箱梁框筋通过由多个矩形、平行四边形或梯形钢筋框,需将多个钢筋框组合形成箱梁框筋,通常情况钢筋框的规格包括侧框筋以及底框筋,组合结构连接时候,需要将不同框筋安装期望摆放角度的摆放,相邻框筋的脚端叠合,并由作业人员通过钢筋扎丝捆扎,并形成整体的箱梁框筋,采用这种方式加工箱梁框筋,工序多,捆扎位置以及捆扎力度难以控制,效率低,做出来的产品质量不稳定,产品的一致性差,不能适合装配式建筑的生产方式,这种自动化程度较低的生产方式,也不能满足规模化生产,延缓了箱梁加工的工作进程,人们建筑施工时费时费力,给人们造成许多不便。
技术实现要素:3.本实用新型的目的是针对现有技术的不足,提供一种箱梁框筋的焊接装置,它结构简单紧凑,生产效率高,能够对箱梁框筋进行自动化生产,同时箱梁框筋的一致性高。
4.本实用新型的目的是这样实现的:一种箱梁框筋的焊接装置,包括工作平台,所述工作平台上设置用于装夹侧框筋的第一夹紧机构以及用于装夹底框筋的第二夹紧机构,所述工作平台上设置下焊接组件,所述下焊接组件位于第一夹紧机构、第二夹紧机构之间区域,所述工作平台上设置可伸缩的第一限位块,所述第一限位块具有一对定位臂,两定位臂之间具有用于容纳框筋脚端的容纳槽,所述工作平台上对应下焊接组件设置可相对下焊接组件移动的上焊接组件,下焊接组件的下焊接头与上焊接组件的上焊接头之间可形成用于夹持侧框筋以及底框筋的焊接空间,所述下焊接组件的下焊接头以及上焊接组件的上焊接头分别通过导体与焊机电连接。
5.所述工作平台上还设置用于侧框筋上段定位的第一定位柱,所述工作平台上设置可相对第一定位柱伸缩的第一定位块,第一定位柱与第一定位块之间具有大小可调节的夹持空间,待焊接的侧框筋两端部可分别通过第一定位块和第一限位块顶紧。
6.所述工作平台对称设置两个第一夹紧机构、第二夹紧机构、第一限位块、上焊接组件、下焊接组件以及第一定位柱。
7.所述工作平台包括顶板,所述顶板设置凹槽,所述第一夹紧机构、第二夹紧机构、下焊接组件沿着凹槽边侧布置。
8.夹紧机构包括定位凸台以及对应定位凸台设置的直线驱动缸,所述直线驱动缸的前段设置夹紧块,所述定位凸台与夹紧块之间形成大小可调节的夹持空间。
9.所述第一定位柱设置在第一调节组件上,所述第一调节组件设置在工作平台底部,所述工作平台上设置供第一定位柱伸出的通孔,所述第一调节组件包括第一定位板、第
二定位板、第三定位板,第一定位柱设置在第一定位板上,所述第一定位板滑动配合于第二定位板上,所述第二定位板滑动配合于第三定位板上,所述第三定位板与工作平台的底部连接;所述第二定位板上设置用于调节第一定位板滑动距离的第一直线调节装置,所述第三定位板上设置用于调节第二定位板滑动距离的第二直线调节装置,所述第一定位板和第二定位板的滑移方向交叉。
10.所述上焊接组件包括两上焊接头,两上焊接头连接于上导电座上,所述上导电座竖直滑动配合在上滑移组件上,所述上滑移组件安装于水平滑台外端部,所述焊机安装于水平滑台外端部,所述水平滑台滑动配合于立架上,所述立架上设置用于调节水平滑台滑移距离的直线驱动装置。
11.所述上滑移组件包括安装框架,所述安装框架内滑动配合导柱,所述导柱的顶端向上伸出安装框架并与安装框架顶端的气缸连接,所述导柱的下端向下伸出安装框架并与上导电座连接。
12.所述上焊接头活动连接于上导电座的条孔内,该条孔的延伸方向与水平滑台的滑移方向交叉。
13.所述直线调节装置包括电机、涡轮蜗杆减速机以及丝杆,所述涡轮蜗杆减速机固定于相邻两定位板中的其中一定位板上,所述电机的输出端与涡轮蜗杆减速机的输入端传动连接,所述涡轮蜗杆减速机的输出端与丝杆传动连接,该丝杆上螺旋配合滑块,该滑块固定于相邻两定位板中的另一定位板上。
14.采用上述方案,有益效果如下,通过将第一夹紧机构以及第二夹紧机分别将侧框筋以及底框筋进行装夹固定,底框筋与侧框筋相邻的脚端叠合,同时通过控制第一限位块对叠合处的钢筋进行定位,下焊接组件的下焊接头以及将上焊接组件的上焊接头将叠合处的钢筋夹紧形成导电通路,通过焊接递送焊接能量,将叠合处的钢筋实现焊接。采用本实用新型,能够对侧框筋以及底框筋能够快速定位,同时能够使焊接位置稳定,两框筋的固定以及焊接效率高,做出来的产品一致性高,方便对箱梁框筋进行自动化生产,适合装配式建筑的连续生产。
15.下面结合附图和具体实施例对本实用新型作进一步说明。
附图说明
16.图1为本实用新型的结构示意图;
17.图2为上滑移组件与水平滑台连接结构示意图;
18.图3为第一定位板与第二定位板配合结构的分解图。
19.附图中,20为定位凸台,21为直线驱动缸,22为置夹紧块,100为工作平台,110为顶板,120为凹槽,130为通孔,200为第一夹紧机构,300为第二夹紧机构,510为第一限位块,511为定位臂,520为容纳槽,600为下焊接组件,610为下焊接头,700为上焊接组件,710为上焊接头,720为上导电座,721为条孔,730为上滑移组件,731为安装框架,732为导柱,740为水平滑台,750为立架,800为第一调节组件,810为第一定位柱,811为第一定位块,820为第一定位板,830为第二定位板,840为第三定位板,850为电机,860为涡轮蜗杆减速机,870为丝杆,871为滑块,a为侧框筋,b为底框筋,c为焊机。
具体实施方式
20.参照附图,将详细描述本实用新型的具体实施方案。
21.参见图1~图3,一种箱梁框筋的焊接装置的一种实施例,包括工作平台100,所述工作平台100上设置用于装夹侧框筋a的第一夹紧机构200以及用于装夹底框筋b的第二夹紧机构300;当然单个侧框筋a可通过两个或两个以上的第一夹紧机构200进行装夹,同样底框筋b可为通过两个或两个以上第二夹紧机构300进行装夹。所述工作平台100上设置下焊接组件600,所述下焊接组件600位于第一夹紧机构200、第二夹紧机构300之间区域,夹紧机构包括定位凸台20以及对应定位凸台20设置的直线驱动缸21,所述直线驱动缸21的前段设置夹紧块22,所述定位凸台20与夹紧块之间形成大小可调节的夹持空间。当然,第一夹紧机构200可与第二夹紧结构的结构相同,可实现对底框筋b或侧框筋a的装夹。
22.所述工作平台100上设置可伸缩的第一限位块510,所述第一限位块510具有一对定位臂511,两定位臂511之间具有用于容纳框筋脚端的容纳槽520,所述工作平台100上对应下焊接组件600设置可相对下焊接组件600移动的上焊接组件700,下焊接组件600的下焊接头610与上焊接组件700的上焊接头710之间可形成用于夹持侧框筋a以及底框筋b的焊接空间,所述下焊接组件600的下焊接头610以及上焊接组件700的上焊接头710分别通过导体与焊机c电连接。为方便操作人员进出和摆放钢筋框,所述工作平台100包括顶板110,所述顶板110设置凹槽120,所述第一夹紧机构200、第二夹紧机构300、下焊接组件600沿着凹槽120边侧布置,采用这种结构也能够起到省料以及减重的效果。
23.进一步地,所述上焊接组件700包括两上焊接头710,两上焊接头710连接于上导电座720上,所述上导电座720竖直滑动配合在上滑移组件730上,所述上滑移组件730安装于水平滑台740外端部,所述焊机c安装于水平滑台740外端部,所述水平滑台740滑动配合于立架750上,所述立架750上设置用于调节水平滑台740滑移距离的直线驱动装置,采用该结构可对侧框筋a与底框筋b叠合处形成两条焊缝,同时上焊接组件700可实现竖直或/和水平位置的调节,方便移开上焊接组件700,便于装夹。具体到本实施例中,所述上滑移组件730可包括安装框架731,所述安装框架731内滑动配合导柱732,所述导柱732的顶端向上伸出安装框架731并与安装框架731顶端的气缸连接,所述导柱732的下端向下伸出安装框架731并与上导电座720连接,采用该结构可实现上滑移组件730竖直方向上的移动。再进一步地,所述上焊接头710活动连接于上导电座720的条孔721内,该条孔721的延伸方向与水平滑台740的滑移方向交叉,采用该结构,可沿条孔721调节上焊接头710位置;当然再配合水平滑台740位置调整,可实现上焊接头710水平位置的调整。
24.进一步地,所述工作平台100上还设置用于侧框筋a上段定位的第一定位柱810,所述工作平台100上设置可相对第一定位柱810伸缩的第一定位块811,第一定位柱810与第一定位块811之间具有大小可调节的夹持空间,通过第一定位柱810可对侧框筋a进行初步定位,也能对第一定位块811推动的侧框筋a进行限位,保证其运动的极限位置稳定。待焊接的侧框筋a两端部可分别通过第一定位块811和第一限位块510顶紧,通过顶紧,能够使侧框筋a保持稳定,使其在上焊接头710的冲击情形下,不易窜动。进一步地,所述第一定位柱810可设置在第一调节组件800上,所述第一调节组件800设置在工作平台100底部,所述工作平台100上设置供第一定位柱810伸出的通孔130,所述第一调节组件800包括第一定位板820、第二定位板830、第三定位板840,第一定位柱810设置在第一定位板820上,所述第一定位板
820滑动配合于第二定位板830上,所述第二定位板830滑动配合于第三定位板840上,所述第三定位板840与工作平台100的底部连接;所述第二定位板830上设置用于调节第一定位板820滑动距离的第一直线调节装置,所述第三定位板840上设置用于调节第二定位板830滑动距离的第二直线调节装置,所述第一定位板820和第二定位板830的滑移方向交叉,采用该结构可根据需求调节第一定位柱810的水平位置。第一直线调节装置或/和第二直线调节装置可为气缸、电动缸或者液压缸等直线驱动装置;具体到本实施例中,直线调节装置包括电机850、涡轮蜗杆减速机860以及丝杆870,所述涡轮蜗杆减速机860固定于相邻两定位板中的其中一定位板上,所述电机850的输出端与涡轮蜗杆减速机860的输入端传动连接,所述涡轮蜗杆减速机860的输出端与丝杆870传动连接,该丝杆870上螺旋配合滑块871,该滑块871固定于相邻两定位板中的另一定位板上,通过该结构可实现驱动相邻两定位板的相对直线运动,在更换框筋规格情形下,便于调节定位柱位置。
25.上述方案,可对附图1中箱梁框筋的一侧进行自动化焊接,焊接后可翻转,对另外一侧进行自动化焊接,为便于箱梁框筋的两角端同时进行焊接,即一个底框筋b两端分别同时与侧框筋a连接固定的情形,减少翻转和装夹的次数,所述工作平台100对称设置两个第一夹紧机构200、第二夹紧机构300、第一限位块510、上焊接组件700、下焊接组件600以及第一定位柱810。所述工作平台100包括顶板110,所述顶板110设置凹槽120,所述第一夹紧机构200、第二夹紧机构300、下焊接组件600沿着凹槽120边侧布置,两第一夹紧机构200分别位于凹槽120两侧,第二夹紧机构300对应于凹槽120底侧部分布置,两夹紧机构可用于共同装夹同一底框筋b,增加底框筋b的装夹刚度,凹槽120方便操作人员进出和摆放钢筋框,同时还能实现减重。
26.采用上述方案进行箱梁框筋焊接时,将两侧框筋a放置于让位凹槽120两侧,侧框筋a套置于对应的定位柱内,通过两第一定位块811分别对两侧框筋a推动,使其达到期望的位置,同时夹紧机构对框筋进行夹紧,同时将底框筋b的两端叠放分别在两侧框筋a的下角端,然后通过第一限位块510对钢筋框叠放处进行定位,保证侧框筋a相对底钢筋框的位置精度,进而保证焊接精度。在箱梁框筋完成了组装和定位后,上焊接头710压在箱梁框筋的上端,上焊接头710和下焊接头610之间形成焊接空间,焊机c的焊接电流流过箱梁框筋并促使叠放的钢筋框完成焊接,完成焊接后,上焊接头710撤离下焊接头610的上方位置,各夹紧机构松开,取出箱梁框筋,完成单个箱梁框筋的焊接。采用本实用新型,它结构简单紧凑,生产效率高,能够对箱梁框筋进行自动化生产,同时箱梁框筋的一致性高。
27.以上所述仅为本实用新型的优选实施例,并不用于限制本实用新型,显然,本领域的技术人员可以对本实用新型进行各种改动和变型而不脱离本实用新型的精神和范围。这样,倘若本实用新型的这些修改和变型属于本实用新型权利要求及其等同技术的范围之内,则本实用新型也意图包含这些改动和变型在内。